El devanado de filamentos 3D permite el concepto de asiento del vehículo
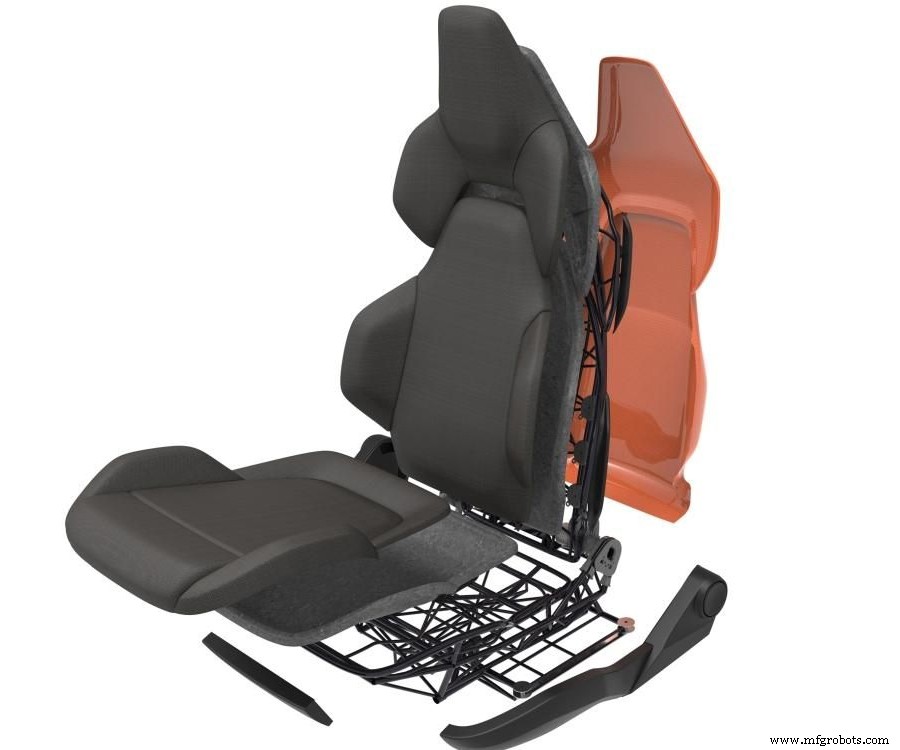
La sostenibilidad y la responsabilidad medioambiental se están convirtiendo en impulsores cada vez más frecuentes de las tendencias tecnológicas en la industria automotriz. Los vehículos de baja energía y bajas emisiones se han convertido en una prioridad para el sector automotriz internacional, y las tendencias hacia tecnologías de transporte alternativas como la electromovilidad y la movilidad aérea urbana (UAM) están ganando impulso. Los fabricantes de equipos originales están buscando materiales y procesos emergentes como facilitadores para estos posibles modos de viaje, pero el cambio en el sector automotriz a menudo es lento. Para que los nuevos materiales y procesos se adopten por completo, no solo deben estar calificados, deben ser rentables y deben permitir una producción de alto volumen.
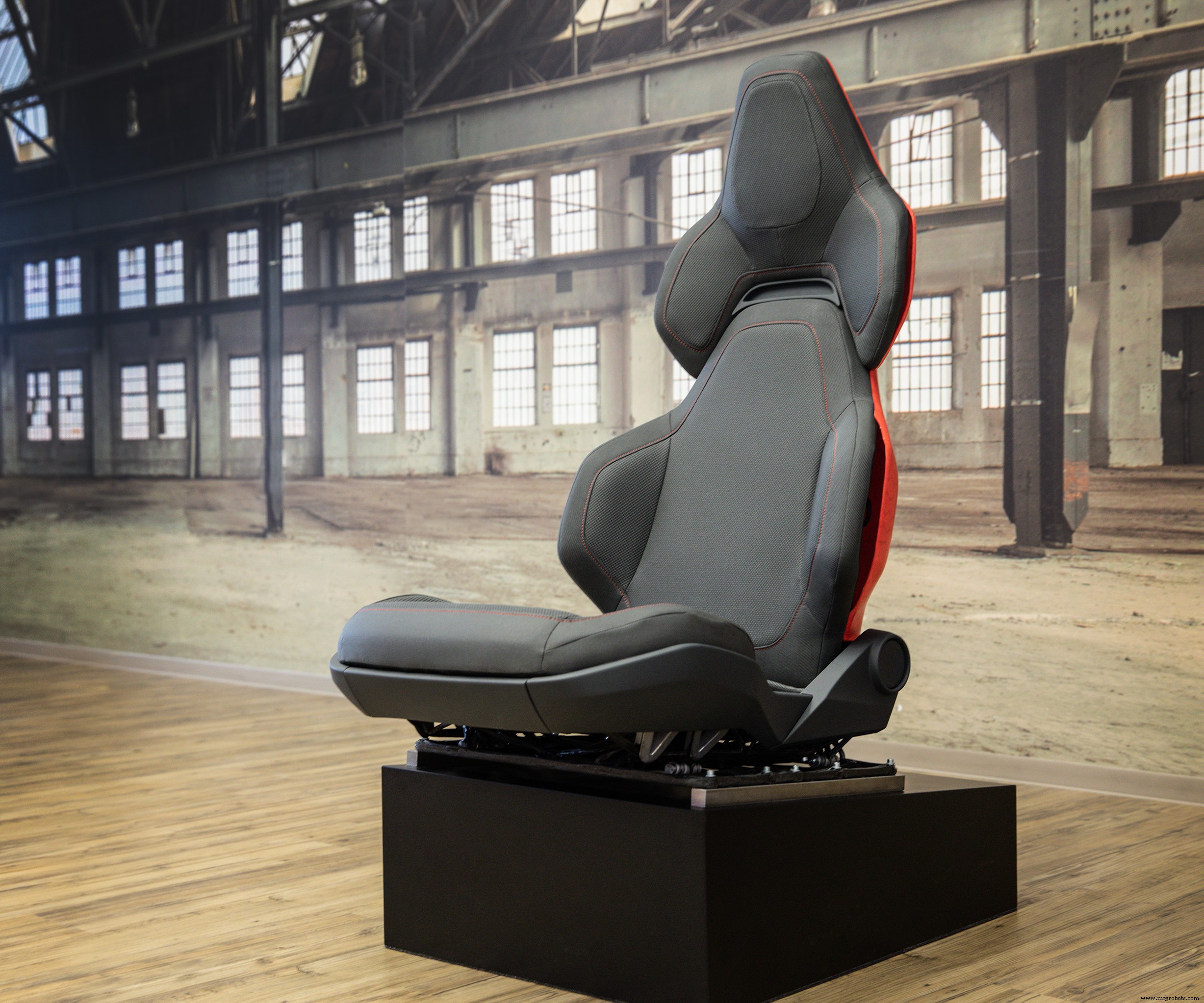
Asiento ultraligero. El concepto de asientos Ultra Leichtbausitz (ULBS) se desarrolló a través de una colaboración entre varias empresas que utilizan una combinación de tecnologías. Fuente | csi entwicklungstechnik
Recientemente, un proyecto innovador con potencial para el sector automotriz, así como para mercados emergentes como hipercoches y taxis aéreos, demostró cómo los nuevos materiales, procesos y tecnologías, y la estrecha colaboración entre empresas, podrían permitir modos de transporte de próxima generación. El objetivo del proyecto era repensar por completo un asiento para automóvil utilizando tecnologías generativas de vanguardia, y para hacerlo utilizando solo la cantidad de material adecuado que se necesita en el lugar correcto: y para producir resultados rápidamente. El prototipo de asiento de vehículo híbrido compuesto de metal ultraligero resultante se desarrolló, desde el diseño hasta la fabricación, en solo siete meses, a través de un enfoque de diseño basado en simulación, métodos ágiles de gestión de proyectos y una estrecha cooperación e integración de sistemas entre las empresas involucradas.
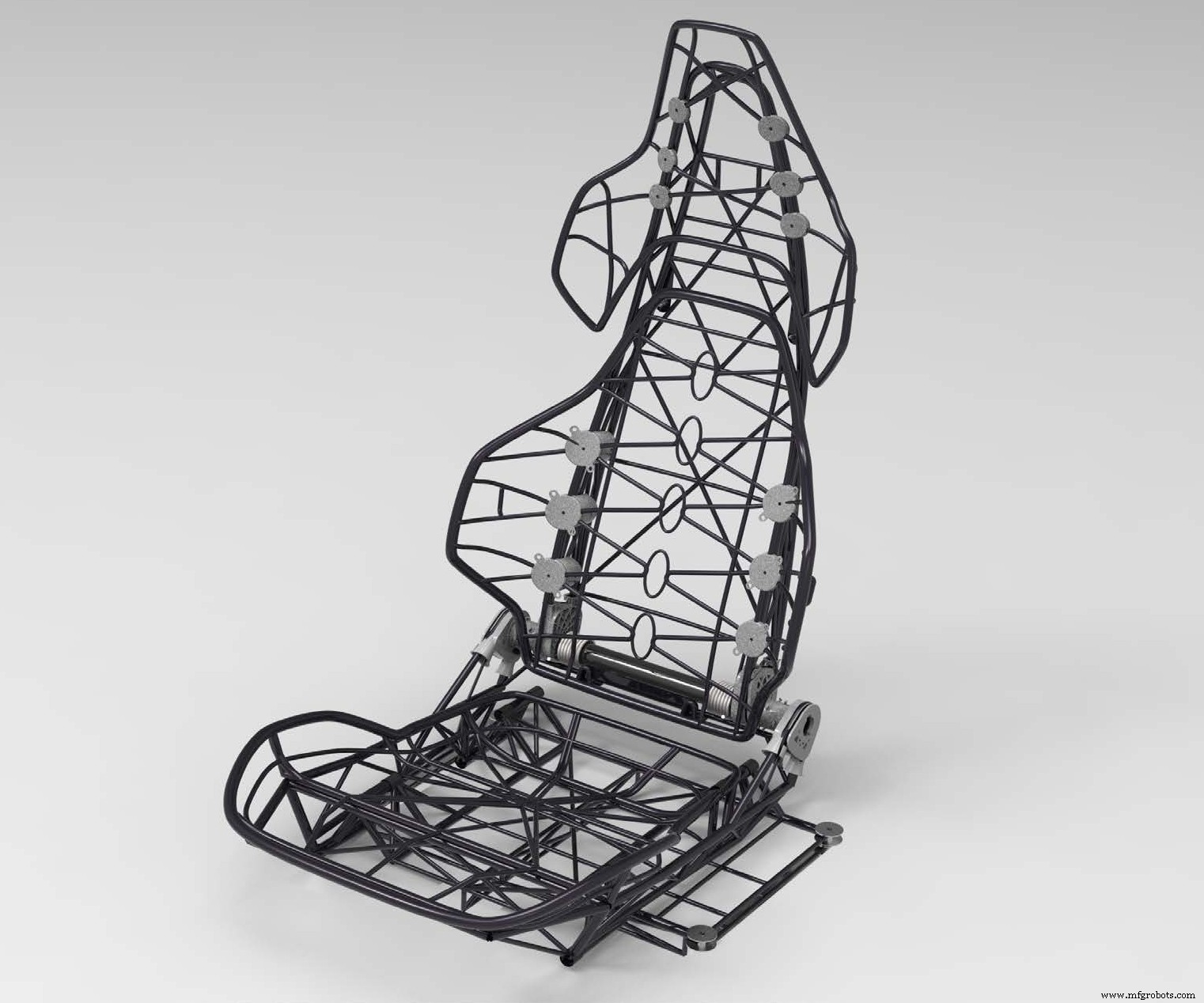
Construyendo un mejor asiento
El estudio de viabilidad del asiento ultraligero Ultraleichtbausitz (ULBS) se desarrolló a través de una colaboración entre varias empresas que utilizan una combinación de tecnologías. La visión del proyecto era, en palabras del grupo, "crear un concepto de asiento ultraligero, sobresaliente en el mercado en términos de optimización de peso". Las empresas iniciadoras csi entwicklungstechnik GmbH (csi, Neckarsulm, Alemania), Alba Tooling &Engineering (Forstau, Austria) y Automotive Management Consulting (AMC, Penzberg, Alemania) desarrollaron el concepto de asiento prototipo en colaboración con Covestro (Leverkusen, Alemania), LBK Fertigung (Friedberg, Alemania), Robert Hofmann (Lichtenfels, Alemania) y 3D | CORE (Herford, Alemania).
El proyecto colaborativo dio como resultado un prototipo de asiento con un peso de poco más de 10 kilogramos, que incluye el cojín, el marco estructural, los insertos funcionales y la consola del asiento que permite montarlo en un vehículo. El asiento es un 20% más liviano que los asientos livianos comparables del mercado, muchos de los cuales son asientos del mercado de accesorios. Según el líder del proyecto ULBS, Stefan Herrmann, responsable del diseño ligero en CSI, actualmente no hay asientos competidores en el mercado que pesen menos de 12 kilogramos.
“Sin embargo, una comparación directa a menudo no es de manzana con manzana, porque los asientos del mercado de accesorios a menudo no incluyen la consola del asiento en la definición de peso”, dice Herrmann, “Además, la comodidad del asiento del ULBS es mucho mayor en comparación con los asientos con peso similar. Los asientos existentes son a menudo asientos de cubo, que pesan incluso menos pero no son tan cómodos, o asientos superdeportivos tradicionales, que pesan mucho más ”.
El ULBS presenta varias tecnologías innovadoras, de las cuales la estructura de esqueleto de fibra itinerante basada en la tecnología de proceso xFK en 3D juega el papel más destacado. (Consulte "Devanado de filamentos, reinventado" para obtener más información sobre xFK en 3D y otras tecnologías de devanado de filamentos). La importancia fundamental de la tecnología galardonada para la deposición de mechas de fibra sin fin radica en su libertad de diseño, en la simulación impulsada por la simulación y el material. Colocación optimizada de la fibra exactamente en la dirección de la carga, así como en la aplicación simple, rentable y sin desperdicio de material de fibra. Para la transferencia de carga en esta estructura de marco se han utilizado piezas impresas en 3D. En las zonas de mayor carga, como los accesorios del respaldo, el asiento utiliza estructuras impresas en 3D de acero inoxidable de alta resistencia y alto módulo. En áreas con menor carga, se utiliza la impresión 3D de aluminio.
csi entwicklungstechnik, una empresa de ingeniería especializada en estructuras de carrocería en blanco (BIW), así como en interiores y exteriores de automóviles con áreas comerciales que incluyen polímeros reforzados con fibra de carbono (CFRP) y fabricación aditiva, supervisó y coordinó el proyecto basado en la idea iniciada por AMC. csi proporcionó el estilo, la superficie, el concepto, la simulación, la ingeniería de diseño y la gestión del proyecto.
Herrmann explica:“csi fue responsable de los paquetes de trabajo en el dominio de la cadena de procesos digitales:estilo, diseño de ingeniería, diseño de superficies, simulación CAE, simulación de topología, simulación de validación y confirmación virtual del proyecto”.
Él enfatiza que lo que hace que el proyecto ULBS sea digno de mención es no solo el uso de materiales y métodos de fabricación innovadores, sino el desarrollo de una pieza compleja que comprende nuevos diseños de componentes en un breve período de tiempo de siete meses utilizando una estrecha colaboración entre los socios.
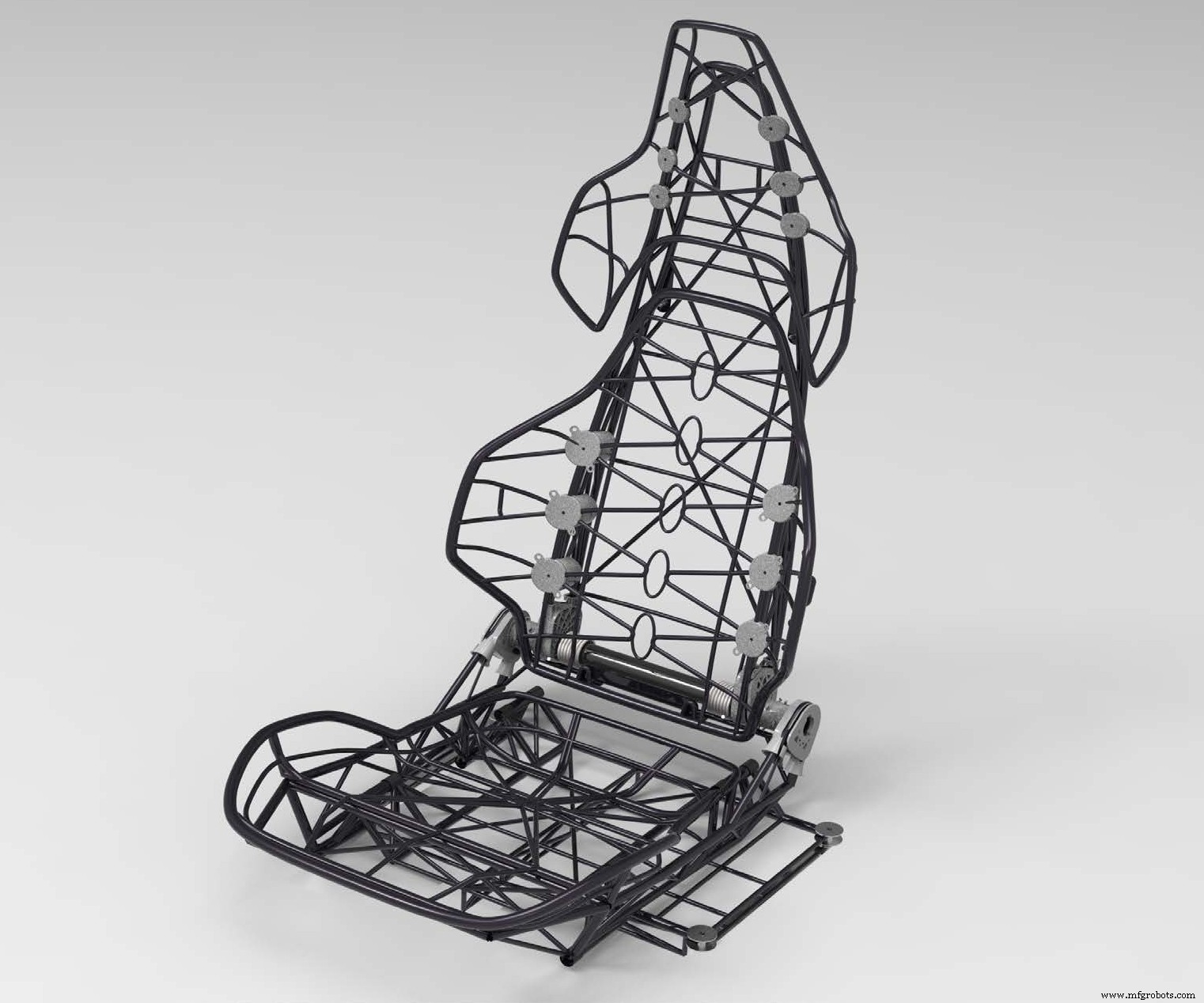
Armazón de asiento enrollado con filamento. Gran parte de la reducción de peso en el proyecto ULBS se debe a la tecnología de proceso de bobinado de fibra de AMC xFK en 3D. Fuente | csi entwicklungstechnik
Dar cuerda a un fotograma
Gran parte de la reducción de peso en el proyecto ULBS se debe a la tecnología xFK en 3D de AMC, una tecnología compuesta de fibra altamente flexible, configurable, rentable y sostenible para componentes de bobinado.
xFK en 3D ya se ha utilizado para una variedad de productos y aplicaciones para diversas industrias y segmentos de mercado. SGL Group Wiesbaden, Alemania) mostró varias piezas de automóviles y bicicletas fabricadas con esta tecnología en la feria internacional de compuestos JEC World 2018. Una de las piezas mostradas, un plato de cadena de bicicleta de fibra de carbono desarrollado por AMC, reduce el peso hasta en un 70%. en comparación con una versión de aluminio.
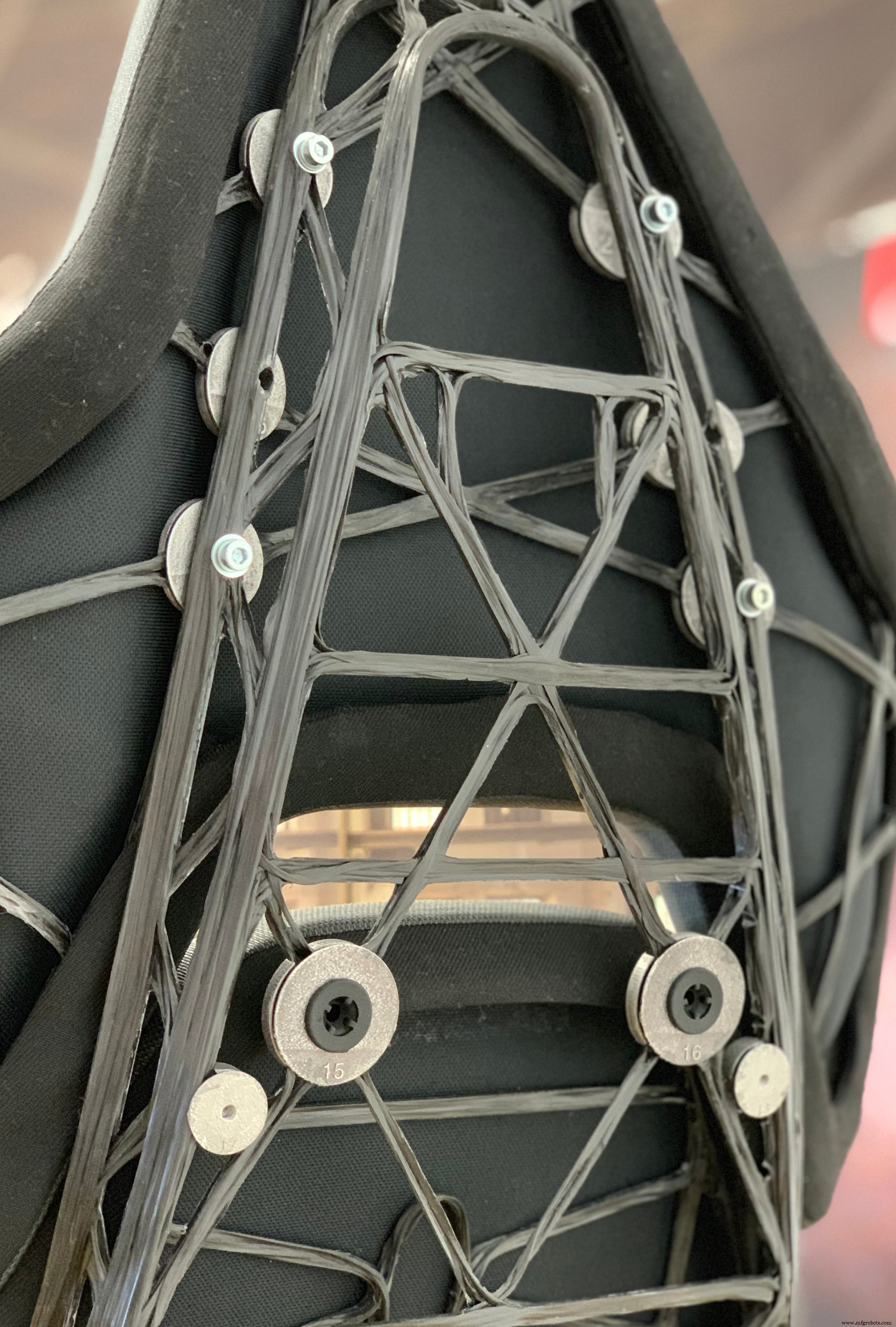
Bujes de bobinado. Una mecha de fibra impregnada de resina termoendurecible se enrolla alrededor de un dispositivo de posicionamiento, lo que permite que las fibras se dispongan para adaptarse a las cargas de cada pieza y las funciones deseadas. Fuente | csi entwicklungstechnik
El proceso xFK en 3D enrolla estructuras portantes sin desperdicio utilizando fibras continuas impregnadas de resina termoendurecible. Una mecha de fibra saturada con resina epoxi se enrolla alrededor de un dispositivo de posicionamiento o bujes de bobinado, lo que permite que las fibras se dispongan específicamente para adaptarse a las cargas de cada pieza y las funciones deseadas.
“Uno de los principales beneficios de xFK en 3D es la eliminación de puntos débiles con respecto a la transferencia de carga y la introducción de carga en estructuras”, dice Herrmann. Explica que los puntos débiles a menudo no se encuentran en el continuo de la estructura, sino en las áreas donde se introducen cargas en la estructura, especialmente donde los componentes vecinos están conectados a la estructura . La tecnología xFK en 3D permite transferencias de carga a través de conexiones y permite que las fibras se alineen de acuerdo con las funciones de los componentes deseados y los casos de carga, y se fabriquen en tres dimensiones.
El proceso de bobinado de filamentos también ofrece beneficios adicionales. El proceso ayuda a minimizar el desperdicio de material:se desperdicia menos del 1% de la mecha de fibra.
csi reconoció las fortalezas de xFK en 3D y diseñó el marco del asiento ULBS para ser construido bajo la asesoría del Dr. Clause Georg Bayreuther, director de tecnología de AMC.
“Trabajando con ingenieros de CSI, consultores de AMC y expertos en herramientas de Alba, se desarrolló este concepto y estructura para la estructura del asiento que se fabricará utilizando el proceso xFK en 3D”, dice Peter Fassbaender, consultor de tecnología e iniciador de xFK en tecnología 3D.
Alba fabricó las herramientas para el armazón del asiento de CFRP y brindó apoyo de ingeniería. Además, aunque el marco del asiento está enrollado con fibra de carbono, las fibras naturales o las fibras de basalto también son buenos candidatos.
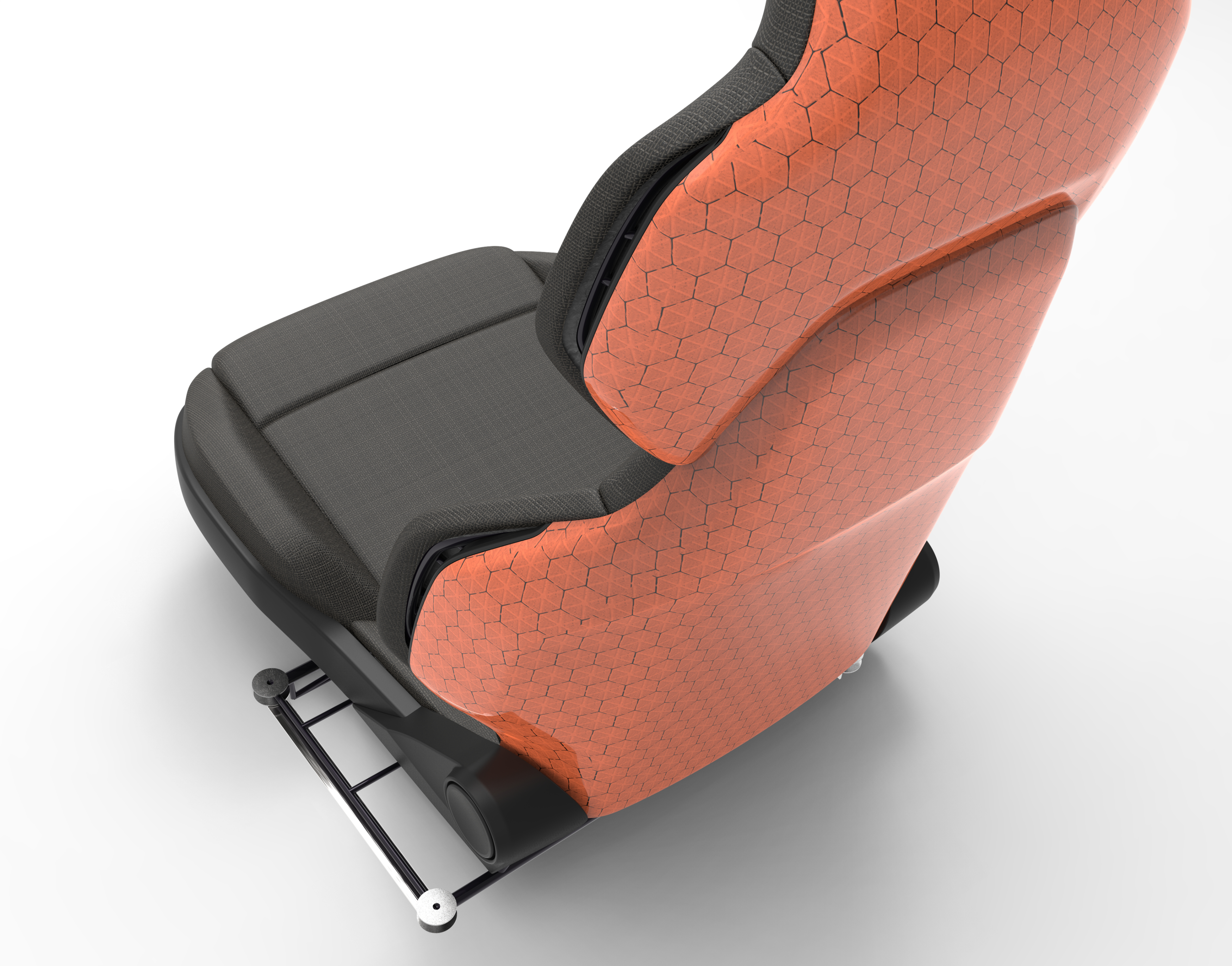
Nuevas tecnologías. El prototipo ULBS utiliza una combinación de nuevas tecnologías que incluyen una carcasa del panel posterior hecha de material de núcleo de refuerzo intralaminar (IRC) y cojines del respaldo del asiento impresos en 3D hechos de poliuretano termoplástico (TPU). Fuente | csi entwicklungstechnik
Una estructura de material híbrida
Además del marco, el prototipo ULBS incluye varias otras innovaciones nuevas. Alba, que suministró las herramientas, también suministró las herramientas, la ingeniería y la fabricación del cuerpo de espuma del asiento y ejecutó el montaje del asiento. Una alfombra de vellón de fibra cubre el marco de CFRP del asiento, que luego se cubre con una cubierta de espuma PUR impresa en 3D. El área del cojín del asiento está hecha de espuma tradicional.
Se logró una mayor reducción de peso mediante el uso de 3D | CORE, un material de núcleo de refuerzo intralaminar (IRC), en la estructura de la carcasa del panel trasero del respaldo del asiento. El material es un núcleo de refuerzo intralaminar (IRC), un núcleo sándwich estructural que comprende cuerpos de núcleo de espuma de poliestireno extruido (XPS) y tereftalato de polietileno (PET) en un patrón de panal integrado. Durante la producción de piezas compuestas, la estructura alveolar se rellena con resina, lo que da como resultado una alta resistencia intralaminar. El 3D | Core se ensambla entre dos capas de fibra de vidrio para crear una preforma, que se infunde con resina epoxi termoplástica mediante moldeo por transferencia de resina asistida al vacío (VA-RTM).
Covestro suministró su adhesivo Dispercoll como aglutinante para las esteras de vellón de fibra, así como el cojín del respaldo impreso en 3D. Según Herrmann, las propiedades mecánicas de Dispercoll proporcionan una buena resistencia a la abrasión, lo cual es importante porque el contacto de la superficie entre el cojín y el marco puede hacer que el vellón se desgaste con el tiempo.
“Si tienes una mecha de una sola fibra, cuando la pones en un tejido, obtienes micro-movimientos entre las partes duras de CFRP y las esteras de vellón. Los componentes del armazón del asiento pueden rozar el tejido y destruirlo ”, explica Herrmann.
Los asientos tradicionales suelen tener una superficie más grande que soporta el acolchado y no tienen este problema. Sin embargo, con xFK en 3D, hay un área de superficie de contacto más pequeña debido a la estructura del marco.
“Cuando xFK en estructuras 3D empuja contra la tela de vellón, debe tener un aglutinante específico y duradero; esto es lo que proporciona Dispercoll en este contexto ”, añade Herrmann.
Covestro también suministró lo que se dice que es el primer cojín impreso en 3D del mundo. Mientras que la espuma convencional y de uso intensivo de herramientas se usa típicamente en los respaldos de los asientos, el uso de los cojines del respaldo del asiento impresos en 3D, que están hechos de TPU (poliuretano termoplástico), aumenta aún más la flexibilidad y adaptabilidad del asiento ULBS con respecto a su estética, opciones de integración funcional y comodidad.
Un asiento para el futuro
El proyecto ULBS logra varios objetivos. El concepto resultante, aunque aún no está en el mercado, tiene el potencial de servir a numerosos nichos de mercado como hipercoches, taxis aéreos, vehículos ultraligeros, micromovilidad, helicópteros, multicópteros y aviación. Si bien es cierto que es más caro que los asientos de automóvil de producción, el ULBS demuestra varias tecnologías que minimizan el desperdicio y, por lo tanto, reducen los costos de materiales. En comparación con otras tecnologías de fibra de carbono, xFK en 3D produce una cantidad muy baja de residuos. De hecho, todo el proyecto tiene como objetivo utilizar recursos mínimos y solo el mínimo necesario de material. El ULBS también ofrece la posibilidad de utilizar recursos renovables y sostenibles como fibras naturales en la estructura del marco, cojines y textiles.
Pero lo que es más importante, el proyecto demuestra cómo las empresas pueden minimizar el tiempo de comercialización al trabajar juntas mediante procedimientos de coordinación cortos y ágiles. También es un buen ejemplo del uso del pensamiento de diseño para llevar con éxito un producto de la idea al prototipo de hardware, centrándose en los requisitos funcionales y mirando hacia el futuro a las aplicaciones futuras y los objetivos de sostenibilidad.
fibra
- Configuraciones de bobinado
- Asiento de bicicleta
- Monociclo
- Asiento de seguridad para niños
- El chip de banda ultra ancha permite el acceso de vehículos desde un teléfono inteligente
- La plataforma de computación Edge permite un acceso profundo a los datos automotrices
- Características de rendimiento del hilo de fibra de vidrio
- Cubierta de fibra de carbono para asiento de inodoro
- El diseño de la compuerta trasera pone a prueba el devanado de filamento modificado
- Las nuevas tecnologías y los mercados en Mundial de bobinado de filamentos caso
- Devanadora de filamento Roth para facilitar los principales recortes de peso / costo de Ariane 6