¿Qué es el casting? explicación detallada | El puesto mecánico
Reparto es un proceso de fabricación que se lleva a cabo desde la antigüedad. Hasta ahora, la "fundición" es la elección de muchos fabricantes como método para fabricar varias piezas. Hoy comencemos definiendo “casting”
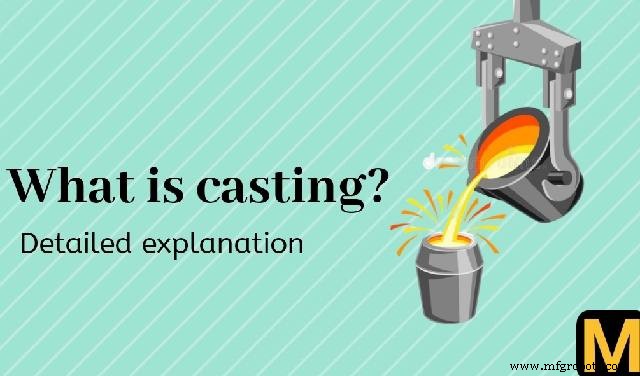
El proceso general de casting es el siguiente:
- El metal se calienta hasta que se licua.
- El metal licuado se vierte en moldes para darle la forma y el tamaño deseados al metal fundido.
- Se permite que el metal fundido se enfríe y solidifique dentro del molde.
- Al solidificarse, el componente se retira del molde, se limpia y se somete a otro proceso de mecanizado si es necesario.
La pieza moldeada o el componente que se retira al solidificarse del molde se denomina Fundición. . La fábrica o taller que fabrica piezas fundidas se denomina “Fundición “.
En la industria existen principalmente dos tipos de fundición:
- Fundición de trabajo
- Fundición cautiva
1. Fundición de trabajo: Este tipo de fundición son centros de fabricación independientes. Las fundiciones de trabajo producen piezas fundidas por contrato/pedido.
2. Fundición cautiva: Estas fundiciones son de propiedad exclusiva. Dado que ser propietario de una fundición no es barato, las fundiciones cautivas suelen ser propiedad de grandes empresas. Es como un departamento del proceso de fabricación de la empresa. La fundición cautiva produce piezas fundidas de acuerdo con las necesidades de la empresa matriz.
Proceso de transmisión:
Diagrama de flujo del proceso de casting.
- Haz el patrón. El material del patrón puede ser:madera, metal o plástico.
- Con la ayuda de patrones, prepare el molde y los núcleos necesarios.
- Sujete el molde correctamente con núcleos colocados correctamente en la cavidad del molde.
- Derrita el metal o la aleación que se va a fundir.
- Vierta el metal fundido/la cavidad en la cavidad del molde.
- Deje que el metal fundido se enfríe y se solidifique. Retire la fundición del molde. Esta operación se llama "Shake out".
- Limpie y termine el yeso.
- Pruebe e inspeccione la fundición.
- Eliminar los defectos si los hubiere y si es posible (Recuperar el yeso).
- Elimine la tensión del yeso mediante tratamiento térmico.
- Vuelva a inspeccionar la fundición.
- El yeso está listo para usar.
Creación de patrones:
El proceso de fundición comienza con la creación de patrones. Los patrones se utilizan para hacer moldes para la fundición en los que se vierte el metal fundido. Los patrones son las réplicas del producto que se pretende moldear. El patrón es un poco más grande en tamaño, ya que incluye todo tipo de concesiones. Algunas de las concesiones son Concesión de contracción: Como los metales tienden a encogerse al solidificarse, el patrón debe hacerse un poco más grande para compensar la contracción. Mecanizado de tolerancia: El mecanizado o acabado de la fundición da como resultado la eliminación de metal, por lo que los diseñadores diseñan el patrón de tal manera que después de todos los procesos de mecanizado, el producto final tenga la forma y el tamaño deseados. Del mismo modo, hay muchas otras asignaciones incluidas en un patrón. ![]() |
Un patrón de madera de una pieza de máquina. |
Los materiales utilizados para la elaboración de patrones son:
- Para la producción a pequeña escala:se utilizan maderas como el pino blanco, la caoba, el arce, el abedul y el cerezo. La madera se utiliza en la producción a pequeña escala o cuando se va a realizar un número menor de piezas fundidas. Los patrones de madera son livianos, económicos en comparación con los patrones de metal, se pueden moldear fácilmente en la forma deseada. Esto hace que los patrones de madera sean una mejor opción. Además de la madera, el patrón de plástico se puede utilizar como alternativa.
- Para producción a gran escala:los metales se utilizan para la creación de patrones cuando se trata de producción a gran escala. Son más duraderos que los de madera y tienen una vida útil más larga, ya que pueden resistir el desgaste. Otras ventajas que hacen que los metales sean una opción adecuada son que los metales no se deforman fácilmente, pueden soportar una manipulación brusca, resistencia al desgaste, es posible un mejor acabado de la superficie, resistencia a la corrosión (excepto los metales ferrosos), etc. Metales como el latón, el aluminio, el metal blanco y el hierro fundido son los preferidos para la fabricación de patrones.
Tipos de patrón:
- Patrón de una pieza
- Patrón dividido o patrón de dos piezas
- Patrón cerrado
- Cope y patrón de arrastre
- Patrón de barrido
- Patrón de esqueleto
Lea también:
- ¿Qué es la máquina de torno?
- Herramientas básicas de taller que debes conocer
- ¿Qué es la soldadura GTAW o TIG?
- Automatización industrial y sus tipos
Moldura :
Ahora que el patrón está hecho, el patrón se usa para hacer molde con él. Cómo ? vamos a ver. De todos los procesos de moldeo, el moldeo en arena es el más utilizado para la fundición. Los moldes de arena son moldes “desechables” o de “uso único”. Después de la colada, el molde de arena se destruye completamente para sacar la pieza fundida del molde. La arena se mezcla con aglutinantes y aditivos junto con agua para aumentar la moldeabilidad de la arena. Para preparar el molde, el material de moldeo está contenido alrededor del modelo. Como se muestra en la figura, la parte superior del molde se llama capa y la parte inferior se llama arrastre. Se permite que el molde se endurezca y el patrón se retira del molde solo para exponer la cavidad así creada para verter metal fundido en él. Los tipos de moldes de arena son:- Moho de arena verde
- Moho de arena seca
- Mohos de arena marga
- moldes de CO2, etc.
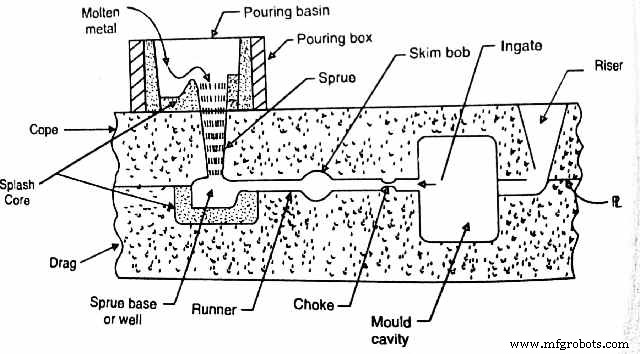
El molde contiene los siguientes elementos para una fundición exitosa:
Núcleo: Por lo general, hecho de arena, madera o metal, el núcleo se usa para hacer agujeros en la fundición. El macho es un cuerpo que se coloca en la cavidad del molde antes de cerrar el molde y verter el metal fundido. El núcleo ayuda así a formar una cavidad dentro de la fundición. Cuenco de vertido: Es el depósito en la parte superior del bebedero (en la tapa) que recibe el vapor de metal fundido vertido desde la cuchara. Bebedero : Un bebedero o compuerta de bajada es un canal vertical que conecta el depósito de vertido con corredores y compuertas. Se hace algo cónico hacia abajo para facilitar el moldeo y, lo que es más importante, para tener un área de sección transversal decreciente correspondiente al aumento de la velocidad del metal fundido a medida que fluye por el orificio del bebedero. Esto evita el flujo turbulento y, por lo tanto, la entrada de aire junto con el líquido en la cavidad del molde. Base o pozo del bebedero: Es el depósito en el extremo inferior del bebedero. Previene la erosión excesiva de arena cuando el metal fundido golpea el corredor en la base de abeto. Además, hay una pérdida considerable de velocidad en el pozo. Corredor: El corredor es generalmente el canal horizontal cuyas funciones son atrapar la escoria y conectar la base del bebedero con las compuertas, permitiendo así que el metal fundido entre en la cavidad del molde. Puertas: Las compuertas son los canales a través de los cuales el metal ingresa directamente a la cavidad del molde. Elevadores: El elevador o cabezales de alimentación son parte del sistema de alimentación. Estos son depósitos del metal fundido que alimentan el metal en la fundición propiamente dicha a medida que se solidifica, para evitar cavidades por contracción en la fundición.Si le gusta esta publicación, háganoslo saber en los comentarios y compártala con amigos y familiares con los enlaces sociales que se indican a continuación.
Tecnología Industrial
- Fundición de espuma perdida frente a moldeado completo:¿cuál es la diferencia?
- Conceptos básicos de la fundición centrífuga:lo que debe saber
- ¿Qué es la soldadura GMAW o MIG? – explicó | El puesto mecánico
- ¿Qué es la extrusión? Explicación detallada | El puesto mecánico
- ¿Qué es la soldadura GTAW o TIG? explicación detallada | La publicación de Mechanical
- ¿Cuáles son los principales tipos de sistemas de transmisión de energía mecánica?
- ¿Qué son las 5S? Una explicación de los elementos de 5S para una cultura Lean
- ¿Qué hay en el proceso de fabricación?
- Mercado de inversión frente a moldeado a presión:¿cuáles son las diferencias?
- Fundición en arena frente a fundición a presión:¿cuáles son las diferencias?
- ¿Qué es la fundición en arena?