Sensores dieléctricos de CC para la producción de compuestos industriales
A medida que los fabricantes buscan simultáneamente reducir el costo y aumentar la tasa de producción de piezas compuestas, la capacidad de ver los procesos de moldeo en el interior en tiempo real y monitorear el flujo de resina, viscosidad, temperatura, presión y Tg / estado de curado se convierte en un diferenciador. Synthesites (Uccle, Bélgica) ha desarrollado esta capacidad. Según los resultados informados por el Centro Aeroespacial Alemán (DLR, Stade) y el Centro Nacional de Compuestos (NCC, Bristol, Reino Unido), esta tecnología tiene el potencial de reducir los tiempos de ciclo hasta en un 50%, con decisiones de curación basadas en Tg y grado. de curado por resina y pieza frente a períodos de tiempo conservadores basados en estudios de materiales genéricos. De hecho, es un avance hacia la producción de Composites 4.0, utilizando datos de sensores para controlar procesos y equipos, y también para mejorar la simulación y el diseño.
Informé por primera vez sobre Synthesites a través del proyecto OPTO-Light (consulte "Termoplásticos sobremoldeados termoestables , Ciclo de 2 minutos, una celda ”). De hecho, la capacidad de unir termoplásticos a termoendurecibles en OPTO-Light sin Las superficies sometidas a ablación con láser se hicieron posibles mediante el uso de sensores en el molde para presión, temperatura, resistividad de corriente continua (DCR) y análisis dieléctrico (DEA). Los sensores DCR fueron suministrados por Synthesites y los de DEA fueron suministrados por Netzsch (Selb, Alemania). Ambos son sensores dieléctricos que miden las propiedades eléctricas de la resina. Discutiré la historia y las diferencias en estas tecnologías a continuación.
La tecnología que Synthesites ha desarrollado con una variedad de clientes comerciales es impresionante, incluida la producción industrial de palas eólicas y las alas con resina infundida para la Serie C, ahora Airbus 220. También se ha demostrado para una variedad de materiales y procesos, incluido el autoclave. preimpregnado curado, infusión de resina y moldeo por transferencia de resina a alta presión (HP-RTM).

- La disminución inicial de la resistividad refleja la disminución de la viscosidad de la resina durante la rampa a ≈120 ° C.
- Durante esta permanencia a 120 ° C, la resistividad aumenta a medida que aumenta la viscosidad de la resina debido a la reacción de la resina y la pérdida de volátiles.
- La resistividad vuelve a disminuir y alcanza un mínimo cuando la resina se calienta a 177 ° C.
- La resistividad aumenta rápidamente a medida que la reacción de curado avanza rápidamente.
- El aumento de la resistividad se ralentiza a medida que la reacción de curado se ralentiza, acercándose a una pendiente cero después de 300 minutos a medida que la reacción de curado se acerca a su finalización.
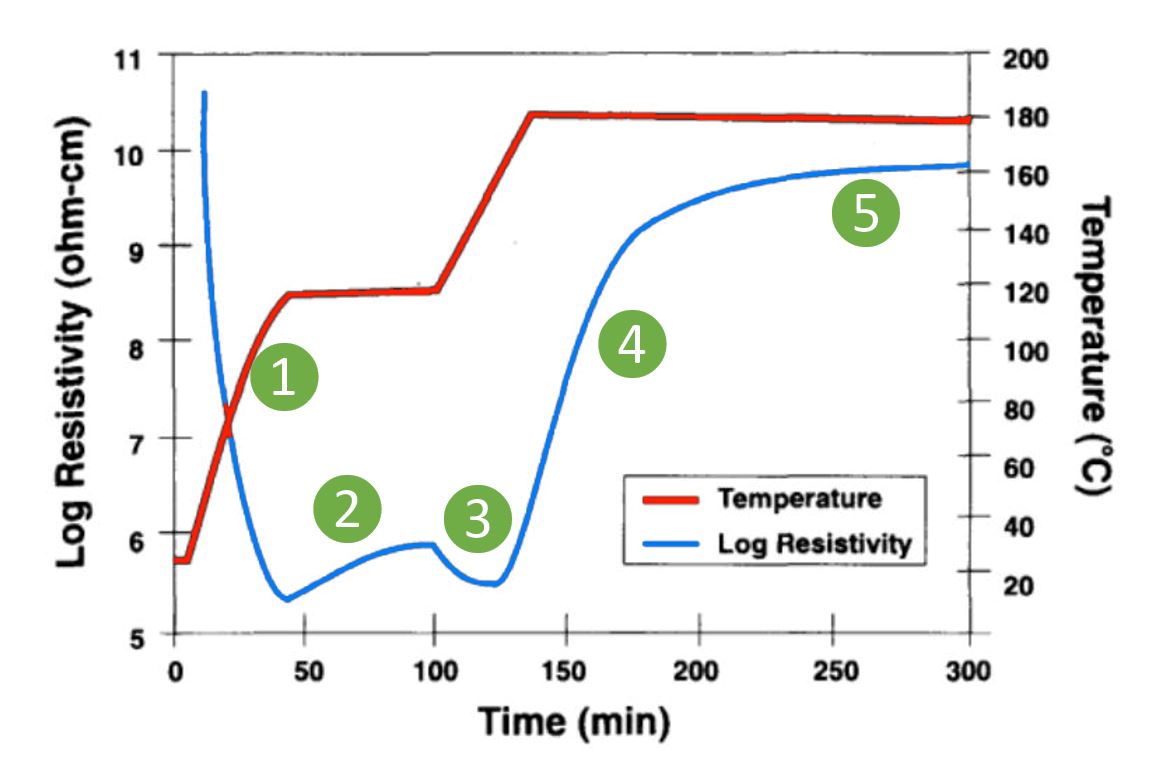
FUENTE | Caracterización no destructiva de materiales VIII editado por Robert E. Green, p. 385.
La conductividad iónica está inversamente relacionada con la viscosidad de la resina antes de la gelificación y con la rigidez después de la gelificación (alta movilidad iónica, baja viscosidad de la resina y baja rigidez). La inversa de la conductividad iónica, la resistividad, está directamente relacionada con los cambios de viscosidad / rigidez en la resina de la matriz.
Se ha demostrado que el aumento de resistividad se correlaciona con el aumento de Tg. Esta es la base de la resistividad de corriente continua (DCR), que es solo DEA usando corriente continua (DC), y la descripción que se dio inicialmente al proceso desarrollado por Synthesites.
Como se explicó anteriormente, esta técnica de usar voltaje CC para DEA se basa en correlaciones entre resistividad y estado de curado. Estos fueron reportados en 1962 por R.W. Warfield en "Propiedades de polímeros reticulados como lo demuestran las mediciones de resistividad eléctrica", Makromoleculare Chemistry, Vol. 58. (Consulte la parte inferior de las referencias utilizadas en esta sección).
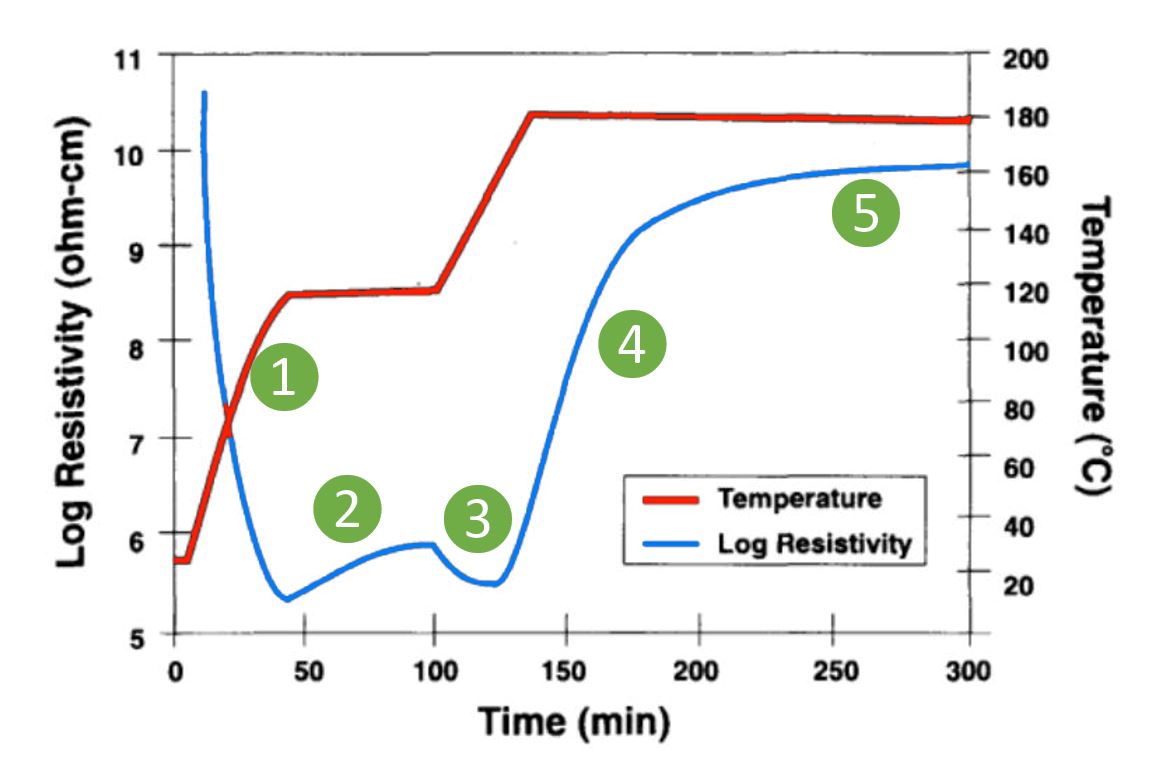
Historial de sensores DEA y CA vs. CC
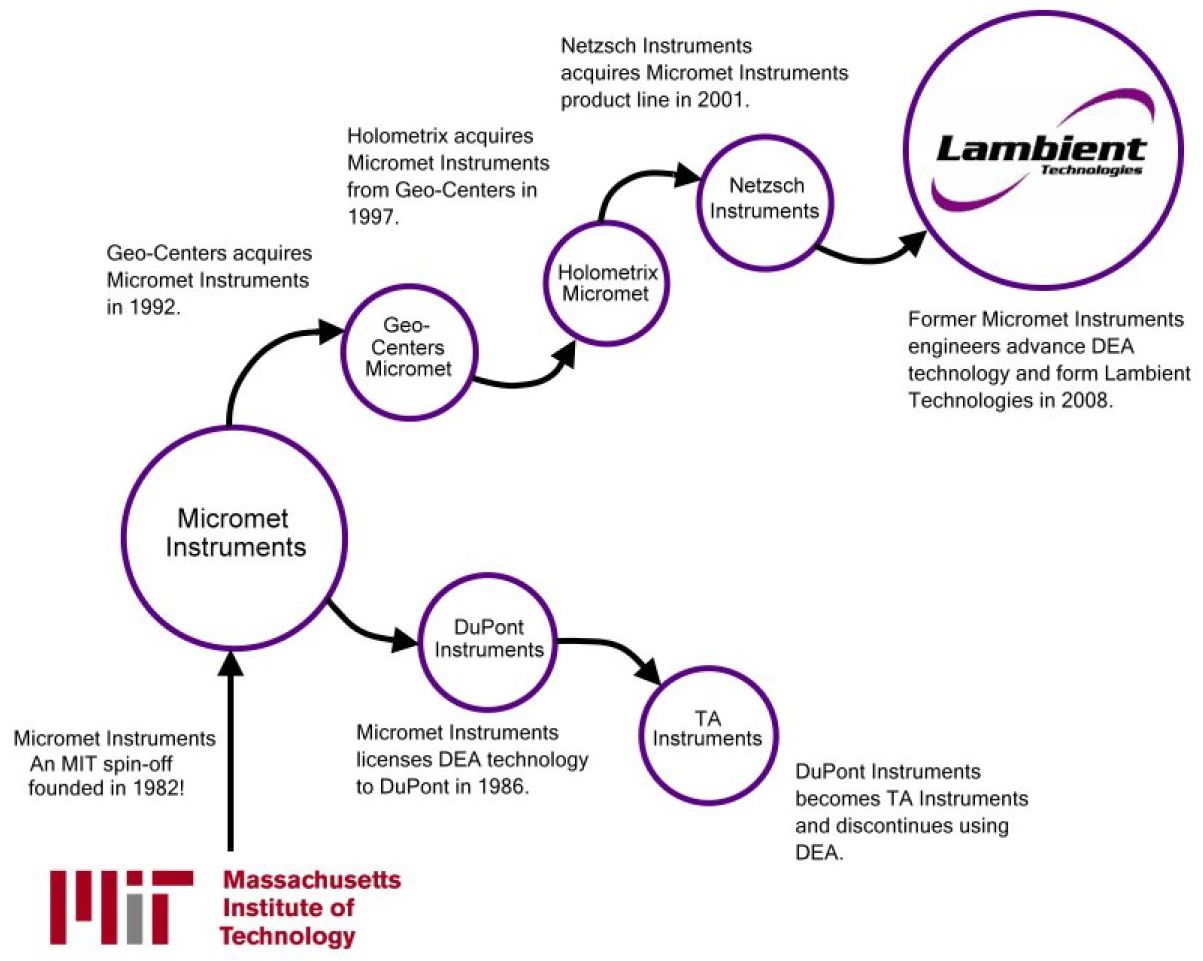
"La idea de la monitorización de la curación es bastante antigua", explica el Dr. Nikos Pantelelis, director de Synthesites. “En la década de 1980, el método de detección dieléctrica se consideraba más maduro que otros, como las fibras ópticas. MIT (Instituto de Tecnología de Massachusetts) trabajó en él e intentó implementarlo en producción. Esta tecnología es lo que Netzsch compró y utiliza hoy ".
Synthesites se estableció en 2008. “Desarrollamos nuestra tecnología desde cero utilizando sensores eléctricos con corriente continua, no con corriente alterna”, relata Pantelelis. “Para nosotros, el inconveniente de usar sensores dieléctricos de CA convencionales es el requisito de excitar la resina en un rango de frecuencias y luego medir la respuesta de impedancia para varias señales. No solo es un desafío procesar todos estos datos, sino que a medida que la resina cambia de líquida a sólida, debe concentrarse en diferentes frecuencias de señal para obtener la información correcta ".
Pantelelis dice que los sensores de CC Synthesites pueden medir una conductividad muy baja y una resistividad alta, "que es necesaria para medir la transformación de las resinas durante el curado". Afirma que el uso de DEA convencional en una sola frecuencia para simplificarlo no proporciona datos precisos. “No tenemos múltiples frecuencias, simplemente aplicamos un voltaje constante. La desventaja es que este enfoque es muy limitado, lo que significa que funciona bien para aplicaciones muy específicas, como el curado de resina, pero no para todo. Sin embargo, al comparar el rendimiento de nuestro equipo con el DEA convencional, el nuestro puede medir todo el rango de curado incluso a temperaturas más bajas. A las empresas que suministran instrumentos y servicios fuera de los compuestos no les gusta nuestro enfoque porque tiene parámetros limitados para ajustar ".
Esto no es un problema para Synthesites porque se ha dirigido específicamente a compuestos. "Nuestro enfoque funciona bien en una amplia gama de resinas compuestas y procesos, incluidos los termoestables, RTM, preimpregnados e incluso termoplásticos reactivos como Elium". (Elio es el termoplástico de baja viscosidad de Arkema (Colombes, Francia) que se puede procesar mediante infusión de resina).
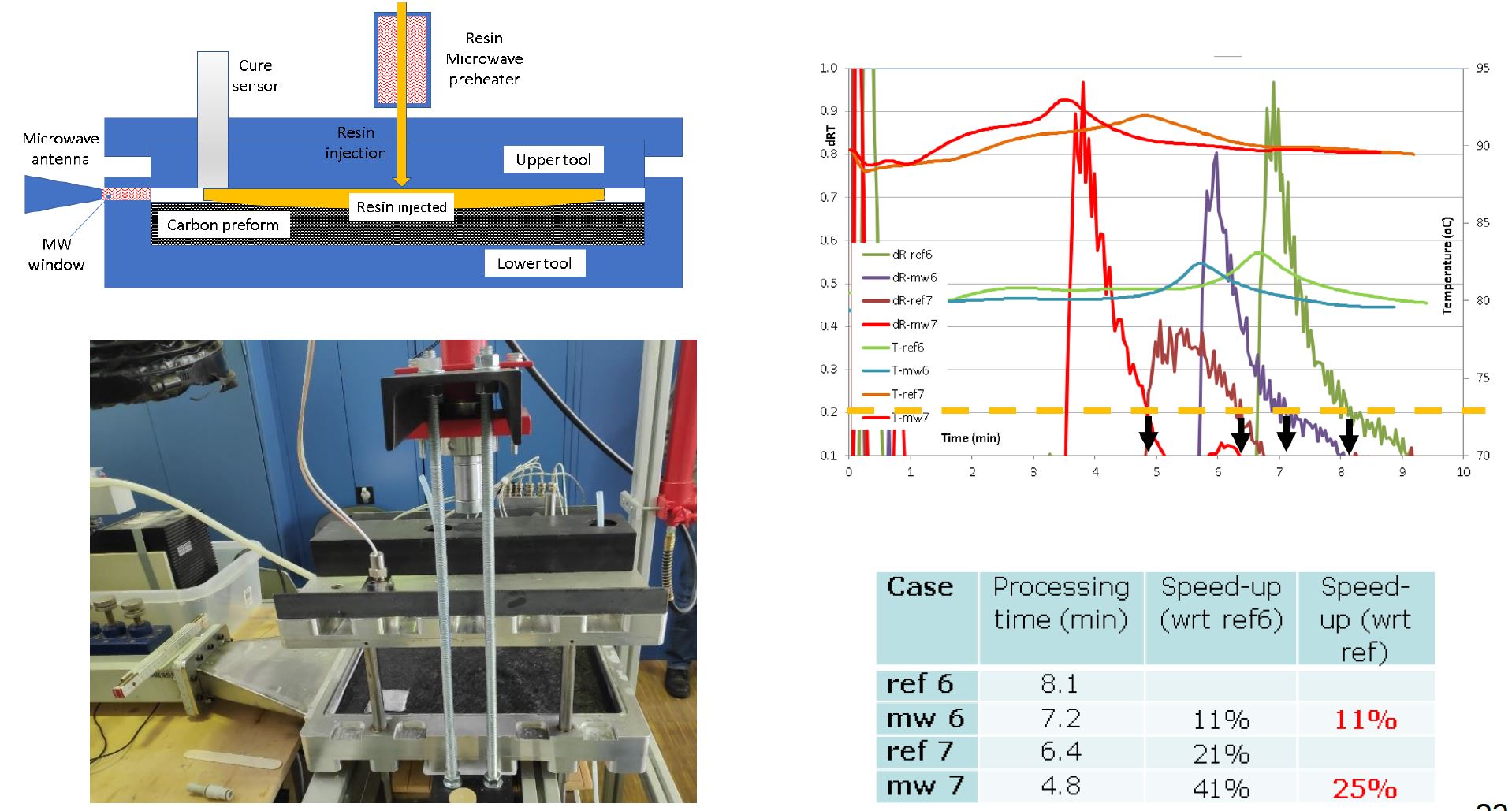
Si la DEA que usaba CC se conocía en la década de 1960, ¿por qué se favorecieron los sensores de CA en la década de 1980 y siguieron adelante? “Hace treinta años, la tecnología para DEA que usaba sensores de CC no estaba tan desarrollada”, señala Pantelelis. “Pero hemos avanzado nuestro enfoque para ofrecer mediciones muy fluidas y precisas para la producción industrial. Hemos demostrado y seguido desarrollando nuestros sistemas con clientes como GE Aviation (Batesville y Ellisville, Miss., EE. UU.) Y Bombardier, que procesan piezas grandes con moldeo de resina líquida. Nuestros sistemas también se utilizan todos los días en la producción de palas eólicas y han demostrado su capacidad para la producción industrial de laminados preimpregnados curados en autoclave ”.
Control de proceso
Pantelelis explica cómo los sensores de CC Synthesites son solo una parte de un sistema integrado para monitorear el procesamiento y curado de compuestos. “Medimos directamente la resistencia y la temperatura, y a partir de esto calculamos en línea la viscosidad, el grado de gelificación y el grado de curado. Utilizamos sensores duraderos en el molde, pero también sensores de compuerta y sensores en línea para entradas, salidas y líneas de alimentación de resina, así como sensores desechables en las piezas. Utiliza los sensores solo donde los necesita ".
Los sensores de temperatura son detectores de temperatura de resistencia de platino (RTD), que ofrecen una precisión mucho mayor (dentro de 0,1 ° C) que los termopares, así como estabilidad durante años frente a la deriva de medición posible con termopares. Los RTD son equipos estándar en muchas aplicaciones industriales. Los sensores de compuerta (consulte el diagrama de control del proceso a continuación) son binarios y notifican el flujo de resina como encendido o apagado, aunque hay una segunda versión que también puede informar la viscosidad. Synthesites ha desarrollado sensores para usar con fibra de carbono sin riesgo de corrosión galvánica, sensores que se pueden usar a través de una bolsa de vacío y sensores moldeados en el molde para adaptarse a la geometría del molde.
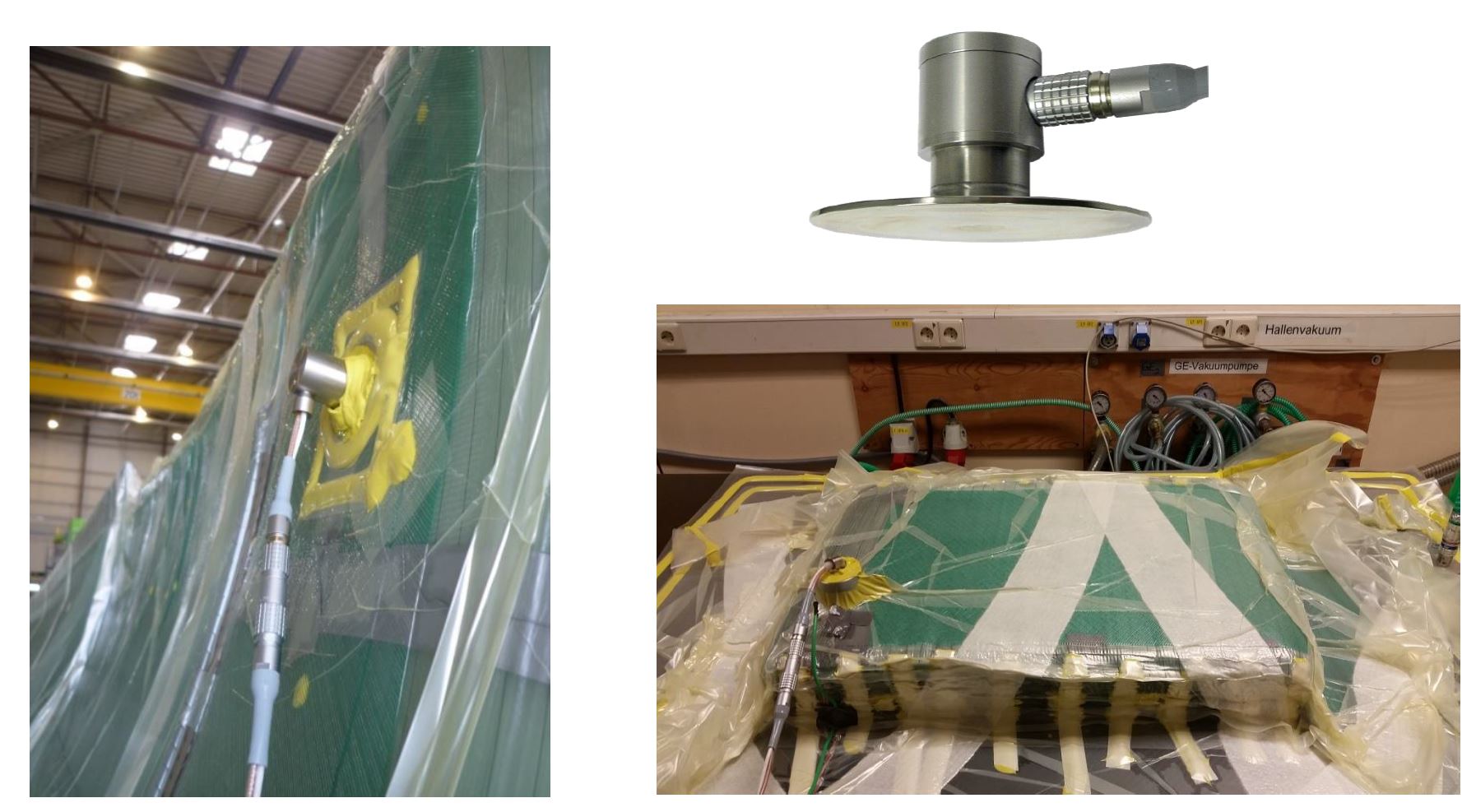
Los siguientes componentes son las unidades de adquisición de datos OPTIFLOW y OPTIMOLD. OPTIFLOW proporciona un control in situ en tiempo real de la llegada de la resina y la temperatura para el moldeo de compuestos líquidos. Verifica y registra el flujo de resina y puede identificar desviaciones de producción durante la infiltración de resina. OPTIMOLD utiliza mediciones de temperatura y resistencia de la resina para realizar cálculos y controlar el estado de la resina, incluida la proporción de mezcla, el envejecimiento químico, la viscosidad, la Tg y el grado de curado. Se puede utilizar con procesos de preimpregnado y moldeado líquido.
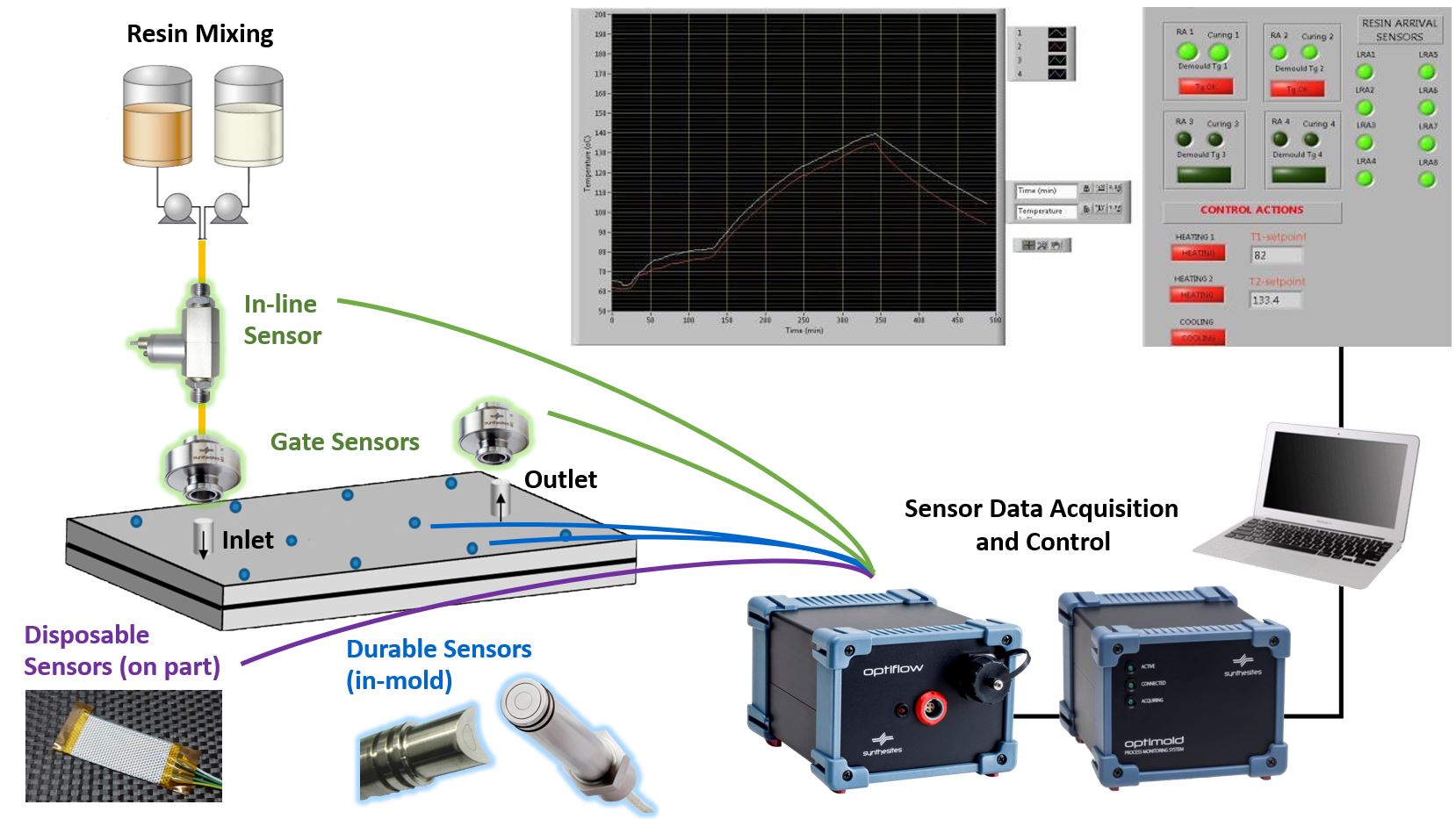
Las unidades OPTIFLOW y OPTIMOLD están controladas por el software OPTIVIEW. “Este software proporciona adquisición y almacenamiento de datos y se proporciona de forma gratuita con nuestro equipo”, explica Pantelelis. “También ofrecemos el software Online Resin State (ORS), una opción más avanzada que los clientes pueden adquirir de forma adicional. Recopila entradas, realiza cálculos en línea y envía resultados para el control inteligente del proceso ”.
Tanto los sistemas OPTIFLOW como OPTIMOLD verifican continuamente para asegurarse de que los sensores estén conectados y las lecturas estén dentro del rango. “Cuando confía en estos sensores para el control del proceso, es imperativo que los sistemas activen la alarma si un sensor no está funcionando o si sus lecturas están más allá de los límites prescritos”, dice Pantelelis. Ambos sistemas también tienen salidas de relé para controlar equipos de proceso. Por ejemplo, las válvulas de la línea de alimentación se pueden abrir o cerrar en función de los datos de llegada de la resina, y el equipo de calefacción / refrigeración se puede gestionar según la viscosidad de la resina. "Puede alimentar la salida de los sensores de presión en OPTIMOLD", señala Pantelelis, "y así controlar la presión en el molde en función de los datos de viscosidad".
Medidas y curvas de datos típicas
Las capturas de pantalla a continuación muestran las mediciones de OPTIMOLD de ensayos de RTM de compresión de alta presión (HP-CRTM) en NCC (Bristol, Reino Unido). El primer conjunto, de una prueba simple a 115 ° C, muestra cómo las mediciones en tiempo real de la resistencia eléctrica y la temperatura de la resina se convierten en viscosidad y Tg estimadas por el software ORS.
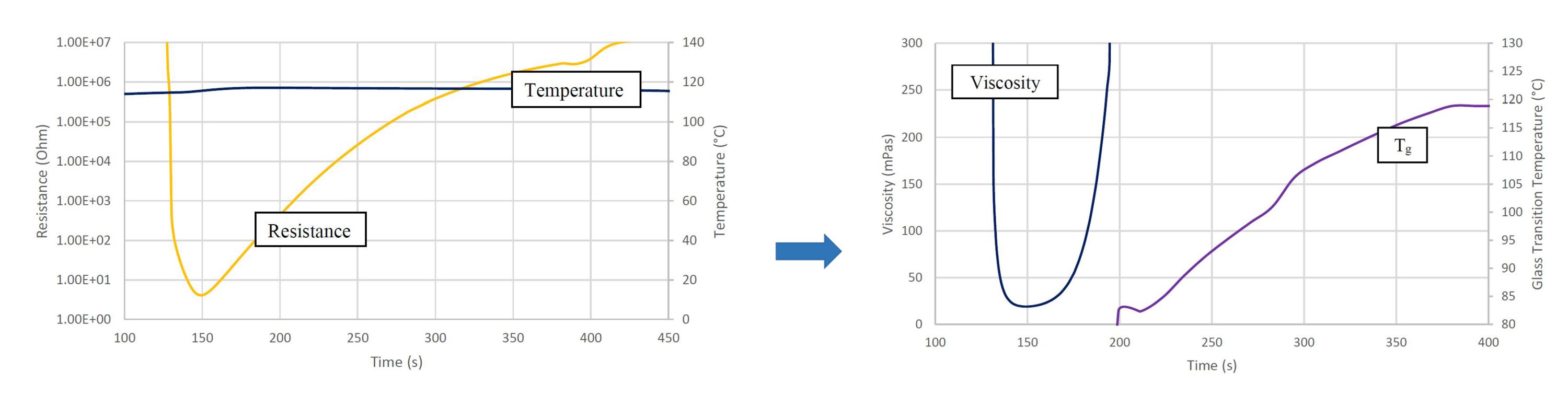
En los gráficos siguientes, la resistencia eléctrica y la temperatura (gráficos superiores) se registraron a 110 ° (izquierda) y 120 ° C (derecha). Debajo de las lecturas de resistencia (R) y temperatura (T) están los gráficos que muestran la viscosidad calculada y la Tg a 110 ° C (izquierda) y 120 ° C (derecha) . Estas medidas fueron de dos sensores OPTIMOLD ubicados en la mitad superior del molde (Sn.1 y Sn.2, foto inferior ) mientras que la presión de la cavidad se registró utilizando dos sensores de presión Kistler 6162A (Sn.3 y Sn.4).
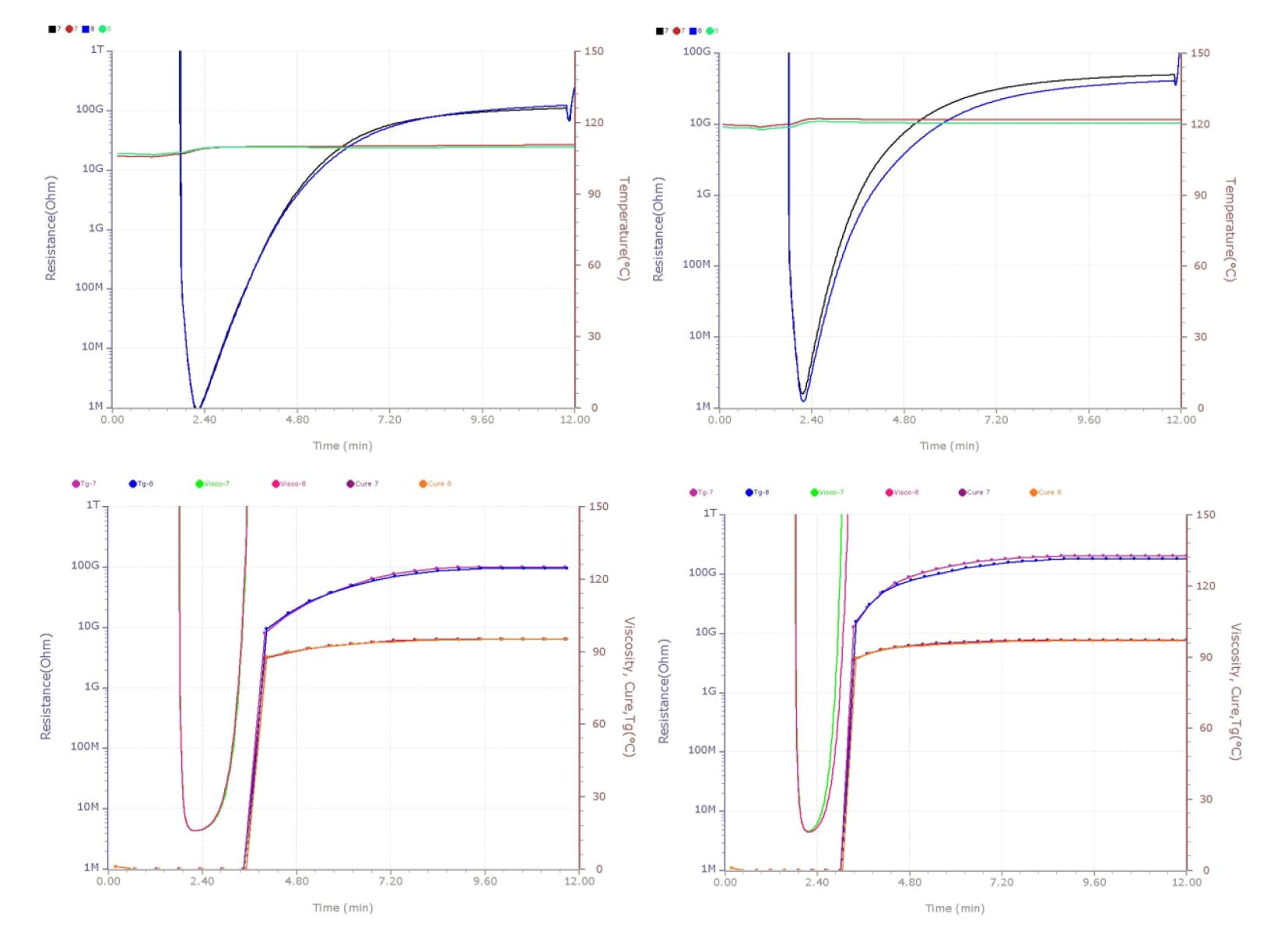
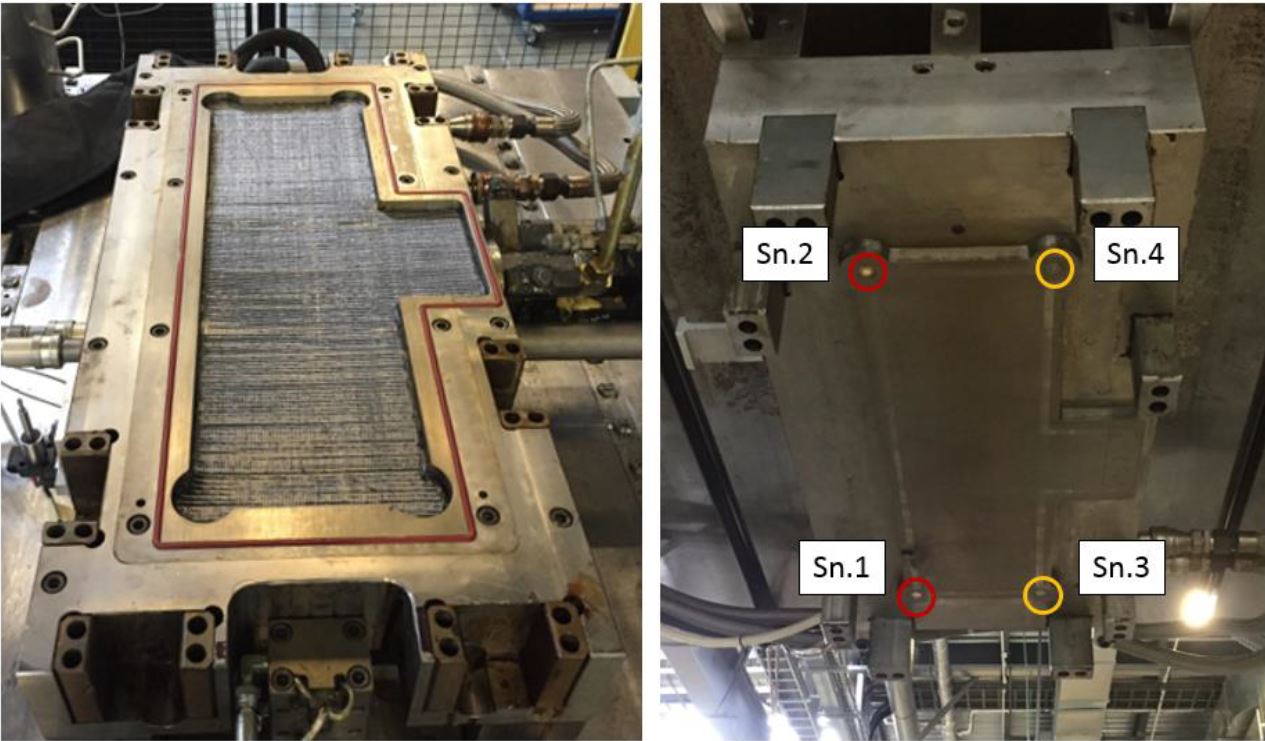
Todos los datos registrados por los sensores en el molde, así como la prensa y el equipo de inyección se pueden recopilar en un solo archivo de registro, lo que permite una imagen detallada del proceso de fabricación de cada componente creado.
Reducción del tiempo de curado
“Tenemos el potencial de reducir el tiempo de curado en más de un 30% porque el fabricante puede ver la Tg en tiempo real, por lo que pueden decidir cuándo detener el ciclo de curado”, explica Pantelelis. “No tienen que esperar para completar un ciclo heredado más largo de lo necesario. Por ejemplo, el ciclo heredado de RTM6 es de 2 horas a 180 ° C para un curado completo. Hemos visto que en ciertas geometrías esto puede reducirse a 70 minutos ".
Entonces, ¿el objetivo es detener el proceso una vez que se complete la cura? "No se trata de un curado completo, sino de alcanzar el nivel de curado que necesita cada componente", dice Pantelelis. “La curación completa lleva demasiado tiempo. La clave es poder ver cuándo se alcanza la curación suficiente. Los fabricantes de palas de viento tienen un objetivo de Tg. Cuando alcanzan eso, pueden comenzar a enfriarse. Por lo tanto, se necesita un sensor que pueda proporcionar mediciones muy precisas de Tg en tiempo real ”.
Synthesites completó un proyecto de demostración con Hutchinson (París, Francia) para producir una cuchilla de suspensión automotriz hecha con fibra de vidrio / epoxi y RTM para el proyecto ECOMISE financiado con fondos europeos (Habilitación de la fabricación de COmposite de próxima generación mediante evaluación estructural in situ y ajuste de procesos, 2013). -2016). El objetivo de este proyecto era optimizar el ciclo RTM basado en el monitoreo de procesos en tiempo real:
- La primera rampa de calentamiento se activará al completar la infiltración de resina basada en sensores.
- La segunda rampa de calentamiento se activará al completar el curado según el cálculo de Tg.
- El enfriamiento se activará al completar el poscurado según el cálculo de Tg.
El sistema Synthesites constaba de dos (2) en molde sensores de curado (CS1, CS2), uno (1) en molde sensor de temperatura y flujo de resina (sensor de flujo 1) y ocho (8) desechables sensores de flujo / temperatura de resina:cuatro (4) incrustados en la pieza de prueba y cuatro (4) unidos a la superficie de la herramienta.
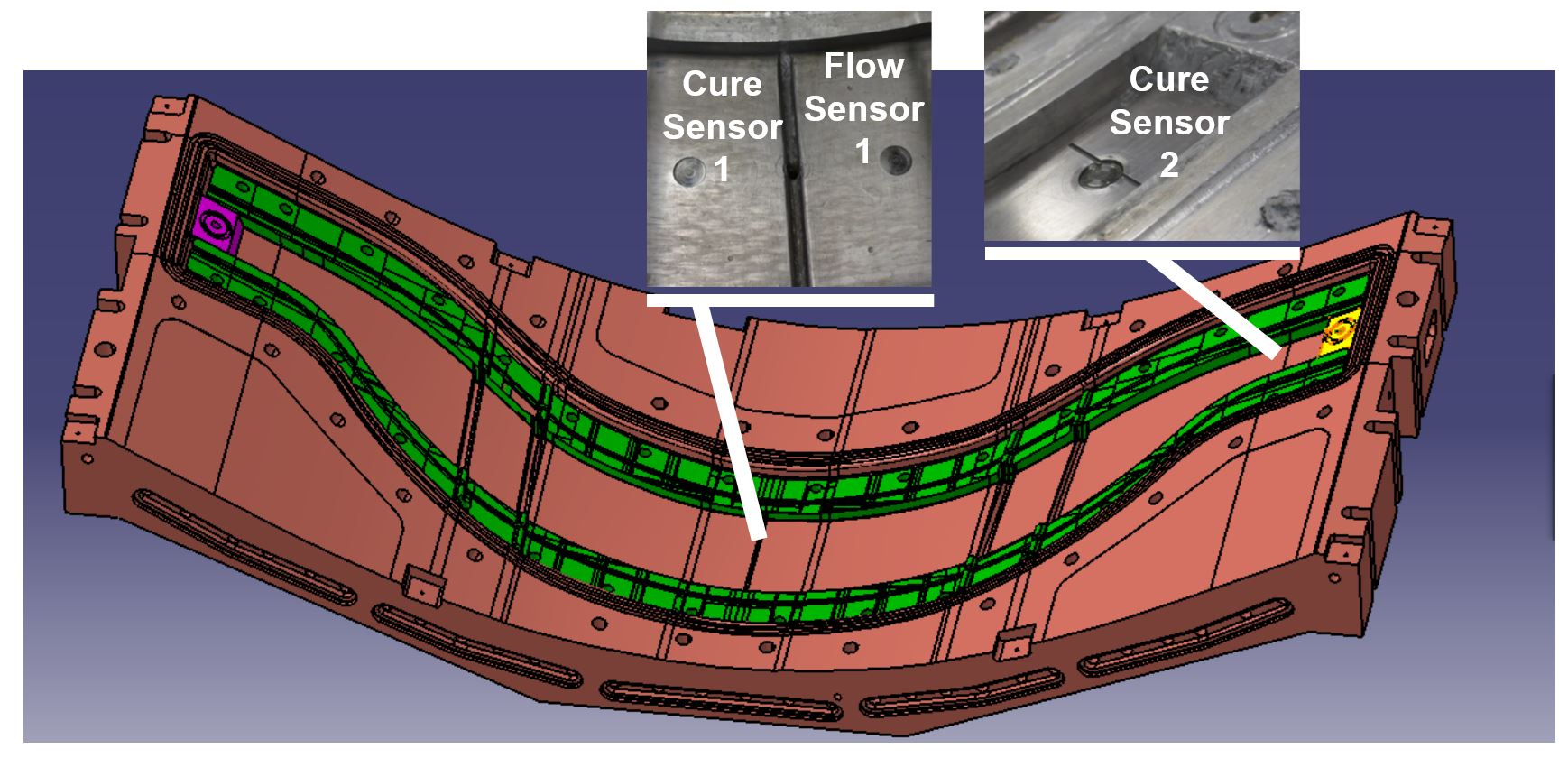
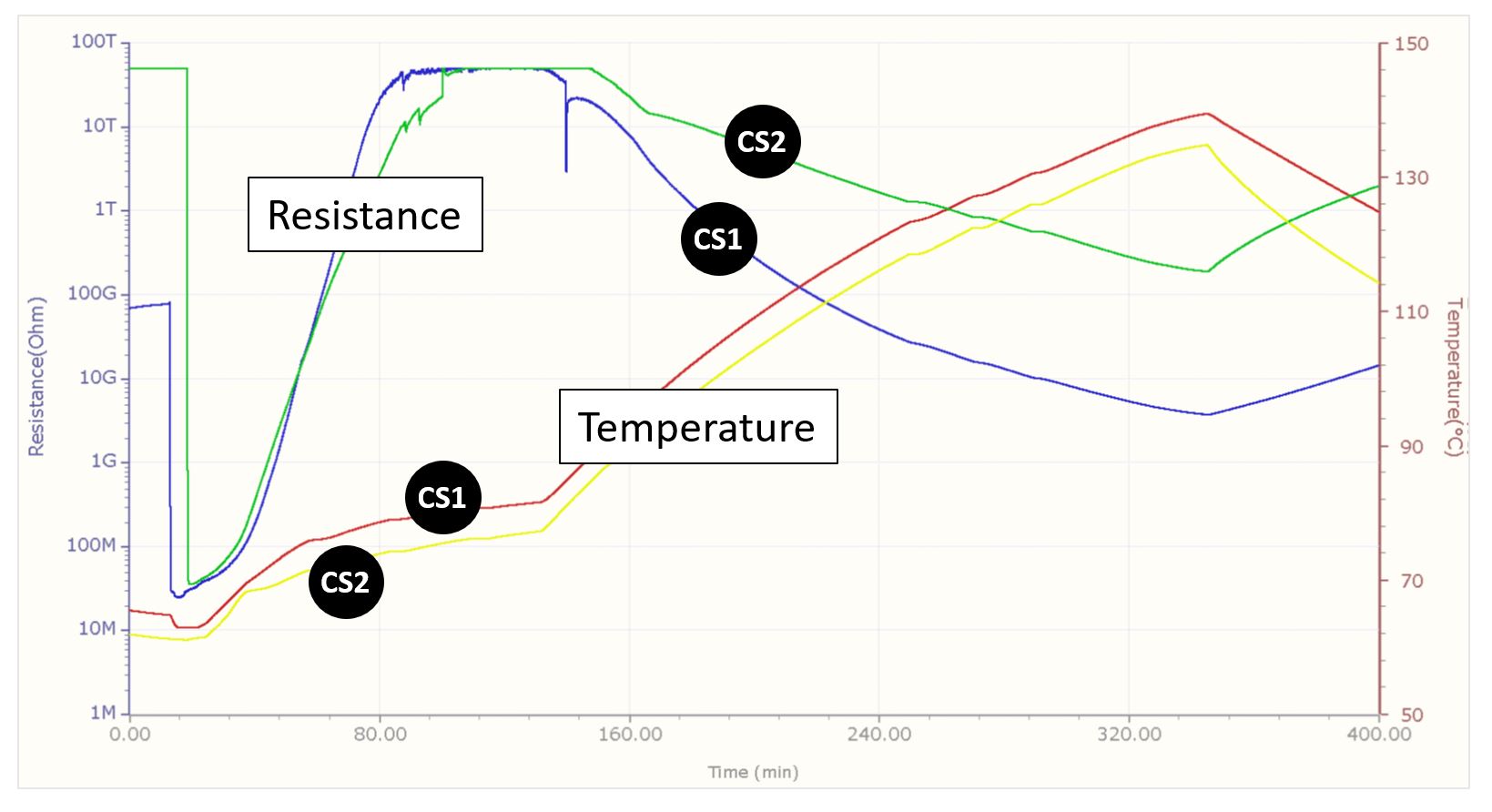
“Las unidades OPTIMOLD y OPTIFLOW se pueden conectar juntas a través de Ethernet para que todos los sensores se puedan registrar en una sesión Optiview”, explica Pantelelis. "Por lo tanto, CS1 y CS2 se conectaron a dos unidades OPTIMOLD, el sensor de flujo en el molde 1 y los ocho sensores de flujo desechables se conectaron a tres unidades OPTIFLOW".
Este sistema de sensores, unidades de adquisición de datos OPTIMOLD / OPTIFLOW y software OPPTIVIEW / ORS se aplicó luego durante las pruebas de moldeo RTM para establecer objetivos para varias etapas del proceso, incluida la inyección / infiltración de resina y dos objetivos de Tg. “Esta fue una pieza gruesa hecha con fibra unidireccional y resina epoxi Huntsman”, dice Pantelelis. “En este caso, usamos sensores de alambre de flujo para verificar el flujo dentro de estas capas UD, que generalmente están empaquetadas de manera apretada y pueden crear desafíos durante la infiltración de resina”.
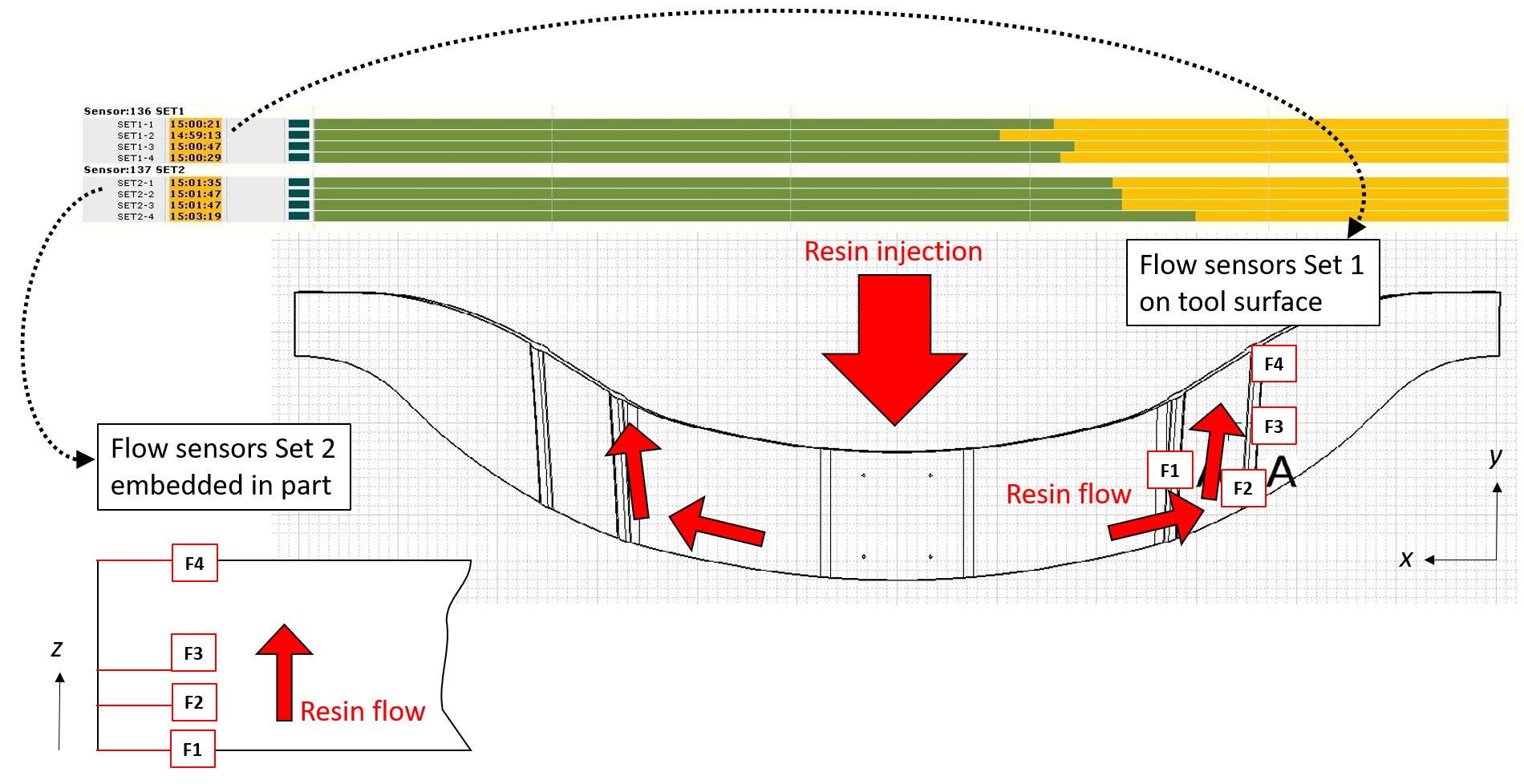
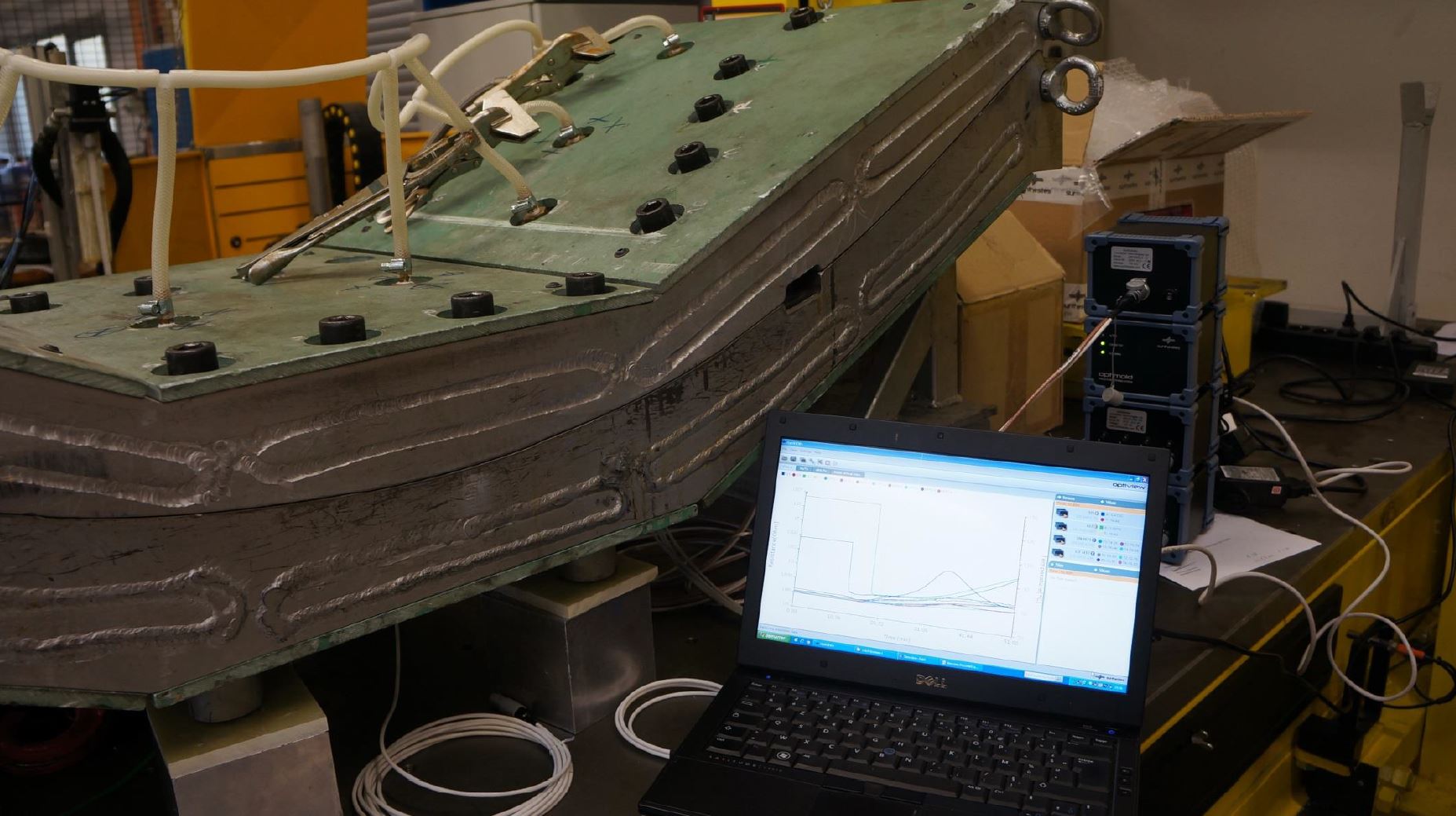
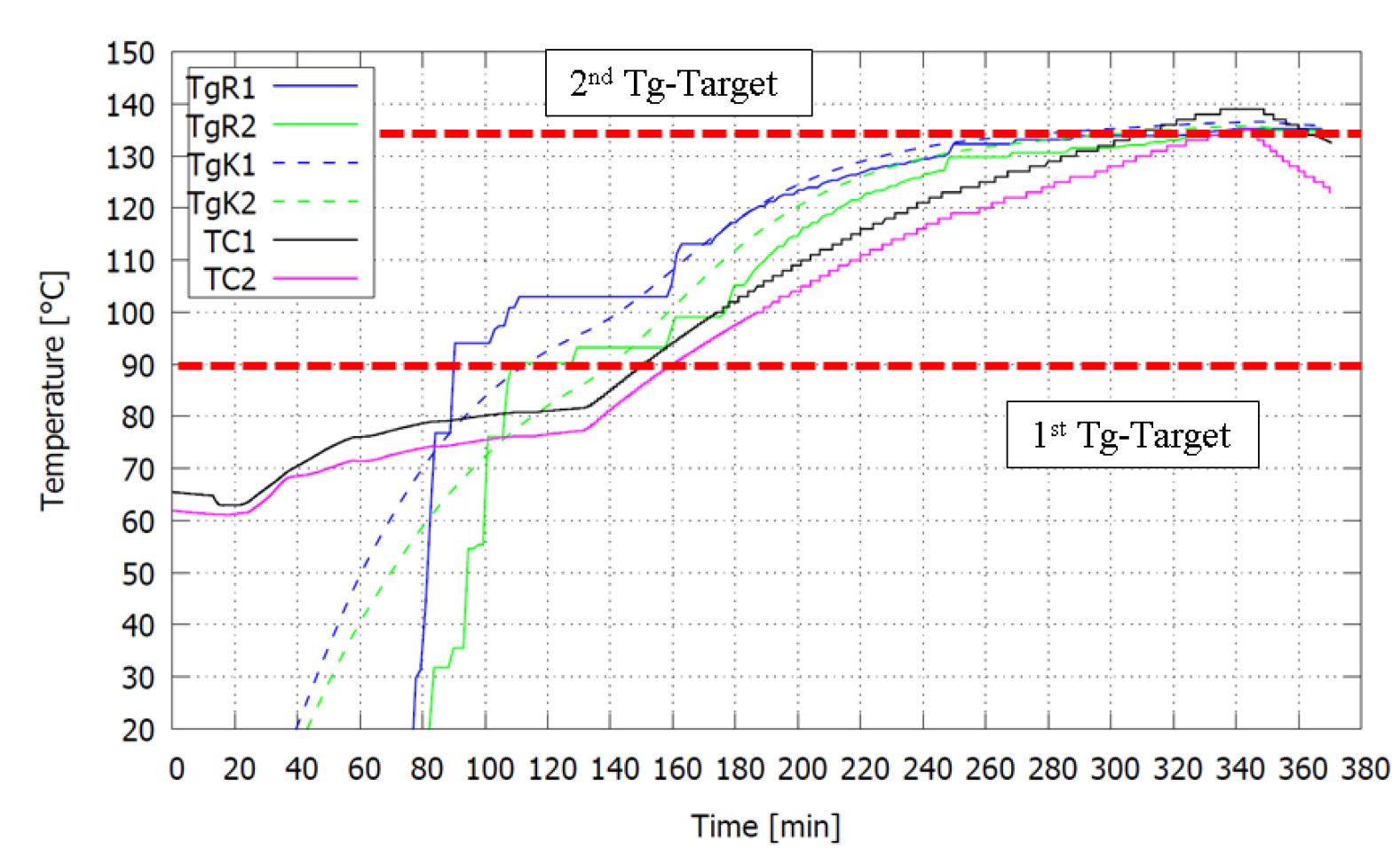
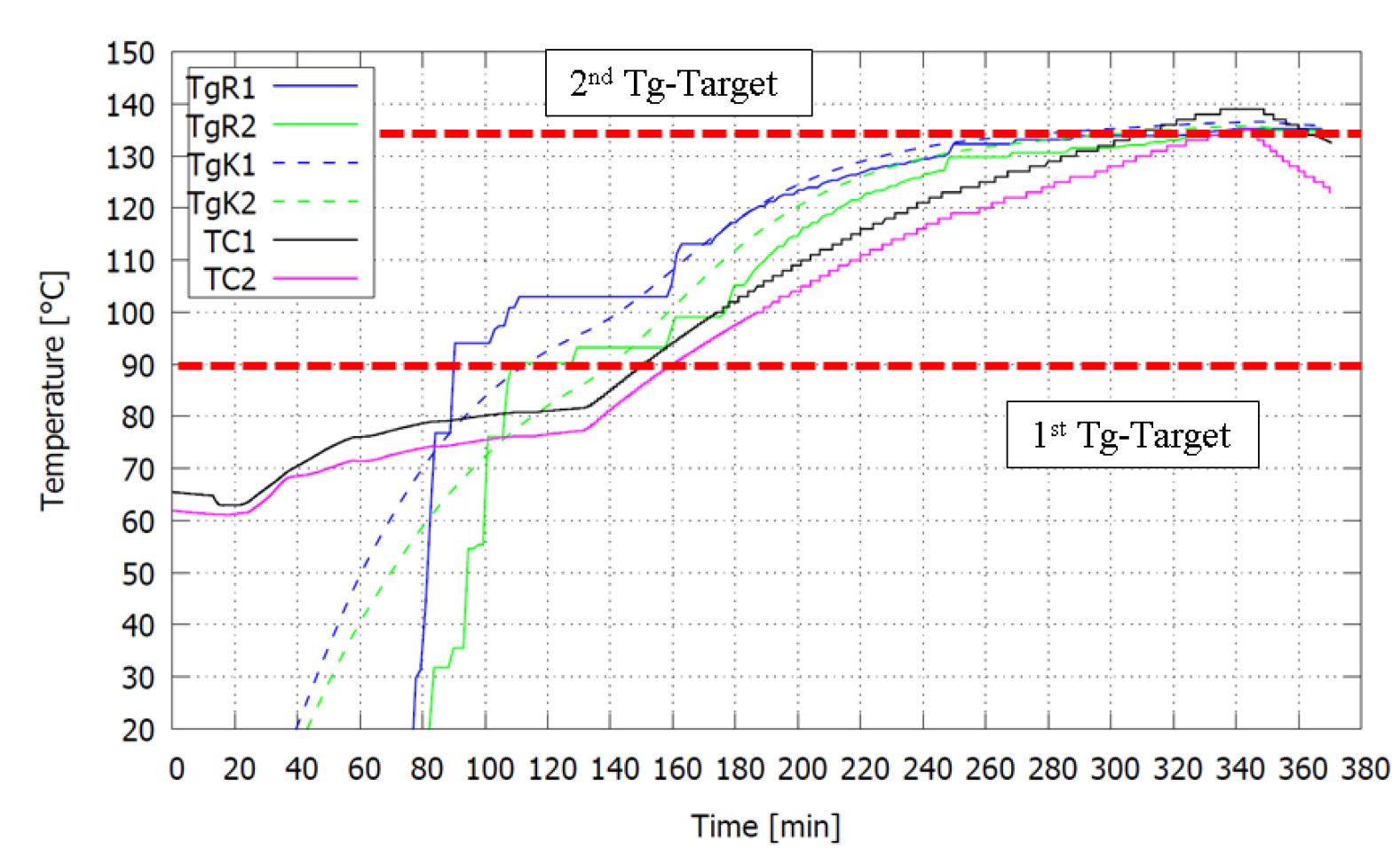
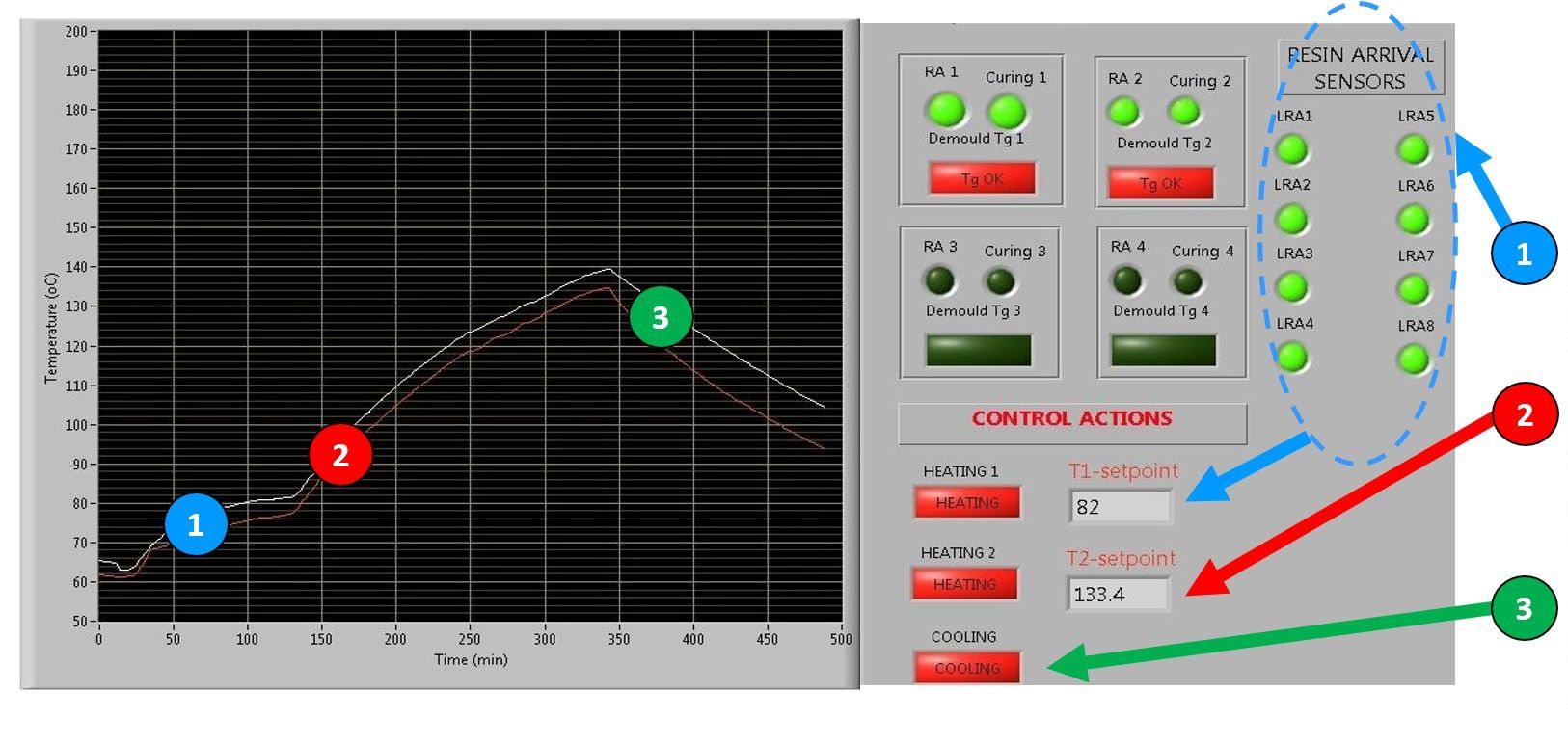
Con este sistema de control de procesos, el proyecto ECOMISE en Hutchinson pudo reducir el ciclo de curado en más del 30%.
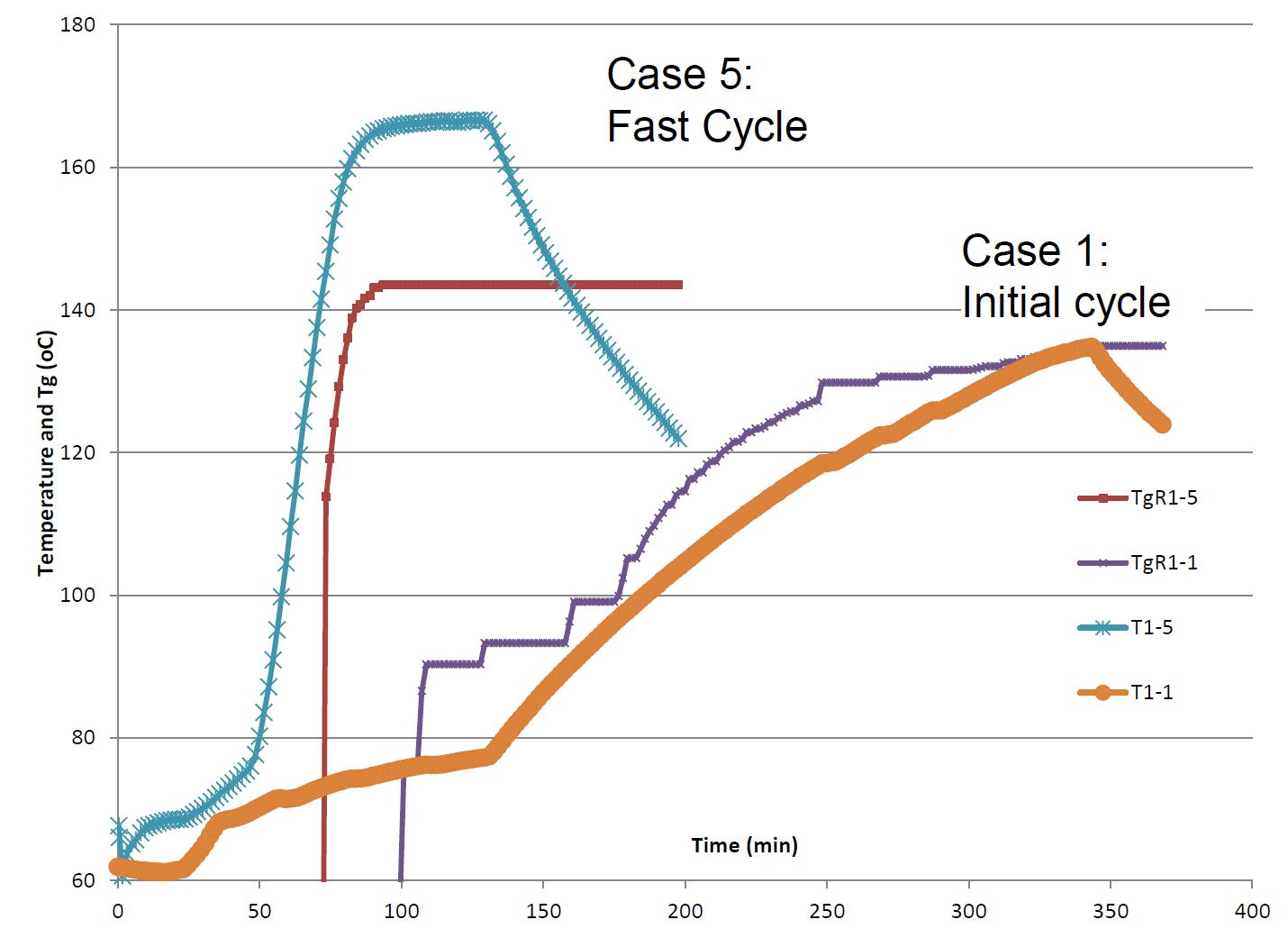
Calibración
Se requiere calibración para el monitoreo de Tg en línea. A medida que las mediciones se recopilan de los sensores a través de las unidades OPTIMOLD, el software ORS las traduce en viscosidad y Tg según la calibración de esa resina específica. "Esta calibración es un trabajo que se realiza antes del procesamiento para proporcionar las correlaciones que el software ORS utilizará para sus cálculos", explica Pantelelis. “Calibramos colocando la resina en un reómetro y midiendo la temperatura y la viscosidad. Aplicando las fórmulas adecuadas, calcula la resistencia y la Tg correspondientes. Desarrollamos la calibración de resinas para nuestros clientes en función de sus estándares y estudiamos los diferentes ciclos de curado de la resina. Luego, el software ORS utiliza estos datos de calibración cada vez que se procesa esa resina ”.

La precisión de los cálculos de Tg en tiempo real del software ORS se demostró en pruebas realizadas por el productor de palas eólicas Carbon Rotec Composite Technology (Lemwerder, Alemania). La Tg calculada en línea por el software ORS se comparó con la Tg medida justo después del desmoldeo mediante la realización de un calorímetro de barrido diferencial (DSC). Para el procesamiento isotérmico, la diferencia media fue de 1,61 ° C y para el procesamiento no isotérmico fue de 2,15 ° C.
“Esta precisión se ha demostrado repetidamente en proyectos privados con otros clientes”, dice Pantelelis.
Avances para la producción industrial
Este control de proceso basado en datos y sensores es de hecho un gran paso hacia la fabricación de Composites 4.0 totalmente automatizada e inteligente. Aunque se ha demostrado en ECOMISE y también con el NCC en Bristol, todavía no se utiliza en la producción diaria. “La idea de usar los sensores para ver la Tg y luego comenzar a enfriar se inició en la fabricación de palas eólicas”, informa Pantelelis, “pero aún no está completamente automatizado. El sistema emite una alarma cuando se alcanza la Tg objetivo y luego el operador detiene el ciclo de curado. La automatización es sencilla y se completará una vez que el fabricante haya validado la precisión del sistema durante la fase piloto ".
“Para lograr este objetivo, hemos desarrollado una nueva estación de trabajo para permitir que el operador de producción supervise el proceso automatizado, que no requiere información de su parte”, continúa. “Hemos visto en la fabricación de palas de turbinas eólicas que el uso de una sola estación de trabajo durante el curado de resina y adhesivo puede acortar el tiempo del ciclo en al menos 2-3 horas sin sacrificar la calidad”.
Aunque Bombardier Belfast, ahora Spirit AeroSystems, utiliza equipos Synthesites en la producción de su ala compuesta infundida con resina para la Serie C, ahora Airbus A220, el control del proceso no está automatizado. Sin embargo, Synthesites también trabajó con Bombardier en ECOMISE, y ese desarrollo se está llevando a cabo. Un logro clave fueron los sensores que se alimentan a través de la pared del autoclave. Como se explicó en mi blog de 2013, "Ala compuesta de la serie C":
Bombardier está inyectando después de que la bandeja se haya colocado en su autoclave de 21,3 m de largo por 5,6 m de diámetro, lo que permite mantener la temperatura y la presión al nivel requerido para reducir la viscosidad y la humectación - Cytec 890 es inyectable a 80˚C. . . Una vez que se completa la inyección de resina, se aplica presión positiva en el autoclave durante la consolidación, lo que hace que los elementos de las herramientas se cierren, compacten el laminado húmedo y expulsen el exceso de resina de la entrada de resina a un vertedero de resina diseñado específicamente.
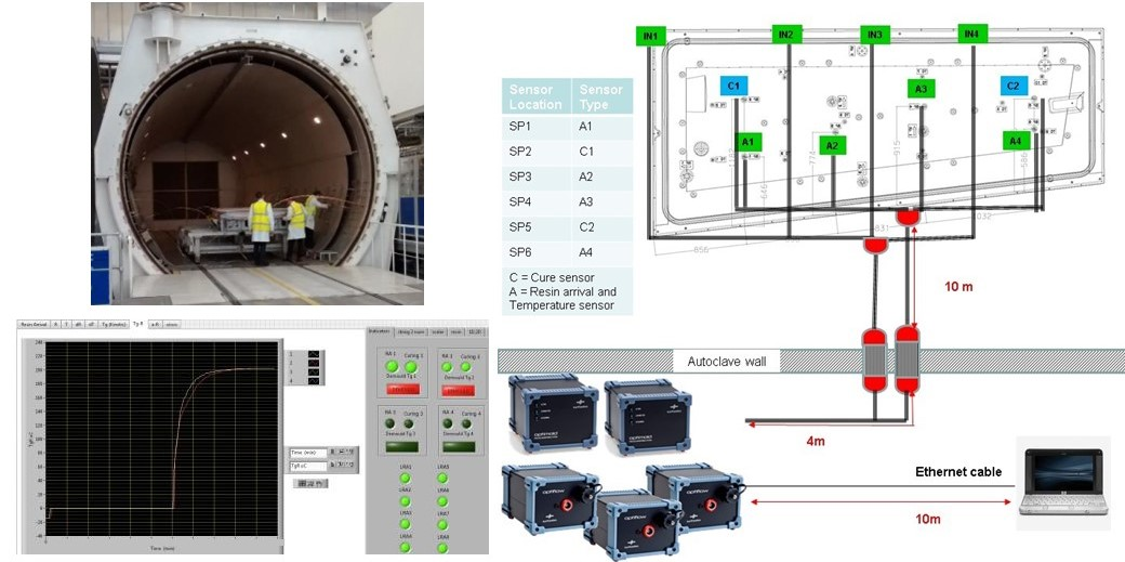
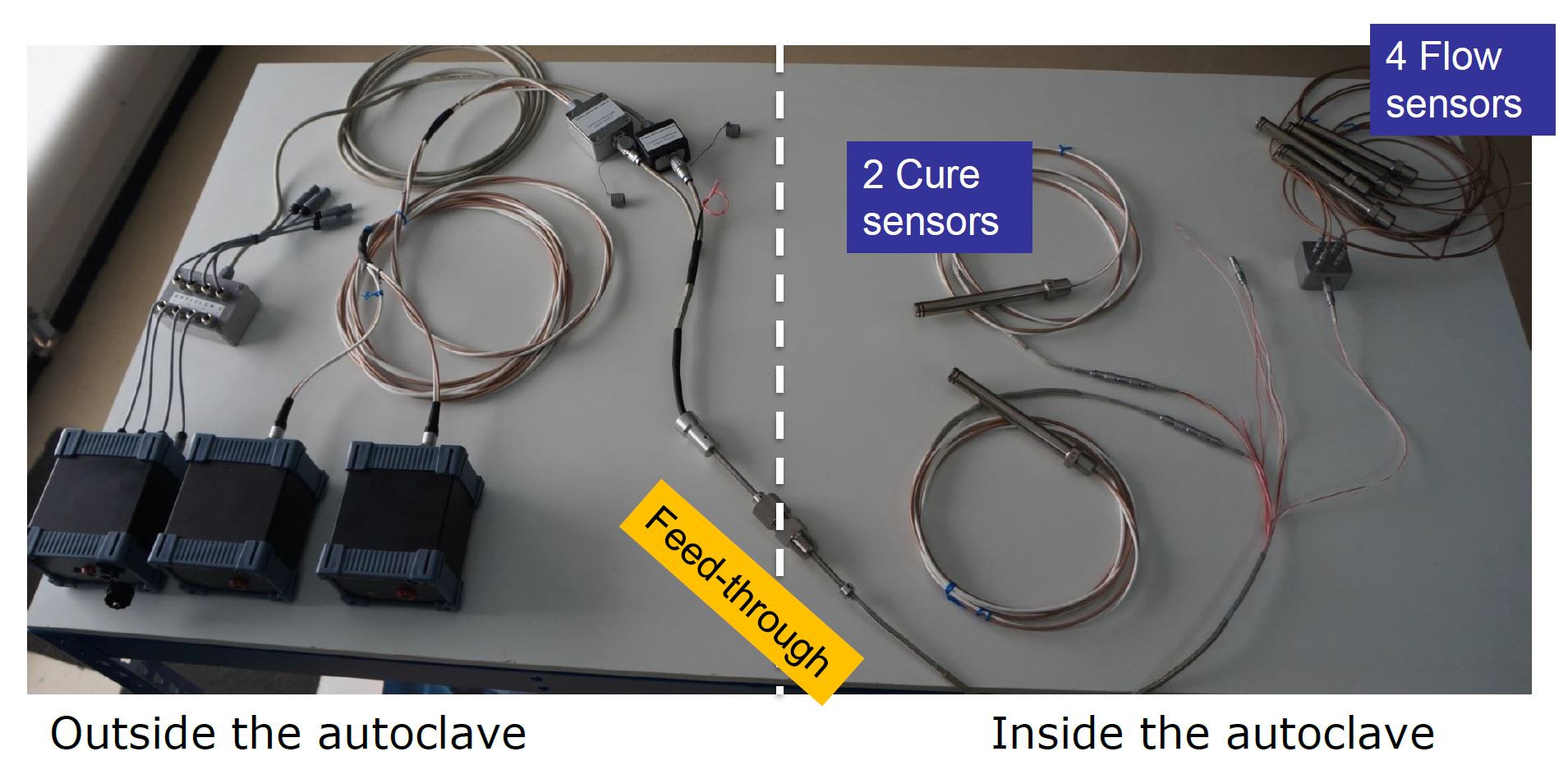
“Como la mayoría de los fabricantes del sector aeroespacial comercial, está interesado en garantizar la calidad y aumentar la tasa”, explica Pantelelis. El diseño a continuación y los resultados de ECOMISE fueron para un demostrador, no una parte comercial. Usó dos unidades OPTIMOLD con dos sensores de curado en el molde y tres unidades OPTIFLOW con cuatro sensores de flujo en el molde y cuatro sensores en línea en las líneas de vacío. “OPTIFLOW puede monitorear hasta cuatro llegadas de resina y cuatro sensores de temperatura / resistencia”, señala Pantelelis. “Los objetivos de la demostración se alcanzaron plenamente. Demostramos que los sensores, cableado y sistemas pueden funcionar sin ningún problema bajo las especificaciones aeroespaciales más desafiantes. Fue interesante que las mediciones de llegada de resina mostraran grandes diferencias en comparación con las simulaciones de flujo. Además, el monitoreo de Tg en línea mostró que el ciclo de curación seguido para ese demostrador específico podría haber sido significativamente más corto ".
“Ahora estamos desarrollando un sistema de monitoreo para las líneas de unión”, dice Pantelelis, “principalmente para la producción de palas de turbinas eólicas pero, en última instancia, para cualquier proceso de unión. Aunque actualmente estamos muy ocupados con la industria de las turbinas eólicas, que está tratando de reducir costos, vemos cada vez más interés en el sector aeroespacial a medida que avanza hacia el moldeo de compuestos líquidos para la producción en masa. Los fabricantes buscan obtener más información sobre lo que sucede exactamente durante el moldeo y cómo pueden estabilizar y optimizar sus procesos ”.
Los proyectos Ecomise y Recotrans recibieron financiación de los Programas de Investigación e Innovación FP7 y Horizonte 2020 de la Unión Europea en virtud del Acuerdo de subvención nº NMP2-SL-2013-608667 y 768737, respectivamente
Referencias de la sección " Análisis dieléctrico (DEA), CA vs. CC" incluir:
- “Monitoreo de curado UV en tiempo real” por VINCENTZ, publicado en European Coatings Journal, número 11/2003, p. 7.
- "Sistemas de monitoreo de procesos en línea - Estudio de pruebas y puntos de referencia" por Reinhold Meier 1 , Swen Zaremba 1 , Florian Springl 1 , Klaus Drechsler 1 , Fabrice Gaille 2 y Christian Weimer 2 - 1 Instituto de compuestos de carbono, TU Munich, Garching, Alemania. 2 Eurocopter Deutschland GmbH, Donauwörth. Proceso de flujo en materiales compuestos - FPCM 11, 9-12 de julio de 2012, Auckland, Nueva Zelanda.
- Caracterización no destructiva de materiales VIII editado por Robert E. Green, Actas del 8 th Intl. Simposio sobre caracterización no destructiva de materiales, 16 al 20 de junio de 1997, Boulder, Colorado, EE. UU., Publicado por Springer Science &Business Media, págs. 384-385.
Otra referencia útil es el “Manual de análisis dieléctrico y monitoreo de curado” de Huan L. Lee, publicado por Lambient Technologies.
Resina
- Sensores y procesadores convergen para aplicaciones industriales
- Nuevos sensores de imagen ams para visión industrial de alto rendimiento
- BASF y Toray en acuerdo de suministro para la producción de cintas CFRT para aplicaciones automotrices e industriales
- Composites de TPE ultraligeros para calzado
- Compuestos de Solvay seleccionados para catamarán de carreras
- Hexion presenta una solución epoxi de dos componentes para la producción de compuestos aeroespaciales
- LANXESS amplía la capacidad de producción de compuestos termoplásticos continuos reforzados con fibra
- El consorcio de compuestos termoplásticos tiene como objetivo la producción de alto volumen para la industria automotriz y aeroespacial
- Sensores de tensión ultradelgados y sin batería para brazos robóticos industriales
- Sensores inteligentes:ventajas y desventajas para la maquinaria industrial
- ¿Cuáles son las innovaciones para el mantenimiento industrial?