Eliminando barreras para aligerar barcos con materiales compuestos
Los compuestos de polímero reforzado con fibra de vidrio y carbono (GFRP y CFRP) se han utilizado para construir embarcaciones marinas durante décadas, incluidos numerosos cazadores de minas de 40 a 60 metros e incluso embarcaciones más grandes, incluidos el Corvette de clase Visby de 72 metros de eslora de la Armada sueca y el velero Mirabella V de 75 metros de eslora . El yate a motor de 141 metros Swift 141 (renombrado Yas ) es una fragata de acero holandesa reconstruida con GFRP / CFRP en suelas debajo de la cubierta y superestructura de tres cubiertas (ver “De fragata a lujoso barco de pasajeros”), que incluye una junta de cubierta de material compuesto con acero.
Y, sin embargo, los compuestos rara vez se utilizan en la construcción naval. Esto se debe principalmente a las regulaciones de Seguridad de la vida en el mar (SOLAS) emitidas por la Organización Marítima Internacional (OMI, Londres, Reino Unido), que exigían que los barcos comerciales se construyeran en acero hasta que MSC / Circ. 1002 se emitió en 2002 permitiendo diseños alternativos.
“El reglamento obliga a realizar un análisis de riesgos que demuestre que el diseño y la construcción alternativos son equivalentes al acero”, explica Stéphane Paboeuf, jefe de la Sección de Materiales Compuestos de la sociedad de clasificación Bureau Veritas (BV, Nantes, Francia). “Este proceso es largo, costoso y la decisión final aún podría ser negativa”. Por lo tanto, aunque los materiales compuestos ofrecen muchas ventajas para la construcción naval, los desafíos de la seguridad contra incendios y las regulaciones han planteado barreras para su uso.
Mientras tanto, los propietarios de barcos, operadores y constructores están buscando soluciones para mejorar la sostenibilidad, incluido un peso más ligero para reducir el uso de combustible, las emisiones de gases de efecto invernadero y el calado de los barcos, este último para vías navegables interiores poco profundas. La resistencia a la corrosión inherente de los composites para reducir el mantenimiento también es atractiva.
En 2017, la OMI emitió MSC.1 / Circ., Un nuevo conjunto de pautas para el uso de compuestos de FRP en barcos comerciales. A medida que se acerca la evaluación de la OMI de estas directrices en 2021, se está llevando a cabo una cantidad asombrosa de actividad. Dos consorcios europeos, FIBRESHIP y RAMSSES, apoyados por la red europea de 378 miembros para aplicaciones ligeras en el mar (E-LASS), están liderando esta ola de proyectos de demostración, que incluye cubiertas, timones, cascos, cabinas modulares y superestructuras, parche reparaciones de juntas soldadas de acero y de material compuesto a acero. Juntos, tienen como objetivo superar las barreras para la construcción de buques compuestos ligeros no solo demostrando el rendimiento estructural y frente al fuego de grandes estructuras y buques completos, sino también desarrollando nuevas rutas para los métodos de certificación y producción, nuevas tecnologías de unión y herramientas de diseño. También están compartiendo información a través de talleres continuos, repositorios de conocimientos y bases de datos de materiales / diseño. Puede que se esté abriendo un nuevo mercado para los compuestos marinos, pero ¿qué soluciones requerirá?
FIBRESHIP y RAMSSES
FIBRESHIP y RAMSSES se iniciaron en junio de 2017, financiados por el programa Horizonte 2020 de la Unión Europea. FIBRESHIP tiene 18 miembros y funcionará hasta mayo de 2020, mientras que RAMSSES tiene 36 miembros y finaliza en mayo de 2021. Ambas incluyen empresas de toda la cadena de suministro que abarcan centros de I + D, universidades, proveedores de materiales y tecnología, fabricantes de piezas, empresas de ingeniería y arquitectura naval. astilleros, armadores y sociedades de clasificación. Estos últimos son responsables de desarrollar reglas específicas para construcciones de barcos individuales basadas en las pautas generales de la OMI. Están autorizados por los estados del pabellón (cada barco lleva la bandera de un país) para auditar la construcción del barco y garantizar que se sigan estas reglas. “Es importante que todas las partes interesadas y los usuarios finales estén involucrados”, dice Alfonso Jurado, jefe de I + D de Técnicas y Servicios de Ingeniería (TSI, Madrid, España) y coordinador del proyecto FIBRESHIP.
“El principal objetivo de FIBRESHIP es desarrollar la capacidad de diseño y producción para grandes embarcaciones marinas (más de 50 metros de eslora) con menos peso”, continúa Jurado. "Esta es también la principal motivación de mi empresa". TSI está diseñando la estructura compuesta de un buque de investigación pesquera (FRV) de 85 metros de eslora total (LOA), que servirá como demostrador y, hasta ahora, logra una reducción de casi un 70% en el peso estructural en comparación con el buque de referencia de acero. “Esto es asombroso, ofrece la posibilidad real de ayudar al sector del transporte marítimo”, dice. Una sección de 20 toneladas de este FRV, que mide 11 por 11 por 8,6 metros (ver imagen de apertura), fue construida por el astillero socio iXblue en La Ciotat, Francia, y exhibida en el segundo taller público de FIBRESHIP en junio de 2019 (ver publicación de noticias con video del demostrador que se está fabricando).
Jurado explica que el FRV es el primero de los tres maletines de barcos compuestos generales que FIBRESHIP está desarrollando. Los dos siguientes son buques portacontenedores LOA de 260 metros y ROPAX de 204 metros, este último combina la capacidad de carga de un buque roll-on / roll-off con las instalaciones de pasajeros de un ferry. “Se eligió el FRV como demostrador porque es más pequeño con una estructura marina más convencional y, por lo tanto, el más factible de ser construido en un futuro cercano”, dice. "Los armadores también han mostrado un interés real en un buque de este tipo". Mientras tanto, RAMSSES tiene 13 demostradores en progreso, 10 de los cuales incluyen materiales compuestos, y también está buscando una embarcación totalmente compuesta.
Jurado señala que las empresas que participan en estos proyectos ven el potencial de estos diseños novedosos y nuevos productos ligeros para proporcionar una ventaja competitiva para sus negocios, así como para la industria naviera de cada país. Pero el progreso no estará asegurado únicamente por los grandes manifestantes. “También debemos contar con el apoyo de las autoridades reguladoras”, agrega. “Un primer paso es involucrar a la OMI y adaptar la normativa SOLAS actual a los nuevos requisitos y demandas de la industria naviera. Sin esto, no podemos seguir adelante porque las compañías de seguros no respaldarán los barcos compuestos reforzados con fibra si no cumplen con los requisitos mínimos y la certificación de seguridad, por ejemplo ”.
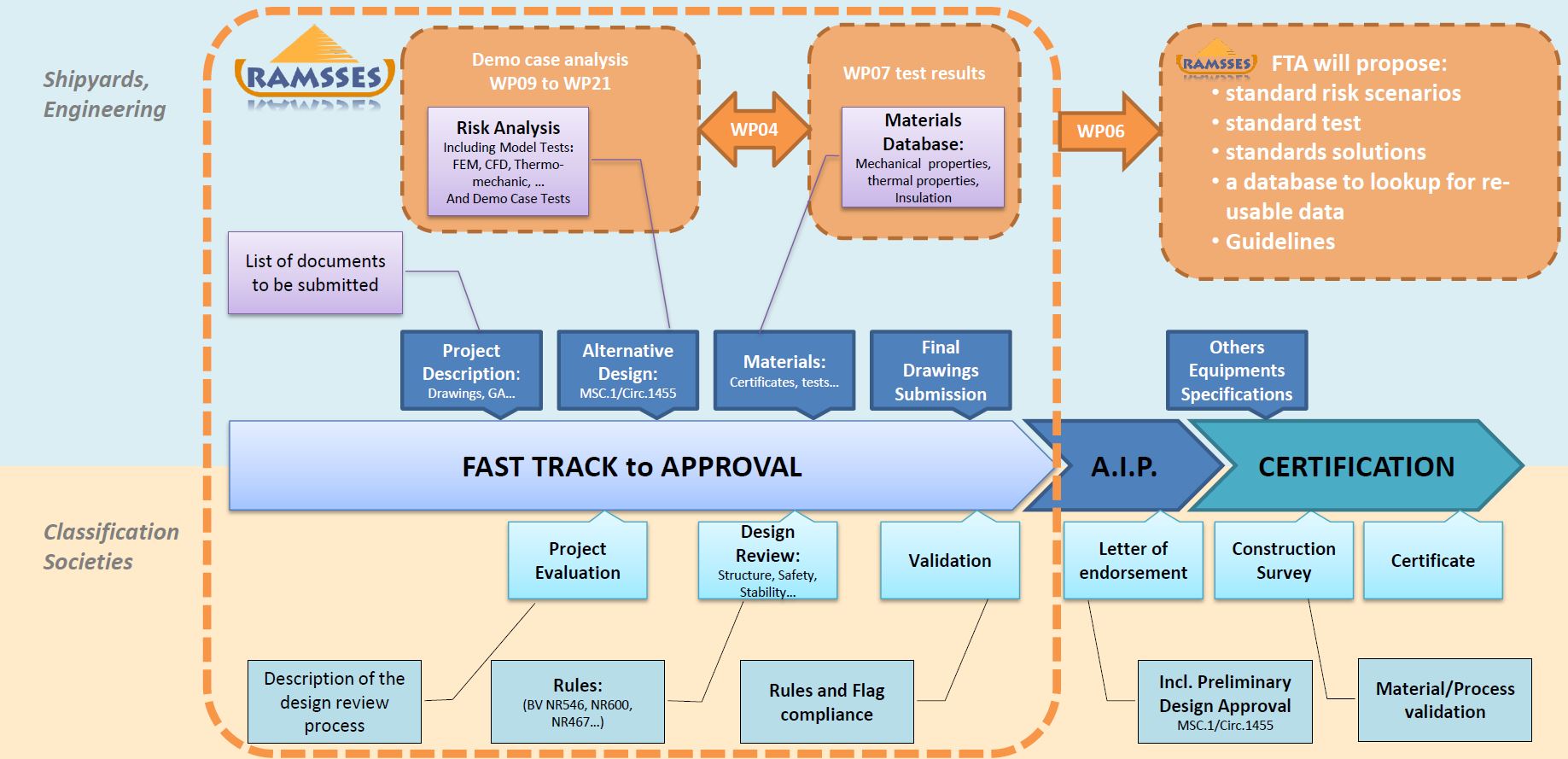
Enfoque propuesto Fast Track to Approval (FTA) para la certificación de materiales compuestos en buques comerciales que se está desarrollando dentro del proyecto RAMSSES, como se presentó durante el Seminario E-LASS de junio de 2019 (Vigo, España). Fuente | RAMSSES y Stephane Paboeuf, Bureau Veritas
"FIBRESHIP está persiguiendo un enfoque a largo plazo mediante el desarrollo de nuevas reglas, mientras que RAMSSES está desarrollando un enfoque a corto plazo utilizando reglas y métodos existentes", explica Paboeuf en BV, que es el único socio de la sociedad de clasificación en RAMSSES, y uno de los tres en FIBRESHIP junto con Lloyd's Register (Londres, Reino Unido) y RINA (Génova, Italia). "En RAMSSES, estamos desarrollando un procedimiento Fast Track to Approval (FTA) basado en la reutilización de los datos del proyecto para estandarizar las pruebas y brindar orientación para el diseño y la aprobación". Este procedimiento debe ser sencillo y de fácil lectura para los astilleros, arquitectos navales y proveedores. La aceleración frente al proceso actual vendrá a través de los apoyos que se están desarrollando en los proyectos de demostración de RAMSSES, que incluyen:
- una base de datos de soluciones preaprobadas y resultados de pruebas de materiales para evitar pruebas repetitivas,
- escenarios de riesgo de incendio que cubren una gama de aplicaciones similares para limitar el número y el alcance de las evaluaciones de riesgo, y
- herramientas de análisis y modelado, incluidos modelos numéricos o estadísticos que pueden reemplazar las pruebas físicas en el futuro.
“En FIBRESHIP, estamos trabajando con Lloyd’s Register y RINA para desarrollar un conjunto de reglas prescriptivas específicamente para grandes embarcaciones construidas con materiales compuestos”, continúa Paboeuf. "Para el rendimiento estructural, estamos definiendo nuevos coeficientes de seguridad para cargas locales y globales". RAMSSES y FIBRESHIP también proponen reemplazar los niveles de clasificación de fuego actuales como A60, B30 y B15 con una nueva convención REIxx, donde R especifica resistencia al fuego (capacidad de carga en caso de incendio), E designa integridad (la prevención de la propagación de humo y llamas). ) y defino el aislamiento contra incendios. "El objetivo es alinear mejor las clasificaciones de resistencia al fuego estructural con los materiales compuestos que se utilizan", explica Paboeuf.
Además, los dos proyectos también se ocupan de las evaluaciones de riesgo debido a la propagación de llamas, la producción de humo y el riesgo de incendio en el espacio de origen, pero también a nivel de seguridad global de los buques. “Para el comportamiento frente al fuego, estamos desarrollando un enfoque de equivalencia local, que se ocupa de la seguridad contra incendios a nivel local en función de las clasificaciones contra incendios de los mamparos y otras divisiones estructurales en cada espacio del buque”, dice Paboeuf. “El segundo enfoque, la equivalencia global, se ocupa del fuego a nivel de embarcación, teniendo en cuenta todos los sistemas (protección activa y pasiva contra incendios, detección, evacuación, etc.) que impactan en la seguridad contra incendios de la embarcación en su conjunto, no solo en cada uno de ellos. espacio dividido ".
“La adopción más amplia de compuestos en la construcción naval será paso a paso”, dice. “Comenzará con piezas pequeñas, como cubiertas y superestructuras, o equipos como líneas de ejes y hélices, antes de avanzar a la construcción de embarcaciones completas, que al principio serán en su mayoría embarcaciones para fines especiales, como embarcaciones de investigación y pruebas sísmicas y de alta velocidad. patrulla. "

Fig. 1 embarcación compuesta RAMSSES de 80 metros
El Astillero Damen (DSNS) está desarrollando una embarcación tipo patrulla costa afuera totalmente compuesta en el proyecto RAMSSES. Su demostrador de sección de casco a escala completa de 6 por 6 por 3 metros se construirá en 2020 utilizando infusión de resina en colaboración con InfraCore Company (ICC) y Airborne International (AIR). Fuente | Astillero Damen y RAMSSES
Demostradores de embarcaciones totalmente compuestos
Además del FRV de 85 metros que está demostrando FIBRESHIP, se está desarrollando un buque tipo patrulla costa afuera de 80 metros de eslora dentro de RAMSSES para que sea el primer buque SOLAS totalmente compuesto. Liderado por Damen Shipyard Group (Gorinchem, Países Bajos), este trabajo lleva adelante los resultados de su proyecto Bluenose iniciado en 2014. Dentro del paquete de trabajo 17 de RAMSSES, Damen está liderando la demostración de un equipo completo de 6 por 6 por 3 metros. Sección compuesta a escala del casco de este buque realizada mediante infusión al vacío, explica Matthias Krause, ingeniero de I + D del Centro de Tecnologías Marítimas (CMT, Hamburgo, Alemania) y co-coordinador del proyecto RAMSSES junto con CETENA (Génova, Italia). “Evonik ha desarrollado una resina novedosa para esta sección de casco de demostración y se han fabricado herramientas de 6 metros de altura. Damen también está trabajando con Airborne International (La Haya, Países Bajos), un proveedor de la industria aeronáutica que también ha construido grandes estructuras infundidas ”. Evonik (Essen, Alemania) ha explicado su función para mejorar la resistencia al impacto y el comportamiento a la fatiga del casco infundido con fibra de vidrio / éster de vinilo.
Otro socio de este demostrador es InfraCore Co. (Rotterdam, Países Bajos), que está desarrollando nuevas aplicaciones para la tecnología InfraCore utilizada por la empresa hermana FiberCore Europe (Rotterdam) en más de 1.000 puentes compuestos y compuertas en todo el mundo. “Originalmente nos unimos a Damen en este proyecto para construir una heliplataforma de 12 a 14 toneladas”, explica el gerente de operaciones de InfraCore, Laurent Morel. “Ahora estamos trabajando con ellos para construir las cubiertas, los mamparos y la estructura del casco. Usaremos infusión tanto horizontal como vertical para producir la sección del casco en un solo disparo. Hasta ahora, lo hemos infundido a una altura de 9,8 metros ". Una vez completado, este demostrador se probará para determinar su desempeño estructural y frente al fuego, y los resultados y las lecciones aprendidas se incorporarán a los nuevos módulos FTA de RAMSSES.
Mazos ligeros
Los materiales compuestos ya se demostraron en el primer portaaviones roll-on / roll-off que utiliza una plataforma de carga compuesta, diseñada y construida por Uljanik Group (Pula, Croacia) como parte del paquete de trabajo 14 de RAMSSES (ver “Bajo peso en el alto mares ”), así como un solárium ligero para un crucero fluvial de 110 metros de eslora (ver“ La cubierta compuesta reduce el calado de un barco fluvial ”) y una cubierta intermedia compuesta para un buque de carga general de 200 metros de eslora. "Una plataforma interpolada es una plataforma removible que puede instalar para dividir la bodega de carga para facilitar diferentes tipos de carga", explica Arnt Frode Brevik, gerente de Compocean (Sandvika, Noruega), un proveedor de soluciones compuestas que surgieron del petróleo y el gas. industria.
“Hemos estado trabajando con Oshima Shipbuilding (Nagasaki, Japón) y DNV GL durante varios años para desarrollar una plataforma de interpolación liviana con el objetivo de reducir el peso en un 50% en comparación con el acero”, dice Brevik. Esto resultó en un prototipo de PRFV de 9 por 2 metros que se probó para impacto y cargas máximas y luego se exhibió en NOR-Shipping 2017.
Compocean ha extendido este desarrollo a un nuevo proyecto con Oshima, DNV GL y el propietario del barco Masterbulk Pte Ltd. (Singapur) para construir un prototipo de cubierta de interpolación compuesta de 27 por 12 metros a gran escala, que se instalará el próximo año y probado hasta finales de 2021.
“Oshima buscaba optimizar los artículos para reducir los costos de combustible y manipulación”, dice Brevik. "Aunque no hay muchas cubiertas de interpolación por barco, es una parte fácil para empezar cuando se introducen nuevos materiales porque no forma parte de la estructura principal del barco". El diseño se basa en una placa de fibra de vidrio infundida con resina de poliéster con refuerzos de sombrero debajo. “Utilizamos una combinación de laminado de ± 45 grados, 0 grados y 0 grados / 90 grados para todas las piezas, pero en diferentes proporciones. La estructura de la plataforma también debe integrar muchos puntos de amarre para asegurar la carga ". La placa se adherirá a los refuerzos del sombrero con un adhesivo estructural, mientras que los pernos se utilizarán en combinación con el sistema de amarre. Un soporte de extremo de acero atornillado unirá el material compuesto a la estructura de acero del barco. “También buscaremos un diseño con juntas puramente adhesivas en el futuro”, agrega Brevik.

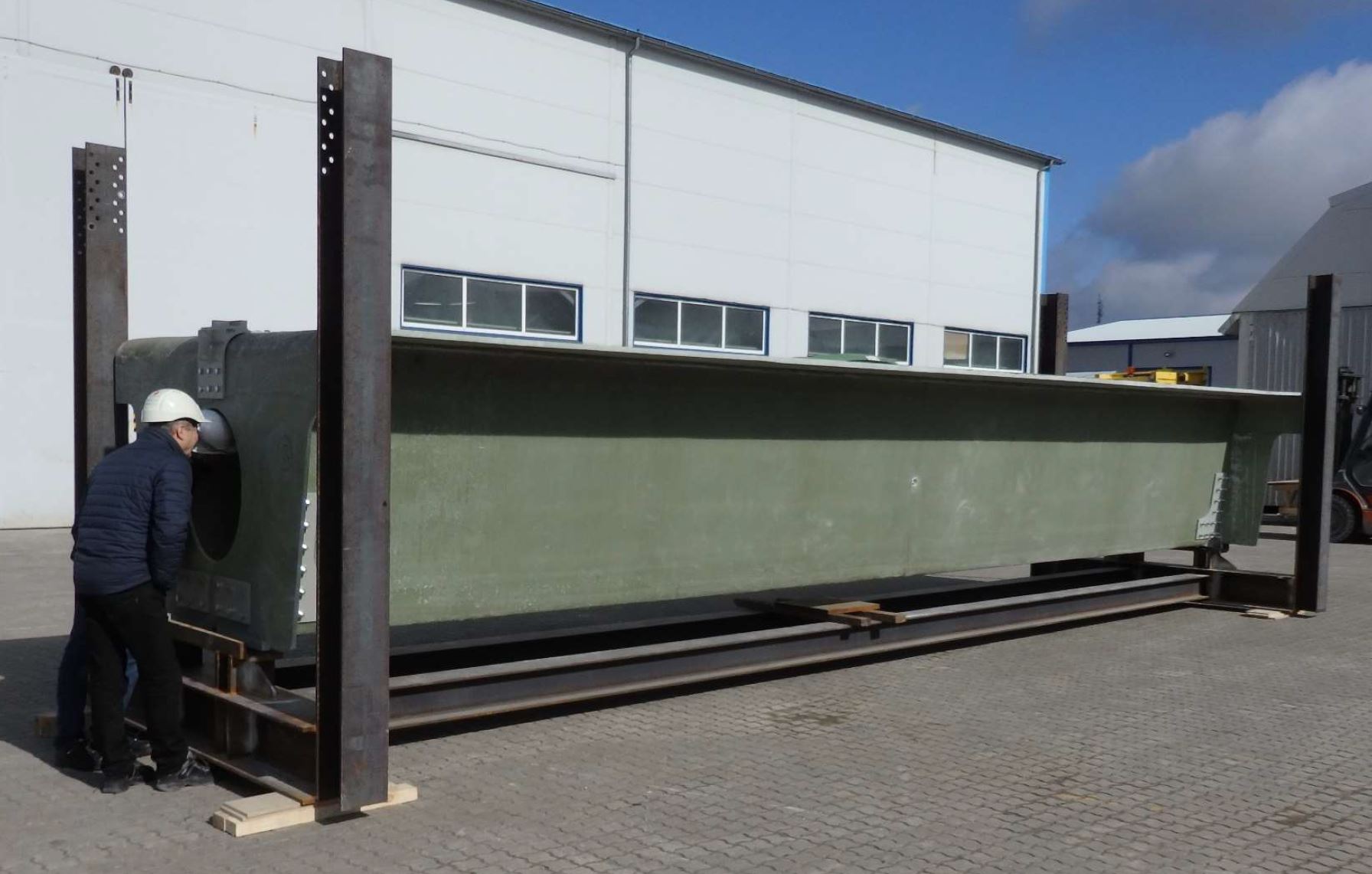
Fig. 2 plataforma de interpolación compuesta
El nuevo diseño de portaaviones de carga general de escotilla abierta 65k de Oshima Shipbuilding utilizará el prototipo de cubierta de interpolación compuesta de Compocean, que ahorra un 50% de peso en comparación con el acero y estará compuesta por múltiples refuerzos de sombrero de FRP infundidos (inserción) adheridos a una placa superior de FRP con conexiones atornilladas de el compuesto a la estructura del barco de acero. Fuente | Compocean y DNV GL
Habiendo recibido la aprobación final de DNV GL para el diseño de la plataforma de interpolación a gran escala, Compocean ha producido los moldes y ha comenzado las pruebas de fabricación. “La plataforma compuesta a gran escala será construida por un socio en Malasia que la transportará en barcaza hasta el barco”, dice Brevik. El siguiente paso es apuntar a una reducción de peso mucho mayor, por ejemplo, escotillas compuestas en la parte superior de las aberturas de carga (placas planas en la parte superior de las "cajas" verdes en el renderizado del barco arriba). "Hay siete grandes tapas de escotilla en este tipo de portaequipajes", señala. "Obtener la aprobación de DNV GL planteará nuevos desafíos, pero el éxito con la plataforma de interpolación ayudará".
Superestructura ligera, cabinas modulares
RAMSSES tiene seis paquetes de trabajo enfocados en superestructuras y componentes compuestos utilizados sobre la cubierta principal, la mayoría con demostradores y resultados de pruebas que se presentarán en 2020. El paquete de trabajo 16, dirigido por Naval Group (París, Francia), está demostrando un módulo de superestructura compuesto liviano unido a una plataforma de acero. El demostrador en tierra representa un bloque estándar para una embarcación tipo patrulla en alta mar. “La construcción naval en materiales metálicos se basa en la construcción en bloques para disminuir tiempos y costos”, explica Jurado. “La construcción de estos bloques con materiales compuestos presenta problemas con la necesidad de moldes grandes, así como técnicas de unión y requisitos de seguridad de las uniones. Fibreship ha estudiado esto y ha desarrollado algunas recomendaciones sobre la unión de bloques basados en compuestos, incluida la secuencia de ensamblaje ". En RAMSSES, Naval Group ha investigado tres tipos de estructuras tipo sándwich, incluido el núcleo de GF / poliéster / balsa, el núcleo de espuma FR epoxi / PET y el núcleo de espuma reforzada con fibra GF / poliéster / 3D. También está desarrollando un sistema de monitoreo de salud estructural (SHM) dentro de las juntas y los paneles compuestos.
El paquete de trabajo 18, dirigido por Chantiers de l'Atlantique (Saint Nazaire, Francia), está desarrollando una solución modular para cabinas de pasajeros. “Por lo general, vienen sin piso porque están soldados a las cubiertas de acero del barco”, dice Krause. “La idea es hacerlos a partir de materiales compuestos, equipados previamente con todos los sistemas auxiliares como calefacción y aire, eléctricos, etc. Al incluir un piso compuesto, estos podrían insertarse en una estructura de acero (como un cajón) en lugar de soldarlos en un cubierta de acero macizo, lo que ahorra mucho peso ". Aunque el proyecto está evaluando materiales compuestos para reducir el tiempo de producción y montaje de paredes, techos y unidades de baño, debido a que reemplazar la plataforma de acero ahorraría aproximadamente 125 kilogramos por metro cuadrado, los pisos compuestos son un enfoque principal. Hutchinson (París, Francia) ha propuesto utilizar su espuma compuesta reforzada con fibra mineral ZALTEX, que resiste temperaturas de -190 ° C a 1.000 ° C.
El paquete de trabajo 13, dirigido por el constructor de cruceros Meyer Werft (Papenburg, Alemania), también tiene como objetivo procesos eficientes de ensamblaje, pero dirigidos a mamparos. . El objetivo es construir dos demostradores, uno en tierra y otro en alta mar (prueba de mar), donde los muros compuestos se unirán a estructuras de armazón de acero y luego se someterán a 80 pruebas mecánicas. El socio del proyecto InfraCore ha realizado análisis para definir los requisitos de aislamiento térmico y acústico, frecuencia propia (vibración), deformación y anchura y altura máximas para muros compuestos. “Se nos ha pedido que desarrollemos paredes interiores y exteriores multifuncionales”, explica Morel en InfraCore. “Para ahorrar tiempo, costo y peso, debemos integrar aislamiento y un buen acabado interior con el panel estructural liviano. Hay hasta 6800 metros cuadrados de estas paredes en cada crucero. Tenemos una oportunidad para ponerlos a bordo de un crucero a mediados de 2020, que podrían ser los primeros muros compuestos aprobados por SOLAS en un crucero en todo el mundo ”.
En el paquete de trabajo 10, Podcomp (Öjebyn, Suecia) está desarrollando un panel alternativo para interiores y exteriores utilizando de base biológica compuestos que deben ser retardadores del fuego y tener un precio competitivo. Se examinaron tres conceptos de sándwich basados en GF / alcohol polifurfurílico (PFA) preimpregnado de Composites Evolution (Chesterfield, Reino Unido) y diferentes materiales centrales. Solo un concepto pasó las pruebas de calorímetro de cono y otras pruebas de fuego realizadas por los Institutos de Investigación RISE de Suecia (Borås). Ahora se está optimizando por peso y costo.
Después de probar el aluminio y la soldadura por fricción y agitación, Baltic Workboats (Nasva, Estonia) ahora está avanzando con materiales compuestos para desarrollar paneles rígidos preinstalados para la cubierta / superestructura de los barcos de trabajo de aluminio (paquete de trabajo 15). Se demostrará el diseño del panel, la conexión con otros paneles y con el resto de la estructura de la caseta, los procedimientos de análisis estructural y la solución de aislamiento, así como las técnicas de instalación a bordo.
BaltiCo (Hohen Luckow, Alemania), un productor de equipos para barcos, está desarrollando otra solución para la superestructura liviana que tiene una nueva puesta en marcha para construir embarcaciones completas utilizando fibra de carbono colocada por robots y envuelta alrededor de la estructura del truss. “Usted construye el esqueleto de la estructura que desea producir, colocando estructuras transversales o nervaduras de PRFV cada medio metro, y luego un robot enrolla fibra de carbono a su alrededor”, explica Krause. El objetivo es un sistema modular ultraligero que utiliza un proceso altamente automatizado. La demostración incluirá la producción y el montaje de dos módulos de cubierta y casco autoportantes en un catamarán ligero de energía solar que no es SOLAS.
Uniones soldadas de acero FRP
“Creemos que el futuro de la construcción naval está en combinar compuestos de FRP, acero y otros materiales en estructuras híbridas”, dice el Dr. Lars Molter, un veterano de 10 años en CMT. “Analizamos la unión, pero no existe un diseño de junta estandarizado que se pueda usar en todos los barcos y no existen reglas generales sobre cómo aplicar la unión adhesiva en los buques SOLAS. Además, debe controlar el medio ambiente y el proceso de vinculación ". Señala que esto es difícil en medio de la soldadura y el corte que típicamente domina la construcción de astilleros. “Le preguntamos a DNV GL qué aprobarían para juntas de materiales diferentes”, dice Molter. “Dijeron que la estructura primaria normalmente requeriría un accesorio mecánico; la unión pura no se certificaría fácilmente sin sujetadores redundantes ”.
Molter y CMT respondieron con el proyecto FAUSST (junta estándar de fibra y acero), financiado por Alemania, que desarrolló un tejido de punto híbrido que pasa de 100% fibras de vidrio a 100% fibras de acero. Este último se suelda a un conector de acero (p. Ej., Placa plana, perfil rectangular, etc.), que luego se puede soldar fácilmente en la estructura de acero de un barco (Fig. 3). El extremo de fibra de vidrio se une a la estructura compuesta mediante infusión de resina. “Este diseño de junta ofrece una inspección 100% NDT porque puede usar UT (ultrasonido) o rayos X en la soldadura”, dice Molter. FAUSST realizó ensayos mecánicos, ambientales y de fatiga en este tipo de juntas y también obtuvo la aprobación en principio de las sociedades de clasificación, pero aún quedaba mucho por hacer para transformar la tecnología en un producto comercial. Por lo tanto, Molter dejó CMT y fundó HYCONNECT GmbH (Hamburgo, Alemania) en 2018.
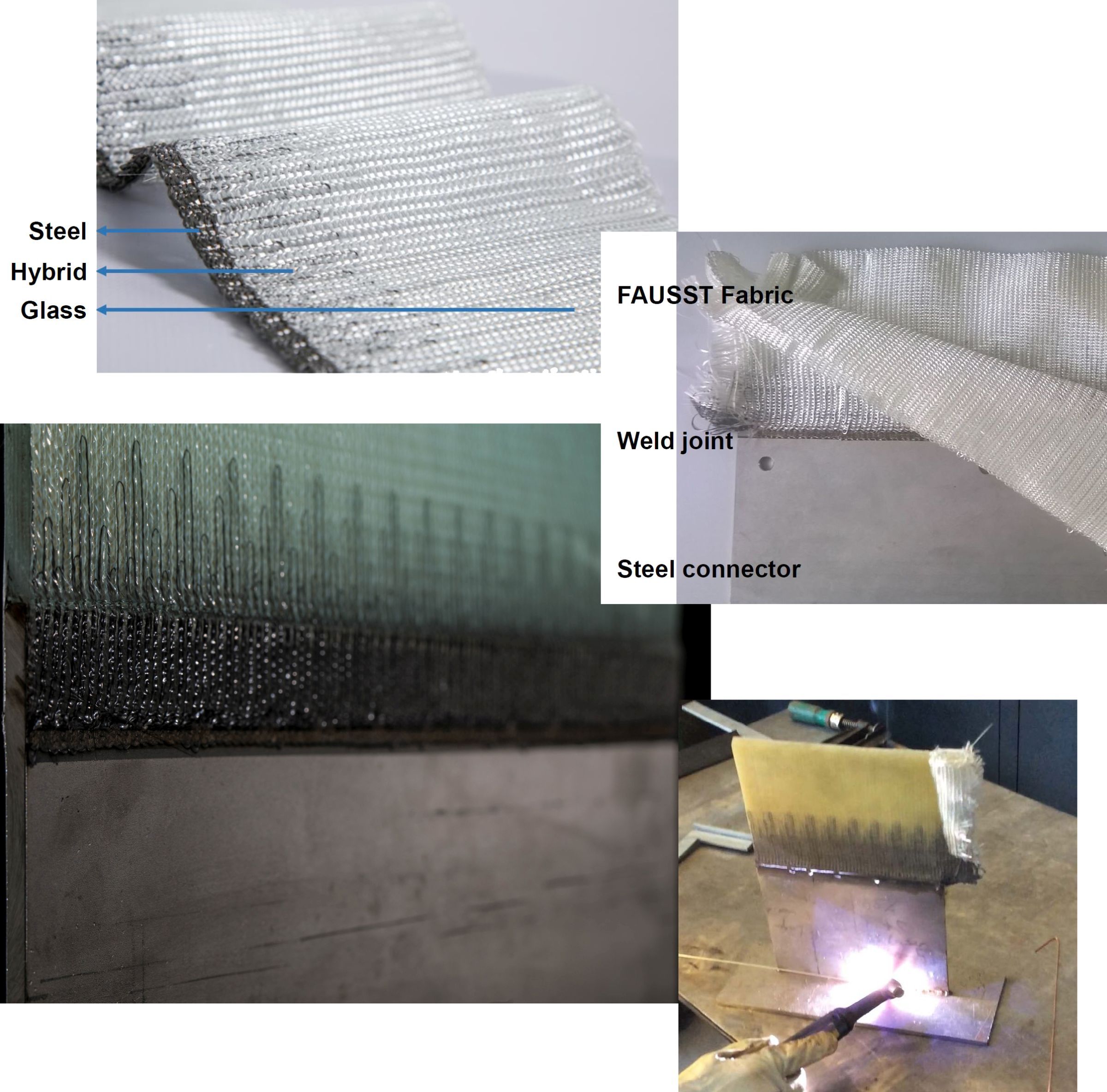
Fig. 3 Junta soldada acero-FRP HYCONNECT
Tejido híbrido de fibra de vidrio y acero FAUSST (arriba a la izquierda) está soldado a presión a una placa de acero u otro conector (arriba a la derecha) y luego se puede integrar en una estructura compuesta mediante infusión de resina (abajo a la izquierda) . Estas estructuras compuestas híbridas luego se sueldan fácilmente en la estructura de acero del barco (abajo a la derecha) .
Fuente | HYCONNECT
“Nos hemos reunido con los astilleros, DNV GL y BV y estamos desarrollando un producto que puede certificarse”, dice Molter. “Simplemente pida sus piezas compuestas con este sistema de unión y luego podrá soldarlas en su barco. Ésa es nuestra visión. Diseñamos la unión de material compuesto a acero y luego entregamos un producto que tiene una tela soldada a un conector de acero (placa, perfil, etc.) ”.
Explica que el diseño de la junta y el tejido se certificarán en un sistema escalonado:"Al aplicar más capas de tejido FAUSST, hay un aumento lineal en la capacidad de carga". Por ejemplo, el producto base podría ser cuatro capas de FAUSST con una barra plana de 1 metro soldada a ella, clasificada para una determinada carga de tracción y flexión. Then there would be some products available to the left (e.g., two-three layers total for a lower load rating) and right (e.g., six layers total for a higher load rating). “We are still finalizing these details, but the goal is a standardized and easy-to-use system,” notes Molter.
HYCONNECT has adapted the fabric technology to handle the difference in stiffness and coefficient of thermal expansion (CTE) between steel and composites; the use of knitted fibers for mechanical interlocking with unidirectional fibers for carrying load through the joint; and the technique required for high-quality press welding of the steel fibers to the steel connector (see "Connecting composites to steel”). “This solution is based on continuous testing,” says Molter. “Because FAUSST consists of standardized ready-made sub-products, it can be supplied quickly, within days.” Prototypes are currently being produced for selected customers, and HYCONNECT will begin full production in 2020.
Composite rudders
Ship rudders are also being developed as FRP-steel hybrids. As part of RAMSSES work package 12, Becker Marine Systems (BMS, Hamburg, Germany) is demonstrating a lightweight composite flap for a steel rudder designed for large container ships. Such rudders typically weigh more than 200 tons, says Jörg Mehldau, head of R&D at BMS. “By adding a hinged aft flap, you can significantly reduce the rudder area.” BMS pioneered this flap rudder, which dramatically reduces ship turning radius and improves course-keeping and maneuverability, enabling berthing without tugboat assistance. A composite flap not only reduces weight but also enables more functional shapes as well as more hydrodynamically- and load-optimized designs.
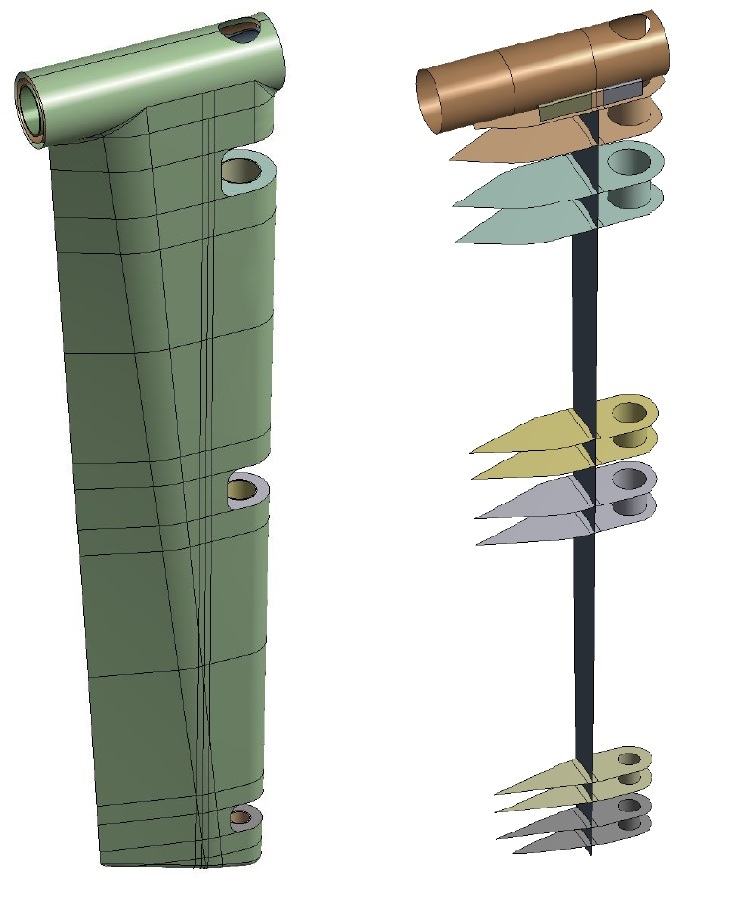
Fig. 4 Composite rudder flap
Becker Marine Systems is working with InfraCore to develop a lightweight, resin-infused rudder flap for the largest container ships. Measuring 11.8 meters long and 0.9 meter wide with a 2.9 meter chord, the full-scale flap must withstand 100 tons/m
2
of load. A 2-meter high demo will be tested 2Q 2020. Source| Becker Marine Systems
“The composite flap we are developing was inspired by the aviation industry,” notes Mehldau. For RAMSSES, the full-scale test case is aimed at one of the largest container ships (≈400 meters long), a flap measuring 11.8 longmeters and 0.9 meters wide with a chord of 2.9 meters (see Fig. 4). “We calculated the forces on this rudder and flap using formulas based on DNV GL rules for this ship’s type, weight and maximum speed,” says Mehldau. BMS then conducted preliminary design and engineering analysis, as well as trade studies for manufacturability and cost. “We first favored filament winding but it was too expensive,” he notes. “For each new ship hull, the rudder is a single design.” Thus, resin infusion was chosen, as was an alternative design from InfraCore. “It was the best for production flexibility, cost and structural performance combined,” Mehldau explains.
“To me, this was a natural fit for InfraCore because the composite lock gates we have built are very similar,” says Morel. He notes container ship rudders must withstand loads of roughly 100 tons per square meter with a surface area of 150 square meters. This matches well with InfraCore’s infusion-based technology used in bridge decks spanning up to 142 meters. Instead of bonding a high-density structural core to faceskins, InfraCore uses a low-density foam core only as a permanent formwork for multiple Z-shaped, two-flanged web structures. These are overlapped, faced with multiaxial fabrics and co-infused to form a robust construction. InfraCore will build a 1:6 scale demonstrator, using glass fiber and polyester resin materials already certified by DNV GL to keep costs low.
Morel notes that the reduced-weight InfraCore composite flap is cost-competitive, “because steel ship rudders are quite complicated to manufacture.” Mehldau agrees, “together with less maintenance and operational cost advantages, we see a successful business case.” The 2-meter -high demonstrator will be finished by 2Q 2020, followed by testing.
“We will test this using a lab test bench and air cushions, which can apply up to 8 bar of pressure equal to at least 80 Mpa of load,” says Mehldau. “We will measure strains and deflections to verify our simulations and perform a break load test.” A lab-scale demonstrator will also be tested via sea trials on a research ship in the Elbe River by CETENA (Genoa, Italy) which serves as project coordinator for RAMSSES along with CMT.
Forward momentum
“The outlook for composites in ships is good because many of the marine sector stakeholders have shown interest in FIBRESHIP, RAMSSES and other projects,” says Jurado. “The largest challenges are the need for new regulations, fire safety aspects, bonding techniques and reduction of shipbuilding costs.” For the latter, he cites automated manufacturing in shipyards as a key issue as well as mold construction and composite materials sourcing and storage. “Composites are already growing in ships,” says Krause at CMT, “but we started this work 20 years ago, so it is a slow process. However, we now have this critical mass and the industry is more connected via E-LASS.”
Jörg Bünker, head of R&D, application service for SAERTEX LEO FR products at SAERTEX (Saerbeck, Germany), agrees:“The drivers to reduce weight are strengthening. Within the next five to seven years, more composite materials will be sold into ships. This is the right time for more projects because IMO needs to see this interest and effort from the industry. Suppliers must show new solutions and shipyards must show where composites can be used, but no one can do it alone.”
Resina
- Enviar en una botella
- Accesorios de ensamblaje de impresión 3D con compuestos Markforged
- Reciclaje:compuestos termoplásticos reforzados con fibra continua con policarbonato reciclado
- Cómo la tecnología móvil está eliminando las barreras para viajar
- TxV Aero Composites cumple con los estándares AS9100
- Mikrosam automatiza los compuestos termoplásticos con el sistema de colocación de múltiples robots sin herramientas
- Hexcel se asocia con Lavoisier Composites, Arkema
- Fabricación continua de fibra (CFM) con compuestos moi
- Cumbre de peso ligero:Orientación a oportunidades de sistemas de propulsión automáticos compuestos
- Ashland se asocia con Velox para la distribución de materiales compuestos en Francia
- Compuestos de impresión 3D con fibra continua