Efecto de los defectos subsuperficiales inducidos por el mecanizado sobre la evolución de la dislocación y las propiedades mecánicas de los materiales a través de la nano indentación
Resumen
Los defectos del subsuelo tienen un impacto significativo en la precisión y el rendimiento de las nanoestructuras. En este artículo, se realiza una simulación de dinámica molecular de nano-indentación para investigar el efecto de los defectos del subsuelo inducidos por el mecanizado sobre la evolución de la dislocación y las propiedades mecánicas de los materiales, en el que el modelo de muestra con defectos del subsuelo se construye mediante nanocorte conforme a la realidad. Se discuten el mecanismo de formación de los defectos del subsuelo y el mecanismo de interacción entre los defectos inducidos por la máquina y la evolución de la dislocación. Se calculan la dureza y el módulo de elasticidad de Young de muestras de cobre monocristalino. Los resultados de la simulación indican que existen residuos de estructura de defectos estables en el subsuelo de la pieza de trabajo, como grupos atómicos, fallas de apilamiento tetraédricas y dislocaciones de varillas de escalera. El procesamiento secundario de nano-indentación puede restaurar los defectos internos de la pieza de trabajo, pero el daño subsuperficial en el área de procesamiento secundario se agrava. La dureza por nano-indentación de las muestras aumenta con la introducción de defectos en el subsuelo, lo que da como resultado la formación de un efecto de endurecimiento por trabajo. La existencia de defectos del subsuelo puede debilitar la capacidad del material para resistir la deformación elástica, en la que la evolución mutua entre dislocaciones y defectos del subsuelo juega un papel importante.
Antecedentes
La fabricación de ultraprecisión a escala nanométrica se considera ampliamente un método eficaz para obtener nanocomponentes con precisión dimensional submicrométrica y calidad de superficie a nanoescala [1]. Algunos defectos estables del subsuelo quedan dentro de la pieza de trabajo después de la fabricación [2, 3, 4, 5]. Los defectos del subsuelo no solo afectan la precisión del procesamiento y la calidad de la superficie, sino que también afectan de manera crítica las propiedades mecánicas y la vida útil de los nanocomponentes. Se han realizado muchos estudios sobre los defectos del subsuelo mediante el método de dinámica molecular (MD), centrándose principalmente en la formación y evolución de los defectos del subsuelo [6, 7], el espesor de la capa de defectos del subsuelo (SSD) [8, 9] y la influencia de los defectos del subsuelo en la integridad de la superficie [10, 11]. Sin embargo, el efecto de los defectos del subsuelo sobre las propiedades mecánicas de los materiales de las piezas de trabajo está menos estudiado. Las propiedades mecánicas de las nanoestructuras son críticas para su rendimiento y vida útil. Por lo tanto, el efecto de los defectos del subsuelo en las propiedades mecánicas de los materiales se ha convertido en los temas clave a investigar.
Se han realizado muchas investigaciones para deliberar sobre la capa SSD mediante simulación de dinámica molecular del proceso de nanocorte. Narayanan [12] estudió la formación de fallas de apilamiento tetraédricas (SFT) en oro monocristalino e introdujo el mecanismo inducido por deformación de SFT. Inamura [13] exploró la formación de viruta y la deformación por deslizamiento del material durante el proceso de nano-corte y señaló que la formación de viruta es inducida principalmente por la deformación por deslizamiento por cizallamiento. Pei [14] estudió el efecto de los parámetros de corte sobre la evolución de la dislocación y el corte forzado durante el proceso de nanocorte y descubrió que cuando la pieza de trabajo es mayor de 40 nm, el efecto de tamaño no es significativo. Dai [15] y Liu [16] adoptaron métodos de simulación y experimentación MD respectivamente para estudiar la influencia de la estructura de la herramienta de diamante y el efecto del tamaño en la evolución de los defectos del subsuelo de la pieza de trabajo. Los estudios anteriores muestran que existen defectos estables del subsuelo en la pieza de trabajo después del nanocorte. Los parámetros de corte y los parámetros de geometría de la herramienta tienen una gran influencia en el espesor y la evolución de la capa de daño del subsuelo, e incluso en la precisión del procesamiento. Sin embargo, las propiedades mecánicas de los materiales de las piezas de trabajo no se pueden calcular analizando los datos relevantes obtenidos por nanocorte.
La nano-indentación es una técnica eficaz para caracterizar las propiedades mecánicas como la dureza y el módulo de elasticidad [17]. Se han realizado muchos estudios sobre nano-indentación para evaluar el rendimiento de las propiedades mecánicas mediante modelos experimentales y teóricos. Zimmerman [18] analizó la emisión de dislocaciones en el proceso de nano-indentación por el vector de deslizamiento. Ruestes [19] estudió la nano-indentación de un solo cristal Fe mediante simulación MD y encontró que la generación de dislocaciones en el subsuelo es necesaria para eliminar el material de la zona de indentación. Huang [20] realizó simulaciones MD de nano-indentación en una matriz de diamante monocristalino y descubrió que la deformación del material de diamante bajo la indentación estaba dominada por la nucleación y propagación de los bucles de dislocación 〈110〉 {111}. Sharma [21] construyó un modelo de partículas duras artificialmente en una matriz de cobre y analizó la influencia de las partículas duras en la evolución de los defectos del subsuelo en el proceso de mecanizado. Peng [22] investigó los mecanismos de fortalecimiento de los recubrimientos de grafeno sobre el sustrato de Cu por nano-indentación, que es el resultado del efecto de homogeneización del estrés generado por la interfaz. Del análisis anterior, se puede ver que los estudios previos sobre el efecto de los defectos del subsuelo se basan principalmente en materiales cristalinos perfectos o en defectos hipotéticos de construcción artificial, lo que está muy lejos de los defectos reales del subsuelo. Por lo tanto, construir el modelo de la pieza de trabajo con defectos del subsuelo de manera realista es esencial para analizar la influencia de los defectos del subsuelo en las propiedades mecánicas de la pieza de trabajo.
En este artículo, se adoptó el método de nano-corte para obtener el modelo de la pieza de trabajo con defectos del subsuelo que se ajustan a las características prácticas. Sobre esta base, se llevó a cabo una simulación de nano-indentación para estudiar el efecto de los defectos del subsuelo en las propiedades mecánicas del cobre monocristalino. En primer lugar, se discutirá el mecanismo de formación y evolución de los defectos del subsuelo durante el proceso de nano-corte, y se analizarán las estructuras típicas de defectos del subsuelo de la pieza de trabajo después del nano-corte. En segundo lugar, se analizará el mecanismo de interacción entre los defectos del subsuelo inducidos por el mecanizado y la nucleación de la dislocación durante la indentación. En tercer lugar, basándose en los datos de carga-desplazamiento obtenidos por nano-indentación, se calcularán la dureza y el módulo elástico de Young de muestras de cobre monocristalino. Finalmente, se resumirán algunas conclusiones novedosas.
Métodos
Modelo de simulación
Para investigar el efecto de los defectos del subsuelo sobre las propiedades mecánicas de los materiales en el nano-mecanizado, se debe construir el modelo de muestra con defectos del subsuelo. En esta investigación, se realiza mediante simulación MD del proceso de nanocorte. En primer lugar, se establece el modelo de simulación MD y se realiza la simulación del proceso de nano-corte. Luego, la muestra y la herramienta de corte se relajaron durante el tiempo suficiente durante la simulación de MD . Finalmente, algunos defectos estables permanecieron en el subsuelo de pieza de trabajo. El diagrama esquemático de los modelos de simulación MD tridimensionales se muestra en la Fig. 1, en el que el modelo de nano-corte se muestra en la Fig. 1a y el modelo de nano-indentación con defectos del subsuelo se muestra en la Fig. 1b. En la Fig. 1, los materiales de la pieza de trabajo y la muestra son cobre monocristalino y la herramienta y el penetrador son materiales de diamante. La herramienta de diamante con hoja de arco se utiliza en el proceso de nanocorte y el radio del borde de la herramienta es de 3 nm. El indentador tiene forma hemisférica en un proceso de nano indentación y el diámetro es de 6 nm. La pieza de trabajo y la muestra se dividen en tres partes, que son capa de Newton, capa de temperatura y capa límite, respectivamente. Para reducir el efecto de tamaño y el efecto de límite, se adopta la condición de límite periódico (PBC) en la dirección [010] del sistema de simulación. Para evitar la interacción inicial entre la herramienta y la pieza de trabajo, la herramienta de corte se coloca 3 nm arriba a la derecha de la pieza de trabajo y el penetrador se coloca 6 nm hasta la muestra. Los parámetros de simulación detallados se muestran en la Tabla 1.
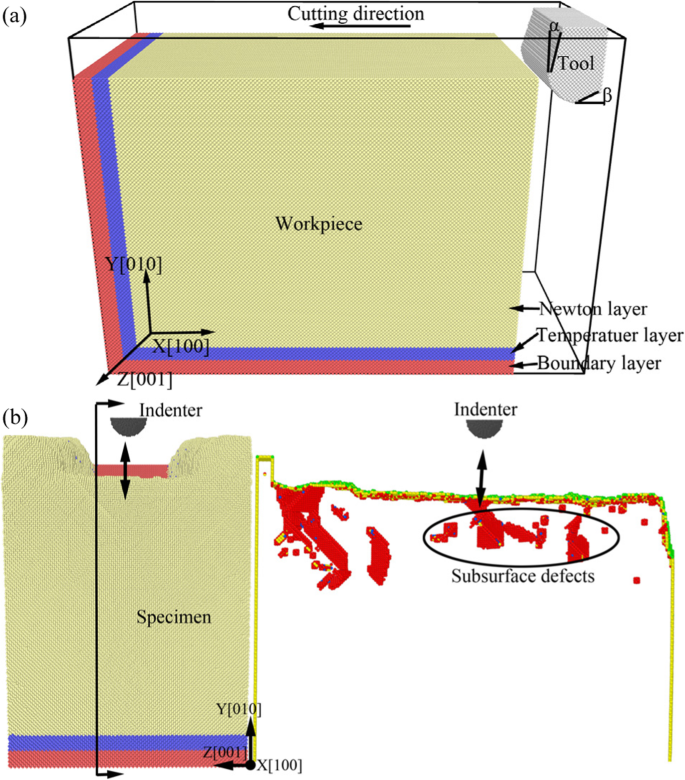
Diagrama esquemático de modelos de simulación 3D MD de cobre monocristalino para nano-corte y nano-indentación. un El modelo para el proceso de nanocorte. b El modelo para el proceso de nano-indentación con defectos del subsuelo
Funciones potenciales interatómicas
En esta investigación, las simulaciones MD tridimensionales se realizaron mediante un simulador masivamente paralelo atómico / molecular a gran escala (LAMMPS). El cálculo paralelo se realizó con la ayuda de la biblioteca de interfaz de paso de mensajes. El potencial Morse, el potencial del método del átomo incrustado (EAM) y el potencial de Tersoff se utilizan en la simulación, que se invocan desde el paquete de software LAMMPS. La interacción entre los átomos de Cu en la pieza de trabajo y los átomos de C en la herramienta se calcula mediante el potencial Morse que se muestra en la Ec. 1 [23].
$$ u \ left ({r} _ {ij} \ right) =D \ left [\ exp \ left (-2 \ alpha \ left ({r} _ {ij} - {r} _0 \ right) \ right ) -2 \ exp \ left (- \ alpha \ left ({r} _ {ij} - {r} _0 \ right) \ right) \ right] $$ (1)donde r 0 , α y D respectivamente son el espaciado atómico, el módulo de elasticidad y la energía de enlace. El valor se muestra en la Tabla 2.
La función interatómica entre los átomos de Cu en la pieza de trabajo se describe mediante el potencial EAM que se muestra en las Ecs. 2, 3 [24, 25].
$$ E =\ sum \ limits_i ^ N \ left [F \ left ({\ rho} _i \ right) + \ sum \ limits_ {j> i} ^ Nu \ left ({r} _ {ij} \ right) \ right] $$ (2) $$ {\ rho} _i =\ sum \ limits_jf \ left ({r} _ {ij} \ right) $$ (3)La interacción entre los átomos de carbono en la herramienta de diamante se calcula mediante el potencial de Tersoff que se muestra en las Ecs. 4, 5 [26].
$$ E =\ frac {1} {2} \ sum \ limits_ {i \ ne j} {V} _ {ij} $$ (4) $$ {V} _ {ij} ={f} _c \ left ({r} _ {ij} \ right) \ left [{V} _R ^ {\ hbox {'}} \ left ({r} _ {ij} \ right) + {b} _ {ij} {V} _A \ izquierda ({r} _ {ij} \ derecha) \ derecha] $$ (5)donde f c ( r ij ) es la función de truncamiento entre átomos, V A ( r ij ) es el potencial dual del término de absorción, V R ( r ij ) es el potencial dual del término de repulsión, y r ij es la distancia atómica entre el átomo i y atom j .
Métodos de análisis de defectos
En el nanocorte de cobre monocristalino, la deformación y las dislocaciones se nuclean en el subsuelo de la pieza de trabajo. En este artículo, se introduce el parámetro de centro-simetría (CSP) para analizar la nucleación de la dislocación y la evolución del defecto de la pieza de trabajo. Para materiales cúbicos de centro frontal (FCC), el valor de CSP se puede calcular mediante la ecuación. 6 [27].
$$ CSP =\ sum \ limits_ {i =1} ^ 6 {\ left | {R} _i + {R} _ {i + 6} \ right |} ^ 2 $$ (6)donde R i tiene la misma longitud de átomos vecinos y R i + 6 es la dirección opuesta de los átomos vecinos. Los valores de CSP de cristal de FCC, dislocación parcial, falla de apilamiento y átomos de superficie son 0, 2,1, 8,3 y 24,9, respectivamente [27].
El método CSP es capaz de identificar el atómico escalonado, pero no puede reconocer el estado de la estructura del cristal atómico local de la pieza de trabajo. Por lo tanto, se introduce el análisis de vecino común (CNA) para identificar el defecto de la estructura cristalina local. En el método CNA original, propuesto por Honeycutt y Andersen [28], las diversas estructuras están representadas por diagramas. Actualmente, hay cinco tipos de patrones de CNA en OVITO [29], donde las estructuras cristalinas locales se identifican como cúbica del centro de la cara (FCC), hexagonal compacta (HCP), cúbica centrada en el cuerpo (BCC), icosoédrica (ICO), y desconocido, respectivamente. En este artículo, también se introduce el algoritmo de extracto de dislocación (DXA) [30] para analizar la evolución del defecto de dislocación. Por DXA, las diferentes estructuras de cristal en la pieza de trabajo se marcarán con diferentes colores y los defectos de dislocación en la pieza de trabajo se representarán con líneas de diferentes colores.
Resultados y discusión
Evolución de defectos subsuperficiales en el proceso de nanocorte
En el proceso de nano-corte, bajo la acción de extrusión y corte de la herramienta de corte en la pieza de trabajo, se elimina el material de la superficie de la pieza de trabajo con el grosor de la profundidad de corte y se forma una nueva superficie mecanizada con un cierto tamaño de precisión y calidad de superficie. La deformación elástica-plástica compleja, incluida la deformación por tensión y la deformación térmica, se produce en la superficie y el subsuelo de la pieza de trabajo, acompañando la transformación de energía y la concentración de tensión. Por lo tanto, se forma la capa de daño subsuperficial y se retira la viruta. La Figura 2 muestra las vistas instantáneas de la evolución del defecto del subsuelo y la eliminación de material durante el proceso de nano-corte de cobre monocristalino. En la Fig. 2, los átomos están coloreados por el valor de los resultados de los análisis de CSP y CNA. En la Fig. 2a yc, los átomos amarillo, verde, rojo y azul son átomos de superficie, átomos de defectos de superficie, átomos de defectos del subsuelo y átomos de FCC. Se puede ver en la Fig.2 que se forman una gran cantidad de estructuras defectuosas típicas en el subsuelo de la pieza de trabajo durante el proceso de nano-corte, como defectos puntuales, defectos de vacantes, fallas de apilamiento, defectos de racimo, dislocaciones prismáticas y bucle de dislocación del tornillo.
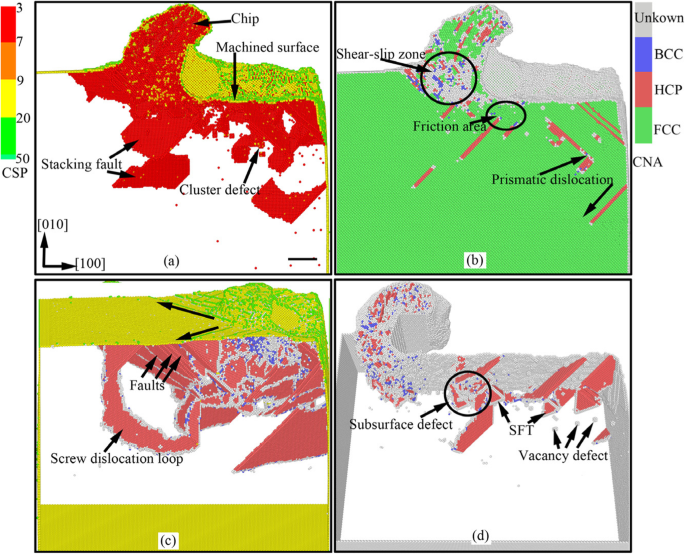
Vistas instantáneas de la evolución del defecto del subsuelo durante el proceso de nano-corte de cobre monocristalino (Color en línea, barra de escala de 5 nm). Las distancias de corte de a , b , c y d respectivamente son 18 nm, 18 nm, 6 nm y 32 nm
Debido al efecto de compresión y cizallamiento de la herramienta de corte, la deformación por deslizamiento por cizallamiento se genera para los átomos en frente de la cara de desprendimiento y la zona de deslizamiento por cizallamiento primaria se forma en la pieza de trabajo durante el proceso de nano-corte, como se muestra en la Fig. .2b. Algunos de estos átomos se deslizan a lo largo de la cara inclinada y la viruta se forma como se muestra en la Fig. 2a. Algunos se mueven hacia abajo y la superficie mecanizada se forma bajo la fricción de apriete de la cara del flanco de la herramienta, como se muestra en la Fig. 2b. Otros se mueven hacia adentro y se forman los defectos del subsuelo, como fallas de apilamiento, defectos de racimo y dislocaciones prismáticas, que se muestran en la Fig. 2a y b.
Debido a la fricción y extrusión de la superficie del flanco de la herramienta, la acumulación de energía se produce para los átomos cerca de la cara del flanco y los átomos se convierten en átomos de alta energía. Cuando la energía atómica se supera un cierto nivel, la energía transportada por los átomos energéticos se liberará y la dislocación se formará bajo la conducción de los átomos energéticos. Por lo tanto, se forman muchas dislocaciones en el área de fricción de la cara del flanco, que se muestra en la Fig. 2d. Con la superficie mecanizada que se está formando, las dislocaciones se nuclean, se extienden y se aniquilan en el subsuelo. Finalmente, las estructuras de los defectos como fallas de apilamiento, SFT y defectos de vacantes se dejan en el subsuelo, como se indica en la Fig. 2d. Las fallas de apilamiento se nuclean en la zona de deslizamiento por cizallamiento debajo de la herramienta de corte, luego se extienden hacia la pieza de trabajo y finalmente se aniquilan en la superficie libre de la pieza de trabajo. Finalmente, la línea de dislocación se forma en la superficie de la pieza de trabajo. Y la línea de dislocación se extiende a lo largo de \ (\ left [\ overline {1} 0 \ overline {1} \ right] \), \ (\ left [\ overline {1} 01 \ right] \) y [101] direcciones. El bucle de dislocación del tornillo, que se encuentra en el borde de la zona de deslizamiento por cizallamiento, consta de varias fallas de apilamiento y una serie de dislocaciones del tornillo. La dislocación del tornillo se forma bajo el impulso del estado de tensión de compresión de la zona de deslizamiento-cizallamiento [11].
En el proceso de nano-corte, las dislocaciones son nucleadas y extendidas bajo la acción de la herramienta de corte. Junto con la agregación y liberación de energía, la fuerza de corte fluctúa con el aumento de la distancia de corte, que se muestra en la Fig. 3 en tres dimensiones. En la Fig. 3, las curvas negra, roja y azul, respectivamente, son la fuerza de avance (Fx), la fuerza de retroceso (Fy) y la fuerza tangencial (Fz). Puede verse en la Fig. 3 que el proceso de corte se divide en dos períodos que son la etapa de corte inicial y la etapa de corte estable. Durante la etapa de corte inicial, la fuerza de avance y la fuerza de retroceso aumentan rápidamente, de forma rectilínea. El valor máximo de la fuerza de avance se alcanza en más de 1100 nN, pero la fuerza de retroceso acaba de llegar alrededor de 600 nN. Cuando la punta de la herramienta corta completamente la pieza de trabajo, se forma la superficie mecanizada, que se muestra como el primer gráfico pequeño firmado como Superficie mecanizada en la Fig. 3. Luego, el proceso de nano-corte se transfiere a la etapa de corte estable. En la etapa de corte estable, las tres fuerzas fluctúan en sus posiciones de equilibrio. La fuerza de alimentación promedio es de aproximadamente 1000 nN y la fuerza de retroceso promedio es de solo 500 nN. Se puede ver en la Fig. 3 que la fuerza de avance disminuye rápidamente a la distancia de corte de 20 nm. Esto se debe a que la acumulación de energía llega a un cierto nivel, que es la energía crítica de deformación de la celosía, que se muestra como el segundo gráfico pequeño en la Fig. 3. Mientras tanto, se actúa una gran resistencia en la herramienta de corte que da como resultado que la fuerza de corte sea un valor pico. Luego, se libera la energía que da como resultado la emisión de dislocación, y la fuerza de corte disminuye, como se muestra en el tercer gráfico pequeño en la Fig. 3. Por lo tanto, la fuerza de corte fluctúa durante la etapa de corte estable. La nucleación, extensión y aniquilación de las dislocaciones condujo a la fluctuación de la fuerza de corte y finalmente dio como resultado el defecto del subsuelo existente en la pieza de trabajo.
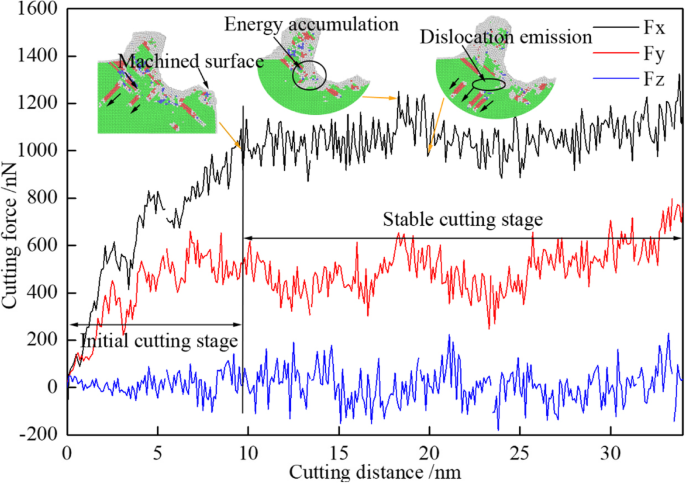
La curva de variación de la fuerza de corte con la distancia de corte (color en línea). Las curvas negra, roja y azul, respectivamente, son la fuerza de avance (Fx), la fuerza de retroceso (Fy) y la fuerza tangencial (Fz)
Con el fin de investigar en detalle la evolución y la emoción de los defectos de dislocación en el subsuelo de la pieza de trabajo durante el proceso de nano-corte, la distribución de la dislocación y su variación con la distancia de corte se analizan minuciosamente mediante el método CNA. La evolución del defecto del subsuelo de la pieza de trabajo en un área determinada se muestra en la figura 4, en la que las distancias de corte de la figura 4a, b, c, d, eyf son respectivamente 8 nm, 10 nm, 12 nm, 20 nm , 24 nm y 32 nm. Puede verse en la Fig. 4a que muchos defectos de dislocación están nucleados en la zona de deslizamiento por cizallamiento bajo la acción de cizallamiento por extrusión de la herramienta de corte durante la etapa preliminar del proceso de corte. Particularmente, una dislocación en forma de V y una falla se forman bajo la acción impulsora de la tensión atómica y la energía en la zona de deslizamiento cortante, que se muestra en la Fig. 4b. En el proceso de procesamiento posterior, la zona de deslizamiento de cizalla se mueve hacia adelante con la herramienta de corte en movimiento. Debido a la disminución de la energía de deformación, la falla se aniquila gradualmente. Mientras la herramienta de corte sigue avanzando, la zona de fricción de la cara del flanco se mueve cerca de la falla. Y la superficie mecanizada de rugosidad se forma bajo la extrusión y fricción de la cara del flanco. Luego, la falla continúa aniquilándose y separándose gradualmente de la superficie de la pieza de trabajo, como se muestra en la Fig. 4d. Finalmente, la falla se transforma en un defecto de racimo que existe constantemente en el subsuelo de la pieza de trabajo. De manera similar, la dislocación en forma de V formada se convierte gradualmente en SFT bajo la interacción de dos fallas de apilamiento y un bloqueo de dislocación. Estos defectos estables se componen de la capa deformada subsuperficial juntos, como se muestra en la Fig. 4e y la Fig. 4f.
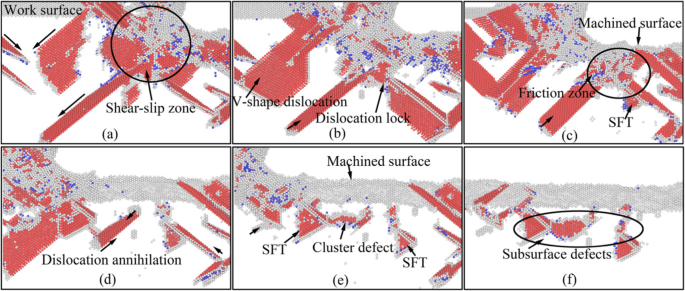
Evolución de defectos del subsuelo de la pieza de trabajo (color en línea). Las distancias de corte de a , b , c , d , e y f respectivamente son 8 nm, 10 nm, 12 nm, 20 nm, 24 nm y 32 nm
Como sabemos, la liberación de la tensión residual y la recuperación del defecto interno se producirán en la pieza de trabajo después del tratamiento de envejecimiento. En la nanofabricación real, algunos de los defectos del subsuelo formados durante el procesamiento desaparecerán después del proceso de mecanizado. Para simular el estado de la pieza de trabajo después del tratamiento de envejecimiento, se realiza una relajación de la dinámica molecular en el sistema de corte durante un tiempo prolongado. El diagrama de distribución del defecto residual en el subsuelo de la pieza de trabajo después de la relajación MD durante un tiempo prolongado se muestra en la Fig. 5, en la que los átomos se colorean de acuerdo con los resultados del análisis por métodos CSP y CNA. Puede verse en la figura 5 que las luxaciones primarias se aniquilan después de la relajación. Los defectos de vacancia, fallas de apilamiento, racimo atómico, dislocación prismática, dislocación de tornillo, SFT y dislocación de varilla de escalera existen en el subsuelo de la pieza de trabajo, como se muestra en la Fig. 5. Según el análisis anterior, estos defectos, que se forman bajo la inducción de tensiones internas complejas y la interacción de los defectos de dislocación afectarán la precisión del tamaño y la calidad de la superficie de la pieza de trabajo después del nanoprocesamiento.
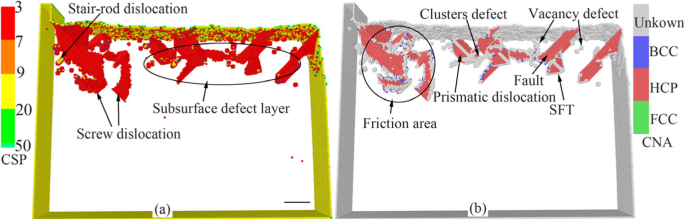
Distribución de defectos residuales en el subsuelo de la pieza de trabajo después del corte nanométrico (color en línea, barra de escala de 5 nm). un Los átomos amarillo, verde, rojo y azul son átomos superficiales, átomos defectuosos superficiales, átomos defectuosos subsuperficiales y átomos FCC. b Los átomos verde, rojo, gris y azul son estructura FCC, HCP, desconocida y BCC
Prueba de nano indentación en una muestra de cobre con defectos del subsuelo inducidos por el mecanizado
Los defectos residuales del subsuelo inducidos por el mecanizado gobiernan las propiedades mecánicas de la superficie, especialmente la dureza y el módulo de Young. Por lo tanto, la investigación de la nucleación y la interacción de las dislocaciones durante la nano-indentación parece muy necesaria. Para investigar la influencia de los defectos del subsuelo inducidos por el mecanizado en las propiedades mecánicas del cobre monocristalino, se puso en práctica el proceso de nano-indentación en la muestra después del nanocorte con los mismos parámetros que la simulación de nanocorte. El resultado de la simulación se muestra en las Figs. 6, 7, 8, 9 y 10. La imagen atómica instantánea de la distribución del defecto subterráneo en el estado inicial de nano-indentación se muestra en la Fig. 6. Se puede ver en la figura que hay varias SFT, una forma de V dislocación, algunas dislocaciones prismáticas y algunos defectos de racimo debajo del penetrador. Estos defectos del subsuelo pueden afectar la nucleación de la dislocación y la expansión de la pieza de trabajo durante el proceso de nano-indentación. Y luego se cambian las propiedades mecánicas del material de la pieza de trabajo.
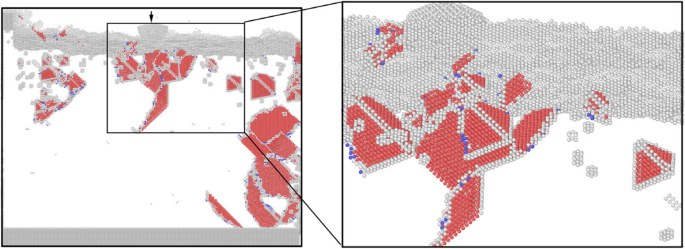
Distribución de defectos subsuperficiales de la pieza de trabajo en el estado de sangría inicial (color en línea). Los átomos rojo, gris y azul son HCP, desconocido y estructura BCC
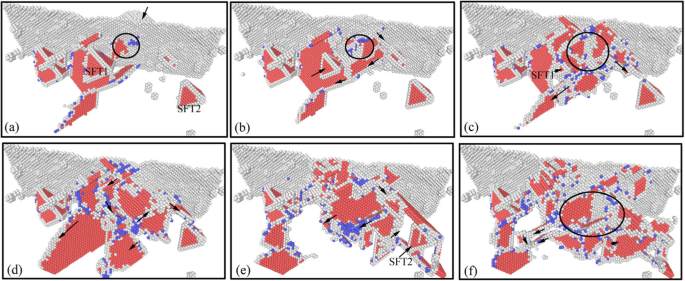
Evolución de los defectos de dislocación del subsuelo en el proceso de carga de nano-indentación (color online). Las profundidades de sangría correspondientes de a - f son 0 nm, 0,5 nm, 1 nm, 2 nm, 3 nm y 4 nm, respectivamente
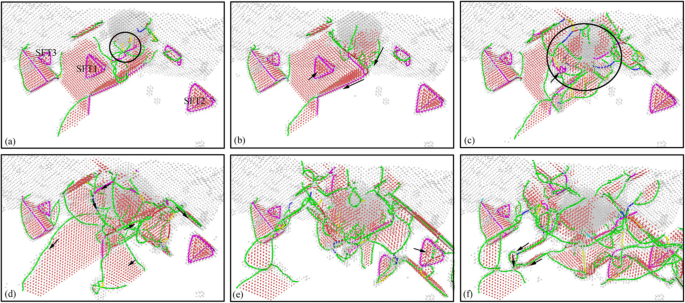
Distribución de dislocaciones subsuperficiales en proceso de carga de nano-indentación (color en línea). Las profundidades de sangría correspondientes de a - f son 0 nm, 0,5 nm, 1 nm, 2 nm, 3 nm y 4 nm, respectivamente. Esquema de colores:azul profundo para dislocaciones perfectas, verde para dislocaciones de Shockley, rosa para dislocaciones de varilla de escalera, amarillo para dislocaciones de Hirth, azul claro para dislocaciones Frank y rojo para dislocaciones no identificadas
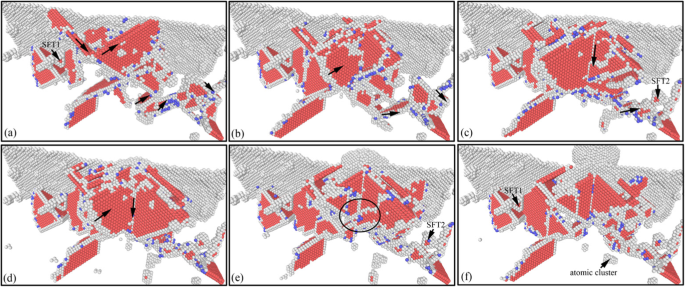
Evolución de defectos del subsuelo en proceso de descarga de nano-indentación (color online). Las profundidades de sangría correspondientes de a –F son 4 nm, 3 nm, 2 nm, 1 nm, 0 nm y - 1 nm, respectivamente
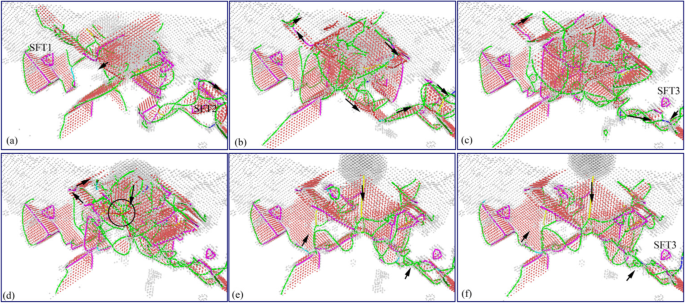
Distribución de dislocaciones subsuperficiales en proceso de descarga de nano-indentación (color online). Las profundidades de sangría correspondientes de a - f son 4 nm, 3 nm, 2 nm, 1 nm, 0 nm y -1 nm, respectivamente. Esquema de colores:azul profundo para dislocaciones perfectas, verde para dislocaciones de Shockley, rosa para dislocaciones de varilla de escalera, amarillo para dislocaciones de Hirth, azul claro para dislocaciones Frank y rojo para dislocaciones no identificadas
La imagen de evolución atómica de las dislocaciones del subsuelo durante el proceso de carga de nano-indentación se muestra en la Fig. 7. Puede verse en la Fig. 7a que la nucleación inicial de la dislocación se produce en la superficie de la muestra cuando el penetrador entra en contacto con la superficie del muestra. Con la presión hacia abajo del penetrador, las dislocaciones nucleadas se expanden gradualmente. Mientras tanto, bajo la influencia de la tensión ejercida por el penetrador, un gran número de dislocaciones se nucleó y se movió a lo largo del sistema de deslizamiento, como se muestra en la Fig. 7b. Bajo la interacción entre las dislocaciones recién formadas y los defectos originales del subsuelo, algunos defectos simples desaparecen gradualmente y las dislocaciones en forma de V continúan evolucionando y aniquilando gradualmente. La SFT debajo del penetrador se reduce gradualmente, como se muestra en la Fig. 7c. A medida que avanza el proceso de indentación, aumenta la escala de nuevos defectos de luxación nucleada, y la luxación en forma de V y SFT1 debajo del indentador desaparecen gradualmente. Simultáneamente, los defectos de dislocación formados durante la indentación evolucionan gradualmente a un bucle de dislocación prismático, en el que las fallas de apilamiento desaparecen gradualmente, como se muestra en la Fig. 7d. El bucle de dislocación prismática recién formado continúa extendiéndose hasta SFT2 en la parte inferior derecha del indentador. Debido a su estructura estable, el SFT2 permanece sin deformarse durante la expansión del bucle de dislocación prismática, como se muestra en la Fig. 7e. A medida que el penetrador presiona hacia abajo, el bucle de dislocación prismática continúa expandiéndose hacia abajo y la escala de los defectos de dislocación en el área del subsuelo aumenta gradualmente. La estructura SFT2 existe de manera estable en el subsuelo de la muestra y no tiene cambios durante el movimiento y la interferencia de los defectos de dislocación, como se muestra en la Fig. 7 f.
Para mostrar más claramente la evolución y distribución de los defectos del subsuelo durante el proceso de indentación, se utiliza el método DXA para analizar la muestra después de la indentación. La imagen de la distribución de la dislocación subsuperficial en cada momento correspondiente de la Fig. 7 se obtiene mediante análisis DXA, como se muestra en la Fig. 8. Las dislocaciones se colorean según el siguiente esquema:azul profundo para dislocaciones perfectas, verde para dislocaciones de Shockley, rosa para varilla de escalera dislocaciones, amarillo para las dislocaciones de Hirth, azul claro para las dislocaciones de Frank y rojo para las dislocaciones no identificadas.
Puede verse en la Fig. 8 que el subsuelo de la pieza de trabajo consiste principalmente en la dislocación de Shockley y la dislocación de la barra de escalera en el estado inicial de indentación. La SFT existente en el subsuelo es una estructura tetraédrica regular que consta de seis dislocaciones de varillas de escalera. Cuando el penetrador hace contacto con la pieza de trabajo, la nucleación de la dislocación en la superficie de la pieza de trabajo son dislocaciones amarillas de Hirsh, como se muestra en la Fig. 8a. A medida que el penetrador presiona hacia abajo, una gran cantidad de dislocaciones se nuclean y se mueven a lo largo del sistema de deslizamiento. Las dislocaciones amarillas de Hirsh se cambian gradualmente a dislocaciones de Shockley verdes, como se muestra en la figura 8b. Bajo la interacción entre las luxaciones recién formadas y la SFT1 original, algunas luxaciones simples desaparecen, gradualmente, como se muestra en la figura 8c. La escala de las dislocaciones del subsuelo aumenta con la caída del penetrador, y las dislocaciones recién formadas son principalmente dislocaciones de Shackley verdes. La interacción entre las dislocaciones de Shockley y SFT1 da como resultado el tamaño de la disminución gradual de SFT1 y la eventual desaparición de SFT1, como se muestra en la Fig. 8d. Con el aumento de la escala de los defectos, aumenta el número y los tipos de dislocaciones en el subsuelo de la muestra. Hay tipos desconocidos de dislocaciones de color rojo que se forman en el subsuelo, y varias dislocaciones de Shockley constituyeron el bucle de dislocación del prisma, como se muestra en la figura 8e. Bajo la interacción de la dislocación de Shockley y la dislocación de la varilla de escalera, el SFT2 y el SFT3 lejos de la región de indentación no desaparecieron finalmente, debido a la extrusión más débil del indentador, como se muestra en la Fig. 8f.
La imagen de evolución de la dislocación del subsuelo durante el proceso de descarga de nano-indentación se muestra en la Fig. 9. La Figura 10 muestra la imagen de distribución de la dislocación del subsuelo correspondiente en la Fig. 9. De los dos gráficos, se puede ver que la escala de defectos del subsuelo aumenta al principio, y luego disminuye gradualmente durante el proceso de movimiento ascendente del indentador. Es causada por la función integral entre la liberación continua de la energía de deformación del material y la fuerza de adhesión ejercida por el penetrador sobre la muestra. En la etapa inicial del proceso de descarga, la fuerza de adsorción ascendente del efecto indentador sobre la muestra no es significativa. La evolución del defecto del subsuelo es impulsada principalmente por la energía de deformación del material, lo que resulta en un aumento de la escala de defectos del subsuelo. Y los principales tipos de dislocaciones en el escenario son la dislocación de Shockley verde y la dislocación de escalera rosa, como se muestra en las Figs. 9a, by 10a, b. La interacción entre el SFT2 y la dislocación de Shockley cercana hace que la dislocación rosada de la varilla de la escalera se convierta en una dislocación verde de Shackley en el área lejana de la acción del penetrador. Mientras tanto, el SFT2 se transforma en un defecto más pequeño que es SFT3, como se muestra en las Figs. 9c y 10c. Con el levantamiento continuo del penetrador, el efecto de adherencia y adsorción que ejerce el penetrador sobre la muestra aumenta gradualmente. Accompany with the deformation energy release, the size and types of dislocations in subsurface increase. And more perfect dislocations, Hirh dislocations, and unknown dislocations are formed, as shown in Figs. 9d and 10d. In later stage of unloading process, the material deformation energy is basically released, and the evolution of subsurface defects is dominated by the adsorption from the indenter. Therefore, the subsurface defects are annihilated rapidly, and the scale of subsurface defects decreases rapidly. And a typical Hirsch dislocation is formed in the direction of the indenter upward, which is shown in Figs. 9e, f and 10e, f. Finally, the scale of subsurface defects decreases considerably, and some typical subsurface defects, such as SFT and atomic clusters, are gradually disappeared. From the above analysis, it can be seen that secondary processing (nano-indentation) can restore the typical internal defects formed in nano-cutting, and the subsurface damage becomes more serious in the secondary processing area. These characteristics of subsurface defects will affect the mechanical properties of materials. Hence, it is necessary to study the effect of subsurface defects on the mechanical properties of material.
Mechanical properties of materials can be calculated by load-displacement curve, such as hardness, elastic modulus, and yield strength. In this study, hardness and Young’s modulus of single crystal copper were investigated. The variation of load on the indenter was monitored during the nano-indentation process, and the load-displacement curve of the nano-indentation process was drawn, as shown in Fig. 11. The max indentation depth of the red and black curves respectively is 2 nm and 3 nm, in which both loading and unloading processes are included. The upward direction of load is defined as positive direction, so the load-displacement curves are all above the zero line in the process of loading, while the load on the indenter changes from positive to negative during unloading. The elasticity restore of deformed matrix material exerts an upward force on the indenter. Therefore, in order to keep the indenter raising in uniform speed, a downward force (positive) is required. With the gradual recovery of deformation, the force gradually decreases until it disappears. Then the force applied on the indenter becomes negative, and the absolute value of the force first increases and then decreases. From the graph, it can be seen that the specimen is in the stage of elastic deformation during loading process, and the load increases in proportion to the displacement. When the displacement of the indenter is 1 nm, the load on the indenter is fluctuated dramatically, as indicated by the arrow on the left side of Fig. 11. This is because that the indenter is pressed down to the SFT1 shown in Fig. 7, which results in the greater impediment to the indenter. When the indenter displacement is in the range of 2 to 3 nm, the fluctuation amplitude of the load increases. This is because the indenter is pressed down to the SSD layer, and the impediment of the indenter to the subsurface defect in the specimen is more significant, so the fluctuation amplitude of the load increases significantly.
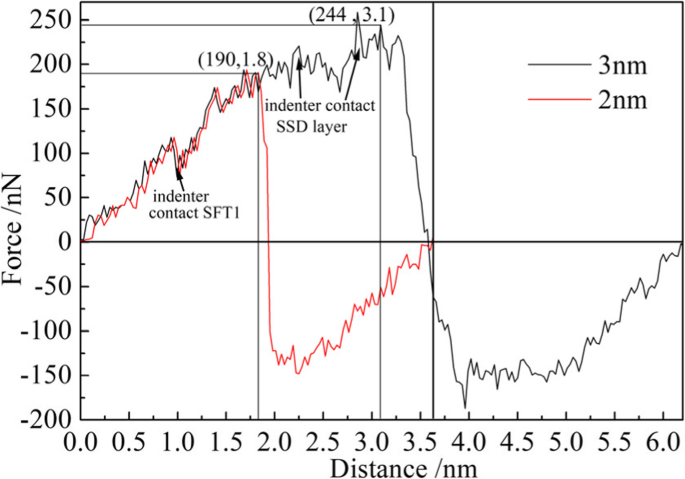
Load-displacement curve of nano-indentation on the machining-induced specimen (color online). The maximum indentation depth of the black curve and the red curve respectively is 3 nm and 2 nm
According to Oliver-Pharr Method [31], nano-indentation hardness can be defined as indentation load divided by the contact area between indenter and specimen, which is calculated by Eq. 7.
$$ H={F}_{\mathrm{max}}/{A}_c $$ (7)In which, F máx is the peak value of the load. A c is projected contact area for indenter and specimen, which can be obtained by
$$ {A}_c=\pi {r}^2 $$ (8)donde r is contact radius for indenter. Because the indenter is hemispherical in shape, r is approximately equal to indentation depth.
The elastic deformation of single crystal copper material is caused by the load exerted from indenter. Based on the previous load-displacement curve, Young’s modulus (E ) of single crystal copper can be calculated by Eq. 9.
$$ E=\frac{\sigma }{\varepsilon }=\frac{F/S}{DL/L}=\frac{F/\pi {r}^2}{DL/L} $$ (9)donde F is applied load, S is contact area, r is projection radius of indenter, DL is material deformation along loading direction, which is equal to indentation depth, and L is the total length of material along loading direction. In this study, L is equal to 30 nm.
According to the Oliver-Pharr method and load-displacement data, nano-indentation hardness and Young’s elastic modulus of single crystal copper materials with subsurface defects can be calculated based on Eqs. 7, 8, 9. Table 3 shows the applied load acting on the specimens by indenter with different indentation depths.
The nano-indentation hardness of single crystal copper can be calculated by Eqs. 7 and 8 combining the data in Table 3. When the maximum depth is 2 nm, F máx =190.67 nN and from Fig. 11 r =2.75 nm. The calculated value of nano-indentation hardness H2 is 8.029 GPa. When the maximum depth is 3 nm, F máx =244.66 nN and r =3 nm. The calculated value of nano-indentation hardness H3 is 8.675 GPa, which is slightly larger than it obtained at indentation depth of 2 nm. It is because the indenter is pressed down to the subsurface defects area at indentation depth of 3 nm, and the deformation resistance of the subsurface defects increases. Therefore, the hardness of the single crystal copper increased. It can be concluded from the result that the subsurface defects make the machined surface much harder, which is work-hardening phenomenon.
The Young’s modulus E of single crystal copper can be calculated by Eq. 9 combining the data in the Table 3. The calculation results are shown in Table 4. It can be noted that the Young’s modulus becomes distinctly higher when the indentation depth is smaller than 1.5 nm. In the initial stage of nano-indentation, the indenter does not contact the defects residual area in subsurface. However, the work-hardening effect makes the specimen material not easily be occurred elastic deformation; therefore, the Young’s modulus of single crystal copper is larger in the initial stage of indentation. The value of Young’s modulus is 119.4 GPa when indentation depth is 2 nm, which is almost the same with Zhang’s research (120.4 GPa) [14]. With the increase of indentation depth, the Young’s elastic modulus of single crystal copper specimens decreases gradually, and the ability of materials to resist elastic deformation is weakened. It is due to the permanent elastic deformation is derived from the dislocation motion and its interaction with subsurface defects. It has been revealed that the nano-cutting-induced subsurface defects will affect the physical and mechanical properties of single crystal copper materials, which is also applicable to other FCC materials. The existence of subsurface defects will enhance the hardness of machined surface and weaken the ability of material to resist elastic deformation, in which the mutual evolution between dislocations and subsurface defects plays an important role. Therefore, it is very important to predict the thickness of subsurface deformation layer and study the surface properties for nano-fabrication.
Conclusiones
The subsurface defects stable exist in workpiece after nano-cutting can affect the mechanical properties, which is critical to the service performance and life of nano-structures. The previous studies are mainly based on perfect crystal materials or artificial constructing hypothetical defects, which is far from the actual subsurface defects. In this paper, molecular dynamics simulation of nano-cutting is performed to construct the specimen model with subsurface defects. Based on the built MD model, nano-indentation simulation is carried out to study the influence of machining-induced subsurface defects on the physical and mechanical properties of single crystal copper materials. The interaction mechanism between dislocation and complex defects during nano-indentation is studied. The nano-indentation hardness and Young’s elastic modulus of single crystal copper materials are calculated. Based on the above analysis, some interesting conclusions can be drawn as follows.
- 1.
The dislocation nucleation and expansion in workpiece subsurface are driven by the extrusion and shearing action of cutting tool during the nano-cutting process, which results in the fluctuation of cutting force. After nano-cutting, there are stable defect structure residues in the subsurface of workpiece, such as vacancy defects, stacking faults, atomic clusters, SFT, and stair-rod dislocations, which together constitute the subsurface defect layer of workpiece.
- 2.
The existence of subsurface defects affects the nucleation and expansion of dislocations during nano-indentation process. Some stable defects directly below the indenter, such as V-shaped dislocation and SFT1, are annihilated after indentation. And SFT2 far from the indentation region is transformed into a smaller one. Secondary processing of nano-indentation can restore typical internal defects of the workpiece, but the subsurface defects in the secondary processing area are aggravated.
- 3.
The nano-indentation hardness of specimens increases with the introduction of subsurface defects, which results in the formation of work-hardening effect. The Young’s modulus of single crystal copper is larger in the initial stage of indentation and gradually decreases with the increase of indentation depth. The existence of subsurface defects can weaken the ability of material to resist elastic deformation, in which the mutual evolution between dislocations and subsurface defects plays an important role.
Disponibilidad de datos y materiales
Las conclusiones de este manuscrito se basan en los datos que se presentan y se muestran en este documento.
Abreviaturas
- MD:
-
Dinámica molecular
- SSD:
-
Subsurface defects
- SFT:
-
Stacking fault tetrahedral
- PBC:
-
Periodic boundary condition
- LAMMPS:
-
Large-scale atomic/molecular massively parallel simulator
- EAM:
-
Embedded-atom method
- CSP:
-
Centro-symmetry parameter
- FCC:
-
Face center cubic
- CNA:
-
Common neighbor analysis
- HCP:
-
Close-packed hexagonal
- BCC:
-
Body centered cubic
- ICO:
-
Icosohedral
- DXA:
-
Dislocation extract algorithm
Nanomateriales
- La evolución del mercado de materiales de impresión 3D:tendencias y oportunidades en 2019
- La evolución de SLS:nuevas tecnologías, materiales y aplicaciones
- ¿Cómo evalúan los ingenieros los materiales plásticos y la resistencia del material?
- Compuesto híbrido Nanoestructurado de sílice / oro-celulosa-Amino-POSS mediante el proceso Sol-Gel y sus propiedades
- El efecto del plasma de no equilibrio por contacto sobre las propiedades estructurales y magnéticas de Mn Х Fe3 - X О4 Espinelas
- Propiedades paramagnéticas de nanomateriales derivados del fullereno y sus compuestos poliméricos:efecto de bombeo drástico
- Efecto sinérgico del grafeno y los MWCNT en la microestructura y las propiedades mecánicas de los nanocompuestos de Cu / Ti3SiC2 / C
- Propiedades de los materiales de ingeniería:generales, físicas y mecánicas
- Lista de 14 diferentes propiedades mecánicas de los materiales
- Propiedades de los materiales de acero y las herramientas utilizadas para punzones
- Diferentes tipos de propiedades mecánicas de los materiales.