Proceso ULCORED
Proceso ULCORED
ULCORED es un proceso de reducción directa (DR), que produce DRI (hierro reducido directo) en un horno de cuba, ya sea a partir de gas natural (GN) o de gas reductor obtenido por gasificación del carbón. El gas de escape del eje se recicla en el proceso después de que se ha capturado el dióxido de carbono (CO2), que sale de la planta DR en una corriente concentrada y se almacena. El paso DRI produce un producto sólido que luego se funde usando un horno de arco eléctrico (EAF). El proceso fue diseñado principalmente en 2006 por un equipo liderado por LKAB, Voest-alpine y MEFOS.
El objetivo del proceso ULCORED fue reducir el consumo de GN necesario para producir DRI. Se logró reemplazando la tecnología de reformado tradicional con oxidación parcial (POx) de GN. Combinado con el dispositivo CCS, ULCORED puede reducir las emisiones de CO2 en un 70 % en comparación con el promedio en la ruta BF.
El concepto del proceso ULCORED consiste en separar el CO2 del gas de proceso. Se caracteriza por un esfuerzo por adoptar el proceso DR basado en gas para minimizar la emisión de gases de efecto invernadero (GEI), utilizando tecnología de captura y almacenamiento de CO2 (CCS) y al mismo tiempo para minimizar el uso de energía. El proceso está diseñado de manera que permite la extracción y el almacenamiento de CO2. Por lo tanto, el proceso también depende de CCS con una captura en proceso similar.
El proceso se basa en la utilización de un cambiador para convertir el gas de monóxido de carbono (CO) del eje en hidrógeno (H2) junto con una unidad de eliminación de CO2. Esto abre una nueva evolución innovadora del concepto de proceso.
Las principales características del proceso ULCORED DR incluyen (i) el uso de oxígeno (O2) en lugar de aire, lo que da como resultado un gas de escape de casi el 100 % de CO2 que solo se requiere comprimir, (ii) hay posibilidades de reducir el requisito de GN entre un 15 % y un 20 %, y (iii) el carbón, la biomasa, la gasificación de biorresiduos y el H2 se pueden utilizar como alternativa al GN.
El concepto de ULCORED es satisfacer la demanda de reducción de emisiones de CO2 utilizando reducción directa a base de mineral de hierro y gas para la producción de DRI. El concepto incluye el uso de oxígeno (O2) al 100 %, POx en lugar de reformadores, shifter para la producción de gas en exceso/reducción libre de CO2 y el agente reductor es gas natural o gas de síntesis de la gasificación de carbón/biomasa. El gas reductor producido por la gasificación del carbón también se puede utilizar en lugar del GN.
Proceso ULCORED DR basado en NG
Las principales características del proceso ULCORED DR basado en GN son (i) sin reformador, (ii) sin calentador y (iii) alta presión. Debido a la alta presión, hay menos velocidad de gas en el eje DR, menos fluidización y menos finos que salen del eje DR. Además, debido a la alta presión, se necesitan unidades de eliminación de CO2 y POx más pequeñas y se necesita menos energía para el compresor de reciclaje.
La originalidad del concepto es el uso de O2 en lugar de aire, lo que significa que no hay nitrógeno (N2) en el gas o es bajo. El reformado se realiza mediante una unidad de POx para el acondicionamiento del gas de reducción (Fig. 1). La tecnología reemplaza el reformado convencional de GN por oxidación parcial del gas para reducir el consumo de GN necesario para producir DRI. La reacción de POx que tiene lugar es CH4 + 0,5O2 =CO + 2H2 con delta H =– 8,6 Kcal/mol.
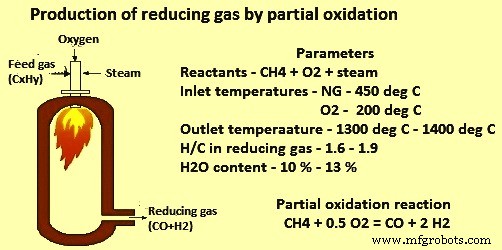
Fig. 1 Reducción de la producción de gas por oxidación parcial
La unidad piloto para la desoxidación parcial se probó en Linde en dos campañas con un quemador de nuevo diseño para gas de alimentación rico en H2. Se utilizó un reactor tubular con gas precalentado (60 % H2 y 40 % CH4). Las conclusiones de las pruebas de la unidad piloto fueron (i) el quemador y el reactor pudieron funcionar sin problemas, (ii) se pudo obtener una llama estable sin una producción significativa de ruido, (iii) se espera que la producción de hollín sea inferior a 300 mg /N cum a 460 mg/N cum volumen de gas húmedo, y (iv) debido a la presión atmosférica, el contenido de CO2 y CH4 fue más alto que los cálculos previos sobre la base del equilibrio asumido. Una presión de funcionamiento superior a 7 kg/cm2 puede reducir este contenido.
El eje DR tiene un flujo a contracorriente de gas reductor inyectado en las toberas y el mineral de hierro se alimenta frío desde la parte superior. El horno funciona a una presión de 6 kg/cm2 y una temperatura de alrededor de 900 grados C. Es probable que el gas de escape contenga principalmente CO, CO2, H2 y H2O.
El gas de escape del eje, que contiene principalmente CO, CO2 y H2O, se conduce a través de un cambiador (de una o dos etapas) que convierte el CO en H2. El uso de un cambiador de gas de agua da como resultado un alto contenido de H2 en el eje de reducción. La reacción del cambiador de agua y gas es CO (g) + H2O (g) <–> CO2 +H2. Casi todo el CO del gas de escape del pozo se convierte en H2 y el CO2 se elimina en la unidad de eliminación de CO2. El aumento de la producción de exceso de gas aumenta la demanda de energía para la unidad de eliminación de CO2 y la producción de O2. El cálculo del nivel correcto de exceso de gas es un proceso iterativo. Los niveles estimados de exceso de gas serán más altos debido a esta razón. Se espera que el nivel de exceso estimado de 2,2 giga calorías por tonelada de DRI compense la demanda de energía adicional. Esto se puede lograr a través de un desvío de algo de gas directamente a la palanca de cambios. La cantidad de gas desviado se determina en función de las propiedades del gas de reducción en el eje de reducción. Debido al aumento de los volúmenes de gas en el sistema, la palanca de cambios y las unidades de eliminación de CO2 necesitan una inversión adicional.
En la unidad de desplazamiento, la reacción de cambio de CO es exotérmica, y el equilibrio favorece la conversión de CO a una alta proporción de vapor a gas y bajas temperaturas, sin verse afectado por la presión. En un sistema adiabático, el deslizamiento de CO alcanzable está determinado por la temperatura de salida. La conversión en un solo lecho de catalizador está limitada por el equilibrio y, a medida que avanza la reacción, la temperatura alta finalmente restringe la reacción adicional. Esta limitación se puede superar con un sistema de dos etapas que consta de un cambio de temperatura alta seguido de un cambio de temperatura baja, con enfriamiento entre lechos. Una temperatura de operación baja brinda el equilibrio termodinámico más favorable y, por lo tanto, el deslizamiento mínimo de CO. La mayoría de las plantas de H2 modernas tienen sistemas de enfriamiento aguas arriba del reactor de cambio de temperatura baja para permitir la operación cerca del punto de rocío del gas de proceso. Se debe utilizar un margen de seguridad por encima del punto de rocío para garantizar la evaporación completa de las gotas de agua que se pueden formar en el enfriador.
Dependiendo de la relación de vapor, el reactor de cambio de baja temperatura puede operar a una temperatura tan baja como 190 °C sin preocuparse por la condensación. En el concepto, el gas superior pasa por un cambiador de alta y baja temperatura con recuperación de calor en el medio. El cambiador de alta temperatura convierte el 97,2 % del CO y el cambiador de baja temperatura completa una conversión del 99,5 %. El intercambiador de calor calienta el gas reciclado y su capacidad se calcula en base a una diferencia de temperatura establecida en el lado caliente de 50 °C. Un exceso de calor en el intercambiador de calor produce vapor a la red de vapor a través de un condensador/rehervidor.
La unidad de eliminación de CO2 se utiliza para eliminar el CO2 del gas produciendo un gas de reducción rico en H2 que se devuelve al proceso. La unidad de remoción de CO2 se decide por una distribución para la eficiencia de remoción de CO2, recuperación de H2 y N2. Los dos procesos de eliminación de CO2 que se pueden utilizar son el proceso de adsorción por cambio de presión al vacío (VPSA) o el proceso de depuración de aminas. La elección de la unidad de eliminación de CO2 (VPSA o amina) depende de los requisitos locales. Si hay excedente de vapor, la extracción de CO2 que requiere energía se puede realizar con energía de vapor en la planta en lugar de la electricidad necesaria para el VPSA. Ambas tecnologías tienen ventajas y desventajas que deben analizarse más a fondo. Ambas tecnologías trabajan con el concepto ULCORED. También existe la posibilidad de utilizar una adsorción por oscilación de presión (PSA) para la eliminación de CO2 en lugar de la unidad VPSA debido a la alta presión disponible en el proceso.
El tipo de proceso seleccionado afecta el diagrama de flujo del proceso y el diseño. El proceso VPSA requiere, incluyendo criogenia y compresión a 110 kg/cm2 de presión, 260 kWh de potencia por tonelada de CO2 capturada. En el caso del proceso de depuración de aminas, con aminas de alto rendimiento (metildietanolamina activada, aMDEA), el proceso completo (aminas y compresión a 110 kg/cm2 de presión) requiere alrededor de 1,6 toneladas de vapor a baja presión y 160 kWh de potencia por tonelada de CO2 capturado.
La parte del gas rico en H2 limpio que contiene N2 se purga del proceso para contrarrestar la acumulación de N2 en el gas de reducción. El gas de purga es un gas valioso que se puede utilizar para la producción de vapor o calefacción dentro del sistema.
El diagrama de flujo del proceso ULCORED basado en gas natural se muestra en la Fig. 1.
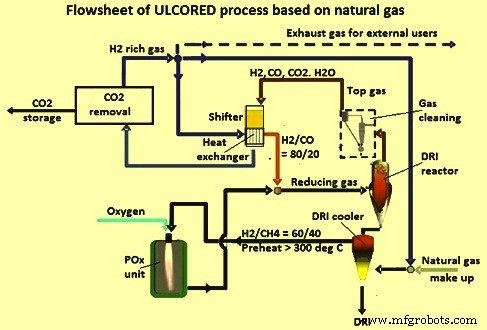
Fig. 2 Diagrama de flujo del proceso ULCORED basado en gas natural
Proceso ULCORED DR basado en la gasificación del carbón
La opción de mayor ahorro de CO2 con ULCORED es el uso de un gasificador de carbón que produce gas de síntesis para la planta DR y gas H2 pobre en CO2 para todos los usuarios de la planta. Este concepto se puede adaptar tanto para sistemas existentes como para sistemas actualizados.
El concepto basado en el carbón se basa en la producción de gas reductor utilizando la tecnología de gasificación de carbón existente y la desulfuración en frío (basada en la tecnología existente) o la desulfuración de gas caliente. El concepto utiliza O2 en lugar de aire e incluye almacenamiento de CO2. El alto contenido de H2 en el eje de reducción se logra a través del cambiador de gas de agua. El exceso de gas H2 se suministra a los demás usuarios de la planta.
La gasificación del carbón es una técnica bien conocida y se espera que sea una de las futuras técnicas de proceso de conversión de energía después del agotamiento de las reservas de petróleo y gas. Hay varias tecnologías desarrolladas para la gasificación del carbón. Existen diferencias entre las tecnologías, pero generalmente funcionan con una eficiencia de conversión de C relativamente alta, generalmente superior al 80 %. Una gran ventaja de la gasificación del carbón es la posibilidad de limpiar eficazmente el gas de síntesis (como el azufre, el mercurio, etc.) antes de su uso.
Dado que el horno de cuba para la producción de DRI opera a una presión de 6 kg/cm2, la presión del gas del gasificador se reduce a través de una turbina de expansión que también recupera energía (de 30 kg/cm2 a 6 kg/cm2).
El proceso ULCORED DR puede integrarse fácilmente con una unidad de gasificación de carbón, incorporando las ventajas de la originalidad del concepto del proceso. El carbón se suministra a la planta de gasificación de carbón. El azufre se elimina del gas de síntesis mediante desulfuración en caliente o en frío. El gas de síntesis limpio se mezcla con gas reciclado rico en H2 limpio, precalentado en el enfriador DRI o del intercambiador de calor entre el cambiador de temperatura alta y baja.
Hay tres formas diferentes de integrar el gasificador con el proceso ULCORED DR. El gasificador se puede integrar como gas de síntesis frío o de forma que se utilice la energía térmica del gas caliente del gasificador. En la Fig. 3 se muestran tres configuraciones diferentes. La posibilidad de producir un exceso de H2 para el sistema se habilita mediante el desvío de gas de síntesis limpio directamente a las unidades de cambio.
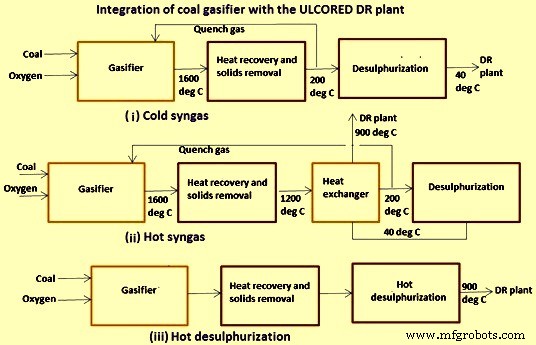
Fig. 3 Integración del gasificador de carbón con la planta ULCORED DR
El oxígeno se consume principalmente en el gasificador de carbón, pero también antes del eje, en un pequeño POX, lo que garantiza una temperatura correcta del gas de reducción. El gas desviado es el gas que se debe desviar al cambiador para garantizar la composición correcta del gas de reducción, es decir, aumentar la cantidad de H2. El CO2 eliminado es la cantidad de CO2 que se separa del flujo principal del proceso en el proceso de eliminación de CO2. El diagrama de flujo del proceso ULCORED a base de carbón se muestra en la Fig. 4.
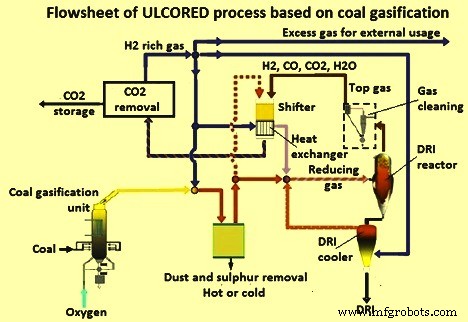
Fig. 4 Diagrama de flujo del proceso ULCORED basado en la gasificación del carbón
El uso de un gasificador de carbón y un cambiador en el sistema hace posible desviar parte del gas de síntesis directamente al cambiador, generando más gas del necesario para la planta de reducción directa. Esta característica hace posible generar un combustible pobre en CO2 para la planta siderúrgica. Permite tener una fuente de CO2 fuera del sistema, lo que permite capturar y almacenar básicamente todo el CO2 generado en el sistema de fabricación de acero.
Estado actual del proceso ULCORED DR
Se han completado estudios profundos del modelo fundamental para el proceso ULCORED DR. Estos estudios de modelos incluyeron modelos a escala de gránulos, modelos de ejes y modelos de procesos mediante simulaciones de diagramas de flujo. Los estudios de modelos han ayudado en la comprensión fundamental del proceso de DR, incluida su dinámica. El modelado del diagrama de flujo ha ayudado en la optimización del diseño del proceso para adaptarse al proceso ULCORED DR en el entorno de la planta siderúrgica. Diferentes enfoques adoptados durante los estudios de modelado han producido resultados similares. Estos estudios han creado una base creíble para la evaluación del concepto en diferentes escenarios. Se han realizado cálculos de balance de materiales, balance de masa, balance de energía y emisiones de CO2 para una tonelada de salida de DRI en frío con 92 % de metalización y 2,76 % de C.
Una de las opciones interesantes es una planta ULCORED DR es la producción de LRI (menor reducción de hierro) y un alto horno (BF) convencional o libre de N2 para producir el metal caliente (HM) con un ahorro adicional de emisiones de CO2. LRI es una opción alternativa en lugar de DRI considerando las pruebas exitosas realizadas en el BF experimental LKAB. La prueba LRI con un producto DR reducido a solo un 65 % de grado de metalización respondió muy positivamente en el BF con una condición de horno notablemente estable y un bajo consumo de coque que estaba por debajo de 200 kg/tHM.
El resultado de estos estudios es que el proceso DR de ULCORED puede ser una "solución rápida" para una mejora de las emisiones de CO2, especialmente donde el gas natural es relativamente barato. En el caso de una planta siderúrgica integrada con ruta BF, LRI puede ser una opción considerando las pruebas exitosas realizadas en el BF experimental LKAB.
El proceso ULCORED DR debe someterse a una prueba piloto primero, un paso que podría aprovechar la oportunidad del horno EDRP (piloto experimental de reducción directa), que LKAB planea construir en los próximos años como complemento de su BF experimental en Lulea, Suecia. Las especificaciones del EDRP son (i) producción de 1 tonelada de hierro por hora, (ii) recirculación de gas superior, (iii) rango de presión de trabajo de 0 kg/cm2 a 8 kg/cm2 en el horno de cuba, (iv) ) flujo de gas en el rango de 1700 N cum a 3100 N cum por hora, y (v) temperatura del horno de cuba en el rango de 900 °C a 1050 °C.
ULCORED probablemente será un candidato para modernizar las plantas de reducción directa existentes, una vez que se haya demostrado su viabilidad a escala piloto y luego de demostración, lo que también tomaría de 10 a 15 años o más.
Proceso de manufactura
- Linterna de gas
- Gas natural
- Bomba de gasolina
- Helio
- Máscara antigás
- Detección de fugas de gas peligroso
- Fabricación de acero verde
- Proceso HIsmelt de fabricación de hierro
- ¿Qué es la soldadura por gas? - Partes, proceso y aplicación
- Comprender el proceso de soldadura por gas
- Entender el proceso de extrusión