Nuevos horizontes en la soldadura de composites termoplásticos
Este blog acompaña al artículo de septiembre de 2018 "Soldadura de compuestos termoplásticos". Es una compilación de imágenes y detalles que no encajaban en el artículo impreso, incluida una línea de tiempo de los desarrollos de soldadura por inducción y detalles sobre la calificación para futuros aviones comerciales, así como secciones breves sobre reparación, desarrollos para automóviles y termoendurecibles a termoplásticos (TS -TP) soldadura.
Solo para reiterar por qué los ensambles de compuestos termoplásticos soldados (TPC) son de interés para estructuras ligeras tanto aeroespaciales como automotrices, compare las dos imágenes a continuación del mamparo de presión trasero del Airbus A320. La imagen superior es la versión actual fabricada en aluminio. Observe la gran cantidad de remaches. Ahora compare eso con el demostrador de TPC soldado presentado por Premium Aerotec en el Salón Aeronáutico ILA 2018 en Berlín. Note la ausencia de remaches. Para los compuestos, esto no solo elimina el peso, el tiempo y el costo de los sujetadores, sino también el tiempo y el costo de colocar y perforar orificios, además de limpiar e inspeccionar esos orificios. También significa estructuras mucho más ligeras sin las almohadillas laminadas necesarias para compensar los cortes a través de las fibras que soportan la carga.
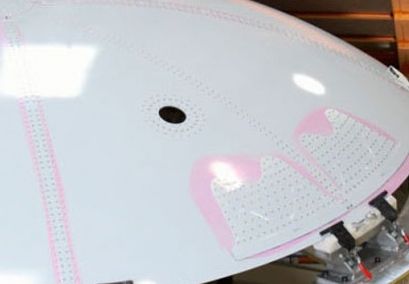
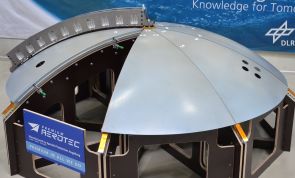
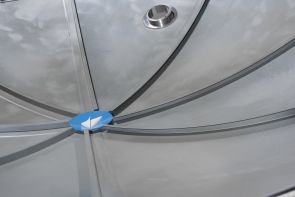
Un mamparo de presión trasero A320 de material compuesto termoplástico soldado (abajo) ofrece una solución sin remaches en comparación con la construcción de aluminio actual (arriba).
FUENTE:RUAG (arriba) y Premium Aerotec (abajo), DLR Center for Lightweight Production Technology (Augsburg, Alemania)
“Otro beneficio es que la inspección de estructuras soldadas es más fácil en comparación con los ensamblajes adheridos”, dice el Dr. Hans Luinge, director de desarrollo de productos e I + D de compuestos termoplásticos para el proveedor de materiales TPC TenCate-Toray Group. “C-scan funciona bien, mostrando si no hay porosidad en el laminado, lo que significa que la soldadura es buena. En el caso de las estructuras adheridas con adhesivo, puede tener una unión de beso o contaminantes que son difíciles de detectar ". Si bien TenCate-Toray no desarrolla tecnología de soldadura en sí, sí respalda una variedad de proyectos de la industria y de los clientes. "Optimizamos nuestros materiales según sea necesario", dice Luinge, "y tratamos de ayudar a dirigir los desarrollos en la dirección correcta en función de nuestra participación desde hace mucho tiempo en esfuerzos como TAPAS y con socios como KVE Composites, TPRC, proveedores de nivel y OEM".
Desarrollos de soldadura por inducción
KVE Composites ha desarrollado la soldadura por inducción para TPC desde 2001. Las primeras aplicaciones utilizaban laminados de tejido de fibra de carbono / PPS, incluidos los elevadores y el timón para los aviones a reacción de negocios Gulfstream G650 y Dassault Falcon 5X.
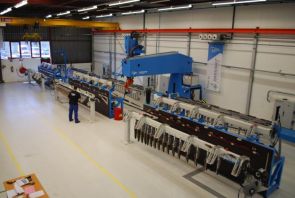
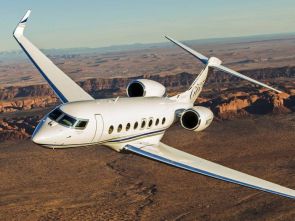
KVE Composites ayudó para desarrollar la producción de GKN Fokker de elevadores y timón (izquierda) soldados por inducción para los aviones Gulfstream G650 (derecha) y Dassault Falcon 5X.
FUENTE:KVE Composites, GKN Fokker (izquierda) y Gulfstream (derecha).
Otras aplicaciones de TPC soldadas por inducción incluyen puertas de acceso al tanque de combustible producidas por AVIACOMP S.A.S. (Launaguet, Francia y ahora parte del Grupo Sogeclair) para el ala del Airbus A220 (anteriormente Bombardier CSeries). (Aviacomp también produjo los largueros para el fuselaje soldado TPC de STELIA que se mostró en el Salón Aeronáutico de París 2017).
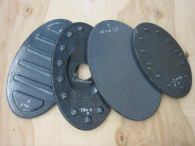
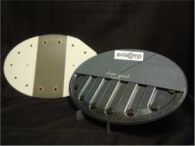
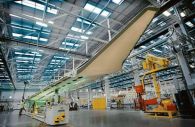
Aviacomp usa inducción tecnología de soldadura desarrollada por KVE Composites en su producción de puertas de acceso al tanque de combustible TPC para el avión de fuselaje estrecho Airbus A220.
FUENTE:Aviacomp, parte de Sogeclair Group.
Esta categoría general de puertas de acceso es una oportunidad para que la soldadura TPC ahorre costos, como se muestra en un estudio de diseño y fabricación completado por KVE Composites. Incluso las aeronaves más pequeñas pueden tener hasta 60 de estos paneles de acceso, todos de formas diferentes y, por lo general, fabricados con una construcción tipo sándwich compuesta con un núcleo de panal mecanizado. “Si utiliza un ensamblaje termoplástico soldado, puede hacer todos los diferentes paneles de acceso para una aeronave con solo $ 100,000 en costos de herramientas, lo que es un ahorro dramático”, dice el director gerente de KVE Composites, Harm van Engelen. “No necesitamos mecanizar el núcleo, solo utilizamos componentes 'similares a los de un lego' (láminas planas y refuerzos estampados) soldados entre sí para formar las diversas formas. Además, nuestras herramientas se parecen más a una plantilla de soldadura, por lo que su costo es relativamente bajo en comparación con lo que están usando en la actualidad. Todos los paneles de acceso de una aeronave podrían fabricarse en una sola celda de soldadura ”.
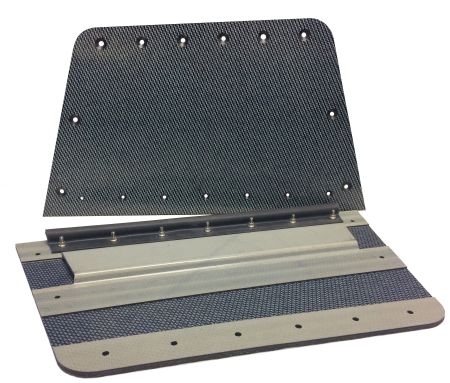
El ensamblaje termoplástico soldado para paneles de voladizo de aeronaves puede fabricarse con células de soldadura y conformado automatizadas y ahorre $ 100,000 en costos de herramientas. FUENTE:KVE Composites.
KVE Composites continúa su desarrollo de tecnologías de soldadura TPC, como se ilustra en los siguientes plazos. La celda de producción que se muestra en la parte inferior para 2019 es la máquina Falko ATL (colocación automática de cinta), producida por Boikon (Leek, Países Bajos) utilizando un efector final de soldadura ultrasónica desarrollado por GKN Fokker. “Esta celda robótica permite un proceso y un sistema de control más eficientes para el siguiente nivel de producción de piezas de TPC en volumen en comparación con los métodos de recogida y colocación que se utilizan en la actualidad”, explica el director de I + D de KVE Composites, Maarten Labordus. “Por ejemplo, puede colocar de forma totalmente automática los laminados de piel y nervaduras para una superficie de control de chorro regional (que es de aproximadamente 60 mm x 3 m), aplicar un paso de formación y consolidación fuera del autoclave y luego completar el ensamblaje en un celda de soldadura contigua ". La máquina Falko ATL también demuestra el control de circuito cerrado ya desarrollado por GKN Fokker para soldadura ultrasónica. “La máquina es capaz de controlar el nivel de energía según sea necesario por tipo de material, espesor y forma, sin embargo, posteriormente se requiere la consolidación por fusión completa de la preforma plana durante el moldeo de la pieza de TPC terminada”, explica Arnt Offringa, director de Aerostructures R&T para GKN Fokker.
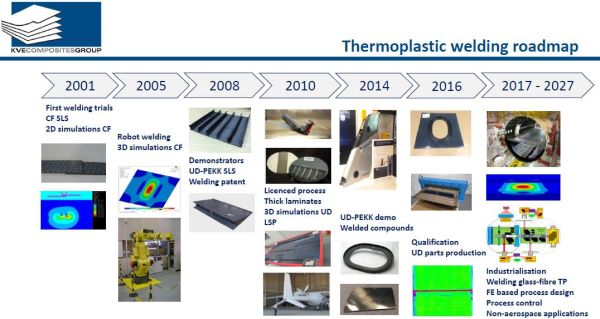
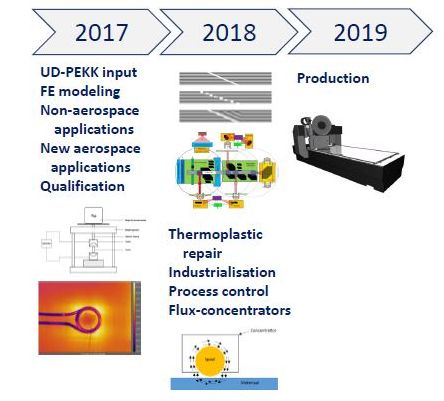
Calificación
Se muestra arriba como una iniciativa de desarrollo clave en 2017, calificación de los procesos de soldadura por inducción para aeroestructuras de TPC es una prioridad constante. Según el resumen de la próxima presentación de KVE Composites en el 4 th En t. Conf. y Exposición sobre compuestos termoplásticos (ITHEC, 30-31 de octubre de 2018 en Bremen, Alemania), en los últimos años, la soldadura de compuestos termoplásticos (TPC) ha experimentado un cambio de polímeros como PPS y PEI hacia polímeros de gama alta como PEEK , PEKK y ahora Low Melt PAEK (LM PAEK, lea más en mi blog “PEEK vs. PEKK vs. PAEK ...”), así como hacia cintas UD colocadas automáticamente y laminados más gruesos para estructuras más cargadas. En respuesta, KVE Composites ha buscado mejorar y estandarizar herramientas y equipos, así como modelos de simulación basados en FEA.
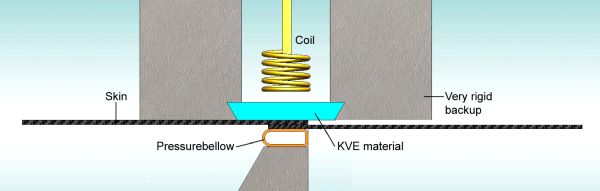
Configuración estandarizada para la calificación de la soldadura por inducción con nuevos materiales.
FUENTE:KVE Composites
Para ayudar en la maduración y calificación del proceso de soldadura por inducción con estos nuevos laminados compuestos, KVE Composites ha desarrollado una configuración estandarizada para soldar cizalla de una sola capa y también cupones de prueba de extracción en L y T. Esta configuración incluye:
- Un marco rígido para soportar cargas de la aplicación de presión al laminado durante la soldadura.
- Un bloque de herramientas inferior que se puede colocar debajo del marco para permitir la soldadura reproducible de paneles estándar.
- Un mandril inflable (debajo de la presión en la figura de arriba) en el bloque de herramientas inferior que puede expandirse en una sola dirección para comprimir el laminado que se está soldando contra un disipador de calor especial ("material KVE" en la figura de arriba) para confinar el calor en la soldadura interfaz.
Al intercambiar los bloques de herramientas inferiores, se pueden soldar una variedad de cupones estándar y luego inspeccionarlos ultrasónicamente, después de lo cual los cupones más pequeños se pueden cortar y probar mecánicamente. Esta configuración estandarizada ya ha sido instalada por:
- Centro de investigación de termoplásticos (TPRC, Enschede, Países Bajos)
- McNair Center de la Universidad de Carolina del Sur (Columbus, SC, EE. UU.)
- Centro Aeroespacial de los Países Bajos (NLR, Marknesse, Países Bajos).
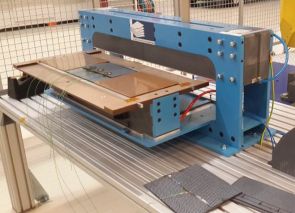

Soldadura por inducción estandarizada configuración en KVE (izquierda) y muestra soldada de fibra de carbono UD / PEKK con termopares para registrar la temperatura en la línea de soldadura (derecha).
FUENTE:KVE Composites.
Reparar
Otra área de desarrollo clave es cómo reparar aeroestructuras de TPC. "Nos estamos centrando primero en las estructuras de tejido CF / PPS que están calificadas y vuelan", dice Labordus. “El proceso es básicamente el mismo que se utiliza para las reparaciones de compuestos termoendurecibles:retire el material dañado, prepare esa área con una bufanda cónica y luego adhiera en un parche de reparación preimpregnado. Labordus dice que uno de los problemas es que el preimpregnado termoplástico a temperatura ambiente es superficial y no se pega, "por lo que es difícil lograr que la geometría coincida". Sin embargo, cree que los sistemas de reparación robótica que están desarrollando Airbus, Lufthansa y otros ofrecen una solución.
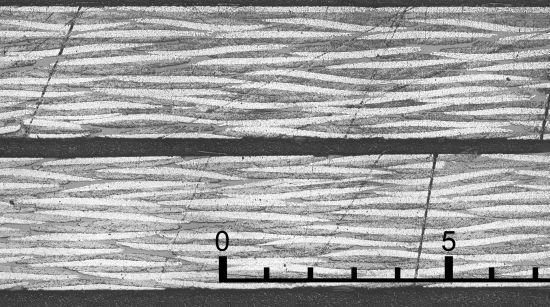
Como parte de su desarrollo continuo de reparaciones de compuestos termoplásticos estructurales soldados, KVE Composites ha logrado uniones cónicas lineales 2D soldadas por inducción en laminados de tejido CF / PPS con espesor uniforme y 90% de propiedades de material virgen.
FUENTE:KVE Composites.
Dichos sistemas utilizan la metrología para medir con precisión las bufandas cónicas mecanizadas por robot y luego unir un parche prefabricado que ha sido mecanizado con precisión robotizada para que coincida. “Queremos utilizar la soldadura por inducción para soldar un parche termoplástico a la estructura original”, dice Labordus, pero aún quedan problemas por resolver. “Dependiendo de la forma de la pieza y el parche, las corrientes de Foucault no se forman en todas partes, por lo que podemos obtener áreas de frío o sobrecalentamiento. KVE Composites ha trabajado en esto y pudo lograr una junta cónica lineal 2D en laminados de tela CF / PPS con un espesor uniforme y una soldadura perfecta. "Estábamos dentro del 10% de las propiedades del material virgen", dice Labordus.
El siguiente paso será soldar por inducción dos partes rectangulares cada una con un borde escarchado y luego soldar un parche ahusado a un agujero circular / elíptico con un escarpado ahusado, que es esencialmente el método utilizado para las reparaciones de compuestos termoendurecibles. “Si eso funciona, pasaremos a laminados UD hechos con PEEK y PEKK”, dice Labordus. Señala que aún no se ha demostrado un sistema para usar una bobina de inducción para hacer reparaciones en el campo, "pero se puede hacer en el laboratorio". Otro problema es cómo aplicar presión para un contacto suficientemente estrecho entre el parche de reparación y la superficie cónica. “En este momento, la presión utilizada en la herramienta de laboratorio es de 5 bar. No estoy seguro de si la presión de la bolsa de la aspiradora es suficiente, pero con un material UD más plano, una barra de la bolsa de la aspiradora solo puede ser suficiente ".
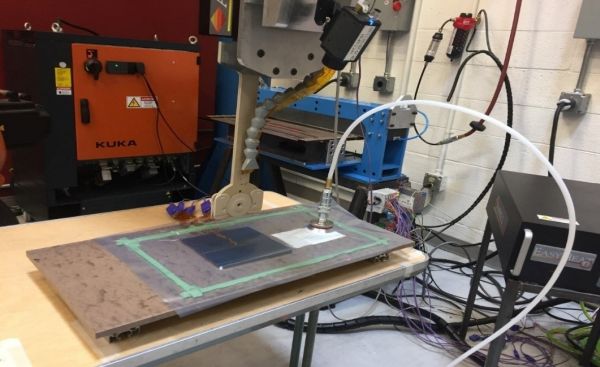
La soldadura por inducción bajo una bolsa de vacío, un posible facilitador para futuras reparaciones de compuestos termoplásticos en el campo, está siendo desarrollada por Michel van Tooren y su equipo en el Centro McNair de la Universidad de Carolina del Sur. FUENTE:Michel van Tooren.
Este trabajo en KVE Composites está siendo ampliado por Michel van Tooren, director del SmartState Center for Multifunctional Materials and Structures, que forma parte del McNair Center de la Universidad de Carolina del Sur (Columbia, SC, EE. UU.). “Estamos soldando compuestos termoplásticos por inducción bajo una bolsa de vacío, que es muy similar a cómo se realizan las reparaciones de compuestos en el campo hoy en día con un adhesivo caliente y una manta térmica”, explica. “La bolsa de vacío se comporta como una herramienta blanda para la compresión de las dos partes. Se aplica corriente de inducción y se logra una reparación por fusión. Solo necesita tener definidos los límites y los parámetros del proceso. En cierto modo, es más fácil que la reparación termoendurecible porque siempre puede volver a fundir la reparación si es necesario, incluso en el otro lado del mundo o después de 20 años de servicio. Y el resultado no es una unión adhesiva, sino una parte cohesiva, por lo que elimina todos los problemas con la unión y cómo saber si tiene una buena unión en una reparación termoendurecible ". Él también cree que con las tecnologías de reparación robótica automatizada que se están desarrollando ahora, "soldar por inducción una reparación sería relativamente sencillo".
Termoendurecible a termoplástico
Van Tooren también está desarrollando soldadura por inducción para unir compuestos termoendurecibles y termoplásticos. “Introducimos termoplástico en un compuesto termoestable, pero solo donde queremos soldar”, explica. “Injertamos una nanopartícula y hacemos un poco de polimerización cruzada. El resultado es una isla de termoplástico implantado y co-fundido químicamente con el compuesto termoestable. Luego puedo soldar en la isla termoplástica ". Una vez más, la visión son métodos alternativos para la unión y ensamblaje de compuestos que eviten perforar agujeros y los problemas asociados con la unión adhesiva convencional.
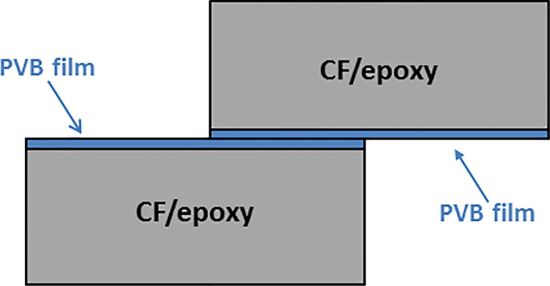
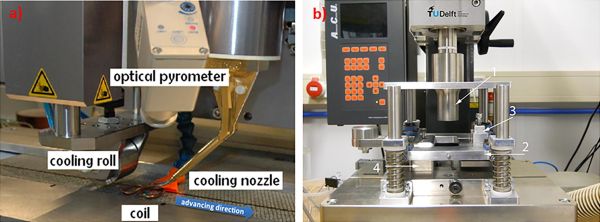
Esquema de una junta TSC-TSC a través de una capa de acoplamiento termoplástico PVB antes de soldar (arriba). Configuraciones (abajo) para soldadura por inducción (izquierda) y soldadura ultrasónica (derecha).
FUENTE:“Soldadura híbrida de compuestos basados en CF / epoxi”.
Varias organizaciones de investigación buscan la soldadura de laminados de compuestos termoendurecibles (TSC) a laminados de TPC (o soldadura TS-TP). Irene Fernandez Villegas en TU Delft, quien es mencionada en el artículo impreso como líder en el desarrollo de soldadura ultrasónica continua de TPC, fue coautora de un artículo de 2017 titulado "Soldadura híbrida de compuestos a base de epoxi reforzados con fibra de carbono" junto con Francesca Lionetto en el Universidad de Salento (Lecce, Italia), Silvio Pappadà en CETMA Composites (Brandisi, Italia), entre otros. Los conceptos básicos son los siguientes:
- El polivinilbutiral (PVB) es un polímero termoplástico semicristalino de bajo costo con una temperatura de fusión de 150-170 ° C que se caracteriza por una excelente capacidad de unión y formación de película y adhesión a muchas superficies.
- Se utilizó PVB (Mowital, suministrado por Kurakay) como capa de acoplamiento, se agregó y se co-curado a una tela de fibra de carbono de 14 capas / laminado epoxi TSC (preimpregnado Hexcel 3501-6 con un 58% de contenido de volumen de fibra y 180 ° C curado).
- El enclavamiento macro-mecánico entre la capa de acoplamiento de PVB y el compuesto CF / epoxi se logró mediante la penetración parcial de la resina de PVB en la primera capa del TSC (típicamente entre 10 y varios cientos de micrones de espesor) durante el co-curado y difusión de los monómeros epoxi en la película termoplástica de PVB.
- Los procesos de soldadura por inducción y soldadura ultrasónica dieron como resultado uniones soldadas adecuadamente fuertes, con las juntas resultantes de CF / epoxi a CF / epoxi soldadas a través de las capas de acoplamiento de PVB que muestran una resistencia al cizallamiento traslapado de ≈25 MPa, que está dentro del rango típico de valores de resistencia para juntas CF / epoxi adheridas.
Automotriz
Casi todas las empresas incluidas en el artículo de impresión de soldadura termoplástica buscan aplicaciones automotrices y aeroespaciales. “La soldadura ayuda a que los compuestos sean competitivos frente al aluminio”, dice Offringa de GKN Fokker. “Automotive también está considerando la soldadura como una alternativa rápida a la unión. Hemos hablado con varias empresas automotrices sobre el procesamiento rápido de compuestos ". Señala que las carrocerías de automóviles compuestas de fibra de carbono son en su mayoría termoendurecibles, unidas con un espesor específico de adhesivo. "Si pudiera hacer estas piezas con termoplástico materiales compuestos y eliminar los espacios entre los componentes soldando el ensamblaje, entonces puede hacer una estructura de carrocería más rígida, lo que aporta beneficios de peso, costo y rendimiento ”.
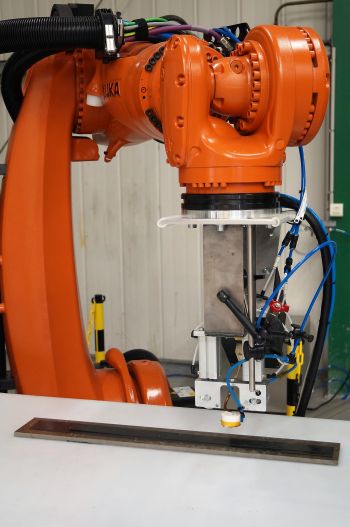
dinámica de integridad compuesta Configuración del proceso de soldadura por inducción.
FUENTE:Integridad compuesta.
Jérôme Raynal, gerente de desarrollo comercial de Composite Integrity también ve potencial. Su empresa trabajó con STELIA Aerospace para desarrollar el proceso de soldadura por inducción dinámica utilizado para unir largueros de cinta CF / PEKK UD y revestimientos de fuselaje en el demostrador TP, presentado en el Salón Aeronáutico de París 2017. “Hemos desarrollado soldadura resistiva para automoción con compuestos de poliamida [PA, nailon] y polipropileno [PP]”, dice Raynal. “Tenemos una variedad de tecnologías diferentes para esto. Por ejemplo, podemos incrustar un alambre metálico en una parte, ponerlo en contacto con otra parte e inyectar corriente. También podemos colocar un parche resistivo de fibra de carbono en la interfaz de soldadura para generar el calor de soldadura requerido ". En un desarrollo, se soldaron dos componentes hechos de CF / PA usando un parche resistivo especialmente diseñado hecho con el mismo polímero y un vellón de fibra de vidrio para aislar eléctricamente el laminado contiguo y concentrar la energía en la línea de soldadura. ¿Qué pasa con las inserciones metálicas que son muy típicas en las piezas de automóviles? “Las piezas con inserciones de metal no son un problema con la soldadura por resistencia, y con la soldadura por inducción se usaría una bobina de diseño especial o se modificaría los campos electromagnéticos y la corriente de alguna otra manera”, responde Raynal. "Esto tendría que desarrollarse, pero es similar a lo que ya hemos demostrado para la producción automatizada de estructuras de aviones".
Nuevos desarrollos y otros proyectos
Una nota sobre la imagen de apertura. Muestra una representación CAD del proceso automatizado desarrollado por el DLR Center for Lightweight Production Technology (DLR ZLP, Augsburg, Alemania) utilizando una soldadura ultrasónica diríjase a un robot industrial KUKA Quantec KR210 para unir ocho secciones de TPC en un mamparo de presión trasero (RPB) para un avión tipo A320. En el artículo impreso adjunto sobre soldadura TPC, hablé del desarrollo de DLR ZLP de una soldadura por resistencia Método que se utilizó en el demostrador A320 RPB de Premium Aerotec exhibido en la feria aérea ILA 2018 en Berlín. Según Lars Larsen, gerente de grupo de tecnologías de ensamblaje y unión en DLR ZLP, “En paralelo al proceso de soldadura por resistencia utilizando un 'puente de soldadura', también hemos desarrollado un cabezal de soldadura ultrasónico accionado por robot. Hemos completado pruebas preliminares para determinar los parámetros relevantes del proceso de soldadura, y en los próximos meses refinaremos la integración de ese efector final de soldadura ultrasónica en nuestro robot. Nuestro objetivo es desarrollar un proceso industrial único para soldar tanto los largueros del fuselaje de las aeronaves como el mamparo de presión trasero fabricado con compuestos termoplásticos ”.
Otros proyectos que no tuve la oportunidad de cubrir esta vez incluyen EireComposites y su participación en los proyectos Ybridio e Innova, buscando el potencial de la soldadura para reducir costos y aumentar la automatización. La compañía informa sobre la capacidad de soldadura por inducción y resistencia para compuestos CF / PEEK, CF / PEKK y GF / PP y que se evaluó la soldadura termoplástica para el ala Bombardier CSeries (ahora Airbus A220).
Tods Aerospace, ahora parte de Unitech Aerospace, participó en un Programa Nacional de Explotación de Tecnología Aeroespacial (NATEP) patrocinado por Rolls-Royce que analizó el desarrollo de una técnica de soldadura por resistencia que no utiliza implantes metálicos incrustados. TenCate-Toray y el National Composites Centre (Bristol, Reino Unido) también fueron socios.
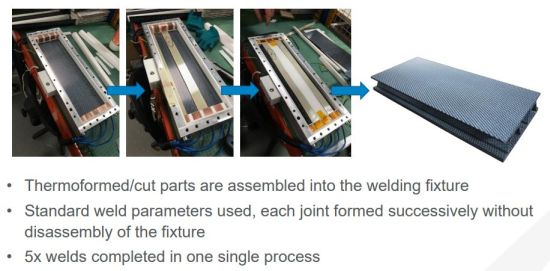
Este demostrador de procesos exploró un método para fabricar estructuras de TPC reforzadas con sombrero. FUENTE:Unitech Aerospace (comience en la Sección 6, p. 39)
Estén atentos, ya que planeo cubrir los desarrollos de Laser Zentrum Hannover (LZH) con soldadura láser de compuestos termoplásticos en un futuro cercano.
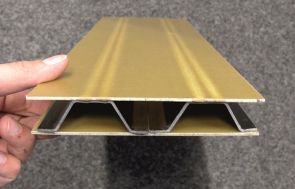
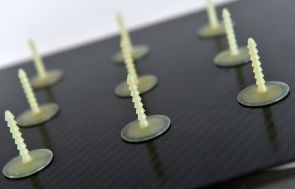
FUENTE:LZH Laser Zentrum Hannover eV
Resina
- Covestro intensifica la inversión en compuestos termoplásticos
- Compuestos termoplásticos en Oribi Composites:CW Trending, episodio 4
- El proyecto RECONTRAS valida el uso de microondas y soldadura láser para obtener composites reciclables
- La nueva bota de senderismo Salewas presenta compuestos termoplásticos
- Solución de problemas de termoformado de compuestos termoplásticos
- Compuestos termoplásticos:soporte de parachoques estructural
- Toray Advanced Composites expande las capacidades de los compuestos termoplásticos
- Teledyne CML Composites invierte en capacidad de procesamiento termoplástico
- El consorcio de compuestos termoplásticos IRG CosiMo presenta nuevas instalaciones
- Compuestos termoplásticos:vista panorámica
- Soldadura de compuestos termoplásticos