Compuestos termoplásticos reciclados para producción
La reciclabilidad ha sido un beneficio prometido durante mucho tiempo del uso de compuestos termoplásticos (TPC). Pero aún no se ha utilizado comercialmente a gran escala. El proveedor de materiales TenCate Advanced Composites y el ThermoPlastic composites Research Center (TPRC) se asociaron con el fabricante de nivel 1 GKN Fokker para demostrar un proceso de este tipo en 2016. El equipo desarrolló un panel de puerta de acceso utilizando desechos de fibra de carbono tejida TenCate Cetex TC1100 / sulfuro de polifenileno (CF / PPS) de la producción de GKN Fokker del elevador y timón Gulfstream G650. Los desechos de producción se cortaron y luego se moldearon por compresión utilizando un proceso y un molde diseñados por TPRC. El panel de la puerta de acceso presentaba nervaduras de refuerzo moldeadas, variaciones de espesor y orificios moldeados con protuberancias. (Un saliente es una característica que sobresale que guía un sujetador dentro del agujero). El uso del material recuperado permitió una pieza liviana con una mayor funcionalidad moldeada al tiempo que formaba un proceso de fabricación de circuito cerrado, ya que el panel de la puerta de acceso se usó en el borde de ataque del timón Gulfstream G650. El proyecto ganó un premio a la innovación JEC en 2016.
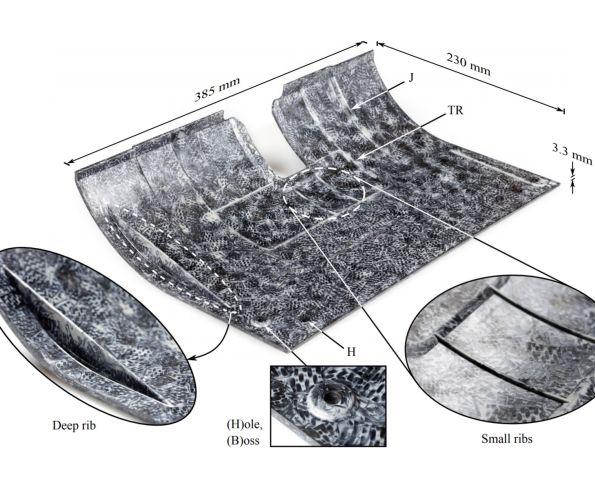
Panel de la puerta de acceso demostrado en 2016 está hecho de material Cetex CF / PPS de desecho y presenta nervaduras de refuerzo y orificios moldeados con salientes. FUENTE | TPRC.
Desde esa investigación, se ha establecido una nueva organización, el Centro de Aplicaciones de Compuestos Termoplásticos (TPAC). “El TPRC se formó hace diez años y trabaja principalmente en la investigación fundamental de TPC para la industria aeroespacial”, explica Thomas de Bruijn, investigador de estructuras ligeras en TPAC. "El TPAC se formó aproximadamente dos hace años, y tiene una forma de trabajar más aplicada. Está vinculado a la Universidad de Saxion y también a las pymes. Nos enfocamos en reducir los costos mediante el desarrollo de procesos más rentables. Juntos, estos dos grupos forman TPC NL, una industria inteligente, centro de innovación digital para la tecnología TPC ”.
La participación del TPAC y también la I + D continua de TenCate han demostrado que este tipo de fabricación de ciclo cerrado no solo es posible, sino también económicamente beneficioso. El enfoque, inicialmente, está en los materiales CF / PPS, y la investigación se realiza en colaboración con socios de la industria para ayudar a implementar esta producción de piezas mejoradas con reciclaje de TPC.
Sin embargo, los procesos reales desarrollados difieren. TenCate se ha centrado en material de fibra más corta que se utiliza como capa de flujo para agregar características geométricas moldeadas y funcionalidad a las piezas de fibra continua. Mientras tanto, TPRC y TPAC han buscado mantener una mayor longitud de fibra, creando un material similar a una masa que se puede moldear por compresión en piezas con propiedades mecánicas más altas que las posibles con los compuestos tradicionales de fibra corta.
TenCate - Partes de la hoja orgánica mejorada de la capa de flujo
“Hace tres años, comenzamos a invertir más de nuestro presupuesto de I + D en reciclaje”, dice Frank ten Napel, gerente de productos de TenCate para termoplásticos. “No se trata solo de obtener una 'etiqueta verde'. Estamos convencidos de que incorporar material reciclado en su pieza ofrece beneficios económicos y constructivos muy reales. Podemos aplicar un nivel de geometría a una pieza que no podríamos lograr de otra manera. Al aplicar una capa de flujo de material reciclado, podemos moldear nervaduras de refuerzo y espesor variable a lo largo de la pieza, así como protuberancias alrededor de los orificios, que distribuyen las cargas inducidas por los sujetadores. Todo esto permite usar menos material de fibra continua, para piezas más delgadas, más livianas y más rentables en lugar de simplemente usar material virgen ". Señala que estas características moldeadas son difíciles de lograr con materiales de fibra continua, "pero al combinar fibra continua más sobremoldeado localizado, se obtiene más libertad de diseño".
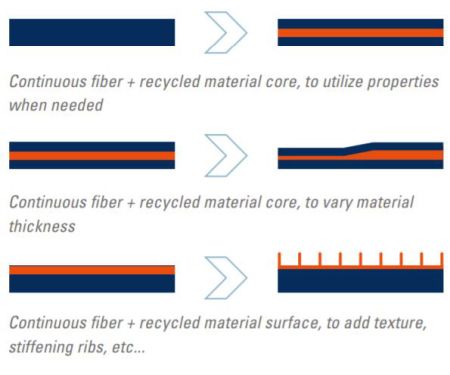

Este demostrador tipo corchete muestra ambos lados de la misma pieza, destacando una capa de organohoja tejida convencional y una capa de flujo de TPC reciclado. Este último presenta nervaduras de refuerzo y protuberancias para inserciones. FUENTE | TenCate
Proyecto de ciclo TPC
Este proyecto de cuatro años comenzó en septiembre de 2015 e incluye socios de toda la cadena de suministro de compuestos termoplásticos (TPC):
- TenCate Advanced Composites (Toray Group) - materiales
- GKN Fokker Aerostructures:diseño y fabricación de nivel 1 de estructuras y ensamblajes aeroespaciales
- Componentes termoplásticos holandeses (DTC):diseño y fabricación para pymes de nervaduras, largueros, soportes, clips, cajas para la industria aeroespacial
- Cato Composites:fabricación y diseño de piezas para las pymes para los mercados aeronáutico, automovilístico, de defensa, deportivos y de consumo
- Nido RecyclingTechniek (NRT):tecnología para triturar y reducir el tamaño de los materiales / piezas a reciclar
TPC-Cycle es facilitado por TPAC y la Universidad de Ciencias Aplicadas de Saxion, en particular su grupo de investigación de estructuras ligeras, y financiado por Regieorgaan SIA, parte de la Organización de los Países Bajos para la Investigación Científica (NWO).
Thomas de Bruijn es director de proyectos de TPC-Cycle e investigador en estructuras ligeras en Saxion / TPAC. Explica que hubo muchos impulsores para iniciar el proyecto TPC-Cycle. “Pudimos ver un aumento en el uso de TPC de fibra continua, especialmente para la estampación, como en clips y soportes. Con este aumento, el volumen de residuos postindustriales se vuelve sustancial. Por tanto, el reciclaje era necesario, tanto para el medio ambiente como para la economía, y también para cumplir con las normativas. Por ejemplo, la legislación europea sobre el final de la vida útil exige que se recicle el 95% del material utilizado en los automóviles ”. Señala que Airbus también ha establecido objetivos de reciclaje y final de la vida útil, y los ha comunicado a sus proveedores. “La cadena de suministro no solo debe decir que puede cumplir con estos objetivos, sino también demostrar esa capacidad con demostradores”, agrega de Bruijn.
“También hemos visto crecer los TPC fuera del sector aeroespacial, en aplicaciones como cajas de alimentos, muebles y componentes industriales porque ofrecen tiempos de ciclo más bajos, estructuras ligeras y más inteligentes”, dice de Bruijn.
Continúa:“Queríamos probar una cadena de proceso de reciclaje comercialmente viable, pero no solo el triturado, que es el reciclaje. Queríamos alto rendimiento. Por lo tanto, elegimos un método de mezcla de bajo cizallamiento para retener una longitud de fibra de 0,5 a 1,0 pulgadas. Para rigidez, solo necesita un par de mm de longitud. Pero para obtener fuerza y resistencia al impacto, necesita más de 0,5 pulgadas de largo ". Además de mantener la longitud de la fibra, otro desafío clave fue lograr una buena homogeneidad en la mezcla de materiales y en el producto reciclado final.
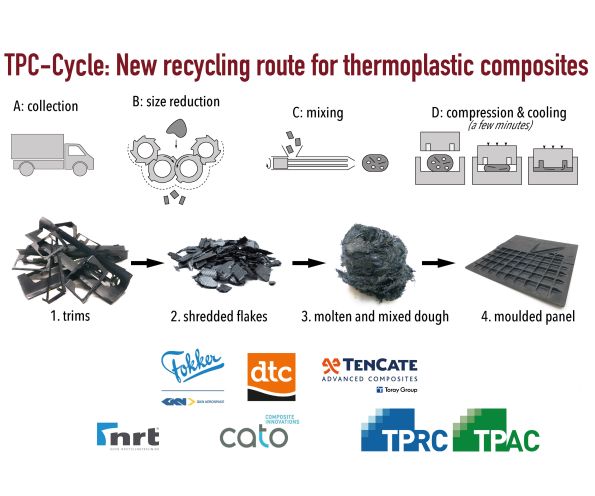
“El objetivo es recolectar los desechos, triturarlos en copos de 0,5-1,0 pulgadas y transformarlos en una masa homogénea, que se extruye y se transfiere directamente a una prensa de moldeo por compresión”, explica el investigador y Ph.D. de TPRC. estudiante Guillaume Vincent. "El procesamiento de la masa se realiza mediante la alimentación de escamas y gránulos de polímero virgen en un mezclador de bajo cizallamiento, lo que reduce la fracción de peso de la fibra al 25-40%". Señala que el proceso es muy similar a la composición directa de termoplásticos de fibra larga (D-LFT), que es común en la automoción. “Sin embargo, los procesos D-LFT requieren millones de dólares de inversión, por lo que solo se utilizan en la producción de alta serie. Hemos modificado nuestro enfoque utilizando máquinas más pequeñas, pero obtenemos resultados similares. Nuestros volúmenes son bajos en comparación con los procesos D-LFT ”.
Vincent describe un ejemplo de dónde vale la pena incluir la cadena de valor de reciclaje completa:"NRT nos ayudó a conectarnos con los fabricantes de máquinas trituradoras más grandes, como Untha". Esta es una parte clave para escalar el proceso de producción de piezas en serie.
La primera cadena de procesos que se está desarrollando es para CF / PPS. Vincent dice que TPC-Cycle ha creado modelos de simulación y métodos de análisis para caracterizar la longitud de la fibra y la distribución de la fibra en el material reciclado. “También estamos comprendiendo cómo estas características del material se transfieren a las propiedades de la pieza moldeada”, observa. Este es, de hecho, el enfoque de su Ph.D. tesis, que se publicará a finales de 2019.
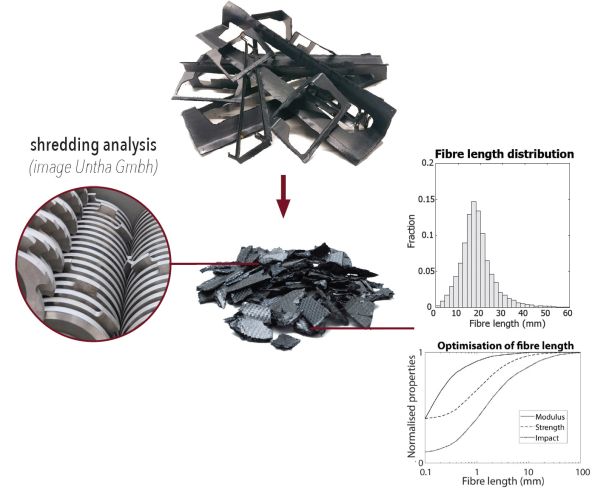
El TPC- El proyecto Cycled ha desarrollado una cadena de proceso completa para reciclar compuestos termoplásticos, incluida la trituración rentable y la caracterización de la longitud y distribución de la fibra. FUENTE | TPRC / TPAC.
Esta masa reciclada a veces se denomina compuesto de moldeo a granel (BMC). Históricamente, BMC era una mezcla similar a una masa de fibra de vidrio corta (<25 mm), pasta de resina termoendurecible y rellenos que se moldeaba por compresión en piezas compuestas. Con menos volumen de fibra y más flujo en comparación con el compuesto de moldeo de láminas (SMC), también ofrecía propiedades mecánicas ligeramente más bajas. TenCate ha vendido termoendurecibles y termoplásticos BMC durante años, aunque este último es un proceso en el que las cintas preimpregnadas unidireccionales cortadas se esparcen en un molde y se presionan. “Nuestro producto es en realidad bastante diferente”, afirma Vincent. “Con BMC termoplástico convencional generalmente no hay mezcla y requiere un ciclo largo de calentamiento y consolidación. Descubrimos que con la mezcla se obtiene un producto más homogéneo y menos concentraciones de estrés en la pieza, por lo que propiedades más altas. Con el BMC termoplástico convencional, obtiene copos más gruesos que tienen regiones ricas en matriz en los extremos que producen concentraciones de tensión en el laminado compuesto ”.
El proceso de mezcla de bajo cizallamiento desenreda los copos en capas y luego separa las capas en haces y los haces en fibras sueltas. El polímero también se mezcla para disminuir el contenido de fibra con el fin de obtener mejores propiedades de flujo, de modo que el material sea más fácil de procesar en formas.
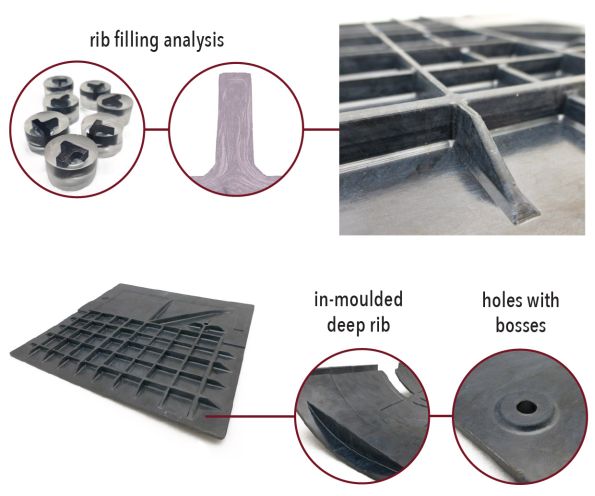
“La masa se extruye y luego se coloca robóticamente en un molde de compresión isotérmico [calentado] abierto”, explica de Bruijn. “Después de mezclar, las fibras de la masa se orientan aleatoriamente. Pero durante el prensado, el flujo de material reorienta las fibras. Esta orientación es menor en comparación con las mezclas que utilizan fibras más cortas moldeadas por inyección, pero es similar de una pieza a otra. Este es uno de nuestros temas de estudio continuo ”.
Costo
La cadena de procesos TPC-Cycle desarrollada hasta la fecha parece económicamente beneficiosa. “Esperamos responder cuánto podemos reducir los costos de las piezas para más adelante en 2019”, dice de Bruijn. "Pero esto es complejo porque necesitas un mercado y tienes que vender el material reciclado". Señala que hay muchos factores económicos. Por ejemplo, la mayoría de los fabricantes de hoy simplemente están tirando los desechos de producción. El costo local para desechar en un relleno sanitario es de € 80 por tonelada ($ 90). “Pero este material que se desecha tiene valor”, dice de Bruijn. “Además, debe tener en cuenta los costos de recolectar los desechos, triturarlos, mezclarlos y luego moldearlos por compresión para obtener piezas nuevas. Sin embargo, este es también un proceso casi en forma de red con tiempos de ciclo cortos debido al molde isotérmico ". En otras palabras, debería haber una reducción o eliminación drástica del acabado y mecanizado secundarios. De Bruin dice que TPC-Cycle ahora está estudiando completar el análisis de costos y el análisis del ciclo de vida.
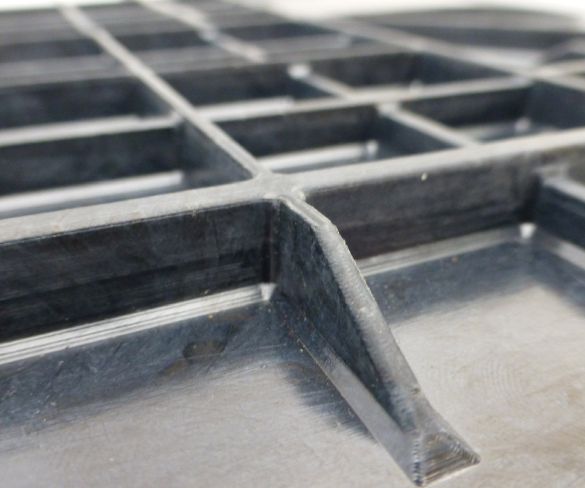
FUENTE | TPRC / TPAC
RESET de Clean Sky
Un tercer proyecto que reitera la importancia del trabajo realizado por TenCate y también en el proyecto TPC-Cycle es el proyecto RESET, que se desarrolló desde enero de 2016 hasta diciembre de 2017 y fue coordinado por el Instituto Tecnológico Leitat de Barcelona, España. Parece que RESET se inició en Clean Sky (2008-2016) y se completó durante Clean Sky 2 (2017-2021).
Los programas Clean Sky y Clean Sky 2 están organizados en un nivel superior de Programas de demostración de aeronaves innovadoras (consulte IADP de vehículos en la imagen a continuación) y un nivel inferior de Demostradores de tecnología innovadora (consulte ITD de sistemas grandes en la imagen de abajo). RESET se completó como parte del ITD de la estructura del avión, específicamente el Paquete de trabajo (WP) A-3.4 Diseño ecológico para la estructura del avión.
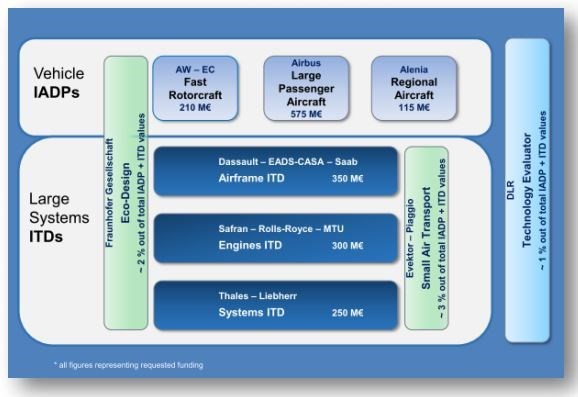
FUENTE:Limpiar Técnica conjunta Sky 2 Propuesta
Para más detalles, consulte “Demostradores de compuestos termoplásticos:hoja de ruta de la UE para las estructuras de los aviones del futuro”
Según Elena Pedone, responsable del proyecto Clean Sky, el equipo de RESET de Leitat desarrolló un proceso para reciclar el material compuesto de aviones usado anteriormente y utilizarlo para fabricar piezas nuevas. Compararon estas piezas recicladas con las fabricadas comercialmente y encontraron que tenían características mecánicas similares. “La tecnología desarrollada en este proyecto podría comercializarse de manera realista en el sector aeronáutico en los próximos años y posiblemente extenderse a otros sectores económicos”, dice Pedone.
Durante el proyecto RESET, se completó el trabajo para investigar los efectos de los materiales de matriz termoplástica PEEK y PPS y la naturaleza química del refuerzo de fibra de carbono. Se estudió la forma del refuerzo, incluida la longitud de la fibra y tejido versus no tejido. También se estudió el efecto del contenido de fibra (relación polímero / fibra).
En un segundo paquete de trabajo, el objetivo principal fue el acondicionamiento y caracterización de CF / PPS reciclados a base de extrusión y los composites moldeados resultantes. Dos partes, un soporte de termoplástico y un taco de termoplástico, se crearon mediante moldeo por inyección y otras dos mediante termoformado, explica la coordinadora científica del proyecto de Leitat, Claudia Aguilar. A continuación, se probaron estas piezas. “Se encontró que las propiedades mecánicas del material eran comparables con la contraparte comercial”, dice Aguilar.
El proyecto RESET afirma haber demostrado un proceso de reciclaje que puede tomar material de desecho de TPC de la producción de aviones y utilizarlo como materia prima para producir nuevas piezas para aviones. “Se utilizó hasta un 70% del material reciclado para producir una nueva familia de materiales compuestos”, dice Aguilar. Añade que “el proceso de reciclaje de RESET permite a la aviación europea limitar la huella medioambiental y reducir los costes de producción de nuevas piezas de aviones. Por lo tanto, el proyecto hace que la industria de la aviación sea más competitiva y más ecológica ”.
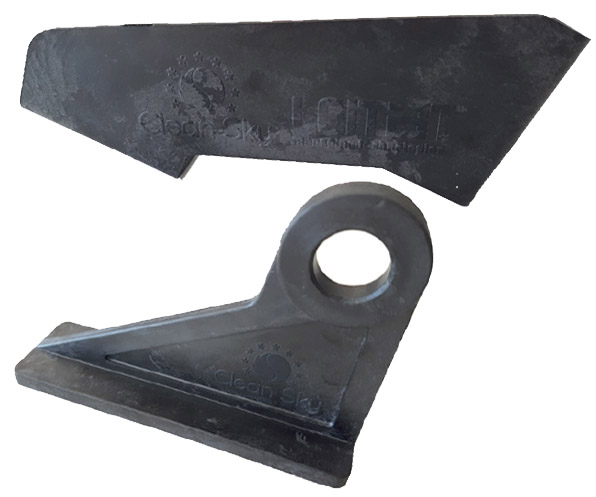
Soporte (izquierda) y cala (derecha) hechos de material CF / PPS reciclado demostrado por el proyecto Clean Sky RESET. FUENTE | Instituto Tecnológico Leitat
El futuro de TPC comienza con el diseño
La afirmación de TenCate y TPRC / TPAC es que estos procesos de reciclaje que ahora se han demostrado no solo son ecológicos, sino económicamente atractivos. Entonces, ¿qué tipo de inversión se requiere? “Depende del volumen de producción”, dice Ten Napel en TenCate. "Las máquinas trituradoras necesarias no son grandes ni caras y el proceso se ha desarrollado hasta donde es bastante sencillo". ¿El tipo de matriz afecta la reciclabilidad? “No”, dice Ten Napel, “pero en términos de viabilidad económica, la fibra de carbono y el PPS, PEEK o PEKK son más viables que la fibra de vidrio y el polipropileno debido a su mayor valor en comparación con este último”.
“Creo que si la industria se ocupará de esto, debería comenzar con el diseño”, continúa. “El mayor obstáculo en este momento es la mentalidad de los ingenieros. Salir y diseñar con material reciclado (o diseñarlos parcialmente en un nuevo producto) es bastante nuevo para ellos ".
Ten Napel admite que TenCate no diseña ni fabrica piezas comercialmente, "pero estamos tratando de inspirar a los diseñadores a pensar de esta manera al desarrollar sus nuevas piezas y estructuras". Él cita los interiores de los aviones y los paneles de acceso y las puertas de acceso como frutas fáciles de reutilizar para reutilizar el material reciclado. "Si nosotros, como industria, podemos acostumbrarnos a reutilizar nuestra propia chatarra y desechos, entonces podemos dar el siguiente paso y comenzar a buscar cómo abordar el final de la vida útil de las piezas".
El mantra sobre el reciclaje de compuestos termoplásticos, simplemente triturar y remodelar, definitivamente se puede adoptar, dice Ten Napel, pero a menudo no tiene mucho sentido económicamente. “Hemos demostrado un mejor proceso y uno que realmente puede crear piezas y programas generales más rentables. Hemos optado por difundir este conocimiento, junto con el TPRC y el TPAC, para inspirar a la industria en cuanto a lo que es completamente posible con los compuestos termoplásticos ". Si los compuestos termoplásticos se van a adoptar a gran escala, el reciclaje como parte inherente de la producción ya no es una opción, es una necesidad.
Resina
- Reciclaje:compuestos termoplásticos reforzados con fibra continua con policarbonato reciclado
- Biomaterial termoplástico "perfeccionado" para aplicaciones médicas
- Karl Mayer lanza la línea de producción de cintas termoplásticas UD
- INEOS Styrolution para construir un sitio de producción para el compuesto termoplástico StyLight
- Hexion presenta una solución epoxi de dos componentes para la producción de compuestos aeroespaciales
- Puerta termoplástica por primera vez para compuestos automotrices
- LANXESS amplía la capacidad de producción de compuestos termoplásticos continuos reforzados con fibra
- Vista previa de CAMX 2018:Compuestos avanzados de TenCate
- Soldadura de compuestos termoplásticos
- TenCate celebra la asamblea del consorcio de compuestos termoplásticos en Brasil
- El consorcio de compuestos termoplásticos tiene como objetivo la producción de alto volumen para la industria automotriz y aeroespacial