AFP en evolución para la próxima generación
Si la colocación automatizada de fibra (AFP) y la colocación automatizada de cinta (ATL) fueron los procesos de fabricación que permitieron la aplicación generalizada de compuestos en el Boeing 787 y Airbus A350, entonces también serán AFP / ATL los que lideren el camino para la próxima generación de productos comerciales. aviones, ahora en tableros de dibujo. ¿La diferencia esta vez? Calificar.
Boeing estima que, para 2037, el mundo necesitará más de 31.000 nuevos aviones de pasillo único para satisfacer la demanda de pasajeros. Airbus prevé la necesidad de más de 28.000 aviones de pasillo único para 2037. Ambas compañías están considerando reemplazar a sus incondicionales de pasillo único:el 737 (Boeing) y el A320 (Airbus). Se espera que ambas compañías empleen compuestos de manera significativa en cualquier avión nuevo que desarrollen. Ambas compañías están diciendo a sus cadenas de suministro que esperen tasas de producción para estos aviones de 60-100 aviones por mes, con énfasis en 100. La categoría de pasillo único, para ambas compañías, representa aproximadamente dos tercios de la demanda global total, lo que significa que el El entorno de fabricación desarrollado para aviones de pasillo único se convertirá en el entorno de fabricación predeterminado para aerocomposites en el futuro previsible.
Todo esto significa que la tecnología de automatización debe desarrollarse ahora si quiere mantenerse al día con los requisitos de calidad y tasa de producción de los aviones de próxima generación. Nada de esto pasa desapercibido para el ingeniero senior de Electroimpact (EI, Mukilteo, Washington, EE. UU.), Todd Rudberg. Rudberg y EI ingresaron al mundo de los compuestos en 2004 cuando la compañía desarrolló la tecnología AFP para la fabricación de la sección del fuselaje delantero 787 Sección 41 fabricada por Spirit AeroSystems (Wichita, Kansas, EE. UU.). Posteriormente, EI pasó a producir sistemas AFP y ATL para la fabricación de otras estructuras 787, estructuras A350, estructuras de motores y, más recientemente, largueros de alas de Boeing 777X. Ahora, Rudberg está mirando el futuro de la fabricación de aviones de próxima generación y ve oportunidades para que AFP mejore. Sustancialmente.
Las oportunidades, dice Rudberg, son obvias cuando uno mira los datos. De hecho, EI ha desarrollado varias métricas para ayudar a la empresa a comprender qué hace bien su maquinaria y qué puede mejorar. Primero, al observar el panorama de las AFP de 2019, Rudberg ve innumerables amenazas a la tecnología AFP actual, que incluyen ATL, colocación manual, cargas planas de telas tejidas y, por supuesto, aluminio.
Las métricas de AFP que desarrolló Rudberg provienen de un proyecto de demostración de producción completa (FPD) para el cual EI realizó cuatro compilaciones de preproducción. Los datos de una de esas compilaciones, realizada en febrero de 2019 con tecnología EI AFP "estándar", revelaron un desafío sustancial en la utilización de la máquina, con el tiempo de uso de la máquina en uno de siete grupos:
- Proyección láser:30%
- Ejecutar:27%
- Inspección:22%
- Descanso:10%
- Parada inducida por el operador:6%
- Recuperación de errores:3%
- Imagen:2%
Visto de otra manera, con la tecnología actual, hay una operación de valor agregado en AFP (ejecutar), y todas las demás se consideran operaciones sin valor agregado. Por tanto, la relación entre operaciones de valor y operaciones sin valor es 1:3. "La industria realmente quiere 3:1, y yo también", dice Rudberg, "y me gustaría hacer esto antes de jubilarme". El objetivo, simplemente, es reducir el tiempo consumido por operaciones sin valor agregado.
También hay una métrica de AFP general que necesita explicación:franjas medias antes de fallar (MSBF). Este es el número medio de cables de fibra colocados entre fallos de colocación. Por supuesto, cuanto mayor sea este número, más fiables serán la máquina y el proceso. La compilación del FPD de febrero, dice Rudberg, tenía 5.365 MSBF.
Los goles
Mirando más de cerca la operación de AFP, dice Rudberg, EI tiene control directo sobre solo tres operaciones:ejecución, recuperación de errores e inspección. Y aquí es donde la empresa centra sus esfuerzos. Dicho esto, Rudberg señala que la estructura del avión también tiene un papel que desempeñar, particularmente en la reducción de las inspecciones de calidad, las roturas y las paradas inducidas por el operador. “Tenemos que darnos cuenta de que los tiempos de ejecución se han reducido mucho porque las máquinas son muy rápidas”, dice, “y cualquier cosa que no agregue valor tiene un impacto masivo en su utilización. Entonces, resulta que este es un deporte de equipo. No solo el OEM (yo) tiene que hacerlo mejor, sino que también el fuselaje tiene cierta responsabilidad ".
Para la fabricación de aeronaves de próxima generación, Rudberg quiere aumentar el MSBF a> 20.000, aumentar el tiempo de ejecución al 77% y eliminar por completo la proyección láser, la parada inducida por el operador y la imagen. ¿Cómo? Rudberg identifica tres áreas tecnológicas que pueden facilitar esta transición:filetas servoaccionadas, inspección en proceso del 100% y gestión de datos, o EI 4.0.
Los tres han sido evaluados por la IE en una serie de compilaciones de proyectos FPD recientes después de la compilación inicial de febrero. Los datos del propio proyecto FPD demuestran que la IE va en la dirección correcta. Rudberg dice que el sistema AFP utilizado, llamado MuSCLE, logró una potencia máxima de 1.500 caballos de fuerza, una aceleración / desaceleración de 0.5G, una tasa de reposo de 4,000 pulgadas / minuto, un tiempo de giro de cabeza de 1 segundo, una velocidad de esquina de mástil de 120 grados / segundo y 6,000 MSBF. (logrado en producción).
La conversión a filetes de servomotor, y lejos de filetes de servomotor, dice Rudberg, se ha realizado para aumentar la velocidad de colocación del remolque, la precisión de colocación del remolque, el control de la tensión del remolque y la confiabilidad general de construcción. La compañía ha pasado los últimos dos años trabajando en un servoaccionamiento compacto que se puede instalar en el cabezal modular EI. Los resultados de la tecnología, hasta ahora, son prometedores; Las pruebas muestran:15.000 MSBF, velocidad de adición 87% más rápida, velocidad de corte 36% más rápida, mejor precisión en la colocación de los extremos. Además, EI demostró que el sistema de filete de servomotor podía usarse para colocar fibras de carbono secas.
La clave para la inspección es la parte "en proceso". EI ya cuenta con tecnología de inspección, desarrollada con Aligned Vision (Chelmsford, Mass., EE. UU.) E implementada en la línea de fabricación de alas 777X que utiliza tecnología láser y de visión para verificar si hay vueltas, espacios, arrugas, errores de colocación de extremos y restos de objetos extraños ( FOD). Sin embargo, este sistema existe independientemente del sistema AFP y requiere un campo de visión despejado para funcionar, lo que significa que el cabezal AFP debe moverse. Rudberg y EI han desarrollado un nuevo sistema de inspección, llamado RIPIT, que es parte integral del cabezal AFP e inspecciona la colocación de la fibra tan pronto como ocurre.
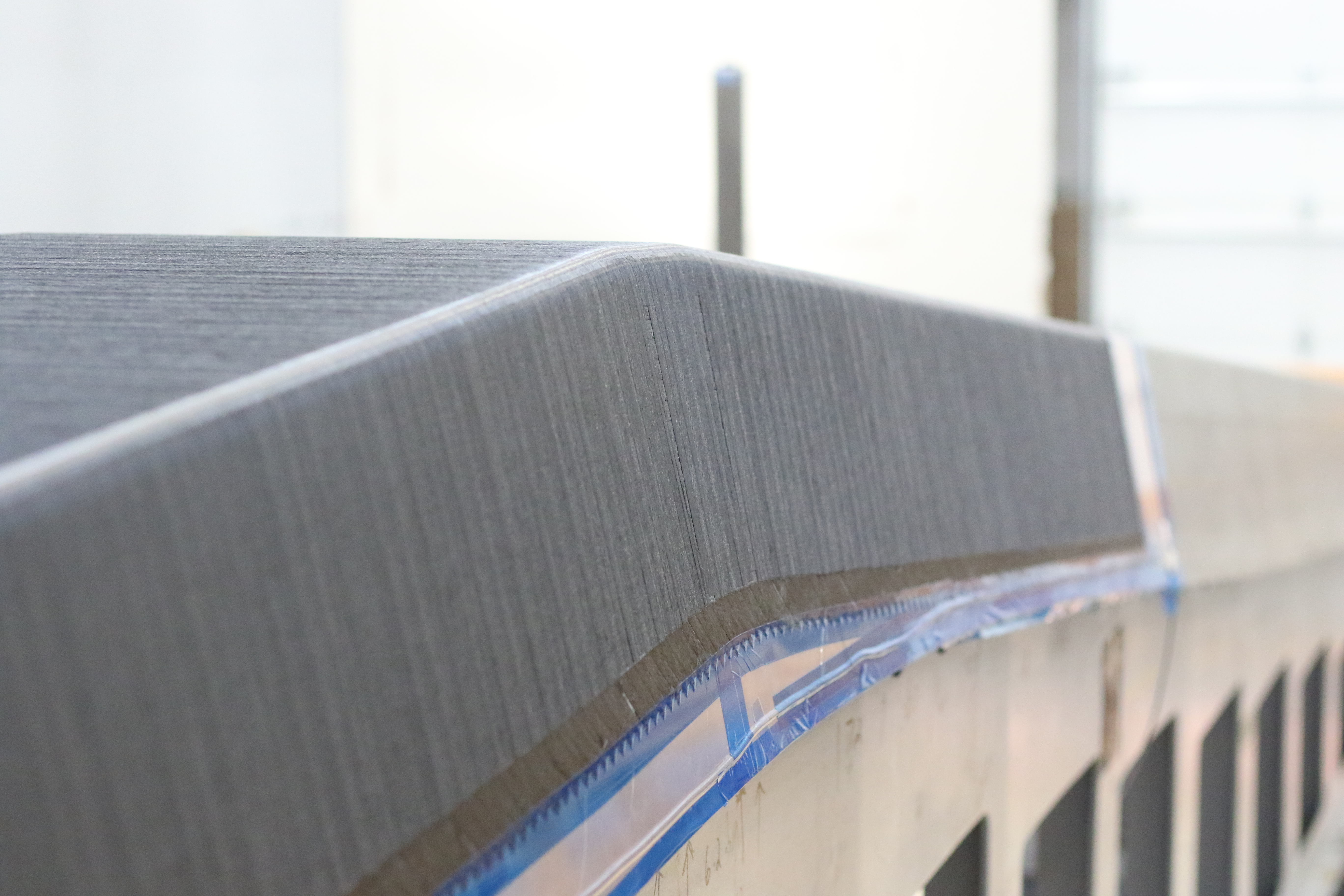
Dado que Boeing y Airbus consideran los procesos de fabricación de compuestos fuera de autoclave, la capacidad de los sistemas AFP para colocar de manera eficiente las fibras de carbono seco será fundamental. Este larguero demostrador muestra fibra seca colocada por un sistema Electroimpact. Fuente | Electroimpacto
EI no divulgará la naturaleza de la tecnología detrás de RIPIT excepto para decir que no está basada en láser o visión. En cualquier caso, Rudberg dice que las pruebas del sistema revelan que es capaz de detectar, en tiempo real, el deslizamiento del remolque a ± 0.030 pulgadas, agregar la ubicación a ± 0.050 pulgadas y cortar la ubicación a ± 0.050 pulgadas. Además, dice Rudberg, "Hemos realizado muchas pruebas correlacionando los datos RIPIT con el sistema de visión calificado por Boeing existente [sistema Aligned Vision usado en 777X] y obtenemos correlación".
El valor de la gestión de datos, dice Rudberg, se basa en la capacidad de los sistemas de EI para ayudar a los fabricantes a ver más claramente qué tan bien está funcionando el proceso de AFP. Con ese fin, EI ha desarrollado un software de visualización de datos, EI 4.0, que ofrece visibilidad no solo del rendimiento de una máquina determinada (según MSBF) durante una construcción determinada, sino también del rendimiento de las secuencias y los remolques individuales. Básicamente, el software ayuda al operador a ver exactamente en qué parte de la cabeza AFP está el problema. "Entonces, usaremos este EI 4.0 para indicar dónde [los operadores] deben ir a buscar en la cabeza de AFP para hacer cambios", dice Rudberg.
Con este software, es posible mostrar gráficamente MSBF para una variedad de funciones de la máquina e identificar cables de fibra problemáticos y secuencias particularmente desafiantes. El software también mide e informa sobre otras actividades de la máquina que podrían afectar la utilización. Con estas herramientas de gestión de datos, EI pudo optimizar y reducir el tiempo de creación del OPS de más de 50 minutos a poco menos de 40 minutos. Otras herramientas incluyen comparaciones de rendimiento de cambio y comparaciones de ángulos de pliegue.
"Creo que la utilización del 75% es una meta o expectativa realista", afirma Rudberg. “Pero, va a requerir trabajo en equipo, va a tomar la iniciativa organizacional y el seguimiento de la estructura del avión, va a necesitar nuestra tecnología mejorada, va a necesitar un mejor mantenimiento preventivo y mantenimiento predictivo, y mejores herramientas para analizar el uso de las células y rendimiento de la máquina ".
Resina
- Industria 4.0 e IoT:Tendencias del mercado para los próximos años
- Realidad aumentada:¿el próximo gran avance para RR.HH.?
- DARPA está trabajando en materiales de próxima generación para vehículos hipersónicos
- Nuevos cristales para tecnologías de visualización de próxima generación
- Cómo prepararse para la próxima interrupción de la cadena de suministro
- Cinco reglas para la próxima crisis de la cadena de suministro
- La comercialización en la nube es el próximo imprescindible para el comercio minorista
- Material para la próxima generación de sensores inteligentes
- COVID-19:demanda de la próxima generación de fábricas inteligentes
- ¿Qué sigue para la revolución de la automatización?
- Generación de nitrógeno en la industria aeroespacial