Los materiales compuestos aceleran la fabricación de fachadas de hormigón
Cada edificio de varios pisos construido hoy requiere una fachada. Derivado de la palabra francesa fachada , que a su vez provino del italiano facciata , significa "cara". En resumen, la fachada es la estructura exterior que da al público que le da al edificio su carácter, color y forma. Para los arquitectos, la fachada marca la pauta para el resto del edificio y dice mucho sobre la intención arquitectónica del diseñador.
Una fachada también es funcional. Proporciona la estructura que rodea las ventanas y puertas, protege el edificio del clima y los impactos y afecta la eficiencia energética del edificio. Una fachada se puede construir con una variedad de materiales, incluidos compuestos, piedra, acero, vidrio u hormigón. El hormigón en una fachada, en virtud de su formabilidad, se puede utilizar para darle a un edificio una apariencia muy dimensional y visualmente impactante, particularmente si las formas del hormigón son variadas.
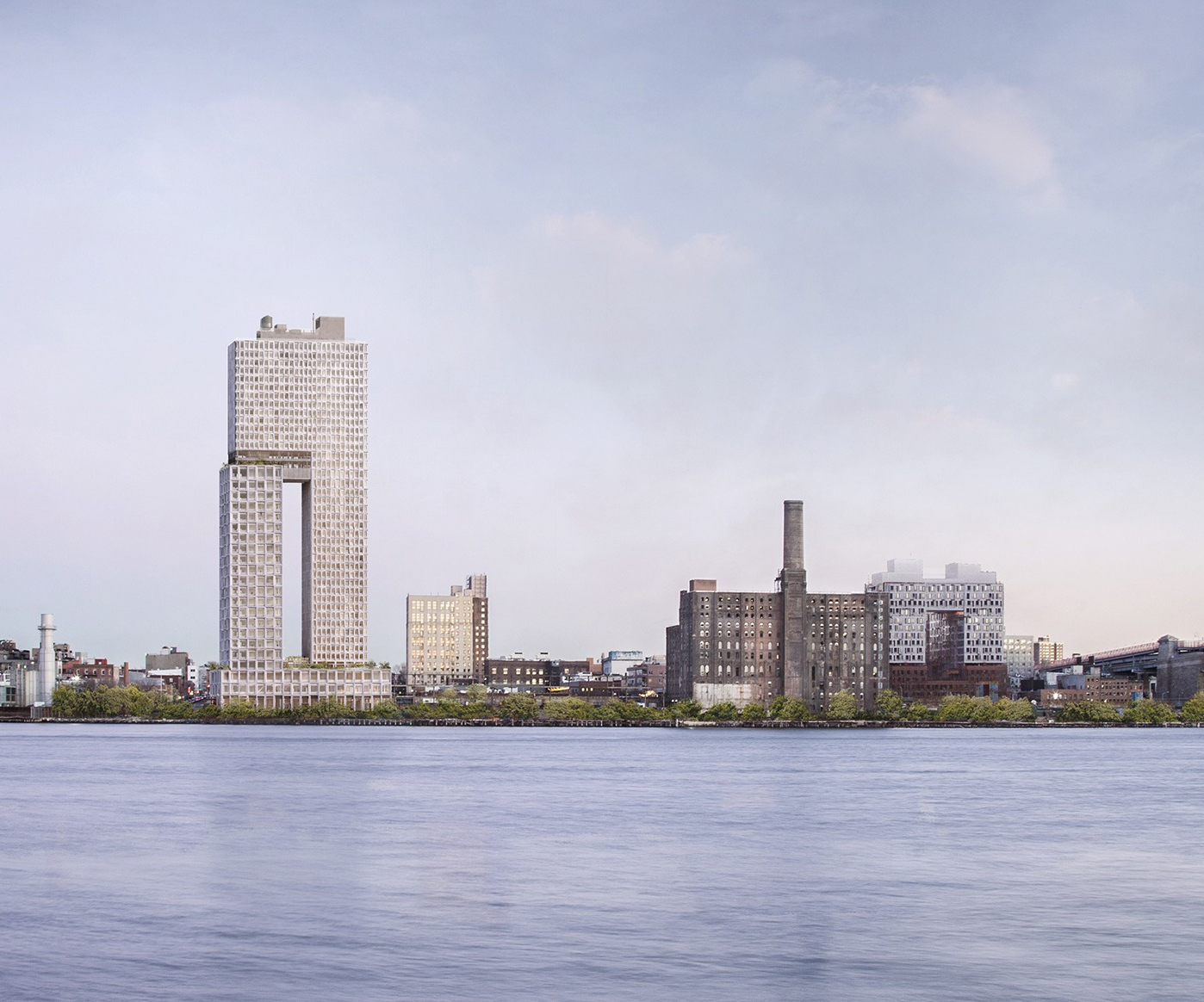
El azúcar es el rey
Este fue el caso en Domino Park, un proyecto de reurbanización de 11 acres a lo largo del paseo marítimo de Williamsburg en Brooklyn, NY, EE. UU. En el corazón de Domino Park se encuentra la refinería de azúcar Domino, de 138 años de antigüedad, que cerró en 2004 y ahora está siendo renovada como oficina y local comercial. Parte de Domino Park incluye varios edificios nuevos, incluido el One South First de 45 pisos y el 10 Grand adjunto. Para estos edificios, el arquitecto COOKFOX (Nueva York, NY) decidió utilizar una fachada de hormigón que presenta múltiples ángulos de superficie, múltiples formas de marcos de ventanas y múltiples anchos de marcos de ventanas para, desde la distancia, transmitir libremente una sensación de cristalinidad del azúcar, en mantener el historial del sitio.
Gate Precast Co. (Jacksonville, Florida, EE. UU.) Ganó el contrato para construir la fachada de hormigón, básicamente, una serie de marcos de ventanas, para el proyecto One South First. La empresa, como es típico en una fachada de hormigón, fabricaría los marcos en sus propias instalaciones y luego enviaría los marcos terminados al lugar de trabajo donde se colocarían en su lugar para su instalación mediante una grúa. Si Gate hubiera decidido seguir la tradición, habría construido moldes de madera con los que dar forma a todos los marcos de hormigón. Gate, sin embargo, decidió no seguir la tradición.
Para comprenderlo, vuelva a 2017, cuando Gate se asoció con el Instituto de hormigón prefabricado / pretensado (PCI, Chicago, Ill., EE. UU.) Y el Laboratorio Nacional Oak Ridge (ORNL, Oak Ridge, Tennessee, EE. UU.) Para realizar una evaluación preliminar de el uso de fabricación aditiva de gran formato para construir moldes compuestos para el conformado de hormigón prefabricado en planta. Esta evaluación se realizó utilizando una máquina BAAM (Big Area Additive Manufacturing) en ORNL. BAAM es una máquina de fabricación aditiva de gran formato con una envolvente de construcción de 25 metros cuadrados, desarrollada conjuntamente por ORNL y Cincinnati Inc. (Harrison, Ohio, EE. UU.) Gate se comprometió a construir moldes compuestos para la fachada One South First. El proyecto requirió 80 moldes en total, 37 de los cuales serían impresos. Los 43 restantes estarían hechos de madera. Cuando se tomó esta decisión, los plazos para la entrega del molde eran ajustados.
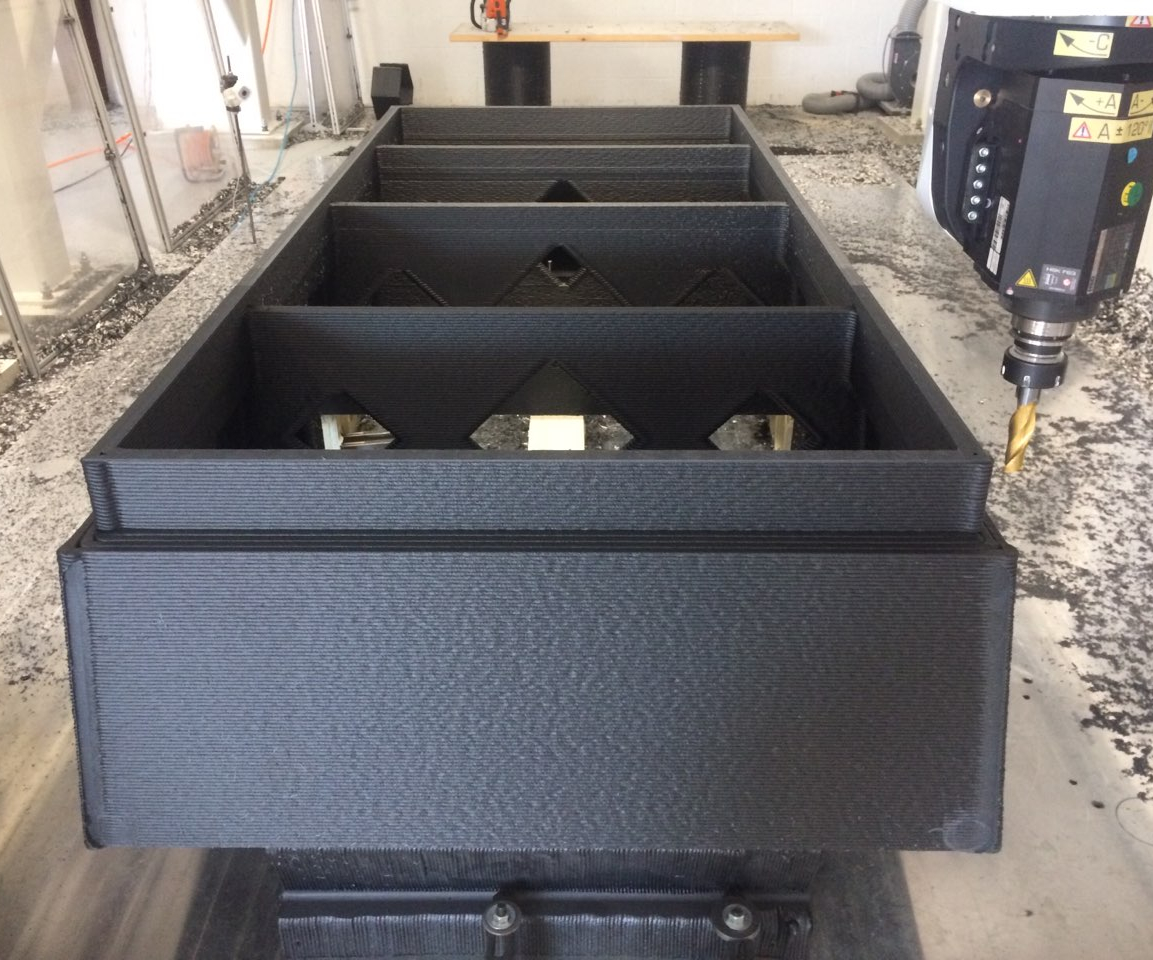
En 2016, Additive Engineering Solutions (AES, Akron, OH) había adquirido su primera máquina BAAM de Cincinnati Inc. Por eso, ORNL y Gate Precast acudieron a AES en busca de ayuda. Andrew Bader, vicepresidente y cofundador de AES, dice que su empresa y ORNL dividieron el paquete de trabajo, con AES produciendo 18 de los 37 moldes. Bader dice que cada molde de marco de ventana mide alrededor de 5 a 6 pies de ancho, 9 a 10 pies de alto y 16 pulgadas de profundidad y pesa alrededor de 500 libras.
Bader dice que el interior de la geometría de los moldes, debido a que están diseñados para producir marcos que rodean ventanas rectangulares, fue relativamente simple. Sin embargo, el diseño de las superficies exteriores de los marcos, como se señaló, fue más complejo, con profundidades y ángulos variados integrados en cada molde. Una forma impresa reemplazó a una forma de madera compuesta por muchas piezas cortadas individualmente clavadas juntas. “La geometría era simple, pero complicada”, dice Bader. "El proyecto requirió varios diseños de marcos únicos, según la ubicación del marco".
Para parte de su producción, AES eligió un compuesto LNP THERMOCOMP AM, un material de alto módulo y baja deformación basado en ABS con un 20% de refuerzo de fibra de carbono cortada suministrado por SABIC (Houston, Texas, EE. UU.). Bader dice que la máquina BAAM tardó de 8 a 10 horas en construir cada molde monolítico, seguidas de 4 a 8 horas de mecanizado y acabado en una máquina CNC Quintax (Stow, Ohio, EE. UU.). Informa que los moldes se lijaron a las dimensiones requeridas, pero no se sellaron.
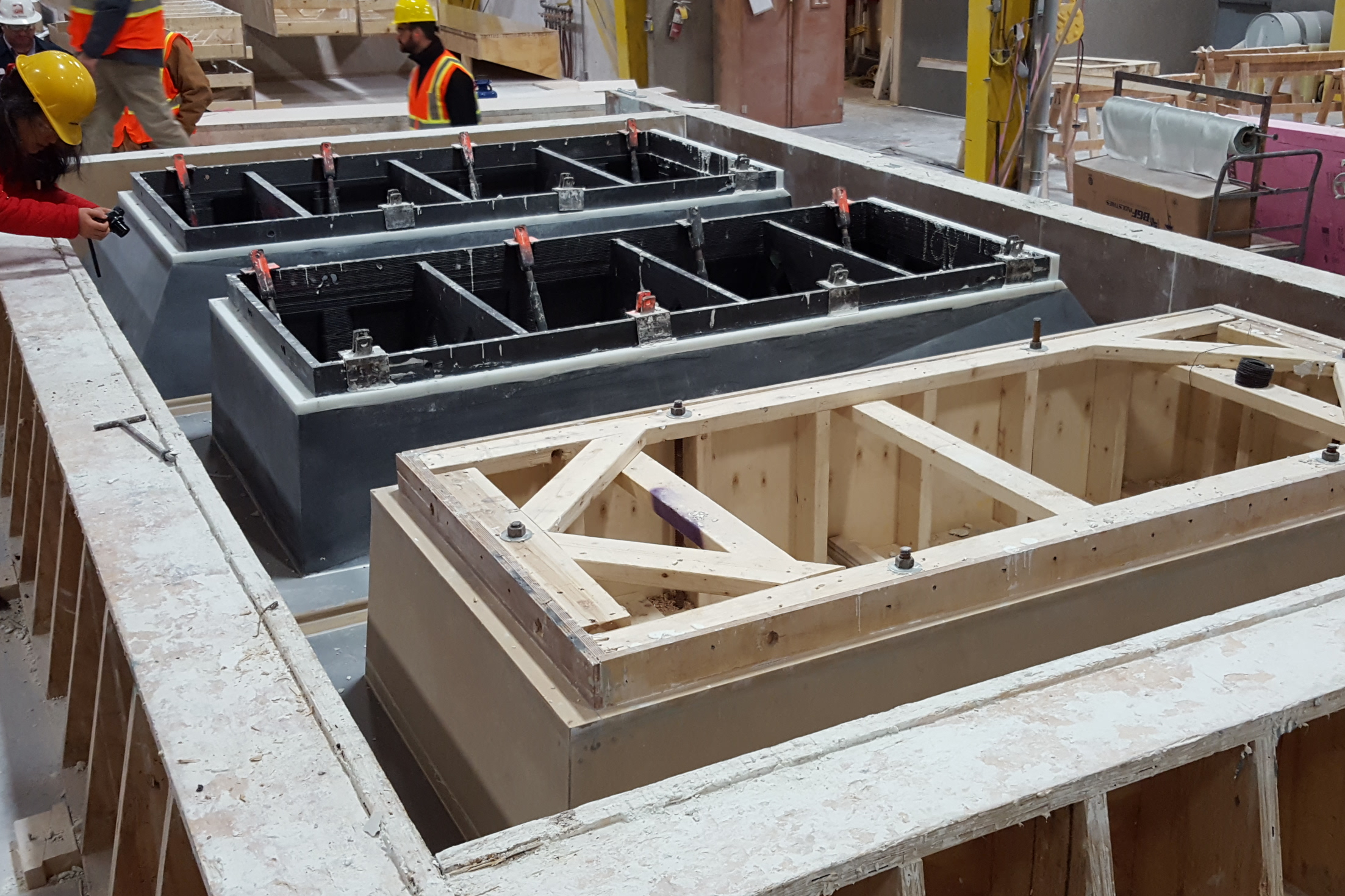
Fabricación de marcos de ventanas
Los moldes se entregaron en las instalaciones de Gate en Winchester, Ky., EE. UU., Donde se utilizaron junto con los 43 moldes de madera tradicionales que Gate construyó para el proyecto. Los empleados de Gate ensamblaron a mano los moldes de madera, luego se aplicó una estera de fibra de vidrio y una capa de resina, con aceite de encofrado rociado para facilitar la liberación del marco de concreto formado. También se roció aceite de encofrado sobre los moldes compuestos para facilitar el desmoldeo.
Para realizar un vaciado de hormigón, se colocaron varios moldes en una mesa de fundición de madera de 40 a 50 pies de largo. Los moldes se agruparon para producir un solo marco, un marco doble o un marco triple. Se colocó una barra de refuerzo de acero dentro de cada molde y se vertió hormigón alrededor de la barra de refuerzo. A continuación, se hizo vibrar la mesa de colada para consolidar el hormigón. Después de 14-20 horas de curado, los marcos de las ventanas se desmoldaron, se lavaron con ácido y se pulieron. Luego, se instalaron las ventanas y el paquete completo se envió en camión al sitio de construcción en Brooklyn.
Bader dice que los moldes compuestos AES, junto con los moldes de madera tradicionales, revelaron rápidamente sus ventajas. Primero, dice, un molde de madera solo permite de 15 a 20 vertidos de concreto antes de que deba retirarse del servicio y restaurarse o reemplazarse. Los moldes AES, por el contrario, permitieron 200 vertidos de hormigón con un mínimo de renovación o tiempo fuera de servicio. Y los 200 vertidos, dice Bader, representaron el final del proyecto, no el final de la vida útil del molde. "Ahí es donde se detuvieron", dice. "Si nuestros moldes se cuidan adecuadamente, creemos que se pueden usar cientos y cientos de veces".
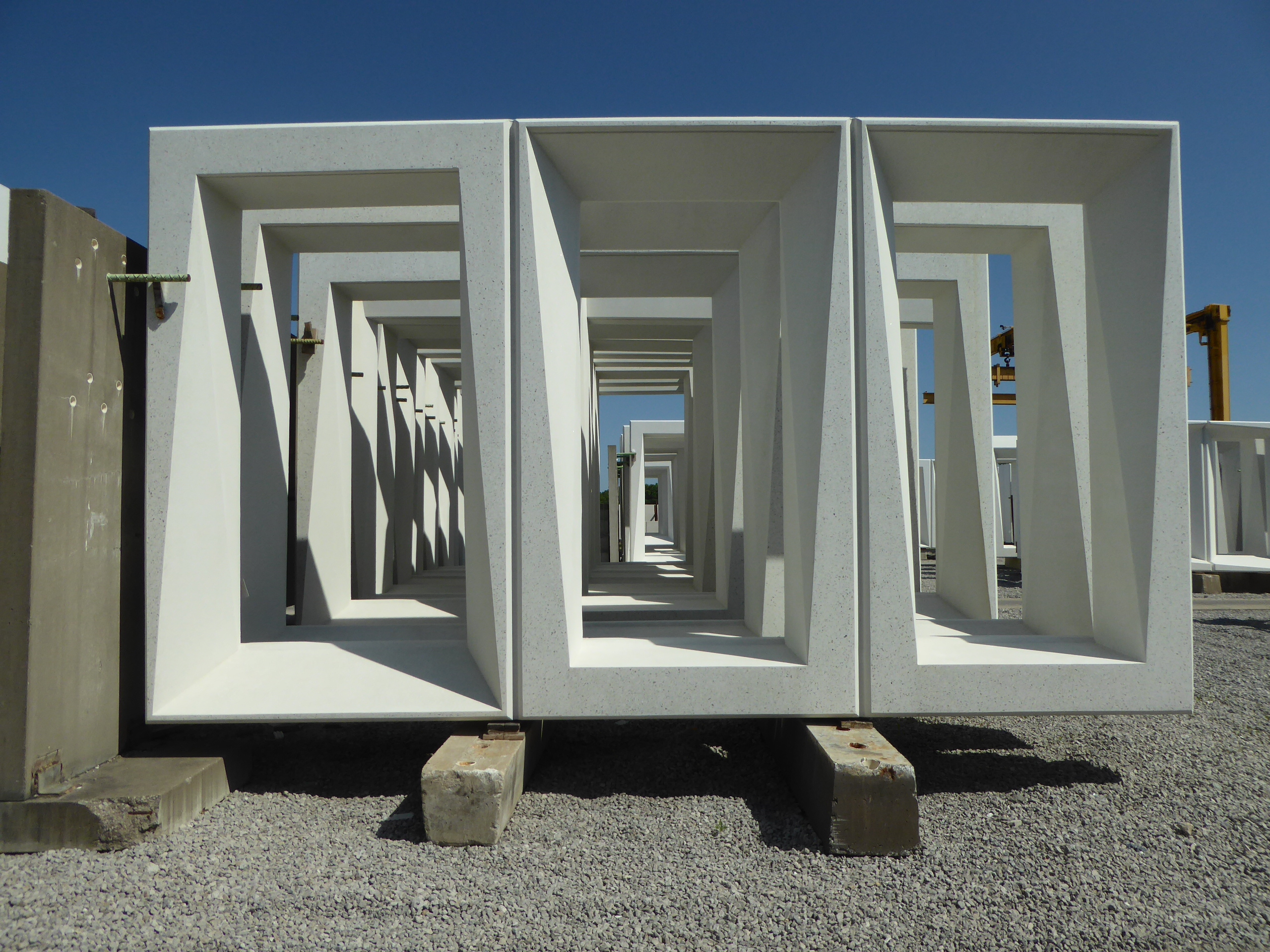
Además, para el uso de 150 vertidos o más, Gate calcula que se habrían necesitado hasta 10 moldes de madera para cumplir con el rendimiento de un molde AES. Además, dado que Gate tarda 40 horas-hombre en producir un molde de madera, sin los 37 moldes compuestos, la empresa no habría cumplido con los requisitos de cronograma del proyecto One South First.
Bader admite que un molde compuesto AES cuesta cuatro veces más que un molde de madera, pero es al menos 10 veces más duradero. “La forma en que se han construido las formas prefabricadas se ha mantenido relativamente sin cambios durante décadas”, afirma Bader. "De repente, un día, estamos haciendo formas 3D de 500 libras y todos se sorprendieron". Dicho esto, reconoce que la fabricación aditiva de tales moldes es más rentable en aplicaciones donde las formas de hormigón tienen geometría complicada o alta repetición - la misma forma muchas veces.
AES, informa Bader, ahora posee y opera cuatro máquinas BAAM y puede producir piezas de hasta 8 pies de altura. Se han construido piezas mucho más grandes uniendo varias piezas.
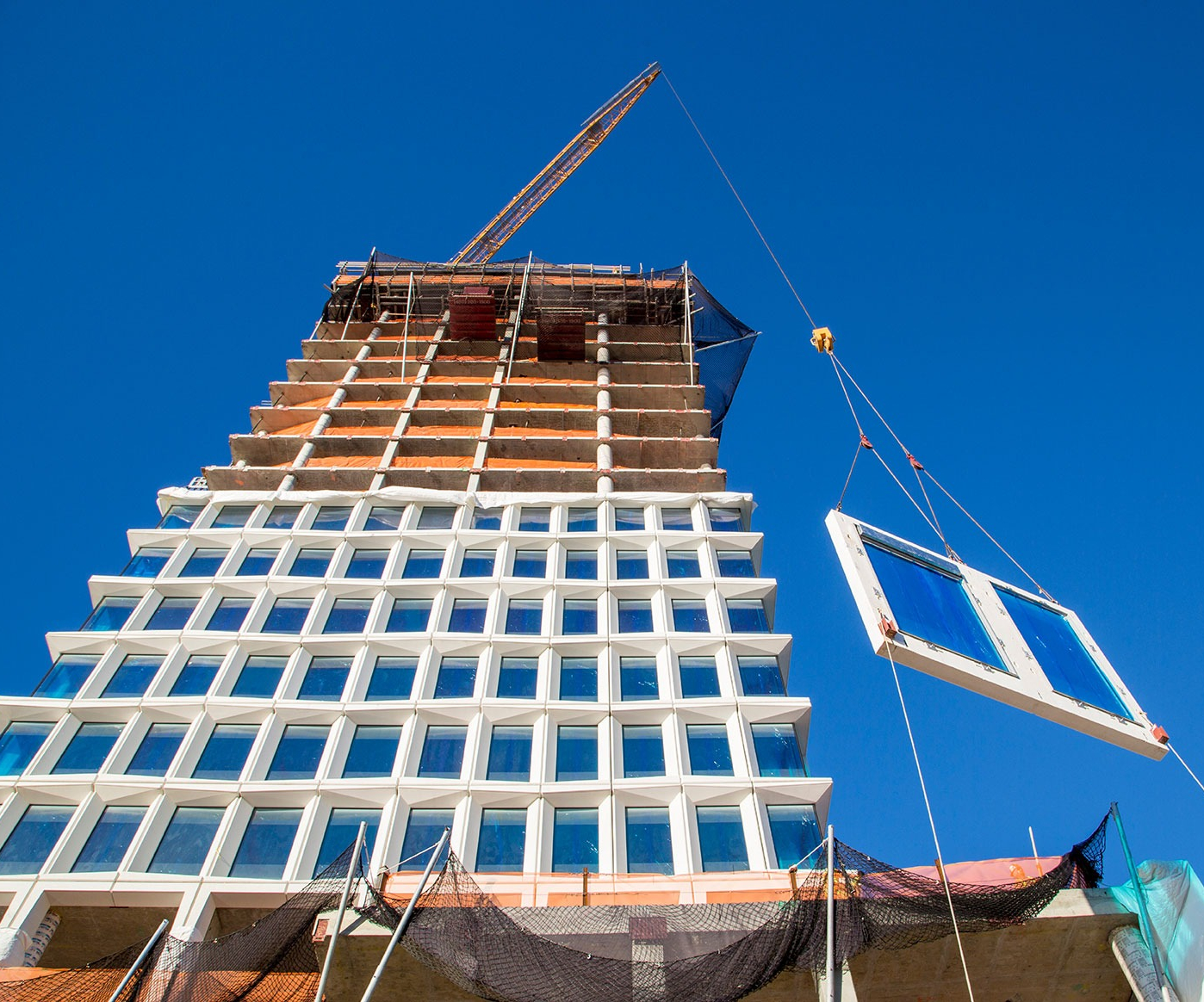
Resina
- Velocímetro
- Hormigón
- CompositesWorld SourceBook 2022
- Solución de problemas de termoformado de compuestos termoplásticos
- La evolución de los compuestos aditivos
- Compuestos termoplásticos:soporte de parachoques estructural
- Compuestos como refuerzos de carrocería automática
- ATL Composites contribuye al proyecto de remediación de pilares de hormigón
- RS Electric Boats selecciona a Norco para la fabricación de materiales compuestos
- Soldadura de compuestos termoplásticos
- Compuestos de alto rendimiento en Israel