Compuestos como refuerzos de carrocería automática
Aunque los compuestos han hecho algunos avances en las estructuras de carrocería en blanco (BIW) de automóviles, el uso de materiales en esta área del vehículo ha estado dominado durante mucho tiempo por el acero y, más recientemente, el aluminio. Debido a esto, los fabricantes de automóviles dependen en gran medida de la soldadura y los sujetadores mecánicos como pernos y tornillos para unir estructuras metálicas. Aunque generalmente son robustas, las uniones soldadas y los sujetadores pueden fallar. También hacen poco para mejorar la rigidez (sin aumentar indebidamente la masa) o para mitigar el ruido / vibración / aspereza (NVH) o la energía del choque que atraviesa un vehículo. Una forma de hacer frente a estos desafíos es reforzar las juntas y cavidades BIW con materiales compuestos junto con adhesivos estructurales.
Un ejemplo de una solución de este tipo es una clase de materiales / tecnologías denominados soluciones corporales compuestas (CBS). Estos incluyen inserciones estructurales 3D para reforzar estructuras primarias de vehículos que combinan elementos de BIW u otras subestructuras de vehículos, soportes termoplásticos (con refuerzo de fibra continua o discontinua) y adhesivos estructurales espumantes activados por calor. Los elementos CBS se instalan en la parte del taller de carrocería al principio de la construcción del vehículo, antes de la aplicación del recubrimiento electroforético para prevenir la oxidación (E-coat).
Los componentes CBS se producen normalmente en un proceso de sobremoldeo por inyección / 2K en el que el portador, que incorpora lengüetas de soldadura o encajes a presión para unir temporalmente el CBS a los componentes metálicos BIW, se sobremoldea selectivamente con adhesivo expandible y posiblemente un sellador adicional (en un proceso 3K) para mayor funcionalidad. El adhesivo sin curar seco al tacto (basado en la química epoxi personalizada) se puede moldear en formas complejas, pero permite la cobertura con capa electrónica de elementos metálicos manteniendo un espacio entre las superficies de metal y compuesto antes de la expansión inducida por el calor durante el poste. -Curado al horno E-coat. A medida que la espuma se expande, los espacios se sellan entre el portador y los componentes circundantes, bloqueándolos juntos en una "macroestructura" similar a una caja que mejora las propiedades mecánicas, particularmente bajo cargas altas y dinámicas.
Cuando se incorporan al principio del diseño del vehículo, los módulos CBS son opciones rentables y rentables para aumentar la rigidez de BIW local y global y mejorar la seguridad y la comodidad de los pasajeros con una masa menor. También permiten soluciones neutrales o de menor costo frente a soluciones totalmente metálicas más pesadas. Inicialmente utilizado en la industria automotriz, una creciente cartera de materiales de soporte y adhesivos ha ampliado los usos de CBS, de los cuales se destacan a continuación.
Diseñado para desafíos de rendimiento
La tecnología CBS fue desarrollada y comercializada por L&L Products Inc. (Romeo, Michigan, EE. UU.). Con una larga trayectoria como proveedor automotriz de selladores, contramedidas acústicas y refuerzos para mejorar el rendimiento de BIW, L&L desarrolló la tecnología para ayudar a los clientes a mejorar la seguridad de los pasajeros y cumplir con los requisitos de accidentes automovilísticos más estrictos a un costo y peso más bajos mientras mejora el procesamiento y el ensamblaje durante la construcción del vehículo. .
Entre 1995 y 2004, CORE Products, una empresa conjunta entre L&L y Gurit Essex (Wattwil, Suiza), fue responsable del desarrollo temprano de aplicaciones y la fabricación de CBS. L&L finalmente adquirió todos los activos de CORE, que ahora opera como L&L Products Europe.
L&L trabajó en estrecha colaboración con sus proveedores de materiales durante el desarrollo inicial y la expansión posterior de la tecnología CBS. Una de estas empresas, Lanxess AG (Colonia, Alemania), ha proporcionado desde hace mucho tiempo soporte de simulación y caracterización de materiales y materiales portadores compuestos a L&L en Europa.
CBS en aplicación
Además de los beneficios ya mencionados, la tecnología CBS proporciona una mejor transición de ruta de carga, gestión de carga multiaxial y absorción de energía; mayor estabilidad de la sección (resistencia al colapso o intrusión); NVH más bajo; y dinámica de conducción mejorada y rendimiento en choques con cargas más altas. Además, ofrece un tiempo de implementación más rápido durante el diseño / rediseño del vehículo y no requiere cambios en la secuencia de ensamblaje en el taller de carrocería. Debido a que la tecnología CBS facilita el control de la transferencia de energía a través de las estructuras de la carrocería al tiempo que minimiza la deformación y / o la intrusión, es ideal para aplicaciones diseñadas para resistir choques frontales, laterales o traseros o aplastamientos del techo para proteger mejor a los ocupantes, los compartimentos de pasajeros y las baterías. También es útil para estructuras que deben aprobar protocolos desafiantes como el Instituto de Seguros para la Seguridad en las Carreteras (IIHS, Arlington, Va., EE. UU.), Pruebas de choque de superposición pequeña.
Lo que hizo que CBS fuera digno de mención fue que fue uno de los primeros enfoques modulares de materiales mixtos, fue fácil de instalar, ofreció estabilidad térmica y química para E-coat y no cambió la secuencia de ensamblaje del vehículo, pero mejoró el rendimiento a menor masa y neutral / menor costo:el santo grial de la industria automotriz.
“La versatilidad de diseño de la tecnología CBS ayuda a simplificar el montaje en áreas con condiciones complejas o de difícil acceso”, explica Núria Ignés, gerente de ingeniería de productos estructurales, L&L Products Reinforce en L&L Products EMEA (Altorf, Francia). “Por ejemplo, el uso de la tecnología CBS en puertas y otros cierres no solo reduce el peso y aumenta la rigidez, sino que puede simplificar la fabricación de la puerta si se integra al principio del proceso de diseño. Gracias a las herramientas CAE y décadas de experiencia, además de la combinación de portador y espuma, que proporciona un acoplamiento robusto al BIW una vez curado, podemos usar la cantidad correcta del material correcto en el lugar correcto para equilibrar la rigidez con la masa y el costo o absorción de energía con acústica y coste ”.
“Un aspecto realmente interesante de la tecnología CBS es su naturaleza 'bio-mimética'”, agrega Peter Cate, gerente de marketing estratégico global de L&L. “Así como los puntales de refuerzo celular en el centro de los huesos son el método más eficiente de la naturaleza para agregar rigidez y manejar cargas en estructuras huecas, una vez que el adhesivo se expande, las unidades CBS refuerzan las cavidades de la carrocería del vehículo de la misma manera, ayudando a los ingenieros a optimizar las estructuras rigidez en la masa más baja ".
"Al aumentar la rigidez local y general y distribuir las cargas de manera más eficaz a través de una estructura, los refuerzos CBS son soluciones a medida para abordar los problemas de rigidez localizada y fatiga del metal sin agregar masa", continúa Pal Swaminathan, gerente de desarrollo comercial, Tepex Automotive, Lanxess Corp (Pittsburgh, Pensilvania, EE. UU.). “Las mejoras de NVH también son comunes cuando la tecnología CBS se integra en las estructuras corporales. Una vez más, un análisis de ingeniería cuidadoso permite el desarrollo y las soluciones de optimización de la ubicación para equilibrar las características de conducción y manejo ”.
Aplicaciones tempranas
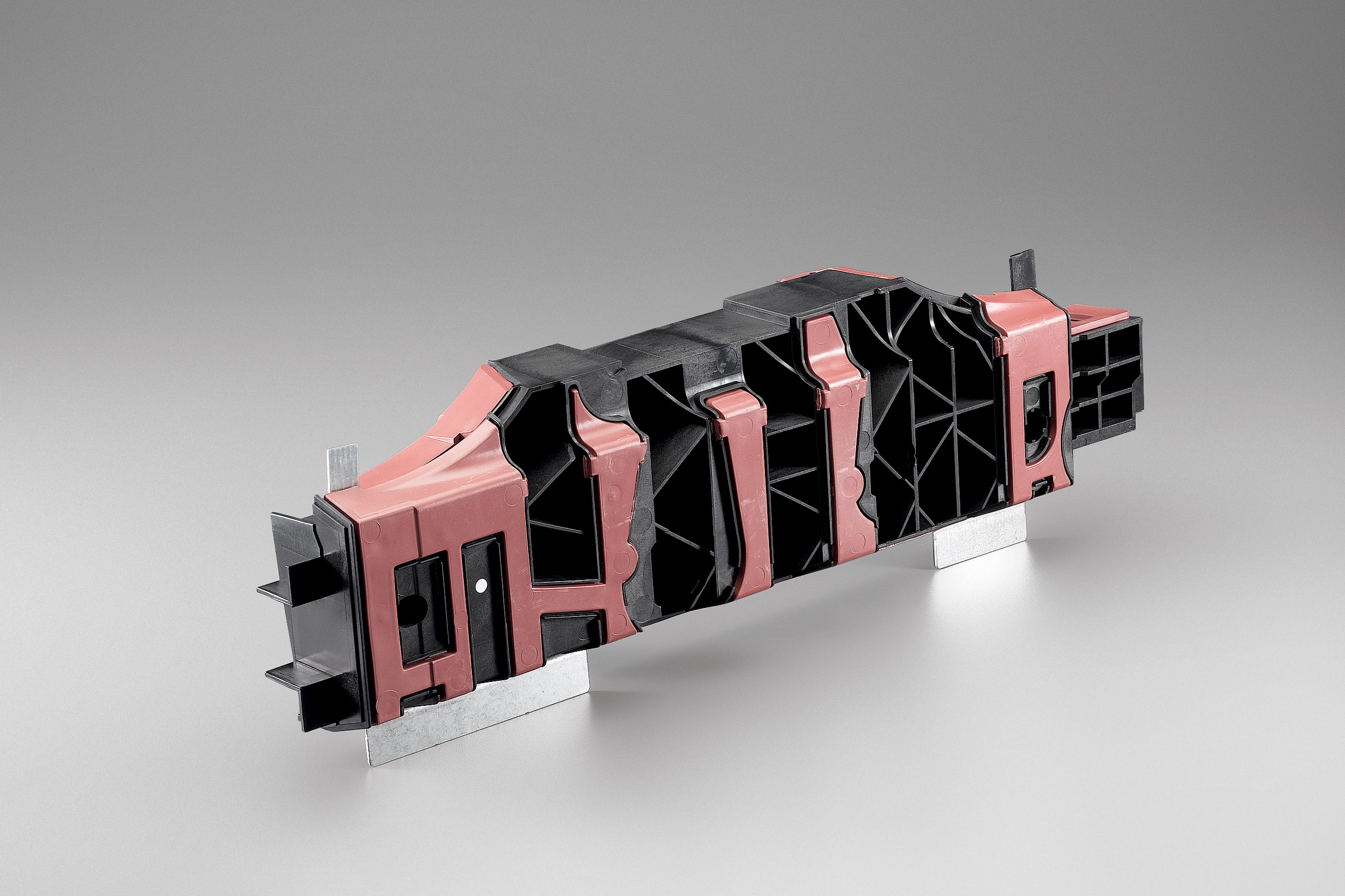
La primera aplicación automotriz comercial de L&L de CBS fue en 1998; en 2002, la tecnología estaba ganando aceptación en el mercado. Un buen ejemplo temprano se implementó en 2006 Citroën C4 Picasso sedán del Grupo PSA (París, Francia, ahora Stellantis N.V., Ámsterdam, Países Bajos). Nueve componentes CBS, en las secciones inferiores de los pilares A, las secciones inferior y superior de los pilares B y en el travesaño sobre el eje trasero, redujeron la masa del vehículo en 12 kilogramos en comparación con las opciones metálicas. Algunas inserciones de CBS aumentaron selectivamente la capacidad de carga y minimizaron la intrusión en el habitáculo durante el impacto, mejorando la seguridad de los ocupantes. Otros mejoraron el rendimiento NVH de BIW. Todos los vehículos se moldearon por inyección a partir del 35% en peso de vidrio corto / poliamida 6 (PA6). Se utilizaron unidades CBS similares en Ford Transit 2012 camionetas de Ford Motor Co. (Dearborn, Michigan, EE. UU.).
Nuevo soporte, opciones de espuma
A lo largo de los años, L&L y sus proveedores han ampliado la tecnología CBS con nuevas formulaciones de espumas, una gama más amplia de resinas portadoras y refuerzos y aplicando el concepto a diferentes estructuras.
Por ejemplo, la mayoría de los portadores CBS para aplicaciones de choque están diseñados con PA6 reforzado con vidrio al 30% en peso, estabilizado al calor, porque se necesita un equilibrio entre rigidez y ductilidad dentro de una forma 3D compleja. Dos de estos soportes se utilizaron en los largueros delanteros para una plataforma de vehículos eléctricos (EV) importante donde, según se informa, no solo simplificaron el ensamblaje (reduciendo el recuento de piezas) sino que también redujeron la intrusión del choque en el cortafuegos en un 20%.
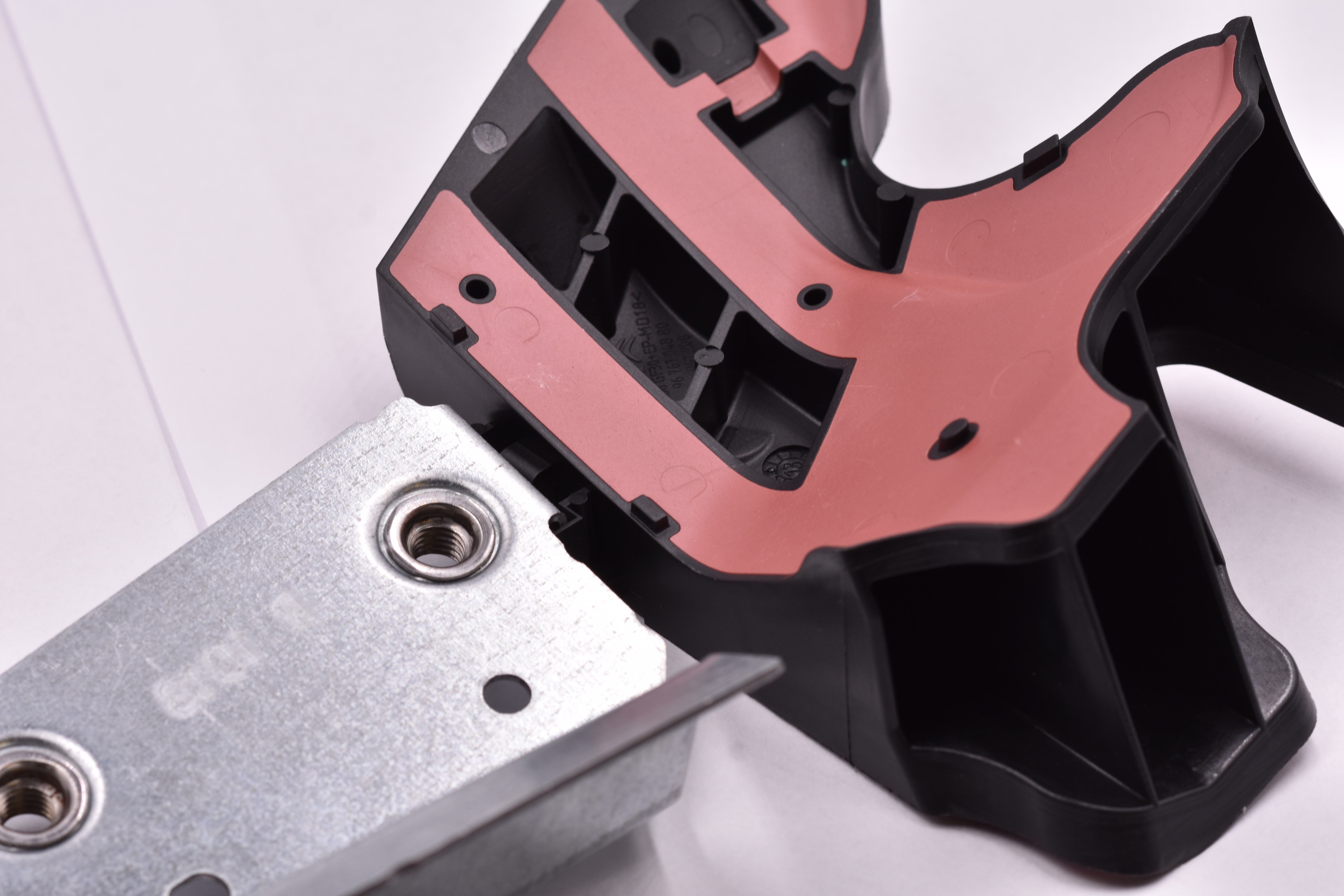
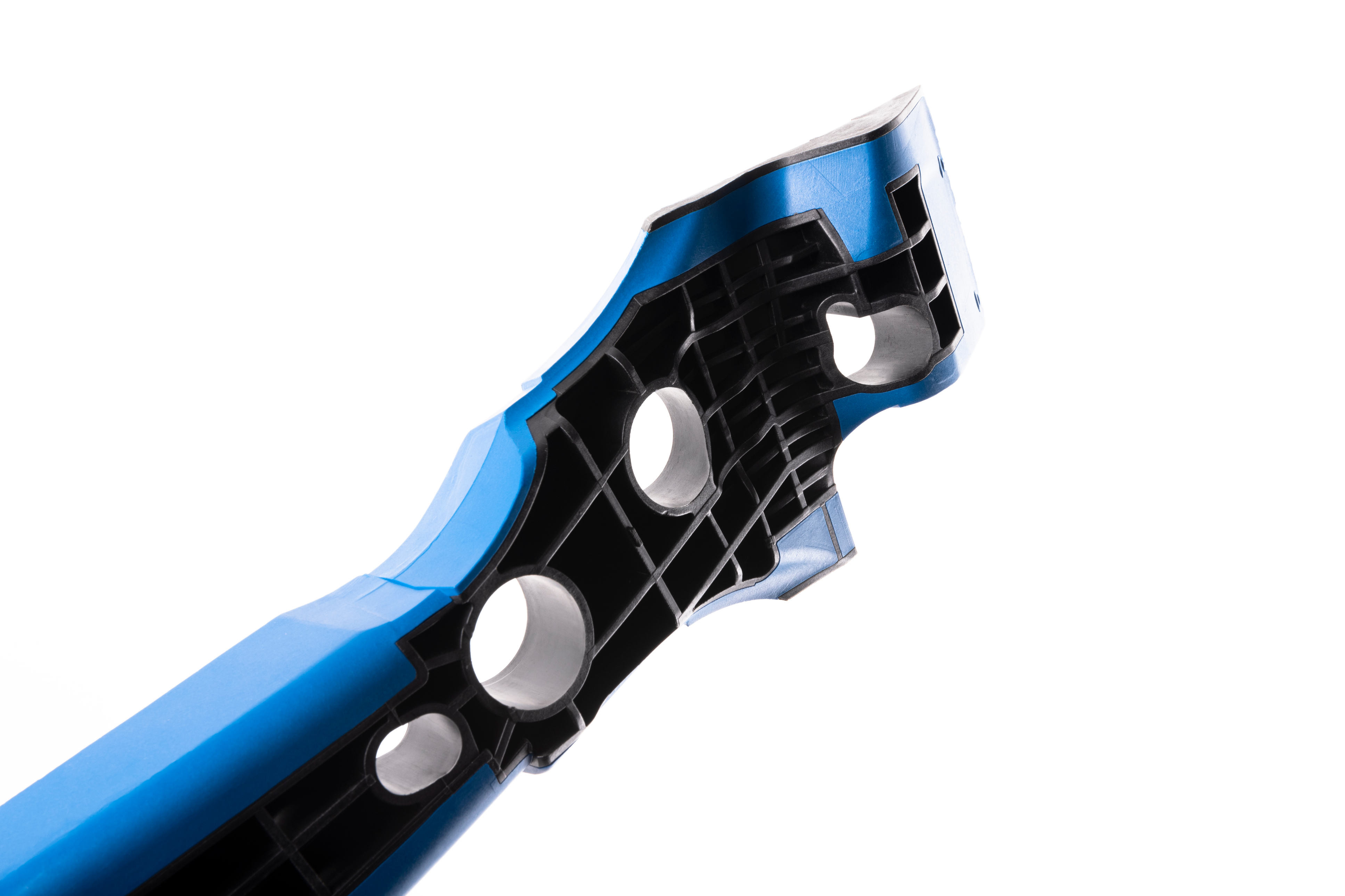
Para requisitos de mayor impacto, ahora hay vehículos híbridos disponibles, como los pilares A de refuerzo en el Porsche 911 Carrera Cabriolet 2019 con carrocería en gran parte de aluminio. coche deportivo de Porsche AG (Stuttgart, Alemania). Al ser un convertible, endurecer el marco sin techo era fundamental para proteger a los pasajeros en caso de vuelcos. Para mantener los vehículos ligeros y ágiles, Porsche reemplazó las pesadas barras antivuelco de acero tubular con inserciones de CBS en los pilares A. Las carcasas de los pilares se fabricaron en acero de alta resistencia, que se estabilizaron y reforzaron mediante inserciones de CBS en el interior de cada pilar. El cuerpo portador principal era una hoja orgánica moldeada por compresión (47% en volumen de tejido de vidrio de tejido de sarga / PA6), que se precalentaba, se preformaba y luego se sobremoldeaba por inyección con nervaduras (30% en peso de vidrio corto / PA6 / 6). El lado de la lámina orgánica lleva el adhesivo expandible L-5235 de L&L. Esta tecnología híbrida no solo cumplió con todos los objetivos de rendimiento y peso (lo que supuestamente no cumplió la opción de acero tubular), sino que redujo la masa del vehículo en 5,4 kilogramos, facilitando el montaje y reduciendo el centro de gravedad del vehículo, lo que mejoró la dinámica de conducción.
Para aplicaciones donde un proceso de horno no está disponible para activar el adhesivo expansivo, o donde se necesita soporte adicional en el taller de pintura, L&L dice que está trabajando en otras soluciones de curado ambiental.
También se han desarrollado varias tecnologías relacionadas basadas en CBS. El sistema compuesto continuo (CCS) de L&L, que pronto tendrá su primera aplicación comercial, combina soportes pultruidos reforzados con fibra de vidrio o carbono, por ejemplo, poliuretano (PUR) con o sin telas y mechas, con selladores o adhesivos estructurales formulados a medida. Los elementos CCS, que también pueden incorporar piezas CBS y componentes metálicos, mejoran la rigidez y la resistencia de las estructuras de sección transversal constante a una masa menor (normalmente un 75% menos que el acero y un 30% menos que el aluminio). Son resistentes a la corrosión, no conductores / eléctricamente aislantes, ofrecen un bajo coeficiente de expansión térmica lineal (CLTE) y proporcionan una gestión de energía altamente predecible, lo que los hace ideales para reforzar miembros estructurales en vehículos unibody o secciones de bastidor para vehículos de carrocería sobre bastidor. más marcos de batería para vehículos eléctricos.
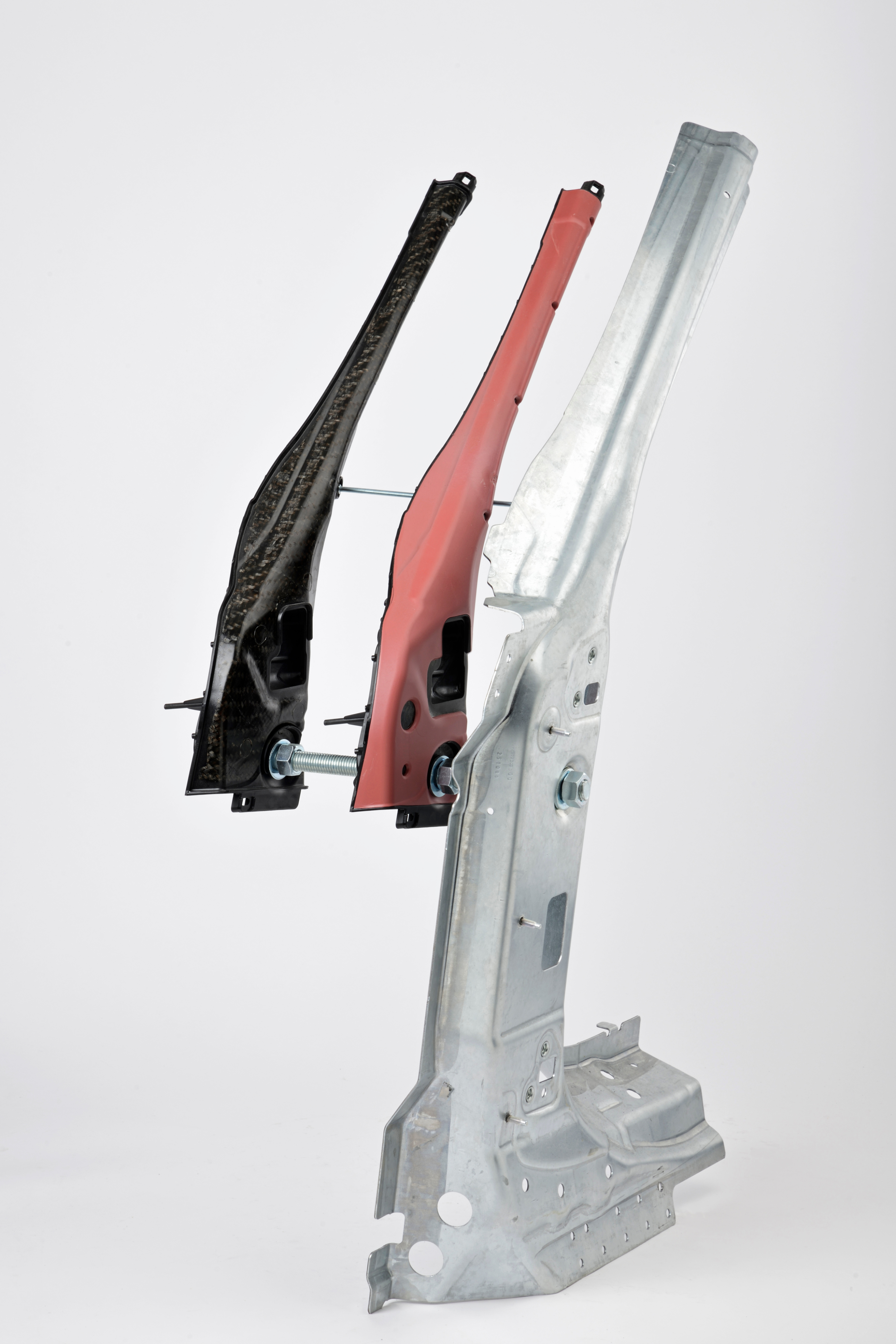
Los refuerzos de paneles compuestos comprenden adhesivos estructurales expansibles autoadhesivos coextruidos con refuerzo de fibra de vidrio que se aplican a las superficies de los paneles metálicos formados en el taller de carrocería. El sistema no solo mejora la rigidez (reduciendo la ondulación y el pandeo) de los paneles grandes / relativamente sin apoyo, sino que también mejora el NVH debido al mayor momento de inercia. Además, ofrece oportunidades para reducir el calibre de los paneles para reducir la masa y el costo. Las aplicaciones comerciales incluyen puertas de automóviles, paneles de techo y piso, capós, guardabarros, compuertas elevadoras y compuertas traseras; las aplicaciones potenciales incluyen carcasas de baterías.
Los refuerzos del panel de nido de abeja cuentan con epoxi liviano, en forma de pasta para aplicación manual o líquido de baja viscosidad para bombeo automático, que, una vez curado, se puede mecanizar o lijar. Estos están diseñados para estabilizar núcleos de nido de abeja, predominantemente en ubicaciones estratégicas en el interior de aviones, por ejemplo, sin agregar exceso de masa. Otros usos incluyen la mejora de bordes (sellado / refuerzo de bordes de paneles compuestos), unión de insertos y refuerzo local donde se instalan bisagras / insertos de metal en paneles compuestos.
Qué nos depara el futuro
Desde su primera patente en 1999, L&L ha presentado numerosos inventos para la tecnología CBS. Dada la amplia gama de opciones de soportes y adhesivos ahora disponibles dentro de esta familia de productos, no es sorprendente que las aplicaciones se hayan expandido más allá de la automoción a camiones y aeroespacial. ¿Qué sigue?
“A lo largo de los años, los productos CBS han evolucionado para satisfacer nuevos requisitos de aplicación que combinan funciones”, añade Ignés. “Por ejemplo, lo que comenzó como un simple refuerzo estructural ha evolucionado no solo para endurecer, sino también para mejorar las funciones acústicas o para aumentar la absorción de energía. Dado el conjunto de propiedades altamente deseables que ofrece la tecnología CBS, esperamos no solo ver crecer el uso automotriz, sino también crecer en otras industrias ”.
Resina
- CompositesWorld SourceBook 2022
- Solución de problemas de termoformado de compuestos termoplásticos
- La evolución de los compuestos aditivos
- Compuestos termoplásticos:soporte de parachoques estructural
- Compuestos como refuerzos de carrocería automática
- Personas en materiales compuestos - Enero de 2019
- CAMX 2018:Presentaciones previas
- Soldadura de compuestos termoplásticos
- Vista previa de SPE ACCE 2018
- Compuestos de alto rendimiento en Israel
- Compuestos de impresión 3D con fibra continua