Entrevista con el experto:Doug Hedges, presidente de Sintavia, sobre cómo lograr la producción en serie con la impresión 3D en metal
Sintavia es un fabricante independiente que brinda servicios de fabricación de aditivos metálicos para industrias críticas como la aeroespacial y de defensa, y la de petróleo y gas. .
Con un enfoque en la producción en serie de piezas metálicas mediante fabricación aditiva, la empresa ofrece un servicio exclusivo de principio a fin que comprende no solo la producción y el posprocesamiento, sino también las pruebas. , metalurgia y caracterización de polvos en su laboratorio interno.
Recientemente, Sintavia anunció sus planes de expansión, mudándose a una nueva instalación de 55,000 pies cuadrados que tiene un énfasis distintivo en la producción.
Esta semana, nos complace conversar con el presidente de Sintavia, Doug Hedges, para analizar cómo la empresa produce piezas metálicas certificadas de alta calidad, por qué la AM es perfecta para la industria aeroespacial y qué la industria de AM puede hacer para acelerar la adopción de la tecnología.
¿Podría contarnos un poco sobre Sintavia?
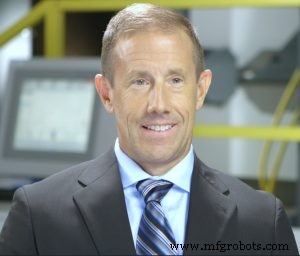
Sintavia fue fundada en 2012 por Brian Neff, director ejecutivo y presidente de la empresa. La compañía se fundó como un esfuerzo interno de fabricación aditiva con una compañía llamada CTS Engines, que es un motor a reacción independiente MRO con sede en Fort Lauderdale, Florida.
Sintavia se convirtió en una empresa independiente en 2015 y nos mudamos a Davie, Florida, donde todavía nos encontramos hoy.
Como empresa, tenemos una amplia experiencia en aviación. Vimos que existía la oportunidad de utilizar estos antecedentes para crear una empresa que esté integrada verticalmente con muchas ofertas diferentes. Para ser bueno en aditivos, también debe ser bueno en metrología, metalurgia, mecanizado, tratamientos térmicos, pruebas, etc.
Entonces, si bien nuestra habilidad principal es la fabricación aditiva, estamos utilizando nuestra experiencia en los campos de fabricación de MRO y OEM para crear una nueva empresa independiente que se centre en la industria aeroespacial y de defensa, así como en el petróleo y el gas.
Lo único de Sintavia es que la integración vertical sustenta todo lo que hacemos:desde el posprocesamiento, la calidad, la metalurgia, el escaneo, etc. Todos estos elementos se encuentran bajo un mismo techo dentro de nuestra planta de producción aquí en Davie, Florida.
La industria aeroespacial es un foco central para Sintavia. ¿Podría explicarnos algunos de los beneficios de la fabricación aditiva para la industria aeroespacial?
La fabricación aditiva funciona bien para la industria aeroespacial por una variedad de razones.
Primero, es importante tener en cuenta que la tecnología comenzó como una herramienta de desarrollo de prototipos para los OEM dentro de la industria aeroespacial y de defensa para iterar rápidamente en diseños y pruebas. los motores. Ahora ha evolucionado hasta un punto en el que las empresas están fabricando motores con piezas aditivas.
Así que sigue siendo un gran impulsor. Pero luego están todos los otros beneficios típicos que hacen de AM una gran tecnología. Aquí, me refiero a la consolidación de soldaduras, fundiciones complejas, aligeramiento, diseño sin herramientas. Por supuesto, la complejidad no es gratuita, pero se amplía enormemente con el uso de aditivos.
Como ejemplo, un enfoque principal para nosotros en términos de selección de piezas son los cuerpos de válvulas externos en el exterior de los motores a reacción y los conductos. También vemos un mercado emergente para chasis e intercambiadores de calor dentro de la industria aeroespacial.
Una de las tecnologías de impresión 3D de metal que utiliza es Powder Bed Fusion. ¿Cuáles son los beneficios de esta tecnología para aplicaciones aeroespaciales?
Bueno, la impresión 3D de metal en general realmente se presta a diseños únicos.
La etapa inicial de lo que estamos haciendo es utilizar la fusión en lecho de polvo con láseres y haces de electrones para construir conductos y componentes de alta presión capa por capa. Obviamente, existe el beneficio de usar la tecnología como una herramienta de reemplazo para las piezas soldadas y fundidas que ya se utilizan en la industria.
Pero el poder de los aditivos va mucho más allá de eso:puede fabricar piezas que son mejores, más ligeras y más resistentes, lo que esencialmente facilita un rendimiento mejorado. En última instancia, para utilizar realmente la potencia de la AM, los componentes deben diseñarse para la fabricación aditiva.
Puede utilizar la fabricación aditiva, principalmente me refiero a láseres, para componentes como intercambiadores de calor y chasis para crear geometrías que antes eran imposibles de fabricar.
También tiene, por ejemplo, cuerpos de flujo o conjuntos de válvulas que puede hacer más rápido y consolidar usando AM. Esto permite a nuestros clientes no solo optimizar sus cadenas de suministro existentes, sino también hacer mejores productos y aprovechar las fortalezas del mercado aeroespacial y de defensa OEM.
Tome los intercambiadores de calor como ejemplo:la fabricación aditiva le permite para hacer paredes muy finas y geometrías pequeñas e intrincadas dentro del componente. Entonces puede tener una pared de 200 micrones o menos. Además, con la fabricación aditiva, ahora tiene una mejor manera de extraer el calor del componente. Esto es genial porque el objetivo final del juego con los intercambiadores de calor es sacar el calor del componente para que pueda incluir más componentes electrónicos.
Utilizamos la fabricación aditiva de metales para mejorar sus productos. Cualquier cosa, desde cuerpos de válvulas, componentes externos de motores a reacción, conductos e intercambiadores de calor hasta chasis y diferentes tipos de estructuras de tuberías que se hicieron mediante soldaduras con una gran cantidad de complejas plantillas y accesorios para soldarlos juntos.
Dicho esto , también hacemos mucho más que eso. Por ejemplo, trabajamos en lo que hay dentro de los equipos de turbomaquinaria, desde un impulsor más pequeño que podría estar dentro de un compresor, hasta un impulsor más grande que podría estar dentro de un cohete.
Tenemos un enfoque dentro del sector aeroespacial comercial - esencialmente motores a reacción - y otro enfoque en la propulsión, que serían piezas de cohetes.
Luego tenemos el "intermedio" dentro de la industria aeroespacial y de defensa, con lo que me refiero a los componentes oscuros que alguna vez se hicieron de 10 a 100 piezas, pero ahora podemos hacer en una pieza singular mediante fabricación aditiva.
¿Podría ampliar algunos de los desafíos de diseño asociados con esas aplicaciones?
AM es un proceso relativamente nuevo en la fabricación. Estamos usando láseres o haces de electrones para derretir el polvo en forma de capas. Básicamente, lo que realmente estamos haciendo es hacer soldaduras de tamaño pequeño a mediano, o "microsoldaduras".
En este proceso de microsoldadura, hay un enfriamiento rápido donde el láser expone el polvo metálico. Tiene un caso de dos extremos:un proceso de impresión muy caliente, con un enfriamiento rápido al lado.
Debido a estas diferencias extremas de temperatura, su pieza está sujeta a distorsión. Por tanto, estas piezas no son como las soldaduras tradicionales hechas con piezas fundidas; son artículos únicos en sí mismos.
Uno de los desafíos clave es poder predecir cómo se moverán estas piezas dentro del proceso de fabricación aditiva. Una parte clave de este desafío es utilizar esta tecnología muy moderna y herramientas de alta tecnología para hacer la predicción al principio, para ayudar con la coordinación completa del proceso.
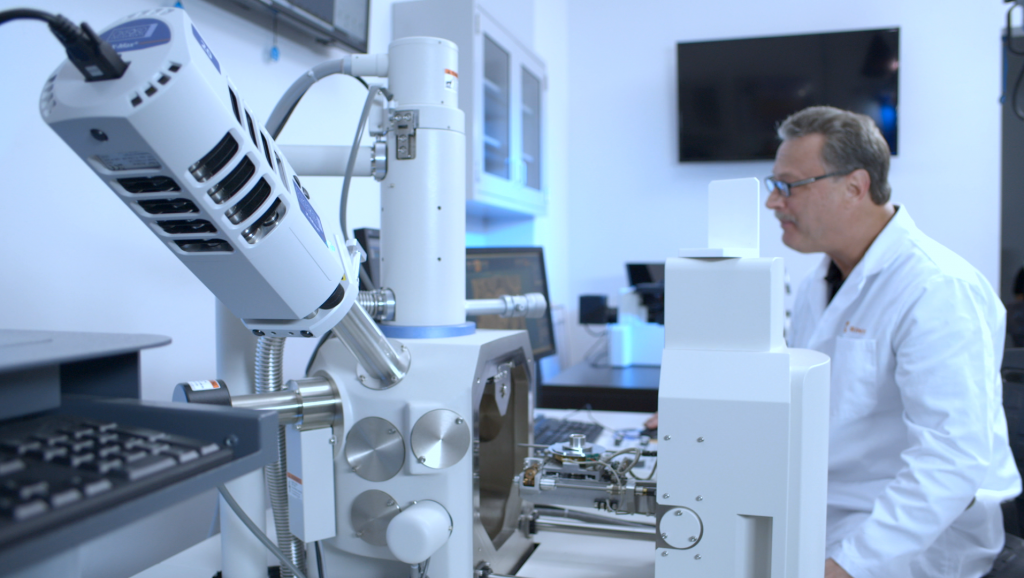
En Sintavia, utilizamos el análisis de elementos finitos (FEA) al comienzo del ciclo de diseño. Los ingenieros de Sintavia obtienen los datos iniciales de nuestros clientes en forma de modelos, dibujos y especificaciones CAD. Nuestros ingenieros trabajan con nuestros clientes para determinar parámetros clave como cómo orientar una pieza en la placa de construcción, en qué ángulo se creará una pieza y cómo se usarán los soportes, ya sea para sujetar la pieza o quitarle el calor. part.
Estamos usando matemáticas para predecir cómo la parte se distorsionará y minimizará esa distorsión para hacer una parte de muy alta fidelidad. Necesitamos saber cómo esa pieza se moverá y cambiará sobre nosotros, de modo que podamos agregar material a las bridas, perforaciones, orificios, etc., para asegurarnos de que haya suficiente material para limpiar al final del proceso. Con este enfoque, también podemos dar cuenta del posprocesamiento de esa parte en un momento posterior.
Una cosa a tener en cuenta es que la fabricación aditiva es un proceso tremendamente poderoso para crear piezas complejas, pero debe usarse en coordinación con los procesos tradicionales. La coordinación del proceso aditivo con el proceso sustractivo es fundamental.
Escuchamos mucho sobre los desafíos que implica el posprocesamiento de piezas metálicas, y ese es uno de los servicios que ofrece Sintavia. ¿Podría explicarnos algunos de los mayores desafíos relacionados con el posprocesamiento y su enfoque?
El posprocesamiento debe ser un esfuerzo coordinado entre el proceso de impresión en sí y el posprocesamiento que acompaña a esa pieza después de la producción.
Un desafío común que la mayoría de la gente no ve es la eliminación del polvo después del proceso. Después del proceso de impresión, se debe eliminar todo el polvo de la pieza. Dado que algunas de estas piezas tienen geometrías muy complejas, fabricamos máquinas personalizadas, ya sean ultrasónicas o sistemas de vibración tradicionales, para eliminar el polvo.
Es típico quitar el polvo de la pieza antes del siguiente paso, que casi siempre es un alivio del estrés. Estamos aliviando el estrés internamente, ya sea con un horno de vacío o un horno de caja para eliminar el estrés residual del proceso de construcción de aditivos.
A partir de ahí, vas a un electroerosión por hilo o una sierra de cinta para quitar la pieza de la placa. Entonces, por supuesto, debe quitar los soportes. Estos soportes pueden ser desde simples soportes de celosía hasta algo muy sólido que se utiliza para sujetar la pieza y producir piezas muy grandes de superaleación de níquel. Estos están sujetos a mucho estrés térmico.
Debido a esto, es posible que necesite un proceso de máquina muy robusto para quitar los soportes de estas partes. Puede haber un trabajo considerable involucrado en eso. Y cuando digo "proceso de la máquina", esto podría significar muchas cosas diferentes. Podría significar algo tan fácil como romperlos con unos alicates en una máquina herramienta de cinco ejes muy rígida para quitar esos soportes de la pieza.
Desde este punto, tiene varias opciones. Por ejemplo, puede ir a HIP, que presentamos en el sitio, o usamos mecanizado. En este caso, cuando digo mecanizado, me refiero al mecanizado para imprimir. Así que esto no es realmente diferente de lo que vería en un taller de máquinas.
En su mayor parte, tenemos un dibujo 2D con muchos controles y mecanizamos esa parte para alinearla con las especificaciones.
Pasando a los polvos metálicos en sí, ¿cuál es el proceso de desarrollo de polvos metálicos en Sintavia?
Para ser claros, realmente no desarrollamos polvos per se. Pero nos hemos involucrado en ayudar a las empresas a desarrollar aleaciones que no estaban disponibles comercialmente en el pasado.
Tenemos empresas con las que trabajamos que tienen, digamos, una variante de acero para herramientas o una variante de acero inoxidable. Por lo general, se trata de aleaciones especiales que se han desarrollado para utilizarlas con algún tipo de ventaja de rendimiento en el futuro.
Lo que sí tenemos son soluciones en polvo aprobadas para vuelos para la industria aeroespacial. Obtenemos el polvo, lo llevamos a nuestro laboratorio y lo ejecutamos a través de una multitud de pruebas antes de que comience la compilación.
Uno de nuestros puntos fuertes en Sintavia es que tenemos una caracterización in situ completa de nuestro polvo dentro de nuestro laboratorio. Esto nos permite tomar muestras y comprender qué le sucede al polvo. Normalmente, otras empresas subcontratan este proceso. Entonces, si bien podemos adquirir materiales de nuestro proveedor de polvo, realizamos pruebas de flujo, morfología, distribución del tamaño de partículas, análisis de gases, ICP para química, etc.
Realizamos alrededor de ocho o nueve pruebas para asegurarnos de que los polvos cumplan con los requisitos de fabricación de nuestros clientes. Luego, a medida que se usa el polvo, tomamos muestras y archivamos estas muestras de polvo para comprender qué sucede con el polvo a medida que continúa la construcción. Esto significa que podemos comprender exactamente qué le sucede al polvo a medida que se usa progresivamente.
Sintavia ha anunciado que planea abrir una nueva instalación con un aumento de máquinas este mes. ¿Podría compartir la visión detrás de esta nueva instalación?
Estamos muy emocionados de abrir nuestra nueva instalación este mes.
La nueva instalación tendrá 55,000 pies cuadrados y vamos a basar esa instalación en nuestro éxito pasado.
Un punto clave es que se basará significativamente en la producción. Vamos a albergar más de $ 30 millones en maquinaria nueva, equipos AM modernos más grandes, sistemas de manejo de pólvora, generadores de respaldo, fuentes de alimentación, gas inerte. Prevemos que sumaremos más de 135 nuevos puestos de trabajo para Sintavia y el sur de Florida.
La nueva instalación es realmente la visión de tomar lo que hemos hecho a una escala más pequeña, hacer funcionar 12 máquinas aquí en nuestra instalación actual y escalar eso a una instalación de 55,000 pies cuadrados con hasta 65 máquinas.
Habrá un gran esfuerzo en la fabricación aditiva, en los tratamientos térmicos. posprocesamiento, acabado, limpieza, etc.
Esencialmente, buscamos controlar el proceso de aditivos en una sola instalación. Ese es realmente el modelo de negocio:queremos ampliar lo que hemos hecho y llevarlo a un proceso de fabricación que garantice la calidad y la repetibilidad para nuestros clientes OEM.
¿Consideraría expandirse a otras industrias en el futuro, como la automotriz o médica, donde también hay una gran demanda de piezas metálicas impresas en 3D?
Sí, absolutamente. Tenemos algunas cosas que suceden tanto en el sector automotriz como en el médico. Y hay otras industrias para las que los aditivos también tienen sentido.
Por ejemplo, estamos involucrados en turbinas de gas industriales. Aunque nuestra experiencia son las turbinas de gas aeronáuticas, las turbinas de gas terrestres para energía son básicamente motores de turbinas aeronáuticas a escala y ligeramente diferentes.
La tecnología también se aplica muy bien al sector biomédico.
Sintavia tiene la acreditación AS9100 - AS9100 es un sistema de gestión de calidad para la industria aeroespacial. Nuestro laboratorio cuenta con la acreditación ISO 17025 para mediciones mecánicas, lo que puede significar cualquier cosa, desde la caracterización del polvo y la química hasta pruebas de tracción y pruebas de fatiga.
La industria biomédica tiene una agencia de acreditación diferente; la mayor parte se reduce a ISO 13485. Una vez que tenga AS9100, puede pasar a ISO 13485. No es un gran salto ir entre estas diferentes industrias. Después de todo:la calidad es calidad y los procesos son procesos. Si puede hacer aeroespacial, puede hacer esa transición a otros mercados.
Además, más allá de todo lo que he mencionado, el control de calidad es el aspecto más importante.
Desde el primer día, nos hemos centrado en desarrollar nuestro sistema de calidad con AS9100, Certificaciones ISO y Nadcap. Todo esto es muy beneficioso para nuestros clientes OEM y definitivamente también puede ser un recurso para otras industrias.
En su opinión, ¿cuáles son algunas de las cosas necesarias para acelerar la adopción de la impresión 3D en metal?
A pesar de toda nuestra tecnología y la destreza que tenemos en análisis, realmente deberíamos centrarnos en lo que impulsa los negocios. El dinero y la velocidad impulsan los negocios. Esto significa que la tecnología debe volverse más rápida, más barata y más establecida.
Dicho esto, estamos viendo cómo están cambiando las cosas. Durante nuestro tiempo aquí en Sintavia, hemos visto cómo ha evolucionado la AM de metal. Por ejemplo, en un momento dado, el aluminio era un material relativamente complicado de imprimir en la fabricación aditiva, pero ahora es casi un lugar común. A medida que veamos láseres adicionales, a medida que veamos la experiencia y el diseño de piezas para aditivos, ofrecerá a nuestros clientes una velocidad más rápida y ahorros de costos.
Todo esto surgió históricamente de la industria de la creación de prototipos, y queremos trasladarlo a la producción en serie. Hay ciertas cosas que debemos hacer para que sea más rápido y económico, brindar calidad y brindar las ventajas que todos saben que los aditivos metálicos pueden ofrecer.
¿Cómo cree que evolucionará la fabricación aditiva de metales en los próximos cinco años y cómo encaja Sintavia en esa visión?
Lo que realmente tenemos que hacer es empezar a fabricar piezas en forma de producción. Para las industrias críticas, debemos asegurarnos de que estamos produciendo piezas de metal reales que sean completamente funcionales.
Sabemos que estas piezas compiten extremadamente bien con las piezas fundidas en cuanto a propiedades mecánicas. Con el proceso y los controles adecuados, también pueden competir con las materias primas e incluso con los productos falsificados en algunos casos.
El control de calidad, es decir, comprender los requisitos de calidad y poder validar su pieza, realmente marcará la diferencia en el futuro.
Pero tampoco podemos perder de vista el hecho de que la tecnología aún es relativamente nueva. Como industria, estamos haciendo muchas cosas por primera vez.
Esto significa que la parte inicial del proceso debe aprenderse en primer lugar.
Por ejemplo, al comienzo del proceso, los ingenieros deberán comprender las estrategias de soporte y dedicar tiempo a aprender la mejor manera de optimizar la geometría de la pieza y la geometría del soporte, lo que a su vez ayudará a producir mejores piezas y garantizará que los soportes se desprendan con relativa facilidad.
Gracias a este trabajo realizado en el Para empezar, habrá tomado lo que fue un paso costoso y lento de eliminación de soporte y lo habrá hecho significativamente menos costoso. El esfuerzo de ingeniería para hacer las piezas es realmente fundamental para lograr que lleguen a un punto de madurez para hacer productos uno tras otro.
¿Cómo se ve el futuro de Sintavia?
¡Parece muy emocionante! Por supuesto, también parece bastante desafiante a medida que nos mudamos a nuestras nuevas instalaciones. Implementaremos la manufactura esbelta. Tenemos la primera instalación de fabricación aditiva ajustada a gran escala desarrollada expresamente para nuestra alineación con los OEM y la cadena de suministro.
En 2019, continuaremos gran parte del trabajo que hemos estado haciendo durante los últimos años, en términos de calificación y desarrollo de piezas para nuestros clientes.
No nombraré nombres, pero si nos fijamos en las principales empresas aeroespaciales a nivel mundial, es muy probable que hagamos negocios para ellas.
En algunos casos, como nuestra relación con Honeywell, donde somos el primer proveedor de AM aprobado para fabricar piezas listas para volar para Honeywell Aerospace. Nos hemos alineado con Honeywell para utilizar nuestra instalación actual y nuestra próxima instalación para sacar eso y fabricar piezas de producción para Honeywell.
Honeywell es un adoptador relativamente rápido de la tecnología y tiene muchísimas aplicaciones. Pero si sale de Honeywell, es muy probable que estemos trabajando para ellos ahora, ya sea un avión o una planta de energía de motores, ya sea un proveedor aeroespacial y de defensa.
Consideramos que 2019 y 2020 serán años relativamente importantes para nosotros, en lo que respecta a la adopción de aditivos metálicos. Es realmente emocionante que Honeywell esté aquí hoy, pero veremos que tendremos más clientes haciendo producción en serie en los próximos años.
Estamos alineando nuestra empresa para proporcionar ese recurso a los OEM del mundo para que puedan tener un socio integrado verticalmente de ventanilla única para producir estas piezas con fabricación aditiva.
¿Alguna idea final?
Me gustaría reiterar que la calidad es nuestro objetivo.
Nuestros clientes son, sin duda, los clientes más reacios al riesgo del mundo. Para que se sientan cómodos volando estos componentes críticos hechos por fabricación aditiva, la calidad es primordial para esto.
Al final del día, queremos ajustar los productos a los dibujos y especificaciones de ingeniería, para usarlos en aplicaciones del mundo real. Para hacer eso, se necesita un enfoque en la conformidad.
Además, hoy AM es donde está toda la atención de los medios y donde se gasta mucho tiempo y dinero. Pero, en última instancia, debería tratarse de tomar la parte que hizo mediante la fabricación aditiva y adaptarla a los requisitos de ingeniería de sus clientes.
Así que sí, nos gusta hablar de fabricación aditiva. Pero también me gusta pensar en ello como avanzado fabricación. Me gustaría alejarme de las palabras de moda de la fabricación aditiva para decir que somos un fabricante avanzado de piezas aeroespaciales de precisión. Queremos fabricar piezas avanzadas para garantizar que nuestros clientes puedan mejorar significativamente sus diseños actuales.
Para obtener más información sobre Sintavia, visite: https://sintavia.com/
Acerca de Doug Hedges
Doug Hedges tiene más de 20 años de experiencia en la industria aeroespacial, desde el diseño de componentes experimentales OEM hasta reparaciones, alteraciones y desarrollo de componentes aprobados por la FAA según las especificaciones y controles estándar de la industria.
Antes de Sintavia, se desempeñó como ingeniero sénior en CTS Engines, desarrollando reparaciones y procesos para la revisión de motores a reacción de General Electric, ingeniero principal de proyectos para HEICO Aerospace, ingeniero sénior de PMA para Kapco Global e ingeniero de diseño para Rolls-Royce. Doug tiene una licenciatura en ingeniería mecánica de la Universidad de Minnesota.
Entrevistas con expertos
La serie Expert Interviews de AMFG muestra a empresas e individuos innovadores que ayudan a dar forma al futuro de la fabricación aditiva. Para obtener más información sobre la participación en la serie, comuníquese con [email protected].
Impresión 3d
- ¿Cómo se puede escalar a producción aditiva en serie con MES aditivo?
- Entrevista con un experto:el profesor Neil Hopkinson, director de impresión 3D de Xaar
- Entrevista con un experto:Philip Cotton, fundador de 3Dfilemarket.com
- Entrevista con un experto:Dr. Alvaro Goyanes de FabRx
- Entrevista con el experto:John Kawola, presidente de Ultimaker, sobre el futuro de la impresión 3D
- Entrevista con el experto:Doug Hedges, presidente de Sintavia, sobre cómo lograr la producción en serie con la impresión 3D en metal
- Entrevista con el experto:Brian Alexander de Solvay sobre el desarrollo de polímeros de alto rendimiento para la impresión 3D
- Entrevista con el experto:Philip DeSimone, cofundador de Carbon, sobre cómo avanzar hacia la producción de gran volumen con impresión 3D
- 4 desafíos de fabricación aditiva que se pueden resolver con software
- Entrevista con el experto:Rush LaSelle de Jabil sobre el futuro de la fabricación aditiva
- Entrevista experta:Tecnólogo jefe de ANSYS sobre cómo lograr el éxito en la impresión 3D en metal con simulación