Estudio de dinámica molecular sobre nanomáquina basada en puntas:una revisión
Resumen
Los enfoques de nanomáquinas basadas en puntas (TBN) han demostrado ser una técnica poderosa y factible para la fabricación de microestructuras. La simulación de dinámica molecular (MD) se ha aplicado ampliamente en el enfoque TBN para explorar el mecanismo que no pudo ser revelado completamente por experimentos. Este artículo revisa el progreso científico reciente en la simulación MD del enfoque TBN. Primero se presentan los métodos de establecimiento del modelo de simulación para varios materiales. Luego, se discute el análisis del mecanismo de mecanizado para el enfoque TBN, incluido el análisis de la fuerza de corte, el análisis de remoción de material y el análisis de defectos en el subsuelo. Finalmente, se dan las deficiencias actuales y las perspectivas futuras del método TBN en simulaciones MD. Es de esperar que esta revisión pueda proporcionar cierta referencia para la investigación de seguimiento.
Introducción
La tecnología de micro y nanofabricación se ha utilizado ampliamente en diversas esferas, como el medio ambiente, la energía, la biología, la medicina, la defensa nacional y otras esferas, que desempeñan un papel cada vez más importante en la promoción del desarrollo nacional y el progreso social [1, 2, 3, 4] . Para realizar micro / nanofabricación de alta precisión, el enfoque de mecanizado mecánico basado en sondas de microscopía de fuerza atómica (AFM) conocido como TBN tiene equipos y operaciones simples, precisión de mecanizado a nanoescala con un bajo requisito ambiental, y se ha demostrado que es un método poderoso y factible enfoque para fabricar microestructuras [5, 6]. Hasta ahora, nanopuntos, líneas / ranuras, estructuras bidimensionales (2D) / tridimensionales (3D) e incluso nanoestructuras en superficies curvas conocidas como los componentes principales de los nanodispositivos ya se han fabricado con éxito mediante el método TBN [7].
Para fabricar nanoestructuras con mayor precisión, se necesita un conocimiento profundo del proceso de mecanizado de los métodos TBN. Muchos académicos han investigado el mecanismo del enfoque TBN con experimentos en varios materiales, como metales [8], semiconductores [9, 10] y polímeros [11]. Sin embargo, es difícil investigar más a fondo el mecanismo interno de los enfoques TBN mediante experimentos. Se ha demostrado que la simulación de dinámica molecular (MD) es una herramienta poderosa para explorar el proceso de nanomáquina que no pudo ser completamente revelado por experimentos [12, 13]. En comparación con el método experimental, el método MD puede explicar mejor el mecanismo a microescala de eliminación de material y generación de superficie mediante el análisis de las fuerzas de corte, el estado de tensión, la disipación de energía y la topografía de la superficie [12].
En el pasado, algunos académicos ya han utilizado la tecnología de simulación MD para investigar los procesos TBN. Fang y col. investigó los efectos de la alimentación de trazado y el ángulo del cono en el proceso de nanolitografía [14, 15]. Isono y Tanaka analizaron los efectos de la temperatura, la maquinabilidad y las fuerzas interatómicas del níquel metálico [16, 17]. Yan y col. estudiaron los efectos de la geometría de la punta en el proceso de litografía basado en AFM [18]. Actualmente, se han investigado algunos procesos nuevos de TBN con simulaciones de MD. Xiao y col. compararon la diferencia entre el método de arado estático y el método de arado dinámico, y encontraron que podían fabricarse nanoestructuras más pequeñas con el método de arado dinámico [19]. Geng y col. han realizado simulaciones MD de nano-arañazos controlados por carga aplicando directamente una carga normal constante en la sonda [20]. Para fabricar nanograbados con mayor densidad, se debe estudiar la alimentación mínima (MF). Ren y col. presentó un enfoque novedoso que implica un criterio de grueso a fino para determinar MF con el uso de simulaciones MD [21]. Los resultados muestran que se obtiene MF de alta precisión. Sin embargo, en el artículo de revisión anterior [12, 13, 22,23,24], estos nuevos avances de la tecnología de simulación MD utilizada para el proceso TBN no se incluyen. Por lo tanto, en esta revisión, nos enfocamos en el estado del arte reciente de la simulación MD para métodos TBN. Primero se discuten las tecnologías de modelado en varios materiales y los nuevos métodos de mecanizado. Luego, se revisa el mecanismo de los métodos TBN, incluido el análisis de la fuerza de corte, el análisis de remoción de material y el análisis de defectos en el subsuelo. Finalmente, en esta revisión también se dan los desafíos restantes y las perspectivas futuras en la simulación MD de TBN.
Métodos de simulación
Para obtener resultados de predicción precisos, es necesario optimizar el modelo de simulación y la configuración de procesamiento relacionada. El modelo de simulación contiene principalmente configuración atómica y función potencial. La configuración atómica se puede clasificar en estructura cristalina y amorfa. Los átomos en materiales cristalinos como cobre, hierro, silicio, etc. están dispuestos de manera regular y ordenada y los materiales amorfos como polímeros están compuestos por cadenas moleculares irregulares. El comportamiento de los materiales en nanoescala se representa en simulaciones de MD por medio de funciones potenciales y se han propuesto y utilizado varias funciones potenciales para simular el comportamiento de los materiales en simulaciones atomísticas. Además, también se debe considerar la configuración de procesamiento, como las diversas condiciones de mecanizado y enfoques de mecanizado. Las siguientes secciones presentarán las metodologías de establecimiento de modelos y la configuración de procesamiento.
Establecimiento del modelo MD
La configuración atómica interna de los materiales cristalinos es diversa, como el cobre (cúbico centrado en la cara), el hierro (cúbico centrado en el cuerpo), el titanio (hexagonal compacto) y el silicio (estructura de diamante) [27, 28]. La mayoría de los materiales cristalinos se encuentran en forma de estructura monocristalina y policristalina. El sólido monocristalino tiene una estructura atómica que se repite periódicamente en todo su volumen sin defectos. Duplicar la celda unitaria en las tres direcciones espaciales puede establecer fácilmente el modelo monocristalino [13]. Al establecer el modelo atómico MD, se deben considerar las diversas orientaciones de la superficie, que pueden influir en las propiedades de mecanizado de la pieza de trabajo [29,30,31]. La estructura policristalina tiene la estructura con diferentes tamaños de grano, que fue construida siguiendo el método de teselación de Voronoi [32]. El material nanotwined (NT) es un tipo de estructuras especiales de policristalino que se ha convertido en objetos de investigación más importantes debido a sus excelentes propiedades mecánicas, como resistencia ultra alta, buena ductilidad y alta tenacidad a la fractura [33,34,35,36]. . En esta revisión, el método para construir NT Cu policristalino se da como ejemplo [25]:primero, se construye una multicapa que consta de múltiples capas de Cu monocristalino de igual espesor y se forma TB entre las capas adyacentes. En segundo lugar, se calcula el ángulo de cada grano. Finalmente, se genera NT policristalino con condiciones de contorno periódicas utilizando la construcción de Voronoi, que acomoda la multicapa y el ángulo de grano obtenido. La Figura 1a presenta las configuraciones atómicas del cobre, incluido el Cu cristalino singular, el Cu policristalino y el Cu policristalino NT, en los que los átomos están coloreados por el vecino común.
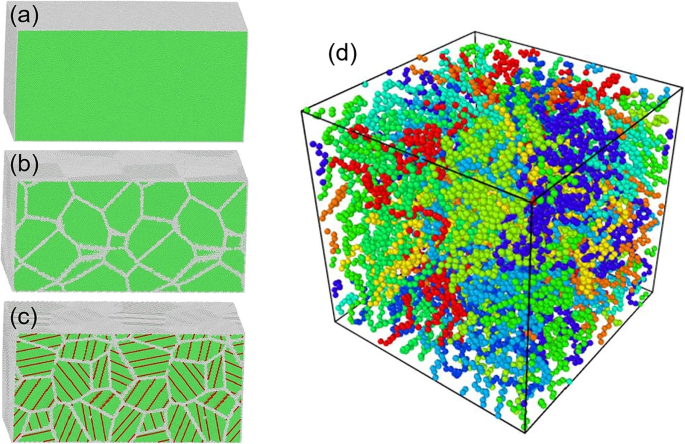
un Microestructura de monocristal de Cu. b Microestructura de nanopolicristalino. c Microestructura de NT policristalino. Los átomos se colorean de acuerdo con los valores de CNA, ya que el verde y el blanco representan FCC y átomos defectuosos [25]. d El modelo equilibrado de átomos unidos de PE amorfo, el modelo fue coloreado por diferentes cadenas moleculares [26]
En estudios anteriores, el polímero se modeló con un modelo genérico de grano grueso [37, 38]. Por ejemplo, los detalles para establecer el modelo de polietileno (PE) se dan de la siguiente manera [39]:(i) el sistema de PE inicial con 10 cadenas moleculares se obtuvo con el uso del algoritmo de paseo aleatorio de autoevitación de Monte Carlo [39]; (ii) el primer átomo de cada cadena se insertó en un sitio disponible de la red al principio y luego la cadena molecular comenzó a crecer a lo largo de una cierta dirección basada en una manera probabilística paso a paso de acuerdo con la longitud del enlace y los sitios desocupados en la célula .; (iii) una vez dada la densidad inicial, se determina el tamaño de la caja de simulación. En nuestra simulación, la dimensión de la caja de simulación inicial era de aproximadamente 80,06 × 80,06 × 80,06 Å 3 para el sistema que consta de 10 cadenas de PE. El modelo MD de PE se muestra en la Fig. 1d.
La geometría de la punta es generalmente compleja y variable, incluida la forma de cono [40], la pirámide triangular [18] y el hemisferio (forma roma) [21], que desempeña un papel importante en el proceso TBN. En particular, la forma de la herramienta piramidal en el modelo MD es consistente con la del proceso de mecanizado AFM y la herramienta esférica es consistente con el grano abrasivo en el proceso de rectificado; por lo tanto, el mecanismo de mecanizado se puede explicar mejor comparando los resultados de la simulación con los resultados experimentales. En la mayoría de los casos, la punta se considera infinitamente rígida, lo que se logra manteniendo constantes las posiciones relativas de los átomos y viajando a velocidad constante [41].
También es fundamental seleccionar las funciones de energía potencial adecuadas que determinen la credibilidad de los resultados de la simulación [21]. EAM es un potencial multicuerpo adecuado para sistemas metálicos [24]. Proporciona una descripción más realista de la cohesión metálica y evita la ambigüedad heredada por la dependencia del volumen, que se emplea para describir la interacción entre átomos metálicos, como el cobre [42] y el hierro [43]. Se ha demostrado que los potenciales de Tersoff [44] y Stillinger-Weber (SW) [45] son los más factibles para modelar materiales con una estructura cúbica de diamante. Para investigar el mecanismo de Si en el proceso TBN, el deslizamiento de dislocación y la transformación de fase deben observarse en simulaciones de MD. En comparación con el potencial de Tersoff, el potencial de SW no solo tiene suficiente flexibilidad para describir una serie de configuraciones de silicio diferentes, sino que también proporciona la coincidencia más cercana a los resultados de nucleación por dislocación ab initio en un silicio libre de defectos [46, 47]. Por lo tanto, la función de potencial SW puede tener más potencial para describir la interacción entre átomos de silicio. Los potenciales de orden de enlace analítico (ABOP), orden de enlace empírico reactivo (REBO) y orden de enlace empírico reactivo intermolecular adaptativo (AIREBO) son una clase de potenciales que amplían la función potencial de Tersoff de acuerdo con la aproximación de enlace estrecho y se basan en cantidades fundamentales [ 48]. El potencial ABOP es ideal para las interacciones entre los átomos de silicio y carbono, que se emplea para investigar la deformación del material y el comportamiento de eliminación en el proceso de SiC. El potencial REBO es particularmente popular en simulaciones de carbono y nanotubos de carbono. El modelo AIREBO fue desarrollado para superar las deficiencias de la función potencial REBO proporcionando una aproximación más precisa que las de los términos REBO y también capacidades adicionales de modelado de interacciones más complejas [41]. Las interacciones intermoleculares e intramoleculares en la muestra de poliestireno se describen mediante el potencial AIREBO bien establecido [49].
La mayoría de las simulaciones de MD se realizaron con el uso de un simulador masivo paralelo atómico / molecular a gran escala (LAMMPS) [50]. Algunos modelos de piezas complejas, como los materiales policristalinos y policristalinos nanotrenados, podrían realizarse con Atomsk [51]. La construcción de polímeros, incluidos átomos, enlaces angulares, impropios y sus diversos tipos, se obtienen del archivo de datos generado por Material Studio (MS) [52]. Tanto Open Visualization Tool (OVITO) [53] como la dinámica molecular visual (VMD) [54] son herramientas útiles para visualizar el modelo o el proceso de mecanizado.
Con el uso de simulaciones MD, se podrían establecer de manera efectiva varios modelos de materiales. Sin embargo, la mayoría de los modelos de piezas de trabajo tienen un tamaño inferior a 50 nm × 50 nm × 50 nm, lo que puede provocar una desviación de los resultados reales [40, 55, 56]. Además, todavía hay una falta de funciones potenciales que podrían describir de manera efectiva algunos materiales como GaAs y Lu 2 O 3 . Por lo tanto, los modelos MD y las funciones potenciales relacionadas aún deben optimizarse para describir el proceso de simulación con mayor precisión.
Configuración de procesamiento
En los experimentos de TBN, el modo de carga controlada generalmente se lleva a cabo aplicando una carga normal constante en la punta. Se ha demostrado que este modo es de mayor precisión, especialmente al realizar nanomáquinas en superficies inclinadas o curvas. Sin embargo, muchas simulaciones MD de procesos TBN se realizan en el modo de controlador de desplazamiento, lo que puede dar lugar a diferencias entre la simulación y el experimento [18, 57]. Por lo tanto, algunos estudiosos han realizado una simulación MD del proceso de nano-rayado controlado por carga aplicando directamente una carga normal constante en la sonda [20, 58]. En los procesos de mecanizado, se puede dividir en tres partes:etapa de relajación, etapa de penetración y etapa de rayado. Además, la punta no es completamente perpendicular a la pieza de trabajo debido a la curvatura del haz del microscopio de fuerza atómica (AFM), el sustrato con un ángulo de inclinación, así como la rugosidad de la superficie de la muestra. Por lo tanto, no se debe descuidar el efecto de la inclinación de la punta. Liu y col. eligió puntas con diferentes ángulos de inclinación para investigar el efecto de la inclinación de la punta en los resultados del mecanizado [59]. Además, el desgaste de la punta es un factor clave para el proceso de mecanizado, que tiene una gran influencia en la calidad del mecanizado. El nano-rayado con lubricación por capa de agua puede reducir el desgaste de la punta para aumentar la vida útil de la herramienta y garantizar la calidad del mecanizado. Sin embargo, el mecanismo de mecanizado afectado por la lubricación por capa de agua todavía no se comprende bien. Para solucionar este punto, Ren et al. utilizó el método de simulación MD para investigar los efectos de la lubricación por capa de agua en los resultados del mecanizado con un cobre monocristalino [60].
Se ha demostrado que el proceso de rayado simple es un método fácil para fabricar nanogroove, pero tiene la limitación en la dimensión de la ranura. Se presentó el método de raspado de múltiples pasadas para aumentar el tamaño del nanogroove [62]. Geng y col. han estudiado la diferencia entre el enfoque de un solo paso y el enfoque de múltiples pasos con simulación MD y resultados experimentales [20]. Tanto los enfoques de un solo paso como los de múltiples pasos se pueden considerar como litografía de arado estático, que se realizan con el modo de contacto del sistema AFM. Sin embargo, la litografía del arado estático puede inducir un desgaste considerable de la punta al realizar un proceso de rayado de larga distancia. La técnica de mecanizado basada en el modo de roscado se denomina litografía de arado dinámico, que tiene el potencial de reducir el desgaste de la punta. La Figura 2 muestra los esquemas de la litografía de arado estática y dinámica sobre cobre monocristalino, respectivamente. Para el arado estático, la punta de diamante primero se alimentó hacia abajo y luego comenzó a arar a lo largo de la dirección negativa de la x eje. Una vez finalizado el arado, la punta se retiró hacia arriba hasta la posición vertical original. Para el proceso de arado dinámico, la punta del diamante se movió a lo largo de una curva sinusoidal con un período y una amplitud pico-valle puntiagudos [19]. Basado en el principio de la técnica de mecanizado basada en el modo de roscado, Sundaram et al. han desarrollado un novedoso método de nanomaquinado utilizando AFM, que se conoce como mecanizado de nanoimpacto asistido por vibración mediante abrasivos sueltos (VANILA). En este método, el AFM se utiliza como plataforma y se inyectan nanoabrasivos en la suspensión entre la pieza de trabajo de silicio y la vibración de la punta del AFM. La energía cinética de los abrasivos es generada por la vibración de la punta del AFM y consecuentemente da como resultado la remoción de material a nanoescala de la muestra [61]. La representación esquemática del proceso VANILA se muestra en la Fig. 2b, c.
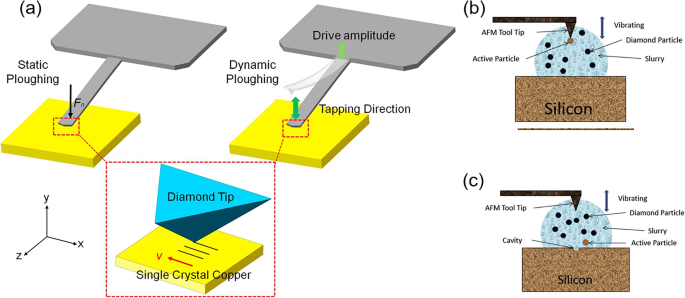
un Los esquemas de la litografía de arado estática y dinámica sobre cobre monocristalino [19]. b La punta de la herramienta AFM golpea una partícula de diamante. c partícula de diamante golpeando la pieza de trabajo [61]
Análisis del resultado de la simulación
Análisis de la fuerza de corte
La fuerza de corte podría reflejar claramente el proceso de remoción de material y el defecto de evolución, que es un parámetro físico importante para comprender el fenómeno de corte [19, 63, 64]. Además, la fuerza de corte está estrechamente relacionada con la potencia de corte y la vida útil de la herramienta, lo que podría proporcionar una guía en el proceso de mecanizado TBN [65]. En el proceso TBN, la fuerza de corte se evalúa principalmente mediante el método de calibración de fuerza, pero la fuerza lateral no se puede obtener mediante este método [66, 67]. Mediante el uso de la tecnología de dinámica molecular, la variación de las fuerzas de corte, incluidas las fuerzas laterales y tangenciales, se puede observar en tiempo real durante todo el proceso [68]. Además, la fuerza media y la fuerza resultante también se pueden recoger mediante el método de simulación MD.
A través del análisis de la variación de la fuerza de corte, se puede reflejar la diferencia de varias estructuras de materiales y la influencia de los parámetros de mecanizado en el proceso TBN. Li y col. encontraron fuerzas más altas para rayar en Cu policristalino en comparación con el monocristal de Cu se atribuye al hecho de que la anisotropía del grano de la superficie tiene poco efecto entre la pieza de trabajo y la punta cuando la punta pasa de un grano a otro grano de diferentes orientaciones del cristal, mientras que el El flujo plástico estable se muestra en la eliminación de material de monocristal de Cu debido a su sistema de orientación única [25]. También se encuentra que la fuerza de corte para diferentes estructuras cristalinas aumenta con el incremento de la velocidad de corte porque una mayor velocidad de nano-rayado produce más virutas [69]. Por el contrario, el cambio de fuerza de corte presenta un comportamiento adverso en el proceso de rayado del SiC, debido a que una mayor velocidad puede generar más átomos de estructura cristalina amorfa, lo que hace que el material de SiC sea más dúctil y más fácil de remover [70]. Yan y col. investigó la procesabilidad de las bicapas de Cu / Ni utilizando el método de simulación MD y encontró que la fuerza de las bicapas de Ni-Cu es mayor en comparación con las de Cu, Ni y las bicapas de Cu-Ni, ya que el movimiento de las dislocaciones fue impedido por la interfase de las bicapas que sirvieron como barrera de propagación [71]. Con respecto a los polímeros amorfos, la propiedad de mecanizado fue influenciada por la velocidad de rayado en tres aspectos diferentes como sigue [72]:en primer lugar, la mayor altura de apilamiento frente a la punta generada a mayor velocidad conduce a una mayor fuerza tangencial debido a más resistencia a la punta. Entonces, una mayor velocidad conduce a una mayor tasa de deformación, lo que puede provocar el endurecimiento por deformación del material. Esto también conduciría al incremento de las fuerzas de corte. Finalmente, con el incremento de la velocidad, el efecto de suavidad térmica permite mecanizar la pieza con mayor facilidad, reduciendo la fuerza tangencial y la fuerza normal. En los procesos de mecanizado de polímeros, las fuerzas de corte aumentan con el incremento de la velocidad, lo que indica que el efecto de endurecimiento por acumulación y por velocidad de deformación juega un papel más importante en la determinación de las fuerzas de rayado. Además de la influencia de los materiales de la pieza de trabajo, la geometría de la punta también juega un papel importante en el proceso de mecanizado [18, 73, 74]. Ren y col. investigó el efecto de los ángulos de la punta sobre las fuerzas de corte con punta en forma de cono. Se encuentra que las fuerzas aumentan con los ángulos de semi-vértice crecientes debido al crecimiento del área de contacto entre los materiales de la punta y la pieza de trabajo [21]. Además, el coeficiente de fricción disminuye fuertemente con el semi-ápice, mientras que la dureza aumenta [75].
Algunos académicos también investigaron la variación de la fuerza de corte en condiciones específicas de mecanizado. Ren y col. analizó la correlación entre el espesor de la capa de agua y las fuerzas de rayado. En la figura 3 se muestra la variación de las fuerzas de rayado con el cambio en el espesor de la capa de agua. la capa de agua más gruesa conduce a fuerzas de corte totales mayores [60]. Además, el efecto de la inclinación de la punta también se analiza mediante el análisis de la dureza (fuerza normal por átomo) y el coeficiente de fricción [59]. Los resultados muestran que la dureza normal es más sensible en la dirección hacia adelante o hacia atrás en comparación y el efecto de la inclinación de la punta lateralmente puede despreciarse. Además, el efecto de inclinación sobre la fuerza normal es la razón principal del cambio del coeficiente de fricción y el efecto de inclinación sobre la fuerza de rayado es mucho menor que el efecto sobre la fuerza normal.
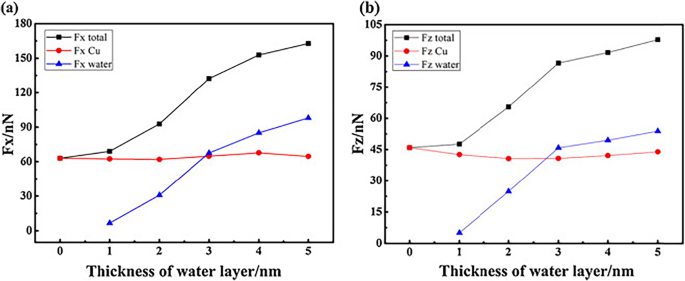
un Variación de las fuerzas de rayado promedio con cambios en el espesor de la capa de agua: a fuerzas tangenciales y b fuerzas normales [60]
Al comparar la fuerza de corte entre el arado estático y el arado dinámico, se puede revelar la diferencia de mecanismo. La fuerza de corte en la litografía de arado dinámico oscila drásticamente con el golpeteo periódico de la punta de diamante, mientras que se observan ligeras fluctuaciones en el arado estático. Además, la fuerza media de mecanizado en el arado dinámico es menor que la mitad de la del arado estático, lo que indica un menor desgaste de la punta en la litografía de arado dinámico [19]. En el proceso de arado dinámico, la orientación de la punta tiene una gran influencia en la fuerza de corte. Yan y col. combinó la profundidad de la ranura y la fuerza de arado para comparar la eficiencia del mecanizado. Los resultados muestran que la cara lateral hacia adelante de la punta tiene la mejor eficiencia, ya que tiene una fuerza de arado similar a la de la orientación hacia adelante de la punta, pero al mismo tiempo más del doble de la profundidad de la ranura [63]. Mediante el análisis de las fuerzas de corte, se pudo explicar con más detalle el mecanismo del proceso de mecanizado TBN con diversos materiales y condiciones de mecanizado. Además, la comparación de las fuerzas de corte en varios modos de procesamiento podría proporcionar una guía para la optimización del proceso del enfoque TBN.
Análisis del estado de eliminación de material
El análisis del estado de la remoción de material también es un método esencial para revelar el mecanismo del enfoque TBN. La eliminación del material y la topografía en el proceso de mecanizado se suelen observar mediante microscopio electrónico de barrido (SEM) y AFM. Sin embargo, la morfología del surco y el estado de eliminación solo se pueden detectar después del procesamiento y el proceso de eliminación de material no se puede entender de forma dinámica. Recientemente, Zhang et al. utilizaron herramientas de corte lineales conectadas directamente en SEM para ver el proceso de formación de viruta en el corte de material, mientras que este método es complicado y SEM debe modificarse [76]. Por tanto, este método es difícil de generalizar. En comparación con el método experimental, el método de simulación MD se puede utilizar fácilmente para explorar el mecanismo de eliminación de material y la generación de superficies en nanoescala, y el proceso de mecanizado se puede observar en tiempo real a través del método MD.
Se sabe a partir de los resultados de la simulación MD del proceso TBN que los estados de deformación se clasifican en estado de arado y estado de corte. Con el movimiento de la punta, los átomos de material de la pieza de trabajo por delante de la punta se aprietan y luego se acumulan para formar la viruta continua durante el estado de corte. Simultáneamente, también se acumulan algunos átomos de material de la pieza de trabajo en los lados izquierdo y derecho de la ranura fabricada después del paso de la punta [57]. Comparando la relación entre el estado de corte y el estado sin corte, podemos determinar si el estado de corte o el estado de arado ocupan la parte dominante cuando se utilizan los distintos radios de la punta para rayar en las diferentes profundidades de rayado [77]. Durante los últimos años, muchos estudiosos han investigado más a fondo las propiedades de los materiales en los estados de eliminación de materiales. Por ejemplo, el material monocristalino muestra anisotropía en el proceso TBN, lo que tiene un gran efecto en la eliminación del material [20]. En comparación con los materiales monocristalinos, los límites de grano tienen un efecto importante sobre las propiedades mecánicas de los materiales policristalinos. Gao y col. encontraron que la orientación del grano más que el tamaño del grano también es dominante en la determinación del perfil del amontonamiento [78]. Además, la geometría de la punta también tiene un fuerte efecto en la eliminación de material. Se seleccionaron tres tipos de punta (cónica, piramidal triangular y punta hemisférica) para revelar el efecto de la geometría de la punta en el estado de eliminación de material. Para la punta cónica, existe una clara dependencia del ángulo de la mitad del vértice. Con un ángulo de punta de medio vértice más grande, aumenta el volumen de viruta y mejora la suavidad de la superficie de rayado, pero requiere una mayor fuerza de rayado, genera un coeficiente de fricción más grande y una temperatura más alta en la pieza de trabajo, y aumenta el daño del subsuelo [40]. Alhafez también investigó el efecto del ángulo de la mitad del ápice en la formación de apilamiento [75]. Se encuentra que cuando se raspa con un pequeño ángulo de la mitad del vértice de la punta, el amontonamiento se acumula principalmente en la dirección de avance, mientras que el amontonamiento lateral domina para la condición de mecanizado del gran ángulo de la mitad del vértice de la punta. Algunos estudios se centraron en la punta piramidal triangular que es consistente con la geometría real de la punta en el proceso de mecanizado basado en AFM [19, 20, 63, 79]. Se compararon principalmente tres direcciones de mecanizado, que son el borde hacia adelante, hacia adelante y hacia adelante. En el proceso de mecanizado de SiC, el estado de eliminación de material se puede controlar simplemente ajustando la dirección de rayado de la herramienta. La dirección de rayado de borde hacia adelante puede proporcionar un proceso más estable, lo que puede dar como resultado una mejor precisión de tamaño y consistencia de las ranuras obtenidas [79]. Sin embargo, el estado de eliminación de material de los polímeros es más sensible a la temperatura en comparación con los materiales metálicos o semiconductores. Durante el proceso de rayado, la temperatura local en la zona de rayado es más alta que la temperatura de transición vítrea, lo que indica que la pieza de trabajo en la zona de rayado se puede quitar de manera dúctil [72]. Zhan y col. investigó los mecanismos microscópicos de fricción del poliestireno amorfo. Descubrieron que la flexibilidad de las cadenas moleculares aumenta con el aumento de la temperatura, lo que puede permitir que las cadenas moleculares se enrollen más fácilmente y vuelvan a su estado original [56]. Du y col. encontró que la velocidad de mecanizado tiene una gran influencia en los resultados del mecanizado del poliestireno. El cambio intracadena domina la deformación permanente de la muestra de poliestireno cuando la velocidad de mecanizado es pequeña, mientras que el deslizamiento entre cadenas es más pronunciado cuando la velocidad de mecanizado es grande [80].
Como se puede ver en la discusión anterior, la mayoría de los estudios se centraron principalmente en la condición seca en lugar de los fluidos. Sin embargo, los átomos acumulados delante de la herramienta se reducen y las rebabas a lo largo de las ranuras no son obvias con un alto espesor de la capa de agua y la rugosidad de la superficie disminuye visiblemente y da como resultado una superficie relativamente lisa. Puede explicarse que la capa de agua actúa como lubricante para reducir la región de adherencia entre la herramienta y la superficie de la viruta recién formada y reduce la fuerza de arrastre exhibida en el límite de la cara de la viruta-herramienta. La consecuencia directa es que la calidad de la superficie mejora enormemente. Con el aumento del espesor de la capa de agua, la calidad de la superficie se puede mejorar gradualmente [60]. En algunos enfoques de mecanizado novedosos, Shockly et al. investigó los efectos de los parámetros (velocidad de impacto, ángulo de impacto y temperatura de funcionamiento) en el mecanizado de nanoimpacto asistido por vibración sobre la formación de nanocavidades y encontró que los parámetros de funcionamiento tienen una influencia sustancial en la profundidad y el ancho de las nanocavidades generadas como se muestra en la Fig. 4 [61]. Xiao y col. encontraron que la profundidad y el ancho de la ranura en el proceso de arado dinámico son más pequeños que los del proceso de arado estático, lo que significa que las nanoestructuras con características pequeñas podrían fabricarse a través de la litografía de arado dinámico. Además, las dimensiones de las ranuras podrían controlarse mediante la relación de amplitud del accionamiento en el proceso de arado dinámico, y esto demuestra que la fabricación de las ranuras también podría ser controlable [19].
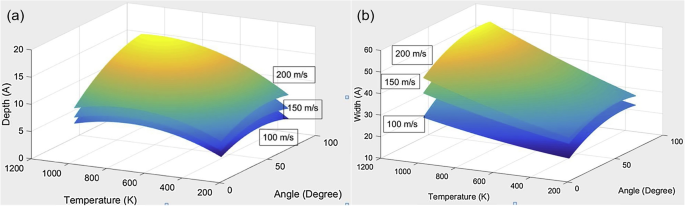
Gráfico de regresión lineal múltiple para a profundidad de la nanocavidad (velocidad de impacto, ángulo de impacto y temperatura de funcionamiento) y b ancho de la nanocavidad (velocidad de impacto, ángulo de impacto y temperatura de funcionamiento) [61]
Durante el proceso de remoción de material, existe un comportamiento de desgaste en la punta. En la mayoría de los estudios anteriores, la punta se define como un cuerpo rígido, lo que significa que el fenómeno de desgaste de la herramienta no se puede observar directamente [13]. Muchos académicos investigaron el desgaste de las herramientas mediante el estudio del estado de remoción de material, la tensión y la distribución de la temperatura [70, 77]. Para reflejar el fenómeno de desgaste real de la punta durante el proceso de mecanizado, Meng et al. fijó la punta como cuerpo deformable y encontró el comportamiento de desgaste de la punta durante el proceso de mecanizado [81]. Los resultados muestran que la forma de desgaste del abrasivo del diamante es principalmente desgaste adhesivo en la etapa inicial y desgaste átomo por átomo en la etapa de estabilidad de procesamiento y la cantidad de desgaste de atribución átomo por átomo del abrasivo se ve menos afectada por la velocidad de corte [ 81]. Es de notar que hay relativamente pocos informes sobre el comportamiento de desgaste de la punta. Con suerte, se espera que el uso del cuerpo deformable de la punta promueva aún más la investigación del comportamiento de desgaste de la punta durante el proceso de nanomaquinado.
El análisis del estado de remoción de material proporciona un soporte efectivo para el monitoreo en tiempo real del proceso de mecanizado. Sin embargo, debido a la limitación de la escala de longitud como se mencionó anteriormente, la morfología de la superficie mecanizada y el proceso de eliminación de materiales solo se pudo analizar mediante comparación cualitativa. It is difficult to predict the accurate processing results.
Defect Evolution Process Analysis
To obtain the information about the defects generated during the scratching process, TEM is usually employed after the FIB sample preparation techniques, which has several disadvantages, such as relatively complicated operation, high cost, and strong material dependence.
The MD simulation method can obtain the defects generated beneath the sample surface easily. Moreover, the defect evolution process during the scratching could also be observed by using the MD simulation approach, which could not be obtained by experimental method. Many available algorithms to extract defect types were presented, including common neither analysis (CNA) [82], centro-symmetry parameter (CSP) [83], slip vector analysis [84], Ackland-Jones analysis [85], etc. However, these methods are not suitable for tracing the propagation of dislocations, especially when a large number of dislocations are generated by tip scratching along certain direction, and we can no longer investigate what is going on inside the specimen using these methods [86]. Chen y col. presented slipping analysis for visualizing the atomic slipping process for material deformation, which could filter out those atoms that have slipped relative to its neighbor atoms during a specified period of time in the condition with large numbers of atoms [86]. By using this method, Xiao et al. investigated the slipping process during dynamic and static ploughing lithography [19]. The relationship between the cutting force and slipping process is shown in Fig. 5. It could be seen that for dynamic ploughing, the sample material mainly flows downwards and sidewards, whereas no obvious downwards material flow is observed in static ploughing process. In addition, the propagation of the dislocation is dependent on the orientation of the tip, leading to the various morphologies of the grooves. Dislocation extraction algorithm (DXA) is also a useful dislocation analysis tool to identify the lattice dislocation and to determine their Burger vector [87]. By using this method, Gao et al. investigated the behavior of the nanoscratching of iron. They found that a distinct reorganization of the dislocation network. At the beginning, the plastic zone grows linearly with the scratching length along the path. Then, the dislocation density decreases rapidly after some length dislocation reactions. Plastic activity then is concentrated only on the scratch front. Only few dislocations remain in the middle of the scratch. Vacancies in this zone are created by dislocation reactions. It is also found that point defects vacancies generated by dislocation reactions and deformation twining [88].
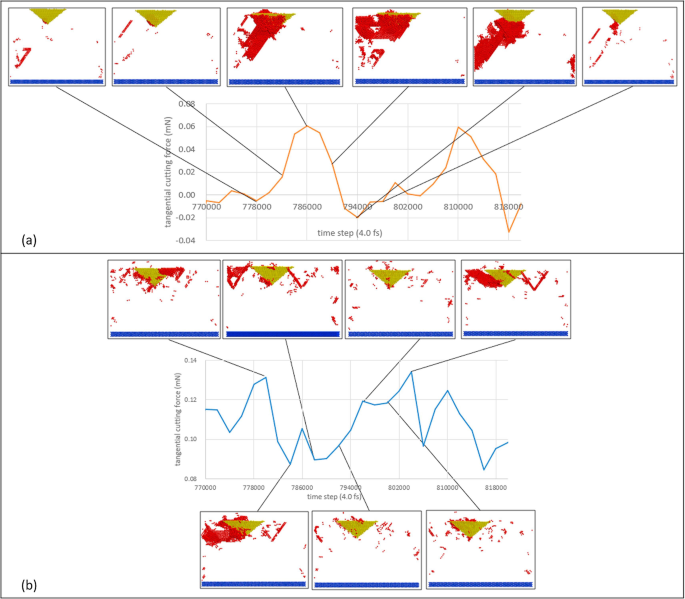
Slipping processes in a dynamic ploughing and b static ploughing [19]
For the polycrystalline materials, the deformation mechanism was mediated by dislocation nucleation within grain interior as well as grain boundary dislocations in polycrystalline material [43]. While the dislocation propagation is associated with the formation of nanovoids and interstitial clusters in the case of larger grain size, and the formation of twins at the grain boundary was dominating for smaller clusters. This behavior was attributed to the transition of dislocation movement from smooth (larger grain) to rough (smaller grain) during scratching process. Li further concluded the difference of material deformation mechanism about single crystal Cu, polycrystalline Cu, and NT polycrystalline Cu. The results show that the plastic deformation is mainly affected by the interaction between dislocations during scratching process in single crystal Cu; while for polycrystalline Cu both dislocations and GB dominate the plastic deformation; and the plastic deformation is controlled by the interactions of the dislocation, grain boundary (GB), and twin boundary (TB) accompanied with twinning/detwinning [25].
Furthermore, many studies focused on the MD simulation of the TBN process on the semiconductor materials, such as silicon, silicon carbide, gallium arsenide, and aluminum nitride. To investigate these brittle materials, phase transformation is also an important deformation mode in addition to dislocation slip [89]. The interaction between dislocation and phase transformation varies with the crystal orientation. The results indicate that prior to the “Pop-In” event, Si (010) undergoes inelastic deformation accompanied by the phase transformation from the Si-I to the Si-III/ Si-XII, which is not occurred in Si (110) and Si (111). While, the phase transformation from the Si-I to the bct-5 is the dominant mechanism of incipient plasticity for each crystallographic orientation, and dislocation nucleation is also an operating deformation mode in the elastic-plastic transition of Si (010). Dai et al. investigated the subsurface damage mechanism on single crystal silicon during TBN process. It is found that the evolution of crystalline phases is consistent with the distribution of hydrostatic stress and temperature [40]. SiC is also a kind of important semiconductor material, which has the similar property as silicon. The SiC material removal process is achieved through the phase transfer from zinc blended to amorphous structure with few hexagonal diamond structures. Higher scratching speed generates more amorphous structure atoms, fewer hexagonal diamond atoms, and fewer dislocation atoms due to larger impaction and less rearrangement time [90]. While Meng et al. found when the phase transition is not the dominant deformation mechanism, the Schmidt coefficient method can effectively predict the sliding motion of 3C-SiC during the TBN process (elastic sliding motion and dislocation slip motion) [79]. Moreover, Meng et al. further studied on the strain rate and heat effect on the removal mechanism of SiC. They found that the strain rate effect and the thermal softening effect directly affect the material removal amount and form of the subsurface damage (SSD). The influence of the thermal softening effect on the stress in the processing region under the condition of high strain rate exceeds that of the decrease in the growth rate of the dislocation generation speed. The polycrystalline SiC removal process is dominated by the amorphous phase transition. Furthermore, several hexagonal diamond structure atoms and dislocations are found in the GBs during the scratching. Higher scratching speed and larger depth of cut promotes more atoms to transfer into the amorphous structure due to larger impaction [81]. Compared with monocrystalline SiC, the microstructure in polycrystalline makes the SiC more soften by generating less normal scratching force and amorphous structure phase transition and thinner plastic deformation induced SSD [91]. Dislocation propagation and phase transition analysis could explain the mechanism in machining process. However, most researches focused on single crystalline materials and the materials with complex structure are rarely reported, which should be further studied.
Future Research Directions and Challenges
At present, the research on the TBN process through MD simulation is widely reported. However, there are still some limitations to be considered. Thus, future directions are discussed in this review.
- (1)
With the development of TBN methods, some novel technologies have been proposed in this field. For example, AFM tip-based nanomilling process has a broad prospect due to its great machining performance and size control properties [92, 93]. However, the mechanism of nanomilling has not been fully understood due to limitation of the detection equipment. With the use of MD simulation, it is hopeful that the variation of the cutting force, the dynamics change of defects, and the removal state of workpiece materials during rotating process of the tip. In addition, sample vibration-assisted nanoscratching method has not been reported yet. MD simulation approach could provide meaningful guidance in the early stage.
- (2)
Due to the limitation of the length and time scales, MD methods still could not fully describe the experimental process quantitatively. In some studies combining experiments and MD simulations, MD simulation approach could only qualitatively explain the experimental phenomena [19, 20, 94]. In particular, for some time-dependent materials such as amorphous polymers, the velocity of the probe has a significant impact on the removal state of polymers. Thus, in order to accurately predict the experimental process and quantitative analyze the experimental results, the improvement of algorithm and computing capability is indispensable.
- (3)
Many nanostructures have been achieved on polymer materials using the TBN method [95,96,97]. In particular, the mechanical machining process of polymer materials based on TBN method keeps the normal load constant so as to guarantee the accuracy of the machined nanostructures [98]. However, the reports of MD simulation of polymer in TBN process are limited until now. Moreover, thermal scanning probe lithography is developing in polymer, which has the potential to improve the machining accuracy of the TBN process. It is necessary to reveal the material removal mechanism of the polymer materials when conducting nanoscale scratching process with the mechanical-thermal effect.
Conclusión
It is undeniable that MD simulations technology plays an increasingly crucial role in nanomachining process to reveal hitherto unknown phenomena [99]. This review concluded the recent progress in MD simulation of TBN method, and the above contents are summarized as follows:
- (1)
The establishment of MD models of various materials and related potential function were summarized. In particular, the modeling process of NT polycrystalline materials and amorphous polymers were discussed in this section. The accuracy of MD models is of great significant to the subsequent simulation results.
- (2)
The new technologies of TBN methods, including multi-scratching, dynamic ploughing, and VANILA were presented. With the help of MD simulation, the mechanism of these methods could be better understood. In particular, the essential difference between static ploughing and dynamic ploughing was revealed by MD method from the aspects of internal defects, morphology and cutting forces.
- (3)
The analysis of MD simulations in TBN process, including the cutting force, the state of material removal, and defect analysis are also summarized. Besides, some novel analysis methods like slipping analysis are also given. With these methods, the processing mechanism based on TBN approach is reviewed, which shows the materials dependence on the TBN machining process.
Abreviaturas
- TBN:
-
Tip-based nanomachining
- AFM:
-
Microscopía de fuerza atómica
- MD:
-
Dinámica molecular
- NT:
-
Nanotwined
- PE:
-
Polietileno
- EAM:
-
Método de átomo incrustado
- SW:
-
Stillinger-Weber
- ABOP:
-
Analytical bond order potential
- REBO:
-
Reactive Empirical Bond Order
- AIREBO:
-
Adaptive Intermolecular Reactive Empirical Bond Order
- LAMMPS:
-
Large-scale Atomic/Molecular Massively Parallel Simulator
- MS:
-
Material studio
- OVITO:
-
Open Visualization Tool
- VMD:
-
Visual molecular dynamics
- VANILA:
-
Vibration-Assisted Nano Impact machining by Loose Abrasives
- SEM:
-
Microscopio electrónico de barrido
- CNA:
-
Common neighbor analysis
- CSP:
-
Centro-symmetry parameter
- DXA:
-
Dislocation extraction algorithm
- GB:
-
Grain boundary
- TB:
-
Twin boundary
- SSD:
-
Subsurface damage
Nanomateriales
- Nano y ánodo de batería:una revisión
- Una revisión sobre la aplicación de biosensores y nanosensores en los agroecosistemas
- Efecto superficial sobre el transporte de petróleo en nanocanales:un estudio de dinámica molecular
- Modelado y simulación de dinámica molecular del corte con diamante de cerio
- El estudio de un nuevo sistema micelar similar a un gusano mejorado con nanopartículas
- Estudio antitumoral de nanogeles de condroitina sulfato-metotrexato
- Estudio del efecto de la dirección de impacto en el proceso de corte nanométrico abrasivo con dinámica molecular
- Estudio de los comportamientos de fricción a nanoescala del grafeno en sustratos de oro utilizando dinámica molecular
- Baja degradación por tunelización de uniones de una sola molécula de alcanos terminados en yodo
- Dependencias de temperatura y presión de las propiedades elásticas de los cristales individuales de tantalio bajo una carga de tracción <100>:un estudio de dinámica molecular
- Un nuevo estudio examina la dinámica y los impulsores de la productividad en la fabricación de EE. UU.