Fabricación continua de fibra (CFM) con compuestos moi
La impresión y deposición 3D de fibra continua está ganando impulso. A medida que crezca el número de empresas que la utilizan y la hacen avanzar, esta tecnología indudablemente dará forma a la industria de los compuestos.
Primero, ofrece fabricación sin moldes ni herramientas. En segundo lugar, ofrece estructuras multifuncionales (por ejemplo, conductividad eléctrica, cambio de forma, detección). En tercer lugar, abre la puerta a un mundo de fabricación híbrida, por ejemplo, laminación sobre impresión 3D y fresado durante la impresión, así como a un panorama casi infinito de desarrollo de materiales, desde fibras de aleación con memoria de forma (SMA) de Nitinol hasta soluciones de nanocompuestos conductores. para el modelado de deposición líquida (LDM). Este último es todo un mundo en sí mismo al que volveré en un blog futuro.
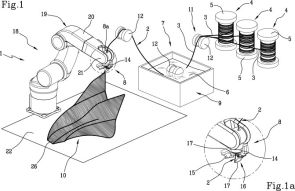
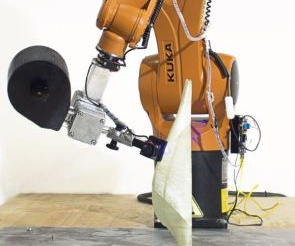
Patente WO2017085649A1 y sistema de impresión Atropos. FUENTE:moi composites.
Moi composites fue establecido en febrero de 2018 por la ingeniera de materiales y profesora Marinella Levi, la ingeniera de diseño Gabriele Natale y el arquitecto Michele Tonizzo. En 2013, el profesor Levi comenzó a trabajar con impresión 3D en el Politecnico di Milano (Milán, Italia). En 2014, había formado + LAB en el Departamento de Química, Materiales e Ingeniería Química "Giulio Natta" de la universidad. Su visión era fusionar la I + D, la enseñanza y la innovación de materiales reuniendo a ingenieros, diseñadores, investigadores y creadores en un centro de impresión 3D multidisciplinario y colaborativo.
2014 Primera herramienta para la impresión 3D de composites termoendurecibles de fibra continua 2015 Patente WO2017085649A1 2016 Asociaciones con Owens Corning y KUKA Robotics,Atropos proyecto y sistema de impresión 2017 Premio a la innovación JEC, asociación con Autodesk,
Subcampeón del premio James Dyson,
Asociación con la automatización COMAU
(Cronología completa)
“Comenzamos con los compuestos moi porque queríamos producir piezas comerciales y participar en proyectos internacionales”, explica Michele Tonizzo. “Hemos descubierto que hay mucho mercado. Fabricamos componentes biomédicos, así como piezas para aplicaciones marinas, de petróleo y gas y aeroespaciales, principalmente utilizando fibra de vidrio. La tecnología CFM es capaz de fabricar soluciones únicas que serían imposibles con los métodos tradicionales ".
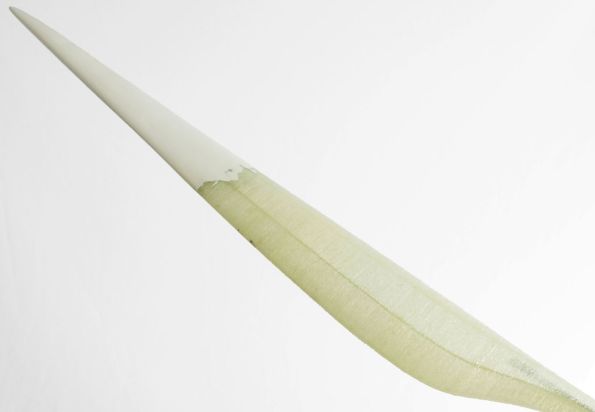
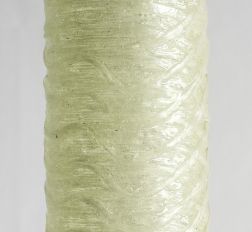
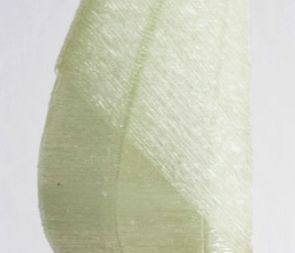
Paleta de hélice impresa en 3D con armadura estructural interna que utiliza fibra de vidrio continua (parte superior). Este proyecto también demostró la colocación de la fibra a lo largo de curvas no lineales (abajo a la izquierda) y laminado de fibra continua con orientaciones de fibra tradicionales (p. Ej., 0 °, + 45 °, -45 °, 90 °, abajo a la derecha). FUENTE:moi composites
Gama de resinas y fibras
Atropos demostró la capacidad de imprimir polímeros termoendurecibles reforzados con fibra discontinuos y continuos, no solo capa por capa, sino también a lo largo de curvas no lineales. Usó luz ultravioleta (UV) para curar los polímeros en su lugar. “Actualmente podemos imprimir con curado UV en epoxi, acrílico y viniléster”, dice Tonizzo. Señala que el acrílico funciona bien para piezas arquitectónicas porque es transparente y no requiere temperatura para curar / post-curar. El viniléster se utiliza para piezas marinas y epoxi para piezas de petróleo y gas y aeroespaciales.
“Para algunas aplicaciones, el curado UV es solo la etapa inicial y luego el curado posterior con calentamiento convencional”, observa Tonizzo. “No estamos atados al curado UV. Hemos impreso con polímeros de curado no UV y entendemos que para aplicaciones de propiedades superiores necesitaremos diferentes opciones de matriz ". Como referencia, la temperatura de transición vítrea (Tg) para su resina más utilizada, un viniléster, es de alrededor de 140 ° C.
“También estamos trabajando con fibra de carbono, pero no con resinas de curado UV”, dice Tonizzo. Señala que tanto la transparencia de la fibra como el color afecta el curado UV. "El problema con el carbono es que es opaco y negro. Esta es la peor combinación. Queremos desarrollar la mejor solución para la fibra de carbono como material, no solo la tecnología más sencilla que funcione. Hay muchas otras opciones de material de curado que podemos usar, por lo que estamos investigando estas ”.
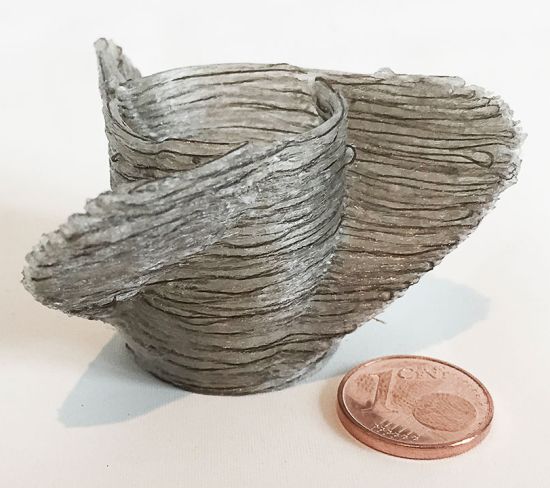
Los compuestos Moi pueden imprima fibras conductoras continuas para funcionalidad eléctrica / térmica, detección, cambio de forma, etc. FUENTE:moi composites.
Moi composites ha impreso fibra de vidrio continua de hasta 2400 tex (207 yd / lb con un diámetro máximo de 24 μm según una hoja de datos de Owens Corning) y está probando fibras naturales. También se ha impreso con fibra de basalto. “Podemos imprimir muy bien con curado UV y fibra de basalto porque en realidad es algo transparente y más marrón que negro”, explica Tonizzo.
Las fibras que conducen la corriente eléctrica también se pueden utilizar en la tecnología CFM. Se pueden colocar según sea necesario en la estructura que se está imprimiendo. Uno de los proyectos enumerados en el sitio web + LAB muestra fibra de Nitinol, que es una aleación con forma de memoria. “Para poder hacer estructuras que cambien de forma”, dice Tonizzo. "Por ejemplo, podría usarlo para liberar tensiones en otras fibras, como en el hormigón pretensado".
Impresión 3D como parte de la fabricación híbrida
Atropos utiliza un brazo robótico Kuka con un sobre de impresión de 0,5 x 0,5 x 0,5 m de altura. “Ahora estamos imprimiendo en un robot Comau con un sobre de 1,0 x 0,5 x 0,8 m de altura, que es el sistema de segunda generación”, dice Tonizzo. “También hemos utilizado robots más grandes con mesas giratorias y volúmenes de construcción de 1,5 x 1,5 x 1 m de altura y hemos demostrado que nuestra tecnología es fácilmente escalable”.
Moi también está desarrollando un cabezal de impresión todo en uno de tercera generación con un sistema para aplicar presión a las fibras, sensores, mecanismos de corte y herramienta de fresado. Tonizzo dice que esto cerrará la brecha entre la impresión 3D y la colocación automatizada de fibras (AFP ). “La impresión 3D no logra el rendimiento de AFP, pero CFM ofrece más flexibilidad. Ya podemos imprimir con fibras de 0,25 mm de grosor y tenemos la capacidad de crear curvas y colocar fibras continuas en la posición ideal ”, añade.
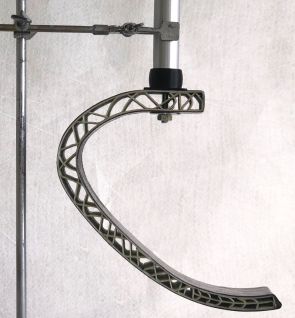
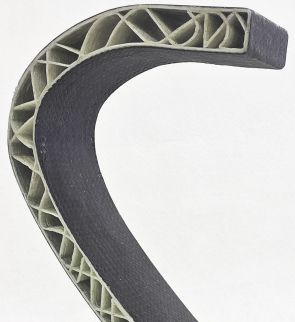
SuPeRIOR es un Prótesis de miembros inferiores optimizadas para un peso, una desviación y un coste mínimos.
Luego, el núcleo estructural impreso en 3D se laminó con fibra de carbono y resina epoxi, seguido de curado con VBO. FUENTE:moi composites.
“La impresión 3D debe usarse para lo que mejor hace”, dice Tonizzo, “que incluye optimizar el flujo de trabajo. Por ejemplo, puede imprimir en 3D un núcleo interno con cortes y direcciones de fibra inteligentes. Luego, usa laminado manual común en la parte superior y cura en un autoclave o solo con una bolsa de vacío ". Describe una pieza que era imposible de hacer convencionalmente con un molde. “Imprimimos el núcleo interno y luego lo envolvimos en laminado y lo curamos en autoclave a 110 ° C y 2 bar de presión durante varias horas. El papel salió genial ". Esta parte está cubierta por un acuerdo de confidencialidad, por lo que no hay más detalles disponibles, pero moi ha producido la prótesis SuPeRIOR de una manera similar, curada no en un autoclave sino solo con una bolsa de vacío (VBO). "Todos los componentes internos utilizan una fibra de vidrio continua", explica, "pero el laminado exterior es tejido de fibra de carbono laminado a mano y resina epoxi". Todo el diseño reduce la desviación y aumenta la personalización al tiempo que reduce significativamente los costos y el tiempo de producción.
Software de optimización basado en vóxeles
Tonizzo explica que el proceso de diseño de piezas combina el algoritmo basado en vóxeles de Autodesk con los algoritmos de moi para la optimización de la tensión y la ruta. Esto es lo que produce la ruta de fibra optimizada para la estructura. El software también trabaja para elegir la ruta más posible de fabricación. “Este es un proceso iterativo”, dice Tonizzo. “El diseño no está completamente automatizado como el diseño generativo. Todavía necesita ingenieros para tomar decisiones. Pero creo que así es como debería ser:el diseñador y el software combinados, no solo la IA ".
Futuro multimaterial, fuerte potencial de mercado
En una de las imágenes de la pala de la hélice impresa Atropos, hay un primer plano que muestra un patrón casi tejido. “En realidad, esto no está tejido, pero pronto será posible”, dice Tonizzo. Me dirige al proyecto de onda sinusoidal en el sitio web + LAB. “Los demostradores mostrados están impresos en 3D en plástico con fibras cortas y el proceso LDM [modelado de deposición líquida] mientras eran investigadores en + LAB. Los algoritmos que usamos entonces son los mismos que ahora estamos avanzando con fibra continua ”.
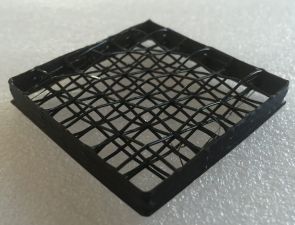
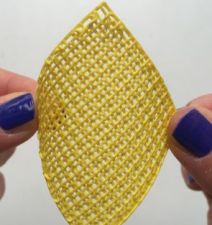
Sine Wave de + LAB muestra patrones de relleno de polímero impreso en 3D con una respuesta elástica sintonizable. FUENTE:+ LAB.
Es obvio del sitio web + LAB, que las innovaciones materiales y las posibilidades para este tipo de impresión son casi infinitas. La pregunta es qué ofrecerá la mayor oportunidad y potencial para soluciones de alta demanda. Mientras tanto, los proveedores de materiales apoyan el desarrollo continuo. Por ejemplo, Owens Corning está interesado en demostrar la fibra de vidrio con más matrices, como cerámica y hormigón. Obviamente, esto es muy interesante para aplicaciones de edificación y construcción, y podría tener un potencial significativo a la luz de las tendencias actuales de fabricación digital y construcción energéticamente eficiente, módulos prefabricados fuera del sitio y sostenibilidad mejorada a través de materiales naturales y reciclados, todos los cuales enfatizan el peso ligero. “El departamento de Giulio Natta del Politecnico di Milano está en un proyecto de la UE para imprimir geopolímeros que se comportan como el hormigón”, añade Tonizzo. “Se curan por sí mismos con el tiempo, pero tienen la consistencia de la arcilla durante la impresión para un mejor flujo. Definitivamente seguiremos trabajando en esta área, así como con nuevos polímeros y fibras ”.
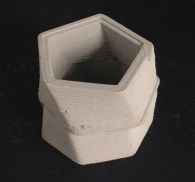
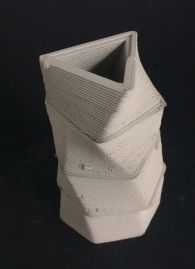
Los compuestos Moi son también imprimiendo con geopolímeros, que se comportan como el hormigón.
FUENTE:+ LAB.
¿Venderán máquinas? “Sí, pero en el futuro”, dice Tonizzo. "Por ahora, estamos produciendo piezas y llevando la tecnología a las instalaciones del cliente, utilizando nuestro conocimiento, cabezal de impresión y software para realizar soluciones de piezas bajo demanda". Agrega que después de haber trabajado el año pasado para mejorar la tecnología con los primeros usuarios de CFM y demostrar el caso de negocios para muchas partes diferentes en diferentes mercados, moi composites ahora está buscando inversionistas para escalar aún más las máquinas y procesos de CFM para oportunidades comerciales de mercado.
Resina
- Accesorios de ensamblaje de impresión 3D con compuestos Markforged
- Fabricación aditiva con composites en la industria aeroespacial y de defensa
- Evaluación de una cadena de suministro de compuestos en proceso de cambio
- Comercialización de termoendurecibles curables por UV para impresión 3D de fibra continua
- Preguntas y respuestas con Ethan Escowitz, director ejecutivo de Arris Composites
- Reciclaje de materiales compuestos:no más excusas
- La fabricación continua de fibra difumina la línea entre la impresión 3D y AFP
- Covestro lanza los termoplásticos de fibra continua Maezio
- Compuestos de impresión 3D con fibra continua
- Severstal invierte en robótica para automatizar la fabricación de compuestos avanzados con Airborne
- GE Digital:Perspectivas operativas con datos y análisis