Leonardo y CETMA:disrupción de los compuestos para reducir el costo y el impacto ambiental
Este blog se basa en mi entrevista con Stefano Corvaglia, ingeniero de materiales, jefe de investigación y desarrollo y director de propiedad intelectual de la División Leonardo Aerostructures (instalaciones de producción de Grottaglie, Pomigliano, Foggia, Nola, sur de Italia) y el Dr. Silvio Pappadà, ingeniero de investigación y director de programas con Leonardo en CETMA (Brindisi, Italia).
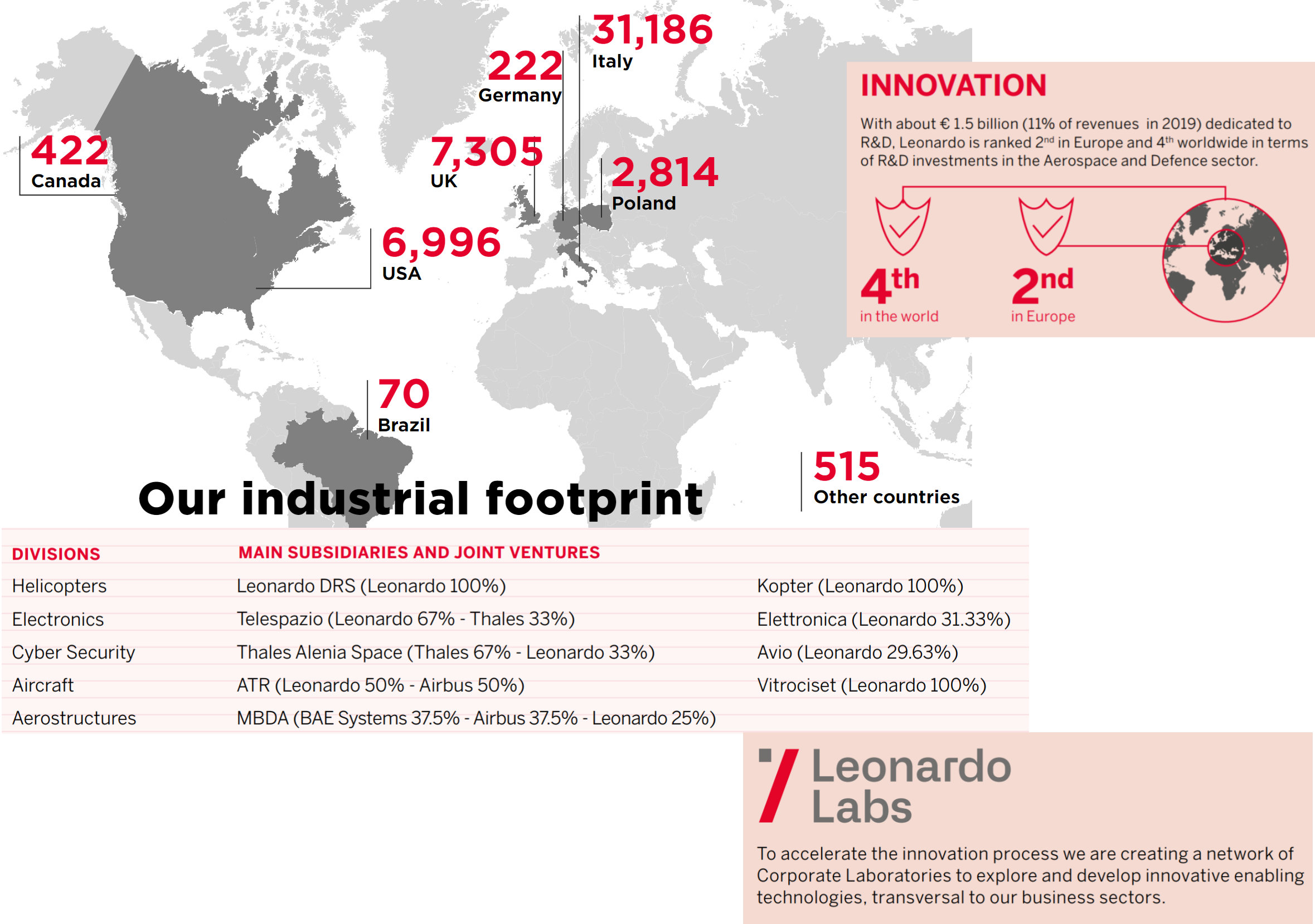
Leonardo (Roma, Italia) es uno de los principales actores del mundo en el sector aeroespacial, de defensa y de seguridad con 13.800 millones de euros en ingresos y más de 40.000 empleados en todo el mundo. La empresa ofrece soluciones integrales a escala global para sistemas aéreos, terrestres, marítimos, espaciales, cibernéticos y de seguridad y no tripulados. Con aproximadamente 1.500 millones de euros (11% de los ingresos en 2019) dedicados a I + D, Leonardo ocupa el segundo lugar en Europa y el cuarto a nivel mundial en términos de inversiones en investigación en el sector aeroespacial y de defensa.
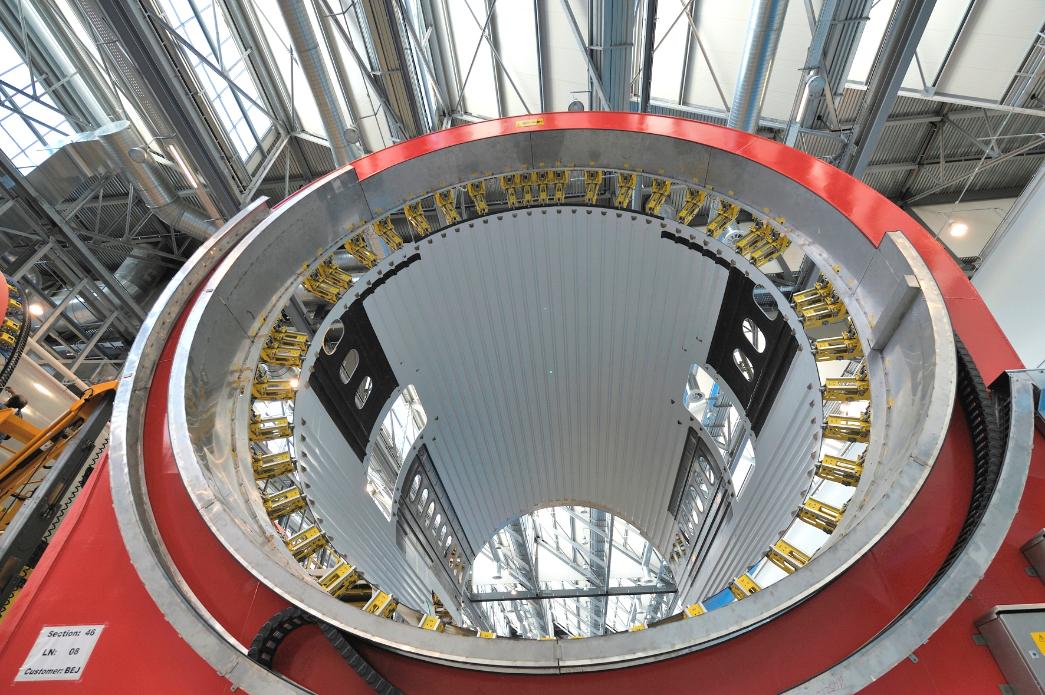
A través de su División de Aeroestructuras, Leonardo proporciona fabricación y ensamblaje de grandes componentes estructurales, incluidos fuselajes y empenajes, en compuestos y materiales tradicionales para los principales programas de aeronaves civiles del mundo.
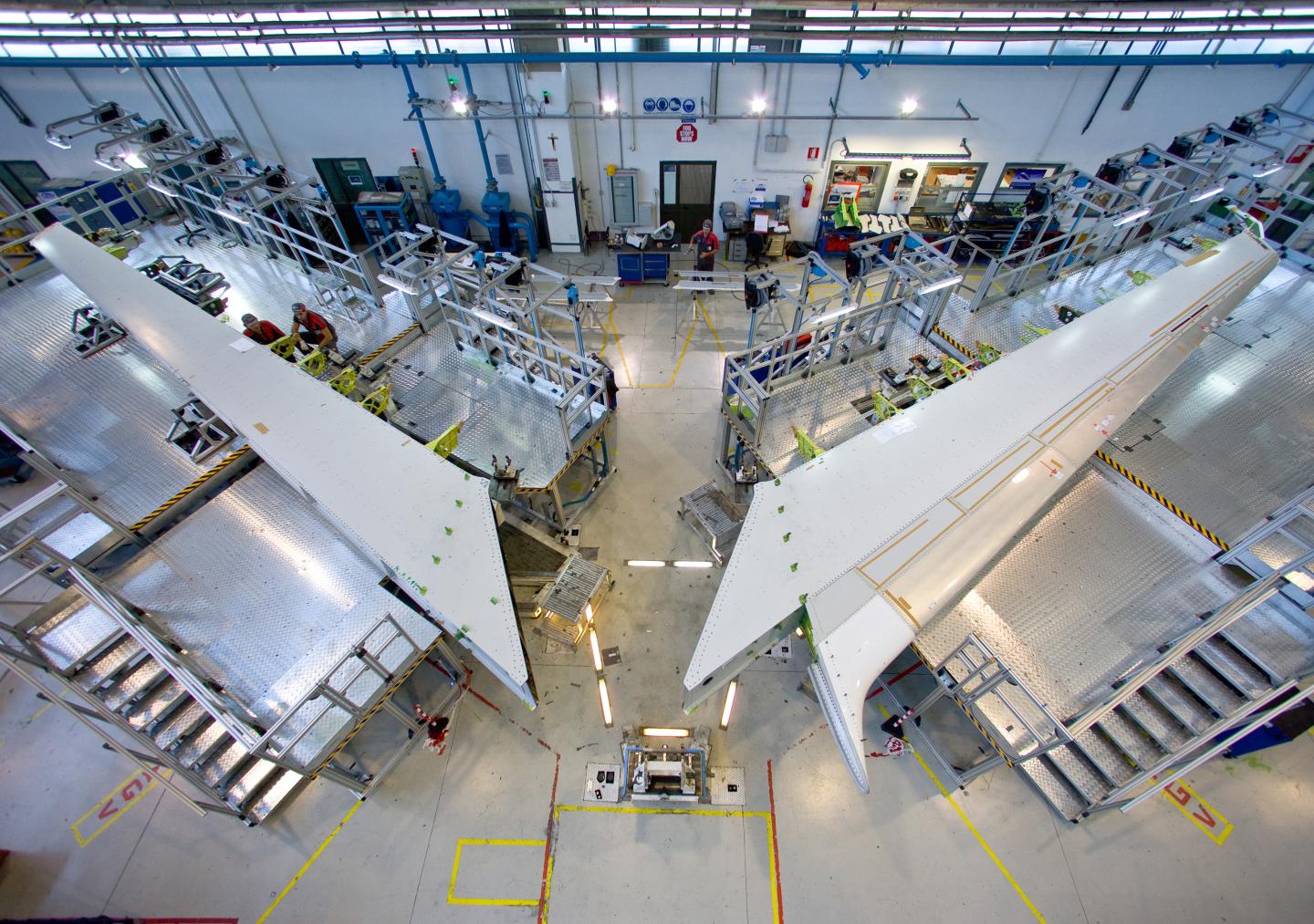
En materiales compuestos, la División Leonardo Aerostructures produce “barriles de una pieza” para las secciones 44 y 46 del fuselaje central del Boeing 787 en su planta de Grottaglie, así como los estabilizadores horizontales en su fábrica de Foggia, que totalizan aproximadamente el 14% del fuselaje del 787. La producción de otras estructuras compuestas incluye, en su planta de Foggia, la fabricación y montaje de empenajes para aviones comerciales ATR y Airbus A220. Foggia también produce piezas compuestas para el Boeing 767 y para programas militares que incluyen el Joint Strike Fighter F-35, el avión de combate Eurofighter Typhoon, el transporte militar C-27J y el Falco Xplorer, el último miembro de la familia Falco de aviones no tripulados producidos por Leonardo.
Trabajar con CETMA
“Tenemos muchas actividades en curso con CETMA, por ejemplo, en compuestos termoplásticos y moldeo por transferencia de resina (RTM)”, dice Corvaglia. “Nuestro objetivo es tener las actividades de I + D listas para la producción en el menor tiempo posible. En nuestro departamento (I + D y gestión de propiedad intelectual), también buscamos tecnologías disruptivas con un TRL más bajo [nivel de preparación tecnológica, es decir, un TRL más bajo es más incipiente y más alejado de la producción], pero buscamos ser más competitivos y ayudar a nuestros clientes en todo el mundo. . ”
“Desde el comienzo de nuestro trabajo conjunto”, añade Pappadà, “siempre hemos buscado mantener bajos los costes y el impacto medioambiental. Hemos descubierto que los compuestos termoplásticos (TPC) ofrecen una reducción en ambos en comparación con los termoestables ".
Corvaglia señala que, "junto con el equipo de Silvio, hemos desarrollado estas tecnologías y construido algunos prototipos de células automatizadas para evaluarlos en producción".
Moldeo por compresión continua (CCM)
“CCM es un buen ejemplo de nuestro trabajo conjunto”, dice Pappadà. "Leonardo identificó algunos componentes fabricados en compuestos termoendurecibles y juntos exploramos la tecnología para proporcionarlos en TPC, observando dónde hay una gran cantidad de piezas en la aeronave, como estructuras de empalme y puntales con geometría simple".
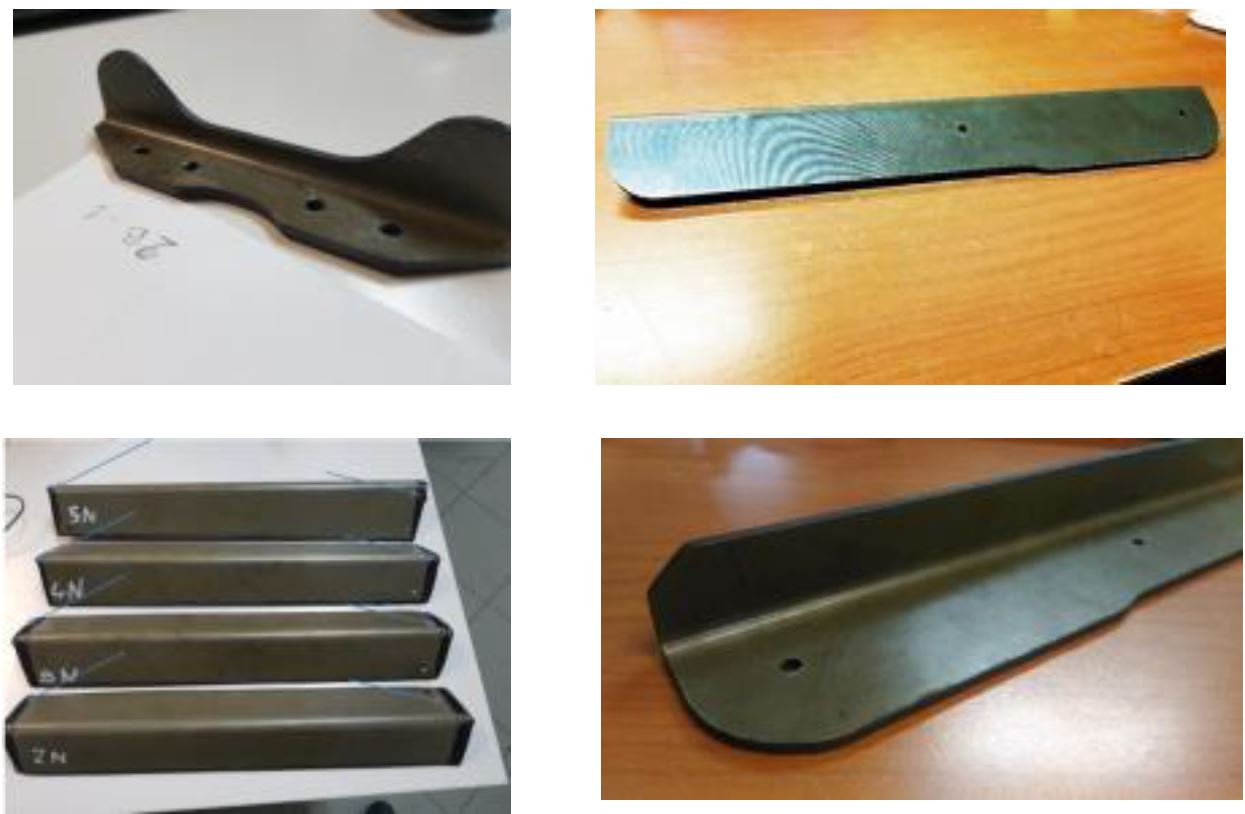
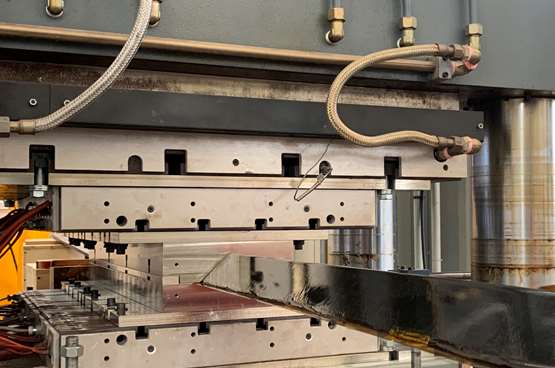
“Necesitábamos una nueva tecnología de producción caracterizada por un bajo costo y una alta tasa”, continúa. Señala que en el pasado, los componentes individuales de TPC se fabricaban con una gran cantidad de residuos. “Entonces, producimos formas de red basadas en moldeo por compresión no isotérmica pero con algunas innovaciones (las patentes están en curso) para reducir la chatarra. Diseñamos una celda totalmente automatizada para esto, que luego una empresa italiana construyó para nosotros ”.
Esta celda es capaz de producir los componentes que diseñó Leonardo, dice Pappadà, “a un ritmo de un componente cada 5 minutos, trabajando las 24 horas del día”. Sin embargo, su equipo tuvo que averiguar la producción de la preforma. “Al principio, necesitábamos un proceso de laminación plana, porque ese era el cuello de botella en ese momento”, explica. “Así que nuestro proceso comienza con un blanco (laminado plano), lo calienta en un horno de infrarrojos (IR) y luego en una prensa para moldear. Los laminados planos se producen generalmente con prensas grandes y requieren un tiempo de ciclo de 4-5 horas. Decidimos investigar un nuevo método capaz de producir laminados planos de forma más rápida. Por lo tanto, desarrollamos una línea CCM de alta productividad en CETMA con el apoyo de los ingenieros de Leonardo. Redujimos el tiempo de ciclo para una pieza de 1 metro por 1 metro a 15 minutos. Es importante destacar que es un proceso continuo, por lo que podemos producir longitudes ilimitadas ”.
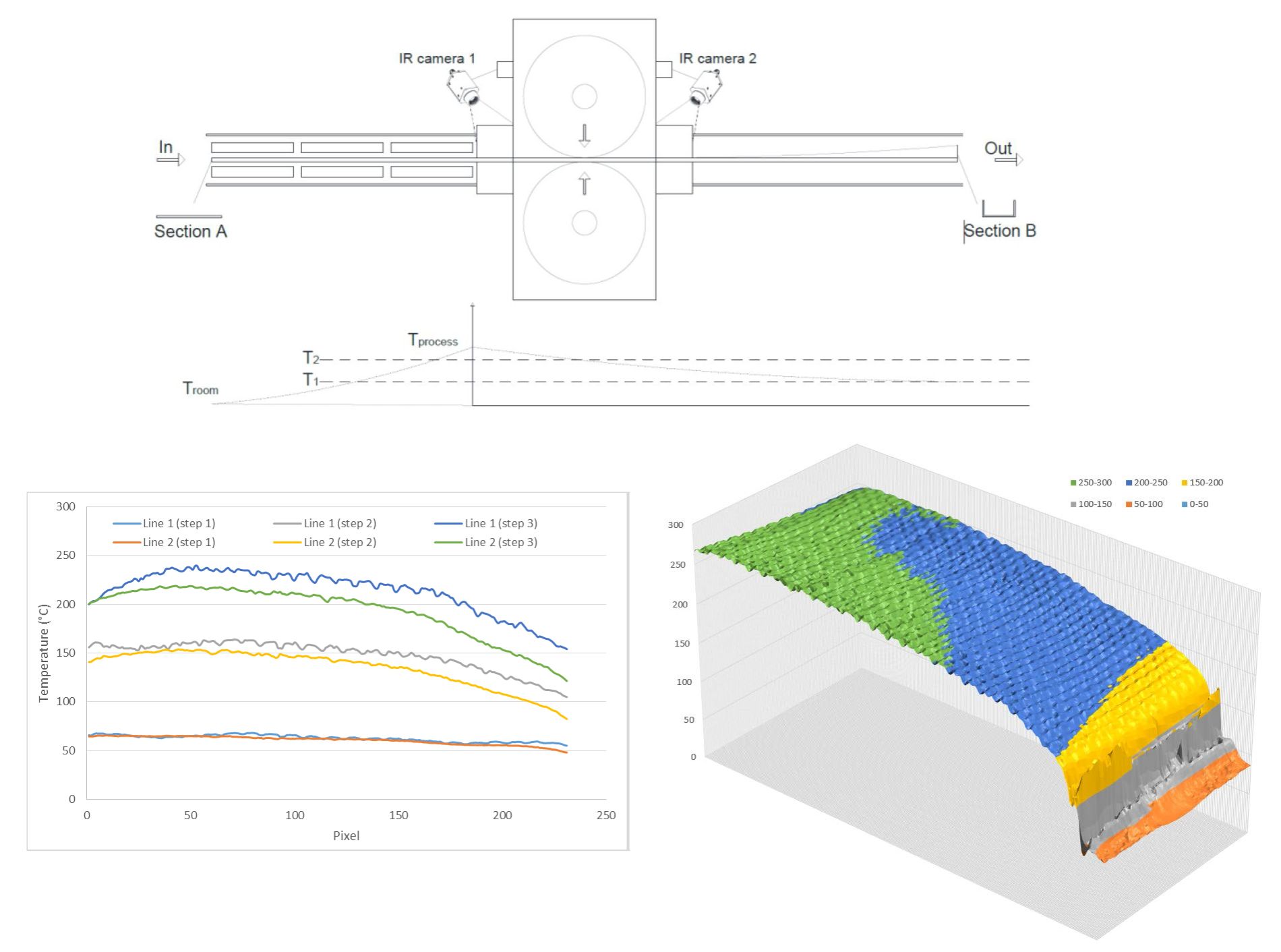
Pero, ¿cómo es esto nuevo en comparación con el CCM utilizado durante más de una década por Xperion, ahora XELIS (Markdorf, Alemania)? “Desarrollamos modelos analíticos y numéricos capaces de predecir defectos como huecos”, dice Pappadà. “Hicimos esto en cooperación con Leonardo y la Universidad de Salento (Lecce, Italia) para comprender los parámetros y su influencia en la calidad. Usamos estos modelos para desarrollar este nuevo CCM donde podemos tener espesores muy altos pero también de alta calidad. Gracias a estos modelos, podemos optimizar la temperatura y la presión pero también cómo aplicarlas. Hay muchos aspectos tecnológicos que puede desarrollar para tener una distribución uniforme de temperatura y presión; sin embargo, necesitábamos comprender el impacto de estos en el rendimiento mecánico y el crecimiento de defectos en las estructuras compuestas ”.
Pappadà continúa, “Nuestra tecnología es más flexible. Además, el CCM se desarrolló hace 20 años, pero no hay información al respecto porque las pocas empresas que lo utilizaron no compartían conocimientos ni know-how. Por lo tanto, tuvimos que empezar de cero, solo con nuestro conocimiento de materiales compuestos y procesamiento ”.
“Ahora estamos trabajando a través de programas internos y con nuestros clientes para encontrar piezas para estas nuevas tecnologías”, dice Corvaglia. "Estas piezas pueden rediseñarse y recalificarse para comenzar la producción". ¿Por qué? “El objetivo es tener un avión lo más ligero posible pero también competitivo en precio. Entonces, también debemos optimizar con espesor. Pero podríamos descubrir que una pieza puede ser aún más liviana o identificar varias piezas con una forma similar, lo que podría permitir ahorros de costos significativos ”.
Hasta ahora, reitera, esta tecnología ha estado en manos de unos pocos. “Pero hemos desarrollado tecnologías alternativas para hacer que estos procesos sean aún más automatizados al agregar un conformado por prensado más avanzado. Colocamos un laminado plano y sale una pieza, lista para usar. Estamos en la fase de rediseño de piezas y desarrollo de CCM planas en lugar de con forma ”.
“Ahora tenemos en CETMA una línea CCM que es muy flexible”, dice Pappadà, “donde podemos aplicar diferentes presiones según sea necesario para lograr formas complejas. La línea que desarrollaremos junto con Leonardo estará más enfocada a componentes que se ajusten a sus necesidades específicas. Creemos que podríamos tener diferentes líneas CCM para paneles planos y largueros en L frente a formas más complejas. De esta manera, podemos mantener el costo del equipo más bajo en comparación con las grandes prensas que se utilizan actualmente para producir piezas de TPC de geometría compleja ”.
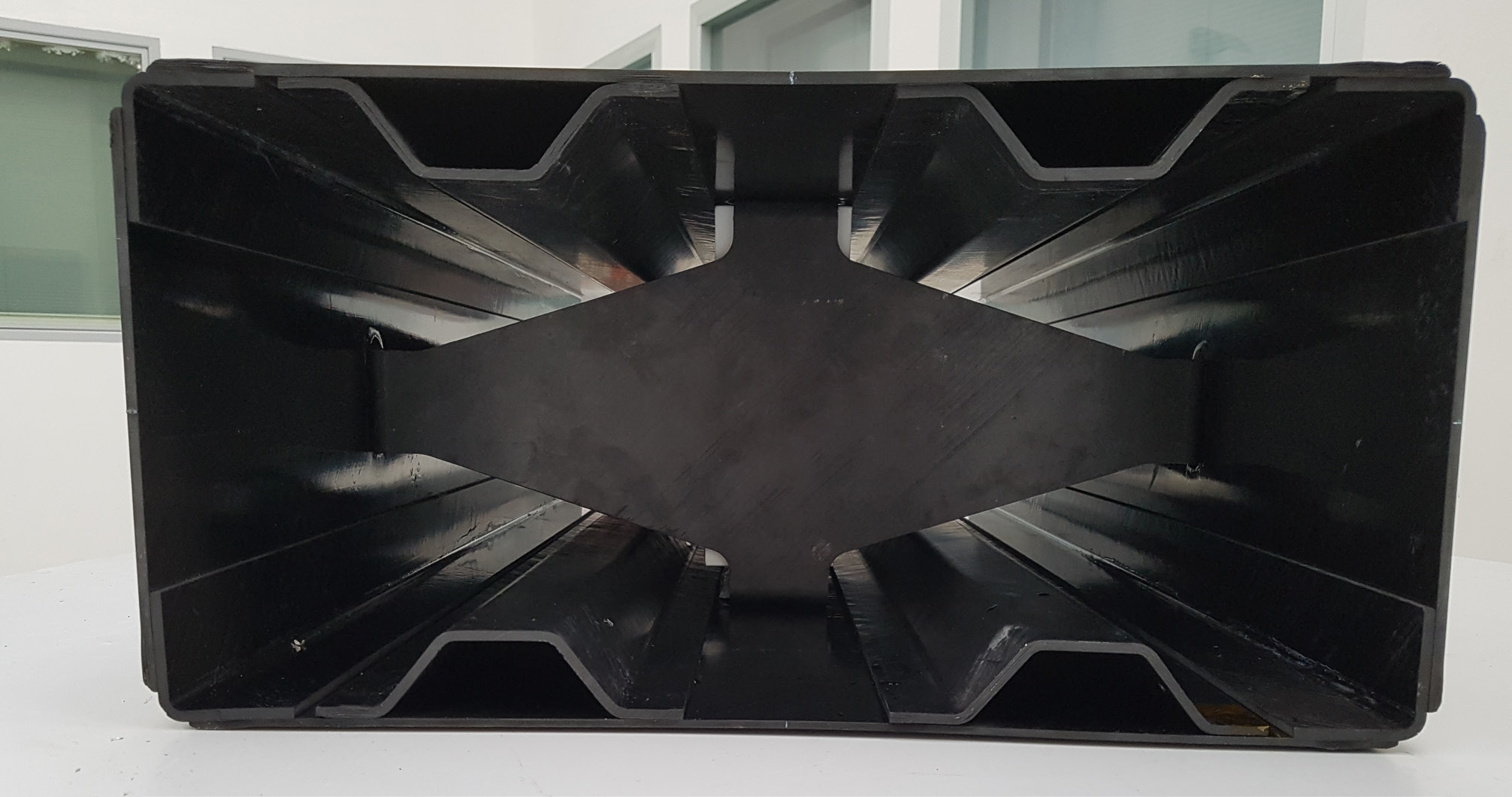
Soldadura por inducción para consolidación in situ
“La soldadura por inducción es muy interesante para los composites porque es posible ajustar y controlar la temperatura muy bien, calentar muy rápido y controlar con mucha precisión”, señala Pappadà. “Con Leonardo, desarrollamos la soldadura por inducción para unir componentes de TPC. Pero ahora estamos pensando en utilizar la soldadura por inducción para la consolidación in situ (ISC) de cintas TPC. Para hacer esto, hemos desarrollado una nueva cinta de fibra de carbono que se puede calentar muy rápidamente mediante soldadura por inducción utilizando una máquina dedicada. La cinta utiliza los mismos materiales de matriz que las cintas comerciales pero con una arquitectura diferente que mejora el calentamiento electromagnético. Estamos optimizando el rendimiento mecánico, pero también pensando en el proceso, tratando de satisfacer diferentes necesidades, por ejemplo, cómo procesar de manera rentable con la automatización ”.
Señala que ISC es muy difícil de lograr con cinta TPC con buenas tasas de producción. “Para tener esto para la producción industrial, debes calentar y enfriar más rápido y aplicar presión de una manera muy controlada. Entonces, decidimos usar soldadura por inducción para calentar una pequeña región solo donde estamos consolidando material pero dejamos el resto del laminado frío ”. La soldadura por inducción utilizada para el montaje tiene un TRL más alto, dice Pappadà. “
El uso de calentamiento por inducción para la consolidación in situ parece muy perturbador, algo que ningún otro OEM o proveedor de nivel está haciendo abiertamente en este momento. "Sí, esta es posiblemente una tecnología disruptiva", dice Corvaglia. “Hemos patentado la máquina y los materiales. Nuestro objetivo es algo que pueda ser comparable a los compuestos termoendurecibles. Muchos han probado AFP (colocación automatizada de fibra) con TPC, pero tienen que hacer un paso secundario para la consolidación. Esta es una gran limitación en términos de geometría, costo, tiempo de ciclo y tamaño de las piezas. De hecho, podemos cambiar la forma de producir piezas aeronáuticas ”.
SQRTM
Además de los termoplásticos, Leonardo continúa buscando tecnologías RTM. “Esta es otra área en la que hemos trabajado con CETMA y patentado nuevos desarrollos basados en una tecnología más antigua, en este caso, SQRTM. El mismo moldeo por transferencia de resina calificado (SQRTM) fue desarrollado inicialmente por Radius Engineering (Salt Lake City, Utah, EE. UU.). “Tener un método fuera de autoclave (OOA) que nos permita utilizar material que ya está calificado es importante”, dice Corvaglia. “También nos permite utilizar preimpregnados que tienen propiedades y calidad bien conocidas. Hemos diseñado, demostrado y patentado un marco de ventana de avión utilizando esta tecnología ”.
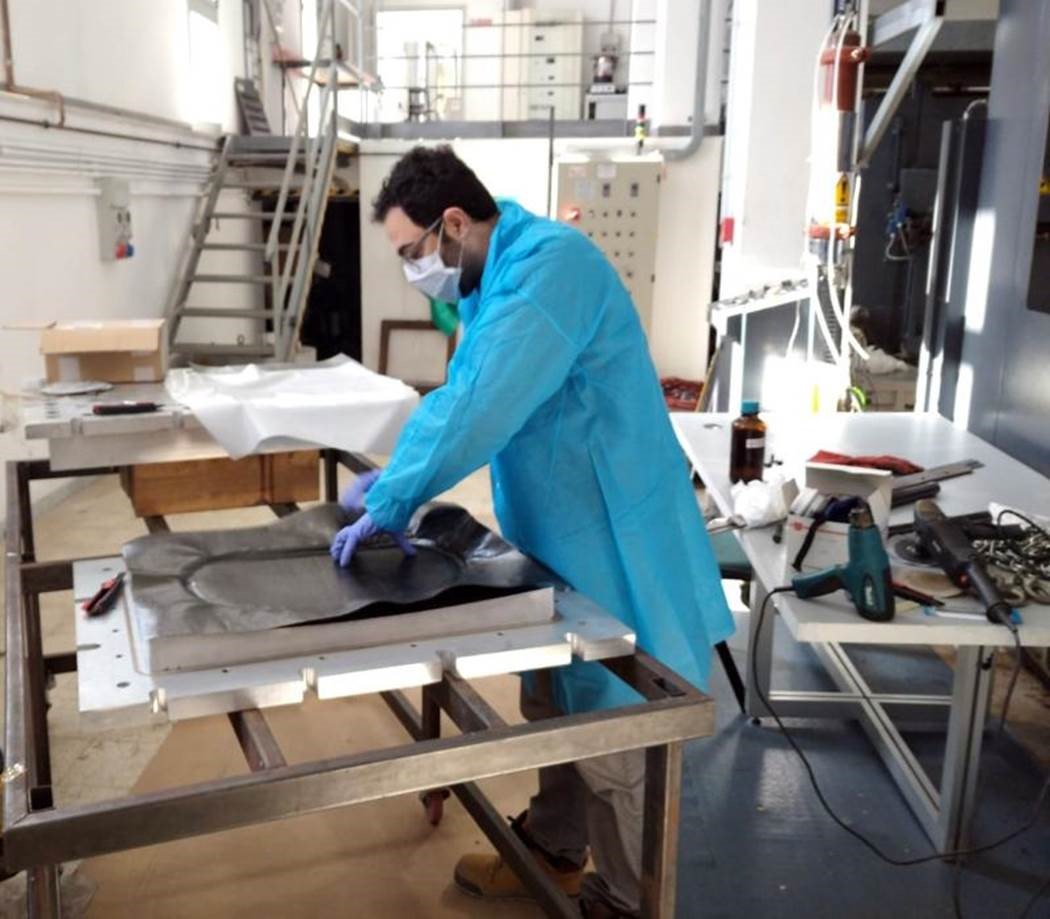
“Esta también es una tecnología más antigua, pero si vas a la web, no puedes encontrar información sobre esta técnica”, señala Pappadà. “Lo importante es que, nuevamente, estamos usando modelos analíticos para predecir y optimizar los parámetros del proceso. Con esta tecnología, podemos tener una buena distribución de resina, sin regiones secas ni acumulación de resina, y un contenido de huecos casi nulo. Podemos producir un alto rendimiento estructural porque podemos controlar el contenido de fibra y esta tecnología se puede utilizar para producir formas complejas. Estamos usando los mismos materiales calificados para curado en autoclave, pero en su lugar en un método OOA, pero también podría decidir usar resinas de curado rápido para reducir el tiempo del ciclo a minutos ”.
“Incluso con el preimpregnado actual, hemos reducido el tiempo de curado”, señala Corvaglia. “Por ejemplo, en comparación con un ciclo de autoclave normal de 8 a 10 horas, podemos lograr de 3 a 4 horas con SQRTM para una pieza como el marco de una ventana. Se aplica calor y presión directamente a la pieza y la masa para calentar es menor. Además, calentar la resina líquida frente al aire en un autoclave es más rápido y la calidad de la pieza es sobresaliente, lo cual es una ventaja especialmente para formas complejas. No hay retrabajos, casi cero vacíos y una superficie de excelente calidad porque la herramienta la controla, no una bolsa de vacío ”.
Futuro visionario basado en la tecnología
Leonardo está produciendo innovación en un conjunto amplio y diverso de tecnologías. Debido a la rápida evolución de la tecnología, considera que la inversión en I + D de alto riesgo (bajo TRL) es crucial para desarrollar las nuevas tecnologías requeridas para los productos futuros, que van más allá del desarrollo incremental (a corto plazo) que ya sostiene en los productos actuales. Esta combinación de estrategias a corto y largo plazo se combinan en el Masterplan de I + D 2030 de Leonardo, una visión unificada para una empresa sostenible y competitiva.
Como parte de este plan, está lanzando Leonardo Labs, una red internacional de laboratorios corporativos de I + D dedicados a la investigación avanzada y la innovación tecnológica. Para 2020, la compañía buscará abrir los primeros seis Laboratorios Leonardo en las áreas de Milán, Turín, Génova, Roma, Nápoles y Taranto y está contratando a 68 investigadores (Leonardo Research Fellows) con habilidades en las siguientes áreas:36 puestos en Inteligencia Artificial y sistemas inteligentes autónomos, 15 en analítica de big data, 6 en informática de alto rendimiento, 4 en electrificación de plataformas aeronáuticas, 5 en materiales y estructuras y 2 en tecnologías cuánticas. Leonardo Labs desempeñará el papel de puestos avanzados de innovación y generadores de las tecnologías futuras de Leonardo.
Cabe destacar que las tecnologías que comercializa Leonardo en aviones también pueden tener aplicaciones en sus divisiones terrestres y marítimas. Estén atentos para más actualizaciones sobre Leonardo y su impacto potencial en los compuestos.
Resina
- Composites de TPE ultraligeros para calzado
- Espuma de polipropileno para mejorar la sostenibilidad y el costo
- Compuestos de grafeno y polímeros para aplicaciones de supercapacitores:una revisión
- Personalización de sensores ultrasónicos para la optimización y el control de procesos compuestos
- OTOMcomposite desarrolla software para la producción de Composites 4.0 utilizando colocación de cinta asistida por láser y bobinado
- Resinas epoxi reprocesables, reparables y reciclables para composites
- Combinación de medidas dieléctricas de CA y CC para el control del curado de compuestos
- Compuestos de Solvay seleccionados para catamarán de carreras
- El consorcio de compuestos termoplásticos tiene como objetivo la producción de alto volumen para la industria automotriz y aeroespacial
- Impacto ambiental de la fabricación de semiconductores y productos electrónicos
- Sensor de gas portátil para el control ambiental y de la salud