Maneras de usar socavaduras con éxito en el diseño de moldeo por inyección
El moldeo por inyección socavado es un proceso que se utiliza para crear piezas con formas y características complejas que impiden que la pieza se extraiga del molde sin dañarla. Las características de socavado en el moldeo por inyección generalmente aumentan la complejidad general de cualquier diseño y los costos asociados. Por estos motivos, es mejor evitarlos siempre que sea posible.
En este artículo, exploraremos en detalle cuándo se producirán muescas en el moldeo por inyección y varios métodos utilizados para crear muescas.
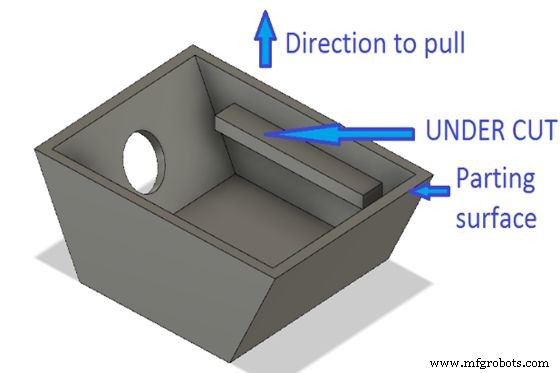
¿Qué situaciones hacen necesario el moldeo por inyección de muescas?
Hay muchos escenarios en los que se hace necesario el moldeo por inyección socavado, pero estos son algunos de los más comunes.
1. Inserciones personalizadas
Usando el proceso de moldeo por inyección de socavado, puede crear insertos personalizados que se ajustan a piezas más grandes. Los maquinistas a menudo usan este tipo de inserto en dispositivos médicos o productos que necesitan un ajuste exacto. También puede usar insertos socavados como alternativa a los tornillos o remaches al unir dos piezas.
2. Orificios laterales
El moldeo por inyección recortado puede crear orificios laterales que son difíciles de producir con métodos tradicionales. Los maquinistas a menudo usan orificios laterales para montar componentes o unirlos a otras piezas del equipo. También puede usarlos con fines estéticos, como agregar un elemento de diseño o ventilar el calor dentro del producto.
3. Hilos verticales
Las roscas verticales son otro uso común para el moldeo por inyección de socavado. Estas roscas se encuentran comúnmente en pernos y tornillos, pero también puede usarlas como parte de un ensamblaje en el que varias partes deben enroscarse juntas para funcionar correctamente juntas como una sola unidad.
4. Accesorios de púas
En el caso de los accesorios con lengüeta, las partes macho deben socavarse para formar un labio, sujetando la parte de acoplamiento hembra del accesorio con lengüeta.
5. Funciones entrelazadas
Si está diseñando una función de enclavamiento, como una lengüeta y una ranura, debe socavar un lado de la lengüeta para poder acoplar el lado con la ranura en otro.
Retos a los que se enfrentan las socavaduras en el moldeo por inyección
Los principales desafíos de la muesca del moldeo por inyección resultan del diseño, la elección de los materiales y los requisitos estéticos de la pieza mecanizada.
1. Falta de calado
Cuanto más complicado sea el arreglo, más problemas encontrará con el diseño socavado. Todo comienza allí. Sería mejor controlar los ángulos de inclinación, los ángulos de la cavidad y otros ángulos complejos para obtener el mejor rendimiento. Para reducir la posibilidad de dificultades en el proceso de eyección, debe realizar el recubrimiento en la carga manual de la sustancia adecuada.
2. Dificultad para sacar materiales del molde
Puede ser difícil incluir características de socavado en algunos materiales. Por ejemplo, algunos materiales, incluidos los plásticos con relleno de vidrio, son más difíciles de quitar del molde. Según la regla general, cuanto más duro sea el material, más dificultades tendrás para extraerlo. Por lo tanto, use la mayor cantidad de tiro posible mientras emplea estos materiales más resistentes. Además, la solución que puede emplear para maximizar su moldura de socavado depende de la flexibilidad y elasticidad general del material.
3. Consideración estética
Las demandas estéticas del proyecto pueden representar otro obstáculo importante. Por ejemplo, la opción de diseño de socavado que puede emplear tendrá ciertas restricciones si trabaja con un componente en el que no desea una línea de partición perceptible en piezas moldeadas por inyección o cualquier otra preocupación estética. En consecuencia, tendrá que hacer frente a dificultades adicionales.
Diferentes formas de utilizar con éxito la muesca en piezas moldeadas
El éxito con socavaduras requiere pequeñas modificaciones del molde y un alto nivel de competencia. Algunos de los diseños que pueden ayudar a minimizar los defectos y el desgaste del molde incluyen los siguientes.
1. Use inserciones cargadas a mano
Los maquinistas emplean plaquitas cargadas a mano cuando es necesario incluir una muesca en el mecanizado para características desafiantes como un labio con un ángulo agudo. También resultan útiles cuando una función adicional, como un orificio mal colocado, hace imposible utilizar una solución estándar, como un desnivel.
Para hacer uso de un inserto cargado a mano, el operador inserta una o más piezas de metal en el molde antes de inyectar el plástico. El número y posición de las piezas depende de cuantos destalonados necesite la pieza mecanizada. Estas piezas de metal crean efectivamente una cavidad, ya que evitan que el plástico fluya hacia los espacios que ocupan.
Una vez que el operador abre el molde después de crear el artículo, debe recuperar físicamente el inserto cargado a mano. La desventaja es que aumenta el costo del moldeo por inyección y el tiempo del ciclo, ya que el operador debe cargar y descargar cada cavidad individualmente.
2. Colocación de líneas de piezas
Mover la línea de separación del molde para superponer una socavadura es a veces la forma más sencilla de tratar las socavaduras. La razón es que cuando la línea de partición divide la característica por la mitad, el operador puede liberar el componente del molde sin necesidad de un socavado. Los maquinistas pueden hacer zigzag en la línea de partición usando este método para alinear con diferentes características, eliminando la necesidad de muescas. Hay, sin embargo, limitaciones a este método. Estos van desde la geometría y las propiedades de flujo del plástico.
3. Insertar resaltes
Los topes son una buena opción cuando se trabaja con telas flexibles y elásticas. El proceso solo difiere del proceso de moldeo por inyección estándar al agregar un solo inserto. El operador retira este inserto primero después de completar el procedimiento. El vacío que deja le da al componente algo de "margen de maniobra". Una vez que se quita el inserto, se puede sacar la pieza del molde. El "margen de maniobra" permite que el maquinista doble ligeramente la pieza mientras la saca del molde, incluso con la presencia de la muesca.
Si bien las compensaciones pueden parecer relativamente sencillas desde el exterior, su uso requiere una consideración cuidadosa de varias cosas. Primero, la pieza debe ser lo suficientemente elástica para no romperse cuando el operador de la máquina la doble. Además, el operador debe asegurarse de que el ángulo de avance oscile entre 30 y 40 grados.
4. Acciones secundarias
En los casos en los que es inevitable tener un socavado, una característica de acción lateral puede ayudar a mantener la pieza funcional. Un núcleo de acción lateral es un inserto que se introduce antes de inyectar el plástico en el molde. Cuando el operario inyecta el material en el molde, no puede llenar el volumen ocupado por este inserto. Luego, el maquinista desliza el inserto hacia afuera después de completar el moldeado.
Sin embargo, a diferencia del caso de los topes en los que el maquinista quita el inserto antes que la pieza, quitan los núcleos de acción lateral después de sacar la pieza. Las acciones laterales también funcionan mejor con materiales rígidos que no se adhieren fácilmente a la superficie del molde. Una desventaja de las acciones secundarias es que cada inserto debe diseñarse específicamente, lo que hace que el procedimiento sea más complejo.
5. Hacer uso de cierres
Los maquinistas usan cierres deslizantes cuando una característica, como un gancho que sobresale del costado de una moldura, no se puede hacer fácilmente con otro método. Inserte un corte deslizante a través del agujero en la pared del componente principal para producir la muesca y el gancho. La otra mitad del molde creará la función de gancho restante.
El problema con los cierres deslizantes es que deben estar muy apretados. Esto se debe a que no puede permitir que el plástico se desarrolle más allá de la forma de la característica si necesita usarlas como dos secciones de acoplamiento de una herramienta. De lo contrario, causará una fricción sustancial cada vez que abra y cierre la herramienta.
Además, debe estirar cada una de esas superficies unos tres grados para evitar daños por moho, lo que daría lugar rápidamente a piezas moldeadas con un acabado inaceptable. Esto es necesario porque el contacto total de metal con metal no ocurrirá hasta que el molde esté completamente cerrado y se forme un sello mecánico entre las dos caras.
Aplicaciones de socavado en moldeo por inyección
El moldeo por inyección con muescas se usa ampliamente en numerosos sectores debido a su capacidad para producir productos con características de muescas. Hemos seleccionado algunas de estas industrias y las explicamos a continuación.
Electrónica de consumo
En esta aplicación, usamos otros métodos para formar elementos como botones y pestañas que son difíciles de lograr. Las socavaduras también se utilizan para crear cavidades para componentes electrónicos en productos electrónicos de consumo, como teléfonos móviles y computadoras portátiles.
Dispositivos médicos
Con otros métodos, como el moldeo por inyección o el mecanizado, puede usar muescas para crear geometrías complejas que no puede fabricar fácilmente. En dispositivos médicos como jeringas y catéteres, las socavaduras crean ranuras a lo largo de su longitud, lo que les permite funcionar correctamente.
WayKen lo ayuda a resolver el problema de socavación de manera efectiva
El proceso de moldeo por inyección de socavado puede ser complicado y requiere mucha experiencia para ejecutarlo correctamente. En WayKen, sin importar el moldeo por inyección de socavado o el socavado en el mecanizado, podemos manejar todos sus requisitos de socavados y brindar los mejores resultados de manera consistente.
WayKen también proporciona herramientas rápidas de alta calidad y servicios de moldeo por inyección de prototipos diseñados para desarrollar su producto de manera rápida y eficiente. Contáctenos para una cotización instantánea y obtenga DFM para ayudarlo a optimizar el diseño de su pieza y minimizar cualquier complejidad.
Conclusión
Existen numerosas razones para utilizar muescas en su proceso de diseño. En primer lugar, identificar la moldeabilidad de sus componentes es vital al diseñar cualquier pieza para moldeo por inyección. Ya sea un diseño de pared recta o una muesca, debe construir la geometría según especificaciones precisas para permitir que el plástico fluya correctamente y produzca una pieza con defectos mínimos.
Preguntas frecuentes
¿Qué son las muescas en el moldeo por inyección?
Una muesca en la moldura es una depresión o protuberancia en una forma que evita que se retire de un molde de una sola pieza. Las muescas en los componentes moldeados evitan que la pieza se descargue directamente de una máquina de moldeo por inyección. Pueden ser muescas internas o externas, con muescas externas en el exterior del componente y muescas interiores en el interior.
¿Qué es el proceso de socavado?
Al extraer el componente del molde, necesita algunos mecanismos para ajustar la parte del molde que toca la socavación para sacar la pieza del molde, ya que la pieza no se puede desmontar directamente sin el dispositivo. Este es el procedimiento Undercut.
¿Qué es una "línea de separación" en el moldeo por inyección?
La línea de separación denota la dirección de la línea del molde del dibujo o el punto en el que el maquinista separa las dos mitades del molde sin dañar la pieza. La línea de separación suele estar en el centro de la pieza. Sin embargo, esto cambia según la forma de la pieza.
Tecnología Industrial
- ¿Qué es el moldeo por inyección de reacción?
- Moldeo por fundición frente a moldeo por inyección
- Termoformado frente a moldeo por inyección de reacción (RIM)
- Moldeo por inyección frente a moldeo por inyección de reacción (RIM)
- Moldeo por fundición frente a moldeo por inyección de reacción
- 6 tipos de compuertas de moldeo por inyección y cuándo usarlas
- Tolerancias de moldeo por inyección:optimícelas de cuatro maneras
- Diseño de puertas de moldeo por inyección:una guía definitiva para la fabricación de plástico
- Ángulo de inclinación para moldeo por inyección:guía de diseño y prácticas recomendadas
- Moldeo por inyección con muescas:uso efectivo de muescas en diseños de moldeo por inyección
- Cuándo usar el proceso de sobremoldeo con moldeo por inyección