Entrevista con el experto:Wiener Mondesir, cofundador de Arevo, sobre la producción del primer cuadro de bicicleta de fibra de carbono impreso en 3D del mundo
La empresa Arevo, con sede en Silicon Valley, fue noticia en 2018 después de presentar lo que llamó el primer cuadro de bicicleta de fibra de carbono impreso en 3D del mundo. El caso de uso mostró las capacidades únicas de la tecnología de impresión 3D compuesta patentada de Arevo, que combina robótica y software para producir piezas compuestas livianas y personalizadas.
Desde entonces, Arevo se ha asociado con el fabricante de bicicletas, Franco Bicycles, para entregar cuadros unibody de fibra de carbono impresos en 3D para una nueva marca de eBikes.
Esta semana, nos complace hablar con Wiener Mondesir, cofundador y director de tecnología de Arevo, sobre la tecnología patentada de Arevo, los beneficios de la impresión 3D compuesta y lo que depara el futuro para la fabricación de compuestos.
¿Podrías contarnos un poco sobre Arevo?
En Arevo, nuestro objetivo es permitir la fabricación de piezas compuestas a escala. Hacemos esto con una confluencia de robótica, materiales y software.
Cuando se analiza la industria de los compuestos, la fabricación de piezas de compuestos representa una gran oportunidad. La fibra de carbono puede ser más resistente que algunos metales y es liviana, por lo que tiene un gran atractivo en muchas industrias.
Pero por varias razones, la adopción de la fabricación de compuestos se ha sofocado, por lo que no se está abordando la oportunidad. Una razón de esto es debido a los procesos de fabricación ineficientes.
La fabricación de compuestos actualmente requiere mucha mano de obra, recursos y capital, lo que significa que en realidad no se escala a grandes volúmenes. Las industrias que realmente han podido capitalizar la fabricación de compuestos han sido aquellas que podían permitirse el caso comercial, como las industrias aeroespacial y automotriz de muy alta gama.
Además, existen largos ciclos de diseño debido a un software inadecuado y una simulación ineficiente. Otra razón que a menudo se pasa por alto es la falta de comprensión de los compuestos en otras industrias.
Arevo está abordando todos estos problemas. Estamos reconsiderando la fabricación de compuestos mediante lo que llamamos la digitalización de compuestos.
Hemos optado por resolver este problema mediante el desarrollo de software que borra la brecha de conocimiento.
Empieza con un modelo 3D y nuestro software hace el análisis, da la orientación final óptima, la cantidad correcta de material y produce instrucciones para fabricar la pieza utilizando nuestra tecnología de fabricación.
Tomemos una telaraña como ejemplo. Cuando miras una telaraña, es una estructura 3D que tiene la cantidad adecuada de material para su propósito.
La fibra, o la seda en el caso de la telaraña, usa solo la cantidad justa de material y está perfectamente colocada donde debe estar. Nos inspiramos en eso cuando creamos una forma optimizada de imprimir piezas compuestas en 3D.
Así que esa es nuestra misión como empresa:permitir la fabricación de compuestos a escala.
¿Cuáles son los beneficios de la impresión 3D compuesta?
Los compuestos de fibra de carbono ofrecen una excelente relación resistencia-peso, por lo que obtienes un material realmente fuerte pero liviano.
Cuando observa la tendencia en la impresión 3D, muchas técnicas diferentes usan estructuras de celosía para metal liviano, que es naturalmente denso y pesado.
Pero si comienza con un material ligero y resistente como la fibra de carbono desde el principio, llegará al resultado final mucho más rápido. Por lo tanto, los compuestos son mucho más adecuados para ciertas aplicaciones que incluso los tipos de productos con estructura de celosía metálica, que se ven muy bien pero no necesariamente cumplen su propósito.
La complicación con la fibra de carbono es que es anisotrópica, lo que significa que es fuerte en una dirección. Eso es lo que hace que sea un poco más difícil de manejar sin herramientas especializadas.
En Arevo, hemos desarrollado el conjunto de herramientas para diseñadores, por lo que no es necesario tener un doctorado para fabricar con compuestos de fibra de carbono. Nuestro software se encarga de eso.
Su cuadro de bicicleta de fibra de carbono impreso en 3D se publicitó ampliamente cuando se presentó. ¿Cuál fue el proceso de creación del cuadro de la bicicleta, desde el diseño hasta la producción?
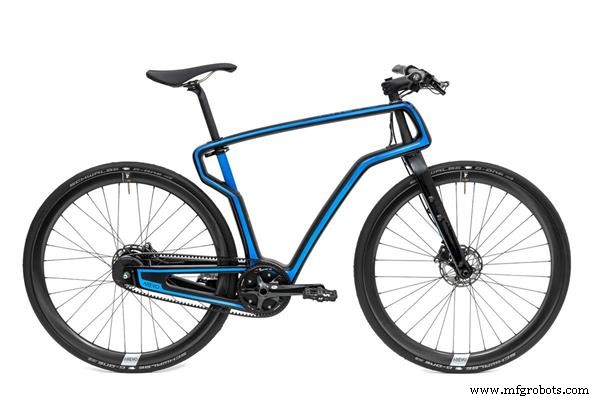
Esa aplicación en particular comenzó como una forma de mostrar lo que es posible con la tecnología.
Un cuadro de bicicleta es muy accesible, pero tiene una forma muy compleja y es una estructura grande que requiere carga, torsión y la capacidad de soportar peso. Así que fue la aplicación perfecta para demostrar nuestra tecnología.
Si da un paso atrás y observa las bicicletas compuestas tradicionales hoy en día, pasan de un diseño a la iteración de prototipos y luego a la producción. Ese proceso lleva cerca de un año.
Además, las bicicletas de composite tradicionales se fabrican mediante un proceso muy manual. Los marcos se unen entre 20 y 30 partes y hasta 40 personas tocan cada marco. Es un proceso que requiere mucha mano de obra y termina con un producto de muy alto costo que no necesariamente escala.
Los diseños también son muy similares, por lo que no puede obtener mucha personalización.
Con nuestra tecnología, redujimos este proceso de casi un año a unos pocos días. El software de Arevo toma un diseño CAD y hace un diseño generativo isotrópico en el marco que se le ocurre a un diseñador. También optimiza la orientación y hace un análisis predictivo.
El siguiente paso tiene lugar en nuestras instalaciones de fabricación. Construimos una planta de fabricación en California que puede producir cuadros de bicicleta personalizados bajo demanda utilizando nuestra tecnología robótica y de deposición.
Cuando lanzamos la bicicleta, todos los grandes fabricantes de bicicletas se acercaron a nosotros porque estaban interesados en la libertad de diseño que ofrecía la tecnología.
Cuando observa el diseño del cuadro de la bicicleta Arevo, en realidad se desvía del diseño de bicicleta convencional. No tiene asiento, por ejemplo, y se ve muy diferente a una bicicleta tradicional.
La bicicleta de Arevo es una bicicleta unibody hecha con fibras de carbono muy fuertes orientadas en la orientación óptima en el espacio 3D. Podemos lograr el diseño en una estructura unibody que lo hace muy sólido y liviano.
Podemos ajustar el recorrido real de la bicicleta utilizando herramientas de software. Podemos ajustar la rigidez en ciertas regiones de la bicicleta y permitir una conducción aún más rebotante si se desea, a pedido. Con las bicicletas tradicionales, esencialmente siempre estás tratando de hacer el mismo cuadro una y otra vez.
Un cuadro impreso en 3D, por otro lado, abre un nuevo modelo de negocio para una industria que está acostumbrada al larguísimo proceso de introducir una nueva bicicleta en el mercado. Hoy en día se fabrican alrededor de un millón de marcos compuestos al año. Y ahora puede introducir marcos muy personalizados bajo demanda con nuestra tecnología.
Nuestro objetivo es continuar creando nuevas aplicaciones que aprovechen esta capacidad.
¿El enfoque personalizado de producción es un modelo comercial escalable?
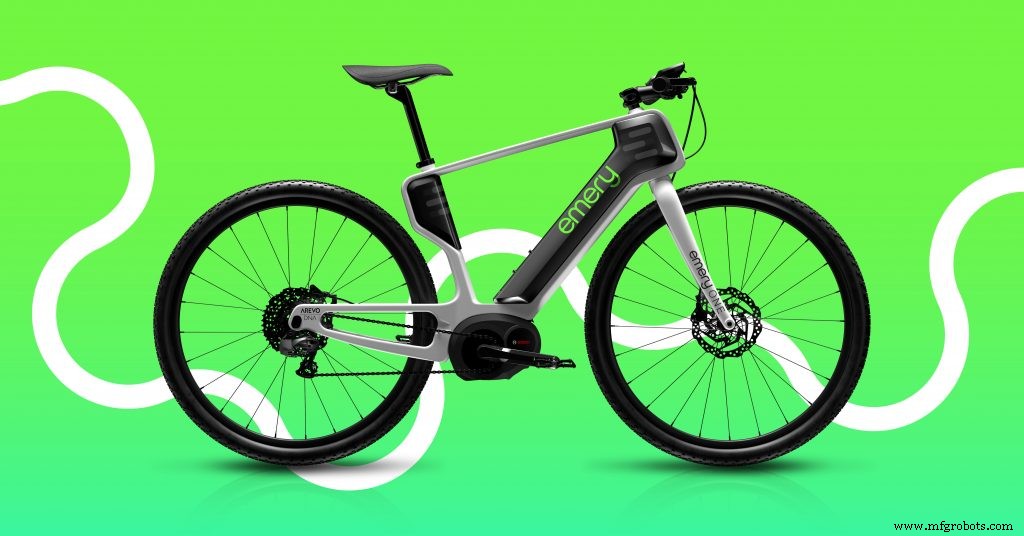
Hay un gran valor en la personalización cuando se trata de bicicletas. Cada persona es única. Se fatiga más cuando no está montando una bicicleta diseñada, configurada o ajustada para su cuadro. Entonces, una bicicleta es en realidad un buen vehículo para demostrar el valor de la personalización.
Existe toda una tendencia en torno a la micro-movilidad y la capacidad de caminar con un vehículo muy conveniente. La bicicleta representa eso. En muchos países diferentes, es una forma de transporte dominante.
Cuando necesite personalizar la forma y la función, no puede hacerlo en una forma de mercado masivo. Pero con nuestra tecnología, un consumidor puede diseñar el marco y nuestro software puede garantizar que el marco que ha diseñado sea estructuralmente sólido.
Luego pueden enviar eso a nuestras células de impresión 3D para hacer esa bicicleta a pedido. Por lo tanto, el proceso desde el concepto hasta la producción se simplifica mucho.
¿Qué otras aplicaciones imagina con su tecnología?
Hoy nos centramos en la bicicleta y las aplicaciones de movilidad. Estas son aplicaciones que pueden aprovechar la propuesta de valor que ofrecemos, que es muy liviana, con una alta relación resistencia-peso y productos personalizados.
Cuando se analizan las industrias, es realmente importante mejorar el rendimiento. en el sector deportivo, así como en las industrias automotriz, energética y aeroespacial.
Tenemos un montón de aplicaciones diferentes en las que estamos trabajando en las que se requiere peso ligero, alto rendimiento y alta personalización. Y esas son las áreas clave en las que se puede utilizar nuestra tecnología.
¿Cómo encaja la robótica en su tecnología?
Cuando observa la impresión 3D, la mayor parte de la impresión 3D se basa en capas y las capas se depositan en los planos X e Y. Cuando observa las propiedades de las piezas fabricadas con ese proceso, tienden a sufrir en la dirección Z.
Usamos un robot de seis ejes totalmente articulado para depositar nuestra fibra de carbono en las direcciones X, Y y Z. Eliminamos el problema de la fuerza Z que afecta a otras tecnologías basadas en capas porque podemos colocarnos en la dirección Z. Esa es una de las capacidades únicas de nuestra tecnología de deposición. La robótica juega un papel importante en eso.
El segundo aspecto es la escala de piezas que se pueden imprimir. Hoy en día, la mayoría de los sistemas están relegados a un cierto sobre de construcción, lo que significa que solo puede fabricar partes de cierto tamaño. Si va más allá de cierto tamaño, la pieza deberá cortarse en subconjuntos para hacer una estructura más grande.
Nuestros robots proporcionan una capacidad de envolvente de construcción infinita porque podemos poner nuestros robots en el pórtico para fabricar piezas aeroespaciales. Al mismo tiempo, el mismo robot puede hacer una bicicleta. El alcance de nuestros robots es un volumen de cuatro metros de altura. Esencialmente, es muy escalable en términos de brindarnos ese sobre con letra grande.
¿Cómo describiría el estado actual del mercado de la impresión 3D compuesta? ¿Qué tan avanzada es la tecnología?
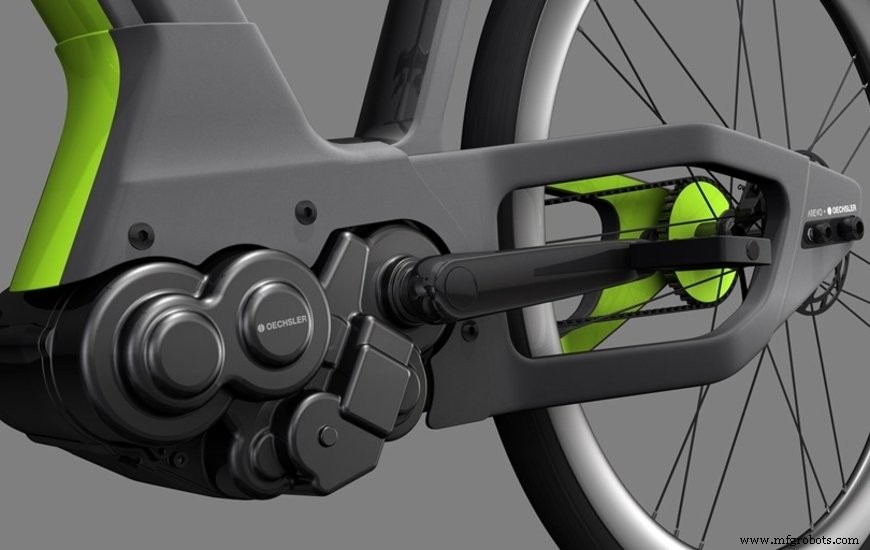
La industria de los compuestos ha estado haciendo aditivos durante bastante tiempo. Es solo que la complejidad de las geometrías se ha limitado a lo que podría caber en un molde, como piezas con una curvatura muy pequeña. Además, las capas generalmente se colocan manualmente, lo que da como resultado una pieza que tiene una complejidad bastante limitada.
Así que la impresión 3D compuesta ha existido por un tiempo. Pero ahora cosas como la robótica automatizada o los sistemas mecatrónicos, que automatizan la colocación de la fibra, permiten geometrías más complejas.
Hay muchas empresas que adoptan un enfoque diferente para automatizar la fabricación de compuestos, desde diferentes tipos de sistemas de resina hasta diferentes casos de uso.
Y eso es muy útil.
En general, creo que el sector de la impresión 3D compuesta se encuentra en un estado saludable, con Arevo a la cabeza.
¿Cuáles son algunos de los desafíos que enfrenta la industria, ya sea la impresión 3D en general o la impresión 3D compuesta específicamente?
Creo que los mayores desafíos surgen de la falta de herramientas de software disponibles para explorar lo que es posible con aditivo. Tiene la mentalidad de mirar las técnicas de fabricación tradicionales y nosotros fuimos educados con técnicas de fabricación tradicionales.
La gente a menudo comienza con piezas que se fabricaron de forma tradicional y quieren forzar el aditivo de ajuste a esa pieza, pero eso no siempre coincide.
Pero cuando realmente explota lo que puede hacer con el aditivo, ya sea a base de metal, compuesto o polímero, en términos de singularidad y complejidad, realmente necesita herramientas para guiarlo a través de ese proceso e informar a los diseñadores. e ingenieros.
¿Cómo cree que evolucionará la industria en los próximos cinco años?
Es muy alentador. Desde los inicios de Arevo, siempre nos hemos centrado en las piezas de producción.
Cuando observa la industria actual, es realmente alentador ver que todo el mundo está hablando de piezas de producción. Ese es el tema común.
En el futuro, espero que la industria comience a hablar también sobre calidad y escalabilidad. A medida que comience a fabricar productos, producir a escala y con mayor repetibilidad será el enfoque clave para la industria.
Garantizar la calidad de las piezas y los procesos es un gran tema de conversación para la fabricación aditiva en este momento. ¿Cuál es el enfoque de Arevo para esto?
Uno de los avances clave que Arevo pudo lograr es nuestro proceso de deposición basado en láser.
Además, empleamos algoritmos de aprendizaje automático que pueden realizar inspecciones in situ. Disponemos de un conjunto de sensores y podemos realizar una inspección in situ de una pieza a medida que se fabrica.
Esto nos permite obtener un material impreso muy homogéneo con menos del 1% de vacíos. Podrías hacer un corte transversal de una pieza y cuando lo subas al microscopio, puedes observar material impreso muy homogéneo.
Esto se traduce en piezas de muy alta calidad cuando se trabaja en aplicaciones muy exigentes como la aeroespacial. Este control de calidad in situ, combinado con nuestro monitoreo de circuito cerrado, es lo que nos permite tener una calidad repetible y predecible.
¿Qué le depara a Arevo los próximos 12 meses?
En los próximos 12 meses, nos centraremos en la ejecución de la fabricación. Desde que lanzamos la bicicleta, en realidad tenemos más demanda de la que podemos satisfacer. Nuestro objetivo para el próximo año es continuar lanzando nuevas aplicaciones, pero principalmente para escalar nuestra capacidad para satisfacer la demanda actual.
Para obtener más información sobre Arevo, visite: https://arevo.com/
Impresión 3d
- Entrevista con el experto:Guillaume de Calan, CEO de Nanoe, sobre el futuro de la impresión 3D de cerámica
- Entrevista con el experto:John Kawola, presidente de Ultimaker, sobre el futuro de la impresión 3D
- Entrevista con el experto:Simon Fried, cofundador de Nano Dimension, sobre el auge de la impresión 3D para electrónica
- Entrevista con el experto:Philip DeSimone, cofundador de Carbon, sobre cómo avanzar hacia la producción de gran volumen con impresión 3D
- Entrevista con el experto:Rush LaSelle de Jabil sobre el futuro de la fabricación aditiva
- Entrevista con un experto:Greg Paulsen de Xometry sobre el auge del modelo empresarial de fabricación como servicio
- Entrevista con el experto:Vicepresidente de asociaciones tecnológicas de VELO3D para ampliar las capacidades de la impresión 3D en metal
- Entrevista con expertos:John Barnes, fundador de The Barnes Group Advisors, sobre el futuro de la fabricación aditiva
- Entrevista de experto:Josh Martin, director ejecutivo de Fortify, sobre su tecnología de fabricación de compuestos digitales
- Presentamos el primer teléfono inteligente de fibra de carbono del mundo
- Toray crea la primera fibra de carbono porosa del mundo con una estructura de poros continuos de tamaño nanométrico