WMG prototipos de chasis CFRP para vehículos de demostración de trenes muy ligeros (VLR)
Revolution VLR es un consorcio en el Reino Unido, liderado por Transport Design International Ltd (TDI, Stratford upon Avon), que ganó fondos en 2013 para desarrollar un bogie ferroviario autopropulsado con un sistema de propulsión híbrido integral. TDI cree que el diseño de vehículos de "tren ligero" más ligeros, es decir, tren muy ligero (VLR), es crucial para proporcionar la próxima generación de transporte público sostenible. En la fase 2 del proyecto VLR, un vehículo demostrador de batería diésel completo de 18 metros de largo estará disponible para pruebas en 2020.
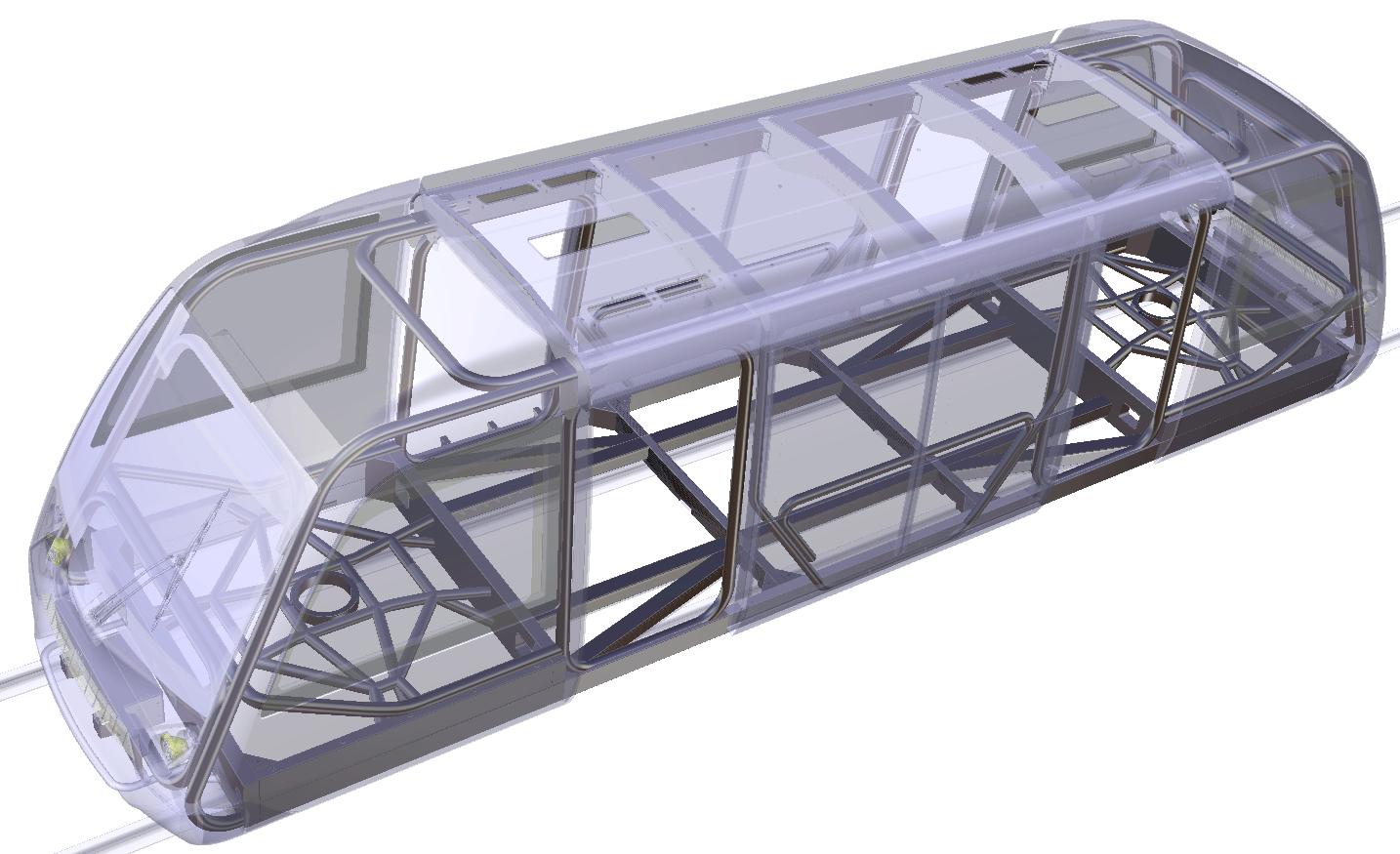
El demostrador Very Light Rail (VLR) es un bogie de 18 metros de largo con un sistema de propulsión híbrido de batería diésel integrado y un chasis ligero hecho de tubos compuestos trenzados. FUENTE | Universidad de Warwick.
Un miembro original de Revolution VLR, WMG en la Universidad de Warwick ha desarrollado un marco de plástico reforzado con fibra de carbono (CFRP) para este vehículo VLR de demostración. WMG apoya desde hace mucho tiempo los compuestos, con iniciativas como el Centro Nacional de Innovación Automotriz, el Centro de Ingeniería de Materiales y el Instituto Internacional de Fabricación de Nanocomposites. Los socios de WMG para este proyecto "BRAINSTORM VLR" incluyen a TDI, Innovate UK del gobierno del Reino Unido (que financia los compuestos), el desarrollador de componentes compuestos estructurales ligeros Far Composites y Composite Braiding. El marco está hecho de una serie de tubos compuestos termoplásticos trenzados que se ensamblan fácilmente mediante unión adhesiva y soldadura simple.
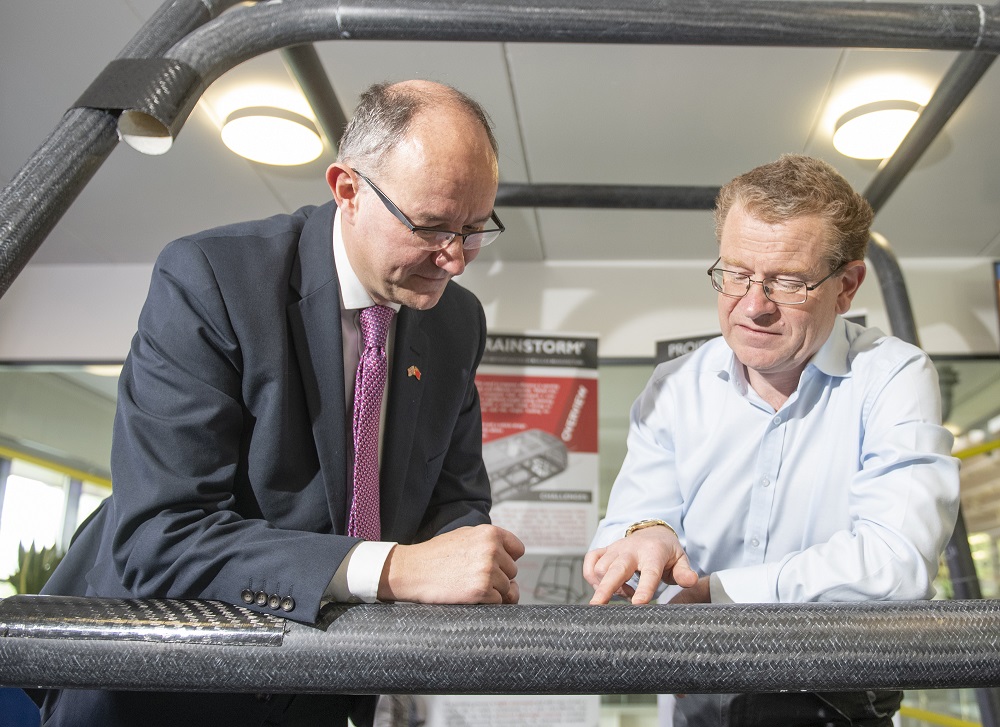
El vehículo prototipo / demostrador VLR utilizará un chasis de estructura espacial hecho de tubos compuestos termoplásticos reforzados con fibra de carbono trenzados que se ensamblan fácilmente mediante uniones adhesivas y una soldadura simple. FUENTE | Universidad de Warwick.
Los diámetros exteriores del tubo se mantienen iguales, con diferentes requisitos de carga y fijación que se manejan variando los espesores de pared. Esto mantiene bajos los costos de herramientas y significa que las uniones se pueden estandarizar. El trenzado permite un proceso de fabricación altamente automatizado:las tasas para el refuerzo solo pueden exceder 1 milla / día, así como un conjunto de materiales a medida, incluidas otras fibras (por ejemplo, vidrio, aramida, termoplástico) y materiales de matriz termoplástica de polipropileno de bajo costo. a polieteretercetona de gama alta (PEEK). Mientras tanto, WMG ha demostrado un ciclo de moldeo completo que se puede reducir a menos de cinco minutos, lo que destaca el potencial de este proceso asequible para aplicaciones de gran volumen.
Los termoplásticos también proporcionan reciclabilidad, según David Goodwin, gerente de ingeniería de Far-UK. “Con los compuestos se puede ahorrar mucho peso, lo que obviamente es atractivo para el funcionamiento del vagón [de ferrocarril]”, comienza, “pero con los compuestos tradicionales, al final de la vida útil del automóvil, simplemente se coloca en un vertedero, que no es ideal. Con este [diseño], hay una ruta para reciclar la carrocería del automóvil cuando eventualmente se quede fuera de servicio o, alternativamente, si sufre un impacto y parte del mismo debe ser reparado y reemplazado ”.
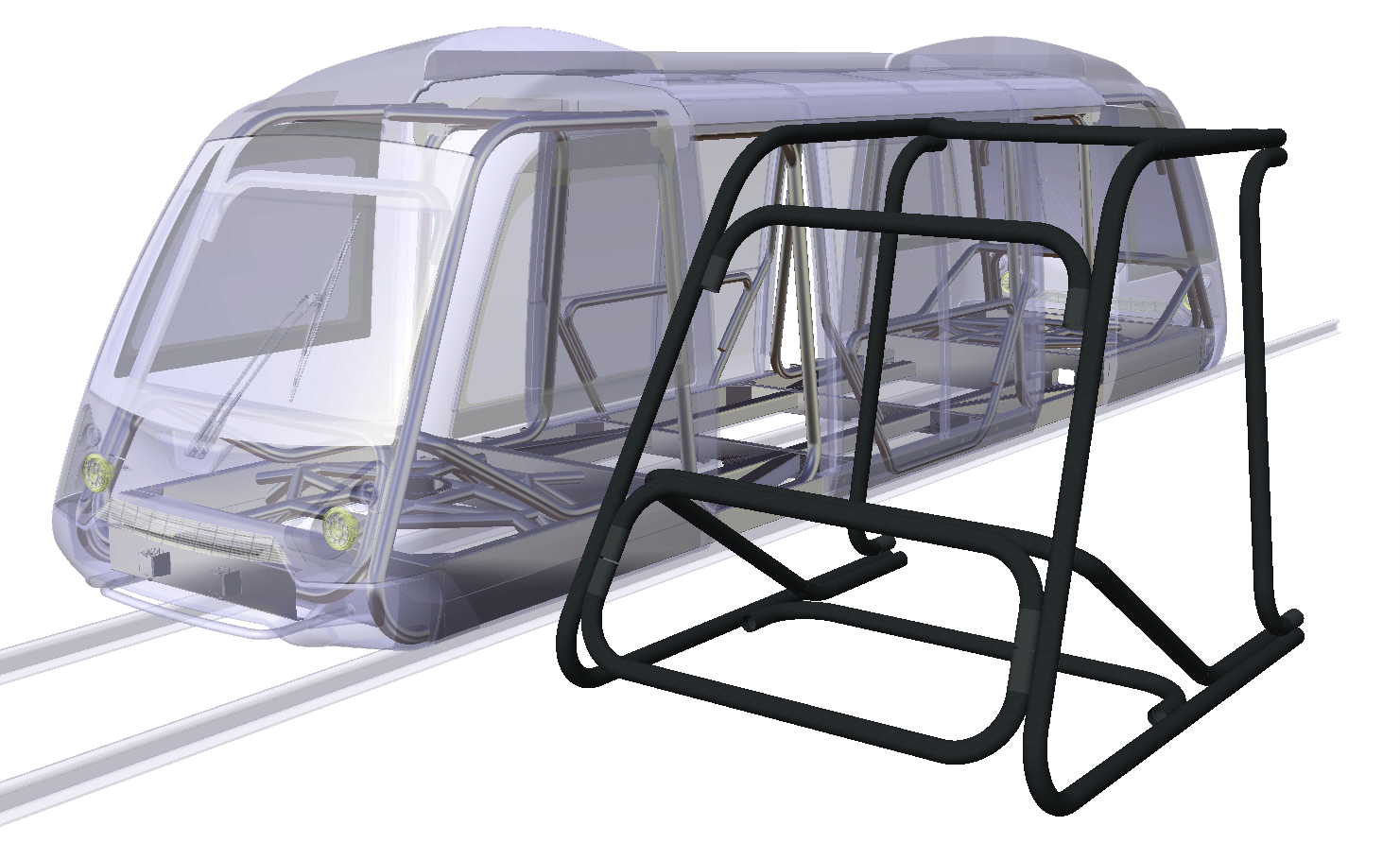
Universidad de Warwick
El diseño del chasis del bastidor espacial tubular también ayuda en este enfoque, permitiendo que cualquier tubo dañado sea simplemente removido y reemplazado por uno nuevo o reparado. "Nuestra asociación de investigación BRAINSTORM VLR ha logrado un ahorro de peso significativo, lo que permite que los servicios de VLR acomoden a más pasajeros al tiempo que reducen la energía necesaria para impulsar el vehículo y la tensión de peso que ejercerá sobre los rieles y la superficie de la carretera", explica el Dr. Darren Hughes. profesor asociado de Materiales y Fabricación en la Universidad WMG de Warwick. “La tecnología también garantiza que el vehículo sea resistente para una larga vida útil, que se pueda reparar fácilmente en caso de accidentes y lo suficientemente fuerte como para proteger a los pasajeros a bordo”.
“El proyecto BRAINSTORM se siente como un verdadero paso adelante para el equipo de Far Composites”, dice el director y gerente general de Far-UK, Lyndon Sanders. “Fue fantástico poder aprovechar la experiencia industrial de TDI para perfeccionar el principio de un nuevo tipo de estructura de carrocería para aplicaciones de transporte público. Agregue a eso el trabajo colaborativo con Composites Braiding y WMG para convertir ese pensamiento en un demostrador físico para mostrar cómo sería en la práctica fue realmente poderoso. Ahora es más que una buena idea, es una revelación para los actores de la industria que pueden verlo, tocarlo e incluso levantarlo ".
Resina
- Composites de TPE ultraligeros para calzado
- Diseño para la fabricación automatizada de composites de aeroestructuras de bajo volumen
- Resinas epoxi reprocesables, reparables y reciclables para composites
- Combinación de medidas dieléctricas de CA y CC para el control del curado de compuestos
- Perseverance rover da un paso para los compuestos en Marte
- Solvay y Leonardo lanzan un laboratorio de investigación conjunto para compuestos termoplásticos
- RS Electric Boats selecciona a Norco para la fabricación de materiales compuestos
- PEEKSense termopar de alta temperatura para el curado de compuestos PEEK
- Compuestos de Solvay seleccionados para catamarán de carreras
- Puerta termoplástica por primera vez para compuestos automotrices
- Ashland se asocia con Velox para la distribución de materiales compuestos en Francia