¿Cuán maduras son las tecnologías de impresión 3D en metal?
[Crédito de la imagen:Laboratorio de Investigación del Ejército de la CCDC]
La impresión 3D de metales abarca una amplia gama de tecnologías, cada una con sus propias ventajas y aplicaciones, así como con su propio nivel de madurez.
Cuando se busca adoptar una tecnología de impresión 3D de metal específica para la producción, es crucial comprender dónde se encuentran actualmente sus capacidades y limitaciones. Sin embargo, cuando se trata de impresión 3D en metal, las empresas enfrentan el desafío de separar la realidad de la publicidad.
Para ayudar a las empresas a evaluar la madurez de las tecnologías clave de impresión 3D en metal más fácilmente, hoy estaremos observando qué tan preparados están para la producción de piezas finales, según un sistema de nivel de preparación tecnológica (TRL), desarrollado por primera vez por la NASA.
¿Qué es exactamente el nivel de preparación tecnológica (TRL)?
Desarrollado por primera vez por la NASA a principios de la década de 1970, el "Nivel de preparación tecnológica" es un enfoque utilizado para evaluar si una tecnología emergente es adecuada para la exploración espacial. En la década de 1990, los TRL se aplicaron en muchas agencias del gobierno de los EE. UU. Y ahora son de uso común en muchas industrias.
El sistema TRL mide la madurez de una tecnología desde el Nivel 1 (Evaluación del concepto) hasta el Nivel 9 (Implementación exitosa) . Cada uno de los nueve niveles demuestra un hito en el desarrollo de la tecnología.
¿Cómo se puede utilizar el TRL para evaluar la madurez de las tecnologías de impresión 3D en metal?
Hemos aplicado este enfoque para evaluar la madurez de las diferentes tecnologías de impresión 3D. Para identificar un TRL para cada tecnología de impresión 3D de metal, hemos analizado su evolución, las industrias que la adoptan, cómo se utiliza hoy y los desarrollos que están dando forma a su futuro.
Notablemente, en algunos casos el TRL puede ser específico de la aplicación. Por ejemplo, la tecnología de deposición directa de energía se encuentra en un TRL 8 para aplicaciones de producción, mientras que sus aplicaciones de reparación han alcanzado el nivel 9.
Según nuestra investigación, creemos que la mayoría de los metales 3D Las tecnologías de impresión han cruzado el TRL 7, que se refiere a pruebas en un entorno operativo para abordar problemas de rendimiento y aplicaciones en prototipos y herramientas funcionales.
Algunas también han demostrado ser exitosas en condiciones normales de funcionamiento (TRL 8) y se encaminan hacia la integración en el ecosistema de fabricación más amplio (TRL 9).
Fusión de lecho de polvo láser

Nivel de preparación tecnológica:8
Laser Powder Bed Fusion (PBF) es una de las tecnologías de impresión 3D de metal más consolidadas. El proceso de PBF metálico implica la aplicación selectiva de un láser potente y afinado a una capa de polvo metálico. De esta manera, las partículas de metal se fusionan capa por capa para crear una pieza.
Los orígenes del PBF metálico se remontan a 1995, cuando el Instituto Fraunhofer de Aquisgrán, Alemania, presentó la primera patente para la fusión por láser de metales. Desde entonces, muchas empresas, incluidos actores establecidos como EOS, Concept Laser (adquirido por GE) y SLM Solutions, ingresaron al mercado de PBF con su versión de la tecnología.
Durante la última década, los fabricantes de impresoras 3D PBF de metal han trabajado arduamente para optimizar la tecnología para la producción. Con este fin, hemos visto a los actores clave del mercado lanzar soluciones para la producción automatizada e integrada.
La mayoría de estas soluciones comparten características similares:son modulares, configurables y ofrecen un alto nivel de automatización en un intento por maximizar la eficiencia y reducir la cantidad de trabajo manual requerido.
Al mismo tiempo, la elección de materiales para PBF se ha expandido continuamente. Por ejemplo, EOS presentó cuatro nuevos polvos metálicos para sus impresoras 3D de metal el mes pasado. Entre ellos se encuentran el acero inoxidable CX, el aluminio AlF357, el titanio Ti64 grado 5 y el titanio Ti64 grado 23.
Gracias a estos desarrollos, el láser PBF se ha abierto camino en muchas industrias y aplicaciones. Una industria que ha estado particularmente interesada en adoptar PBF metálicos es la aeroespacial.
Hoy en día, las piezas de metal PBF impresas en 3D están alimentando sistemas cruciales de aeronaves y naves espaciales, como motores. Aquí es donde las capacidades clave de la tecnología, la producción de piezas complejas con un ensamblaje simplificado y menos desperdicio de material, realmente brillan.
A partir de ahora, la tecnología láser PBF es capaz de entregar piezas funcionales repetidamente. Sin embargo, todavía se requieren algunos ajustes y pruebas antes de que los fabricantes puedan comprometerse con la producción a gran escala. Es por eso que sugerimos que actualmente se encuentra en el Nivel de preparación tecnológica 8.
En el futuro, la facilidad de uso y la confiabilidad de los sistemas PBF metálicos aumentará, impulsada de muchas maneras por los avances en software y en general. flujo de trabajo.
Un ejemplo que respalda esta tendencia proviene del fabricante de impresoras 3D de metal con sede en California, VELO3D.
Al desarrollar su tecnología láser PBF, llamada Intelligent Fusion, la empresa se ha centrado fundamentalmente en la integración de software y hardware. El resultado es un sistema estrechamente integrado que puede imprimir piezas con menos soportes, un mejor acabado de la superficie y, según se informa, una mayor tasa de éxito. Esto, a su vez, conduce a una mayor confiabilidad, una producción más rápida y menos posprocesamiento.
Laser PBF sigue siendo la fuerza impulsora de la industria de la impresión 3D de metal. Las impresoras 3D de Metal PBF tienen la base instalada más grande entre otras tecnologías de impresión 3D de metal. Y los fabricantes de impresoras 3D PBF tienen la mayor participación en el mercado de la impresión 3D de metal en comparación con las empresas que producen otros tipos de impresoras 3D de metal.
Por eso, en primer lugar, se están desarrollando varios materiales para tecnologías de PBF metálicas. Esto significa que la evolución de esta tecnología continuará, impulsada por la demanda de piezas de metal complejas impresas en 3D de alto rendimiento.
Fusión por haz de electrones
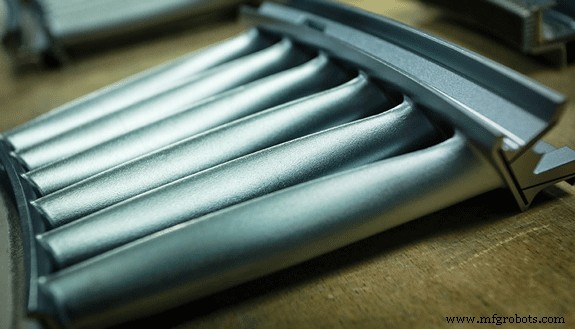
Nivel de preparación tecnológica:8
La fusión por haz de electrones, como el láser PBF, pertenece a la familia de tecnologías de impresión 3D de fusión en lecho de polvo. El EBM funciona de manera similar al láser PBF en que los polvos metálicos también se funden para crear una pieza metálica completamente densa.
La diferencia clave entre las dos tecnologías es la fuente de energía:en lugar de un láser, los sistemas EBM utilizan un haz de electrones de alta potencia como fuente de calor para derretir capas de polvo metálico.
Desde que patentó la tecnología en 2000, la empresa sueca Arcam sigue siendo el fabricante clave de impresoras 3D EBM.
Después de la adquisición de la empresa por parte de GE en 2016, la tecnología EBM siguió evolucionando. En 2018, Arcam lanzó su próxima generación de máquinas EBM, la Spectra H.
La 'H' significa 'metal caliente', lo que significa que puede procesar materiales propensos a agrietarse y a altas temperaturas como el aluminuro de titanio (TiAl) a temperaturas que alcanzan los 1000 ° C.
Arcam EBM Spectra H tiene una serie de características nuevas destinadas a aumentar la productividad y reducir los costos generales.
Por ejemplo, el EBM Spectra H está equipado con una potencia HV de 6kW unidad, que ayuda a reducir los pasos de precalentamiento y poscalentamiento en un 50% en comparación con otras máquinas EBM actualmente en el mercado.
Además, el proceso de estratificación se ha mejorado para reducir las altas temperaturas. Esto permite a los fabricantes ahorrar hasta cinco horas en una construcción de altura completa y aumentar las velocidades de impresión hasta un 50% en comparación con otras máquinas EBM.
La empresa de aviación de GE, Avio Aero, está utilizando 35 Arcam Máquinas:31 máquinas Arcam A2X y 4 máquinas Arcam EBM Spectra H. En Avio Aero, las impresoras 3D se utilizan para producir palas de TiAl para turbinas de baja presión del nuevo gran motor GE9X.
Además de la industria aeroespacial, la industria médica está utilizando ampliamente la tecnología para producir implantes médicos. . El primer uso de EBM para esta aplicación se remonta a 2007.
Fortalecida por los recursos y la experiencia de GE en AM de metales, la tecnología EBM está en camino hacia la industrialización. La tecnología se está aplicando en entornos de producción dentro de industrias altamente reguladas como la aeroespacial y médica. Teniendo en cuenta estas aplicaciones, EBM ha alcanzado el TRL 8.
Deposición directa de energía
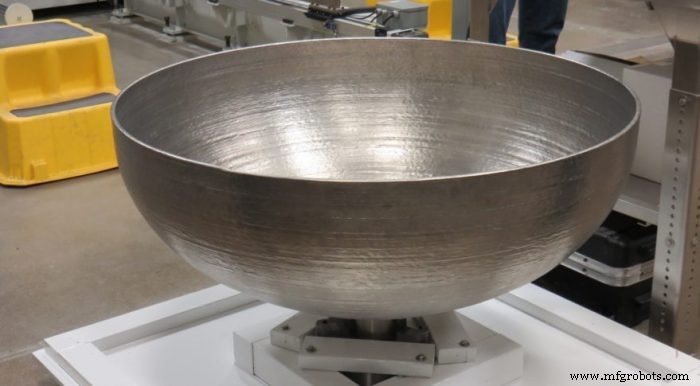
Nivel de preparación tecnológica:8
Con origen en los procesos de soldadura, la Deposición Directa de Energía (DED) implica la fusión del metal con un láser o un haz de electrones mientras el material se empuja a través de una boquilla hacia una plataforma de construcción.
Los sistemas DED utilizan alambre o polvo como materia prima. La mayoría de los sistemas utilizan materiales comerciales listos para usar desarrollados para soldadura o pulvimetalurgia. El uso de materiales disponibles en el mercado tiene muchas ventajas, incluida una selección más amplia de materiales, mayor calidad y menor precio.
Una de las primeras y más exitosas aplicaciones de DED ha sido la reparación de componentes dañados. La tecnología se utiliza para agregar material a las partes dañadas, como álabes de turbina e inserciones de moldes de inyección. Al reparar las piezas desgastadas, DED ayuda a reducir el tiempo de inactividad y los costos asociados con el reemplazo de una pieza, al tiempo que extiende la vida útil de la pieza.
Para permitir el uso de DED más allá de las aplicaciones de reparación, los fabricantes de sistemas DED han estado desarrollando y optimizando soluciones para la producción de piezas metálicas funcionales.
Por ejemplo, Sciaky, uno de los pioneros de la tecnología DED, ha introducido el control de circuito cerrado en sus sistemas de fabricación aditiva por haz de electrones. El sistema de monitoreo de procesos de Sciaky combina imágenes ópticas en tiempo real con visión artificial para medir el tamaño, la forma y la temperatura del baño de fusión.
Basado en los datos obtenidos de la imagen, un sistema de control de circuito cerrado luego da comandos de ajuste al software que controla la potencia del haz, la velocidad de alimentación del alambre y el movimiento de la máquina. Gracias a esto, la repetibilidad del proceso se puede mejorar sustancialmente.
La tecnología DED ya se ha aplicado en múltiples aplicaciones aeroespaciales y de defensa. Los ejemplos incluyen cúpulas de tanques de combustible de titanio para satélites, piezas estructurales de titanio para el Boeing 787 Dreamliner y piezas de repuesto para vehículos militares.
La tecnología se ha establecido como una solución de mantenimiento fácilmente disponible. Con esta aplicación, DED se sitúa en TRL 9.
Cuando se trata de aplicaciones de producción, DED también se puede utilizar como herramienta de fabricación. Sin embargo, se necesitan más desarrollos en términos de avanzar en el control del proceso y mejorar la resolución de impresión.
A partir de ahora, la tecnología produce formas casi netas, que necesitan un mecanizado sustancial para lograr la especificación de la pieza y un buen acabado superficial. La mejora de la resolución de impresión permitirá a los fabricantes reducir el tiempo y el costo necesarios para el mecanizado secundario.
Inyección de aglutinante metálico
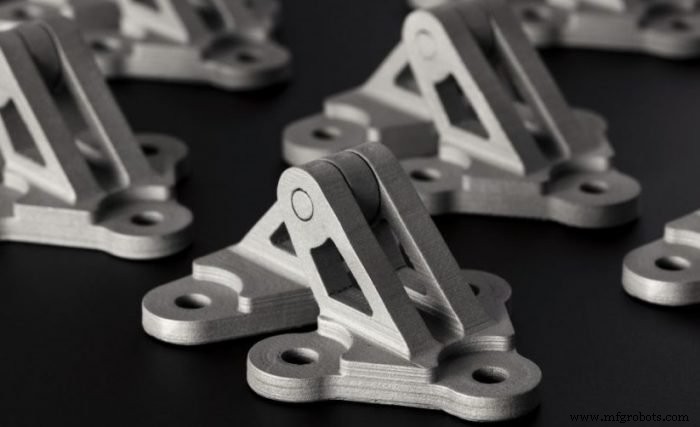
Nivel de preparación tecnológica:varía
Metal Binder Jetting está evolucionando rápidamente hacia una tecnología de fabricación muy prometedora. Sin embargo, el nivel de preparación de la tecnología varía mucho entre las tecnologías de inyección de aglutinantes metálicos en el mercado actual.
El chorro de aglutinante metálico se desarrolló por primera vez en 1993 en el MIT. El proceso de impresión comienza esparciendo una fina capa de polvo, con los cabezales de impresión depositando estratégicamente gotitas de aglutinante en el lecho de polvo. El proceso se repite capa por capa hasta que la pieza está completa, con el polvo no utilizado (alrededor del 95%) reciclado.
ExOne, que ha estado licenciando la tecnología del MIT desde 1996, siguió siendo la única empresa que ofrecía metal. servicios y sistemas de inyección de aglutinante hasta principios de la década de 2010. Los sistemas de inyección de aglutinante de metal de ExOne se utilizaron en gran medida para crear prototipos y herramientas de metal.
Sin embargo, a medida que las patentes de inyección de aglutinantes metálicos comenzaron a expirar, la competencia se intensificó, lo que alentó a la empresa a comenzar el desarrollo de soluciones a nivel de producción. La última, la impresora 3D X1 25PRO, se lanzó comercialmente hace unos meses.
Otro gran actor en el mercado de inyección de aglomerantes metálicos es Digital Metal. Sus impresoras 3D DM P2500, introducidas por primera vez en 2017, han producido más de 300.000 componentes en diversas industrias, incluida la aeroespacial, artículos de lujo, herramientas dentales y equipos industriales.
También hay algunos recién llegados al campo del chorro de aglutinante de metal, incluidos HP y Desktop Metal.
Después de presentar su tecnología Multi Jet Fusion para piezas de polímero en 2016, HP presentó la próxima extensión de sus ofertas de aditivos en 2018:un sistema de impresión Metal Jet 3D. Con un nuevo sistema, HP busca poner la tecnología en un entorno de producción de alto volumen.
Para lograr esto, la empresa ha equipado su sistema con más boquillas y ha introducido un agente aglutinante innovador. Combinados, se informa que estos avances hacen que el proceso de impresión sea más rápido y sencillo.
La tecnología detrás de la impresora 3D de Desktop Metal es lo que la compañía llama Single Pass Jetting (SPJ), una versión más rápida del proceso típico de inyección de aglutinante. La empresa afirma que su sistema puede imprimir hasta 12.000 cm3 / h, lo que se traduce en más de 60 kg de piezas metálicas por hora.
Curiosamente, el sistema de producción Metal Jet y Desktop Metal de HP comparten un valor algo similar proposición. Ambas máquinas basadas en chorro de aglutinante buscan interrumpir la fabricación tradicional al permitir una mayor velocidad y escalabilidad.
Si bien el sistema de producción de Desktop Metal se lanzó a principios de este año, la tecnología de HP está programada para su lanzamiento en 2020 y actualmente solo está disponible a través del servicio de producción HP Metal Jet.
Es cierto que muchas de las tecnologías de inyección de aglomerantes metálicos han aparecido solo recientemente. Significa que necesitarán algo de tiempo para demostrar que están listos para aplicaciones de producción en serie a través de más pruebas, ya sea internamente o en el sitio del cliente.
Con un historial en aplicaciones de producción, las tecnologías más antiguas, como las de Digital Metal y ExOne, se encuentran entre los niveles de preparación tecnológica 7 y 8. Esperamos que las tecnologías más recientes de inyección de aglutinantes de metales alcancen y superen el TRL 8 en los próximos años.
Los sistemas de inyección de aglutinantes metálicos continuarán evolucionando en un intento por abordar los mercados que desafían la penetración de otras tecnologías de impresión 3D de metales, incluida la producción de bienes industriales y automotrices de mayor volumen. Esto crea muchas oportunidades de crecimiento interesantes para esta tecnología en el futuro.
Deposición de metales ligados
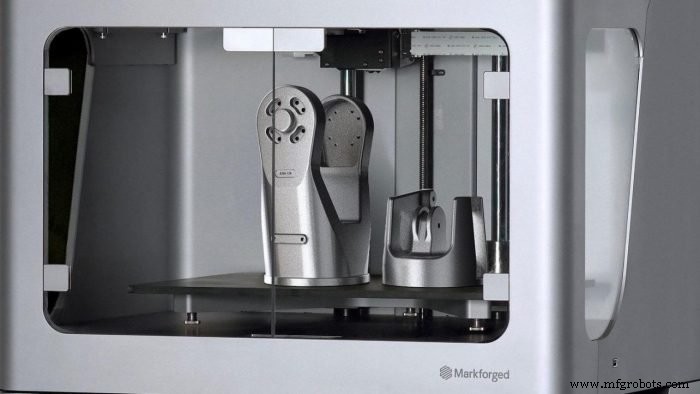
Nivel de preparación tecnológica:7
Bound Metal Deposition es un recién llegado al espacio de fabricación aditiva de metales. La tecnología funciona de manera similar a la Fabricación de filamentos fundidos (FFF), donde un filamento se calienta y se extruye a través de una boquilla, creando una pieza capa por capa. Sin embargo, a diferencia de los filamentos de plástico utilizados en FDM, la extrusión de metales utiliza filamentos hechos de polvos metálicos o gránulos envueltos en aglutinantes de plástico.
Las dos empresas más destacadas que trabajan en esta área son Markforged y Desktop Metal. Ambas empresas presentaron por primera vez sus sistemas de impresión 3D de metal (Metal X de Markforged y Studio System de Desktop Metal) en 2017.
Actualmente, la tecnología se utiliza en gran medida para crear prototipos de metal y herramientas de forma más rápida y económica.
Un ejemplo es Dixon Valve &Coupling Company, un fabricante y proveedor de accesorios para las industrias de transferencia de fluidos. La empresa ha utilizado Metal X de Markforged para imprimir mordazas de agarre en 3D. Estas herramientas son esencialmente abrazaderas, que están montadas en un brazo robótico que agrega anillos de sellado a los acoplamientos de acero.
La producción de tales herramientas toma 14 días y cuesta $ 355. En comparación, la impresión 3D de una pinza de metal cuesta $ 7 y requiere 1,25 días para completarse, una reducción de más del 90% tanto en el costo como en el tiempo de entrega.
Si bien la tecnología de deposición ligada está logrando grandes avances en el costo- prototipos eficaces y acelerar el tiempo de comercialización, su uso en el lado de la producción sigue siendo limitado. Por un lado, estos sistemas se posicionan como impresoras 3D de metal compactas, que pueden ser difíciles de escalar.
Sin embargo, a medida que más empresas adoptan la tecnología, especialmente para ubicaciones remotas como plataformas petrolíferas, es posible que veamos más ejemplos. de piezas de repuesto y de uso final creadas mediante deposición de metal enlazado en los próximos años.
Innovando con la impresión 3D en metal
La mayoría de las tecnologías de impresión 3D de metal han alcanzado niveles de preparación tecnológica bastante altos, lo que significa que son adecuadas para aplicaciones de producción.
Obviamente, queda mucho trabajo por hacer, especialmente en la mejora de la economía y la velocidad de las tecnologías de impresión 3D en metal. Actualmente, los procesos de lecho de polvo, DED y el chorro de aglutinante metálico son considerablemente más costosos que los sistemas de fabricación convencionales.
Los sistemas de deposición de polvo ligado de menor costo brindan cierta accesibilidad a la impresión 3D de metales y podrían ofrecer un buen punto de entrada para las empresas más pequeñas.
En última instancia, el avance de la tecnología en sí es solo una pieza del rompecabezas. Es igualmente crucial que el ecosistema en torno a la impresión 3D en metal continúe evolucionando. Esto puede implicar el desarrollo de una solución de software mejor integrada y más fácil de usar, la automatización de las operaciones de posprocesamiento y la creación de flujos de trabajo optimizados.
Solo juntando todas las piezas, hay una manera de lograr una innovación significativa de procesos y productos con la impresión 3D de metal.
Impresión 3d
- Cómo se diseñan los modelos de objetos para la impresión 3D
- Cómo se utilizan los puentes en la impresión 3D
- ¿Cómo puede la impresión 3D beneficiar a la fundición de metales? Aquí hay tres formas
- Impresión 3D en metal:¿Dónde estamos hoy?
- ¿Qué grado de madurez tiene su industria en la adopción de la impresión 3D? [Infografía]
- 10 emocionantes tecnologías de impresión 3D que han surgido en los últimos 12 meses
- Cómo las impresoras 3D de escritorio están transformando la impresión 3D
- AM en todo el mundo:¿Qué tan madura es la impresión 3D en la región de Asia y el Pacífico?
- Cómo evolucionará el mercado de hardware de impresión 3D en 2020
- ¿Cuán sostenible es la impresión 3D industrial?
- Comprender las tecnologías de impresión 3D