Formación de cortinas calientes
Esta barra lateral en línea para el artículo de marzo de 2021, "Avanzando en la caja de alas con infusión de OOA" tiene como objetivo reunir lo que CW ha escrito sobre la formación de cortinas calientes a lo largo de los años en un solo lugar y, con suerte, proporcionará un recurso útil. A continuación se muestran extractos de varios artículos, de 2010 a 2020, con fotos para ayudar a demostrar cómo la formación de cortinas en caliente ayuda a automatizar la producción de materiales compuestos.
2010, GKN Aerospace, mástiles A400M
De: "Los largueros de las alas de material compuesto llevan los enormes motores turbohélice"
Phil Grainger, director técnico y tecnólogo jefe de GKN Aerospace, explica que la construcción manual de una pieza tan grande, como se hizo en los primeros largueros del A400M, es lenta, con una tasa de colocación típica de 0,75 kg / h (1,5 lb / h). Sin embargo, durante la producción en serie, la pieza se colocará plana, utilizando una capa de cinta automatizada (ATL) y posteriormente se formará una capa caliente . en forma de cesárea. En este punto, se podrán alcanzar tasas de laminado de 25 kg / h (50 lb / h). Grainger enfatiza que estas son tasas promedio alcanzables durante un turno, en partes reales.
Para automatizar el proceso, GKN Aerospace ha invertido en un gran ATL con un lecho de 20 m / 63 pies, fabricado por MTorres (Navarra, España). El ATL puede colocar las preformas complejas en sus formas desarrolladas a partir de un preimpregnado unidireccional, utilizando una cinta unidireccional de fibra de carbono / epoxi endurecido 977-2 suministrada por Cytec Engineered Materials Ltd. (ahora Solvay, Wrexham, Reino Unido). Para formar la cesárea, la preforma se moverá de la capa de cinta a un formador de cortinas calientes proporcionado por el fabricante de equipos Aeroform Ltd. (Poole, Dorset, Reino Unido). Para facilitar la extracción de vacío, la capa se colocará entre dos diafragmas hechos de película de poliimida Kapton, suministrada por DuPont Electronic Technologies (Circleville, Ohio). Se evacuará el espacio entre las películas y luego se aplicará calor infrarrojo desde arriba de la pieza para elevar la temperatura a 60 ° C / 140 ° F durante un período de una hora. Esto asegura que incluso el material en el centro de la sección más gruesa en el extremo de la raíz se caliente uniformemente a la misma temperatura. Luego se aplicará presión suavemente para formar el laminado, constreñido por los dos diafragmas sobre una herramienta liviana que representa con precisión la superficie interior del larguero. Este proceso de formación de C se logra muy lentamente durante un período de 20 minutos. (Después de la formación, las películas de Kapton se descartan).
2014, FACC, solapas A321
De:"FACC AG:Aerocomposites powerhouse"
En la Planta 3 se fabrica una amplia variedad de flaps, carenados y superficies de control de vuelo. Aquí también, las eficiencias de la colocación de cinta automatizada (ATL) y la formación de cortinas en caliente son explotados. Este último aplica calor y presión a las preformas planas de ATL utilizando un núcleo y una almohadilla de formación flexible para producir formas tridimensionales (ver Fig. 7). Un ejemplo es A321 en curso producción de solapas, que utiliza una celda de trabajo automatizada de última generación diseñada a medida por Fill (Gurten, Austria).
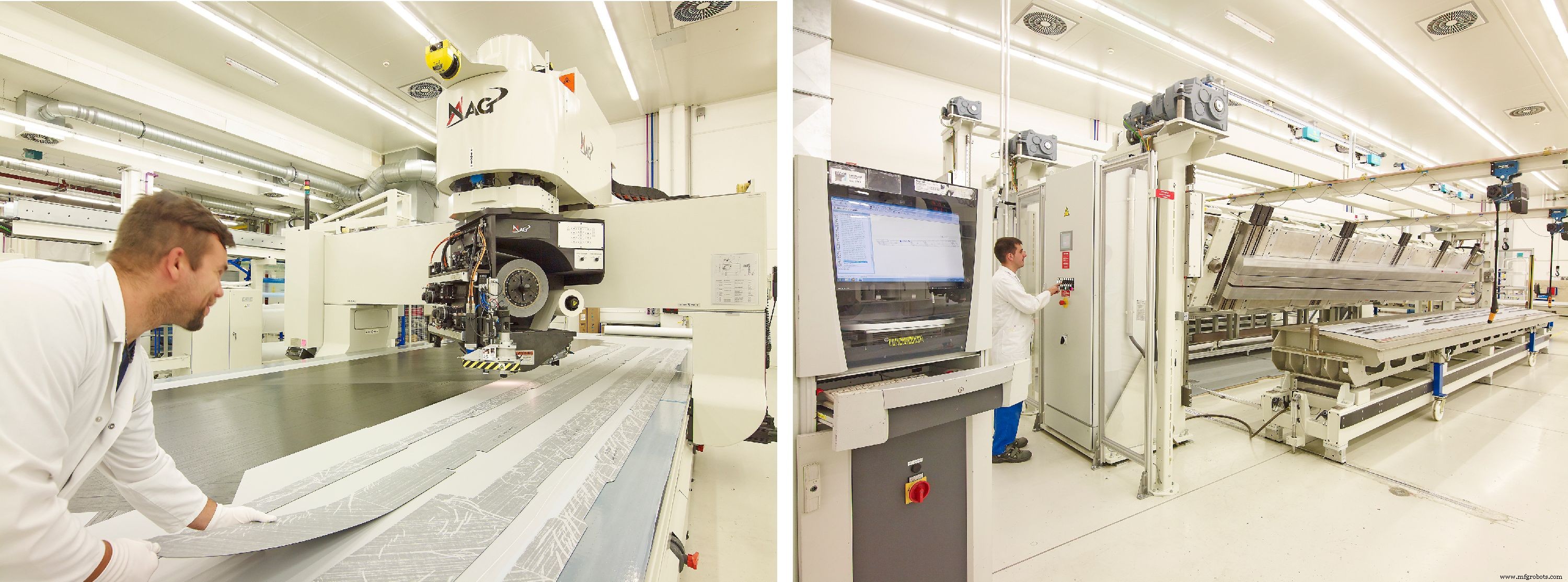
2018, relleno, preformado automatizado
De:"Preformado automatizado, Parte 7:Llene Gesellschaft"
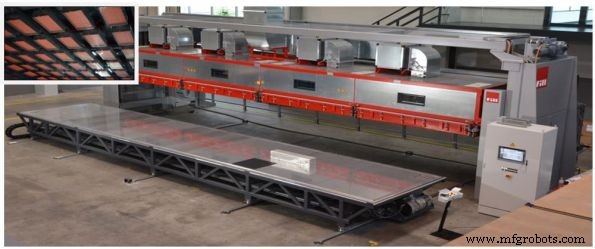
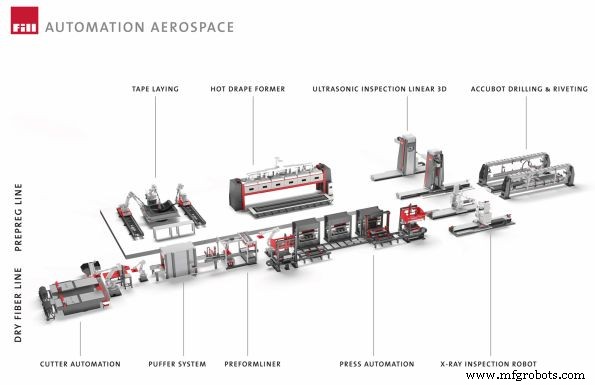
En los artículos recientes de la gira que Sara Black y yo escribimos sobre compuestos de alto rendimiento en Israel, notamos que la mayoría de las empresas utilizaban formación de cortinas en caliente . De hecho, en Elbit Cyclone, nuestro guía turístico Jonathan Hulaty declaró:"No sé cómo se hace este tipo de producción de piezas preimpregnadas de alta velocidad sin formación de cortinas en caliente", refiriéndose a vigas y montantes para ensamblajes de Boeing 787. Formadoras de cortinas calientes (HDF) también son considerados indispensables por FBM e Israel Aerospace Industries.
Fill ha suministrado sistemas HDF durante años, incluidas varias unidades en producción en FACC. Básicamente son sistemas de formación al vacío, equipados con infrarrojos u otros tipos de elementos calefactores y una membrana de caucho de silicona reutilizable para calentar y comprimir, reducir el volumen, capas de preimpregnado en sus herramientas antes del curado. El HDF se convierte en una pieza clave en la línea completa de producción de aerocomposites que se muestra a continuación.
2018, FBM, 787 piezas
De:"La fusión de empresas emprendedoras centradas en el metal afirma que los compuestos son lo primero"
CW se conduce primero a una sala limpia, donde los trabajadores colocan una variedad de piezas. Este día, en varias estaciones, cada una equipada con una pantalla computarizada de asistencia para la colocación, el enfoque son las partes del Boeing 787. Las pantallas táctiles fáciles de entender muestran claramente los ángulos de colocación de cada capa y cómo están para ser colocado en cada herramienta. Una máquina de “guillotina” de Century Design (San Diego, CA, EE. UU.), Con una mesa giratoria de 2 m de diámetro y una cuchilla en el centro, permite cortar rápidamente capas en ángulo del preimpregnado de carbono / epoxi. Las herramientas para los marcos de las puertas 787 son mandriles de acero con forma, generalmente más largos que anchos, desde unos pocos centímetros de largo hasta ~ 2 m de largo, que se utilizan para producir cientos de marcos, soportes y clips. Los técnicos de laminado utilizan una mesa de corte de cama plana automatizada de Assyst-Bullmer Inc. (Wakefield, Reino Unido) para cortar hasta 50 capas apiladas en una sola operación.
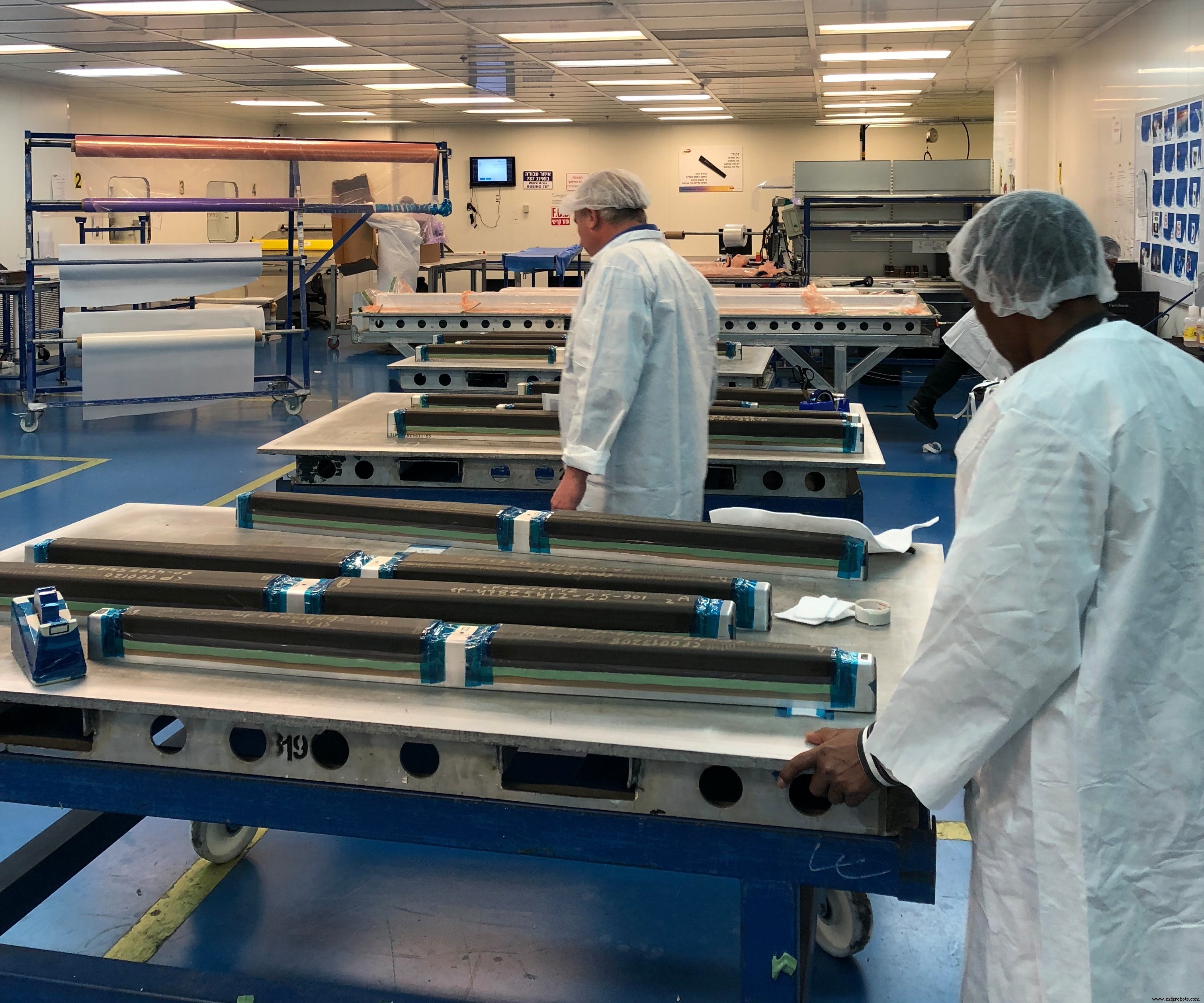
Corte, preparación y colocación de piezas pequeñas dentro de la sala limpia de FBM para una amplia variedad de piezas esterilizadas en autoclave más pequeñas. Crédito de foto: CW , Sara Black.
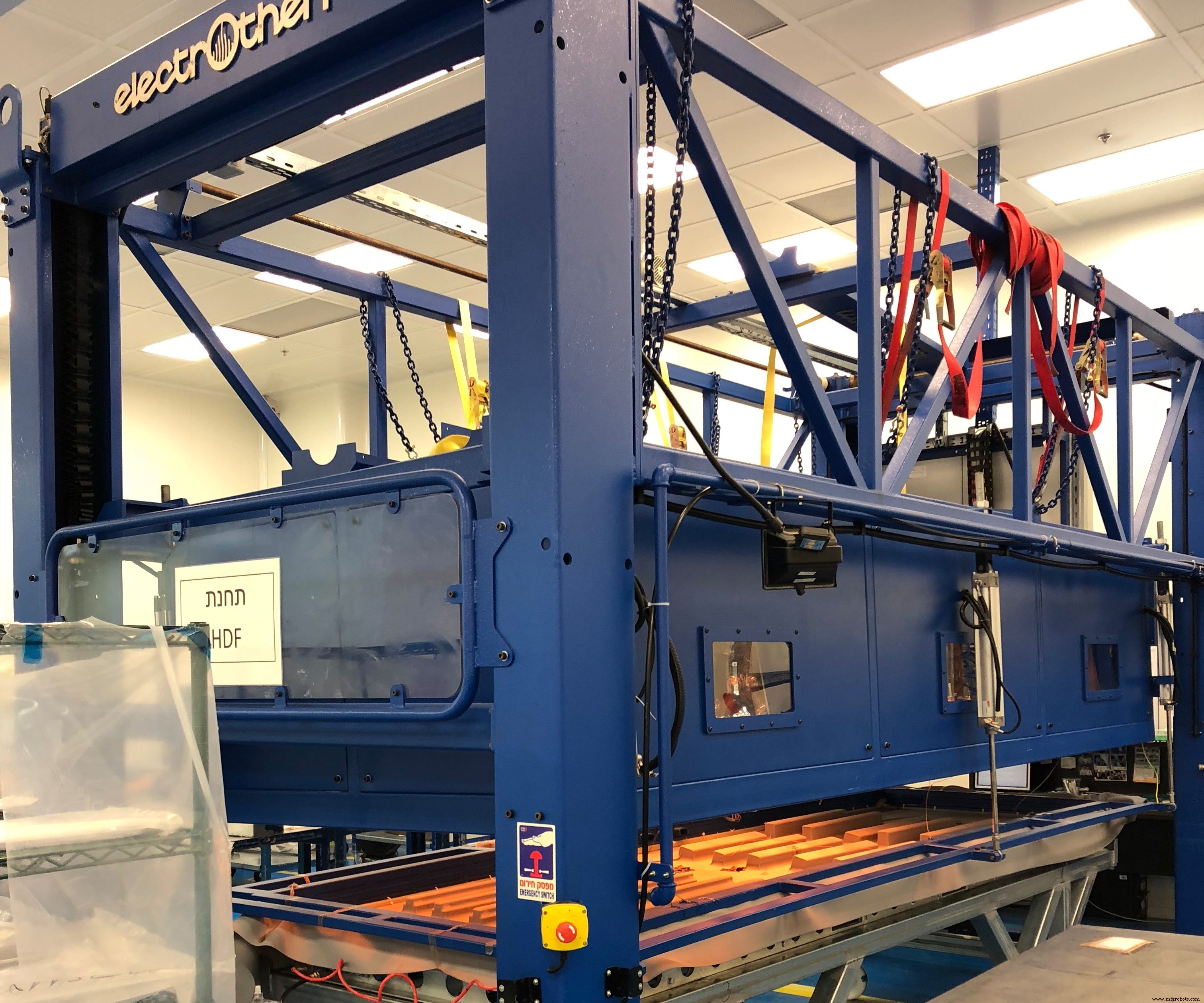
La máquina formadora de cortinas en caliente de FBM, suministrada por la compañía israelí Electrotherm Industry, elimina los pasos de reducción de volumen intermedios, formando hasta 50 capas unidireccionales de una sola vez, y se le atribuye la aceleración del proceso de laminado de FBM antes del curado. Crédito de la foto: CW , Sara Black.
La sala limpia está dominada por un formador de cortinas en caliente (HDF) . Fabricada por ElectroTherm Industry (Migdal HaEmek, Israel), la máquina estática (la empresa también fabrica versiones móviles en carros) es un sistema de formación al vacío hecho a medida, equipado con elementos calefactores infrarrojos y una membrana de caucho de silicona para calentar y comprimir el compuesto. bandejas en las herramientas, antes de curar. El HDF Puede dar forma a hasta 50 capas apiladas, dice Poliker, sin pasos intermedios de reducción de volumen:"Buscábamos eliminar la complejidad del proceso, por lo que formamos las capas de una sola vez". Después de que el preimpregnado se caliente y se consolide en el HDF , se coloca una masilla sobre toda la bandeja, antes de embolsar. Fabricado con un compuesto de fibra de carbono, el sellador presenta un acabado superficial rugoso. Poliker no revelará detalles del material patentado, pero sí dice que puede soportar temperaturas de curado en autoclave de 177 ° C:"Simula una herramienta de matriz combinada". Añade que las herramientas de mandril se reacondicionan internamente, según sea necesario. El ensacado y los consumibles son suministrados por Airtech International (Huntington Beach, CA, EE. UU.).
2018, Elbit Cyclone, 787 partes
De:"Al servicio del mundo de los compuestos en Israel y EE. UU."
A la derecha, los trabajadores de la sala limpia para las piezas del Boeing 787 colocan preimpregnado para una variedad de piezas, desde pequeños clips y montantes hasta complejas vigas en J, I y C, así como puertas de tren de aterrizaje de morro de varias piezas. El preimpregnado se corta utilizando un cortador de tela automático Assyst Bullmer (Wakefield, Reino Unido) y una máquina de guillotina para cortar pilas gruesas en cualquier ángulo. El congelador de preimpregnaciones se encuentra junto a la sala limpia. Hulaty señala que a veces se cortan pilas de preimpregnado, se preparan y se vuelven a colocar en el congelador. Los sistemas de proyección láser Aligned Vision (Chelmsford, MA, EE. UU.) Ubicados en toda la sala limpia ayudan a colocar las manos.
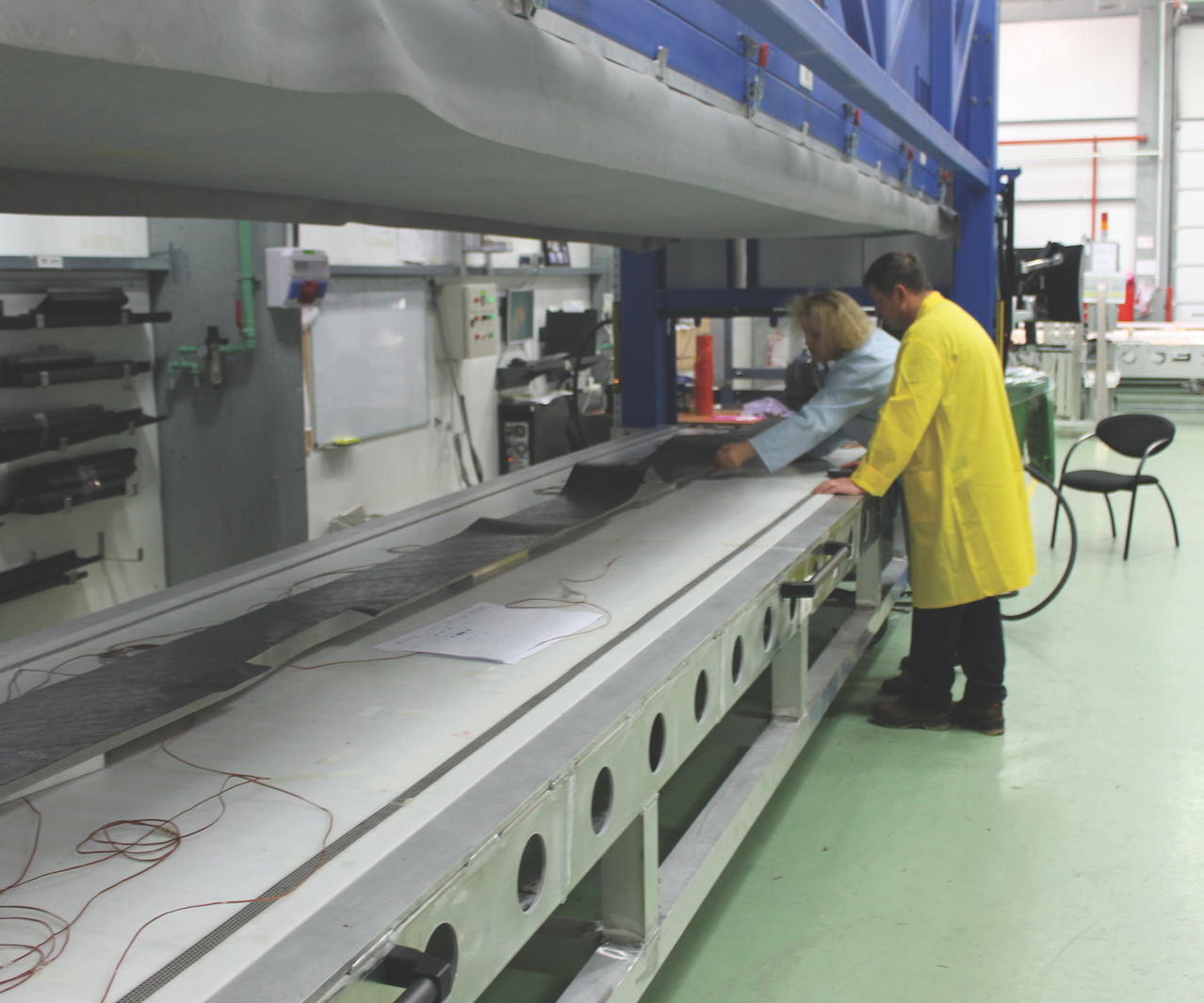
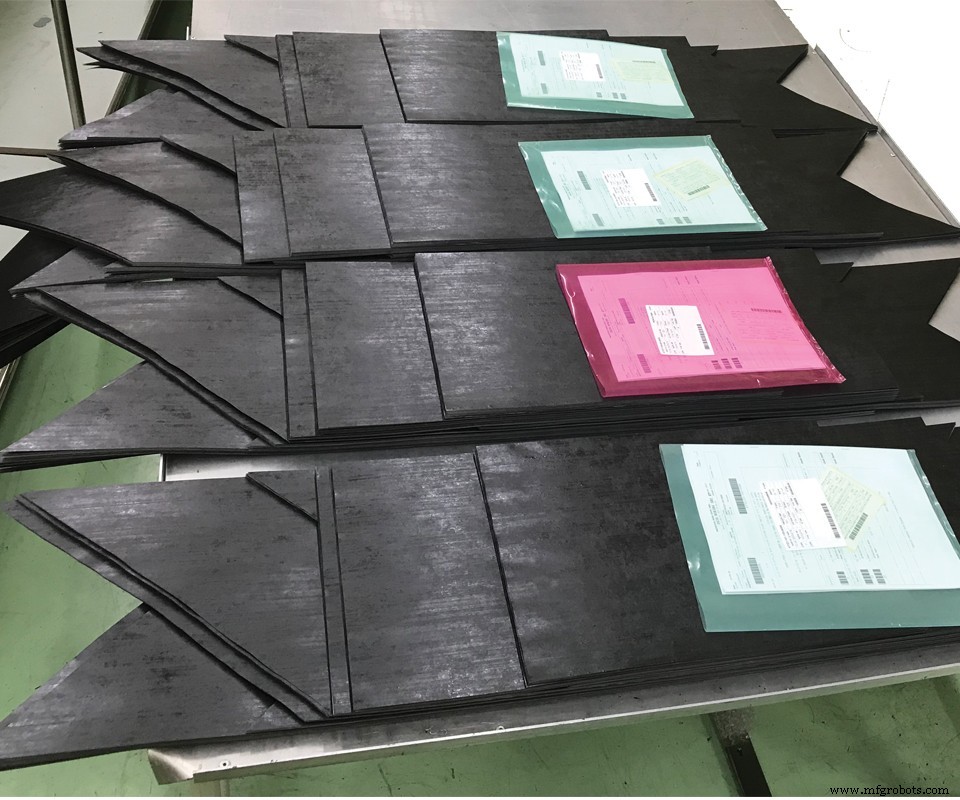
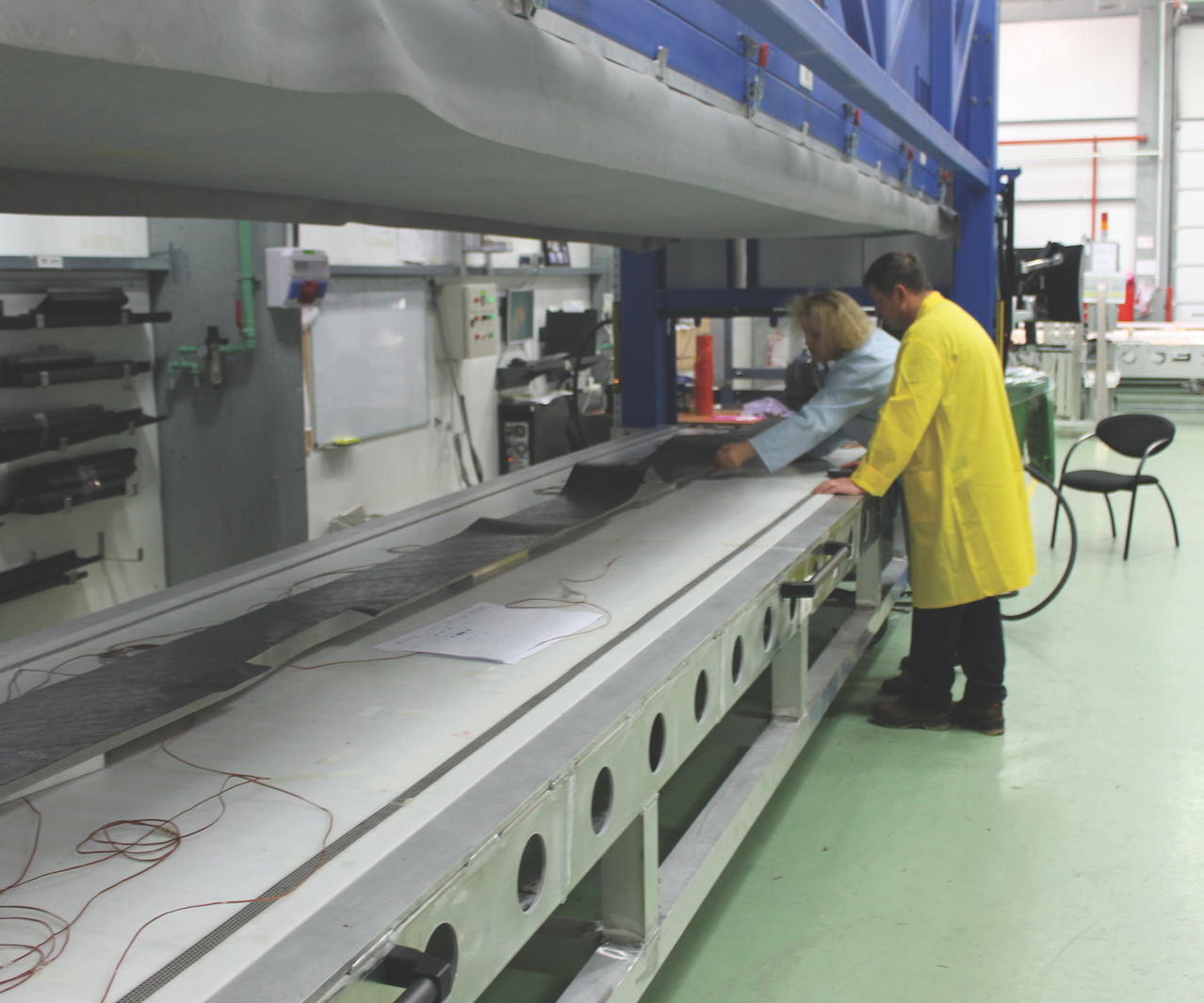
Las piezas de las vigas del piso de plástico reforzado con fibra de carbono (CFRP) se colocan sobre mandriles de metal macho. Hulaty detalla el proceso simplificado:“Primero colocamos las pilas de preimpregnado y luego las aplicamos al mandril. Esto ahorra mucho tiempo en comparación con la aplicación gradual sobre la herramienta. A continuación, se cubren las capas con un revestimiento de CFRP de nuestro propio diseño, que ayuda a garantizar una repetibilidad del 100% en las piezas ”.
Se forma una cortina caliente La máquina se asienta a lo largo de la pared trasera de la sala limpia, lo que permite eliminar el volumen de muchas piezas por ciclo. "No sé cómo se hace este tipo de producción de piezas preimpregnadas de alta velocidad sin formación de cortinas en caliente", dice Hulaty en referencia a piezas como vigas y montantes. Y, sin embargo, reconoce que este paso no es el cuello de botella ni el autoclave. “El mecanizado al final, después del curado, es el cuello de botella”, sostiene, y explica que para las piezas de vigas de piso largas, es más rápido apilar una pila simple y mecanizarla después del curado. “El autoclave no es el problema porque podemos apilar muchas piezas para curar al mismo tiempo”, agrega. "Por lo tanto, obtenemos una buena tasa de producción por ciclo de curado".
2018, IAI, aeroestructuras
De:"La piedra angular de la aerodefensa de Israel lista para un mayor alcance mundial"
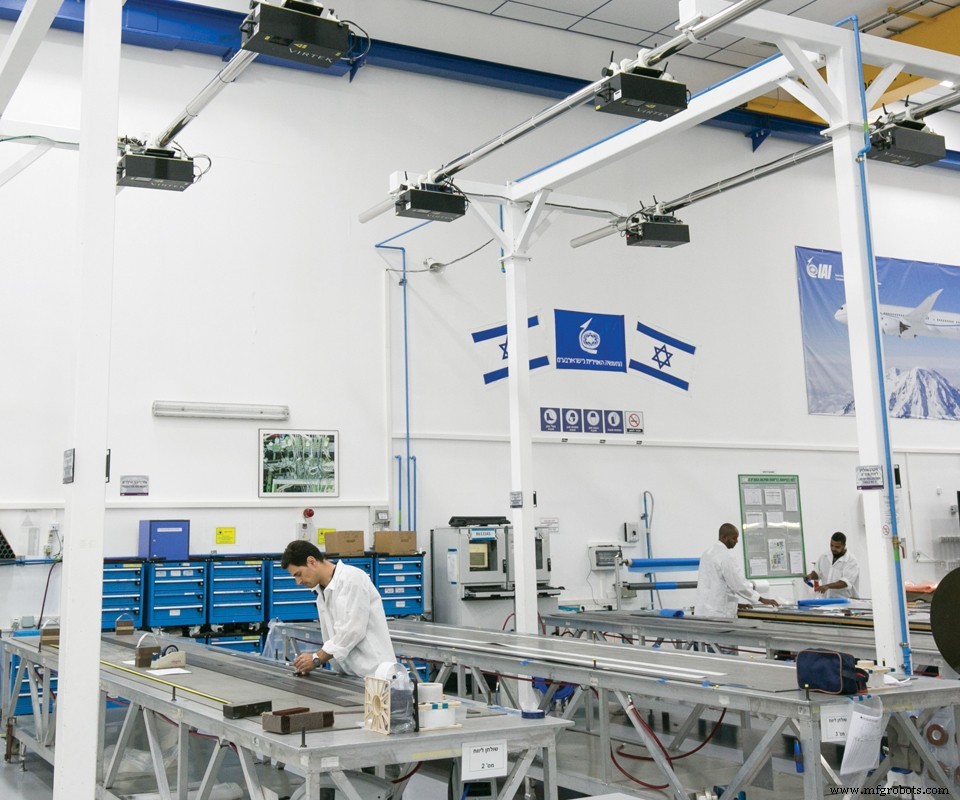
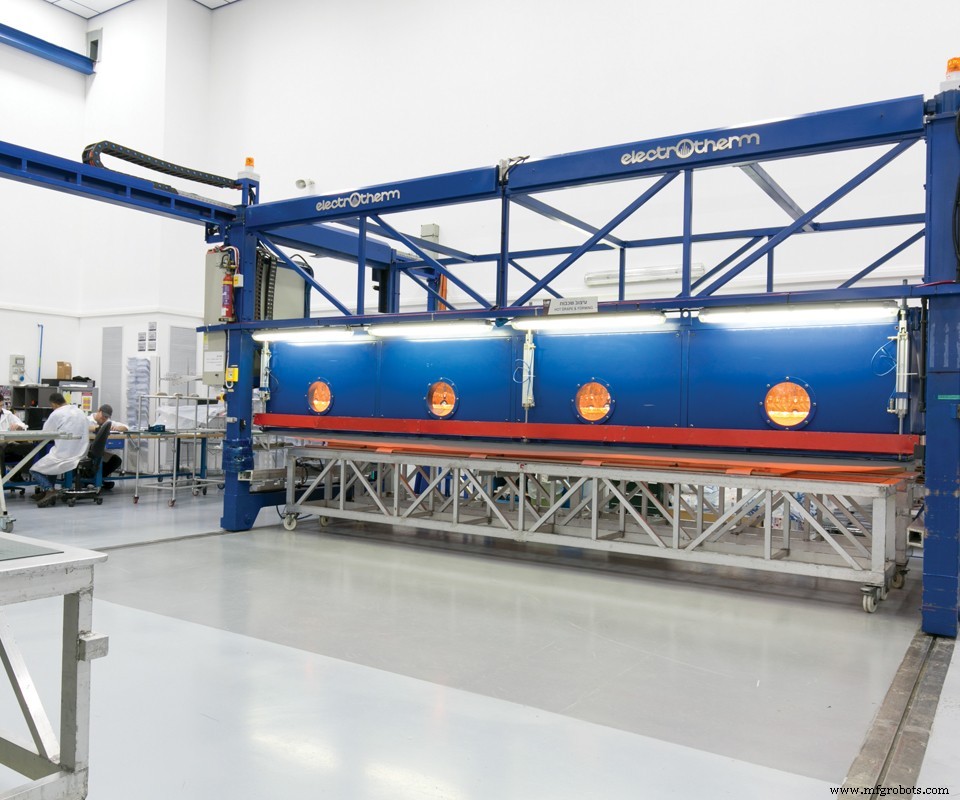
IAI utiliza una máquina formadora de cortinas en caliente para reducir el volumen de capas gruesas de preimpregnado en masa, eliminando la necesidad de pasos intermedios convencionales de reducción de volumen. Crédito de la foto:Industrias Aeroespaciales de Israel
Las operaciones de materiales compuestos del IAI abarcan la fabricación de piezas y ensamblajes para jets ejecutivos y aviones comerciales, vehículos aéreos no tripulados (UAV) y aviones militares. Las piezas producidas incluyen estabilizadores verticales y horizontales, timones, estructuras de alas, góndolas de motor, vigas de piso, marcos de puertas, mamparos estructurales, nervaduras y refuerzos, superficies de control, carenados y radomos. Entre sus capacidades de fabricación se encuentran el laminado manual preimpregnado y el laminado automático de cinta (ATL), formación de cortinas en caliente , curado en autoclave y fuera del autoclave (OOA), incluidos los procesos de moldeo líquido, como la infusión de resina y el moldeo por transferencia de resina (RTM), además de uniones y ensamblajes complejos. La compañía también diseña y construye sus propias herramientas, posee todas las certificaciones clave de calidad aeroespacial y de compuestos y proporciona garantía de calidad a través de pruebas e inspecciones no destructivas integrales.
- La capacidad de producción del IAI es significativa, con 10 autoclaves, siete de los cuales pertenecen a la Div. Aeromontajes. y varían en tamaño desde 4,5 m de largo y 2 m de diámetro, hasta el más grande con 14 m de largo y 4,7 m de diámetro.
- Las capas de preimpregnado se eliminan antes del curado mediante una formación de cortinas calientes máquina (6,9 por 2,7 por 3,1 m) de Electrotherm Industry (Migdal HaEmek, Israel).
2020, Strata, flaps internos del A350-900
De:"Strata entrega 100 juegos de flaps internos para A350-900"
Diseñado para aumentar la capacidad de sustentación total del ala de un avión, se monta un IBF [flap interior] en el borde de salida del ala para aumentar la superficie del ala durante el despegue y el aterrizaje y mejorar la estabilidad durante el vuelo. Strata dice que planea automatizar completamente el proceso de fabricación de IBF, utilizando formación de cortinas en caliente (HDF) y máquinas de colocación de cinta automatizadas (ATL) robóticas controladas por computadora, que obtuvieron la calificación de primera parte (FPQ) y el diseño FAI y verificaciones de calidad a principios de este año.
Como parte del proceso, la compañía dice que la máquina HDF preforma componentes de fibra de carbono para piezas de aviones, lo que permite una producción más rápida de piezas compuestas de alta calidad, y su sistema de calentamiento por radiación infrarroja suaviza rápida y uniformemente la fibra de carbono para producir piezas precisas que se dice que están libres de arrugas por tensión. Además, las dos máquinas ATL de Strata colocan materiales preimpregnados unidireccionales en una cama plana antes de transferirlos a un molde para su posterior procesamiento. Según Strata, su área de trabajo de 2,5 metros por 10 metros permite el procesamiento automatizado de grandes capas compuestas, eliminando la necesidad de una máquina de corte ultrasónica separada y reduciendo los tiempos de procesamiento.
2020, Techni-Modul, nervadura de ala y larguero
De:"Compression RTM para la producción de aeroestructuras futuras"
“Para nosotros, OPTICOMS también se trataba de automatización”, dice Chevallet. Techni-Modul Engineering suministró no solo un sistema de inyección C-RTM para el proyecto OPTICOMS, sino también un robot pick-and-place y una formación en caliente (HDF) máquina, todo integrado en una celda de producción totalmente automatizada. … “Hemos automatizado el clásico apilado manual de pliegues mediante pick and place robótico”, dice Chevallet. “El robot recoge las capas de un cortador automático y las transfiere a la herramienta de preformas calentada que se asienta sobre una mesa de compactación [Pasos 1 y 6] ". Se aplica una capa despegable (película azul en el Paso 6), un respiradero (material blanco en el Paso 6) y una membrana de vacío reutilizable con bisagras (azul claro a la izquierda en los Pasos 2 y 6), seguido de vacío y calor para dar forma previa y eliminar el aire del pila textil ( formación de cortinas en caliente, HDF ) mientras derrite los finos velos termoplásticos para crear una preforma compacta.
Costilla y larguero de ala OPTICOMS
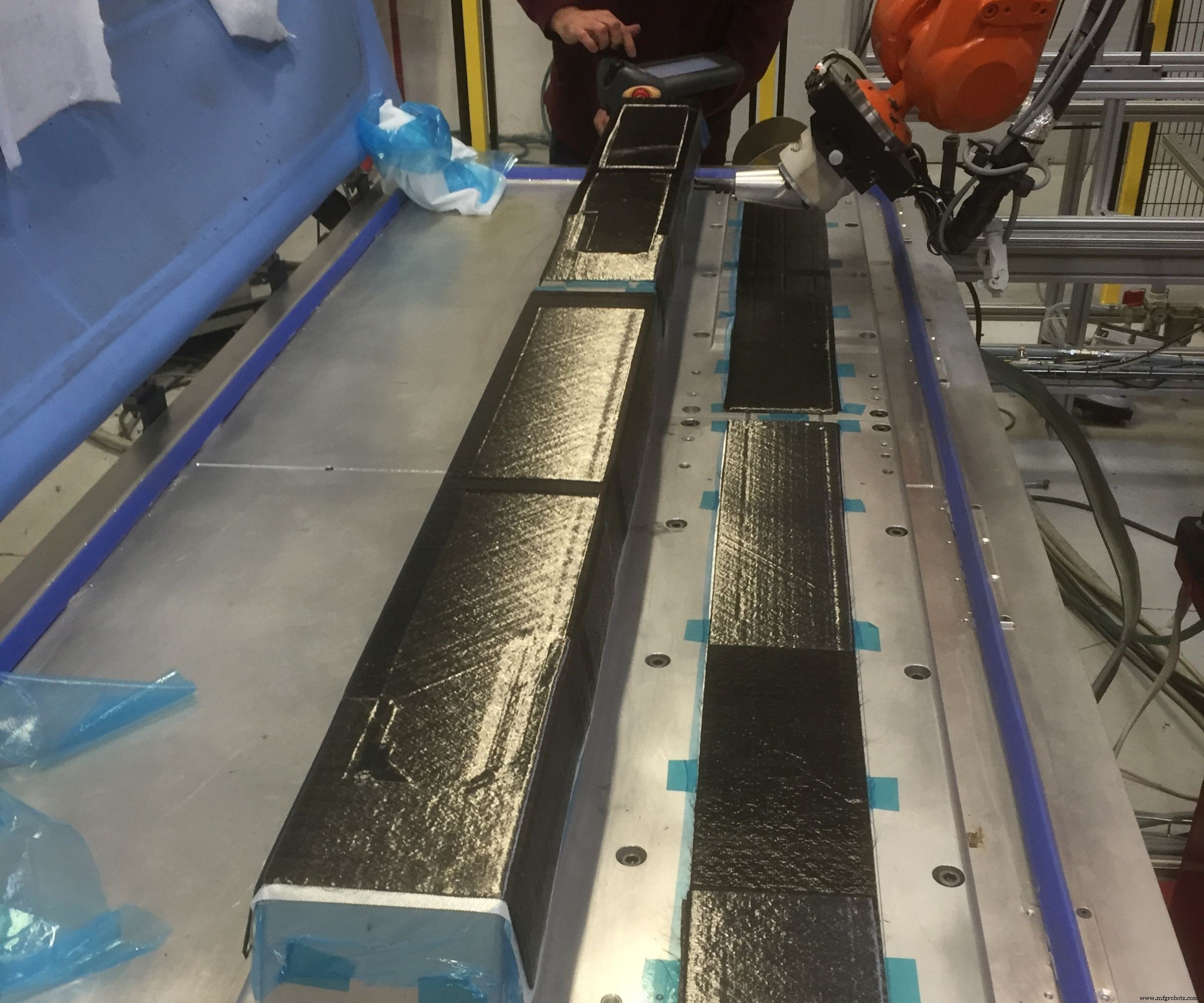
Paso 2. Las herramientas de preformado se asientan sobre una mesa de compactación con una membrana de vacío reutilizable con bisagras (azul, a la izquierda) que se usa para completar una reducción de volumen calentada cada 5-8 capas durante el laminado. Crédito de todas las imágenes:Tecni-Modul Engineering.
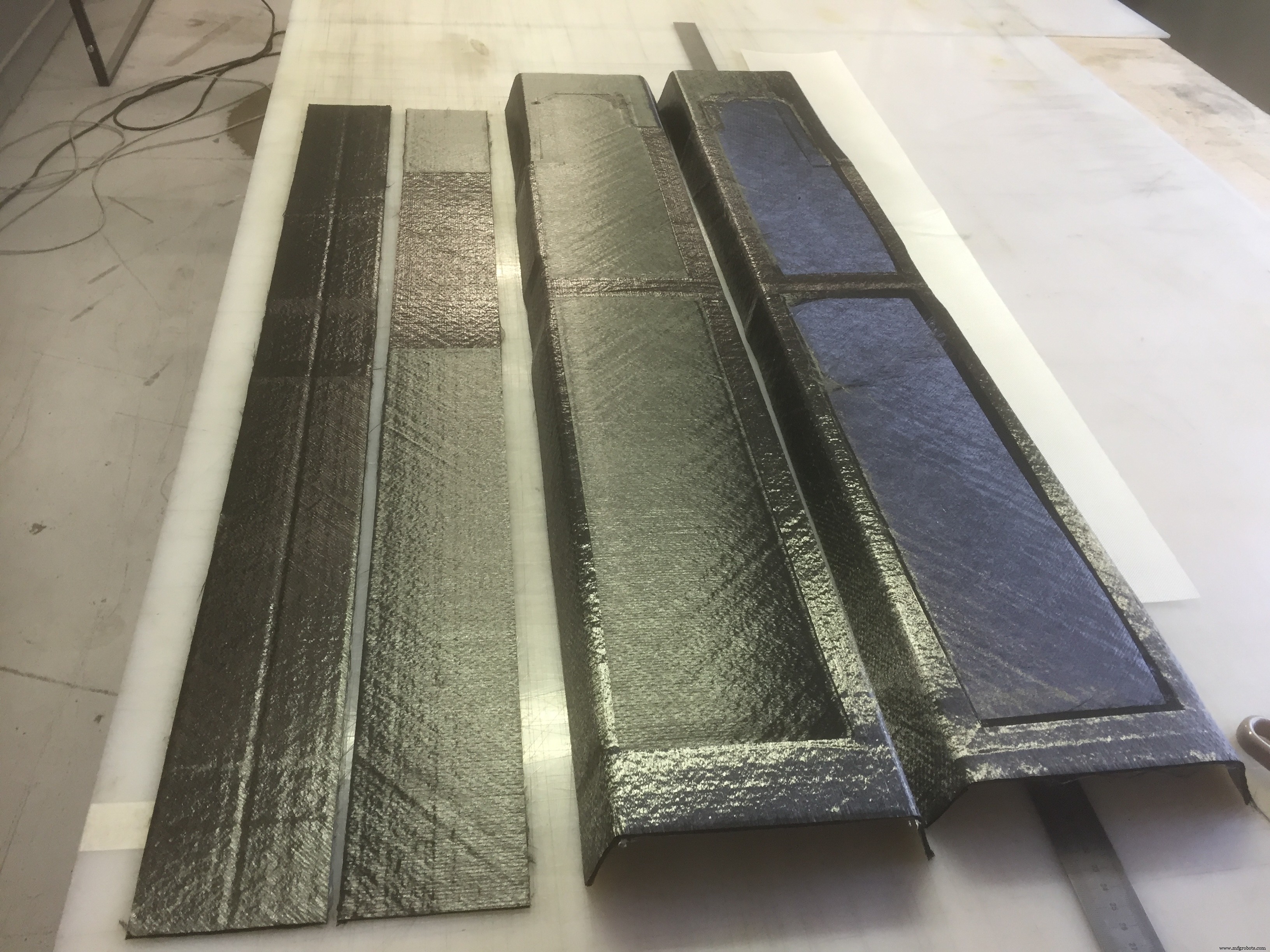
Paso 3. Cada ciclo de preformado de larguero produce una preforma de viga en C (dos comprenden el alma de la viga en I) y una preforma de ala plana. Aquí se muestran dos juegos necesarios para cada zanca de vigas en I.
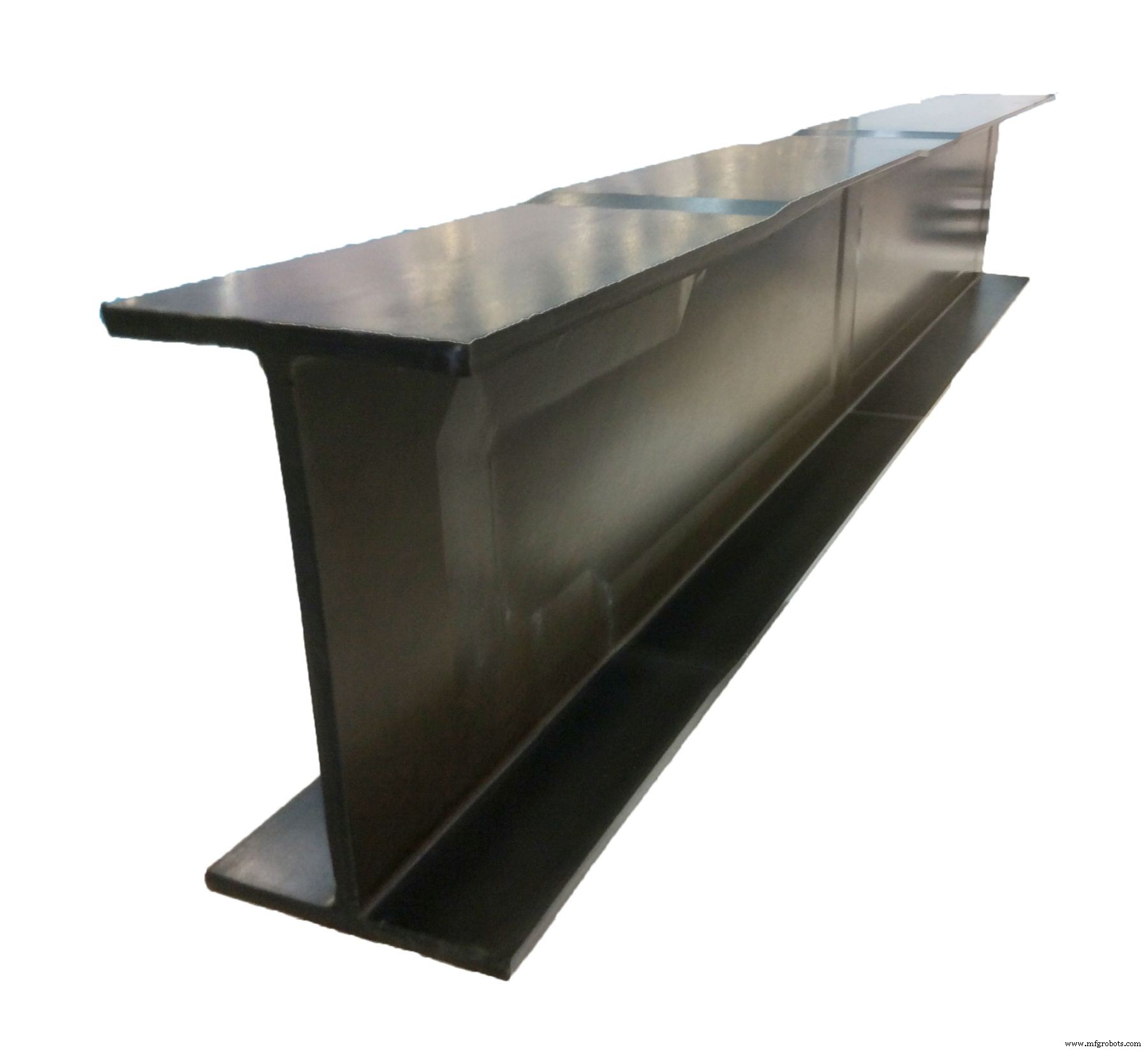
Paso 5. Larguero de vigas en I fabricado con preformas de HDF y RTM para el proyecto Clean Sky 2 OPTICOMS.
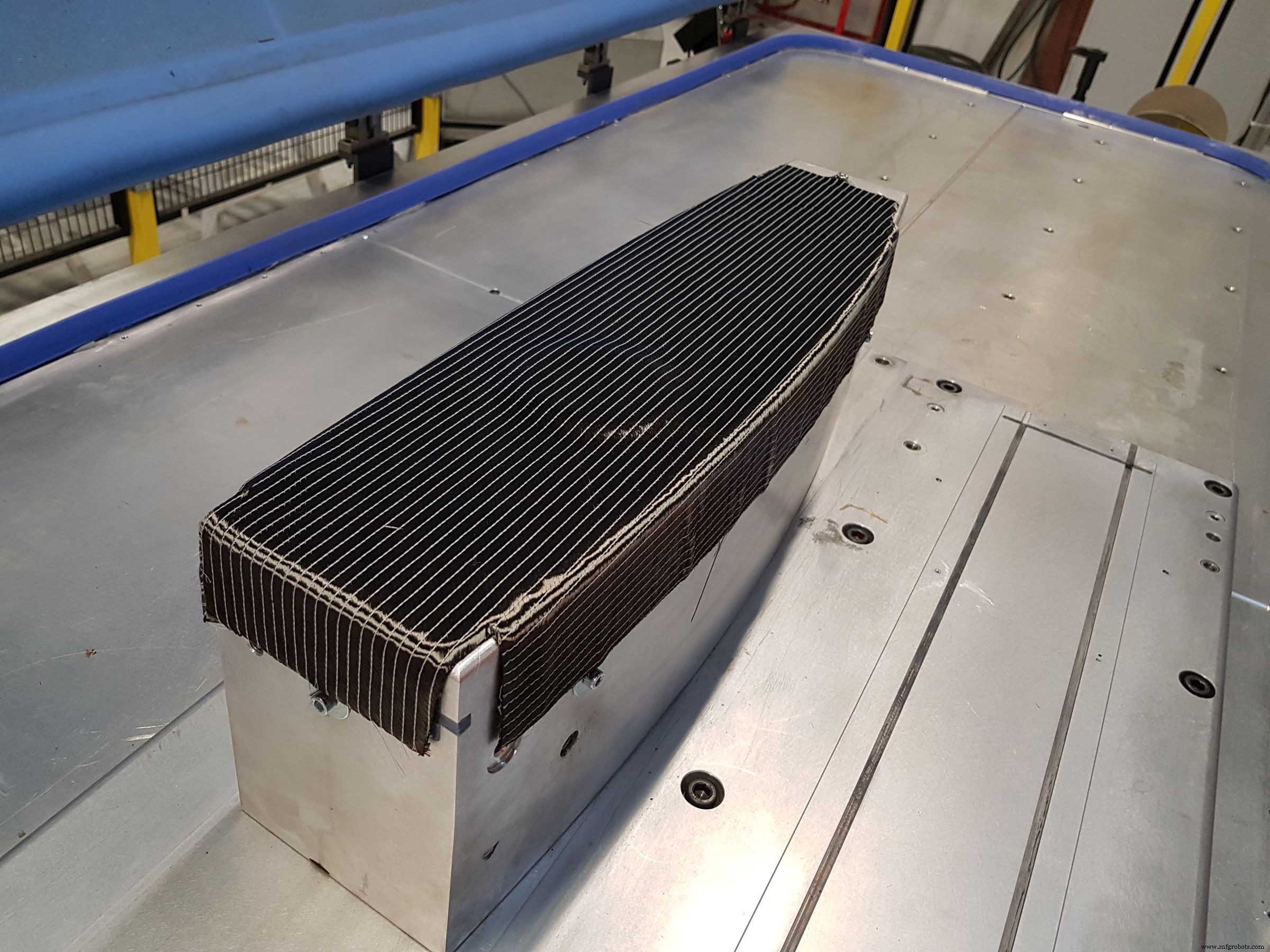
Paso 6. Un robot coloca las capas cortadas en la herramienta de preforma calentada. Cada 5-8 capas, se completa una reducción de volumen calentada para compactar la preforma.
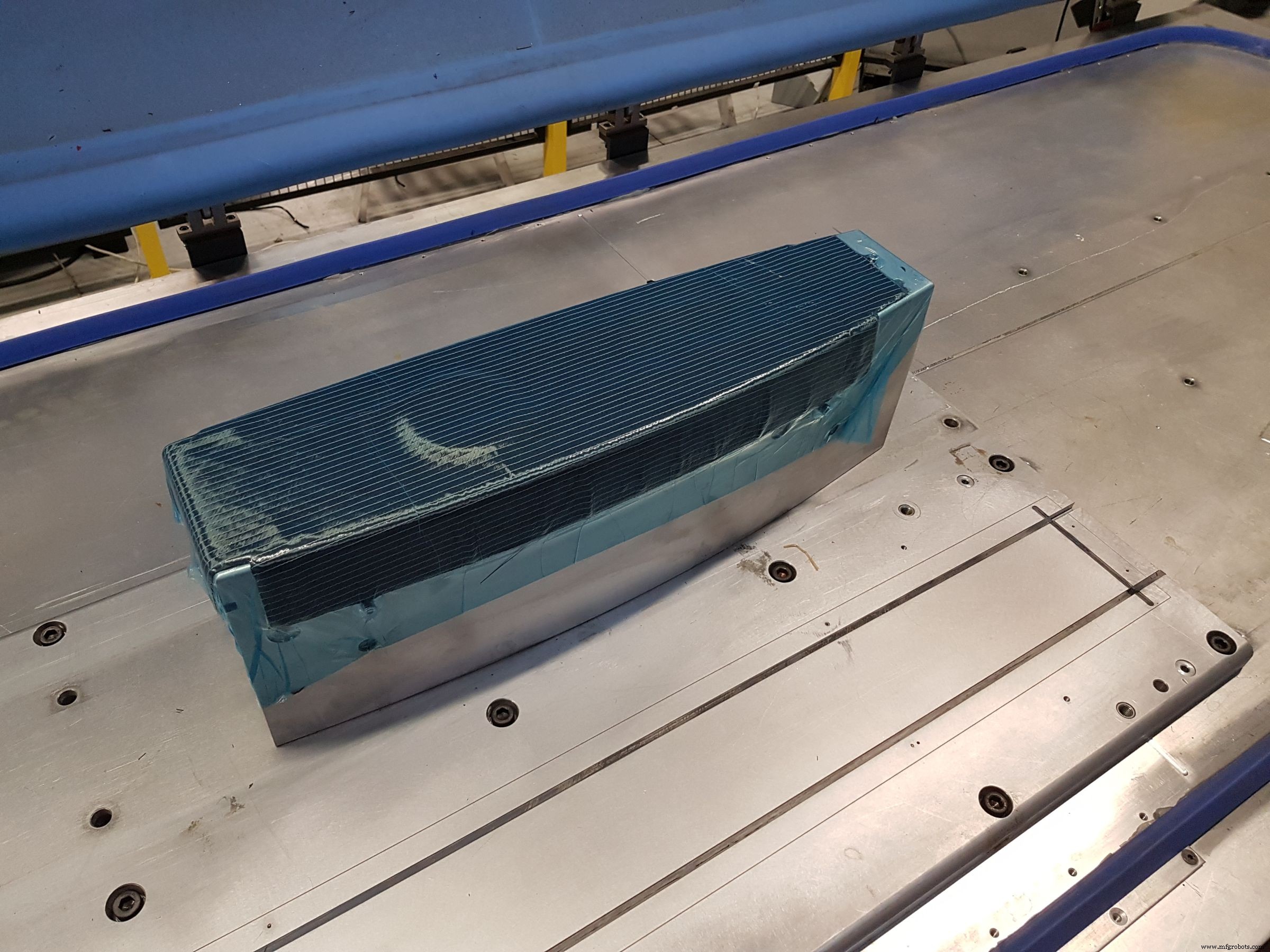
Antes de reducir el volumen, se aplica una película de liberación azul.
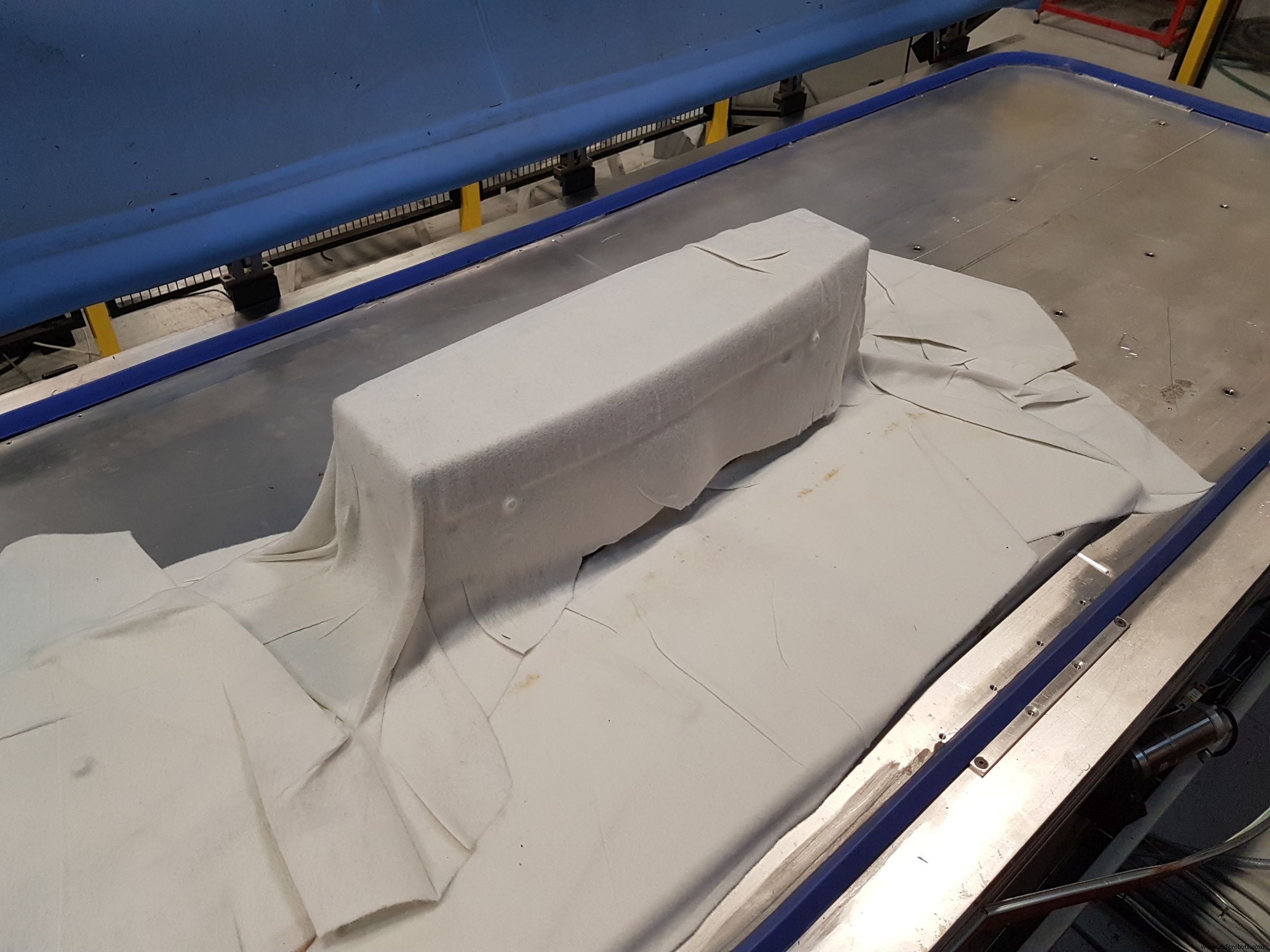
El respiradero se utiliza para extraer aire a través de la preforma.
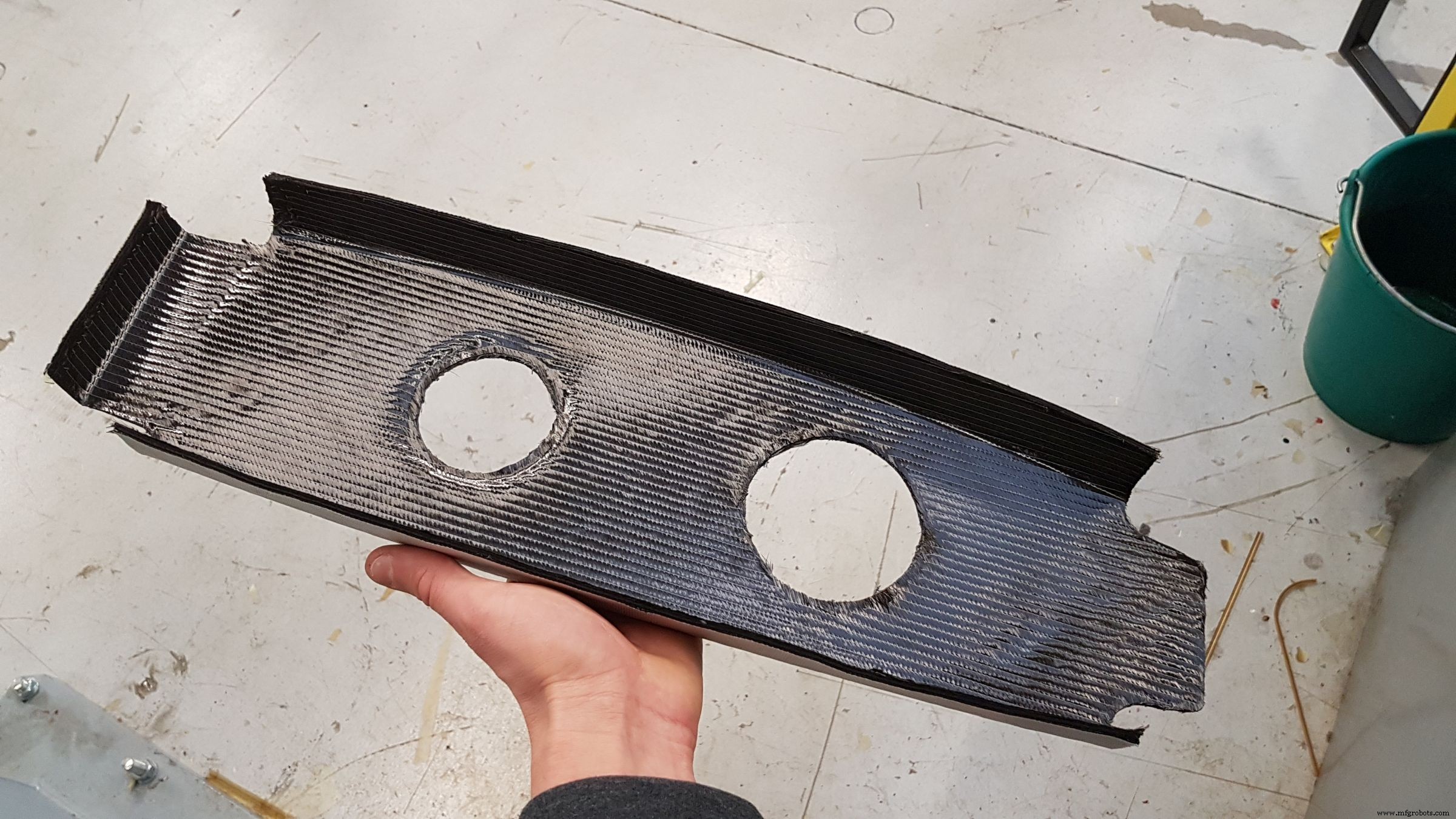
Después de la reducción de volumen final, la preforma se enfría en la herramienta y se recortan los recortes.
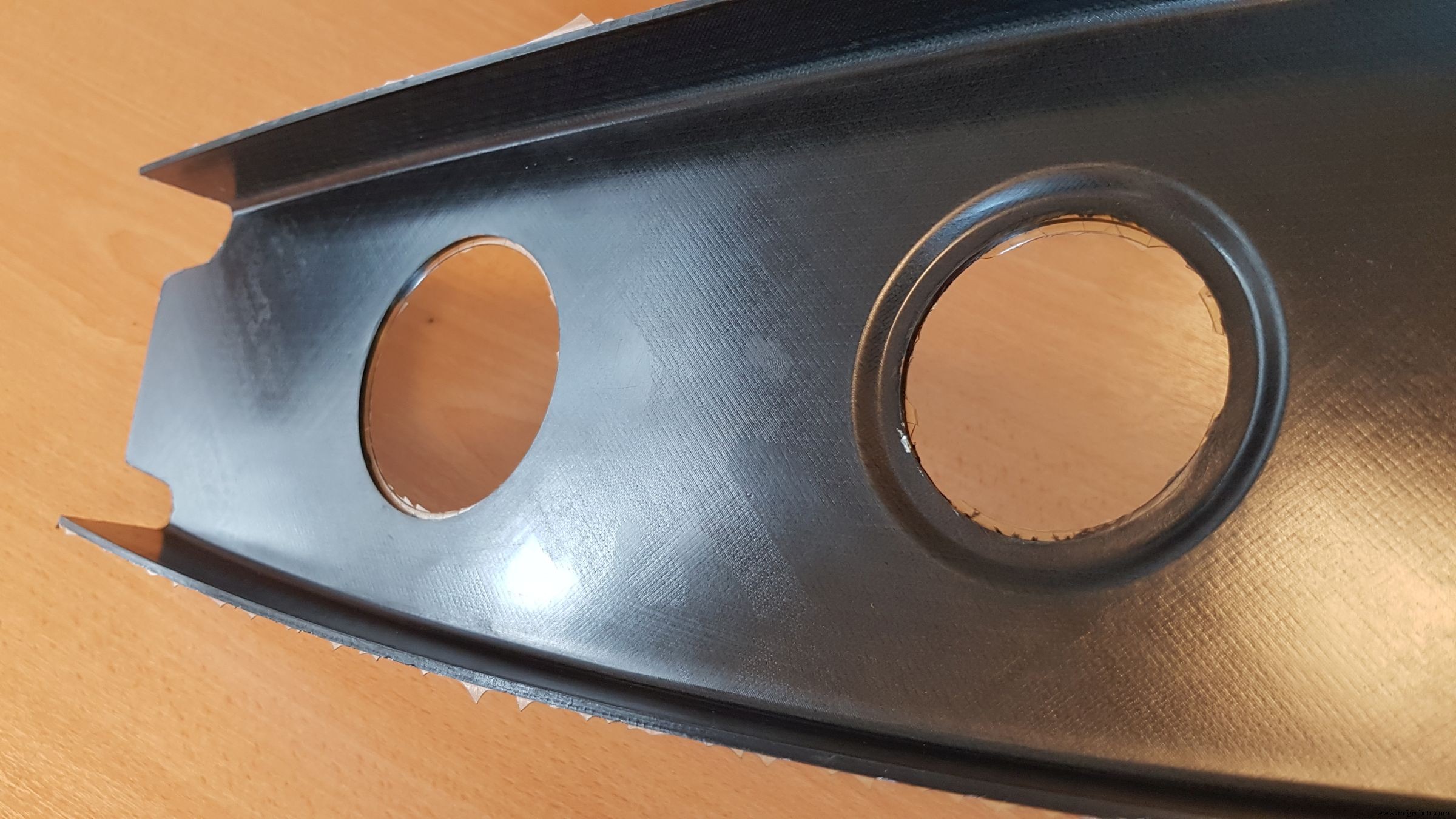
Paso 10. La preforma de nervadura se moldea con RTM y resina epoxi.
Anterior Siguiente“La cantidad de capas que se pueden compactar a la vez depende de los materiales y la forma de la pieza”, explica Chevallet. “Para piezas con curvatura baja, como una piel de alas, posiblemente podría compactar cada 50 capas. Sin embargo, la nervadura OPTICOMS tiene ángulos de 90 grados y el larguero de la viga en I de prueba tiene forma de T, por lo que debe tener cuidado de no formar arrugas en las capas durante el preformado ". Agrega que formas tan complejas pueden requerir compactación cada 5-8 capas, pero aún pueden ser parte de un proceso industrializado de alto volumen:Apilar capas , compactación HDF de 2 minutos , reabrir y apilar nuevamente, seguido de ciclos repetidos de compactación con un enfriamiento final de la preforma en la herramienta antes de transferirla al molde RTM.
fibra
- Perro caliente
- ¿Qué temperatura tiene una cortadora de plasma?
- Grados de acero laminado en caliente
- Proceso de formación de chapa
- AISI 1008 laminado en caliente
- AISI 1015 laminado en caliente
- AISI 1017 laminado en caliente
- AISI 1006 Laminado en Caliente
- AISI 1010 laminado en caliente
- AISI 1012 laminado en caliente
- AISI 1016 laminado en caliente