Parte 4 del diseño de piezas moldeadas por inyección:Deformación
Hemos estado hablando de diferentes desafíos y fallas que pueden surgir en las piezas moldeadas por inyección que pueden causar defectos cosméticos, tensiones internas en estas piezas y provocar retrasos en la comercialización, y cómo diseñar piezas moldeadas por inyección para prevenir estos problemas. Un área que hemos mencionado pero no abordada en la urdimbre de piezas moldeadas por inyección después del ciclo de inyección. Esto se debe a un enfriamiento diferencial del plástico en la pieza recién moldeada y puede deberse al grosor variable del material, las características internas o las uniones de las paredes, las relaciones de aspecto de la pieza y el proceso de moldeo por inyección.
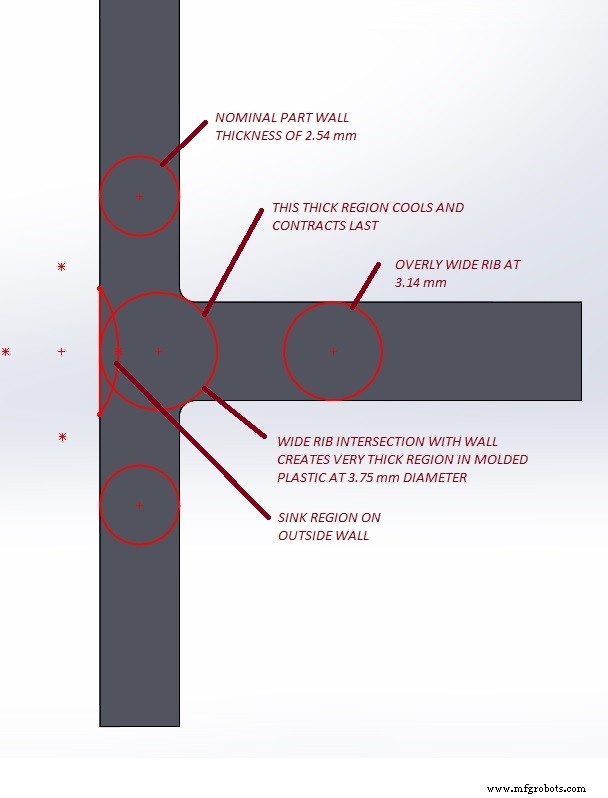
La deformación de las piezas de plástico moldeado por inyección es realmente un desafío y puede ser una sorpresa. Aunque el análisis de flujo del molde utilizando archivos CAD de diseño 3D puede ayudar a predecir esto, existen varios parámetros que afectan la deformación, no solo la geometría de la pieza, por lo que las predicciones no son exactas. A menudo, pequeñas cantidades de deformación prevista pueden terminar siendo más severas ya que las tensiones internas en la pieza de plástico y el flujo frío del material plástico después de la creación de la pieza pueden causar más flexión que no pasará desapercibida cuando se ensambla el producto. Aunque muchos aspectos de ajuste, forma y función de un nuevo diseño de pieza de plástico pueden confirmarse durante las etapas del prototipo, utilizando piezas mecanizadas o impresas, la deformación no se manifestará necesariamente aquí.

Es por estas razones que es clave seguir varias pautas generales para mantener espesores de pared de piezas de plástico relativamente consistentes con transiciones graduales, y seguir las recomendaciones para los tamaños de nervios y salientes, que discutimos recientemente. Sin embargo, esto no siempre es suficiente. Algunos diseños de productos debido a sus funciones o estilos requeridos aún pueden presentar desafíos importantes con respecto a la prevención de deformaciones en las piezas moldeadas por inyección. Las esquinas afiladas, los lados planos muy grandes y las formas de piezas abiertas o no simétricas pueden tener problemas para mantener la forma y el ajuste previstos.
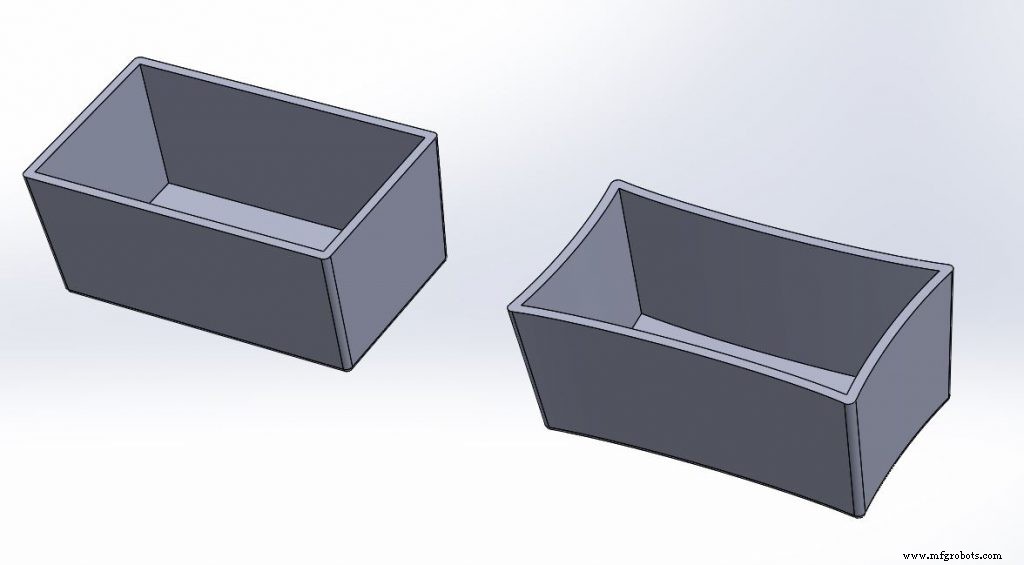
Un defecto de deformación clásico es una pieza de cerramiento de 5 lados con sus paredes laterales deformadas hacia adentro. Aunque la pieza tiene un grosor de pared relativamente consistente en los 5 lados del cerramiento, las esquinas pueden representar secciones más gruesas que pueden enfriarse y encogerse más lentamente, tirando del interior de las paredes de la pieza más que de los lados exteriores.
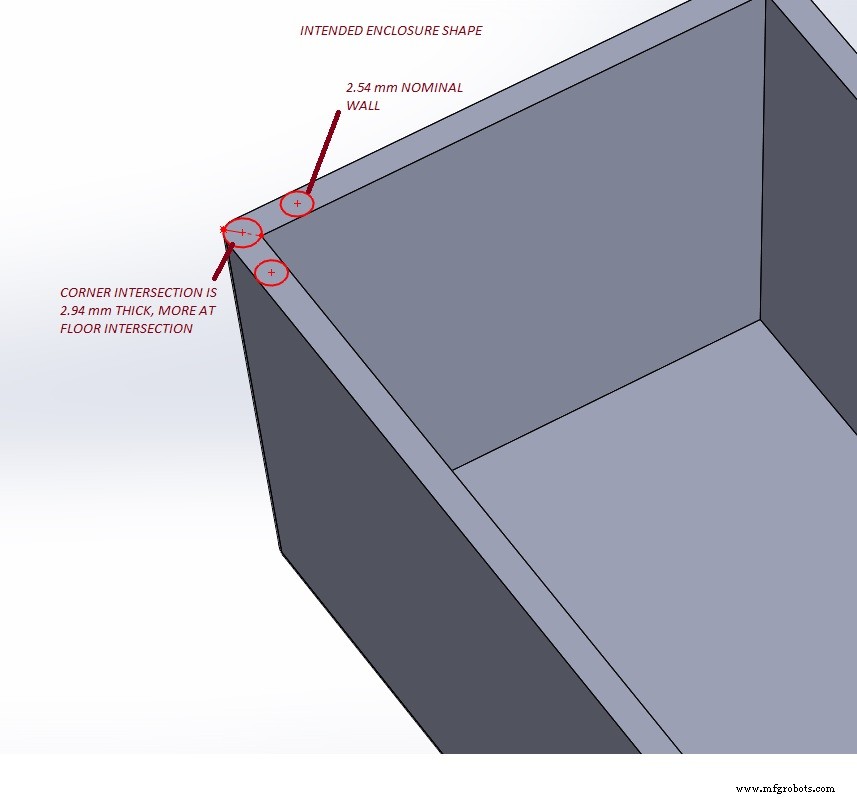
Se debe tener cuidado para tener cuidado en estas esquinas con respecto al grosor o agregar relieves de perforación. Una opción es aumentar los radios de las esquinas en el exterior de la pieza y mantener un espesor de pared común a los radios del redondeo interior.
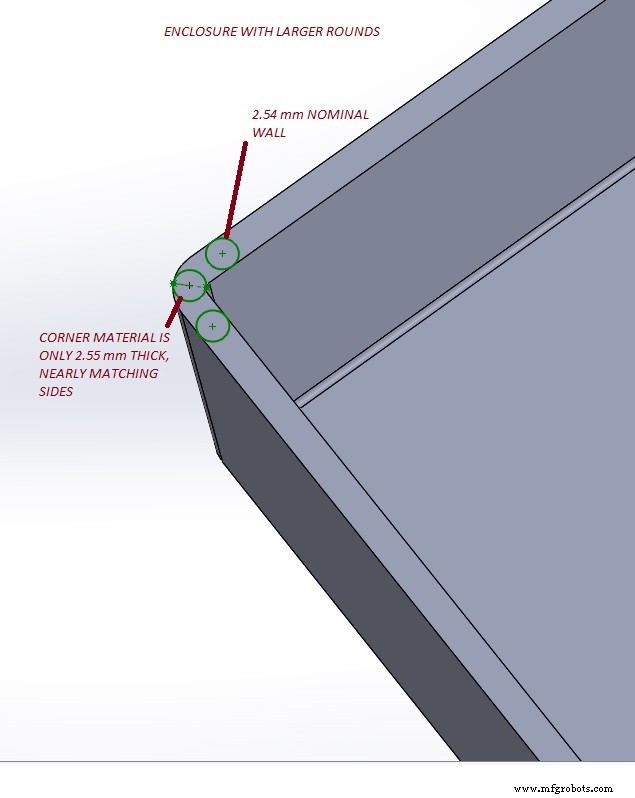
Alternativamente, si se necesita una apariencia de bordes más nítidos en el exterior del producto, las esquinas interiores con núcleo pueden adelgazar localmente el grosor por las esquinas interiores afiladas.
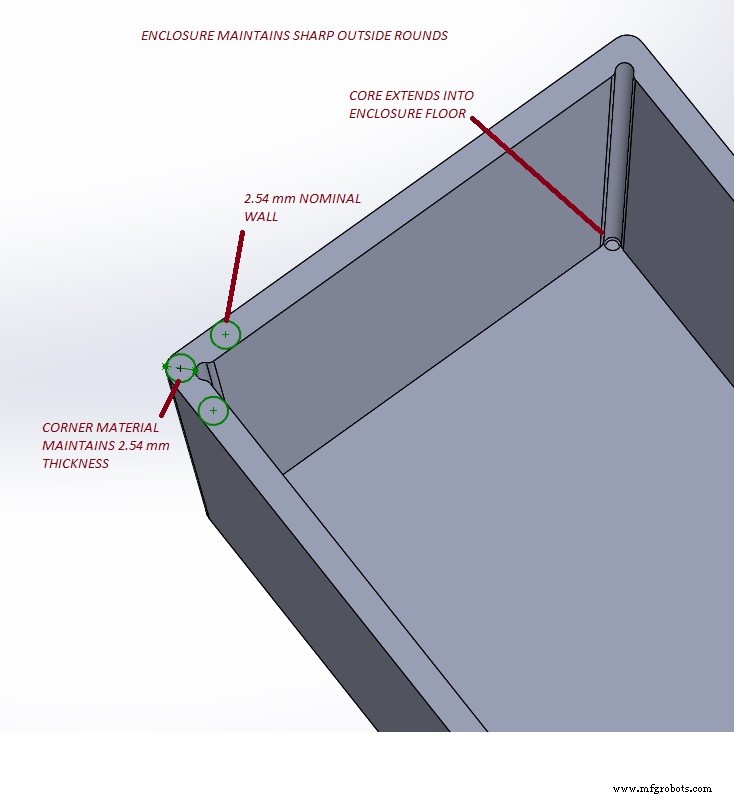
Como se señaló, este enfoque de extracción de núcleos se aplica también a la intersección de las paredes laterales y la pared del piso.
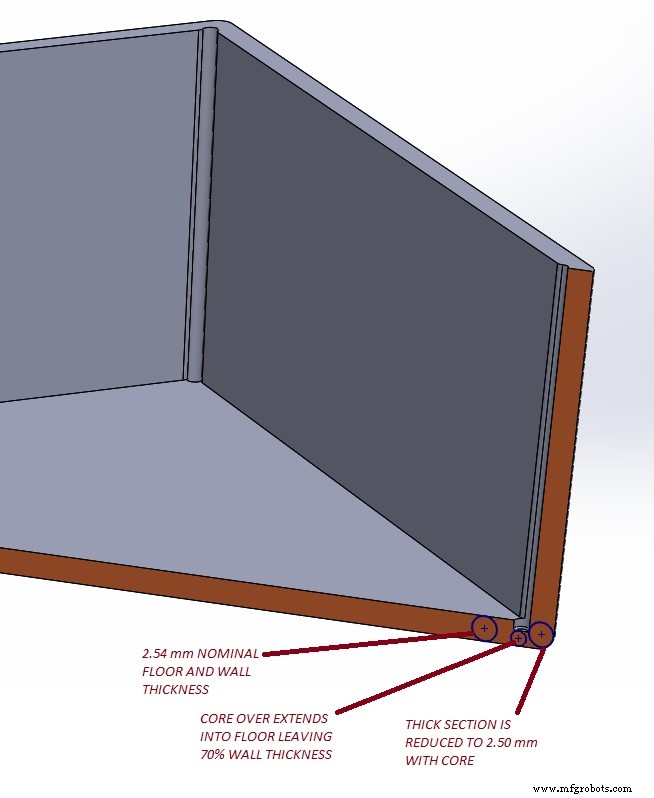
Los productos diseñados con grandes planos planos tienen un aspecto limpio y moderno definido para las empresas que a menudo quieren cambiar su imagen y diferenciarse de la competencia. Pero las piezas de plástico como esta tienen su propio desafío para mantener la planitud en superficies más grandes.
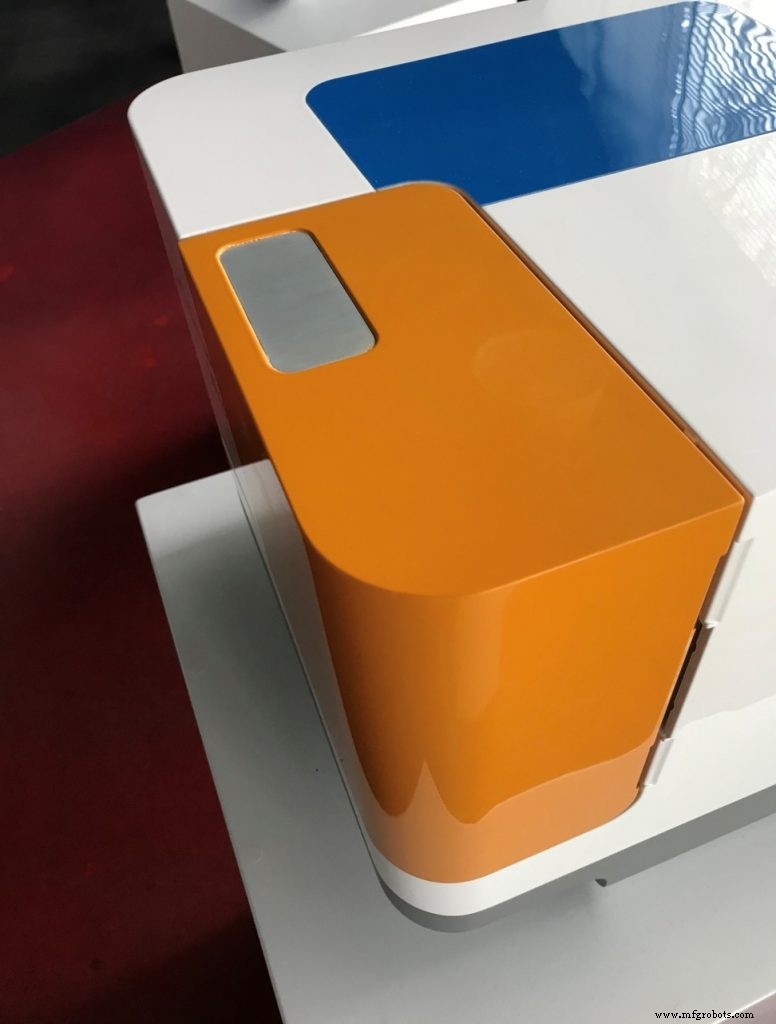
Con un acabado brillante, cualquier pandeo, hundimiento o desalineación se resalta y se nota mucho. El ojo de pez de la luz reflejada puede hacer que las superficies se vean extrañas. Las piezas de la línea de equipos de laboratorio Protein Simple, modelo WES que se muestra, ni siquiera tenían calado para optimizar el aspecto ortogonal que se deseaba. A pesar de que estas piezas se moldearon con plástico de espuma estructural, este proceso solo alivia algunas de las preocupaciones por los fregaderos y la deformación. La clave para obtener piezas perfectas fue diseñarlas con cambios mínimos abruptos en el grosor de la pared y trabajar en estrecha colaboración con el equipo de moldeo para comunicar la planitud requerida y ayudar a diseñar accesorios posteriores a la inyección para evitar deformaciones durante el enfriamiento.
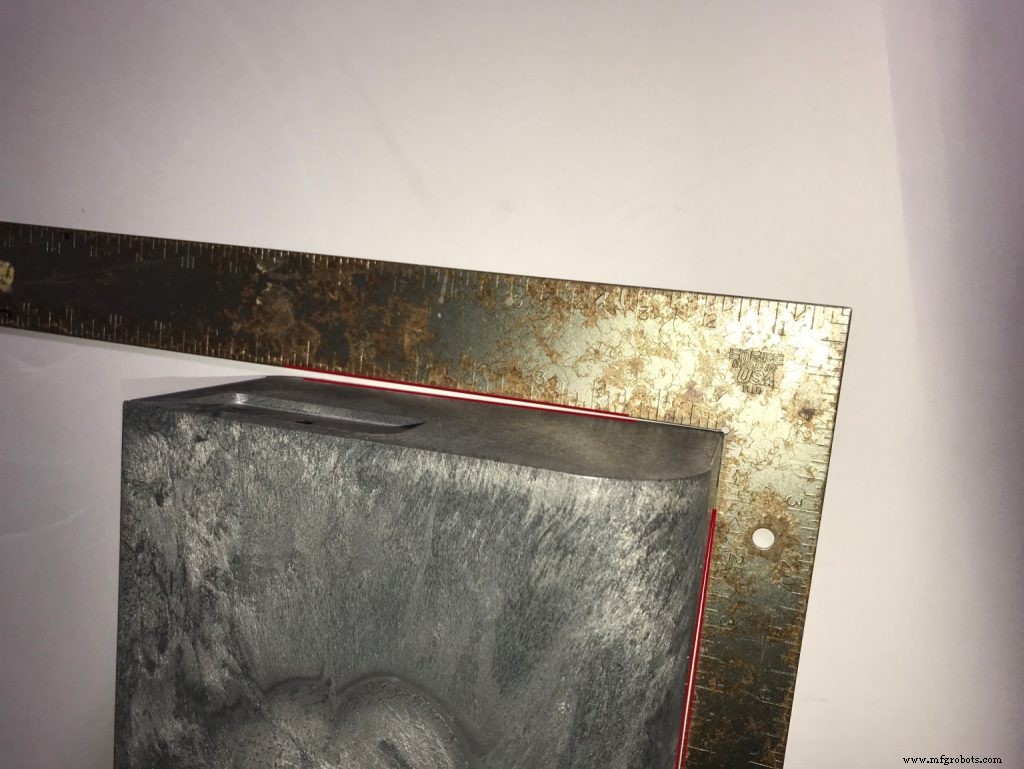
Dado que las piezas se producían en cantidades menores, los accesorios eran una opción viable, pero tenían que diseñarse para lograr los resultados deseados. En muchos casos, un moldeador diseñará sus propios accesorios para cumplir con las tolerancias y las indicaciones de forma en los dibujos de ingeniería. Estos accesorios fueron desarrollados conjuntamente por el equipo de diseño de productos de StudioRed y la casa de moldes.
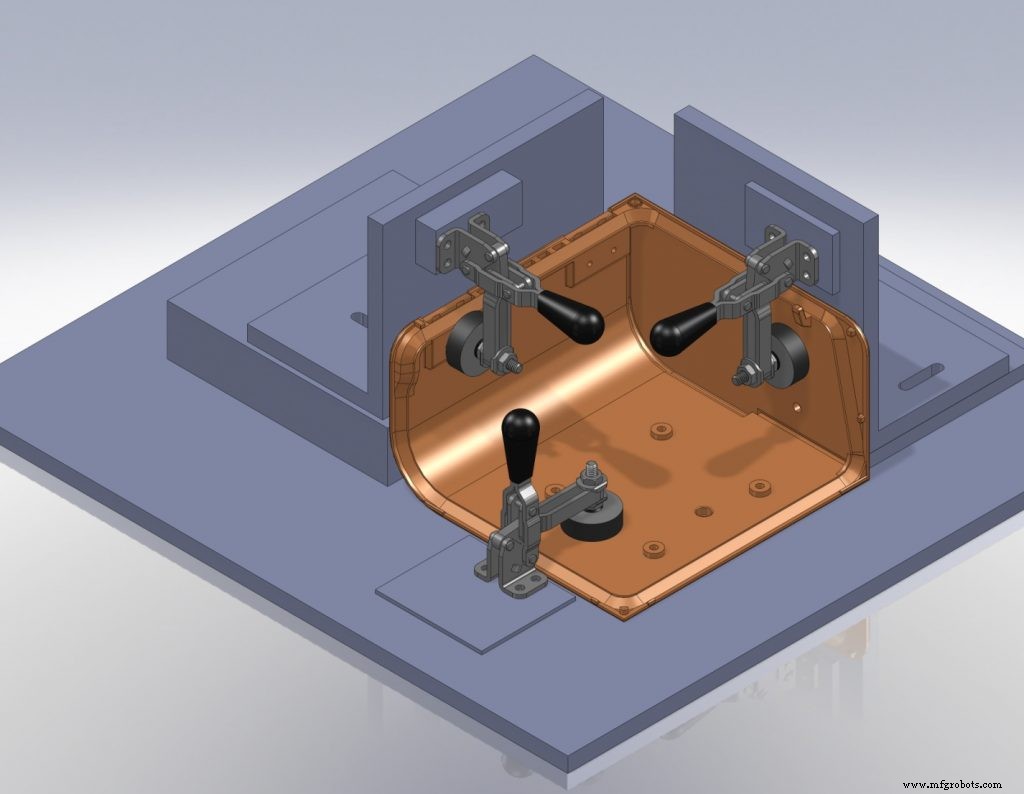
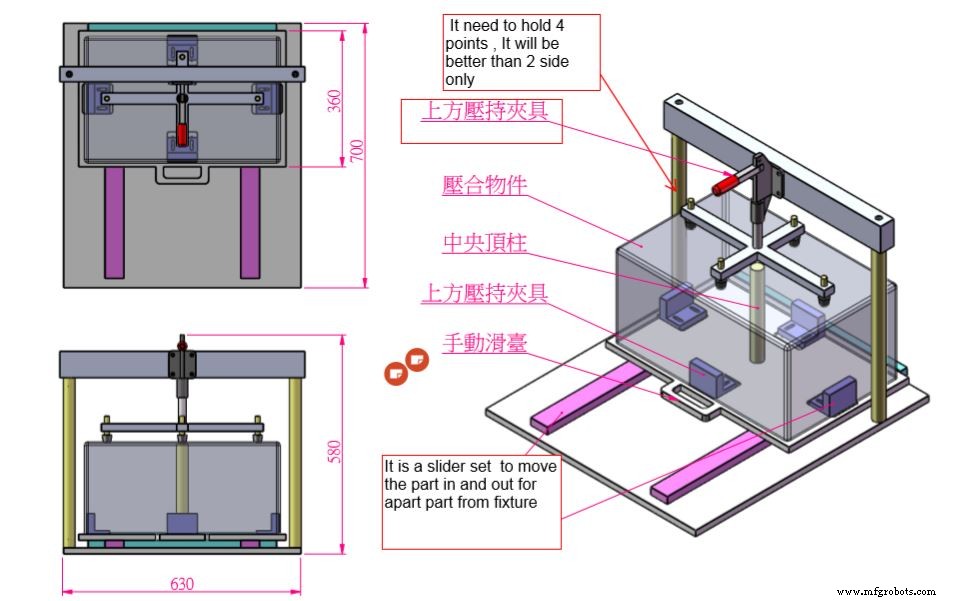
El esfuerzo adicional en ingeniería y el uso de accesorios logró los resultados deseados para la apariencia del nuevo producto de Protein Simple, y a un costo menor que el acabado manual adicional de piezas deformadas. La nueva apariencia no solo fue reconocida por un premio de diseño, sino que también llevó el mensaje de marca deseado al mercado, y las ventas respondieron con un aumento de 6 veces durante el primer mes.
Acabamos de analizar los desafíos del moldeado de plástico donde la planitud y la alineación son cruciales, y cómo las secciones gruesas pueden distorsionar la forma deseada. También hay situaciones en las que una pieza de plástico moldeada por inyección puede diseñarse para tener grandes aberturas o regiones faltantes impulsadas por el ensamblaje, la ruptura de la pieza u otros requisitos funcionales como la ventilación. Estas formas asimétricas y tramos delgados de plástico pueden provocar deformaciones. Este suele ser el desafío con los diseños de bisel para servidores, conmutadores y productos de almacenamiento montados en bastidor.
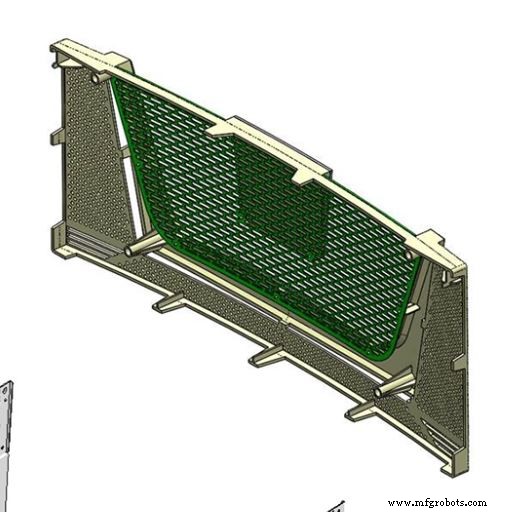
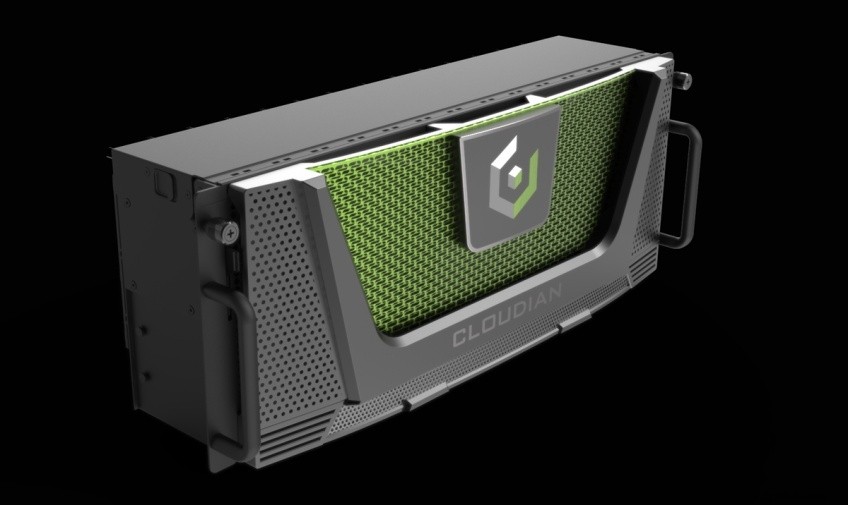
El bisel puede ser clave para proporcionar la marca del producto montado en bastidor y levantarlo por encima de un chasis de metal genérico. Además de proporcionar algo de seguridad y disfrazar las plataformas de hardware de los proveedores OEM debajo.
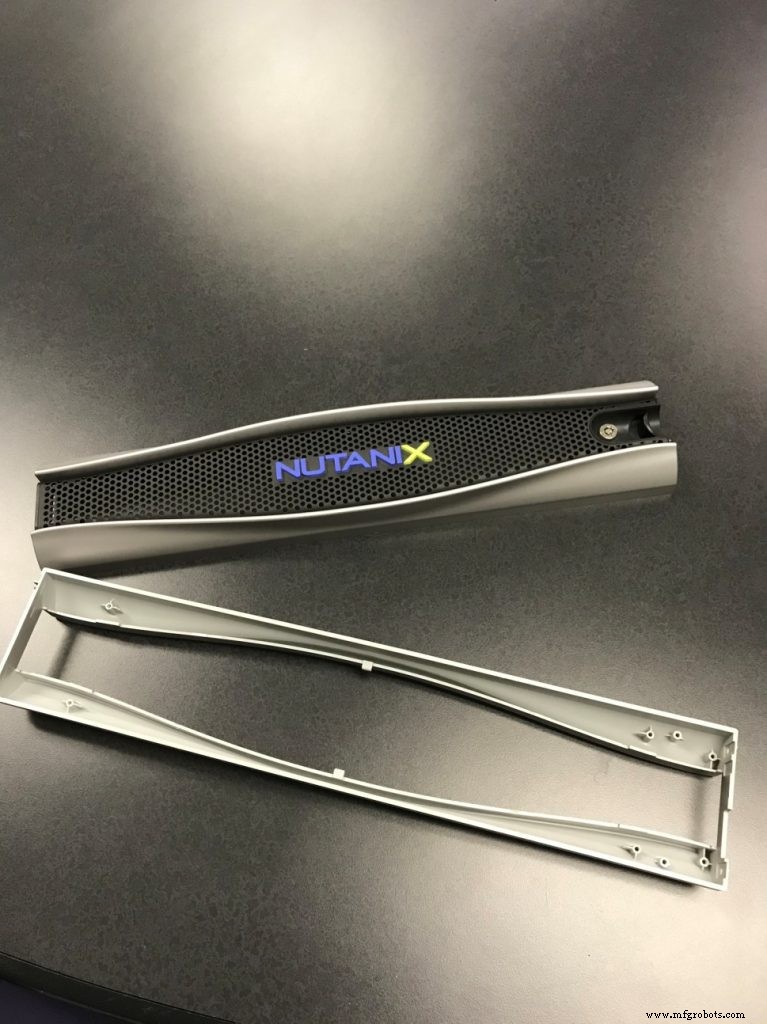
Si la parte moldeada por inyección del bisel se vuelve demasiado delgada o tiene que cubrir aberturas muy grandes para satisfacer las necesidades de ventilación del área abierta, el acceso y otras partes, entonces la parte puede deformarse fácilmente a través de las secciones de puente.
Es posible que la deformación de la pieza ni siquiera se revele hasta que se disparen las piezas de plástico del segundo artículo a medida que el proceso de moldeo se marca más. Pero los problemas de ajuste en el chasis del producto informático pueden notificar las combaduras y las curvas de manera muy visible.
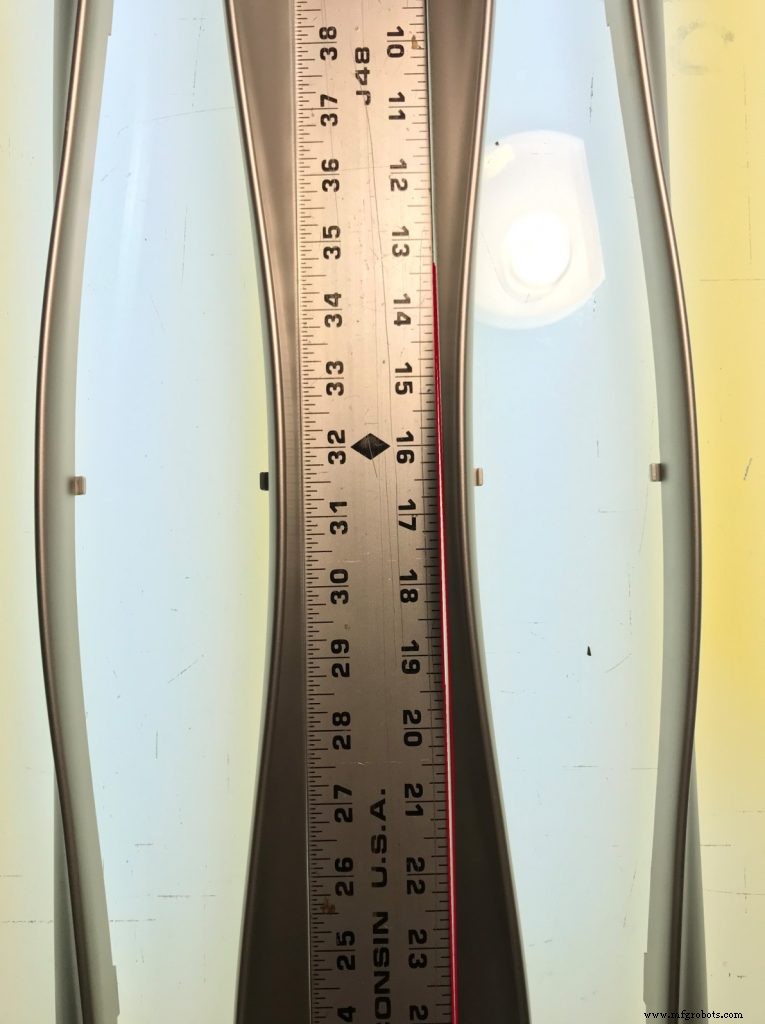
Muchas veces no se puede contar con el soporte estructural adicional de otras piezas, como pantallas de perforación de metal, ya que pueden ser removibles o pueden no formarse con mucha precisión debido a los objetivos de materiales y costos.
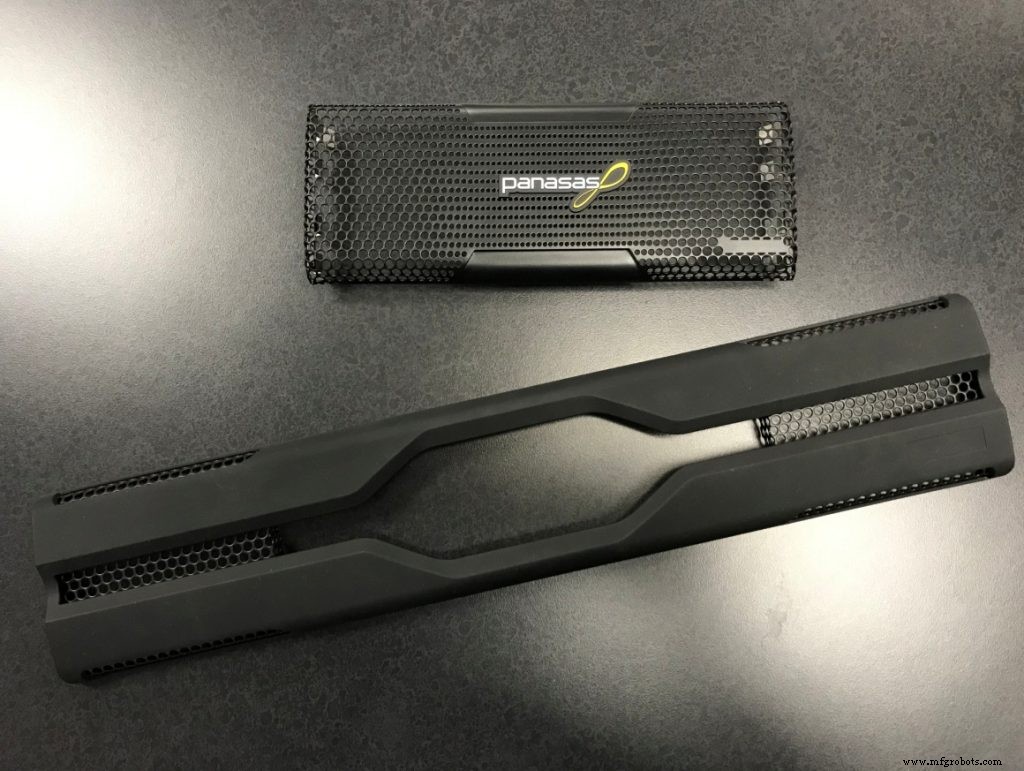
Estos desafíos con piezas de bisel moldeadas por inyección con grandes regiones abiertas a través de las piezas o secciones transversales excéntricas se resolvieron mediante una revisión minuciosa de los espesores del material y las transiciones en toda la pieza, trabajando en estrecha colaboración con el equipo de moldeo, ajustando el proceso y los tiempos de enfriamiento, y agregando post inyección. accesorios para mantener la forma de las piezas de plástico después del moldeado en los casos más extremos.
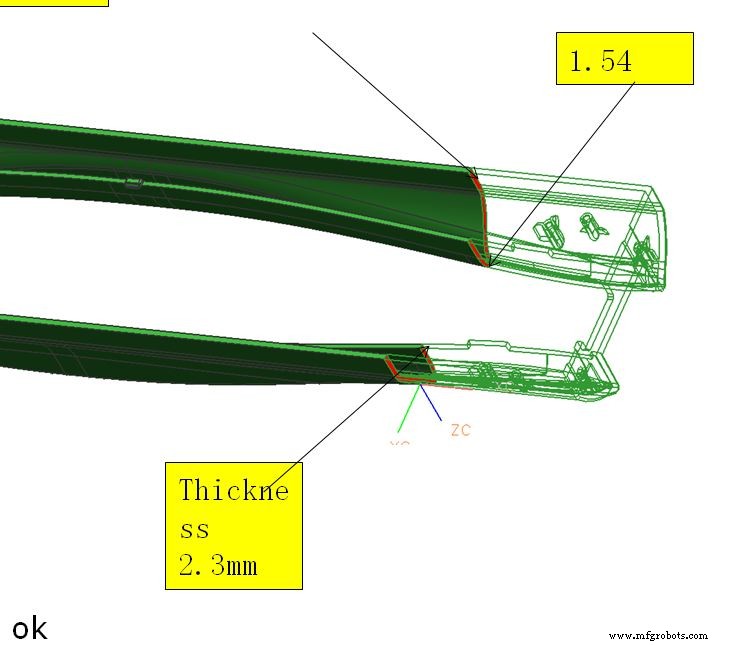
Los resultados fueron componentes de alta calidad que se ajustan bien a varios chasis y proporcionaron definiciones de marca para las empresas que deseaban diferenciarse.
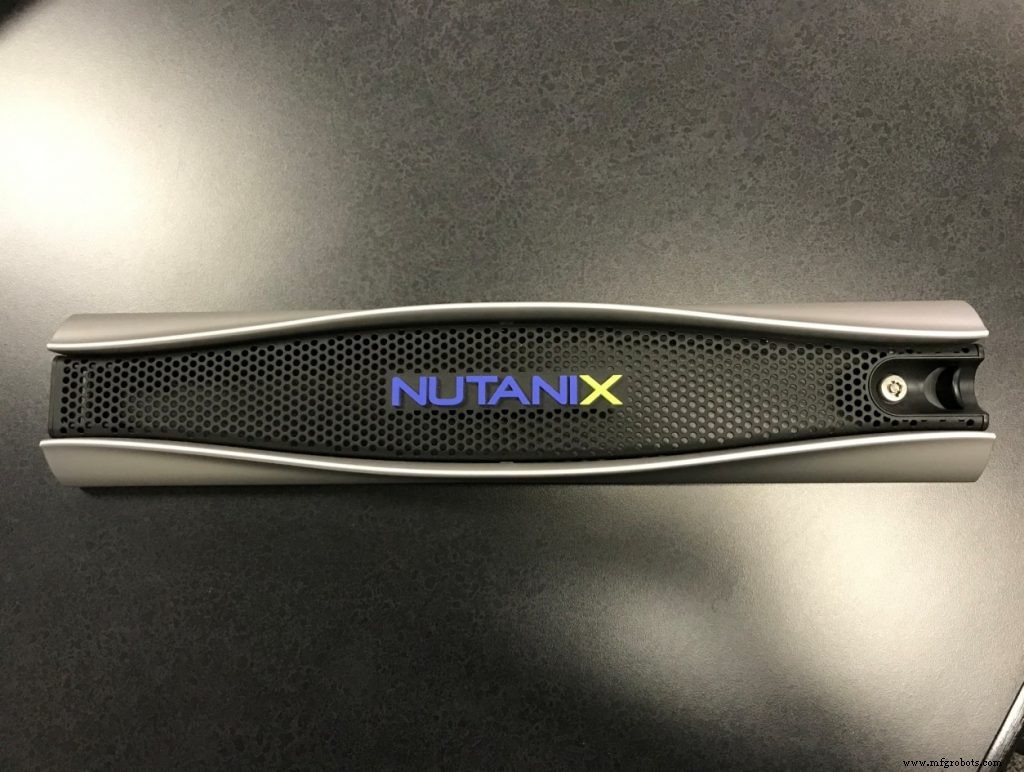
Entonces, aunque la deformación puede ser un desafío para algunos diseños de piezas, incluso una sorpresa durante las primeras tomas del molde, seguir las pautas de diseño básicas sobre los espesores de las piezas y trabajar con el equipo de moldeo puede resolver rápidamente los problemas para producir diseños de productos de alta gama que se ven como se pretendían y funcionan como necesario.
Ver más como este:cortes, marcas de hundimiento, jefes
Proceso de manufactura
- Diseño de piezas moldeadas por inyección Parte 6:Gestión de equipos y fabricantes por contrato
- Diseño de pieza moldeada por inyección Parte 5:Borrador
- Parte 3 del diseño de piezas moldeadas por inyección:salientes
- Parte 2 del diseño de piezas moldeadas por inyección:Marcas de fregadero
- 6 Consideraciones de diseño importantes para la impresión 3D en metal
- Cómo diseñar una pieza compuesta termoendurecible [Infografía]
- Diseño para impresión 3D Parte 3:Reducción del tiempo de impresión
- Directrices de diseño para la fabricación:Parte 2
- Directrices de diseño para la fabricación:Parte 1
- ¿Cuál es el mejor acabado superficial SPI para su pieza moldeada por inyección?
- Consejos de diseño para moldeo por inyección