Horno de cúpula:piezas, principio de funcionamiento, aplicaciones
En este artículo discutiremos sobre Horno de cúpula, Partes de cúpula, Diagrama de horno de cúpula, Zonas en cúpula, Operación de cúpula.
El objetivo principal en cúpula es producir hierro de la composición, temperatura y propiedades deseadas a la tasa requerida de la manera más económica. Además, este horno tiene muchas ventajas distintivas sobre los otros tipos, por ejemplo, simplicidad de operación , continuidad de la producción y mayor producción junto con un alto grado de eficiencia.
Se utilizan varios tipos de hornos de fusión en diferentes talleres de fundición, según la cantidad de metal que se derrita a la vez y la naturaleza del trabajo que se lleva a cabo en el taller. Solo horno de cúpula utilizado en fundiciones para fundir arrabio refinado junto con chatarra se describe a continuación.
Partes del horno de cúpula
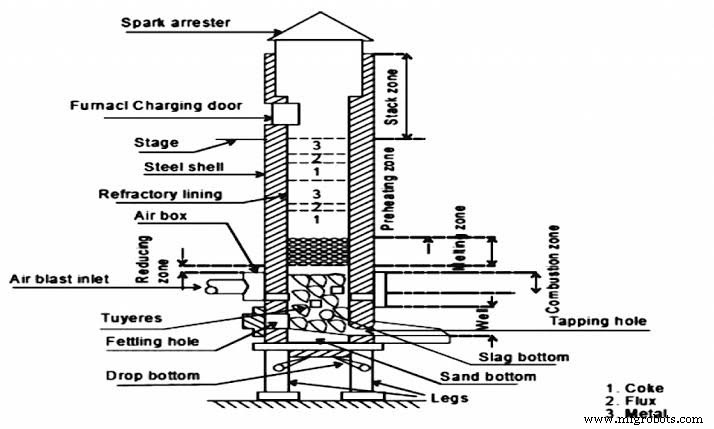
El horno de cúpula consiste en una lámina de acero vertical, cilíndrica, de 6 a 12 mm de espesor, y revestida interiormente con ladrillos refractarios al ácido o al ácido. arcilla de apisonamiento. Los ladrillos refractarios o la arcilla de apisonamiento utilizados consisten en óxido de silicio ácido (SiO2) y alúmina (Al2O3). El revestimiento es generalmente más grueso en la región inferior donde las temperaturas encontradas son más altas que en la región superior.
El caparazón está montado sobre una base de ladrillo o sobre columnas de acero. En una disposición de columna de acero, que se utiliza en la mayoría de las cúpulas modernas, la parte inferior de la carcasa está provista de puertas abatibles a través de las cuales se pueden descargar los desechos, que consisten en coque, escoria, etc. al final de una fusión. En las cúpulas de fondo abatible, el fondo de trabajo se construye con arena de moldeo que cubre las puertas abatibles.
Este fondo se inclina hacia el orificio de colada de metal situado en el punto más bajo en el frente de la cúpula. Opuesto este agujero del grifo , y algo más arriba hay otro agujero, llamado agujero de escoria , que permite sacar la escoria.
Un volumen constante de aire para la combustión se obtiene de un ventilador motorizado. El aire se transporta desde el soplador a través de un tubo llamado tubo de viento (entrada de chorro de aire), primero a una cubierta circular alrededor de la carcasa llamada caja de viento. y luego en el horno a través de una serie de aberturas llamadas toberas que se disponen a una altura de entre 450 a 500 mm por encima del fondo de trabajo o lecho de la cúpula.
Estas toberas son generalmente 4, 6 u 8 en número dependiendo del tamaño de la cúpula y pueden colocarse en una o más filas. El área total de las toberas debe ser de un quinto a un sexto del área de la sección transversal de la cúpula dentro del revestimiento al nivel de la tobera. Por lo general, las toberas tienen un tamaño de 50 × 150 mm o 100 × 300 mm. A veces se proporcionan toberas auxiliares para aumentar la eficiencia de fusión.
Se proporciona una válvula en la tubería de explosión para controlar el suministro de aire. Según el tamaño del cubilote, el tipo de hierro fundido y la compacidad de la carga, la presión del aire puede variar de 250 mm a 400 mm de agua para hornos pequeños y medianos y de 400 mm a 850 mm para hornos pequeños y medianos. horno de gran tamaño.
A veces se instala un medidor de volumen para saber el volumen de aire que pasa. La cantidad de aire necesaria para fundir una tonelada de hierro depende de la calidad del coque y de la relación coque-hierro. La larga práctica demuestra que se necesitan entre 800 y 900 metros cúbicos de aire para fundir una tonelada de hierro en un horno de cubilote, suponiendo que se utilice una proporción de 10 a 1 de hierro a coque. Para una relación más baja, se necesitarán mayores volúmenes de aire.
Se proporciona una puerta de carga a través de la cual se alimenta metal, coque y fundente al horno, y está situada de 3 a 6 m por encima de las toberas, según el tamaño de la cúpula. Una gran plataforma o escenario suele rodear la cúpula a un nivel de unos 300 mm por debajo de la parte inferior de la puerta de carga.
El caparazón generalmente se continúa durante 4,5 a 6 m, por encima de la puerta de carga para formar una chimenea. En la parte superior del horno un casquete cónico llamado chispero detenido, impide que la chispa salga al exterior. La chispa detenida enfría las chispas y permite que solo escape humo por la abertura. A veces, un horno de cubilote puede equiparse con un colector, un ajustador y una precipitación para minimizar la contaminación atmosférica.
Zonas en horno de cúpula
Sobre la base de las reacciones de combustión, todo el eje de la cúpula se puede dividir de la siguiente manera:
Zona de crisol:- Está entre la parte superior del lecho de arena y la parte inferior de las toberas. El hierro fundido se acumula aquí. Esto también se llama el bien o hogar .
Zona de combustión u oxidación:- Se sitúa normalmente 150 a 300 mm encima de la parte superior de las toberas. Todo el oxígeno del chorro de aire se consume aquí debido a la propia combustión que tiene lugar en esta zona. Así se libera mucho calor y este se suministra desde aquí a otras zonas.
El calor también se desprende debido a la oxidación del silicio y el manganeso. Debido a este alto calor, siendo la temperatura de 1550° a 1850°C, gotas fundidas de hierro fundido se vierten en el hogar. Las reacciones químicas que ocurren en esta zona son:
C + O2 —–>CO2 + Calor
Si + O2 —–>SiO2 + Calor
2 Mn + O2 —–> 2 MnO2 + Calor
Zona reductora:- Se extiende desde la parte superior de la zona de combustión hasta la parte superior del lecho de coque. En esta zona se produce la reducción de CO2 a CO y la temperatura desciende hasta unos 1200°C en el lecho de coque. Debido a la atmósfera reductora, la carga está protegida de cualquier influencia oxidante. La reacción que tiene lugar en esta zona es:
CO2 + C (coque) —-> 2 CO-Calor
Zona de fusión:- Comienza desde la primera capa de carga de metal sobre el lecho de coque y se extiende hasta una altura de 900 mm. La temperatura más alta se desarrolla en esta zona para la combustión completa del coque y el hierro se funde aquí. La temperatura en esta zona ronda los 1600°C. En esta zona también se produce una absorción considerable de carbono por parte del metal fundido de acuerdo con las siguientes reacciones:
Zona de precalentamiento o zona de carga :- Comienza por encima de la zona de fusión y se extiende hasta la parte inferior de la puerta de carga. La zona de precalentamiento contiene carga de cúpula como capas alternas de coque, fundente y metal y se precalientan allí a una temperatura de aproximadamente 1100°C antes de llegar a la zona de fusión.
Zona de acumulación :- La zona de chimenea se extiende desde arriba de la zona de precalentamiento hasta la parte superior de la cúpula. Lleva los gases generados dentro del horno a la atmósfera.
Capacidad del horno de cúpula
La producción de un horno de cubilote se define como las toneladas de metal fundido obtenidas por hora de calor. Las capacidades (tamaños) de la cúpula varían de 1 a 15 toneladas (o incluso más) de hierro fundido por hora. El tamaño depende no solo del área de la sección transversal de la cúpula, sino también de la intensidad del consumo de coque.
Pero la intensidad del consumo de coca se entiende las toneladas de coque quemadas por m2 del área de la sección transversal de la cúpula en la unidad de tiempo. Se ha observado que 14 cm de superficie en planta de cúpula queman alrededor de 1 kg de coque por hora. El diámetro de la cúpula varía de 1 a 2 m con una altura de 3 a 5 veces el diámetro.
Funcionamiento del horno de cúpula
Los diferentes pasos involucrados en la operación del horno de cúpula son:
La primera operación en la preparación de un horno de cubilote es limpiar la escoria y desecho en el revestimiento y alrededor de las toberas de la corrida anterior. Los puntos defectuosos o los ladrillos rotos se reparan con una mezcla embadurnadora de arcilla refractaria y arena de sílice o ganister. La preparación del fondo de arena de la cúpula se inicia tan pronto como se ha completado el parcheo del revestimiento.
Las puertas inferiores se elevan y mantienen en esta posición mediante puntales metálicos. La arena del fondo se introduce a través de la puerta de carga y se apisona bien alrededor del revestimiento ya través de la intersección de las puertas del fondo. Esta capa de arena se acumula hasta una altura de 100 a 200 mm por encima de la puerta de hierro fundido.
La superficie del fondo de arena está inclinada desde todas las direcciones hacia el orificio de colada para que el metal fundido pueda drenarse completamente de la cúpula en cualquier momento. Se proporciona una abertura de unos 35 mm de diámetro para la eliminación de la escoria, y se forma un orificio de grifo alrededor de un patrón de madera de unos 20 mm de diámetro. La cúpula debe secarse completamente antes de disparar.
2. Disparando la cúpula
Al encender un horno de cúpula, se enciende un fuego de leña en el fondo de arena. Esto debe hacerse de 2,5 a 3 horas antes de que se requiera el metal fundido. Sobre la leña encendida se construye un lecho de coque. Cuando la madera se está quemando bien, se vierte coque en el pozo desde arriba en varias porciones asegurándose de que el coque comience a quemarse también.
El coque se agrega a un nivel ligeramente por encima de las toberas y el chorro de aire se enciende a una velocidad de soplado más baja de lo normal para encender el coque. Tan pronto como comienzan a aparecer manchas rojas sobre la parte superior del lecho de combustible, se introduce coque adicional en la cúpula para alcanzar una altura de 700 a 800 mm por encima de la fila superior de toberas.
El lecho de coque debe estar completamente caliente antes de terminarlo hasta su altura final. La altura del lecho de coque se determina usando una vara de medir que ha sido preparada para indicar la distancia desde el umbral de la puerta de carga hasta la parte superior del lecho de coque. La capa de coque que descansa sobre el fondo de arena antes de comenzar el calentamiento se denomina carga de fondo. La cantidad de coque en el lecho depende de la presión del aire suministrado a la cúpula.
La altura de la carga del lecho o lecho de coque es muy importante para el funcionamiento de la cúpula; afecta la temperatura, la velocidad de fusión y la composición química. En igualdad de condiciones, una cama baja producirá un metal más frío que una que sea alta.
3. Cargando la cúpula
Tan pronto como el lecho de coque alcanza la altura correcta y se enciende de manera uniforme, se cargan capas alternas de arrabio, coque y fundente (piedra caliza) desde la puerta de carga hasta que la cúpula está llena. También se agrega chatarra adecuada junto con el arrabio, para controlar la composición química del hierro producido. La proporción de esta chatarra es ordinariamente del 25 al 50 por ciento del peso total del metal vertido.
Cuando se usa una cantidad considerable de chatarra de acero junto con arrabio, se usa una pequeña cantidad, digamos del 2 al 4 por ciento de ferro-manganeso como desoxidante. El peso de la carga de metal debe ser del 10 al 15 por ciento de la salida horaria de la cúpula. El objeto de agregar fundente es eliminar las impurezas en el hierro y proteger el hierro de la oxidación, reducir el punto de fusión de la escoria y aumentar su fluidez para una fácil eliminación. Además de la piedra caliza, el espato flúor y la ceniza de soda también se utilizan a veces como material fundente.
La cantidad de piedra caliza requerida puede ser de 30 a 40 kg por tonelada de hierro fundido o 25 por ciento en peso del coque cargado. La relación entre el metal fundido y el coque cargado depende de un gran número de factores. Por lo tanto, no es posible dar recomendaciones definitivas para esta relación que se puede lograr en diferentes clases de trabajo. La tabla 11.11 se brinda solo como guía y muestra una buena práctica promedio en la industria. Más comúnmente se mantiene 10:1. Esto significa que se requiere 1 tonelada de coque para fundir 10 toneladas de hierro.
4. Remojo de hierro
Una vez que la cúpula esté completamente cargada hasta la puerta de carga, la carga debería absorber el calor durante unos 45 minutos. La carga se calienta lentamente ya que el chorro de aire se mantiene a una tasa de soplado más baja de lo normal (prácticamente se mantiene cerrada) durante este tiempo. Esto hace que la plancha se empape.
5. Chorro de aire
Al final del período de remojo, se enciende a máxima potencia. Antes de encender la explosión, las aberturas de la tobera y el orificio de roscado se mantienen cerrados. Después de que la explosión ha estado activa durante unos minutos, digamos unos 10 minutos, el metal fundido comienza a acumularse en el hogar. Cuando el metal de la cúpula comienza a derretirse, la velocidad de carga debe ser igual a la velocidad de fusión, de modo que el horno se mantenga lleno durante todo el calor. Al final de la fusión, se detiene la carga, pero se mantiene el chorro hasta que todo el metal se haya derretido.
6. Roscado y escoriado
El primer golpeteo se puede hacer de 40 a 50 minutos después de encender el chorro de aire completo. Durante este período, se recolecta suficiente metal en el hogar sobre el lecho de arena. Cuando la escoria se acumula en el pozo, se abre el orificio de escoria y la escoria se escurre, preferiblemente hacia un bogie para facilitar su extracción. El metal fundido se recoge en cucharones y se lleva a los moldes para su vertido. Se repite el mismo procedimiento hasta fundir todo el metal y terminar la operación.
7. Cierre de la cúpula
Cuando termina la operación, la explosión se apaga y el soporte debajo de la puerta inferior se derriba para que las placas inferiores se abran. Esto permite que los restos de la cúpula caigan al suelo o en un cubo. Luego se apagan y se retiran de debajo de la cúpula.
Por lo general, las cúpulas funcionan de manera continua, al igual que los altos hornos, pero solo funcionan durante los períodos que sean necesarios. En muchas fundiciones, el período de fusión no supera las 4 horas, pero los cubilotes pueden funcionar continuamente durante 10 horas o más.
Eficiencia del horno de cúpula
La eficiencia térmica o de fusión de una cúpula en porcentaje se expresa como:
(Calor utilizado en precalentamiento, fusión y sobrecalentamiento) / (Calor potencial en coque + calor de oxidación de Fe, Si, Mn + calor en el chorro de aire) x 100
La eficiencia de un horno de cubilote varía de 30 a 50 por ciento dependiendo de
1. Tasa de coque o relación de coque expresada como la inversa de la relación metal-combustible en porcentaje,
2. Tasa de explosión, y
3. Tamaño medio de coque.
Requisitos de aire para hornos de cúpula
Para la combustión completa del combustible en el horno de cubilote, se requieren alrededor de 8,4 m3 de aire por kg de coque a temperatura y presión atmosférica normales. Si la proporción de harina a coque es de 10:1, lo que se considera una cifra satisfactoria, el coque requerido por tonelada de hierro será de 1000/10 kg, es decir, 100 kg. Así, el volumen de aire requerido por tonelada de fundido es>
8,4 x 100 =840 m3.
Para permitir fugas, etc., el aire suministrado suele ser un poco excesivo, es decir, alrededor de 900 m3 por tonelada de hierro.
Dimensiones del horno de cúpula
Las dimensiones principales de una cúpula se seleccionan sobre la base de datos empíricos. Por lo tanto, el área de la sección transversal A. de una cúpula depende de la salida por hora diseñada y se determina a partir de la fórmula
Donde d =diámetro de la cúpula en el claro, m, Q =rendimiento de la cúpula de diseño, toneladas por hora, Q2 =rendimiento específico por metro cuadrado de área transversal, toneladas por hora. Como regla, Q1 =6 a 8 toneladas por hora.
La altura útil de una cúpula (distancia desde el eje de las toberas principales hasta el borde inferior del orificio de carga) depende del diámetro y se diseña según la relación H:d =de 3 a 5.
La altura del horno de cúpula afecta directamente a la tasa de fusión , consumo de combustible y la temperatura y calidad del metal fundido . Si es demasiado alto, el coque puede triturarse a medida que cae la carga; si es demasiado bajo, el metal no se calienta lo suficiente, el tiro se reduce y la salida de la cúpula disminuye.
El diámetro interior de la cúpula determina la cantidad de coque consumida y la cantidad de hierro fundido por unidad de tiempo. Se ha encontrado que 14 cm? del área del plano de la cúpula quema alrededor de 1 kg de coque por hora. Así, una cúpula que tenga una capacidad de 3 toneladas por hora requerirá (3x100) o 300 kg de coque por hora, suponiendo una relación metal-combustible de 10:1. El área de la cúpula será por lo tanto igual a (14×300) o 4200 cm². Entonces el diámetro interior será
Raíces cuadradas de (4200×4 )/ π
=73 cm (aprox.)
Cargas de horno de cúpula
Si se desean productos de calidad uniforme, se debe prestar especial atención a la carga de la cúpula. Por lo general, varios grados de arrabio y chatarra están disponibles para el hombre de fundición. Para lograr la composición deseada del metal fundido, estos grados deben ajustarse y controlarse. Dado que los diversos elementos del metal experimentan cambios químicos durante la operación de refundición, se deben dar concesiones para su pérdida o ganancia al completar la carga. La pérdida o ganancia de varios elementos es la siguiente.
5. Fósforo: Prácticamente no hay pérdida ni ganancia en el contenido de fósforo.
Esto fue todo sobre el horno de cúpula, sus zonas, operaciones y partes. Espero que te haya gustado el artículo. Por favor dé su opinión en los comentarios a continuación.
Tecnología Industrial
- Sensor de posición del acelerador - Principio de funcionamiento y aplicaciones
- Sensor RVG - Principio de funcionamiento y sus aplicaciones
- Sensor de pulso:principio de funcionamiento y sus aplicaciones
- Principio de funcionamiento del sensor RTD y sus aplicaciones
- ¿Qué es la impresión 3D? Principio de funcionamiento | Tipos | Aplicaciones
- Horno de cúpula:principio, construcción, funcionamiento, ventajas, desventajas y aplicación
- Mecanizado por chorro abrasivo:piezas, principio de funcionamiento, aplicación
- Mecanizado por chorro de agua:principio de funcionamiento, aplicaciones, ventajas
- Proceso de mecanizado ultrasónico:principio de funcionamiento de las piezas, ventajas
- Hoja de datos Hc06: Introducción a Pinout, características, aplicaciones y principio de funcionamiento
- Principio de funcionamiento del proceso de fundición a presión y sus aplicaciones.