Compuestos termoplásticos:preparados para dar un paso adelante
Los compuestos termoplásticos (TPC) no son nuevos en el sector aeroespacial, pero en los últimos años el uso de termoplásticos en aviones comerciales ha alcanzado un punto de inflexión. Si bien los TPC se han utilizado durante algún tiempo para piezas más pequeñas, como clips y soportes, o componentes interiores más pequeños, los termoplásticos se han abierto camino en estructuras de aviones más grandes de forma incremental y ahora parecían estar preparados para desempeñar un papel más importante en el futuro de los aviones comerciales.
En marzo de 2018, Toray Industries Inc. (Tokio, Japón), el mayor fabricante de fibra de carbono del mundo, adquirió TenCate Advanced Composites (Morgan Hill, California, EE. UU. Y Nijverdal, Países Bajos) por 930 millones de euros (desde entonces, TenCate cambió su nombre a Toray Advanced Composites). La medida parecía ser un esfuerzo por fortalecer las capacidades de termoplásticos de Toray en preparación para la próxima ola de desarrollo de aviones comerciales. Poco después de ese anuncio, Hexcel (Stamford, Connecticut, EE. UU.) Y Arkema Inc. (King of Prussia, Pensilvania, EE. UU.) Anunciaron una alianza estratégica para desarrollar soluciones de compuestos termoplásticos para la industria aeroespacial, combinando la habilidad de Hexcel en la fabricación de fibra de carbono con la polietercetonacetona de Arkema. (PEKK) experiencia en resinas. Y en el transcurso del año, varias otras piezas del rompecabezas de los termoplásticos parecieron encajar en su lugar.
En abril de 2018, Premium Aerotec GmbH (Augsburg, Alemania) presentó un demostrador para un mamparo de presión A320 de Airbus (Toulouse, Francia) que había desarrollado y fabricado utilizando fibra de carbono en una matriz termoplástica. El demostrador, que consta de ocho segmentos soldados, ilustra cómo la soldabilidad de los termoplásticos tiene el potencial de permitir componentes de aviones más grandes. (Obtenga más información sobre el demostrador de mamparo de presión A320 de Premium Aerotec).
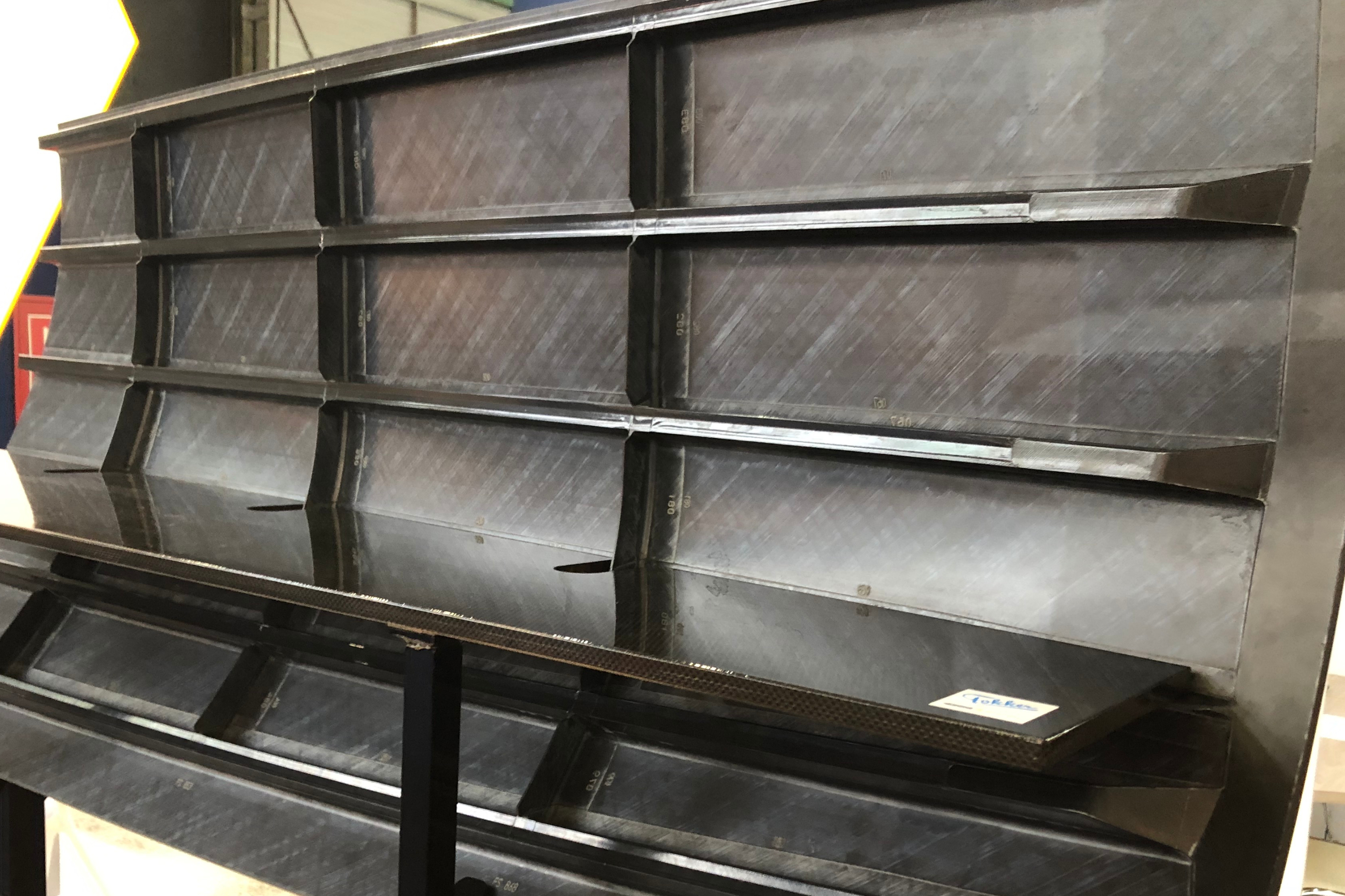
En agosto de 2018, Solvay (Alpharetta, Georgia, EE. UU.), Premium Aerotec y Faurecia Clean Mobility (Columbus, Ohio, EE. UU.) Lanzaron IRG CosiMo (Industry Research Group:Composites for Sustainable Mobility), un consorcio centrado en el desarrollo de materiales y tecnologías de proceso destinadas a permitir la producción de grandes volúmenes de compuestos termoplásticos para los mercados aeroespacial y automotriz. El consorcio combina empresas a lo largo de toda la cadena de proceso de compuestos termoplásticos, desde materiales hasta maquinaria y aplicaciones en la industria automotriz y aeroespacial. (Obtenga más información sobre el consorcio IRG CosiMo aquí).
Solvay se ha asociado con GKN Fokker (Hoogeveen, Países Bajos) para promover la tecnología y una mayor adopción de TPC para grandes estructuras aeroespaciales desde junio de 2017. La compañía lanzó la producción de polímero PEKK en septiembre de 2017 y luego duplicó su capacidad de cinta termoplástica UD calificada en 2018. Anteriormente En 2019, Solvay encargó un laboratorio de investigación de TPC dedicado en Alpharetta, Georgia, EE. UU., destinado al desarrollo de materiales de próxima generación. Solvay planea comenzar la calificación de una nueva línea de cintas UD a fines de 2019.
Teijin Ltd. (Tokio, Japón) anunció en enero de 2019 que su cinta de fibra de carbono TENAX y cinta preimpregnada unidireccional termoplástica / fibra de carbono (TENAX TPUD) ha sido calificada por Boeing (Chicago, Illinois, EE. UU.) Para su uso como intermedio avanzado. material compuesto para piezas estructurales primarias (lea la noticia completa aquí).
A medida que avanzan estas y otras tecnologías y materiales similares, gradualmente se enfoca una imagen de cómo podría comenzar a verse la industria aeroespacial en los próximos años y décadas. El papel de los TPC se está convirtiendo en una parte cada vez más importante de ese panorama.
Los fabricantes están interesados en aprovechar los beneficios de fabricación y los tiempos de procesamiento rápidos de los termoplásticos, y en usar TPC para comenzar a hacer estructuras más grandes, como paneles de fuselaje y nervaduras. Además, los termoplásticos cuentan con una alta tenacidad a la fractura; buenas propiedades mecánicas; reciclabilidad; llama baja, humo y toxicidad (FST), y se puede almacenar a temperatura ambiente. Y a medida que los fabricantes de equipos originales y los proveedores de nivel aeroespacial se familiarizan con los termoplásticos, se utilizan para piezas más complejas, conjuntos soldados y estructuras primarias.
Según Steve Mead, director gerente de Toray Advanced Composites (antes TenCate), “[los grandes fabricantes de aviones] realmente están buscando una solución de material que tenga las capacidades de velocidad del aluminio y las capacidades de peso del material a base de fibra de carbono:tipo de puente termoplástico esa brecha ".
Procesabilidad de los TPC
Una gran parte de por qué los TPC están encontrando su lugar en los programas de aeronaves es su procesabilidad. Debido a que los termoplásticos ya están completamente polimerizados, tienen tasas de producción más rápidas que los termoestables, que deben curarse.
"Cuando observa la cantidad de tiempo que lleva fabricar una pieza termoendurecible hoy y lo compara con la cantidad de tiempo que lleva fabricar una pieza de compuesto termoplástico, [termoplástico] es unas 10 veces más rápido", dice Mike Favaloro, presidente y Director ejecutivo de CompositeTechs LLC (Amesbury, Mass., EE. UU.), Una consultora de la industria de materiales compuestos.
Una gran ventaja de la colocación automatizada de fibras termoplásticas (AFP) en comparación con la AFP termoendurecible, particularmente dada la falta de ciclo de curado, son las tasas de producción más altas debido a un tiempo de procesamiento más rápido. Se pueden encontrar ahorros de costos en la laminación in situ y la consolidación posterior fuera del autoclave (OOA). Además, sacar el autoclave de la ecuación permite el desarrollo de estructuras más grandes.
David Leach, director de desarrollo comercial de ATC Manufacturing (Post Falls, Idaho, EE. UU.), Reconoce que el costo unitario de los termoplásticos excede el costo de los termoestables, pero argumenta que los precios de los materiales de TPC bajarán. Además, dice, las eficiencias de procesamiento ofrecen una oportunidad para reducir costos en la actualidad. El consenso general en la industria de los compuestos es que los procesos termoplásticos OOA, en este momento, ofrecen ahorros de costos de más del 30 por ciento en comparación con los termoestables.
“Los termoplásticos se están abriendo camino en los programas incluso después de que los aviones hayan entrado en producción”, señala Leach. "Es un testimonio de los beneficios económicos de los termoplásticos".
El potencial de los polímeros matriciales de alto rendimiento se extiende más allá de lo que está disponible actualmente en el mercado. Doug Brademeyer, director de Ultra-Polymers Materials en Solvay, dice que la compañía está trabajando tanto internamente como con socios para desarrollar polímeros hechos a la medida para los diferentes procesos de fabricación.
"Estamos entusiasmados con estas soluciones PAEK personalizadas y podemos llevarlas rápidamente a la comercialización en nuestros activos a escala mundial, según las necesidades del cliente", dice Brademeyer.
PAEK de bajo derretimiento
Dado que los fabricantes de equipos originales y los proveedores de aeronaves se esfuerzan por lograr tasas de producción más altas y tiempos de ciclo más cortos, la procesabilidad es clave. La polieteretercetona (PEEK) ha sido durante mucho tiempo el polímero termoplástico preferido, ya que tiene la base de datos más grande y es el más calificado. Pero según Favaloro, la poliariletercetona de bajo punto de fusión (LM PAEK) ofrece algunas ventajas, especialmente para los métodos de procesamiento automatizados como ATL.
"PEEK se puede procesar mediante estampado y moldeo continuo, pero LM PAEK procesa a una temperatura más baja, tiene una viscosidad de trabajo más baja que permite un mejor procesamiento automatizado y tiene un menor grado de cristalinidad que reduce las tensiones residuales de moldeo", dice. “El objetivo final es usar una máquina ATL para colocar [la cinta] y terminar con ella; necesita el grado correcto de cristalinidad, una buena ventana y buenas velocidades de colocación”.
LM PAEK tiene una amplia ventana de proceso de 350-385ºC. Como referencia, las temperaturas de procesamiento de sulfuro de polifenileno (PPS) oscilan entre 330 y 350 ° C, mientras que las temperaturas de procesamiento de polietercetonacetona (PEKK) y PEEK son de 380 ° C y 400 ° C, respectivamente.
"El material ha ganado mucha tracción debido a su procesabilidad", dice Scott Unger, director técnico de Toray Advanced Composites. Toray Advanced Composites colaboró con Victrex (Lancashire, Reino Unido) para producir Cetex TC1225, una cinta unidireccional que utiliza LM PAEK.
“La intención con el desarrollo de TC1225 era crear un producto que se procesara fácilmente a temperaturas cercanas a las utilizadas para PPS, tuviera una posición de costo favorable para el usuario final y tuviera las propiedades mecánicas y de resistencia a fluidos de PEEK”, dice Unger. "Con TC1225 LM PAEK, siento que logramos todos esos objetivos".
Cetex TC1225 se encuentra actualmente en proceso de calificación por el Centro Nacional de Rendimiento Avanzado de Materiales (NCAMP, Wichita, Kansas, EE. UU.). Además, Toray dice que hay dos importantes calificaciones basadas en la estructura del avión en los trabajos para el material, así como un par de programas de calificaciones basados en mercados emergentes como taxis aéreos y movilidad aérea urbana.
Según se informa, las cintas que utilizan LM PAEK están produciendo velocidades de colocación mejoradas. Tim Herr, director de Aerospace SBU en Victrex, dice:"Las tasas de depósito que podemos lograr tanto para AFP in situ como para AFP consolidadas fuera de autoclave no tienen precedentes". Indica que se pueden alcanzar 60 metros por minuto en paneles consolidados al horno; Según se informa, es posible alcanzar 20 metros por minuto con la consolidación in situ.
En términos de calidad, Unger afirma que PAEK de bajo punto de fusión ofrece la capacidad de obtener la misma calidad de laminado utilizando la colocación de fibra in situ que con un laminado de fibra colocada que se ha sometido a una consolidación en horno posterior a la colocación de fibra.
Unión de materiales compuestos
La soldabilidad de los TPC es una gran ventaja del material para su uso en el desarrollo de aviones. La unión / soldadura por fusión ofrece una alternativa a la fijación mecánica y al uso de adhesivos, ambos métodos empleados para unir piezas de compuestos termoendurecibles.
Stephen Heinz, director de desarrollo de productos de Solvay, dice:“La unión y soldadura juega un papel importante en el futuro del ensamblaje y tiene el potencial de reducir costos y mejorar la confiabilidad de las aeroestructuras. Empresas como GKN Fokker están liderando la demostración de la soldadura ”.
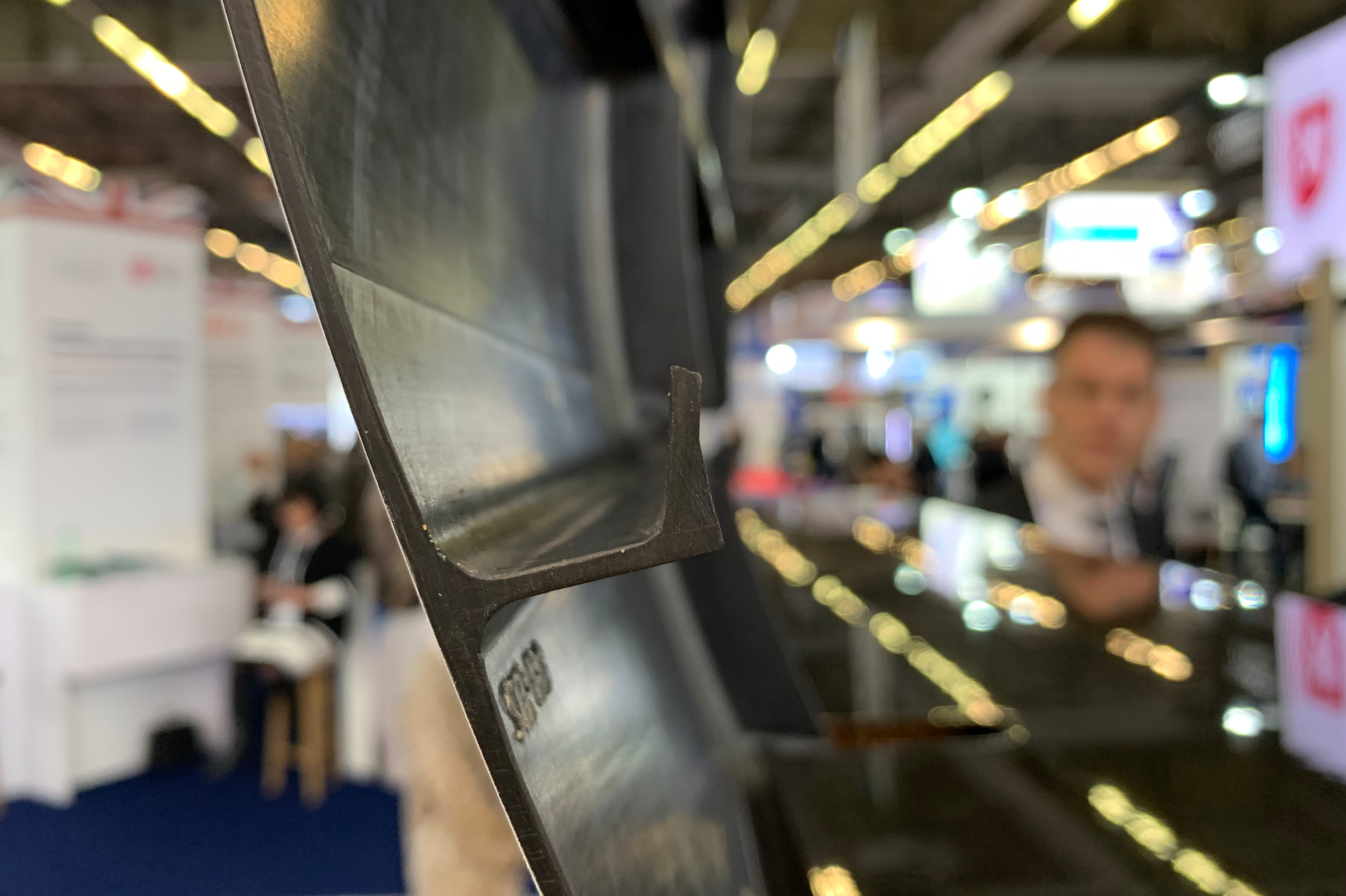
GKN Fokker (Hoogeveen, Países Bajos) ha estado trabajando para desarrollar TPCwelding durante algún tiempo, habiendo comenzado a experimentar con la soldadura por resistencia de termoplásticos en la década de 1990. La empresa ha estado utilizando procesos de soldadura termoplástica para unir nervaduras y revestimientos internos de vanguardia. En JEC World 2019, la compañía exhibió un panel de fuselaje compuesto termoplástico de área reglada fabricado con cinta APC (PEKK-FC) UD de Solvay. El panel es el resultado de un proyecto de I + D conjunto entre GKN Fokker y Gulfstream Aerospace (Savannah, Georgia, EE. UU.). Según se informa, la pieza es el panel compuesto de menor costo, debido a la rigidez de la ortogrid simple "unida a tope" y los marcos completamente soldados.
“Con los termoplásticos, una ortogrid se puede simplificar enormemente 'uniendo a tope' la rejilla a la piel”, explica Arnt Offringa, director de Desarrollo de Tecnología de Compuestos Termoplásticos de GKN Fokker. “La rejilla ahora se compone de preformas simples y planas que se consolidan conjuntamente con el laminado de la piel para formar una cáscara integralmente rígida de bajo costo. Los marcos están soldados a la rejilla. Estas soldaduras se cargan a cortante, por lo que es factible omitir todos los pernos ”.
Si bien las estructuras termoplásticas soldadas se han utilizado en las cabinas de aire durante algún tiempo, la tecnología ahora parece estar bien preparada para su uso en estructuras primarias. Mike Favaloro cree que los fabricantes aeroespaciales y los OEM están ganando confianza con los TPC, particularmente con el control de procesos. "En un horizonte de 10 años, comenzaremos a ver que se adopta mucho más", dice.
Lea más sobre la tecnología de soldadura en el artículo de Ginger Gardiner "Soldadura de compuestos termoplásticos".
Sin herramientas
Otra innovación en el horizonte que podría permitir la aceleración del uso de termoplásticos es la fabricación de compuestos sin herramientas. El concepto, como su nombre lo indica, evita la necesidad de moldes y herramientas tradicionales, reemplazándolos por robótica.
El fabricante aeroespacial General Atomics Aeronautical Systems Inc. (GA-ASI, San Diego, California, EE. UU.) Está desarrollando un proceso de este tipo para la fabricación de estructuras compuestas termoplásticas. Composite Automation LLC (Cape Coral, Florida, EE. UU.), Utilizando equipos Mikrosam (Prilep, Macedonia), trabajó con GA-ASI para desarrollar la automatización. El proceso utiliza dos robots de 6 ejes que trabajan juntos para colocar cinta termoplástica. Un robot consta de un sistema de colocación de cinta unidireccional estándar que proporciona calentamiento por láser para realizar la consolidación in situ del material termoplástico. El segundo robot proporciona apoyo, trabajando frente a la capa de cinta automatizada (ATL) para proporcionar una superficie de herramienta móvil contra la cual el ATL coloca la cinta. (Para obtener más información, consulte “Proceso de desarrollo de compuestos termoplásticos sin herramientas de General Atomics Aeronautical”).
Reciclabilidad
Otro beneficio de los TPC es la reciclabilidad. Debido a que los polímeros termoplásticos se pueden volver a fundir y remodelar, varias empresas están considerando los TPC como una forma de reutilizar los materiales.
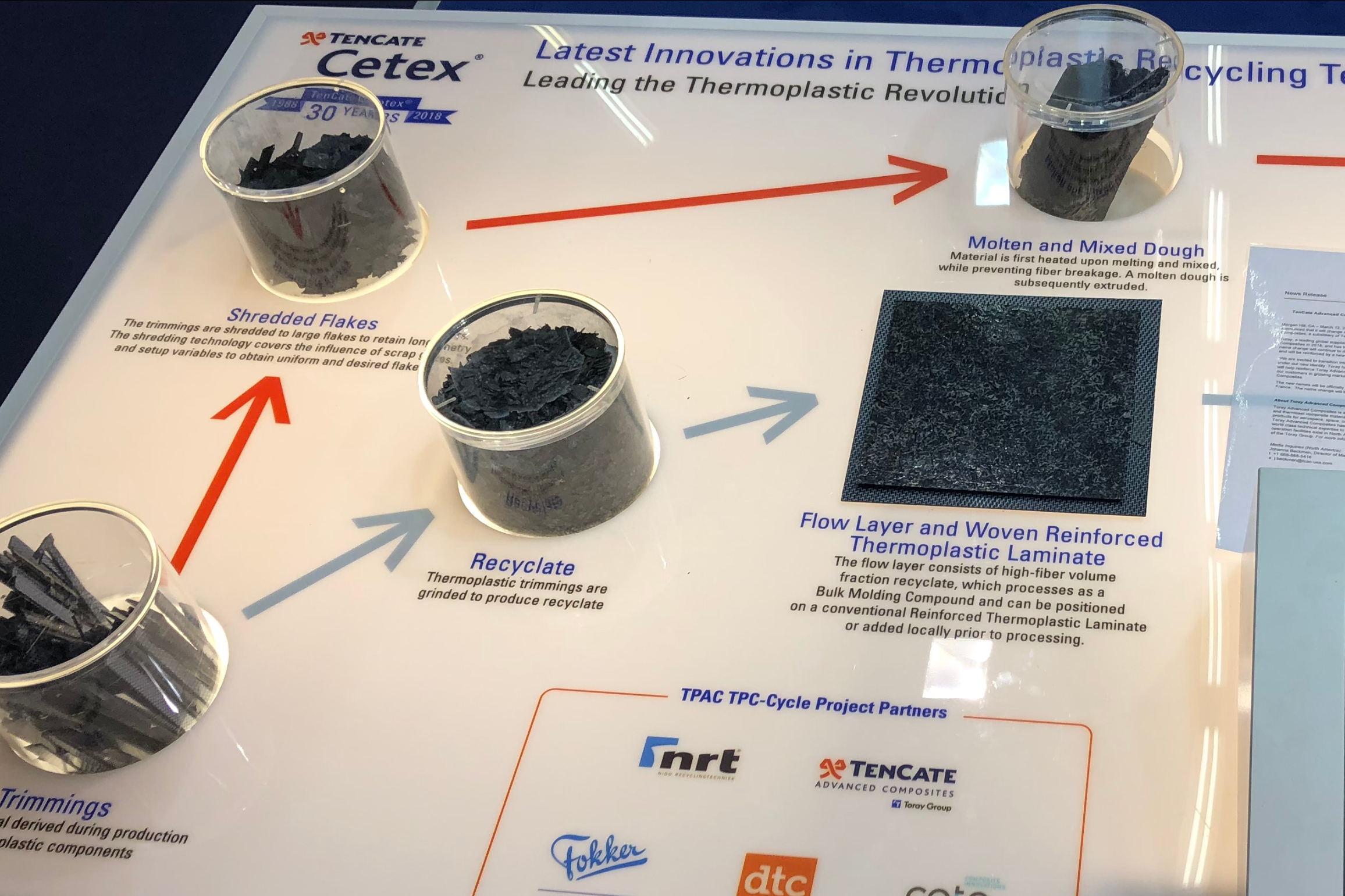
Una de estas iniciativas de reciclaje, operada por el Centro de Aplicación de Compuestos Termoplásticos (TPAC, Enschede, Países Bajos) y el Centro de Investigación de Compuestos Termoplásticos (TPRC, Enschede, Países Bajos), se centra en la reutilización de la chatarra de producción del procesamiento de TPC, desde la recolección hasta la trituración y reprocesamiento hasta la aplicación. El proyecto TPC-Cycle está trabajando para desarrollar una ruta de reciclaje asequible y respetuosa con el medio ambiente para los mercados de alto volumen y alta gama, todo mientras se produce un material que conserva la mayor cantidad posible de propiedades mecánicas de los materiales termoplásticos originales. El proyecto cuenta con tiempos de ciclo cortos, fabricación de formas de red y se dice que permite la producción de formas complejas.
La colaboración incluye varios socios industriales en la cadena de valor, desde materiales, fabricación, diseño y aplicación, incluidos GKN Fokker, Toray Advanced Composites, Cato Composite Innovations (Rheden, Países Bajos), Dutch Thermoplastic Components (Almere, Países Bajos) y Nido RecyclingTechniek (Nijverdal). , Países Bajos).
El material adecuado para el trabajo adecuado
Entonces, en medio del estruendo de entusiasmo por estos materiales, la pregunta que surge es, ¿han llegado los TPC? Los proveedores aeroespaciales de nivel 1 y nivel 2 están invirtiendo en termoplásticos. Hay más interés e inversión de proveedores pequeños y medianos. Consorcios como IRG CosiMo están analizando los mercados aeroespacial y automotriz para avanzar en las tecnologías de proceso para lograr una producción de alto volumen.
“Es la Trifecta”, dice Mead, “los fabricantes de equipos originales están invirtiendo, la gente de maquinaria está invirtiendo, se ha desarrollado el material adecuado. Todos los componentes de la receta se están uniendo ".
En términos más amplios, ¿qué significa todo esto cuando se trata del uso de materiales en aviones de próxima generación? Después de todo, hay numerosos materiales compitiendo por un lugar en los aviones del futuro, y la innovación no se está desacelerando:los compuestos termoendurecibles continúan evolucionando; el aluminio y el titanio seguirán desempeñando un papel.
“A medida que los fuselajes desarrollan una base de calificación con termoplásticos, ahora tienen una opción”, dice Unger. “Y esa elección se basará en la selección del material adecuado para una aplicación determinada que cumpla con la tasa de producción y los requisitos de costo para el componente o estructura en cuestión. Al observar la aviación comercial en el futuro, lo que creo que verán los aviones que hacen es usar el material adecuado para el trabajo correcto. Si un material permite la estructura más adecuada al menor costo y cumple con los requisitos de velocidad de construcción del programa, ganará su camino hacia el avión ”.
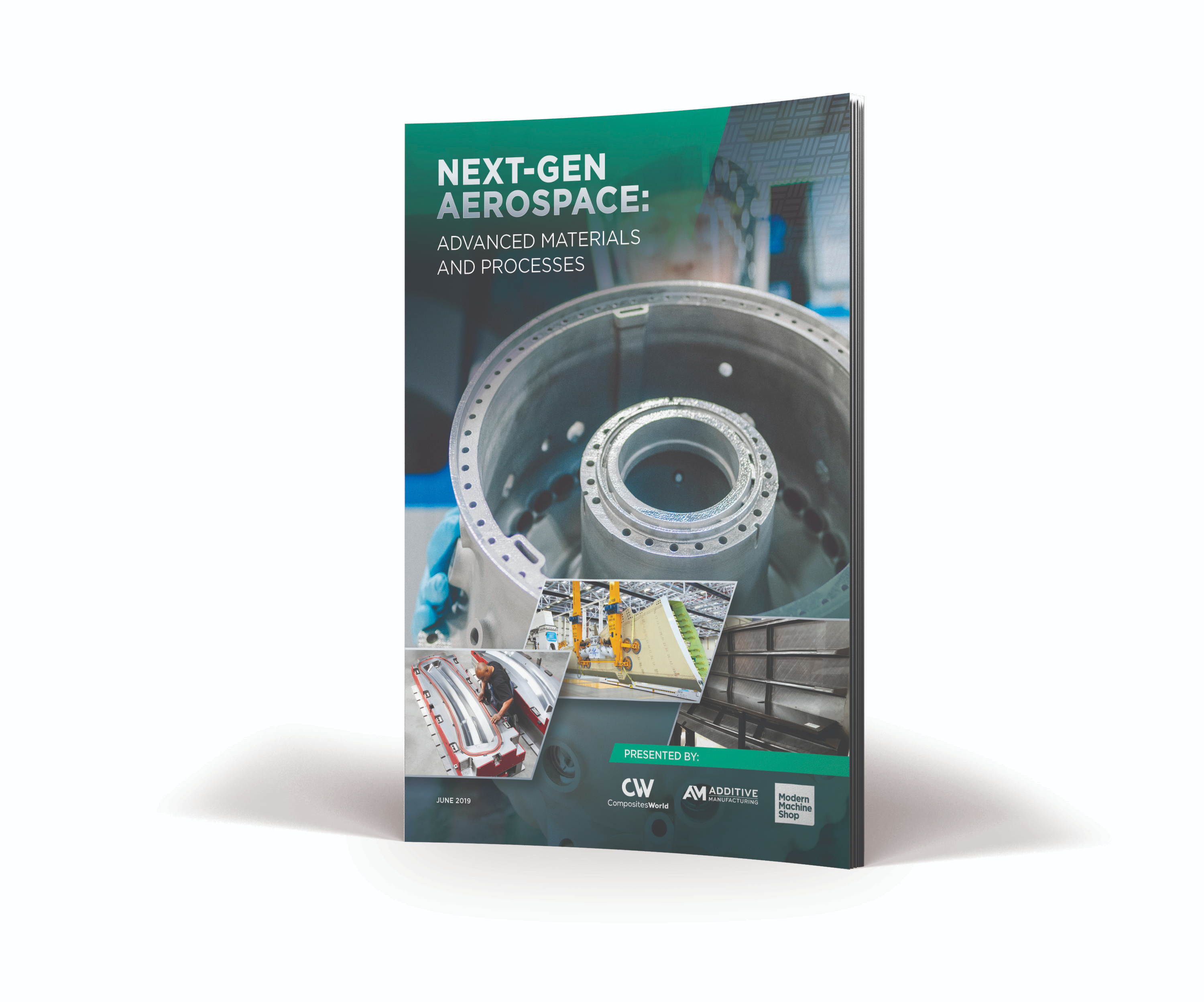
La próxima generación de fabricación aeroespacial
Con la proyección de que la industria de la aviación comercial se duplicará en los próximos 20 años, satisfacer la demanda de aviones de pasajeros y de carga requerirá nuevas tecnologías y tasas de fabricación sin precedentes.
Obtenga más información sobre los materiales y procesos que darán forma a los aviones de próxima generación en una colección de historias de CompositesWorld, Modern Machine Shop y Fabricación aditiva , disponible para leer o descargar gratis . Consíguelo aquí.
Resina
- Covestro intensifica la inversión en compuestos termoplásticos
- Compuestos termoplásticos en Oribi Composites:CW Trending, episodio 4
- Solución de problemas de termoformado de compuestos termoplásticos
- Compuestos termoplásticos:soporte de parachoques estructural
- Toray Advanced Composites expande las capacidades de los compuestos termoplásticos
- Teledyne CML Composites invierte en capacidad de procesamiento termoplástico
- ACMA lanza el programa Thermoplastic Composites Conference 2020
- Puerta termoplástica por primera vez para compuestos automotrices
- Compuestos termoplásticos:vista panorámica
- Vista previa de CAMX 2018:Compuestos avanzados de TenCate
- Soldadura de compuestos termoplásticos