Propiedades de resistencia a la corrosión de las aleaciones de aluminio
En las fundiciones de metales, el aluminio y sus aleaciones se encuentran entre los principales materiales de fundición debido a sus extraordinarias ventajas sobre otros metales. La aleación de aluminio tiene ductilidad, alta colabilidad, alta resistencia y, sobre todo, alta resistencia a la corrosión en diferentes ambientes y agentes químicos.
La resistencia a la corrosión del aluminio es creada por una película de óxido inerte formándose sobre una superficie metálica que proporciona una capa protectora, evitando que la superficie de aluminio quede expuesta a su entorno.
Se forma una película de óxido en la superficie debido a la reacción química de la superficie de aluminio con el oxígeno y el agua. De hecho, esta es la primera etapa de la corrosión del metal. Aunque la película de óxido tiene un grosor de solo 5-10 nm, previene la oxidación del metal tan pronto como se expone a un entorno oxidante como el agua.
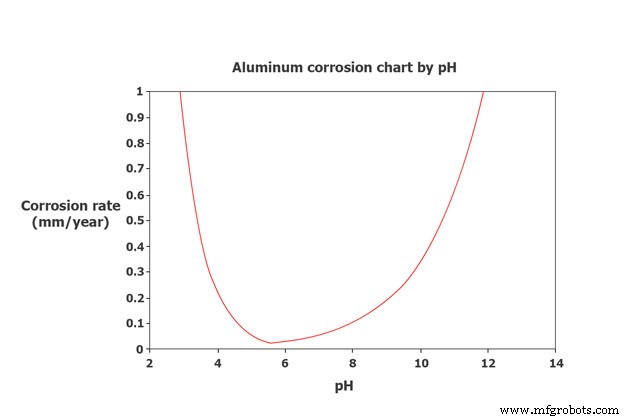
En la mayoría de los entornos, la velocidad de corrosión de las aleaciones de aluminio disminuye con el tiempo, en parte porque la estabilidad de la película de óxido determina su resistencia a la corrosión, que depende del valor del pH. del medio ambiente.
Por lo general, las películas de óxido son estables en el rango de pH de aproximadamente 4 a 8. Si el pH está por debajo de 4, disolverá los ácidos, y si el pH está por encima de 8, disolverá el álcali para crear sólidos cristalinos, que es el óxido.
En la industria de la fundición, para mejorar las propiedades de fundición del aluminio y reducir los defectos de fundición del aluminio, las fundiciones de metal suelen añadir un mayor contenido de Si. a la aleación de aluminio, lo que hace que la corrosión localizada sea más probable y desalienta el anodizado para reducir la resistencia a la corrosión del aluminio fundido.
Para optimizar la resistencia a la corrosión de las aleaciones de aluminio fundido, es necesario comprender la relación entre el proceso de producción de la aleación de aluminio y la microestructura del aluminio. Por lo tanto, realizamos una evaluación exhaustiva de la investigación sobre la corrosión de los metales en general y aleaciones de aluminio en particular según varios métodos de fundición de aluminio, como fundición en arena, fundición a presión a baja presión, etc.
Este es el artículo más detallado, completo y sencillo que puede encontrar sobre la corrosión de las aleaciones de aluminio, que es altamente reactiva y tiene varias propiedades sobresalientes.
Echemos un vistazo más de cerca con nosotros:¡fundición de fundición VIC!
Naturaleza corrosiva de las aleaciones de aluminio
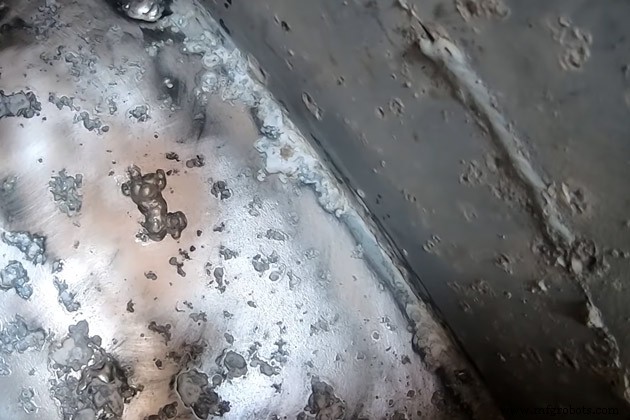
La corrosión de las aleaciones de aluminio en un entorno sustancial se debe a las reacciones catódicas y anódicas. coexistiendo a la misma velocidad en la superficie metálica.
La reacción catódica es el proceso de oxidación del metal, y la reacción anódica es la reducción de la sustancia en el medio ambiente. La oxidación y la reducción ocurren simultáneamente y los electrones se transfieren entre los dos reactivos. Por lo tanto, el metal transporta electricidad.
Reacción de oxidación :Al → Al 3+ + 3e
Reacción redox de hidrógeno :H + + e → ½ H2
O reacción redox de oxígeno :O2 + 2H2 O + 4e – → 4OH –
En esencia, estas reacciones ocurren en la microestructura de la aleación. La microestructura de una aleación de aluminio está determinada por los elementos de la aleación y por el tratamiento termomecánico.
Con aleación de aluminio puro sin elementos metálicos añadidos, no hay posiciones de metal dentro de la microestructura. Como resultado, es poco probable que ocurra la reacción catódica, lo que minimiza la posibilidad de corrosión.
Con respecto a las aleaciones de aluminio heterogéneas mezcladas con componentes de aleación, se forman partículas intermetálicas para producir precipitados de 1-300 nm de diámetro. Los precipitados constan de diferentes características electroquímicas que son las zonas atacadas por la corrosión.
Límite de corrosión de aleaciones de aluminio
La resistencia del aluminio a la corrosión aumenta a medida que aumenta su pureza. Sin embargo, debido a la alta ductilidad del aluminio, cuanto más pura es la aleación de aluminio, menos aplicaciones ofrece.
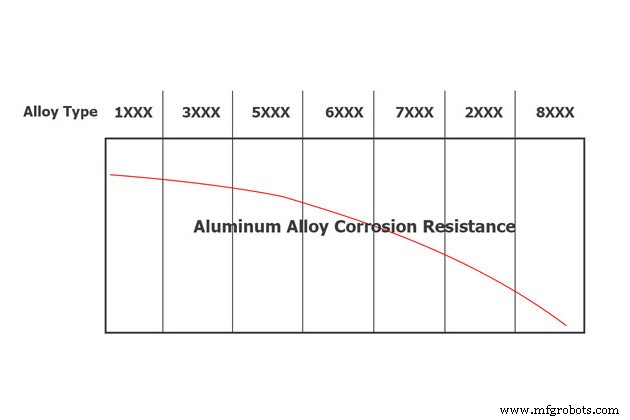
Por lo general, los metales se agregan para aumentar la dureza y la colabilidad del aluminio. , lo que conduce a una disminución de su resistencia a la corrosión.
A continuación se muestran los análisis de la resistencia a la corrosión de las aleaciones de aluminio.
1. La aleación de la serie 1xx.x:Aluminio comercialmente puro
La aleación de la serie 1xx.x es la aleación más pura, contiene aproximadamente un 99,93 % de aluminio puro y tiene una tasa de corrosión medida muy baja, aproximadamente 0,8 µA en 1 cm 2 a 2,3 cm 2 .
Debido a la excelente resistencia a la corrosión, la serie 1xx.x no se aplica mucho a diario debido a su baja dureza.
Algunas de sus aplicaciones incluyen aleaciones de la serie 100 utilizadas en la industria del embalaje de papel aluminio y como material para utensilios de cocina. También se utiliza para producir aleaciones secundarias o como recubrimiento para otras series.
2. La aleación de la serie 2xx.x:Aluminio – cobre
La aleación de aluminio de la serie 2xx.x contiene un alto contenido de Cu, alrededor del 4-10 %, por lo que tiene altas propiedades mecánicas y se utiliza en estructuras, especialmente en la industria de la construcción aeroespacial.
Sin embargo, la adición de Cu a la aleación afectará su durabilidad. . Aunque la dureza mejora significativamente (alrededor de 500Mpa), es susceptible a la corrosión en ambientes industriales con humedad.
La serie 200 tiende a formar defectos de fundición, por lo que a menudo se limita a la producción de patrones simples de fundición. .
Una prueba electroquímica con 0.5M H2 SO4 solución midió la tasa de corrosión de aproximadamente 0,45 µA/cm 2 , en comparación con la medición en solución de NaCl al 3%. Este experimento se realizó con tres aleaciones de Al-Cu con una proporción de Cu de 5 %, 10 % y 15 %, respectivamente, y se concluye que la velocidad de corrosión de las 3 aleaciones fue la misma.
Se realizó otro experimento utilizando el método de solidificación direccional, investigando el efecto de la velocidad de enfriamiento y el contenido de Cu de la aleación Al-4.5%Cu.
Se tomaron tres muestras en tres posiciones diferentes de la superficie del enfriador de metal. Observando a nivel microscópico, muestra una mejor velocidad de corrosión cuando la velocidad de enfriamiento es mayor.
3. La aleación de la serie 3xx.x:Aluminio – Manganeso
La aleación de aluminio de la serie 3xx.x generalmente está disponible en láminas delgadas. Es una aleación de aluminio con la adición de silicio y un componente de manganeso de alrededor del 1% para mejorar la resistencia a la corrosión en la solución sólida. La resistencia de esta aleación es media, unos 110 MPa.
Si se realizan trabajos en frío y recocido, la serie 3xxx logrará excelentes propiedades mecánicas. También tienen altas propiedades de fundición, por lo que hasta el 90% del aluminio fundido mundial pertenece a la serie 300. Por lo tanto, la investigación de la corrosión con aleaciones de aluminio fundido se suele realizar en la serie 300. .
Se han realizado muchos experimentos sobre la corrosión de aleaciones de la serie 3xx.x, principalmente con tecnología de fundición por gravedad y fundición a presión.
Fundición de aleación de aluminio mediante tecnología de fundición por gravedad
Un estudio demostró que la densidad de corriente de corrosión y el parámetro de impedancia de Al-8%Cu-3%Si inducen una mayor resistencia a la corrosión que el Al-6%Cu-1%Si.
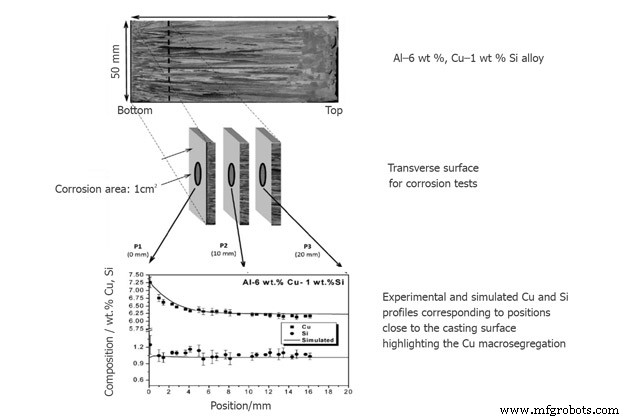
Las pruebas de corrosión se realizan en la posición de la sección transversal de fundición, a 0, 10 y 20 mm de la superficie de fundición fría.
Este experimento muestra que el Si y el espacio entre los brazos de las dendritas secundarias (SDAS) dependen unos de otros y afectan la resistencia a la corrosión de Al-6%Cu-1%Si.
En la matriz de aluminio α, las aleaciones de aluminio fundido forman fácilmente compuestos intermetálicos . La presencia de manganeso en la serie 300 compensa el efecto catódico del Fe en los compuestos intermetálicos, haciéndolos menos corrosivos.
Los investigadores también realizaron experimentos sobre los efectos del Sr en la corrosión de las aleaciones de aluminio.
Las microobservaciones mostraron además el cambio del eutéctico de silicio de una morfología gruesa y delgada a una morfología de fibra conectiva.
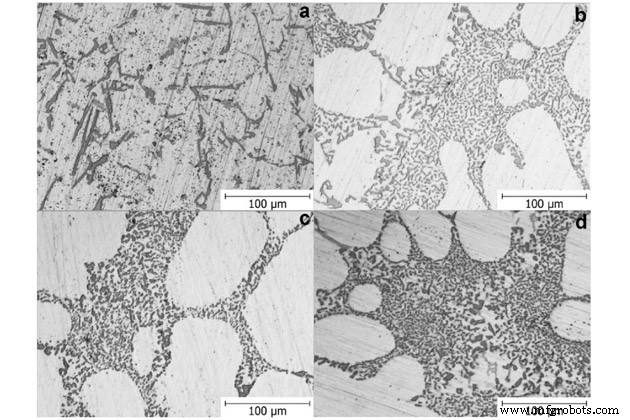
una. sin Sr agregado
b:Sr 120 ppm
c:Sr 170 ppm
d:Sr 250 ppm
Conclusión :La morfología de las fibras unidas del silicio eutéctico mejora la resistencia a la corrosión de las aleaciones de aluminio. Los niveles detallados de resistencia a la corrosión se muestran en la siguiente tabla:
Adición Sr | Antes | Después |
120 ppm | 13,8 µA/cm 2 | 0,42 µA/cm 2 |
150 ppm | 10,2 µA/cm 2 | 1,47 µA/cm 2 |
Fundición de aleación de aluminio con tecnología HPDC (fundición a presión a alta presión)
Según los documentos registrados, este experimento roció metal a tres temperaturas diferentes:579°C, 643°C y 709°C con dos presiones de inyección de 35 MPa a 70 MPa. La observación de la microestructura muestra que a baja temperatura, la dendrita del aluminio se fragmenta y a alta temperatura, la dendrita se refina más.
Este experimento concluye que cuanto mayor es la porosidad, menor es la resistencia a la corrosión de la aleación de aluminio. La porosidad aumenta gradualmente según los siguientes resultados experimentales:
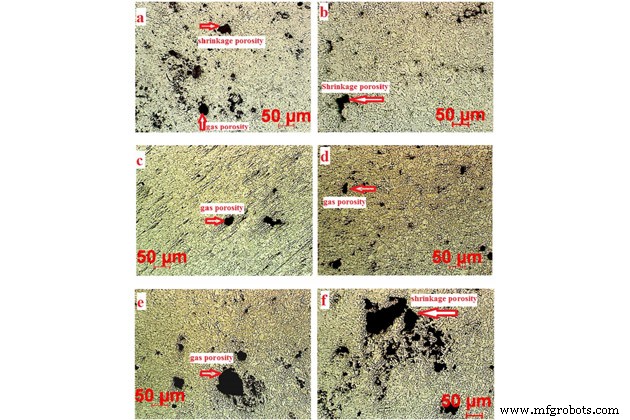
a:579 °C / 35 MPa (3,15 % de porosidad)
b:579 °C/70 MPa
c:643 °C/35 MPa
d:643 °C/70 MPa
e:709 °C/35 MPa
f:709°C / 70 MPa (4,91 % de porosidad)
Con la tecnología HPDC, se crean burbujas de aire debido a la alta tasa de inyección, lo que da como resultado una fundición de alta porosidad y provoca defectos de porosidad de gas.
4. La aleación de la serie 5xx.x:Aluminio – Magnesio
La serie 5xx.x contiene menos del 6 % de Mg. El magnesio tiene una solubilidad en aluminio que mejora la resistencia a la corrosión y la dureza de la aleación. La dureza de la serie 500 es superior a 380MPa.
La serie 500 puede resistir la corrosión en ambiente de agua de mar , por lo que se aplica en la industria marina.
La investigación sobre la resistencia a la corrosión de la aleación Al-3%Mg-1%Si mediante el método de fundición por gravedad y fundición continua encontró una corrosión severa en la zona libre de precipitados.
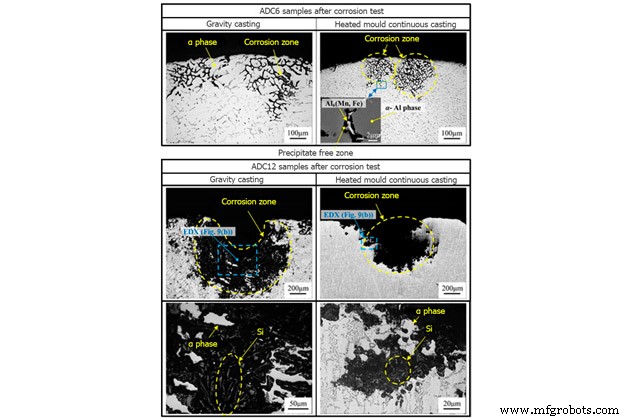
La figura anterior muestra los resultados del experimento; Con la tecnología de fundición por gravedad, la aleación Al-3Mg-1Si se corroe a un ritmo mayor que la fundición continua. De hecho, la tecnología de colada continua tiene una tasa de enfriamiento más rápida , lo que lleva a una proporción de solución sólida más alta .
La Serie 500 también tiene un problema de corrosión:un trastorno de alta densidad que puede causar Mg2 de fase β perjudicial Al3 precipitación sobre aleaciones con> 3 % de Mg y exposición a altas temperaturas durante largos períodos.
5. La aleación de la serie 6xx.x:Aluminio – Magnesio – Silicio
La aleación de aluminio de la serie 6xx.x a base de silicio aumenta la fluidez y reduce el punto de fusión.
Esta aleación tiene una dureza> 300 MPa, principalmente en forma extruida y en forma de lámina.
Se añaden silicio y magnesio a la aleación, por encima del 1,4 % aumentará la resistencia al envejecer.
La serie 600 obtiene buena resistencia a la corrosión , por lo que se utiliza ampliamente en el entorno marino y en la fabricación de motores de trenes.
6. La aleación de la serie 7xx.x:Aluminio – Zinc – Magnesio
La aleación de la serie 7xx.x tiene una durabilidad de hasta 580 MPa; tan alta resistencia se logra debido a la fase η (MgZn2 ) precipitación. Por ello, es muy utilizado en la industria aeroespacial .
La desventaja de la serie 700 es la reducción de la resistencia a la corrosión; son susceptibles a la erosión ambiental y al agrietamiento por corrosión bajo tensión.
Para reequilibrar la resistencia a la corrosión, se realizaron tratamientos térmicos complejos, como tratamientos térmicos secundarios.
7. La aleación de la serie 8xx.x:Aluminio – Litio
La aleación de aluminio de la serie 8xx.x se mezcla con el elemento Li, con una solubilidad en aluminio de hasta el 16 %.
La serie 800 es muy ligera y obtiene una gran rigidez; por lo tanto, tiene un alto potencial para el uso de la industria aeroespacial.
En el pasado, las aleaciones de aluminio que contenían litio tenían la tasa de corrosión más alta. entre todas las aleaciones de aluminio; pero hoy en día, las aleaciones de Al-Li con Cu añadido han superado esta limitación.
8. La aleación de la serie 9xx.x:Aluminio – Nikel
Aleación de la serie 9xx.x con níquel agregado para aumentar la dureza pero reducir la ductilidad y la resistencia a la corrosión .
Un estudio sobre aleaciones de Al-5%Ni:tomó 1 muestra de la aleación en la posición P1, que está a 10 mm del borde del molde con una velocidad de enfriamiento de aproximadamente 8 °C/s, y 1 muestra a 60 mm de distancia del borde del molde. borde del molde a un enfriamiento de 0,6 °C/s.
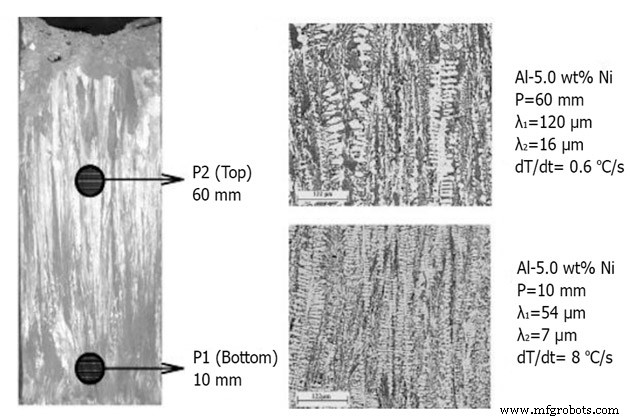
El resultado fue que la tasa de corrosión de la posición P2 es de 1,5 µA/cm 2 , y en la posición P1 es 3,5 µA/cm 2 .
Obtenga más información sobre los tipos de aluminio:https://vietnamcastiron.com/types-aluminum/
Efecto de los elementos de aleación sobre la corrosión de la aleación de aluminio
1. El efecto del magnesio
Se agrega magnesio a la aleación de aluminio para mejorar las propiedades mecánicas. Mg reduce la velocidad de reacción de la reacción catódica cuando está presente en solución sólida (debido a la baja densidad de corriente de intercambio de Mg) y aumenta la resistencia a la corrosión.
2. El efecto de Si
Si se agrega con Mg crea un Mg2 Precipitado de Si que aumenta la dureza de la aleación de aluminio pero provoca corrosión local . Agregar Si en exceso provocará agrietamiento por corrosión bajo tensión debido a la aparición de Si en el límite y acelerará la reacción catódica.
3. El efecto del Cu
Similar al Mg, la presencia de Cu hace que una aleación de aluminio forme una reacción catódica localizada que provoca corrosión. Sin embargo, el objetivo principal de las aleaciones de las series 600 o 700 es agregar Cu a la composición para reforzar la dureza. , no para el objetivo anticorrosión.
4. El efecto del Zn
Agregar Zn a la aleación de aluminio puede formar la fase τ Al-Mg-Zn en lugar de la fase β Al3 mg2 , que provoca fisuración por corrosión bajo tensión . Las aleaciones que se usan en la industria aeroespacial todavía usan Zn para formar un precipitado de dureza mejorada.
5. El efecto del Fe
En el proceso de producción, la aleación de aluminio a menudo mezcla Fe en la composición. El proceso de eliminación de Fe es muy costoso. El Fe es difícil de disolver en la aleación y mantiene una reacción catódica, lo que resulta en reducción de la resistencia a la corrosión. . El Fe combinado con Mn o Cu en la aleación también es un factor que impide la resistencia a la corrosión.
6. El efecto del magnesio
Incluir manganeso en la aleación de aluminio reducirá la concentración de Fe y aumentará la resistencia a la corrosión. Sin embargo, si la cantidad de Mn supera el límite de solubilidad (1,25 % en peso), dará lugar a la formación de Al6 Mn, que aumenta la reacción catódica y provoca problemas de corrosión .
7. El efecto de Li
El litio juega el papel de aumentar la dureza de la aleación de aluminio, por lo que la aleación Al-Li se usa ampliamente en el campo de la aviación. Sin embargo, apareció Li a lo largo de los límites de los granos, lo que provocó un aumento rápido en la tasa de corrosión y la propagación local de la corrosión. .
Tipos de corrosión de aleaciones de aluminio
Corrosión uniforme
La corrosión uniforme es un tipo de corrosión común que ocurre cuando el pH es demasiado alto o demasiado bajo. . Todas las áreas superficiales de aleación se erosionan al mismo ritmo. La película de óxido de aluminio no puede proteger el metal y se erosionará gradualmente.
La corrosión uniforme se puede identificar y manejar fácilmente usando pintura o revestimientos a un nivel de corrosión permitido.
Con aleaciones de aluminio se pueden utilizar inhibidores como ácido crómico o protección catódica.
Corrosión galvánica
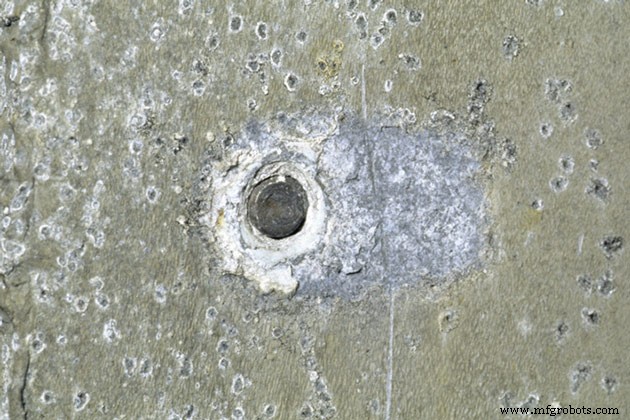
La corrosión galvánica ocurre cuando una aleación de aluminio se conecta a un material conductor , reaccionando con más fuerza en un entorno conductivo . En el punto de contacto entre el aluminio restante y el metal se formará un ataque de corrosión. Por ejemplo, en soldaduras metálicas, la corrosión se formará concentrada en el lado del metal menos noble.
La corrosión galvánica también ocurre con aleaciones de aluminio heterogéneas que contienen compuestos intermetálicos. Por ejemplo, en las aleaciones de aluminio que contienen cobre, la corrosión aumenta significativamente si se sumerge en agua o en entornos hostiles.
En el caso de que el aluminio y el acero inoxidable entren en contacto en un ambiente seco, el nivel de corrosión solo aumentará ligeramente. Pero en un ambiente húmedo, aumentará notablemente.
Para evitar que se produzca corrosión galvánica, es necesario separar los dos metales insertando un material aislante como caucho de neopreno en la posición de contacto de los dos metales o rediseñando, de modo que los dos metales no se toquen entre sí.
Corrosión en grietas
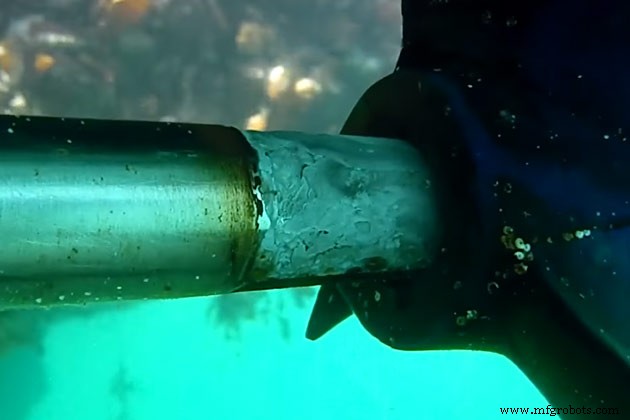
La corrosión por grietas se origina en espacios o juntas y luego se propaga a áreas de la superficie en un ambiente húmedo.
Un ejemplo típico es la ubicación donde el perno y el metal al que está atornillado se oxidan, en presencia de humedad o agua que ingresa al espacio.
Corrosión por picaduras
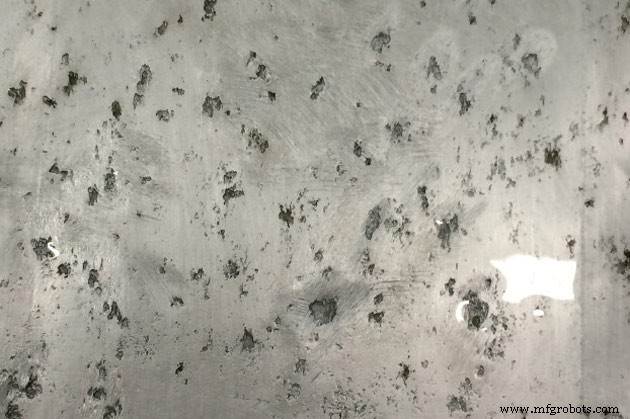
La corrosión por picadura es una forma de corrosión local que ocurre en una superficie metálica cuando se empapa en un ambiente húmedo. .
La corrosión por picadura generalmente ocurre cuando la superficie de la aleación se cubre con una película delgada de óxido, que se forma durante la fabricación del metal o la reacción con el medio ambiente.
Con respecto a la aleación de aluminio, la película de óxido de aluminio se forma muy rápidamente y la unión crea una barrera entre las superficies metálicas. Sin embargo, esto aún no evita el contacto entre la humedad y los agujeros en la superficie metálica.
Cuando aparecen vacíos en la superficie debido al impacto de una celda local, estos agujeros, si no pueden repararse mecánicamente por sí mismos, se llenarán con productos corrosivos que parecen nódulos.
Corrosión Intergranular
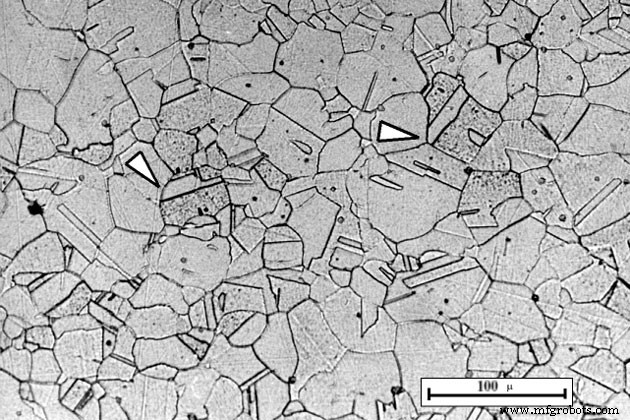
La corrosión intergranular es un ataque de corrosión local a lo largo del límite de grano o adyacente al límite de grano del metal, creando un camino de corrosión.
El límite de grano es una concentración de partículas extrañas, la desviación aquí hace que sea más activo que el área interna, por lo que la tasa de corrosión aquí es más rápida.
El nivel de corrosión puede variar dependiendo de su microestructura , que a su vez depende del tratamiento térmico. El tratamiento térmico produce precipitados de partículas y puede hacer que el límite de grano más activo y destruye rápidamente el material.
Corrosión por Exfoliación
La corrosión por exfoliación es la corrosión que aparece a lo largo de los límites de grano que corren paralelos a la superficie metálica. En comparación con el metal base, el producto corrosivo es más pesado, lo que obliga al metal a separar capas. , haciendo que el metal se hinche .
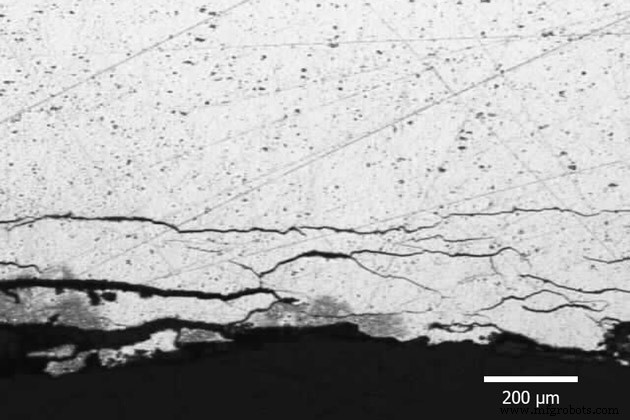
La corrosión por exfoliación suele ocurrir en las aleaciones Al-Mg-Cu y Al-Zn-Cu.
La extensión de la corrosión depende principalmente de la composición y distribución del precipitado en el límite de grano.
Agrietamiento por corrosión bajo tensión
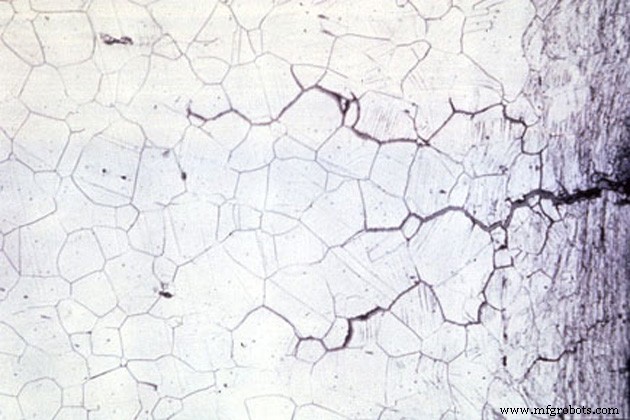
El agrietamiento por corrosión bajo tensión (SCC) es el deterioro de las propiedades mecánicas de una aleación bajo la influencia del estrés y un ambiente corrosivo. Inicialmente, debido a la tensión mecánica, aparecen pequeñas grietas, luego, en el ambiente corrosivo, las grietas se desarrollan muy rápidamente, creando una rápida destrucción del material.
De 8 aleaciones de aluminio, las aleaciones de las series 2xx.x, 5xx.x y 7xx.x son las más susceptibles a SCC.
El ímpetu de dos agentes:la tensión de tracción estática y el entorno específico inducen el agrietamiento intergranular o transgranular del metal. SCC puede ocurrir inesperadamente y progresar rápidamente.
El entorno específico es un factor esencial en causar SCC. Solo una concentración muy pequeña de algunos productos químicos altamente activos puede crear una grieta y conducir gradualmente a una destrucción catastrófica de la aleación.
Fatiga por Corrosión
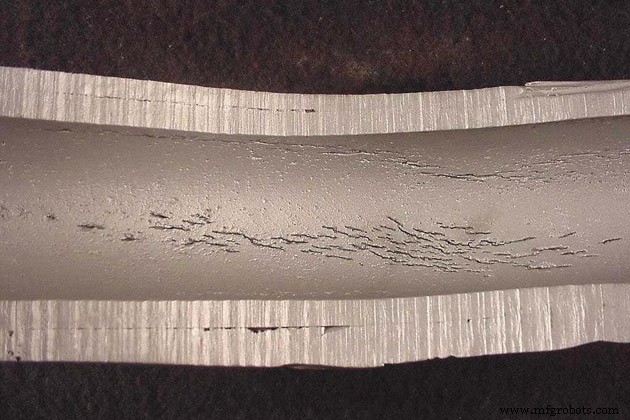
La fatiga por corrosión es la degradación mecánica del material bajo los efectos del estrés y la corrosión cíclica .
Aunque la superficie de aluminio tiene una película de óxido de aluminio naturalmente protegida, esta puede romperse cuando se somete a efectos corrosivos cíclicos.
La resistencia a la fatiga del material disminuye con cada ciclo y no depende de sus condiciones metalúrgicas .
Experimentando la resistencia a la corrosión de la aleación de aluminio en NaCl, la resistencia a la fatiga es de 108 ciclos y su resistencia a la corrosión está en el rango de 25% a 35%, en comparación con la del aire.
Corrosión filiforme
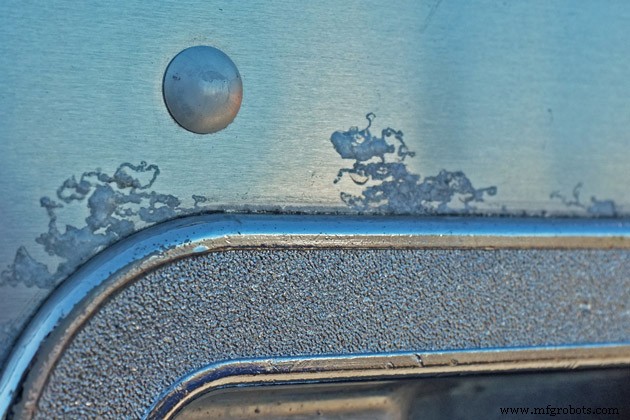
La corrosión filiforme es un caso especial de corrosión en grietas, en el que fibras finas aparecen como finos túneles en direcciones aleatorias y sin bifurcaciones; estas finas fibras contienen productos corrosivos.
La corrosión filiforme puede ocurrir en una superficie metálica desprotegida o debajo de la delgada película protectora de metal, de aproximadamente 0,1 mm de espesor. La película puede ser un revestimiento o una protección contra la corrosión.
Cuando el material entra en contacto con el agua y el oxígeno, hace que los productos corrosivos penetran en el espacio entre el revestimiento y la superficie metálica, especialmente a través de arañazos , expandiéndose así gradualmente en grupos corrosivos.
Resistencia a la corrosión del aluminio
Para resistir eficazmente la corrosión de las aleaciones de aluminio, es necesario aislar completamente la superficie metálica del entorno. . Para conseguirlo, es necesario utilizar un recubrimiento orgánico como pintura.
Sin embargo, pintar sobre una superficie de aluminio no es un proceso fácil porque la superficie del aluminio no tiene porosidad. . Por lo tanto, es necesario promover una película de óxido en la superficie a través del anodizado. o recubrimiento de conversión para mejorar la adherencia de la pintura.
1. Crea un revestimiento en la superficie de aluminio
1.1. Técnica de anodizado
El método más común para resistir la corrosión del aluminio y sus aleaciones es el anodizado. Este es un método para crear una película de óxido relativamente gruesa fuera de la superficie de aluminio para ayudar a resistir la corrosión.
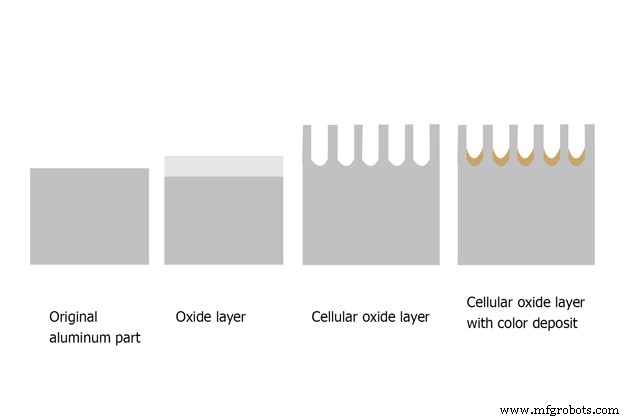
Inhibidores se puede agregar a la capa exterior de la capa anodizada mientras se forma esta capa, o también se puede agregar después de la formación para aumentar el nivel de protección del metal.
Existen diferentes tipos de anodizado:
- Este es un proceso popular y de larga data para desarrollar electroquímica para la película protectora de óxido en la superficie. Se forma una película de óxido controlando rápidamente la oxidación superficial del aluminio. La película es relativamente delgada, de 0,5 μm a 18 μm, y no conduce la electricidad.
- Este método es más ecológico que el anodizado crómico. Utiliza corriente continua y una solución electrolítica, que es ácido sulfúrico, para oxidar la superficie de aluminio. La corriente eléctrica pasó a través de la liberación de oxígeno de la superficie de aluminio, formando una capa de óxido de 1,8 μm a 25 μm. Este proceso crea una capa apretada de espuma en la parte superior y necesita sellado para cerrar los poros.
- Este método utiliza una pieza de aleación de aluminio como ánodo para la electrólisis en un ambiente de agua que contiene ácido sulfúrico, y se selecciona al menos un compuesto del grupo de molibdato, wolframio, vanadato y manganita. El espesor máximo de la capa de óxido es de 50 μm.
- Este método es bastante similar al anodizado con ácido sulfúrico, pero produce una capa de óxido más gruesa que aumenta la resistencia a la corrosión. El espesor de la capa de óxido es de aproximadamente 20 µm a 100 µm y está estrictamente controlado para evitar la deformación térmica.
1.2. Recubrimiento de conversión química
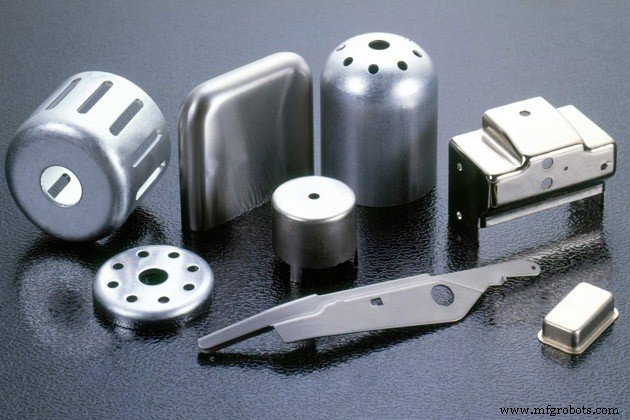
El recubrimiento de conversión química también se conoce como película química. o recubrimiento cromado . Este es el proceso de aplicar cromato al sustrato de metal para crear una superficie resistente a la corrosión, duradera y con conductividad eléctrica estable.
Este revestimiento de conversión es a la vez un inhibidor de la corrosión y una imprimación para una mejor adhesión a la capa final.
Para realizar este procedimiento es necesario sumergir la parte metálica en el químico que contiene el compuesto de cromo durante varios minutos para formar una película del espesor adecuado. El recubrimiento de conversión química es la película que se seca y se endurece.
Este proceso se describe de la siguiente manera:
Reacción redox entre cromo y aluminio:
Cr 6+ + Al 0 → Cr 3+ +Al 3+
Luego reacciona con hidróxido en agua para crear una solución alcalina:
cr 3+ + 3HO – → Cr(OH)3
Al 3+ + 3HO – → Al(OH)3
La solución alcalina se seca y endurece, formando una capa seca, principalmente Cr2 O3 , que tiene un grosor de aproximadamente 0,2-0,3 μm.
Sin embargo, este revestimiento cromado es bastante tóxico. , por lo que hoy en día, la gente usa métodos de procesamiento alternativos como monocapas autoensambladas, química sol-gel, tierras raras, cobalto, etc. Esto está destinado a proteger contra la corrosión del metal de las superficies que han sido eliminadas previamente por partículas IM.
2. Recubrimientos orgánicos
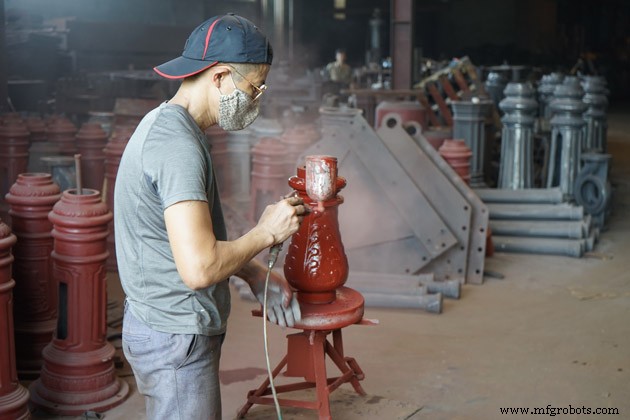
Una vez que la pieza de aluminio se cubre con el ánodo o se convierte químicamente, la superficie está lista para ser recubierta con el revestimiento orgánico. El sistema de recubrimiento orgánico consta de una imprimación y una capa de acabado .
Primer es la capa protectora principal que inhibirá la corrosión cuando se trata de contacto con agua o metal. El acabado aumentará el nivel de protección y también se utilizará con fines estéticos.
Cómo pintar aleaciones de aluminio:https://vietnamcastiron.com/painting-cast-aluminum-process/
Conclusión
From the studies of aluminum alloys based on the chemical basis, microstructure and environment, we can apprehend the crucial factors in aluminum alloy selection and development.
The microstructure determines the mechanical strength and the corrosion performance of the alloy. Gathering information on corrosion types as well as analyzing the corrosion resistance of aluminum alloys will enhance the study of surface treatment.
Increasing the corrosion resistance while ensuring a higher alloy strength requires more intensive research and testing. The current method of hardness enhancement, which simply precipitating the crystalline matrix, is no longer possible.
Read more about the most popular aluminum casting defect:https://vietnamcastiron.com/aluminum-casting-shrinkage/
This document was compiled by Mr.Dinh Tien Vu from VIC, based on following sources:
UK Aluminum industry Fact Sheet 2:Aluminum and Corrosion from Alfed.
Review Corrosion of Cast Aluminum Alloys from MDPI.
Durability and Corrosion of Aluminium and Its Alloys:Overview, Property Space, Techniques and Developments By N. L. Sukiman, X. Zhou, N. Birbilis, A.E. Hughes, J. M. C. Mol, S. J. Garcia, X.
Please cite the sources if you would like to use the information in this document.
Proceso de manufactura
- Varias aleaciones de aluminio para la fabricación
- Propiedades y aplicaciones de las aleaciones de cobre-níquel
- Propiedades y propósitos:Aluminio Bronce
- Propiedades del material de aluminio 6061
- Encontrar aluminio satisfactorio
- Cómo las propiedades únicas del cuproníquel resisten la corrosión marina y las aves
- Cómo evitar la corrosión del aluminio
- EN 12163 Grado CuNi3Si1 TH
- Printdur® Ni625
- Sanicro 41 Trabajado en Caliente
- Sanicro 41 Trabajado en Frío