Entrevista con el experto:Vicepresidente de asociaciones tecnológicas de VELO3D para ampliar las capacidades de la impresión 3D en metal
La impresión 3D de metales puede ser una tecnología innovadora, pero no está exenta de desafíos. Es un proceso que requiere consideraciones de diseño que requieren mucho tiempo, procesamiento posterior y cierto grado de prueba y error para lograr una impresión exitosa. En un intento por resolver estos y otros desafíos asociados, la empresa con sede en California, VELO
3D
, presentó su impresora 3D de metal Sapphire basada en láser el año pasado.
Como resultado de cuatro años de desarrollo, la impresora Sapphire cuenta con dos elementos clave:su tecnología Intelligent Fusion ™ y el software de preparación de impresión Flow. Las dos funciones funcionan de la mano para permitir beneficios potencialmente revolucionarios, como una repetibilidad mejorada e impresiones sin soporte. Esto último, en particular, es posible gracias a la capacidad de la impresora Sapphire para imprimir voladizos extremos sin la necesidad de estructuras de soporte.
En la entrevista de expertos de esta semana, estamos hablando con Zachary Murphree, vicepresidente de tecnología Asociaciones en VELO
3D
, para discutir el valor de su tecnología Intelligent Fusion ™, sus aplicaciones más atractivas y lo que sigue para el sector de AM de metales.
¿Podría contarme un poco sobre VELO? 3D ?
VELO
3D
se fundó con el objetivo de ampliar las aplicaciones para la fabricación aditiva de metales.
Parte de lo que motivó la fundación fue la frustración en torno a la fabricación aditiva que nuestro fundador, Benny Buller, experimentó al intentar fabricar piezas para la producción. Metal AM no estaba cumpliendo algunas de las promesas que se habían hecho, como la complejidad sin costo y la aceleración del proceso de desarrollo del producto.
Hay algunos puntos importantes de conversación en torno al metal AM que no son del todo ciertos. Parte de nuestro objetivo es eliminar esa frustración y ampliar la gama de aplicaciones para que metal AM realmente cumpla sus promesas.
Para lograr este objetivo, echamos otro vistazo al proceso para comprender la física fundamental del mismo. Al comprender completamente el proceso, hemos desarrollado un sistema que puede imprimir cosas que antes se consideraban no imprimibles y expandir la gama de geometrías que pueden considerarse rentables para la fabricación aditiva.
Así es como desarrollamos nuestros dos productos clave:la impresora de metal Sapphire y el software Flow. Estos dos productos conforman el sistema que permite la impresión 3D de piezas que no se pueden producir con ningún otro sistema.
VELO 3D salió del modo sigiloso con la impresora Sapphire el año pasado y presentó la empresa públicamente en la Feria Internacional de Fabricación. ¿Qué valor aporta su sistema al mercado?
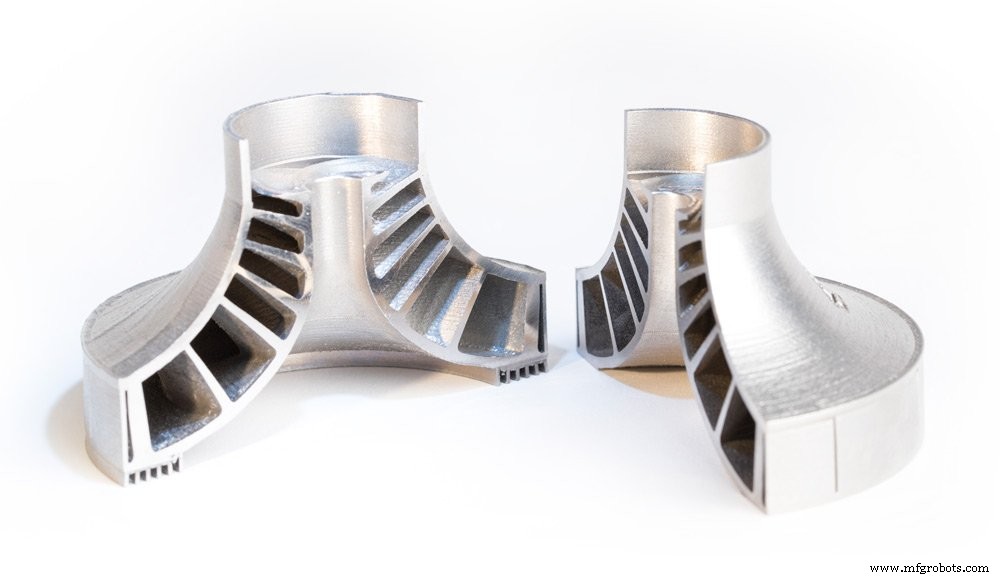
Una de las cosas importantes que tratamos de enfatizar es que nuestra tecnología no es solo el hardware físico. La impresora Sapphire es la parte más visible de nuestra solución, pero es solo un componente. Para permitir que el sistema haga lo que puede hacer, se requiere nuestro software de preparación de impresión Flow. El proceso no se puede ejecutar en otros sistemas; realmente tuvimos que desarrollar el hardware desde cero para habilitar los procesos que estamos ejecutando.
Esta combinación nos permite lograr una fabricación sin soporte, que se reduce al control de procesos. VELO
3D
se ha centrado en eso desde el principio. Al controlar el proceso y ejecutarlo en una ventana muy estrecha, podemos imprimir piezas en voladizos de muy bajo ángulo sin soportes.
¿Cómo funciona la tecnología?
El proceso comienza con la geometría CAD. Trabajamos con la geometría CAD subyacente y no con formatos de archivo teselados como un archivo STL. El archivo CAD se importa primero a nuestro software de preparación de impresión Flow.
El software le permite orientar la pieza y colocar los soportes, algo similar a lo que se puede hacer con algunas de las soluciones de software existentes. Pero lo que es diferente aquí es que nuestro software Flow es muy consciente de los procesos. El hecho de que se haya desarrollado conjuntamente con el hardware significa que es un sistema muy integrado.
El software también puede predecir factores como cuándo se deformarán las piezas o cuándo se producirán fallas de soporte durante la construcción, y puede proporcionar retroalimentación sobre la orientación y los soportes incluso antes de que comience la impresión.
También tenemos una función de corrección de deformaciones que nos permite deformar previamente la geometría para que la pieza que salga de la máquina al final de la impresión tenga la geometría correcta. Este es un software de simulación térmica.
La parte final del software de preparación de impresión es la asignación de parámetros. Esto, nuevamente, está estrechamente integrado con el hardware para que podamos definir los parámetros de la trayectoria de la herramienta de una manera muy específica para la geometría de una pieza. Estos parámetros tienen muchos más matices que los que se obtienen con algunos de los sistemas convencionales de fabricación aditiva de metales.
Todo esto junto le brinda un archivo de impresión que incluye gran parte de la inteligencia del proceso. Por eso llamamos a nuestra tecnología Intelligent Fusion.
La impresora Sapphire está diseñada para ejecutar esas instrucciones de construcción de una manera muy controlada. Gran parte del éxito que tenemos se basa no solo en controlar la atmósfera, la cámara, el lecho de polvo y el flujo de gas de manera muy ajustada, sino también en el proceso en sí.
Una de las cosas que tenemos en el sistema es un sistema de control de piscina de fusión de circuito cerrado que nos permite alcanzar las temperaturas objetivo para que el proceso sea exitoso. También tenemos un repintador sin contacto que nos permite fabricar piezas de formas que no se pueden hacer en otros sistemas.
¿Podría ampliar los desafíos específicos que está resolviendo su tecnología?
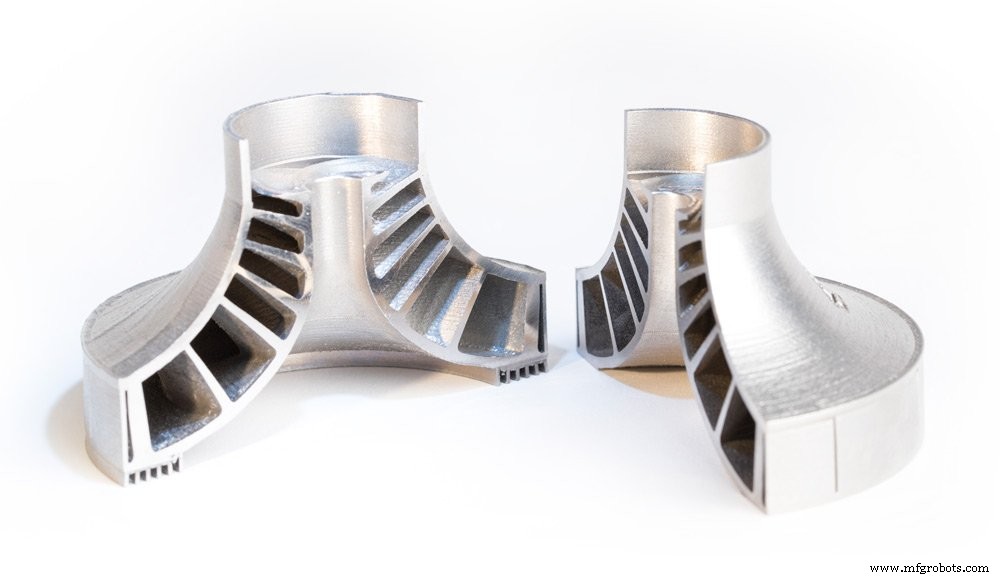
Al hablar con los clientes, definitivamente he visto que los ingenieros están interesados en utilizar AM de metal como técnica de fabricación.
Pero a pesar de ser una industria de treinta años, todavía hay mucho de inmadurez en la forma en que se fabrican las piezas, especialmente cuando se compara con los métodos de fabricación establecidos.
Cuando imprime piezas, a menudo es difícil conseguir que se puedan imprimir en primer lugar. Mucho de eso se reduce a las restricciones geométricas. El mayor ejemplo de esto es la regla estándar de los 45 grados, cuando no puede imprimir voladizos sin soporte que estén a menos de 45 grados de la horizontal. Si bien este es el estándar, la gente lo ha estado presionando un poco más bajo. Dependiendo del material y la máquina, puede llegar a 40 o 35 grados.
Si bien ha habido algunas innovaciones, esta sigue siendo una restricción bastante fundamental. Significa que a menudo hay que colocar soportes en lugares donde será muy difícil, si no imposible, quitarlos después.
Si observa una voluta para la carcasa de una bomba o una carcasa de turbo, que es una parte de forma toroidal con apariencia de rosquilla hueca, los soportes en el interior significan que no es un buen candidato para metal. SOY.
Los impulsores cubiertos son otro desafío. Durante mucho tiempo, la gente ha querido, pero realmente ha luchado, imprimir esas partes.
En el ámbito de las turbinas de gas, tienes blisks, álabes y venas del estator que son buenos candidatos para el aditivo, pero la cantidad de soportes que tienes que agregar para imprimirlos con éxito hace que AM no sea un ideal. solución. Si no fuera por eso, estas piezas serían un buen candidato para la impresión 3D porque son bastante difíciles de fabricar con otros métodos.
Entonces, empujando los límites del diseño con la capacidad de imprimir hasta 5 -10 grados sin ningún soporte con un buen acabado superficial, estamos habilitando muchas aplicaciones diferentes.
¿Cómo coloca su tecnología junto con otras tecnologías de impresión 3D en metal?
Depende de lo que estés haciendo. Hay aplicaciones que ahora tienen bastante éxito en metal AM. Quizás sería beneficioso usar VELO
3D
tecnología sin soporte para acelerar la producción. Pero al final del día, hay personas que están imprimiendo piezas realmente buenas en otros sistemas.
Así que creo que en términos de aditivo, definitivamente hay espacio en la mesa para muchos jugadores diferentes. Cuando se compara el tamaño de la industria AM con el tamaño de la industria manufacturera tradicional, tenemos mucho espacio para crecer antes de que se convierta en un mundo de perros come perros.
Si bien pensamos que nuestra tecnología puede reemplazar muchas de las tecnologías actuales, eso no significa que no haya espacio para otras también.
¿En qué industrias ve las mayores oportunidades de crecimiento para VELO? 3D ?
Como era de esperar, la industria aeroespacial es una industria clave porque ha sido uno de los primeros en adoptar la impresión 3D. El razonamiento es bastante claro:hacen una fabricación de alto valor, tienen piezas que son caras de fabricar y tienen muchas complejidades geométricas, por lo que pueden beneficiarse de la AM de metal.
Y la industria aeroespacial es enorme. Existe la propulsión, que se puede descomponer en turbinas de gas o en aplicaciones que no respiran aire, como los motores de cohetes, que es otra aplicación realmente buena. A continuación, tiene aeroestructuras, componentes estructurales reales, en estructuras de aviación y satélites en el espacio
También hay muchas aplicaciones en el lado electrónico, particularmente alrededor de envolventes y componentes de radiofrecuencia. Los intercambiadores de calor son otro componente que puede resultar difícil de fabricar de forma tradicional, dependiendo de la geometría. Entonces, en el sector aeroespacial, hay mucho que perseguir.
Luego está la oportunidad para AM de metal en aplicaciones industriales, principalmente porque es algo similar a la aeroespacial. Aunque no son tan valiosas, las aplicaciones pueden incluir componentes de potencia de fluidos u otros tipos de piezas de bombas, colectores e intercambiadores de calor.
¿Cuáles son algunos de los mayores puntos débiles que ve cuando los clientes se comunican con usted?
Los mayores desafíos están relacionados con las geometrías que se pueden imprimir.
Otra gran cosa que la industria necesita abordar para ser más ampliamente aceptada es la variación de parte a parte. Si eres un ingeniero que diseña piezas para metal AM y son componentes críticos, debes tener un gran impacto en los permitidos de tu diseño para poder usar aditivos metálicos.
La razón de eso es que la consistencia del material que sale del sistema no es necesariamente la que usted desea que sea. Debe diseñar para la parte más débil que pueda obtener, lo que significa que no está aprovechando completamente algunas de las capacidades de AM, especialmente cuando se trata de aligeramiento o mejora del rendimiento. Debes tener muchos márgenes integrados en tu parte.
Una de las cosas que también estamos tratando de abordar con nuestro sistema, y con muchas de las capacidades de metrología incorporadas, es la parte a parte, construcción a construcción y variación de máquina a máquina, así como las propiedades mecánicas de la pieza final.
Eso es algo que abrirá muchas puertas porque todavía hay dudas sobre el uso de AM de metal, y las personas no están 100% seguras de lo que van a sacar al final del día.
¿Qué consejo le daría a las empresas que quieran adoptar la tecnología AM de metales, pero que no saben por dónde empezar?
Hay diferentes motivaciones detrás de la adopción de la tecnología AM. Algunas personas tienen un impulso corporativo para simplemente adoptar AM de metal. Pero eso no es necesariamente algo que lleve a casos convincentes de aditivos metálicos.
Creo que es realmente importante tener una razón convincente para necesitar aditivos metálicos. Muchas veces las empresas dirán:“¿Qué pasa si hacemos exactamente la misma pieza con aditivo metálico? ¿Cómo hacemos las comparaciones de costos? ¿Lo ponemos todo en una matriz y averiguamos cuál es la más rentable? " Eso no significa necesariamente aprovechar todas las ofertas de aditivos metálicos.
Cuando se trata de eso, el metal AM es otra herramienta en la caja de herramientas de fabricación. Necesitas tener dolor para hacer la transición. Por lo tanto, debe tener una pieza que necesita hacer, o que tiene dificultades para hacer con alguna otra técnica de fabricación, o necesita más funcionalidad del producto final que requiere que diseñe nuevas funciones y nuevas geometrías.
¿Cómo describiría el estado actual de la industria de AM y cómo cree que evolucionará en los próximos cinco años?
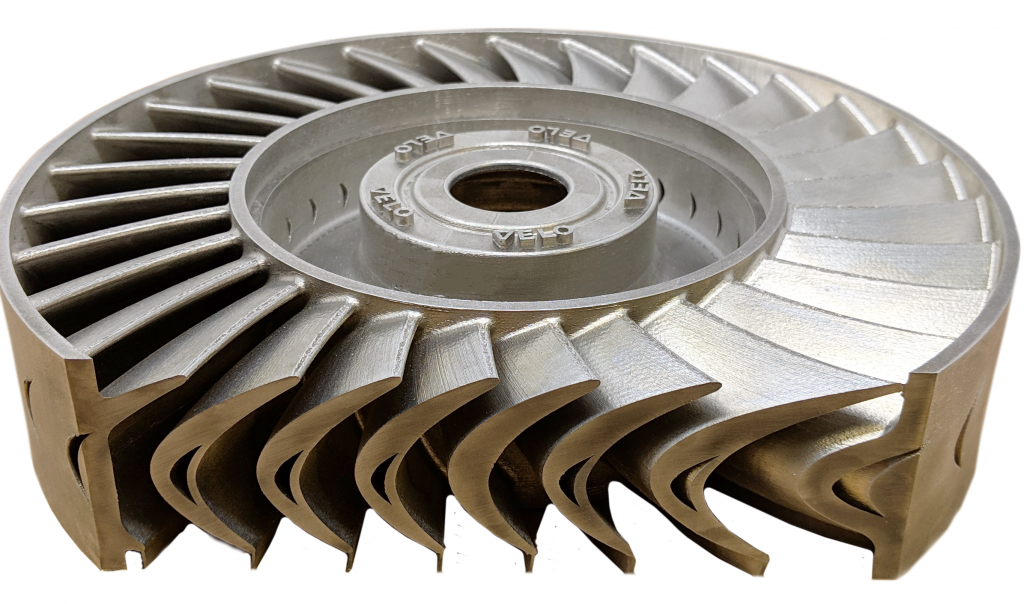
Metal AM está madurando. Hay algunos casos claros de empresas que han entrado en producción con éxito. Estamos llegando a un punto de inflexión y la cantidad de piezas que realmente van a producirse está aumentando.
Dentro de cinco años, verá muchos fabricantes por contrato que se han ampliado considerablemente y tienen cientos de estos sistemas en su piso, produciendo piezas con contratos de producción a largo plazo. La industria ha estado trabajando para lograrlo durante mucho tiempo.
La gente está ganando confianza en el aditivo metálico como solución. VELO
3D
‘s La tecnología jugará un papel importante en eso porque nuestro objetivo es acelerar la producción y brindarle a la gente confianza en la calidad de una pieza que sale al final de la impresión.
Con esas dos cosas combinadas, puede comenzar a incorporar bastantes aplicaciones más que pueden ser cuestionables hoy, pero que realmente podrían ser buenas candidatas para AM.
¿Hay tendencias en particular que le entusiasmen?
Hay bastantes tendencias interesantes que vemos.
Un área que me entusiasma particularmente es el mercado espacial, específicamente alrededor de cohetes y satélites pequeños.
Hay innovadores empresas que están iterando rápidamente y tienen ciclos de desarrollo rápidos. Buscan piezas finales de alto valor bien alineadas con las capacidades de VELO
3D
‘s Sistema de zafiro. Es un mercado que se está adoptando rápidamente y está previsto que crezca en una cantidad bastante considerable.
La otra gran cosa es que el mercado tiene muchas adyacencias y también se alimenta del mercado aeroespacial más tradicional. Estas empresas más pequeñas y más rápidas pueden resolver algunas de las cosas en los próximos cinco años que atraerán a los principales contratistas de defensa y empresas aeroespaciales.
Cómo es el desarrollo de materiales en VELO 3D ? ¿Hay planes para ampliar aún más su cartera de materiales?
Ahora mismo estamos imprimiendo en Inconel 718 y Ti64. Intentamos estar orientados al cliente, por lo que nuestro futuro desarrollo de materiales estará impulsado por casos comerciales sólidos.
Existen sólidos argumentos comerciales en torno a otros titanios y aluminio, pero no necesariamente los mismos materiales que ofrecen otros fabricantes de metal AM. Queremos abordar las necesidades específicas de los clientes y responder a lo que pide el mercado en lugar de a lo que es necesariamente posible hoy en día.
VELO 3D se ha asociado recientemente con Praxair. ¿Qué significa esta asociación para ti?
Hemos tenido una relación realmente excelente con Praxair Surface Technologies. Son uno de nuestros proveedores de polvo certificados.
Estamos tratando de asegurarnos de que nuestros clientes tengan acceso a materia prima de alta calidad y Praxair es absolutamente un proveedor de eso. Con ellos, estamos trabajando en el desarrollo de nuevas aleaciones y asegurándonos de que nuestros clientes estén satisfechos con las aleaciones que obtienen de sus proveedores.
¿Cuál ha sido la reacción de sus clientes desde su lanzamiento?
Ha sido positivo. Definitivamente tengo la sensación de que nuestros clientes están entusiasmados cuando ven la amplitud completa de lo que estamos abordando aquí, y cómo nos hemos propuesto resolver muchos de los problemas que existen con el software y el hardware en torno a metal AM. . Eso habla de ser una empresa orientada al cliente:comprender los desafíos que enfrentan nuestros clientes y desarrollar soluciones para mejorar sus vidas.
En general, me encanta ofrecer recorridos aquí en VELO
3D
, porque la respuesta es siempre muy entusiasta y la gente parece estar muy emocionada de empezar a utilizar la tecnología y llevarla internamente.
Por último, ¿cómo será el 2019 para VELO? 3D ?
2019 va a ser un año muy emocionante para VELO
3D
. Estamos empezando a salir al mercado y la gente se está volviendo mucho más consciente de nuestra empresa y nuestras capacidades. Estamos viendo eso tanto en la demanda del sistema como de las piezas impresas en el sistema y del sistema en sí.
Para nosotros, este será el año de la tecnología sin soporte, cuando realmente Empiece a hacer que la gente diseñe VELO
3D
en su producto final.
Para obtener más información sobre Velo
3D
, visite:www.velo3d.com
Impresión 3d
- Polvos de metal refractario VS tecnología de impresión 3D
- Entrevista con un experto:Dr. Alvaro Goyanes de FabRx
- Considerando lo que significa la nueva tecnología de impresión en metal para AM
- Entrevista con un experto:Dr. Bastian Rapp de NeptunLab
- Estereolitografía:la tecnología de impresión 3D original
- Entrevista con el experto:Duncan McCallum, director ejecutivo de Digital Alloys, sobre la impresión Joule y el futuro de la impresión 3D en metal
- Entrevista con el experto:Guillaume de Calan, CEO de Nanoe, sobre el futuro de la impresión 3D de cerámica
- Entrevista con el experto:John Kawola, presidente de Ultimaker, sobre el futuro de la impresión 3D
- Entrevista con el experto:Simon Fried, cofundador de Nano Dimension, sobre el auge de la impresión 3D para electrónica
- Impresión 3D en metal:¿Dónde estamos hoy?
- Entrevista experta:Tecnólogo jefe de ANSYS sobre cómo lograr el éxito en la impresión 3D en metal con simulación