Control de la morfología de la superficie secundaria de nanofibras de PVDF electrohiladas mediante la regulación del disolvente y la humedad relativa
Resumen
Este trabajo presenta un método simple y confiable para generar directamente nanofibras de fluoruro de polivinilideno (PVDF) con morfología superficial secundaria (por ejemplo, superficies porosas, superficies rugosas, superficies ranuradas y porosidad interior) mediante el uso de sistemas solventes simples / binarios y humedad relativa. Aclaramos los mecanismos responsables de la formación de estas morfologías explorando sistemáticamente las interacciones moleculares entre el polímero, el (los) solvente (s) y el vapor de agua. Nuestros resultados demostraron que la formación de la morfología superficial secundaria necesitaba la presencia de vapor de agua, un no solvente del polímero, a un nivel apropiado de humedad relativa. La formación de la morfología de la superficie secundaria dependía de la velocidad de evaporación de los solventes (ACE, DMF y sus mezclas), así como de la interdifusión y penetración del no solvente (agua) y el solvente (s). ). Los resultados de N 2 Las isotermas físicas de adsorción-desorción mostraron que las fibras macroporosas (> 300 nm) exhibían el área de superficie específica más alta de 23,31 ± 4,30 m 2 / gy volumen de poros de 0,0695 ± 0,007 cm 3 / g, lo que permite altas capacidades de absorción de aceite de 50,58 ± 5,47 g / g, 37,74 ± 4,33 g / gy 23,96 ± 2,68 g / g para aceite de silicona, aceite de motor y aceite de oliva, respectivamente. Creemos que este trabajo puede servir como guía para la formación de diferentes estructuras de nanofibras macroporosas, rugosas y ranuradas con porosidad interior mediante electrohilado.
Antecedentes
El electrohilado es un método de formación de fibras que implica fuerzas electrostáticas para expulsar y estirar chorros de polímero en fibras. Actualmente, el proceso produce fibras con un diámetro que varía desde unos pocos nanómetros hasta varios micrómetros [1]. Varias morfologías de fibras electrohiladas, incluidas fibras con cuentas [2], fibras porosas [3], fibras ranuradas [4], fibras multicanal [5], fibras en cinta [6], fibras una al lado de la otra [7], fibras huecas [8 ], las fibras jerárquicas [9], los nanocompuestos en forma de grano de arroz [10], las fibras de alas de mariposa [11], las fibras de núcleo-vaina [12] y las fibras rizadas [13] pueden formarse controlando los parámetros de electrohilado [14].
Las nanofibras electrohiladas han demostrado propiedades excelentes, como alta superficie específica, flexibilidad, facilidad de funcionalidad, variedad de morfología y estructura, resistencia direccional superior y alta porosidad, lo que las convierte en una forma de material preferida para diferentes aplicaciones, como la recolección de energía [15], sensores [16], filtración [17,18,19], aplicaciones biomédicas [20], superficies autolimpiantes [21,22,23], etc. Los estudios han demostrado que al regular las morfologías secundarias (p. ej., superficies porosas, ranuras superficies, superficies rugosas y porosidad interior) de las fibras electrohiladas, sus propiedades y comportamiento podrían mejorarse o modificarse en gran medida. Por ejemplo, las fibras porosas han mostrado un uso extensivo en una amplia variedad de aplicaciones tales como catálisis, filtración e investigación biomédica debido al aumento de sus áreas superficiales específicas a través de la introducción de poros intrafibra [24]. Se han utilizado fibras rugosas para mejorar la salida eléctrica de los dispositivos de energía de barrido debido al aumento de las áreas de fricción [25]. Las fibras ranuradas han presentado un gran potencial en el área de la ingeniería de tejidos y las superficies superhidrofóbicas [26]. Además, el aumento del área de superficie específica y la porosidad conduce a un mejor rendimiento de absorción [27, 28], catálisis [29, 30], etc.
Anteriormente, hemos informado la producción de fibras de poliestireno con estructuras y distribuciones de macroporos sintonizables mediante el uso de una boquilla de microfluidos que contiene tres canales que permite la mezcla de líquidos de dos canales de entrada y electrohilado sincronizado de la mezcla resultante del otro canal de salida [3] . Además, hemos informado de la fabricación de acetato butirato de celulosa y fibras de poliestireno con una estructura ranurada mediante electrohilado utilizando un sistema de disolventes mixtos que consta de un disolvente de alto punto de ebullición y un disolvente de bajo punto de ebullición [4, 31].
En este estudio, demostramos la fabricación de nanofibras de fluoruro de polivinilideno (PVDF) con estructuras de superficie macroporosa, rugosa y ranurada y poros interiores utilizando electrohilado sin involucrar ningún método especial de recolección o tratamiento posterior al hilado. Aquí, se seleccionó el PVDF como modelo porque se puede disolver en diferentes disolventes.
Hasta donde sabemos, hasta ahora, no se han investigado sistemáticamente estudios que maniobren la formación de nanofibras de PVDF electrohiladas macroporosas (> 300 nm), rugosas y ranuradas con porosidad interna controlando la humedad relativa. En este documento, informamos el electrohilado de soluciones de PVDF a cuatro niveles de humedad relativa (5%, 25%, 45% y 65%) utilizando sistemas de disolventes simples y binarios. El objetivo principal de este trabajo es investigar la factibilidad de fabricar fibras macroporosas, rugosas y estriadas con estructuras interiores sólidas y porosas utilizando diferentes niveles de humedad relativa, y conocer sus mecanismos de formación. Al investigar sistemáticamente el efecto de la humedad relativa sobre la morfología de la superficie secundaria de las fibras de PVDF electrohiladas, llegamos a la conclusión de que la humedad relativa juega un papel importante en la determinación de la superficie y la morfología interna de las fibras de PVDF. Este estudio puede proporcionar pautas útiles para la preparación de la estructura superficial secundaria de nanofibras mediante electrohilado.
Métodos
Productos químicos y materiales
Los sedimentos de PVDF (Mw =275.000) se adquirieron de Sigma-Aldrich, Inc. La acetona (ACE) y la N, N-dimetilformamida (DMF) se adquirieron en Shanghai Chemical Reagents Co., Ltd., Shanghai, China. Todos los materiales se utilizaron sin purificación adicional.
Electrohilado de fibras PVDF con morfología de superficie secundaria
Para obtener fibras macroporosas, rugosas y estriadas, 18% ACE ( w / v ) Solución de PVDF, DMF al 35% ( w / v ) Solución de PVDF y 25% (ACE / DMF) ( w / v ) Se prepararon soluciones de PVDF en las proporciones de disolvente (4:1, 2:1, 1:1, 1:2 y 1:4), respectivamente, y cada solución se cargó en una jeringa de plástico. En este trabajo, la relación de disolvente fue la relación de volumen y la concentración de la solución fue peso / volumen ( w / v ) (g / ml). Se utilizó una aguja de jeringa de calibre 21 como hilera, que se fijó en una bomba de jeringa (KDS 100, KD Scientific Inc., EE. UU.) Conectada a un proveedor de alto voltaje (Tianjin Dongwen Co., Ltd., China). Se colocó un colector de tambor conectado a tierra (40 cm de longitud y 20 cm de diámetro) a 18 cm de la hilera y se fijó la velocidad de rotación a 2 rpm para obtener fibras orientadas al azar. Todos los experimentos se realizaron a 20 ° C bajo diferentes niveles de humedad relativa (5%, 25%, 45% y 65%). La temperatura se ajustó mediante el sistema de aire acondicionado central del laboratorio y la humedad relativa se controló mediante la humedad ambiental, que podría ajustarse aún más con una ventana estrecha (± 2%) mediante el uso de un humidificador / deshumidificador. Todas las muestras se prepararon a una velocidad de alimentación y un voltaje aplicado de 1,5 ml / hy 18 kV, respectivamente. Todos los parámetros anteriores se ajustaron para obtener fibras con diferentes morfologías y diámetros similares.
Diagrama de fase ternaria
Las curvas del punto de enturbiamiento se determinaron mediante el método de titulación a una humedad relativa del 65%. Las soluciones de PVDF se prepararon disolviendo el polímero en los sistemas de un solo solvente usando ACE y DMF, y sistemas de solventes binarios usando ACE / DMF en la proporción de solvente de 1:1. Las soluciones homogéneas adquiridas se valoraron con agua desionizada como no disolvente. Al comienzo de la turbidez permanente, se anotó la composición de la solución y la cantidad de no disolvente utilizado y se trazó en el diagrama de fase ternario, que se utilizó para representar las curvas binodales [32, 33].
Caracterización
La morfología de la superficie y la sección transversal de las nanofibras de PVDF electrohiladas se comprobaron bajo microscopía electrónica de barrido de emisión de campo (FE-SEM) (S-4800, Hitachi Ltd., Tokio, Japón) después del recubrimiento de oro. Se prepararon secciones transversales de las fibras colocándolas en nitrógeno líquido y rompiéndolas manualmente. El diámetro de la fibra se midió utilizando un software de análisis de imágenes (Adobe Acrobat X Pro 10.1.2.45) de acuerdo con las imágenes SEM. N 2 Se midieron las isotermas físicas de adsorción-desorción (JW-BK132F, Beijing Science and Technology Co., China) para determinar el área de superficie específica, la distribución de poros y el volumen total de poros.
Absorción de aceite
La capacidad de absorción de aceite se midió a 25 ° C usando el siguiente método. Luego, se prepararon 15 mL de mezcla agua-aceite con una proporción de 1:1 y se colocaron en un vaso de precipitados. Además, se agregaron 0,3 g del sorbente al vaso de precipitados para absorber el aceite durante 1 h, y luego el sorbente húmedo se trasladó a una malla de malla y se drenó durante ~ 40 min para asegurar que no quedaran gotas de aceite en el sorbente. La capacidad de absorción de aceite se calculó de acuerdo con la siguiente ecuación:
$$ Q \ kern0.5em =\ kern0.5em \ frac {m_0- {m} _1} {m_1} $$donde Q es la capacidad de absorción de aceite (g / g), m 0 es la masa total del sorbente húmedo después de la absorción de aceite drenada durante ~ 40 min (g), y m 1 es la masa del sorbente antes de la absorción (g).
Resultados y discusión
Para explorar el efecto de la humedad relativa en la morfología secundaria de fibras de PVDF electrohiladas, 18% ( w / v ) Solución de PVDF con ACE, 35% ( w / v ) Solución de PVDF con DMF y 25% ( w / v ) Las soluciones de PVDF con diferentes relaciones ACE / DMF se electrohilaron.
Fibras electrohiladas de ACE
Las fibras obtenidas de la solución de PVDF / ACE a diferentes niveles de humedad relativa se han exhibido y comparado (Figs. 1 y 2). Se formaron fibras lisas utilizando una solución de PVDF / ACE a una humedad relativa del 5% (Fig.1a y archivo adicional 1:Figura S1A), mientras que las fibras macroporosas se produjeron a una humedad relativa del 25%, 45% y 65% (Fig. 1b-dy archivo adicional 1:Figura S1B-D). La formación de poros superficiales debe atribuirse a la separación de fases inducida por calor (TIPS) [24].
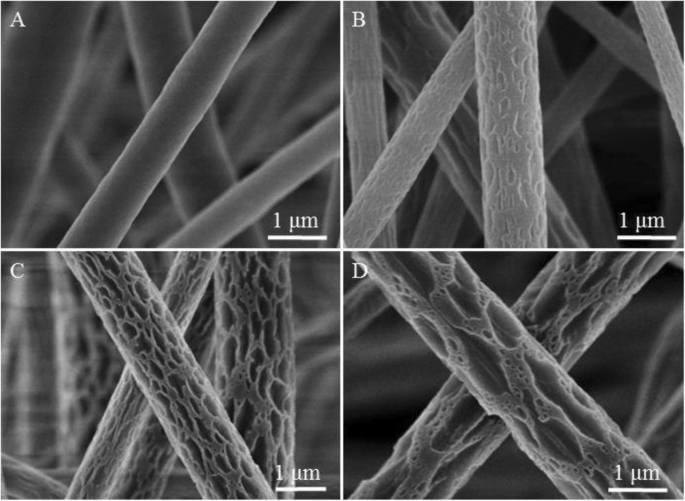
Imágenes SEM representativas de muestras fabricadas mediante electrohilado al 18% ( w / v ) Solución de PVDF de ACE a diferentes niveles de humedad relativa. un 5%, b 25%, c 45% y d 65%
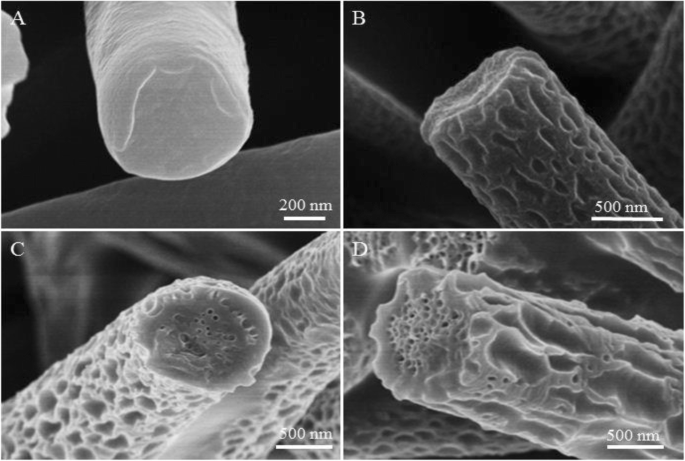
Imágenes SEM transversales de muestras fabricadas mediante electrohilado al 15% ( w / v ) Solución de PVDF de ACE a diferentes niveles de humedad relativa. un 5%, b 25%, c 45% y d 65%
Para confirmar el mecanismo de formación de fibras macroporosas de PVDF formadas a partir de una solución de PVDF / ACE, se verificó la sección transversal de las fibras formadas a diferentes niveles de la humedad relativa estudiada. Encontramos que a la humedad relativa de 5% y 25%, las fibras formadas tenían un interior sólido (Fig.2a, b), mientras que las fibras con poros interiores se formaron a la humedad relativa de 45% y 65% (Fig.2c, D). Por lo tanto, podemos concluir que las fibras se formaron con una superficie lisa y un interior sólido a la humedad relativa del 5% debido a la ausencia de separación de fases. Mientras que se formaron fibras macroporosas con interior sólido debido a TIPS. Mientras que las fibras macroporosas con poros interiores se formaron a una humedad relativa de 45% y 65% debido a la coexistencia de TIPS y separación de fases inducida por vapor (VIPS). En otras palabras, cuando los solventes altamente volátiles se evaporaron, absorbieron una gran cantidad de calor y así enfriaron la superficie de las fibras, lo que las llevó a condensarse y atraer gotas de agua sobre la superficie de las fibras. Cuando la humedad relativa aumentó, la tasa de evaporación de las gotas de agua disminuyó, dando lugar a la coalescencia entre las gotas formadas macro gotas cuyo mecanismo se conoce como el crecimiento de nucleación (NG) [34]. Después de que las macrogotas de agua condensada se secaron, formaron macroporos en la superficie de las fibras. Mientras que, la parte de las gotas de agua que penetraron en la fibra finalmente se secó para formar poros interiores. El mecanismo de formación de las fibras macroporosas a alta humedad relativa se demuestra en la Fig. 3a. A alta humedad relativa, la tasa de evaporación de las gotas de agua condensadas en la superficie de las fibras disminuyó, dando a estas gotas más tiempo para fusionarse debido a NG. Por lo tanto, el tamaño de los macroporos en la superficie de las fibras aumentó de ~ 50 nm a una humedad relativa del 25%, a ~ 100 nm a una humedad relativa del 45% y a ~ 400 nm a una humedad relativa del 65%. . Todas las superficies y morfologías internas obtenidas de la solución de PVDF / ACE a diferentes niveles de humedad relativa se resumen en la Tabla 1. Es importante destacar que el aumento de la humedad relativa del 5 al 65% conduce al aumento del diámetro de las fibras de ~ 0,77 a ~ 1,81 μm (adicional archivo 1:Figura S2A).
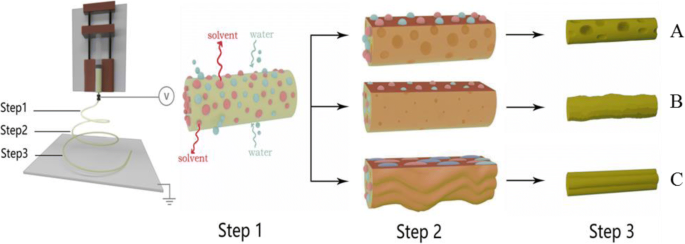
Diagramas de proceso del chorro de solución durante el electrohilado a alta humedad relativa. Paso 1:evaporación del disolvente y condensación del agua, paso 2:penetración de las gotas de agua y generación de poros, y paso 3:alargamiento y solidificación de fibras. un Fibras macroporosas, b fibras rugosas y c fibras ranuradas
Fibras electrohiladas de DMF
Aquí, 35% ( w / v ) La solución de PVDF se electrohilaron a diferentes niveles de humedad relativa (5%, 25%, 45% y 65%).
Se produjeron fibras lisas utilizando una solución de PVDF / DMF a una humedad relativa del 5% (Fig.4a y archivo adicional 1:Figura S3A), mientras que las fibras rugosas se formaron a una humedad relativa del 25%, 45% y 65% (Fig. .4b – d y archivo adicional 1:Figura S3B-D) debido a la inestabilidad de pandeo [35] y estiramiento por fuerza eléctrica [26]. De acuerdo con la sección transversal de fibras formadas a la humedad relativa anterior estudiada, encontramos que las fibras con interior sólido se obtuvieron solo a la humedad relativa del 5% (Fig.5a), mientras que las fibras con poros interiores se formaron a la humedad relativa de 25%, 45% y 65% (Fig. 5b-d). En este caso, podemos decir que las fibras se formaron con una superficie lisa e interior sólido debido a la ausencia de separación de fases, mientras que las fibras se obtuvieron con una superficie rugosa y poros interiores debido a VIPS [24]. En otras palabras, la difusión y penetración corporativas de DMF y vapores de agua jugaron un papel esencial en la formación de fibras con poros interiores; Debido al hecho de que la presión de vapor del agua (2,34 kPa) es más alta que la de DMF (0,36 kPa) a la temperatura de 20 ° C, es razonable suponer que el vapor de agua saturó la región cercana de la interfaz entre el aire. y el chorro primero, luego seguido de su acción como no disolvente para precipitar una capa de PVDF sobre la superficie del chorro de líquido. La capa de PVDF solidificado ayudó a atrapar el DMF en el interior y disminuyó su velocidad de evaporación, lo que posiblemente impidió que el vapor de agua se condensara rápidamente o se acumulara en la superficie para formar gotas grandes. El vapor de agua penetró en la vaina y entró constantemente en la fase PVDF-DMF, lo que resultó en una rápida separación de fases. La figura 3d ilumina el mecanismo de formación de fibras rugosas a alta humedad relativa. Todas las superficies y morfologías internas obtenidas de la solución de PVDF / DMF a diferentes niveles de humedad relativa se resumen en la Tabla 1. Curiosamente, el aumento de la humedad relativa del 5 al 65% conduce al aumento del diámetro de las fibras de ~ 0,8 a ~ 1,79 μm (Archivo adicional 1:Figura S2B).
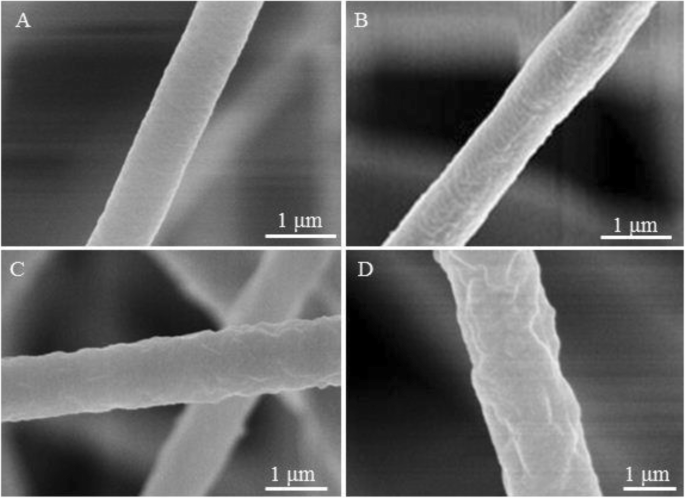
Imágenes SEM representativas de muestras fabricadas mediante electrohilado al 35% ( w / v ) Solución de PVDF de DMF a diferentes niveles de humedad relativa. un 5%, b 25%, c 45% y d 65%
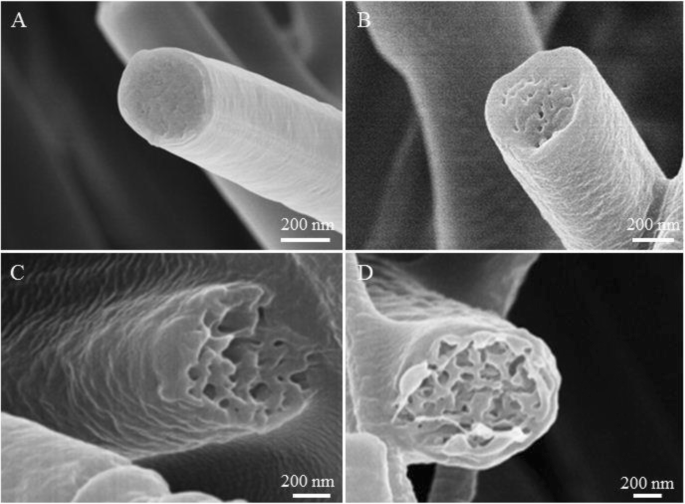
Imágenes SEM transversales de muestras fabricadas mediante electrohilado al 35% ( w / v ) Solución de PVDF de DMF a diferentes niveles de humedad relativa. un 5%, b 25%, c 45% y d 65%
Fibras electrohiladas de la solución de mezcla ACE / DMF
En este caso, el 25% ( w / v ) Se electrohilaron soluciones de PVDF con diferentes relaciones ACE / DMF (4:1, 2:1, 1:1, 1:2 y 1:4) a diferentes niveles de humedad relativa. Por 25% ( w / v ) (ACE / DMF en la proporción de disolvente de 4:1), se formaron fibras lisas a una humedad relativa del 5% (Fig.6a y archivo adicional 1:Figura S4A), se produjeron fibras ranuradas longitudinales poco profundas del pilar a la humedad relativa de 25% (Fig. 6b y archivo adicional 1:Figura S4B), y las fibras ranuradas longitudinales del pilar se produjeron a una humedad relativa del 45% y 65% (Fig. 6c, dy archivo adicional 1:Figura S4C, D). Por 25% ( w / v ) (ACE / DMF en la proporción de disolvente de 2:1), se formaron fibras lisas a una humedad relativa del 5% (Fig.6e y archivo adicional 1:Figura S4E), se fabricaron fibras rugosas con una humedad relativa del 25% (Fig.6f y archivo adicional 1:Figura S4F), se obtuvieron fibras ranuradas de pilar longitudinal poco profundo a una humedad relativa del 45% (Fig.6g y archivo adicional 1:Figura S4G), y fibras ranuradas longitudinales de pilar se produjeron en el relativo humedad del 65% (Fig. 6h y archivo adicional 1:Figura S4H). Por 25% ( w / v ) (ACE / DMF en la proporción de disolvente de 1:1) a la humedad relativa del 5%, se observaron fibras lisas (Fig.6i y archivo adicional 1:Figura S4I), se produjeron fibras rugosas a la humedad relativa del 25% y 45% (Fig. 6j, ky archivo adicional 1:Figura S4J, K), y pilar pequeñas fibras ranuradas se produjeron a una humedad relativa del 65% (Fig. 6l y archivo adicional 1:Figura S4L). Por 25% ( w / v ) (ACE / DMF en las proporciones de disolvente de 1:2 y 1:4), cuando la humedad relativa ≤ 25%, se observaron fibras lisas (Fig.6m, n, q, ry Archivo adicional 1:Figura S4M, N , Q, R), mientras que las fibras rugosas se produjeron a una humedad relativa de 45% y 65% (Fig. 6o, p, s, ty Archivo adicional 1:Figura S4O, P, S, T).
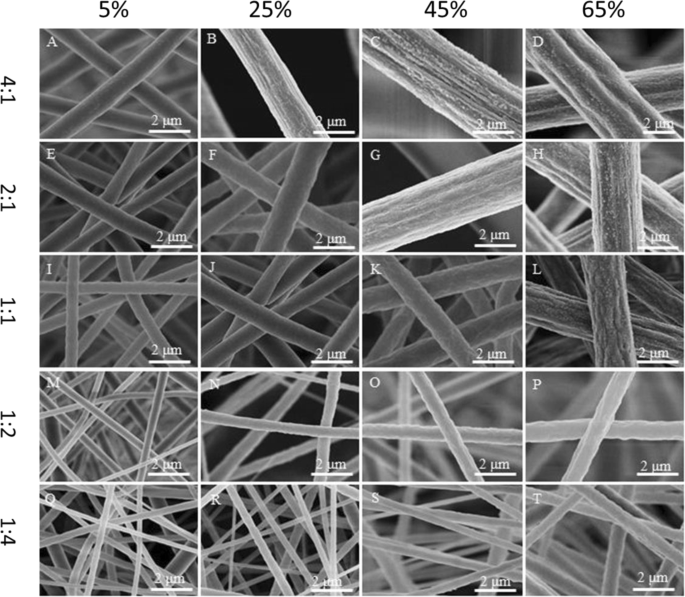
Imágenes SEM representativas de muestras fabricadas mediante electrohilado al 25% ( w / v ) Soluciones de PVDF de ACE / DMF a diferentes niveles de humedad relativa (5%, 25%, 45% y 65%) y proporciones de solventes. un - d 4:1, e - h 2:1, i - l 1:1, m - p 1:2 y q - t 1:4
Para ser más precisos sobre el mecanismo de formación de las fibras ranuradas de PVDF formadas a partir de ACE / DMF, verificamos la sección transversal de las fibras formadas en todas las proporciones de solventes y diferentes niveles de humedad relativa estudiados. Notamos que a la humedad relativa del 5%, todas las fibras formadas tenían un interior sólido. Aquí, concluimos que no ocurrió separación de fases en la formación de fibras con superficie lisa e interior sólido (Fig. 7a, e, i, m, q). A la humedad relativa del 25%, 45% y 65%, todas las fibras producidas tenían poros interiores. Las fibras ranuradas con poros interiores se fabricaron mediante un mecanismo de alargamiento basado en arrugas [36]. En este caso, debido a la rápida evaporación del ACE altamente volátil (presión de vapor, 24 kPa) y la separación de fases, se formó una piel vítrea en la etapa inicial del electrohilado, posteriormente se formó la superficie arrugada del chorro debido a la formación. de los poros interiores, y luego se alargan en fibras ranuradas (Fig. 7b – d, g, h, l). La Figura 3c explica el mecanismo de formación de las fibras ranuradas a alta humedad relativa. La formación de nanopilares en la superficie de las fibras ranuradas podría deberse al hecho de que el ACE atrapado en las fibras por la piel vítrea, que se enfrentó a una rápida evaporación de ACE, pero aún pueden existir algunos puntos débiles, lo que resulta en la formación de nanopilares.
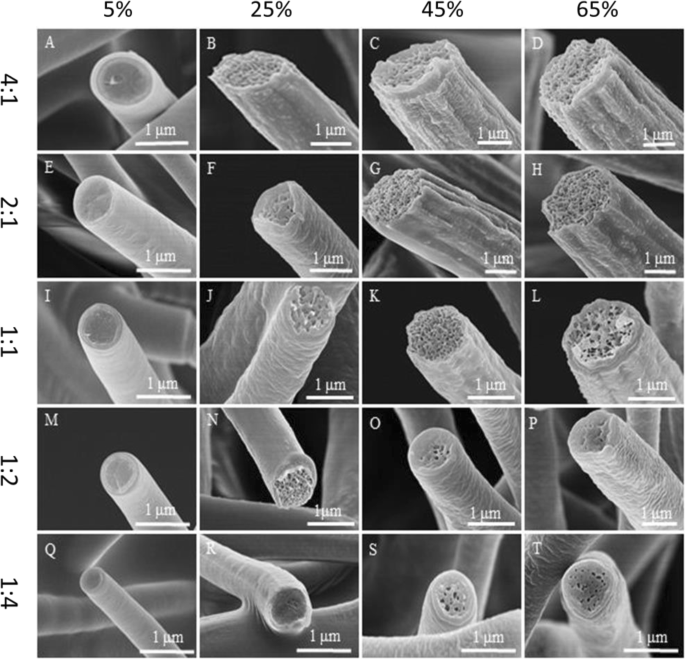
Imágenes SEM transversales de muestras fabricadas mediante electrohilado al 25% ( w / v ) Soluciones de PVDF de ACE / DMF a diferentes niveles de humedad relativa (5%, 25%, 45% y 65%) y proporciones de solventes. un - d 4:1, e - h 2:1, i - l 1:1, m - p 1:2 y q - t 1:4
Se formaron fibras con superficies rugosas y poros interiores debido a VIPS (Fig. 7f, j, k, o, p, s, t). También se formaron fibras con superficies lisas y poros interiores debido al VIPS (Fig. 7n, r) [24, 37]. Cabe mencionar que el ancho y la profundidad de las ranuras aumentaron al aumentar la humedad relativa. Todas las superficies y morfologías internas obtenidas de la solución de mezcla ACE / DMF a diferentes niveles de humedad relativa se concluyen en la Tabla 1. Notamos que aumentar la humedad relativa del 5 al 65% conduce al aumento del diámetro de las fibras de ~ 1 a ~ 3.75 μm , ~ 0,85 a ~ 2,9 μm, ~ 0,6 a ~ 2 μm, ~ 0,35 a ~ 1 μm y ~ 0,26 a ~ 0,7 μm para las siguientes proporciones de disolventes de 4:1, 2:1, 1:1, 1:2 y 1:4, respectivamente (Archivo adicional 1:Figura S2C-G).
Debido a la importancia de la alta humedad relativa en la formación de estructuras superficiales secundarias de las fibras de PVDF, ilustramos el comportamiento de fase de las soluciones de electrohilado creando un diagrama de fase a la humedad relativa del 65% (Fig. 8). El diagrama está dividido en dos zonas por una curva binodal. El chorro de solución está despejado y es homogéneo al extruirse de la hilera (zona I). Con la alta tasa de volatilización de ACE, la baja tasa de volatilización de DMF y la subsiguiente permeación de agua en el chorro de solución, la proporción de los componentes (PVDF, solvente (s) y agua) en el chorro se altera dinámicamente para seguir el camino mostrado por las flechas. El chorro de solución comienza a entrar en la zona II, después de cruzar la curva bimodal, donde se vuelve turbio y se separa en multifase debido a la inestabilidad termodinámica [37, 38]. Un solvente volátil más alto (ACE) está representado por una flecha más pronunciada, que corresponde a un proceso más rápido de separación de fases.
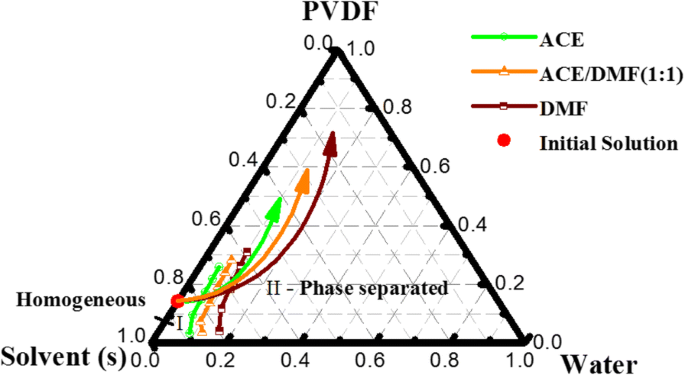
Diagrama de fases de PVDF, solvente (s) y agua a una humedad relativa del 65%. El punto rojo se refiere a la solución inicial
Para cuantificar el área superficial y la estructura de los poros de las fibras, se analizaron las isotermas de adsorción de nitrógeno de las fibras macroporosas (Fig. 1d), las fibras rugosas (Fig. 4d) y las fibras acanaladas (Fig. 6l) que tenían diámetros similares. elegido para comparar. Las áreas de superficie específicas de las fibras macroporosas, acanaladas y rugosas fueron de 23,31 ± 4,30 m 2 / g, 10,26 ± 2,19 m 2 / gy 4,81 ± 0,58 m 2 / g, y los volúmenes de poros fueron 0.0695 ± 0.007 cm 3 / g, 0,0182 ± 0,003 cm 3 / gy 0,0135 ± 0,002 cm 3 / g, respectivamente (Fig. 9a). Estos resultados se coordinaron con la máxima adsorción de nitrógeno de las fibras macroporosas, acanaladas y rugosas que eran de 20,06 cm 3 / g, 12,29 cm 3 / gy 7,49 cm 3 / g, respectivamente (Fig. 9b). Además, confirmamos que los mesoporos (2-50 nm) existían en las fibras macroporosas, acanaladas y rugosas (Fig.9c), mientras que los macroporos (> 100 nm) solo aparecían en las fibras macroporosas, lo que resultaba en su área de superficie específica y volumen de poros elevados (Fig. 9d).
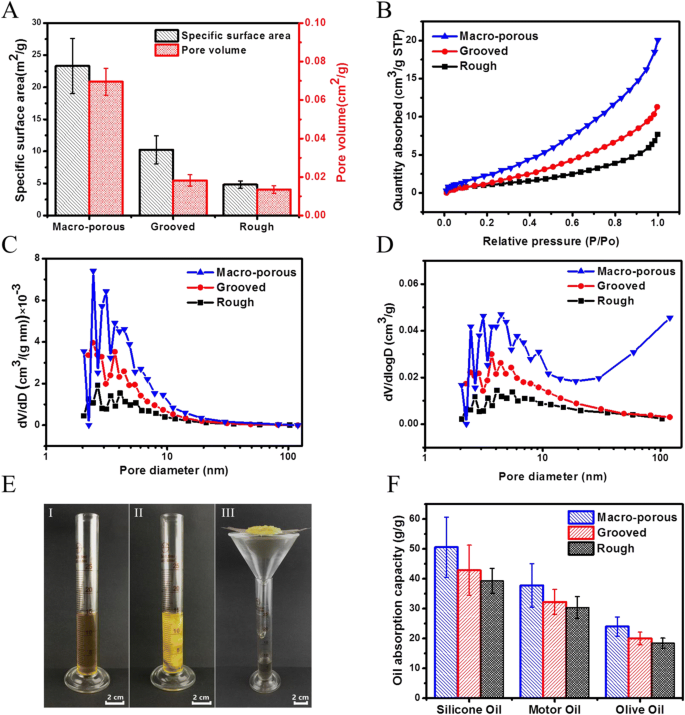
Caracterizaciones de las fibras macroporosas, estriadas y rugosas. un Área de superficie específica y volumen de poros. b Las isotermas de adsorción de nitrógeno. c dV / dD:curva de diámetro de poro. d dV / dlogD:curva de diámetro de poro. e Imágenes de absorción de aceite. (I) 15 mL de mezcla agua-aceite (1:1) sin sorbente, (II) durante la absorción, (III) durante el drenaje. f Capacidades de absorción de aceite
Dado que el PVDF es un material hidrófobo pero no oleófobo, los absorbentes de PVDF pueden absorber aceite mientras repelen el agua. A continuación, demostramos la aplicación de fibras macroporosas, acanaladas y rugosas para la absorción de aceite (Fig. 9e). Se seleccionaron tres aceites típicos (aceite de silicona, aceite de motor y aceite de oliva) para comprobar las diferentes muestras.
Las propiedades típicas de estos aceites se enumeran en la Tabla 2. Como se esperaba, entre los tres tipos de materiales de absorción de aceite, las fibras macroporosas mostraron la mayor capacidad de absorción de aceite de 50.58 ± 5.47 g / g, 37.74 ± 4.33 g / g, y 23,96 ± 2,68 g / g para aceite de silicona, aceite de motor y aceite de oliva, respectivamente (Fig. 9f). Particularmente, las fibras macroporosas exhibieron 1,18, 1,17 y 1,19 veces la capacidad de absorción de aceite de las fibras ranuradas para aceite de silicona, aceite de motor y aceite de oliva, respectivamente. Además, las fibras macroporosas exhibieron 1,29, 1,24 y 1,26 veces la capacidad de absorción de aceite de las fibras rugosas para aceite de silicona, aceite de motor y aceite de oliva, respectivamente. Estos resultados deben atribuirse al hecho de que las fibras macroporosas tienen el área superficial más alta, mientras que las fibras rugosas tienen el área superficial más baja entre todas las muestras. Entre los tres tipos de aceite estudiados, todas las muestras analizadas exhibieron la mejor capacidad de absorción de aceite de silicona, posiblemente debido a la mayor viscosidad del aceite de silicona.
Conclusiones
Hemos demostrado un método apropiado y confiable para la formación de nanofibras de PVDF macroporosas, rugosas y ranuradas con poros internos. Para comprender el mecanismo responsable de la formación de fibras de PVDF, probamos tres sistemas de solventes (es decir, mezcla de ACE, DMF y ACE-DMF) bajo diferentes niveles de humedad relativa (5%, 25%, 45% y 65%). %). Descubrimos que no se producía separación de fases a la humedad relativa del 5% utilizando los disolventes anteriores, lo que resultó en la formación de fibras lisas con un interior sólido. Encontramos que la formación de macroporos en la superficie de las fibras con interior sólido a la humedad relativa del 25% debe atribuirse a TIPS debido a la alta presión de vapor de ACE y al mecanismo de nucleación, mientras que la formación de macroporos en la superficie de las fibras con poros interiores a la humedad relativa de 45% y 65% debe atribuirse a la coexistencia de los mecanismos TIPS y VIPS. Además, encontramos que la baja presión de vapor de DMF jugó un papel fundamental en la producción de fibras rugosas con poros en los interiores por VIPS. Mientras que el mecanismo de elongación basado en arrugas jugó un papel clave en la fabricación de fibras ranuradas con una estructura interior porosa. Las fibras macroporosas (> 300 nm) exhibieron el rendimiento más alto de absorción de aceite de 50.58 ± 5.47 g / g, 37.74 ± 4.33 g / gy 23.96 ± 2.68 g / g para aceite de silicona, aceite de motor y aceite de oliva. respectivamente. Es importante destacar que nuestra comprensión de los mecanismos responsables de la formación de las fibras de PVDF macroporosas, rugosas y ranuradas con porosidad interior puede servir como una referencia importante para la fabricación de fibras electrohiladas mediante la regulación del solvente y la humedad relativa.
Abreviaturas
- ACE:
-
Acetona
- DMF:
-
N, N dimetilformamida
- PVDF:
-
Fluoruro de polivinilideno
- CONSEJOS:
-
Separación de fases inducida térmicamente
- VIPS:
-
Separación de fases inducida por vapor
Nanomateriales
- Nanofibras y filamentos para una mejor administración de fármacos
- Producción de fibra de carbono y piezas de fibra de carbono:¿Cuáles son los conceptos básicos?
- Presentación de la estructura atómica y electrónica de las nanofibras de carbono de copa apilada
- Las nanofibras jerárquicas de poliamida 6-ZnO antibacteriana fabricadas por deposición de capas atómicas y crecimiento hidrotermal
- Efecto del tratamiento de recocido in situ sobre la movilidad y morfología de transistores de efecto de campo orgánico basados en TIPS-pentaceno
- Formación y propiedades luminiscentes de Al2O3:nanocompuestos de SiOC en la base de nanopartículas de alúmina modificadas por feniltrimetoxisilano
- Ajuste de las morfologías de la superficie y las propiedades de las películas de ZnO mediante el diseño de la capa interfacial
- Electrohilado sobre sustratos aislantes controlando la mojabilidad y la humedad de la superficie
- Los efectos de acoplamiento de los polaritones de plasma superficial y las resonancias magnéticas dipolo en metamateriales
- Efecto de la morfología y la estructura cristalina en la conductividad térmica de los nanotubos de titania
- Vea las ventajas del rectificado cilíndrico y de superficies interno