Prueba de soldadura LM PAEK para demostrador multifuncional de fuselaje
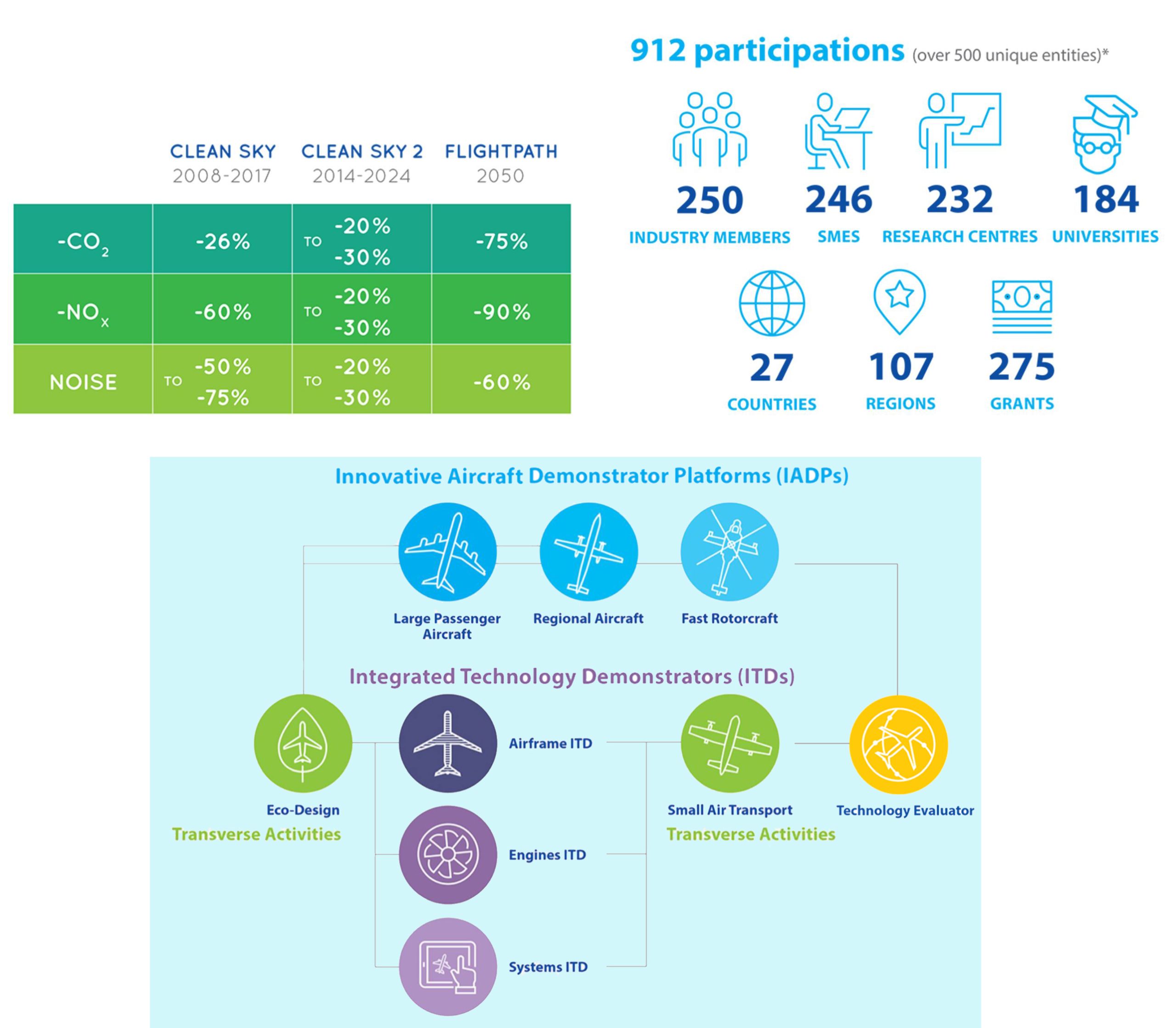
Este tipo de investigación aeronáutica comenzó con el Programa Marco (PM) de la Comisión Europea para la financiación de I + D, que abarca desde el FP2 (1987-1991) hasta el FP7 (2007-2013). Estos programas han contribuido sustancialmente a la maduración de una amplia variedad de tecnologías hasta el nivel de preparación tecnológica (TRL) 6 y la implementación en aviones como el Airbus A350.
Una de las diferencias en Clean Sky 2 es su organización en torno a grandes manifestantes. El MFFD es una de las tres secciones de fuselaje a gran escala que se producen dentro de la Plataforma de demostración de aeronaves innovadoras (IADP) de grandes aeronaves de pasajeros (LPA) (consulte el texto azul en la parte superior del cuadrado azul en la infografía anterior) . Dentro de la LPA IAPD hay tres plataformas. El MFFD se encuentra dentro de la Plataforma 2 “Estructura del sistema de cabina de integración física innovadora”, que cuenta con otros dos grandes demostradores.
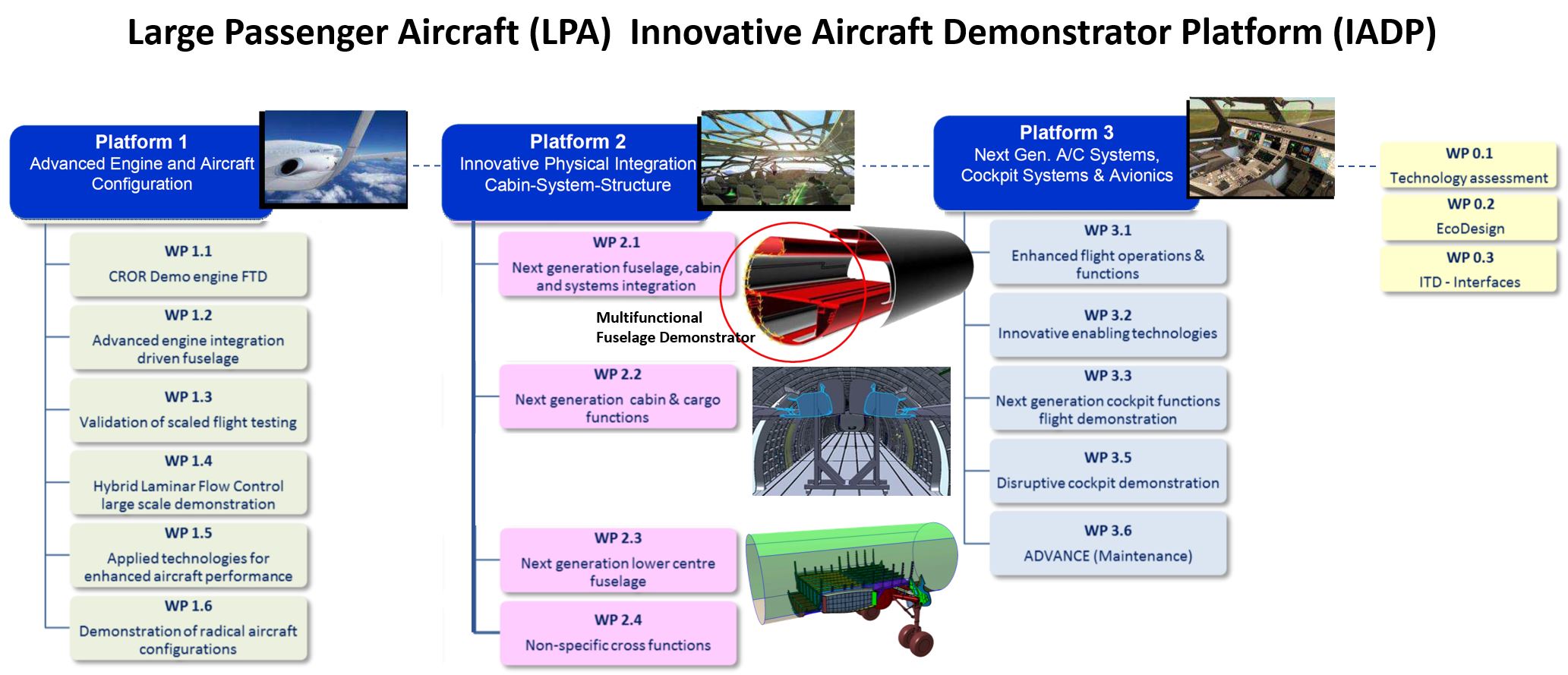
Para entender lo que esto significa, vuelvo a lo que me dijeron los ingenieros de Airbus Airframe Research &Technology (R&T) de Getafe, España, mientras investigaba compuestos multifuncionales en 2015. En esencia, dijeron:“Ya no queremos la duplicación y desperdicio de hacer un cilindro estructural exterior y un cilindro interior; queremos integrar la estructura del avión con los sistemas de cabina ”. Luché por visualizar lo que esto significaba, hasta que vi un boceto del MFFD.
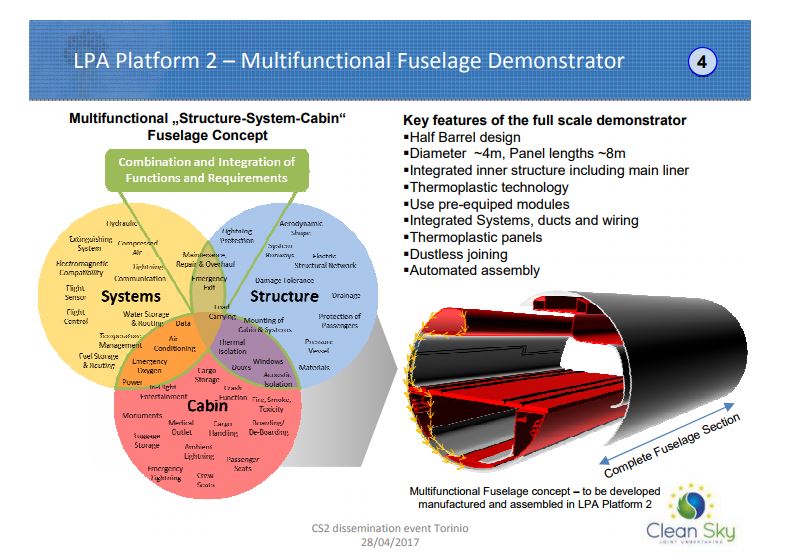
FUENTE | Difusión de Clean Sky 2 (CS2) y “Demostradores de compuestos termoplásticos:hoja de ruta de la UE para los fuselajes del futuro”.
“La modularidad, la integración y la creación de plataformas comunes son clave”, dice Ralf Herrmann, fuselaje típico de I + T de fuselaje de Airbus Operations GmbH (Bremen, Alemania) y líder del programa MFFD. Cito aquí desde la página de MFFD en el sitio web de Clean Sky 2:
Herrmann:"Sabemos desde hace mucho tiempo que los beneficios de la reducción de peso y la reducción de los costos recurrentes en la producción de aviones, cuando se utilizan compuestos termoplásticos - solo se puede lograr mediante la integración de varias disciplinas. Esto significa que centrarse en la estructura únicamente no puede lograr el beneficio completo de la tecnología de compuestos ".
La versatilidad de los termoplásticos debe aplicarse en combinación con un enfoque de diseño, según Paolo Trinchieri, responsable del proyecto de Clean Sky 2:“Es necesario eliminar la separación artificial de funciones en la etapa de prediseño de la aeronave y para planificar una alta tasa de producción de fabricación, montaje e instalación de aeronaves desde el principio ”.
Herrmann fue anteriormente el gerente de proyecto para el proyecto MAAXIMUS (estructura de aeronave más asequible a través del tamaño nUmerical extendido, integrado y maduro) del FP7. Desde abril de 2008 hasta septiembre de 2016, MAAXIMUS incluyó a 60 socios y tenía como objetivo demostrar el desarrollo rápido y la validación correcta a la primera, madurando habilitadores virtuales y físicos simultáneamente, de un fuselaje compuesto altamente optimizado para lograr una reducción del 50% en el tiempo de ensamblaje de grandes secciones de fuselaje, reducción del 10% en los costes recurrentes, reducción del peso estructural un 10% y un ciclo de desarrollo un 20% más corto. Los objetivos del MFFD pueden verse como una extensión:
- Habilite tasas de producción de 70-100 aviones / mes
- Reducir el peso del fuselaje en 1000 kg
- Reducir los costos recurrentes en un 20%.
Un habilitador clave es la unión sin polvo (sin agujeros, sin sujetadores) a través de componentes compuestos termoplásticos soldados. Herrmann explica que el enfoque secuencial actual para la fabricación de aeronaves, en el que la estructura del fuselaje debe estar bastante completa antes de que se puedan instalar los sistemas más las características de cabina y carga, requiere mucho tiempo y es “sensible a fallas”. En cambio, MFFD busca elementos estructurales y módulos de sistema altamente integrados y preequipados que se pueden instalar con bastante anticipación, mucho antes del ensamblaje final.
Cambio a juntas longitudinales y LM PAEK
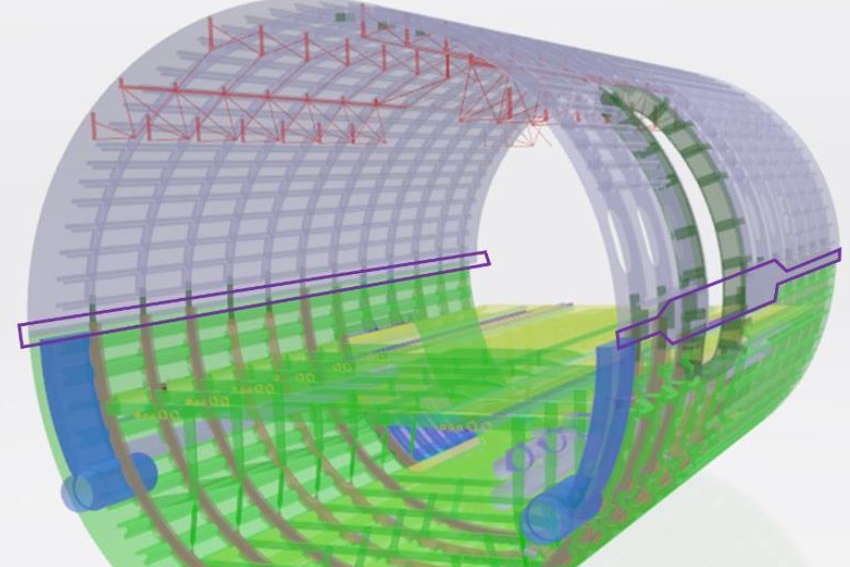
Las actividades del proyecto MFFD comenzaron en 2017. Cada año hay al menos una convocatoria de propuestas (PPC) en la que los líderes del proyecto describen temas que necesitan un mayor desarrollo. Como se puede ver en la imagen a continuación, el diseño de la junta diagonal que se muestra en CFP08 (abril de 2018) había cambiado a una junta longitudinal en CFP09 (septiembre de 2018).
“La junta de sesgo presentó problemas con respecto a la accesibilidad y la sujeción de las estructuras del piso que nos dimos cuenta de que serían difíciles de superar dentro del período de tiempo dado”, explica Herrmann. “Entonces, decidimos recurrir al diseño convencional para reducir el riesgo. Nuestro principal interés es mostrar cómo integrar todos los sistemas y elementos de cabina que se pueden instalar antes del Ensamblaje de Componentes Principales (MCA). Esta será también la primera vez que este material compuesto termoplástico se aplica en estructuras de fuselaje primario a gran escala para grandes aviones de pasajeros ”.
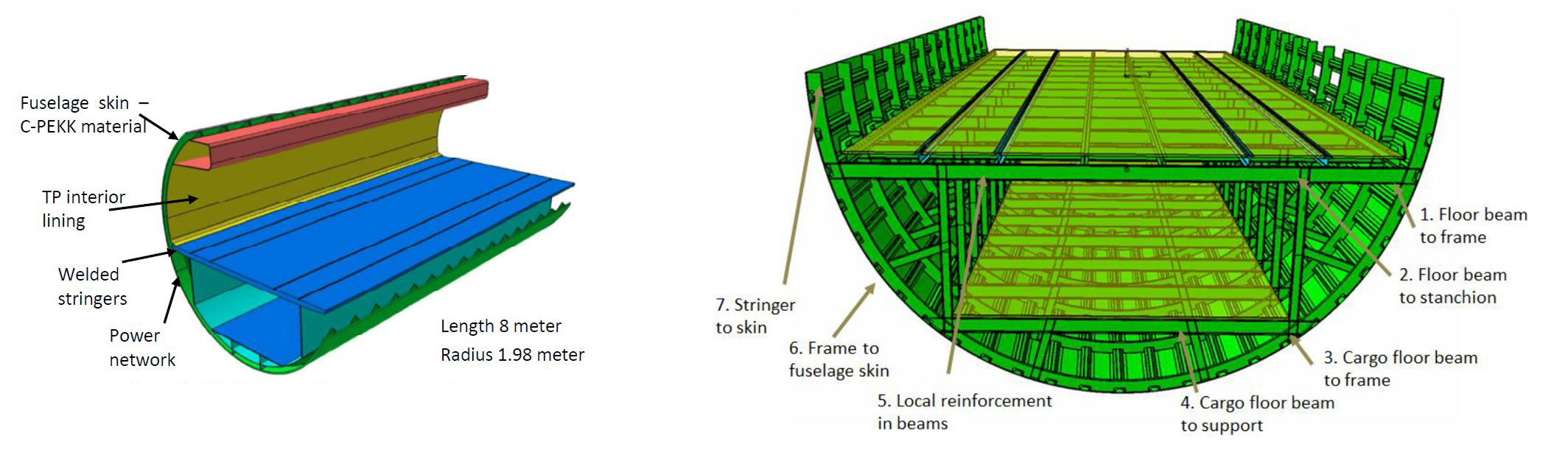
El diseño del MFFD cambió de un diseño de junta diagonal a una junta longitudinal más convencional en 2018. FUENTE | CFP08 p. 87 (izquierda) y CFP09 p. 133 (derecha).
Otro cambio fue en el material de la matriz del compuesto termoplástico (TPC). Los temas de MFFD en CFP08 y CFP09 se refieren a fibra de carbono / PEKK (polietercetonacetona), pero en CFP10 (marzo de 2019), el material de referencia se describió como fibra de carbono y PAEK (poliariletercetona). PAEK es la familia general de polímeros dentro de la cual residen PEEK, PEKK y LM PAEK.
Como se describe en mi blog sobre PEEK frente a PEKK frente a PAEK, el proveedor de materiales Cetex TenCate, ahora Toray Advanced Composites, produce los tres polímeros como cinta reforzada con fibra de carbono y afirma que las propiedades son básicamente las mismas. Sin embargo, Cetex TC1225 CF / LM PAEK la cinta se derrite a 305 ° C mientras que TC1320 CF / PEKK la cinta se derrite a 340 ° C . Y, según Scott Unger, director de tecnología global de Toray Advanced Composites, "LM PAEK tiene un flujo mucho mejor ... y también se puede procesar a velocidades más altas que PEKK y PEEK". TC1225 también cuesta menos.
Fuselaje inferior del MFFD:proyecto IMPRESIONANTE
STUNNING es el nombre del proyecto para el desarrollo y fabricación de la mitad inferior totalmente equipada del MFFD. El proyecto tiene como objetivo madurar aún más:
- Procesos de ensamblaje automatizados
- Tecnologías de fabricación y ensamblaje de termoplásticos
- Tecnologías integradas de desarrollo de diseño y fabricación
- Desarrollo de arquitecturas de sistemas eléctricos avanzados.
Bas Veldman, director de programa de GKN Fokker (Hoogeveen, Países Bajos) y director de proyecto de STUNNING, explica que el MFFD tendrá 8 metros de largo y 4 metros de ancho con un radio de 2 a 2,5 metros, que es la escala real para un pasillo único. Aviones de la familia A320. "Es similar a la A321, que no es exactamente circular, sino que tiene una forma de huevo (un poco más alta que ancha)", agrega.
La sección inferior del fuselaje de 180 ° comprenderá la carcasa inferior del fuselaje con largueros y marcos soldados, la cabina y la estructura del piso de carga, y los elementos principales del interior y del sistema relevantes. “Entregaremos módulos grandes y equipados previamente para un ensamblaje plug-and-play muy rápido”, dice Veldman.
GKN Fokker es el socio principal de STUNNING y tiene cuatro divisiones que participan, incluidas Aerostructures (Papendrecht, Países Bajos), Fokker ELMO (Hoogerheide, Países Bajos), GKN Fokker Engineering Romania (Bucarest) y GKN Fokker Technologies (Papendredcht, Países Bajos). GKN Fokker ELMO es un proveedor de mazos de cables para aeronaves y tecnología de sistemas eléctricos. “Es responsable de la arquitectura de sistemas en STUNNING y se enfocará en optimizar el sistema eléctrico”, explica Veldman, “y colabora con el consorcio CFP08 MISSION en el desarrollo de un innovador sistema de bus de energía”.
“Diehl Aviation (Laupheim, Alemania) es responsable de la estructura interior, incluidos los subsistemas y el piso, los paneles de las paredes laterales y cómo se unen, las interfaces de monumentos y los multipuertos del sistema inteligente”, continúa Veldman. "NLR (Centro Aeroespacial de los Países Bajos, Ámsterdam) es responsable de la fabricación de la piel del fuselaje y los largueros, y TU Delft está ayudando con el montaje, basándose en su experiencia con la soldadura ultrasónica". (Consulte "Soldadura de compuestos termoplásticos" para obtener más información sobre la soldadura ultrasónica).
Programa de prueba de soldadura MECATESTERS
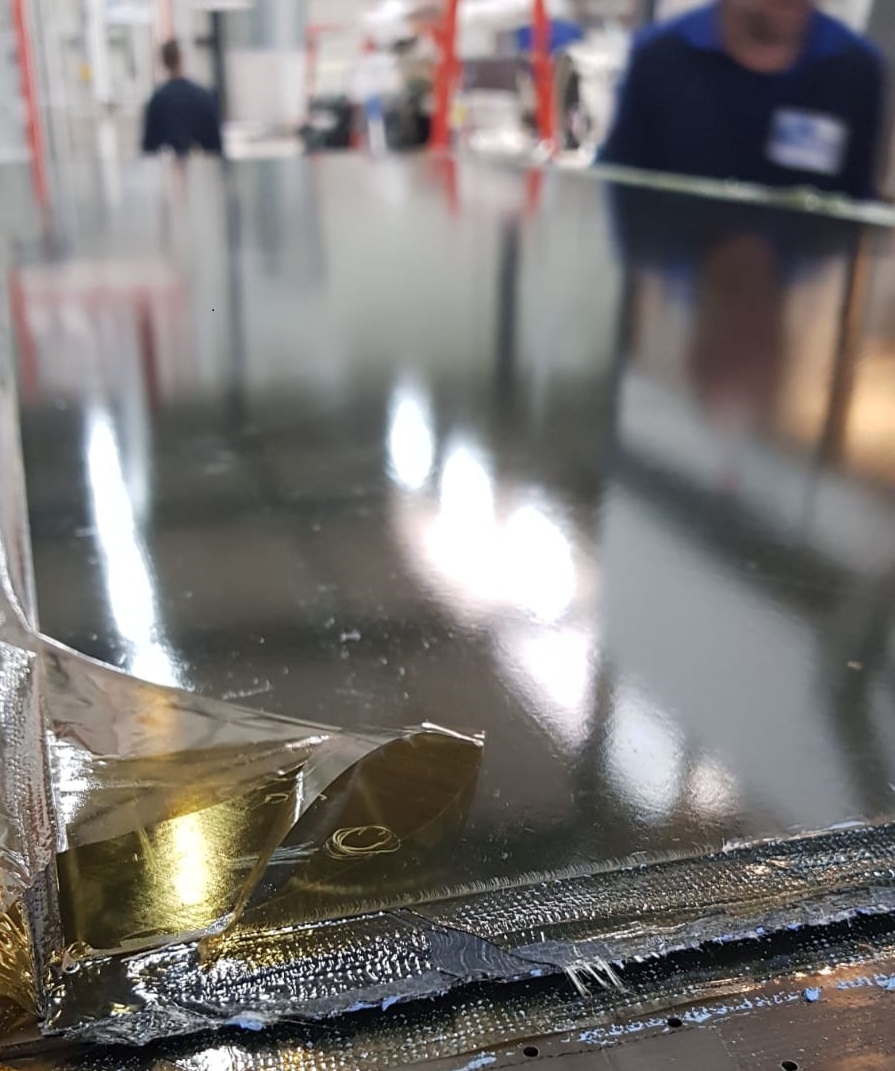
“STUNNING ha lanzado siete temas de CFP y cinco han comenzado a trabajar, incluidos MAYA, MISSION, EMOTION, TCTool y MECATESTERS”, dice Veldman. Este último es un gran programa de prueba de soldadura con KVE Composites (La Haya, Países Bajos) y Rescoll (Pessac, Francia) que comenzó en abril de 2019 con una duración de 30 meses. Veldman explica que, aunque KVE tiene una larga historia con la soldadura por inducción de compuestos termoplásticos de tela y cinta UD, las piezas soldadas por inducción que vuelan en aviones hasta la fecha han utilizado tela. "En STUNNING estamos estableciendo las mejores prácticas con refuerzos UD y materiales LM PAEK, y también comparando la soldadura por inducción con la soldadura por conducción en condiciones ambientales y de carga en servicio típicas". Aunque la soldadura por resistencia y la soldadura ultrasónica se incluyen en otros paquetes de trabajo de MFFD y CFP (consulte “ Uniendo las dos mitades ”A continuación), la soldadura por inducción y la soldadura por conducción son las únicas dos técnicas en MECATESTERS.
Labordus en KVE explica que para los tres paquetes de trabajo MECATESTERS (WP 1, 2 y 3), KVE hará todos los laminados de prueba utilizando cinta de fibra de carbono TC1225 UD / LM PAEK curada en autoclave (consulte “Primer laminado Toray LM-PAEK para Proyecto Clean Sky MECATESTERS ”). KVE también preparará muestras soldadas por inducción para las pruebas, mientras que GKN Fokker producirá muestras soldadas por conducción y Rescoll realizará todas las pruebas físicas. “El nombre Rescoll deriva de la investigación y el collage, que en francés significa vinculación”, dice Labordus. "Son conocidos por su investigación sobre todos los tipos de unión y ofrecen un laboratorio de pruebas bien equipado para polímeros y compuestos, que incluyen mecánica, ambiental, inflamabilidad y todas las pruebas posibles para calificar en las industrias aeroespacial, automotriz, ferroviaria y otras".
Parámetros y pruebas de proceso
“De hecho, estamos comenzando con WP 2 para establecer los parámetros del proceso, como los límites superior e inferior para la temperatura y la presión de la soldadura por inducción”, dice Labordus. "Por ejemplo, tenemos un nominal presión que usamos normalmente, pero iremos a presiones más bajas hasta que comencemos a ver defectos como huecos, y luego evaluaremos esas propiedades de soldadura para establecer el límite de presión más bajo ". Las pruebas también evaluarán la velocidad de la soldadura, que afecta la tasa de enfriamiento y cristalinidad de la soldadura, y potencialmente las propiedades mecánicas. Los mismos parámetros se investigarán en Fokker para la soldadura por conducción.
Para la evaluación, el programa MECATESTERS realizará múltiples pruebas, que incluyen:
- Prueba de cizallamiento según ASTM D5868–01
- Prueba de tracción y cizallamiento en cupones de perfil en L
- GIC y GIIC según ISO 15024 e ISO 15114, respectivamente
(esta prueba de resistencia se completará en el WP 1)
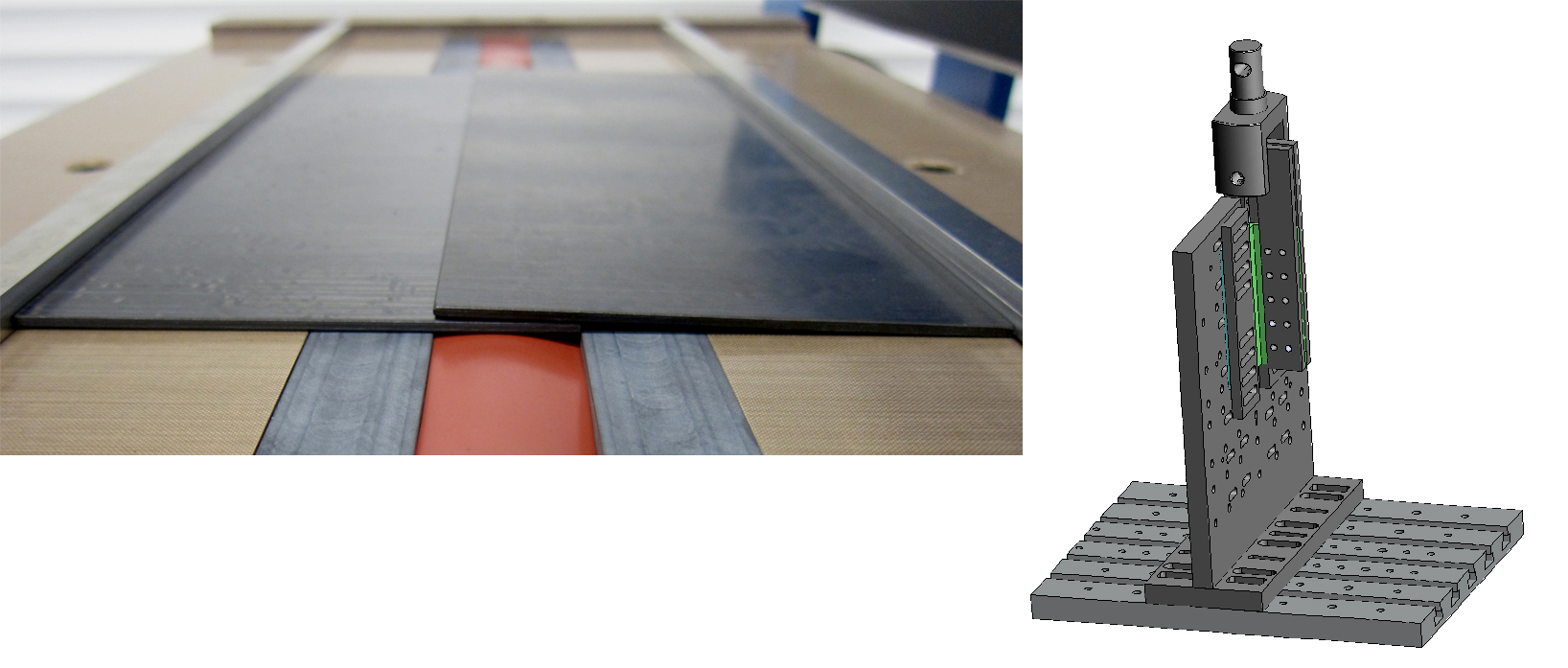
Cupón de cizallamiento de solapamiento de laminado de cinta UD listo para soldadura por inducción (izquierda) y accesorio de prueba para pruebas combinadas de corte y desprendimiento de cupón de perfil en L soldado utilizando la herramienta desarrollada por Rescoll (derecha). FUENTE | KVE Composites, Rescoll.
“El método de prueba de extracción proviene de un estándar interno que ha desarrollado GKN Fokker”, explica el ingeniero de Rescoll Thomas Salat. “La prueba de arranque de los perfiles soldados es perpendicular a la piel para la carga de desprendimiento”, señala Labordus, “y paralela a la piel para la carga de corte. Pelar y cortar son los dos extremos, pero también probaremos nuevas combinaciones de estos que reflejen las condiciones prácticas de carga en servicio ". Esta prueba se completará para dos espesores de laminado distintos derivados del diseño del fuselaje del MFFD - 2,2 y 2,8 milímetros - a temperatura ambiente (RT), temperatura fría (-55 ° C) y temperatura alta (80 ° C) utilizando carga estática.
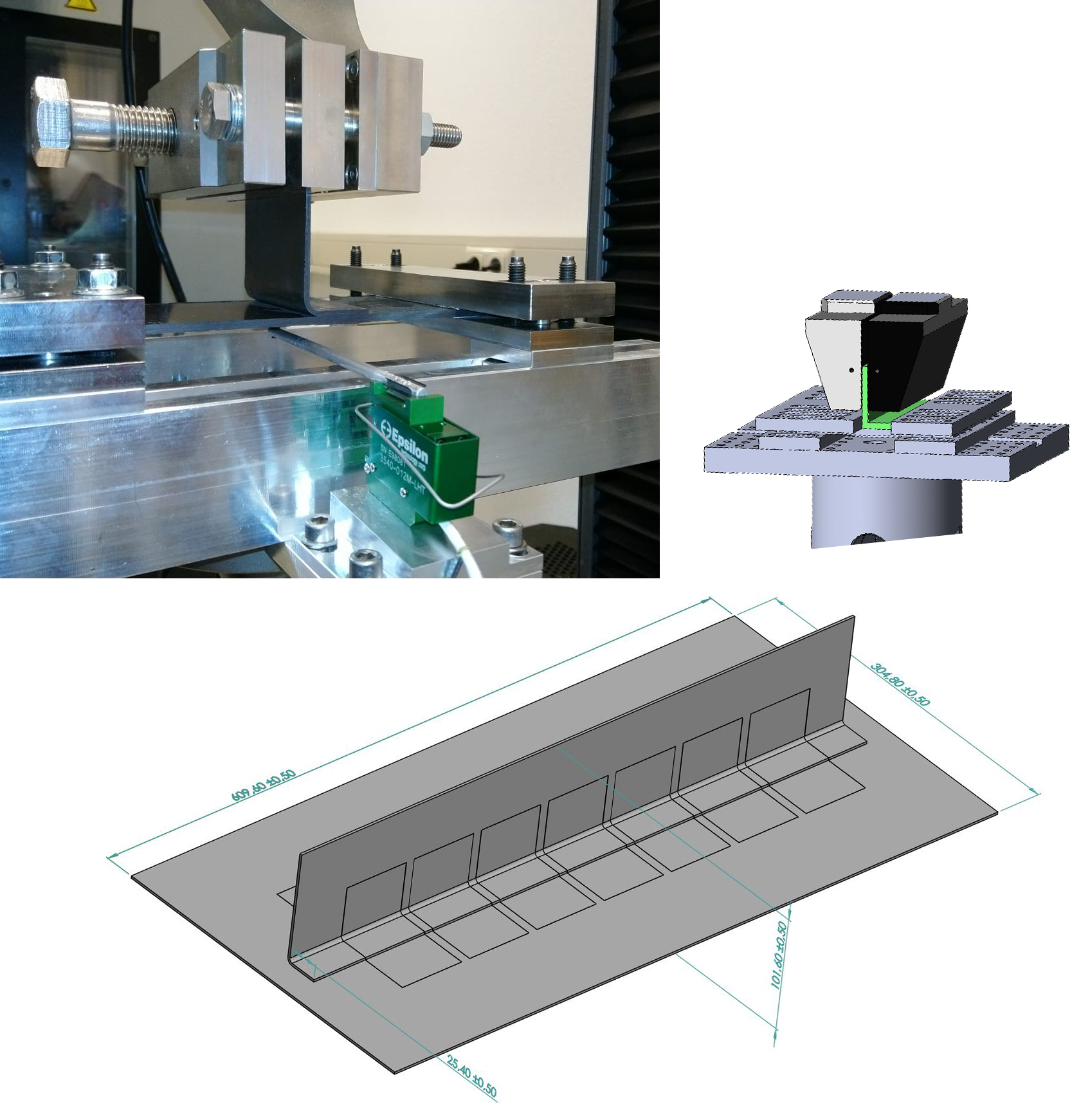
Pruebas de extracción en cupones de perfil L en KVE Composites (arriba a la izquierda). En MECATESTERS, este tipo de prueba utilizará una pinza y una configuración de prueba desarrollada por Rescoll para eliminar la desviación de la piel (arriba a la derecha). Los cupones de prueba se cortarán de paneles soldados (parte inferior). FUENTE | Rescoll, KVE Composites.
Preparación de superficies, envejecimiento y fatiga
WP 1 comenzará con pruebas de resistencia. “Para las pruebas de fisurización (GIC y GIIC), iniciaremos una grieta en el material compuesto y mediremos cómo se comporta esta grieta cuando se carga”, explica Salat. “Una es una prueba estática que aumenta la carga hasta que falla. También haremos una prueba dinámica en la que repetimos la carga estática un millón de veces, que tarda de una a dos semanas en completarse. Veremos si la soldadura compuesta puede soportar esta fatiga. Este modo II es un nuevo tipo de prueba cíclica. Estamos desarrollando un método tomado de un documento técnico publicado por la Universidad de Europa y finalizando los parámetros ahora ”.
También en WP 1, los parámetros de soldadura establecidos en WP 2 se utilizarán para examinar los efectos de la preparación de la superficie, así como el envejecimiento y la fatiga. “Observaremos los contaminantes de la superficie y cómo estos pueden afectar la soldadura”, dice Labordus. “También investigaremos tres tipos diferentes de agentes de liberación que se utilizan comúnmente en el procesamiento de prensa y autoclave; tipos específicos de preparación de superficies que incluyen lijado, abrasivos y tratamiento con plasma; y también el uso de una película de resina adicional en la superficie que se está soldando. Además, estudiaremos la influencia de la orientación de la fibra, por ejemplo, más / menos 45 grados en la interfaz de soldadura ”.
Rescoll también utilizará una cámara de acondicionamiento a 70 ° C y 90% de humedad para simular el envejecimiento en servicio, dice Salat. "Luego realizaremos las pruebas estándar para ver si afecta el rendimiento de la soldadura". Labordus agrega que se tomará un número limitado de muestras a 100 ° C y 120 ° C, "para validar la afirmación de que los compuestos termoplásticos no tienen una caída brusca por encima de los 80 ° C".
Además de la prueba de fisurización dinámica / GIIC, la prueba de fatiga se realizará en los modos de corte y arranque de una sola vuelta. “Comenzaremos con el 80 por ciento de la carga de falla estática y llegaremos al 50 o 75 por ciento de esta en fatiga durante un millón de ciclos”, dice Labordus. “También haremos otras pruebas, pero todavía las estamos discutiendo”, agrega Salat.
Soldadura a soportes compuestos cortos
Aunque los detalles de WP 3 aún se están ultimando, su objetivo es investigar las soldaduras de los soportes moldeados por compresión hechos de material de fibra corta a la piel laminada UD. “Volveremos a comparar los parámetros del proceso y caracterizaremos las propiedades mecánicas de la soldadura”, dice Labordus, “pero todavía estamos trabajando para definir la geometría para la prueba”.
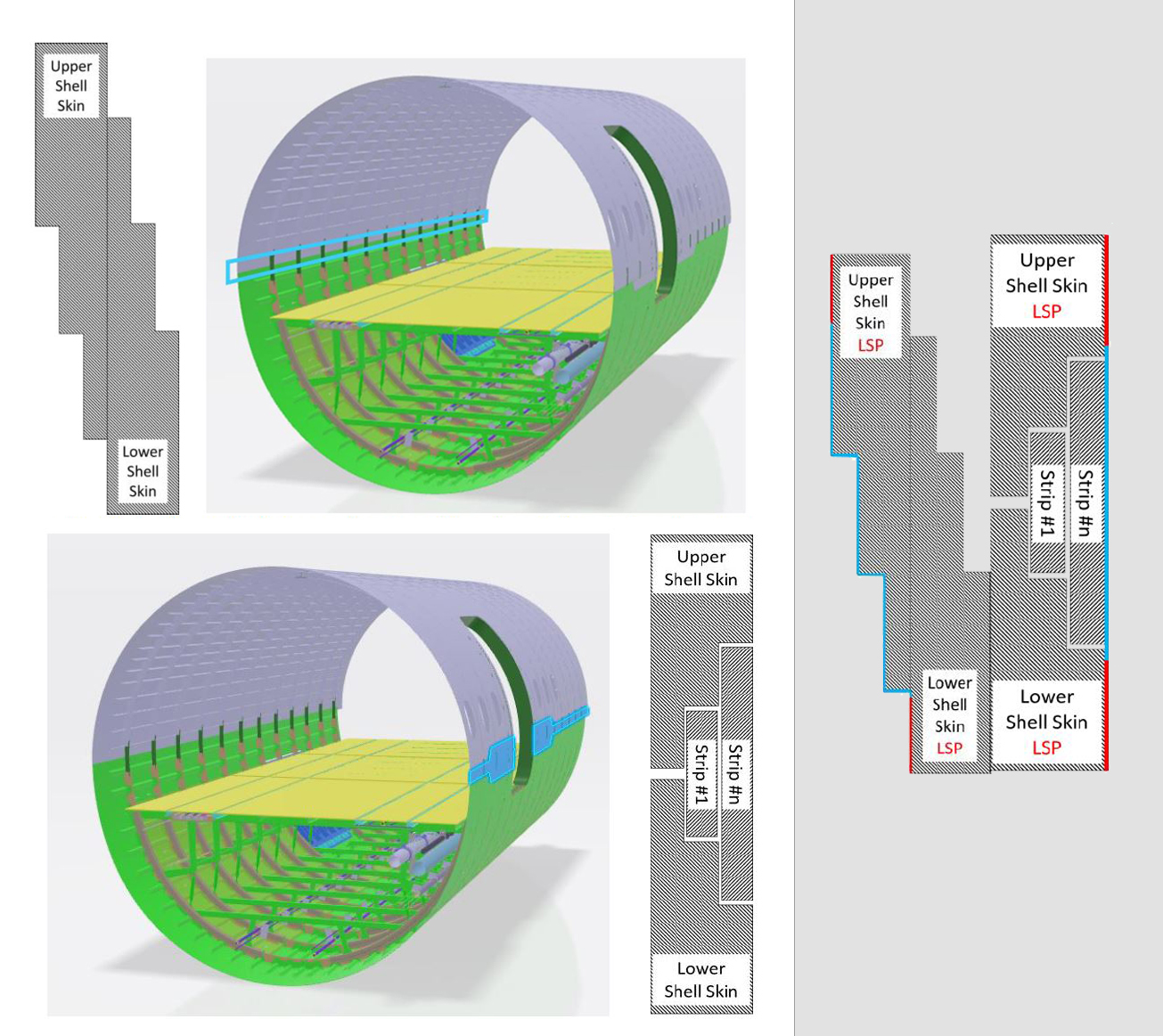
Largueros y clips soldados a un fuselaje termoplástico. FUENTE:Clean Sky 2 11 th Convocatoria de propuestas JTI-CS2-2020-CfP11-LPA-02-35, “Características innovadoras de detención de desprendimiento para juntas soldadas termoplásticas largas”, Figura 2, p. 94.
Clips y soportes soldados
Como se describe en el tema JTI-CS2-2019-CfP10-LPA-02-31 del CFP10, todos los clips del marco y los soportes del sistema para el fuselaje inferior del MFFD se fabricarán mediante moldeo por inyección de compuestos de fibra corta fabricados mediante la reutilización de desechos de fábrica de el director de temas de la producción de laminados TPC de fibra continua de GKN Fokker. CF / PAEK es el material de referencia y la soldadura es el método de unión de referencia, aunque no se prescribe el método de soldadura específico.
De acuerdo con el texto CFP10, el fuselaje inferior del MFFD tendrá 13 marcos y alrededor de 36 largueros, lo que requerirá aproximadamente 500 clips de marco (tenga en cuenta que estas son estructuras primarias que requieren pruebas estructurales y este total incluye clips utilizados para pruebas) y aproximadamente 270 soportes del sistema (que son estructuras secundarias) divididas según los tipos que se muestran a continuación:20 soportes del sistema (1), 120 soportes del sistema (2), 50 soportes del sistema (3) y 80 soportes del sistema (4).
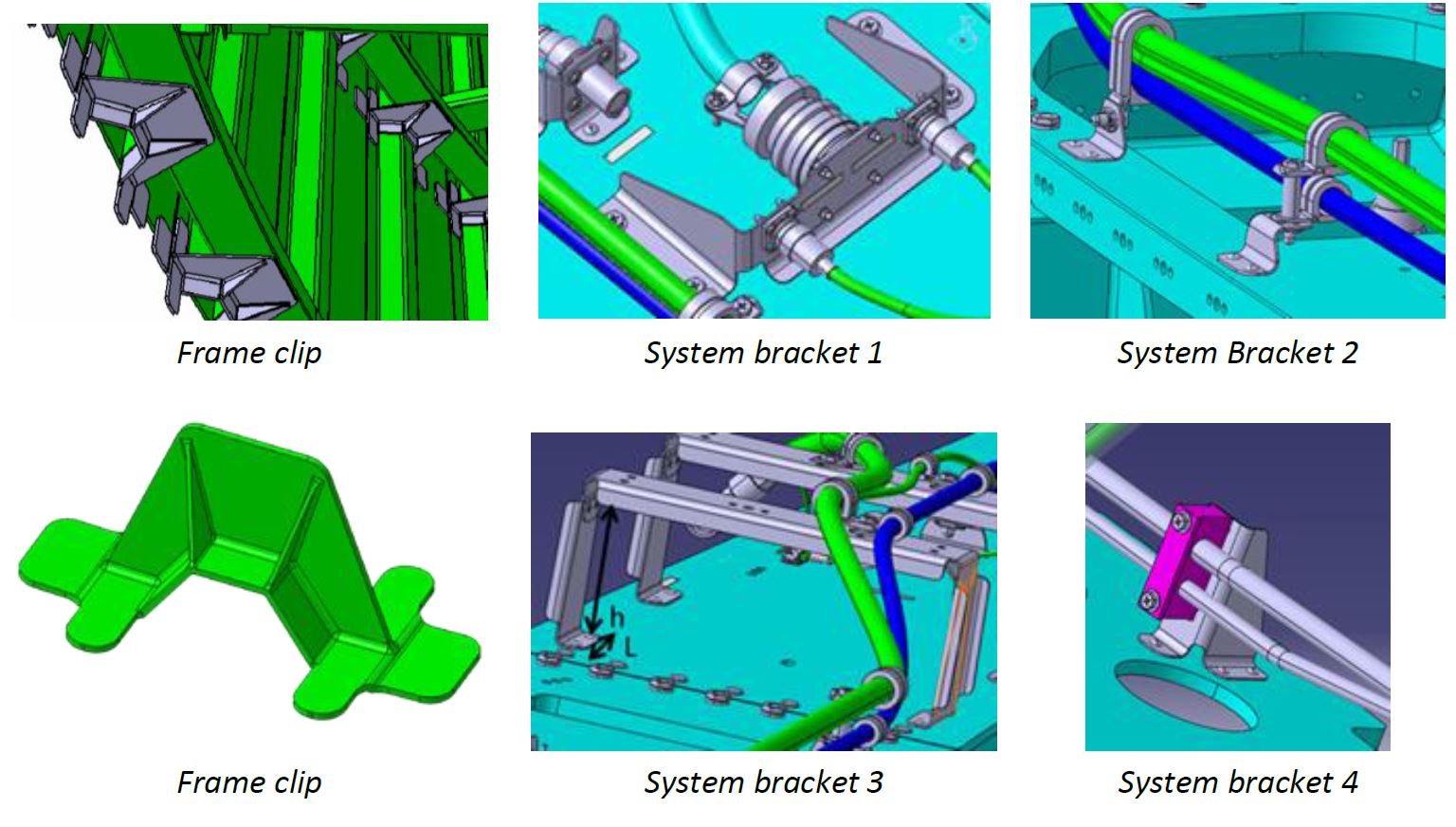
Ejemplos de piezas que se entregarán en Clean Sky 2 tema JTI-CS2-2019-CfP10-LPA-02-31, Figura 2. FUENTE | Clean Sky 2 CFP10, pág. 146.
También en CFP10 está el tema de fuselaje superior MFFD JTI-CS2-2019-CfP10-LPA-02-30, “Desarrollo de sistemas de soldadura innovadores para juntas estructurales de Composites Termoplásticos a base de matrices” liderado por Aernnova Composites Illescas (Illescas, España). Programado para comenzar después del 1T 2020, su objetivo es desarrollar un sistema de soldadura para lograr una unión estructural entre las piezas de refuerzo (refuerzos, cuñas, accesorios) y los marcos estructurales para obtener una Estructura envolvente de puerta (DSS) altamente integrada. Espero dar más detalles sobre el fuselaje superior del MFFD en un futuro blog. Por ahora, es suficiente entender por qué el paquete de trabajo 3 de MECATESTERS es importante y cuánto se logrará una vez que se completen MECATESTERS, STUNNING y el MFFD.
Uniendo las dos mitades
Una vez completado, la mitad inferior del MFFD irá al Instituto Fraunhofer de Tecnología de Fabricación y Materiales Avanzados IFAM (Stade, Alemania) para unirse con la mitad superior, explica Veldman. "Estamos comprometidos a entregar nuestra mitad del fuselaje para fines de 2021", agrega.
Como se señaló anteriormente, Ralf Herrmann en Airbus es el líder del proyecto MMFD; Así, Airbus integra el trabajo de Fraunhofer IFAM y el consorcio CFP07 MultiFAL (Sistema de automatización multifuncional para la línea de montaje del fuselaje), que se encarga de unir las dos mitades del fuselaje, trabajando en conjunto con los equipos STUNNING y superior del fuselaje. —Para desarrollar soluciones para los innumerables desafíos.
Algunos de estos se revelan dentro de dos temas en el 11 th Convocatoria de propuestas (noviembre de 2019), ambas dirigidas por Airbus para comenzar después del cuarto trimestre de 2020 y tituladas "Herramientas, equipos y auxiliares para el cierre de una junta cilíndrica longitudinal":
- JTI-CS2-2020-CfP11-LPA-02-33, ":Integración de la correa de tope y continuidad de la protección contra rayos"
- JTI-CS2-2020-CfP11-LPA-02-34, ":Integración de unión superpuesta y acoplamiento de marco"
Escrito por Piet-Christof Woelcken, director de temas de Airbus Bremen y líder del paquete de trabajo de MFFD, los principales desafíos en estos temas incluyen:
JTI-CS2-2020-CfP11-LPA-02-33
- Unión de correa a tope (Fig. 3 a continuación):
- El lado izquierdo del demostrador (en la dirección del vuelo) incluye el borde de la puerta del pasajero. La variación del grosor de la piel en esta área requiere una integración escalonada de la correa del trasero, uniendo las pieles superior e inferior.
- Dada la complejidad de la junta, soldadura por conducción el uso de una placa de presión calentada es la tecnología de unión preferida.
- Continuidad eléctrica de la protección contra rayos (Fig. 4 a continuación):
- La continuidad eléctrica de la protección metálica contra rayos (LSP) debe lograrse a través de ambas juntas longitudinales en el exterior del fuselaje.
- Se espera que el cabezal de herramientas provisto para la integración de la correa de tope se pueda usar para este propósito.
JTI-CS2-2020-CfP11-LPA-02-34
- Junta superpuesta (Fig. 2 a continuación):
- La junta de superposición de 8 metros de largo en el lado derecho de los demostradores (en la dirección de vuelo) conecta las cubiertas superior e inferior del fuselaje. En una dirección longitudinal, el espesor de la piel por debajo de 3 mm es constante en la zona de soldadura. En la dirección circunferencial, los revestimientos presentan una geometría escalonada para mejorar el rendimiento estructural.
- Soldadura ultrasónica es la unión preferida para lograr una alta tasa de producción.
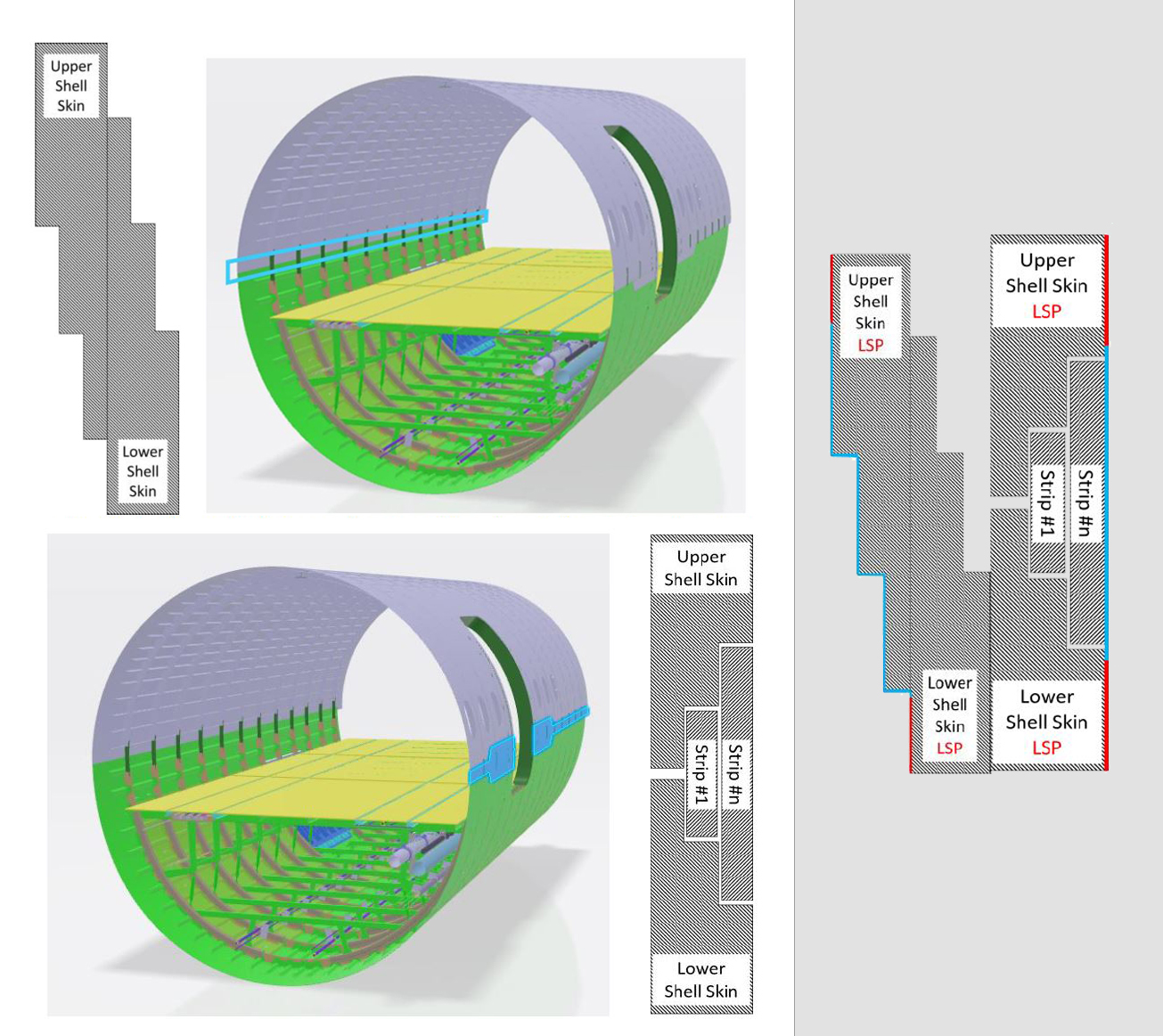
Fig. 2 (arriba a la izquierda) :Junta superpuesta:se ha adoptado un enfoque escalonado en el diseño de la junta superpuesta. Tenga en cuenta que la carcasa inferior se encuentra en el lado interior del fuselaje. Fig. 3 (Abajo a la izquierda) : Integración de la correa a tope:varias tiras superpuestas requieren integración a través de la junta escalonada. Tenga en cuenta que la correa de tope se encuentra en el exterior del fuselaje. Fig. 4 (derecha) :Se debe lograr la continuidad eléctrica del LSP metálico a través de las juntas longitudinales en el exterior del fuselaje del CFRP. El rojo indica LSP preequipado, el azul indica LSP que se aplicará como parte de este tema. FUENTE | Clean Sky 2 11 th Convocatoria de propuestas JTI-CS2-2020-CfP11-LPA-02-33 y -34, “Integración de la correa de tope y continuidad de la protección contra rayos”, págs. 78 y 86.
JTI-CS2-2020-CfP11-LPA-02-34
- Integración de acoplamiento de marco (Fig. 5):
- Junta superpuesta:los acoplamientos del marco debajo de la junta superpuesta deben unir estructuralmente los marcos de la carcasa superior e inferior.
- Correa para el trasero:los acoplamientos del marco debajo de la correa para el trasero deben unir estructuralmente los marcos de la carcasa superior e inferior, así como conectarse a la piel.
- Soldadura por resistencia es la tecnología preferida para este desafío técnico.
Integración de acoplamiento de bastidor. Tenga en cuenta que los acoplamientos del bastidor difieren por lado como parte de la demostración de tecnología. FUENTE | Clean Sky 2 11 th Convocatoria de propuestas JTI-CS2-2020-CfP11-LPA-02-34, “Utillajes, equipos y auxiliares para el cierre de una junta cilíndrica longitudinal:junta superpuesta e integración del acoplamiento del marco”, Fig. 5, pág. 86.
Métodos de soldadura, cabezales de herramientas y tolerancias
Herrmann explica que la soldadura por conducción se demostrará en el lado izquierdo a través de la unión de la correa a tope y la soldadura ultrasónica en el lado derecho a través de la unión de superposición, mientras que la soldadura por resistencia se utilizará para los acoplamientos del marco. “MFFD demostrará muchos enfoques técnicos, por lo que no es lo mismo que en la fabricación de un fuselaje real, sino que está diseñado como un vehículo para demostrar y madurar tecnologías”, agrega.
Desarrollo de cabezales de herramientas de soldadura
El objetivo de estos dos temas escritos por Woelcken es desarrollar los cabezales de herramientas necesarios para estas uniones soldadas. “Cuando sueldas dos piezas juntas, debes aplicar calor y presión”, explica. “Entonces, esto es aplicado por el cabezal de herramientas durante la soldadura. Para el proceso de soldadura por conducción tipo Fokker, se aplica activamente calor y presión en un lado y se ejerce presión pasiva desde un soporte en el otro. La junta a tope es una pila de seis cintas, y en la unión colocaremos la pila y la calentaremos durante la soldadura. Sin embargo, debido a que el material de cinta LM PAEK UD es relativamente nuevo en la soldadura, debemos comprender las condiciones del proceso y cómo podemos compensar las tolerancias. Por lo tanto, debemos definir los materiales y el espesor, así como la geometría del cabezal de herramienta ”.
"Tenga en cuenta que el uso de este tipo de juntas a tope es un proceso estándar para lo que estamos haciendo en otras juntas de nuestra aeronave", señala Woelcken. “Para el MFFD, queremos dejar el fuselaje superior e inferior sin cambios con respecto a esta práctica estándar para minimizar la cantidad de material que tenemos que adaptar”.
Flexibilidad en tolerancias
Woelcken señala que debido a que las superficies de soldadura superiores se funden esencialmente en líquido y luego se presionan juntas, "esto brinda mucha flexibilidad para adaptarse a las tolerancias". Tenga en cuenta, actualmente, con termoestable Alas y fuselajes de polímero reforzado con fibra de carbono (CFRP), estos problemas de tolerancia se abordan aplicando un adhesivo de calce líquido. Aunque pocas personas quieren discutir esto públicamente, el tema general del calce en aeroestructuras compuestas ha sido ampliamente reconocido y se han publicitado iniciativas para reducirlo y / o eliminarlo, como el método de ensamblaje Flexmont para planos de cola verticales.
" Esperamos obtener ventajas al abordar las tolerancias mediante el uso de compuestos termoplásticos ”, dice Woelcken,“ particularmente al explotar nuestros conceptos de diseño y aprovechar nuestra experiencia con CFRP termoestable y soldadura metálica. La clave estará en el monitoreo in situ durante el calentamiento y la aplicación de presión ”. Destaca que el calor es el parámetro número uno. “Me sorprende lo tolerantes que son los procesos de soldadura de compuestos termoplásticos a la presión. El principal desafío es la contención de esa presión y cómo disminuye. Actualmente, estamos monitoreando la parte posterior de la junta soldada ”.
Sistema de planta de ensamblaje automatizado Fraunhofer IFAM (arriba a la izquierda) con dimensiones al comienzo del tema de trabajo CFP07 (arriba a la derecha) se está modificando para acomodar un fuselaje de 360 ° para soldar las juntas longitudinales y circunferenciales del MFFD. FUENTE | Fraunhofer IFAM y cfk-valley.com, Clean Sky 2 7 th Convocatoria de propuestas, JTI-CS2-2017-CfP07-LPA-02-22, p. 76.
Automatización de ensamblajes
En el 7 th Convocatoria de propuestas, el tema JTI-CS2-2017-CfP07-LPA-02-22, “Desarrollo de un sistema de planta automatizado de tamaño completo para juntas longitudinales y circunferenciales del fuselaje” está dirigido por Fraunhofer IFAM dentro del consorcio MultiFAL. El extracto a continuación arroja algo de luz sobre cómo se podrían implementar los cabezales de herramientas de soldadura discutidos anteriormente, ahora en desarrollo:
“Para realizar el proceso de ensamblaje de un fuselaje termoplástico, las tolerancias se convierten en un tema importante. The positioning and orientation of the fuselage shells, as well as resulting deformations caused by the welding process, need to stay within the tolerances. Comparable accuracies can be oriented to the state-of-the-art process of longitudinal joint. Here, the position error in each direction should be within 0.5 mm (in some exceptions up to 1 mm). … it can be assumed that a pre-load on the joint surface from both sides of approximately 1000N (independent of the welding technology) for a welding seam of 20 mm width is required by the automation system.”
Fraunhofer IFAM — which was also CTC Stade’s partner in developing the Flexmont VTP assembly process — describes its starting point:an in-house assembly plant system which can manipulate parts from 2 to 8 meters long and up to 6 meters high, including a 180° shell of a single-aisle aircraft. The system is enabled by a flexible arrangement of 10 cooperating hexapods (see “Reconfigurable Tooling:Revolutionizing composites manufacturing”), 24 linear units and modular rack elements. Vacuum grippers with 6-axis force and torque sensors adjust the pose and shape of the part, as required, to manage tolerances during assembly. The guidance and monitoring of these rapid, iterative adjustments is achieved through optical measuring devices.
According to the CFP07 text, Fraunhofer IFAM will modify this assembly plant system for holding a complete 360° fuselage, with work scheduled to begin in Q2 2018 and completed in 36 months.
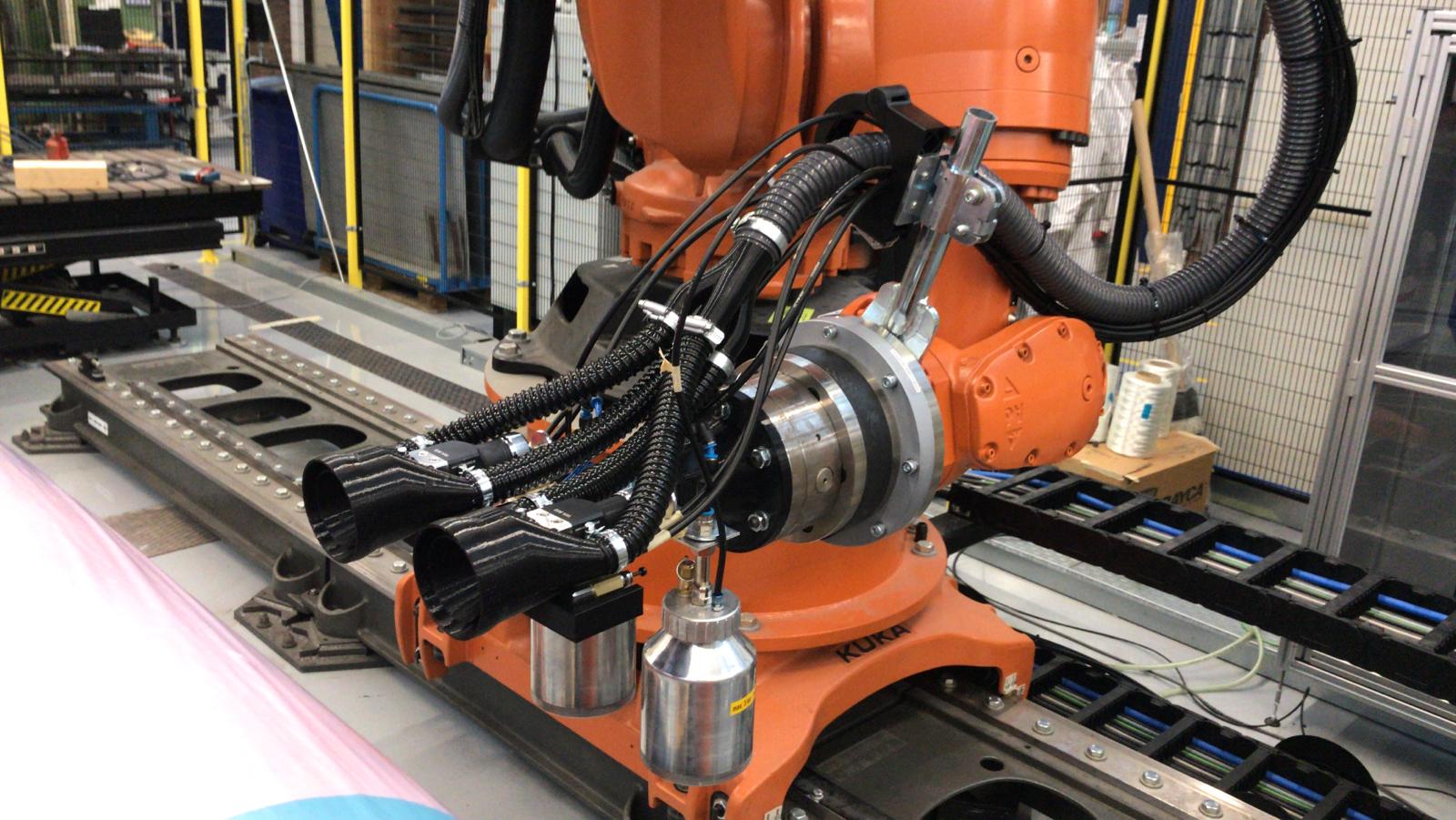
The STUNNING consortium is working with SAM|XL to develop automation for assembling the MFFD lower fuselage. SOURCE | samxl.com
Within STUNNING, activities are planned with the collaborative research center SAM|XL (Smart Advanced Manufacturing XL, Delft, Netherlands) to demonstrate automated welding techniques for assembling the lower fuselage. Specializing in automation for manufacturing large, lightweight composite structures, SAM|XL brings together TU Delft’s Aerospace Engineering group and Robotics Institute. GKN-Fokker is a major participant. One of the methods being investigated is sequential spot ultrasonic welding, which was proven in the Clean Sky 1 Eco Design project and TAPAS 2 as a fast and effective for connecting short fiber-reinforced brackets or clips to fuselage structures.
In her 2016 paper, titled “Smart ultrasonic welding of thermoplastic composites,” Villegas states that it is possible to scale up the ultrasonic welding process via sequential welding — that is, letting a continuous line of adjacent spot welds serve the same purpose as a continuous weld bead. Lab-scale sequential spot welding was used in the Clean Sky EcoDesign demonstrator’s TPC airframe panel, using flat energy directors to weld a CF/PEEK hinge and CF/PEKK clips to CF/PEEK C-frames (Fig. 6). Experimental comparisons with mechanically fastened joints in double-lap shear and pull-through tests showed promise. The process is further explored in 2018 papers {and 2019 papers} by Villegas’ TU Delft team member Tian Zhao {and in Villegas’ 2019 paper}.
— “Welding thermoplastic composites”, G. Gardiner, 2018.
The STUNNING consortium’s work with TU Delft and SAM|XL is adapting this technology to weld multiple system and semi-structural brackets, stiffening elements and stringers to the MFFD lower fuselage shell.
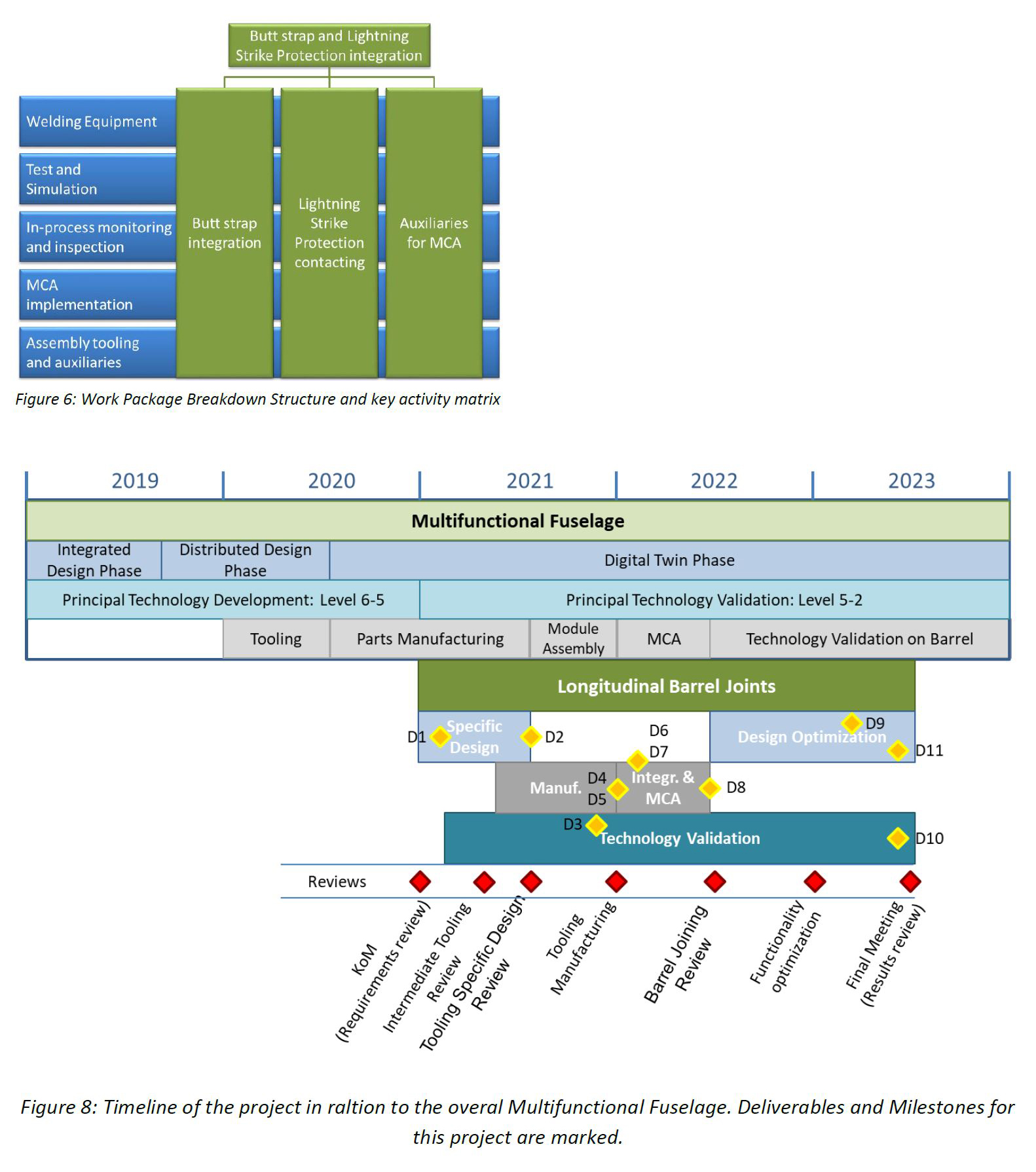
Work breakdown and timeline for MFFD assembly. SOURCE | Clean Sky 2 11 th Call for Proposals JTI-CS2-2020-CfP11-LPA-02-33, “Tooling, Equipment and Auxiliaries for the closure of a longitudinal Barrel Joint:Butt strap integration and Lightning Strike Protection continuity”, pp. 79 and 82.
Digital twin phase, 2020 and beyond
According to the Clean Sky website, the MFFD program reached an important milestone in Nov 2019 with the successful passing of its Critical Design Review (CDR). In the timeline above, the MFFD design enters a “Digital Twin Phase” in 2020-2021. ¿Qué significa esto? “Though we have wrapped up the majority of the design phase, we are taking it a bit further by working with a specific lifecycle management approach,” explains Herrmann. “We are modeling imperfections and nonconformities from the NDT results and process parameters during component manufacturing. We want to combine this Industry 4.0 data with lifecycle management so that we continue to tailor the design according to what we are actually manufacturing. We want to see how far we can push this and what we can accomplish by the end of Clean Sky 2.”
For 2020, the chief agenda is manufacturing. “We hope to present various parts as they come together this year,” says Veldman. What will the largest challenge be for the STUNNING program? “Assembly,” he answers. “Not so much within STUNNING, but our lower fuselage has interfaces with the door surround structure, multiple Airbus-delivered components and the whole upper fuselage. Getting everything delivered at the right time and then bringing it all together will require a number of developments yet.”
That brings us to perhaps the biggest question:Will thermoplastic composites be used on the next aircraft entering production in 2030-35? “For sure, we want to try to use the technologies we are working on,” says Herrmann, “but I cannot say if or when thermoplastic composites will be on future aircraft. The most important part for us is that they are an enabler for dustless joining regarding ramping production to more than 70 aircraft per month. We have to show that it is feasible, not only with metallics but also with thermoplastic composites.”
“By the end of this project, we will have a more complete understanding of thermoplastic composite welding and will gain approval for its use in large primary aircraft structures,” says Salat. “If we can use this for future aircraft, we can achieve significant weight savings and improved sustainability.” But perhaps just as important is Clean Sky’s ability to bring Europe’s aviation research and innovation stakeholders closer together. “We have quarterly meetings where I sit with all of the LPA steering committee,” says Veldman. “I’m talking to the whole of the European aerospace industry, and it most certainly helps to open up opportunities for the future, not only for companies who can supply to us, but for a wide range of collaborations.”
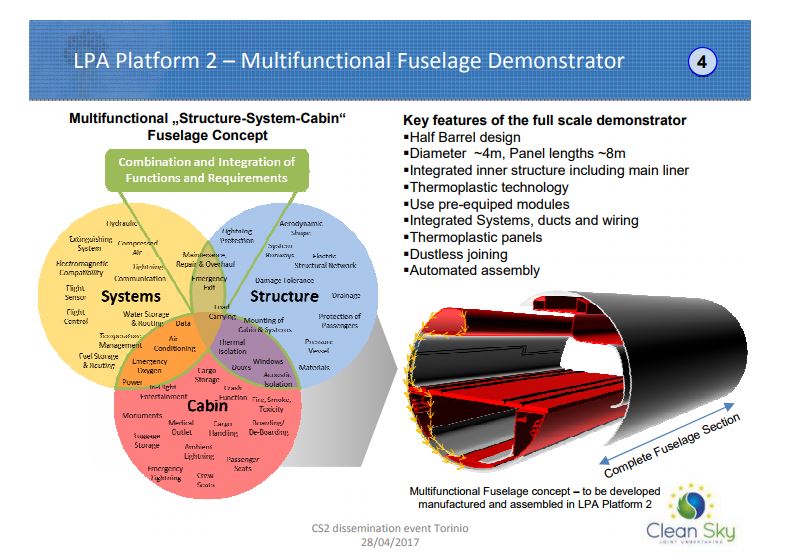
Resina
- 10 startups de impresión 3D a tener en cuenta en 2020
- Aplicación destacada:Impresión 3D para cabinas de aviones
- Exprimir el valor de los datos para AI
- 6 consejos de soldadura para el mantenimiento de la planta
- ¿Busca un plástico ultrarresistente? ¡Echa un vistazo a FR-4!
- Materiales:compuestos y concentrados de grado médico para soldadura láser
- Consejos y trucos para soldar Inconel
- Diseño para la fabricación automatizada de composites de aeroestructuras de bajo volumen
- Victrex y Bond se asocian para la impresión 3D de piezas PAEK
- La primera sección de fuselaje compuesto para el primer avión comercial compuesto
- Los mejores consejos para soldar aluminio