¿Comprar nuevo o reconstruir? Un enfoque sistemático para decisiones de mantenimiento difíciles
Existe una idea errónea en el mundo de la fabricación acerca de la confiabilidad y tiene implicaciones significativas para las fábricas, gerentes, técnicos, profesionales de la confiabilidad y resultados finales en las plantas de fabricación de todo el mundo. La idea errónea se basa en un enfoque de confiabilidad basado en el riesgo que puede fallar en identificar adecuadamente las mejoras de productividad, lo que lleva a mayores costos.
El error que cometen algunos profesionales de la confiabilidad es el siguiente:cuando buscan respuestas cuando una máquina o proceso de producción falla en la fábrica, adoptan un enfoque basado en el riesgo para centrarse exclusivamente en el proceso de fabricación en lugar de analizar la causa raíz de la falla. .
Las estadísticas revelan que el 50 por ciento de los pedidos de mantenimiento y reparación requieren una pieza. El control de la confiabilidad y los gastos de capital de mantenimiento y los presupuestos de gastos dificultan la mejora del enfoque de confiabilidad, ya que hasta el 20 por ciento de los gastos operativos de la planta están relacionados con el mantenimiento y el 73 por ciento de los inventarios de MRO de mantenimiento están inactivos.
Afortunadamente, existe un enfoque diferente. El análisis a nivel de proceso es sin duda importante, por lo que los profesionales de la confiabilidad no se equivocan al evaluar el proceso de fabricación cuando intentan mejorar la productividad y aumentar el tiempo de actividad. Donde algunos departamentos de confiabilidad se equivocan es en no profundizar en las causas raíz. Lo que se necesita es un enfoque que lleve el proceso unos pasos más allá, analizando las tendencias de los datos para comprender cómo y por qué fallan los componentes a nivel del sistema.
Este documento examinará los problemas inherentes a un enfoque basado en riesgos que se centra exclusivamente en el análisis a nivel de proceso. Se delineará la solución, que es la expansión de esa estrategia para incluir análisis a nivel de componentes, incluyendo un examen de factores, desarrollo e implementación de acciones correctivas que trabajen para eliminar fallas y mejora continua. Luego, el documento revisará los resultados que los fabricantes pueden esperar cuando modernicen su enfoque de confiabilidad.
Un enfoque de confiabilidad basado en el riesgo
En las instalaciones de fabricación, los ingenieros de confiabilidad generalmente usan una estrategia de mapeo de flujo de valor, identificando cada fase del proceso que convierte las materias primas en un producto terminado y analizando cada paso del flujo de trabajo en detalle. El equipo de producción es una parte clave del flujo de valor, y los ingenieros de confiabilidad tienen la tarea de asegurarse de que todos los componentes sean lo más confiables posible para garantizar el máximo rendimiento.
Como parte de su estrategia de confiabilidad, los ingenieros de confiabilidad identifican cada componente (sistemas eléctricos, hidráulicos, etc.) trabajando metódicamente en cada sistema y evaluando cómo la falla de cualquier componente afectaría la producción.
Por ejemplo, el ingeniero de confiabilidad podría identificar una línea hidráulica como un punto de falla y, utilizando la estrategia basada en el riesgo, crear un plan de mitigación que podría incluir mantener un suministro de repuestos para la línea o construir redundancias para garantizar que las operaciones continúen o mejoren. volver a la normalidad rápidamente en caso de una falla del sistema.
Estos pueden ser pasos necesarios, pero cuando los profesionales de la confiabilidad atacan la confiabilidad desde un nivel de proceso en lugar de a nivel de componentes del sistema, pueden tomar decisiones que conduzcan a gastos costosos e innecesarios.
Ya sean los costos significativos asociados con el reemplazo de sistemas de procesos complejos o el bloqueo de capital en un inventario de componentes de MRO que quizás nunca se implementen, el enfoque de confiabilidad basado en el riesgo es un enfoque ineficiente y costoso para prevenir fallas en la línea de producción.
El problema con el enfoque basado en el riesgo es que no llega lo suficientemente lejos, ya que no aborda la causa raíz de la falla, que probablemente sean los componentes. Hay varios puntos de falla para cualquier componente dado.
Los componentes antiguos o los productos obsoletos, los defectos de diseño y las piezas mal identificadas son solo algunos ejemplos de los factores que pueden provocar que un equipo falle a nivel de componente.
Para modernizar verdaderamente su enfoque de confiabilidad, los profesionales de la confiabilidad deben comprender cómo y por qué fallan los componentes a nivel del sistema. Un enfoque de confiabilidad a nivel de componentes define mejor la causa raíz de la falla y reduce las inversiones en inventario y futuras inversiones de CAPEX.
Es importante recordar que hay una historia detrás de cada componente que falla; Los profesionales de la confiabilidad deben tomar medidas para asegurarse de que la historia no se pierda en los contenedores de basura y chatarra. La confiabilidad, el mantenimiento y las piezas de repuesto juegan un papel crucial, como se ilustra en la Figura 1.
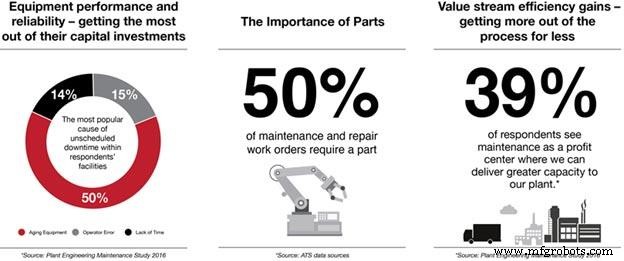
Figura 1. La importancia de la confiabilidad, el mantenimiento y las piezas de repuesto
Considere el ejemplo de la vida real de un variador de servomotor envejecido, que también resulta ser un producto obsoleto que causa múltiples fallas en la línea de producción. Utilizando el enfoque basado en el riesgo, el ingeniero de confiabilidad determina que las fallas aleatorias de la placa indican una unidad más allá de su vida útil y puede implementar un plan de CAPEX para reemplazar la base de instalación y minimizar las demoras en la producción.
Sin embargo, si el ingeniero de confiabilidad sigue una estrategia a nivel de componentes, el examen del punto de falla incluiría un análisis de la causa raíz que determina que las fallas aleatorias de la placa de circuito se deben a la antigüedad.
El ingeniero de confiabilidad podría desarrollar un procedimiento de reconstrucción para la placa de circuito, reemplazando los componentes viejos con componentes premium más nuevos. En un escenario de la vida real, este enfoque resultó en una reducción del 54 por ciento en fallas.
Al abordar la causa raíz del problema de esta manera en lugar de centrarse exclusivamente en las soluciones a nivel de proceso, el ingeniero de confiabilidad no solo pudo extender la vida útil de los componentes sino también disminuir sus tasas de falla con el tiempo. El gráfico de tendencias ilustrado en la Figura 2 a continuación muestra la reducción de fallas correlacionadas con la evolución de los estándares de los procedimientos de reconstrucción.

Figura 2. Reducción de la tasa de fallas correlacionada con la evolución de los estándares mínimos
Los problemas de diseño también pueden contribuir a fallas en los equipos de producción. Por ejemplo, un ingeniero de confiabilidad analiza una falla recurrente del tablero de control en un motor y determina que falla porque el tablero de control se sobrecalienta.
Si el ingeniero de confiabilidad estuviera considerando solo factores a nivel de proceso, la acción correctiva podría ser establecer un mínimo / máximo de inventario para garantizar que haya un stock de piezas de repuesto del motor impulsor disponible para minimizar las demoras en la producción.
Sin embargo, si el ingeniero de confiabilidad sigue una estrategia a nivel de componentes, el examen del punto de falla incluiría un análisis de la causa raíz que descubre una falla de diseño. En el ejemplo de la vida real, se encontró que el variador de frecuencia del motor tenía un tablero de control que estaba ubicado demasiado cerca de un disipador de calor, lo que provocó que los capacitores fallaran.
Después de identificar la causa raíz, el fabricante implementó un plan correctivo que incluía un retiro proactivo en otras instalaciones y una solución de ingeniería que resultó en la reubicación del tablero de control lejos del disipador de calor, lo que resultó en una reducción del 96 por ciento en fallas, como ilustrado en la Figura 3 a continuación.
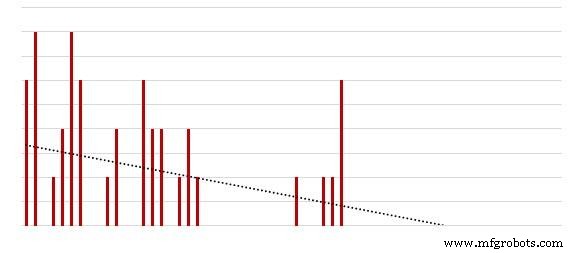
Figura 3. Reducción de la tasa de desechos
Un tercer ejemplo de la vida real de cómo un enfoque a nivel de proceso puede generar gastos innecesarios y un aumento de incidentes de fallas involucra a una fábrica que tuvo un problema con instalaciones incorrectas de transductores de presión debido a la identificación errónea de las piezas.
El fabricante almacenó varios modelos de transductores para una variedad de aplicaciones con un solo número de pieza. Según el enfoque basado en el riesgo, la acción correctiva fue establecer un mínimo / máximo de inventario para garantizar que el stock estuviera disponible cuando fallaran los transductores de presión.
Un ingeniero de confiabilidad realizó una evaluación a nivel de componentes e identificó el problema con los transductores de presión instalados incorrectamente. El ingeniero de confiabilidad implementó un plan correctivo para almacenar transductores según los parámetros de presión establecidos y establecer nuevos SKU para cada parámetro. Como resultado, las fallas disminuyeron un 37 por ciento a medida que se implementó el plan, como se ilustra en el cuadro de la Figura 4 a continuación.
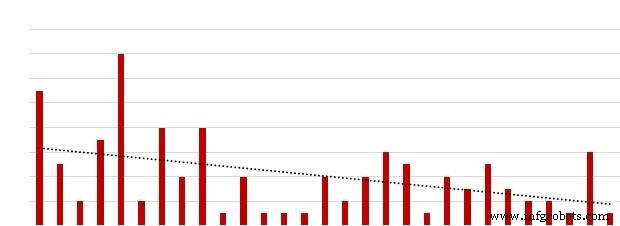
Figura 4. Disminución de la falla del transductor
Como muestran estos tres ejemplos, comprender cómo y por qué fallan estos componentes a nivel del sistema es la clave para establecer un verdadero rendimiento de confiabilidad. Al profundizar más allá del nivel de proceso, los ingenieros de confiabilidad pudieron analizar las causas raíz y desarrollar soluciones que mejoraron el tiempo de actividad, redujeron los gastos operativos y aumentaron la eficiencia. Las nuevas tecnologías también pueden desempeñar un papel clave en el logro de la eficiencia.
Por ejemplo, la fabricación aditiva (impresión 3-D) es una tecnología emergente que también se puede utilizar para mejorar la confiabilidad a nivel de componentes. Si bien la tecnología de fabricación aditiva está cambiando rápidamente, es un método eficaz para diseñar soluciones que eviten el desgaste prematuro y las fallas.
Los prototipos se pueden fabricar de una manera muy rentable para garantizar que el diseño cumpla con los requisitos de ajuste, forma y función de la aplicación de diseño original. Se pueden utilizar varios materiales, como el titanio, en el proceso de fabricación aditiva para hacer que los componentes sean mucho más duraderos en sus entornos operativos.
Hay muchos ejemplos que ilustran la eficacia de un enfoque a nivel de componentes. Al capturar información sobre fallas de componentes, los ingenieros de confiabilidad pueden identificar mejoras simples de "ganancia rápida" y crear procedimientos de trabajo estándar y programas de capacitación de técnicos que dan como resultado ahorros importantes.
Un enfoque de confiabilidad basado en componentes
Los departamentos de confiabilidad que van más allá de un análisis a nivel de proceso para enfocarse en problemas a nivel de componentes dentro de los subsistemas pueden mejorar significativamente los resultados, pero hacerlo requiere una forma diferente de pensar sobre los puntos de falla y las estrategias de mitigación.
Los profesionales de confiabilidad que participan en la transición a una estrategia a nivel de componentes pueden beneficiarse de perspectivas externas, como los métodos utilizados por los fabricantes de equipos originales (OEM) y la experiencia de terceros.
Las mejoras fundamentales pueden ser oportunidades adicionales para mejoras basadas en la confiabilidad y pueden incluir la implementación de procesos de almacén, incluidas las 5-S, las mejores prácticas de identificación y almacenamiento de piezas, los procedimientos de certificación de pruebas para los componentes utilizados para la resolución de problemas y el seguimiento del núcleo para garantizar que la historia no lo haga. ser arrojado a la papelera de reciclaje.
El desarrollo de estándares de mantenimiento también puede ser un componente clave, como la participación de recursos técnicos en el proceso de RCA y lecciones de un solo punto que documenten el conocimiento tribal a nivel de componente.
Adoptar completamente el nuevo paradigma de confiabilidad requiere mirar más allá de las teorías abstractas y aprovechar la experiencia práctica para desarrollar nuevas soluciones. Tener acceso a la experiencia del equipo de manera más amplia puede conducir a mejores resultados y un fuerte compromiso de generar valor.
Rendimiento de confiabilidad real
Lamentablemente, el enfoque de la confiabilidad basado en el riesgo puede generar mayores costos para los fabricantes. Sin embargo, sigue siendo un análisis valioso y debe seguir siendo una función central del profesional de la confiabilidad.
Pero una comprensión moderna de la confiabilidad incluye el reconocimiento de que es probable que la verdadera causa raíz de la falla sean los componentes, más que el proceso de producción en sí. Además, implica adoptar nuevas tecnologías, análisis de vanguardia y mejores prácticas para lograr un resultado más confiable y rentable.
Un ejemplo de rendimiento de confiabilidad real en acción se puede encontrar en la experiencia de un líder reconocido en llantas de reemplazo para vehículos comerciales y de pasajeros que implementó un nuevo enfoque para administrar su inventario de piezas reparables.
Un profesional de confiabilidad externo evaluó la situación única de la empresa y desarrolló un plan para administrar su programa de piezas a través de un programa de gestión de piezas reparables in situ. Con un programa de gestión de piezas más proactivo, el fabricante vio caer las fallas en las piezas en un 53 por ciento. El programa de administración de piezas reparables también pudo reducir el inventario de piezas en un 15 por ciento, lo que resultó en ahorros significativos.
Con un mayor tiempo de actividad y disponibilidad de la máquina, el fabricante pudo satisfacer de manera más eficiente la creciente demanda de sus productos. Un gerente senior de la división de mantenimiento corporativo de la empresa observó que al obtener acceso a la experiencia de terceros y al concentrarse en mejorar la confiabilidad de los activos reparables de la empresa, el fabricante pudo reducir sus costos generales al tiempo que mejoraba la efectividad de la fabricación.
En otro ejemplo que ilustra el valor del verdadero rendimiento de confiabilidad, un proveedor automotriz de primer nivel trabajó con un profesional de confiabilidad para mejorar los problemas a nivel de componentes e identificó un problema con la vida útil de los husillos de bolas. La confiabilidad fue un problema porque los husillos de bolas se instalaron en varias máquinas y tuvieron que solicitarse a Alemania. Eso significó que el proveedor automotriz tuvo que lidiar con plazos de entrega largos y / o esporádicos.
Un enfoque más inteligente de la confiabilidad
Las empresas de fabricación de todo el mundo están perdiendo una oportunidad de oro al centrarse exclusivamente en las mejoras a nivel de proceso, que son una parte importante de una estrategia de confiabilidad general, pero que no son lo suficientemente profundas como para capturar todas las ganancias de productividad y ahorros de costos disponibles.
Al descuidar el análisis de la causa raíz de las fallas a nivel de componentes y subsistemas, los departamentos de confiabilidad que se adhieren a un enfoque basado en el riesgo les están costando tiempo y dinero a sus empresas.
Como ilustran los ejemplos cubiertos en este documento, existe una mejor manera. Los puntos de falla a menudo ocurren a nivel de componentes. Los expertos en confiabilidad que amplían su enfoque más allá de una revisión a nivel de proceso para incluir un análisis de la causa raíz pueden identificar y mitigar los problemas causados por factores como fallas de diseño, antigüedad de los componentes e instalación incorrecta.
Al obtener una mejor comprensión de cómo y por qué fallan los componentes a nivel del sistema y cambiar su forma de pensar para incluir nuevas perspectivas, los profesionales de la confiabilidad pueden mejorar los resultados en todos los niveles. Con la ayuda de nuevas tecnologías como las piezas habilitadas para IoT y el uso de análisis de datos para estimar el comportamiento de manera más eficaz e implementar estrategias como programas de mantenimiento predictivo, los profesionales de la confiabilidad modernos pueden hacer que la máquina funcione para ellos para entregar piezas confiables, procesos confiables y ahorros confiables.
Mantenimiento y reparación de equipos
- El caso del mantenimiento móvil:Fiix se detiene en el podcast Asset Reliability @ Work
- ¿Qué es la cultura de confiabilidad?
- Los mejores en mantenimiento y confiabilidad
- Outsourcing de mantenimiento:un modelo de excelencia operativa
- Aero estándar alabado por idea de mantenimiento y confiabilidad
- Los detalles importan en el mantenimiento y la confiabilidad
- SMRP es valioso para los profesionales de M&R
- Fiabilidad orientada a la familia
- SMRPCO obtiene la aprobación para el reembolso de las tarifas del examen según la factura de GI
- 5 claves para mantener la confiabilidad del equipo
- Boeing presenta una nueva herramienta de mantenimiento de registros para aerolíneas