La ingeniería detrás de la máscara facial Fast Radius
Por Izzy de la Guardia, ingeniera de aplicaciones, Fast Radius
Si bien la pandemia mundial ha revelado muchas vulnerabilidades en nuestra cadena de suministro, también ha generado innovación. En particular, la impresión 3D ha permitido a los profesionales y aficionados canalizar sus miedos en acción con una velocidad y accesibilidad sin precedentes. Experimentamos esto de primera mano en la creación de nuestro diseño de respirador de código abierto.
Aquí hay un vistazo al proceso y cómo pudimos crear cuatro prototipos distintos y realizar tres sesiones de prueba de usuario en solo dos semanas aprovechando la impresión 3D, un equipo multifuncional y las redes personales y profesionales de nuestra empresa.
Prototipado rápido y pruebas de usuario
A medida que muchos estadounidenses comenzaron a refugiarse en el lugar a mediados de marzo, Fast Radius recibió múltiples solicitudes de respiradores impresos en 3D en medio de la creciente preocupación por la escasez de EPP. Fui contactado por nuestro Gerente General, John Nanry, un viernes por la tarde para liderar el esfuerzo de diseño para responder a esta necesidad. Horas después, teníamos nuestro primer diseño listo para imprimir, inspirado en los diseños de código abierto de Copper 3D y La Factoría 3D
El enfoque principal de nuestro diseño fue la capacidad de fabricación en todas nuestras máquinas aditivas internas (Stratasys FDM, Carbon DLS™ y HP Multi Jet Fusion) al garantizar ángulos de voladizo adecuados y ventilación por vacío. Produjimos nuestro primer prototipo en Carbon DLS esa noche.
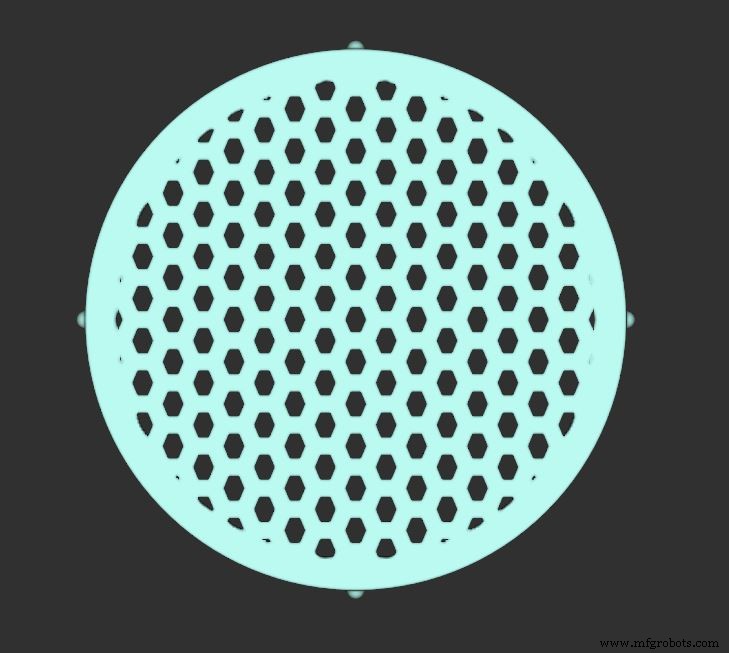
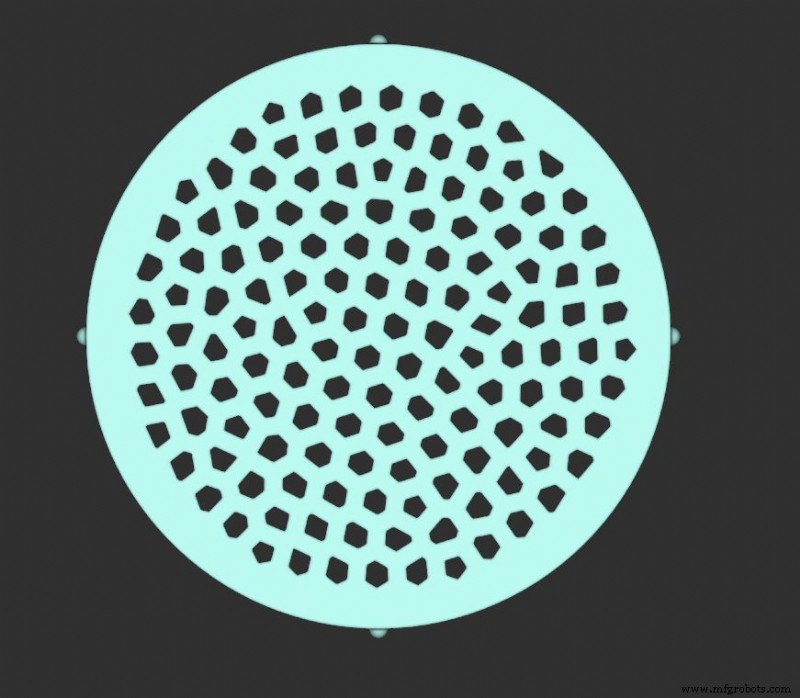
Las herramientas de diseño avanzadas, como nTop Platform, admitían iteraciones rápidas, como cambiar de un patrón voronoi a un patrón hexadecimal más regular que era más fácil de manejar para las impresoras FDM de aficionados
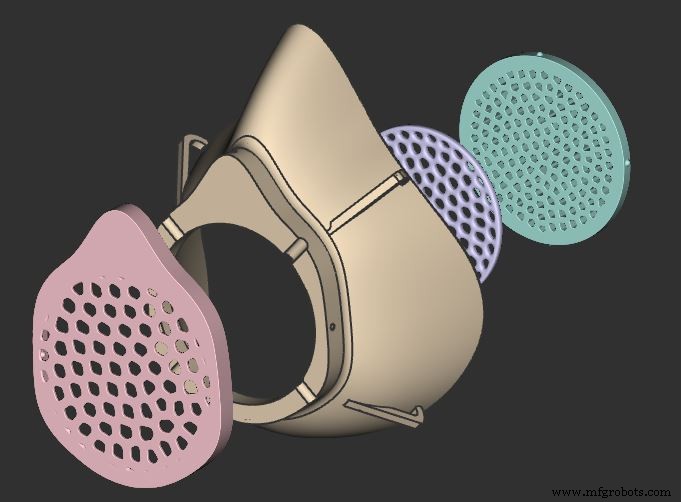
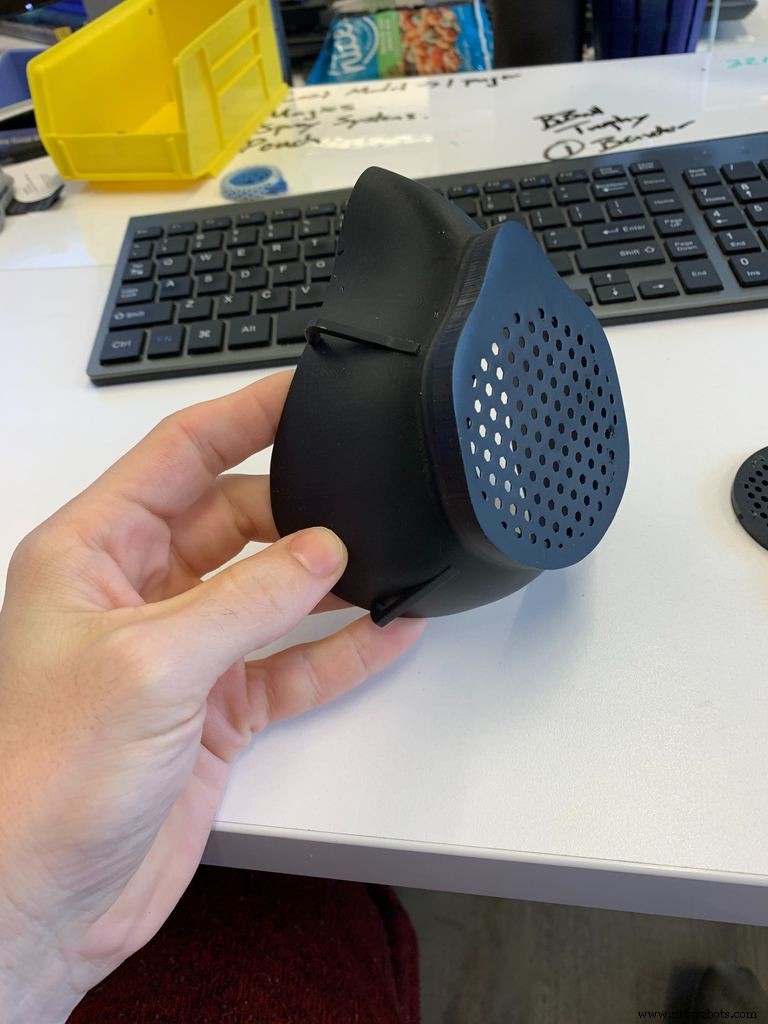
Nuestro primer prototipo impreso incluía voladizos y canales compatibles con FDM para evitar vacíos en DLS
Estos prototipos informaron cambios de diseño adicionales:consolidar la cubierta frontal con el cuerpo principal de la máscara para imprimir como una sola pieza, engrosar los bucles de la correa para mayor durabilidad y reducir la densidad del patrón de cuadrícula y hacerlo circular para facilitar la impresión en FDM. Pudimos comenzar a imprimir nuestros segundos prototipos el sábado por la noche, solo 24 horas después del proyecto.
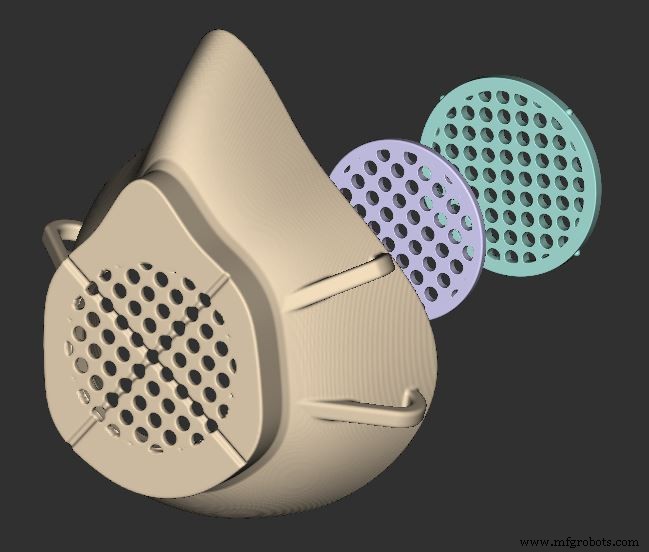
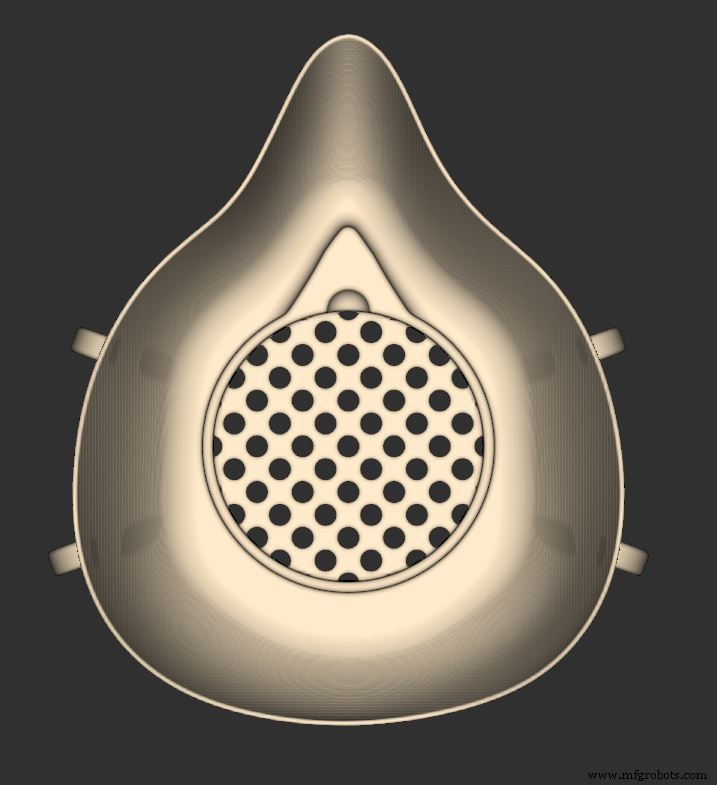
Piezas consolidadas de nuestro segundo prototipo impreso (izquierda). Interior de la máscara con recesión para insertar el dedo y sacar la cubierta del filtro a presión (derecha).
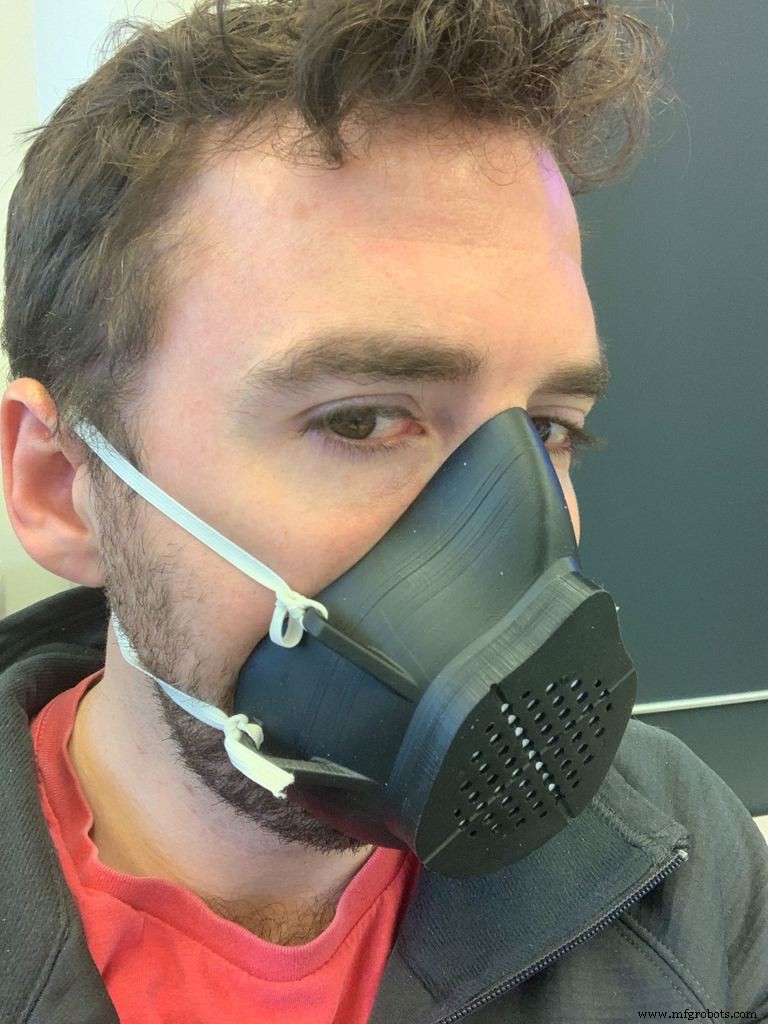
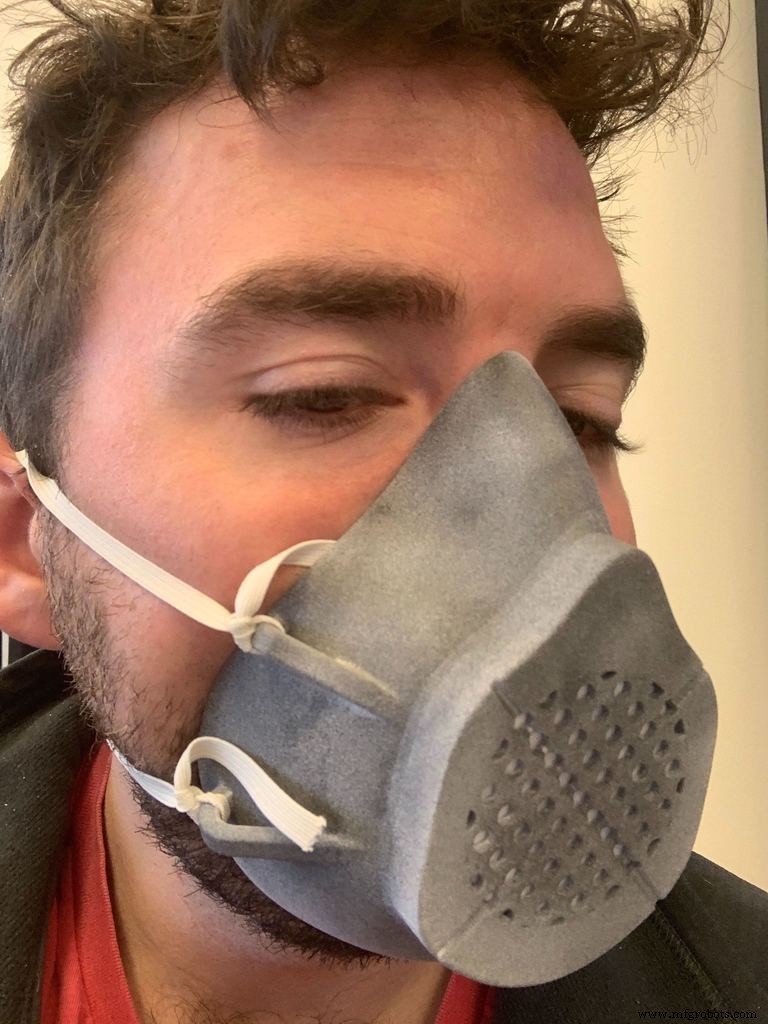
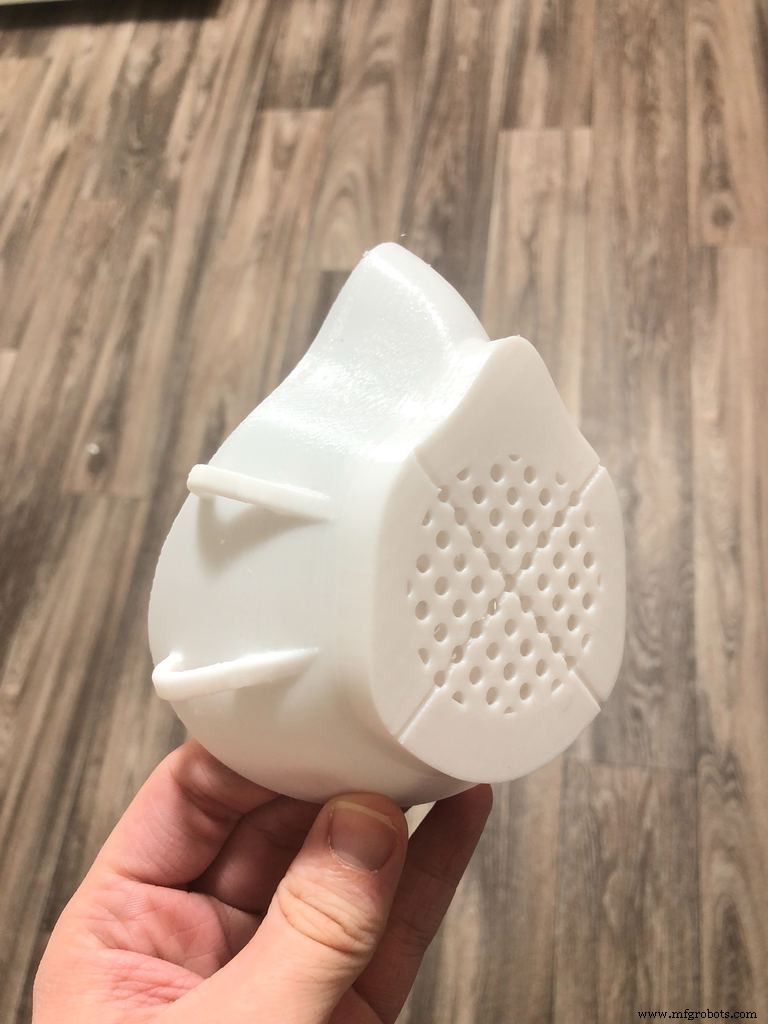
Segundo prototipo impreso en Carbon RPU70 (izquierda), HP PA12 (centro) y PLA impreso en FDM (derecha)
Paralelamente al proceso de diseño, aprovechamos nuestra red para comprender mejor la necesidad e identificar a las personas para las pruebas de usuario. En menos de 24 horas, nuestros amigos de P33 nos conectaron con una docena de médicos y empleados de una fundación de investigación médica para brindar una mayor comprensión de las máscaras N95. Nuestros empleados también se acercaron a los profesionales médicos que conocían. Para el domingo, solo dos días después de iniciar el proyecto, realizamos pruebas de ajuste con nuestro segundo prototipo en 10 personas en cuatro ubicaciones.
Las siguientes dos semanas continuaron con este patrón:diseñar, imprimir, probar, repetir. Nuestro tercer prototipo impreso presentó un rediseño del mecanismo de retención del filtro. La geometría del perímetro del semicírculo compensado funciona como una leva que bloquea la pieza en su lugar cuando se tuerce por fricción (ver a continuación). Hay dos pestañas que empujan la cubierta hacia abajo en la posición girada o bloqueada para asegurar un buen sello alrededor del filtro. Creamos una versión con un área perforada en forma de corazón para que la máscara fuera menos intimidante. Comenzando con esta ronda de prototipos, diseñamos y probamos máscaras en dos tamaños diferentes.
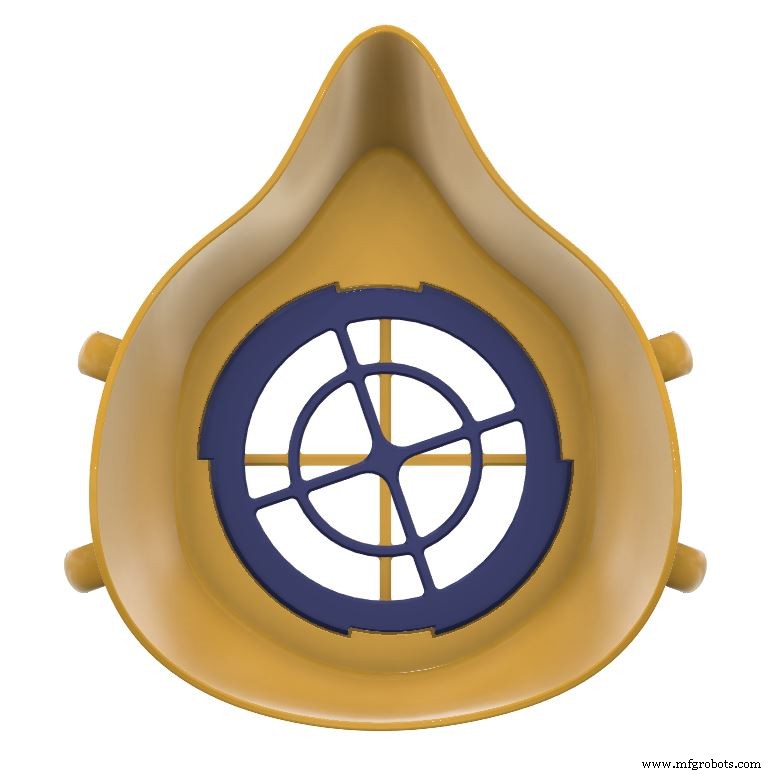
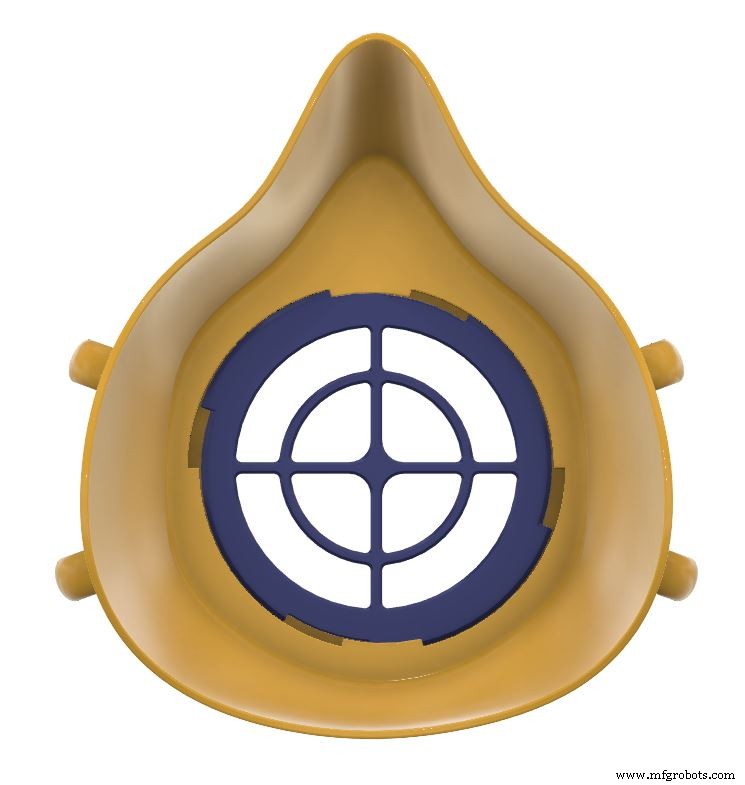
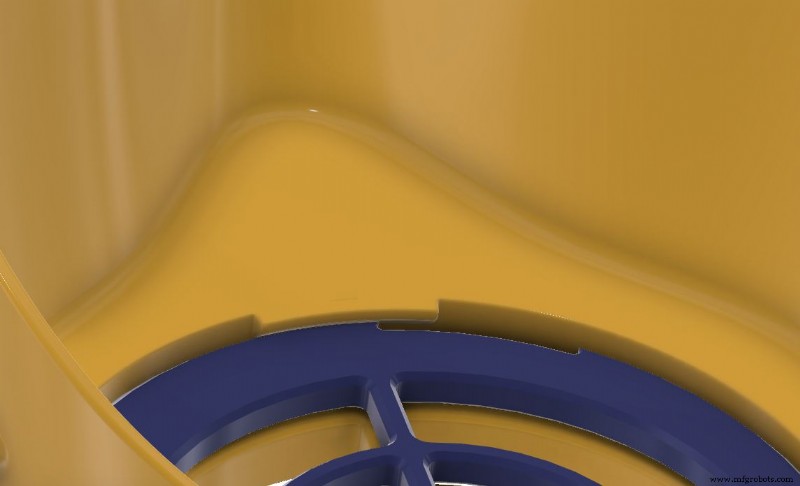
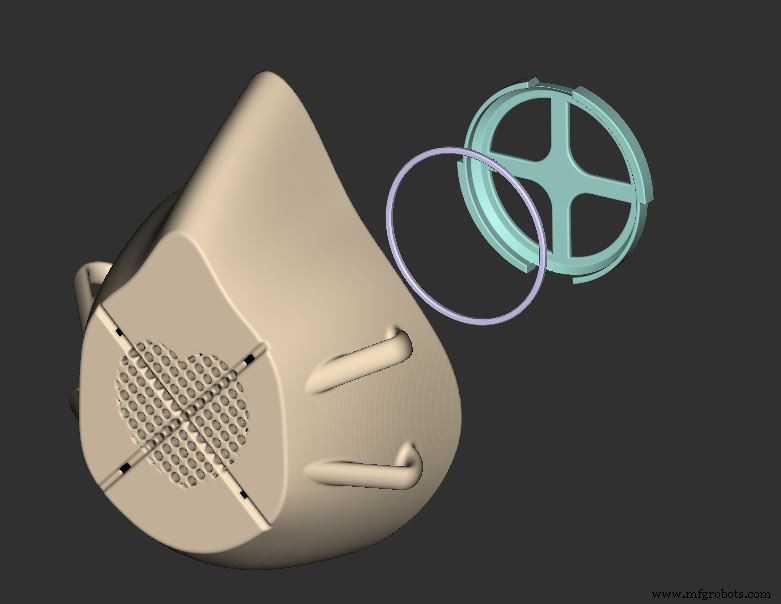
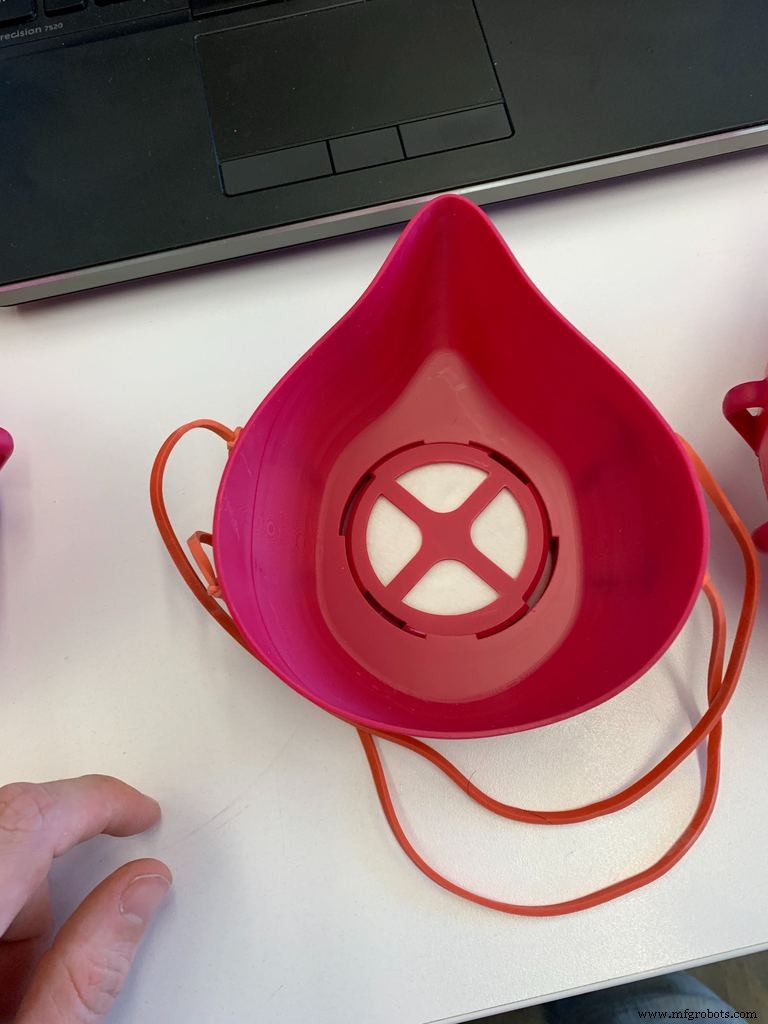
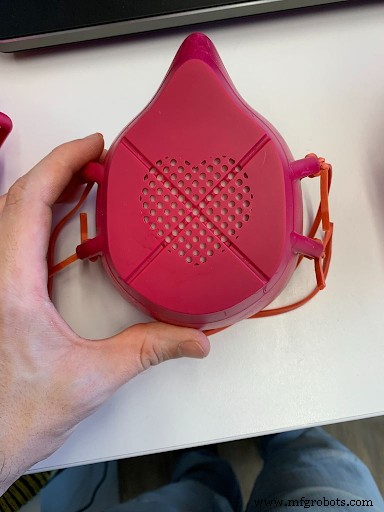
Tercer diseño de prototipo impreso con tapa giratoria.
Para el cuarto prototipo, nos preocupaba principalmente la facilidad de respiración y el ajuste adecuado. Para abordar esto, intentamos maximizar la región perforada y minimizar su densidad (lamentablemente perdiendo el corazón) para reducir la resistencia al flujo de aire. También modificamos las medidas de los dos tamaños en función de los comentarios de las pruebas de los usuarios. En este punto, confiábamos lo suficiente en la función y el tamaño de la máscara para lanzar la versión uno como un diseño de código abierto.
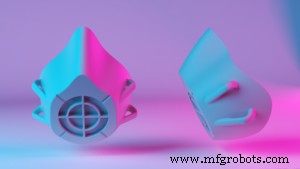
Diseño para la accesibilidad
Para que la máscara esté disponible para la mayor cantidad de personas posible, creamos un diseño de código abierto que podría fabricarse en impresoras 3D domésticas. Esta decisión agregó restricciones de diseño y materiales. Una mascarilla rígida no podía adaptarse a una amplia variedad de formas faciales, por lo que exploramos la posibilidad de agregar un material flexible al borde interior de la mascarilla para mejorar su sellado en la cara.
Hicimos un prototipo de un primer concepto usando SIL 30 en Carbon DLS. Continuamos probando muchos métodos para crear un sello efectivo en la cara (descrito a continuación), incluido un guante cortado, silicona impresa y moldeada, material protésico facial de vestuario moldeable, sellos de TPU y PLA impresos con FDM y burletes. En última instancia, nos decidimos por burletes, que son biocompatibles, fáciles de limpiar y fáciles de conseguir.
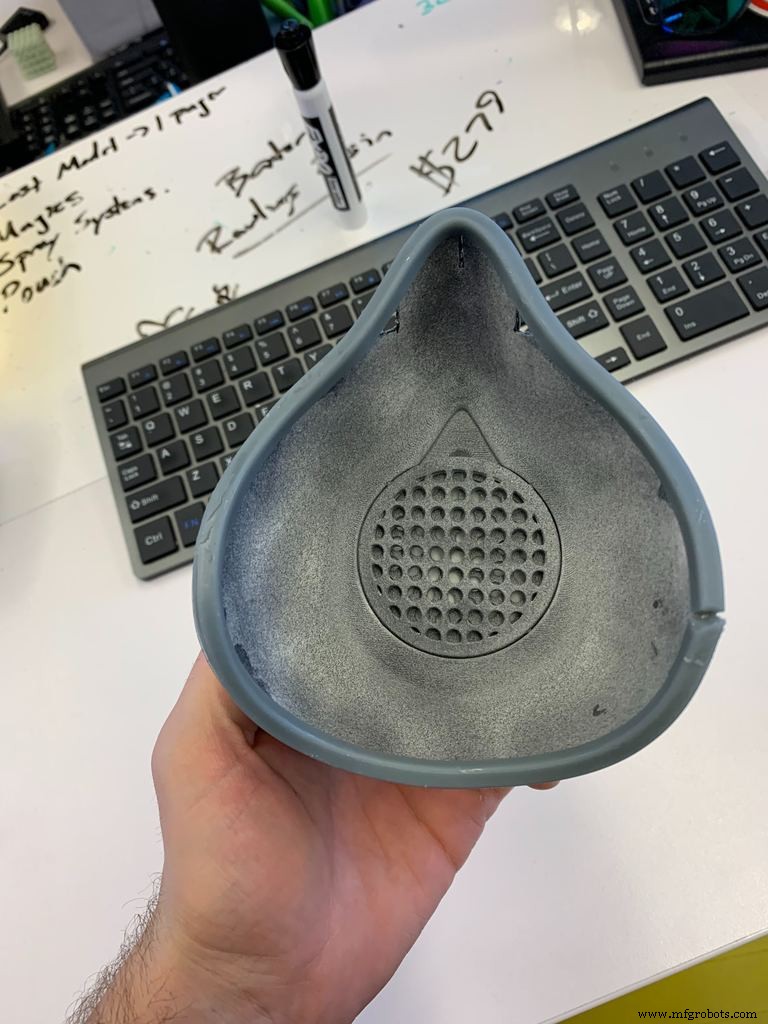
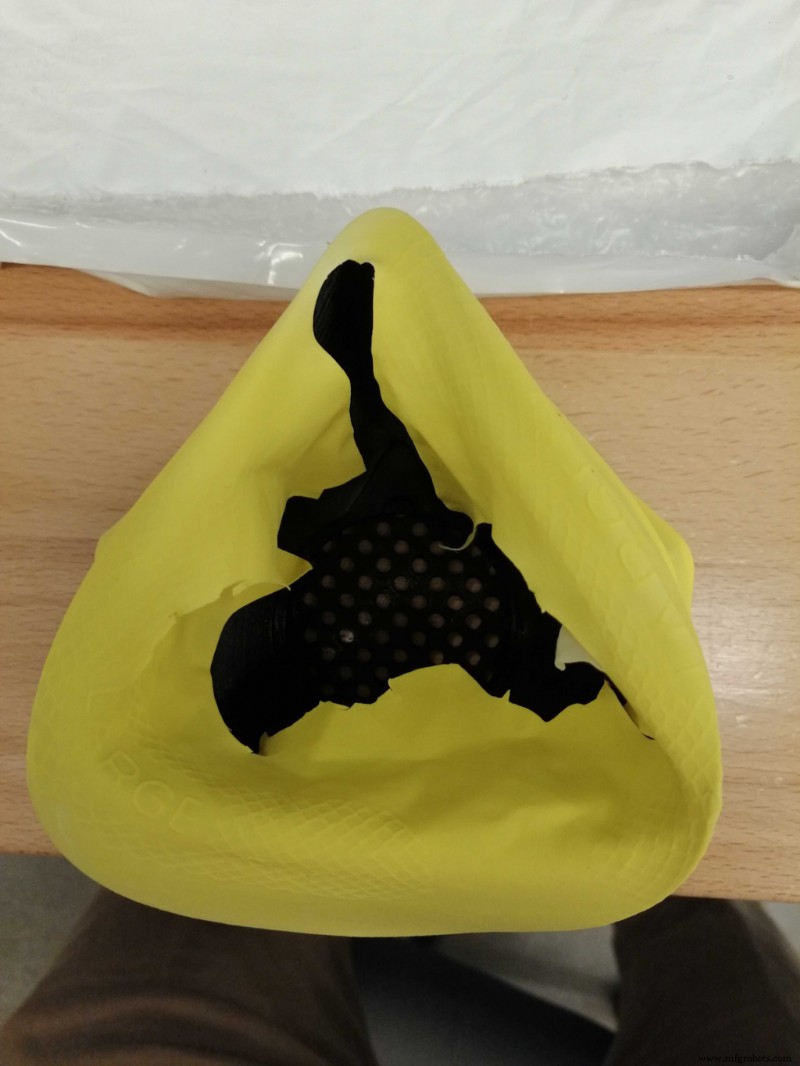
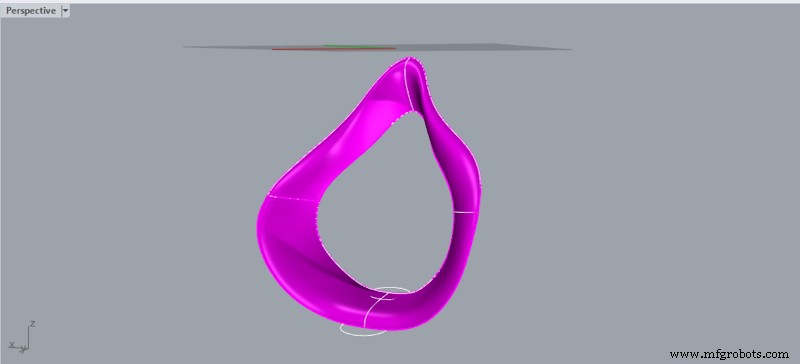
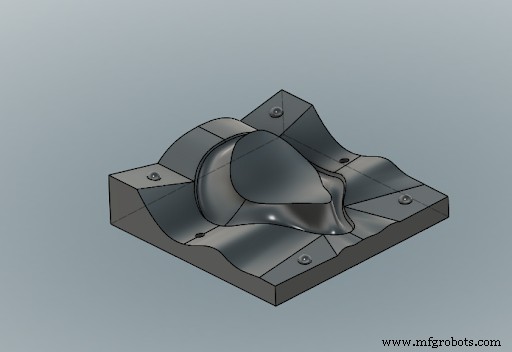
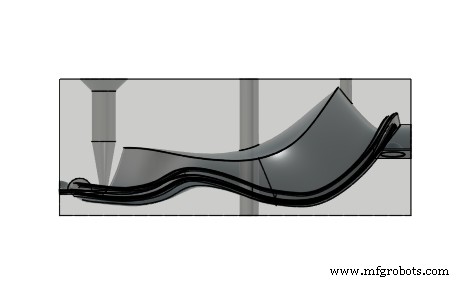
Mockup de formulario para silicona moldeable
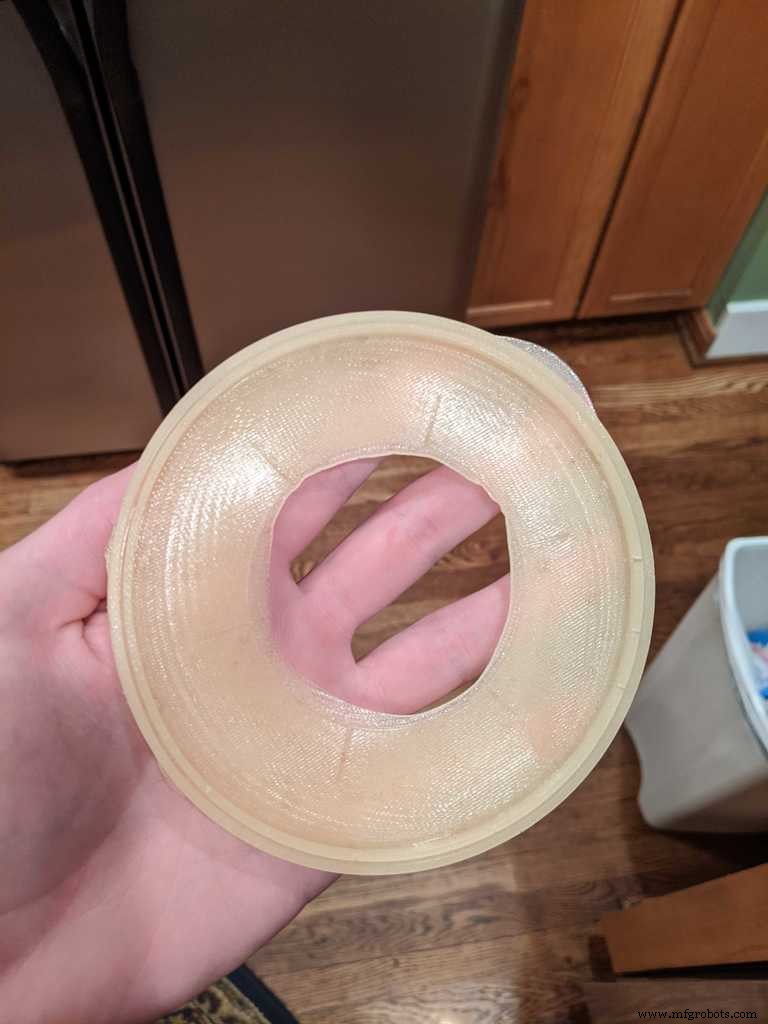
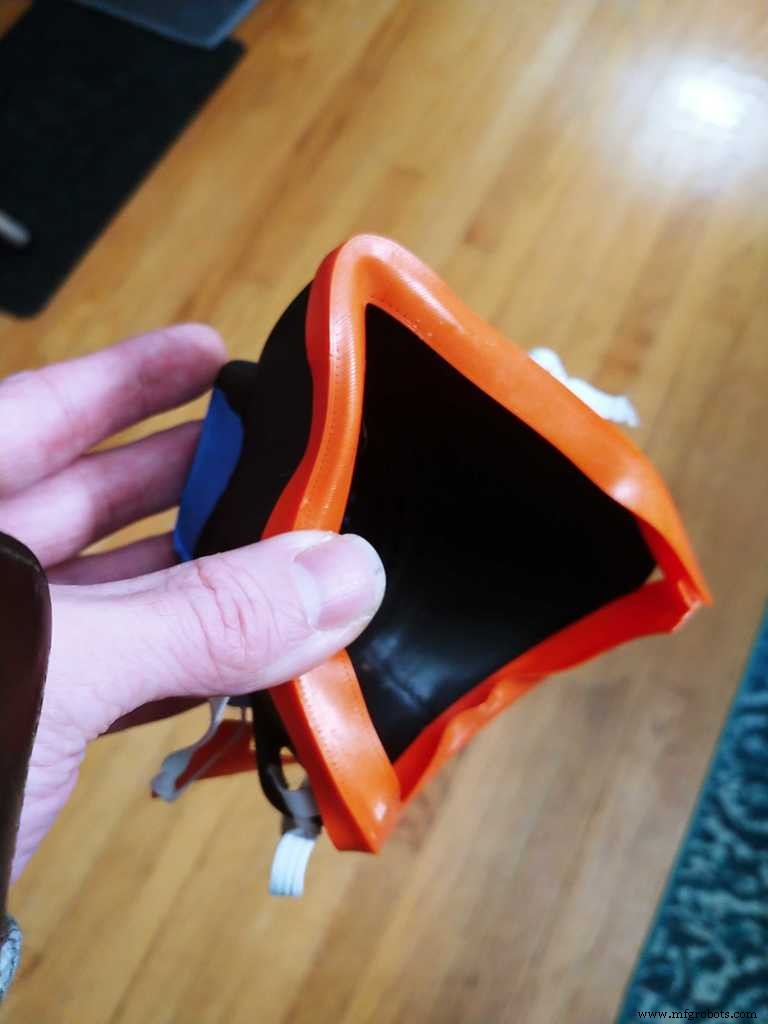
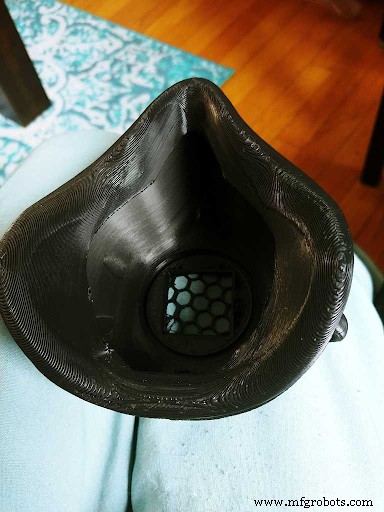
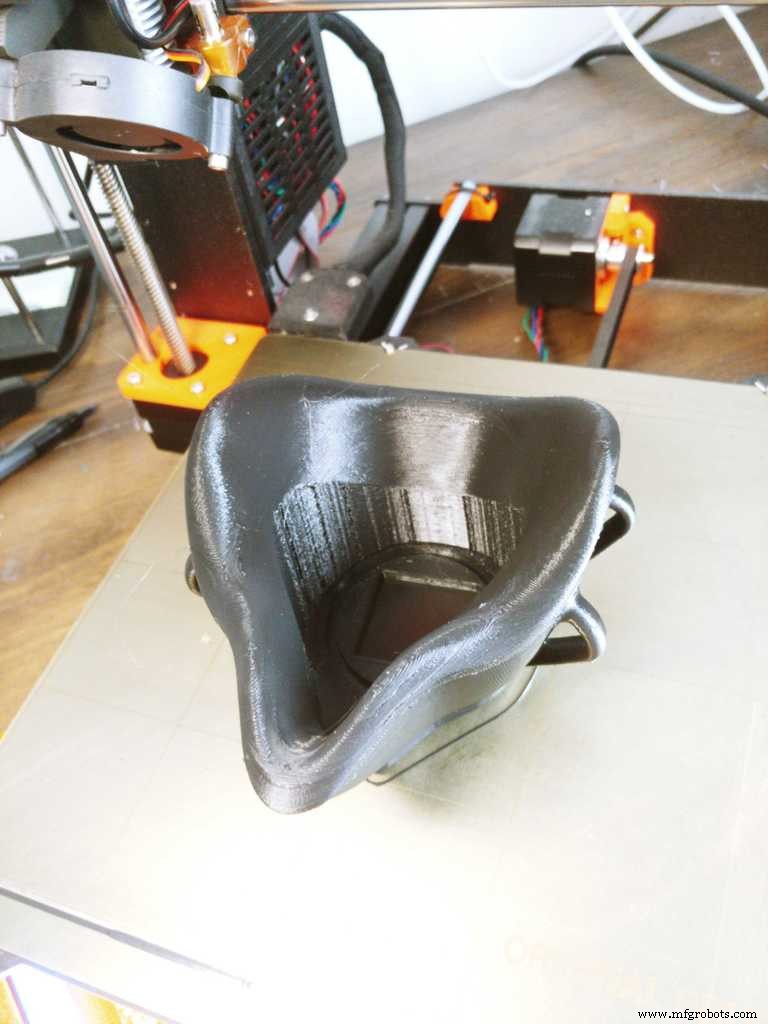
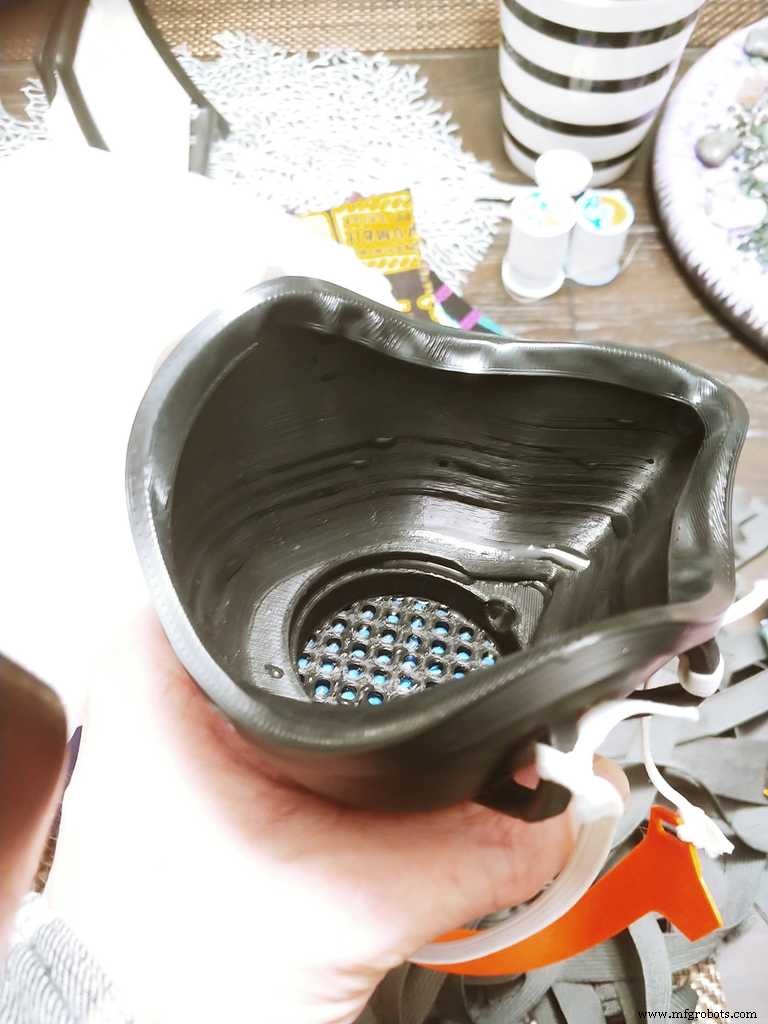
Sello PLA delgado integrado
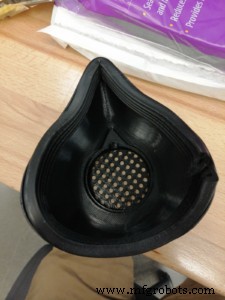
Formación rápida de equipos
Atribuyo la exitosa iteración rápida de este proyecto no solo al poder de las herramientas de diseño digital y la tecnología de fabricación aditiva, sino también a la dedicación y diversidad del equipo que reunimos de diferentes partes de la empresa. Daniel Baker (Gerente de Ingeniería de Manufactura) brindó retroalimentación a DFM y trabajó toda la noche para imprimir y postprocesar prototipos. Tim Ouradnik (Ingeniero de aplicaciones) obtuvo material de sellado, ensambló prototipos y condujo por todo Chicago para realizar pruebas de usuarios con distanciamiento social. Uriah Foley y Eldon Whitis (técnicos de laboratorio) probaron prototipos y exploraron sellos integrados en sus impresoras 3D personales en casa fuera del horario laboral.
Nick Tonini (Gerente de programa) brindó infinitas soluciones inventivas y comentarios sobre el diseño. Jerry O'Leary (diseñador jefe) mejoró nuestros diseños y creó representaciones conceptuales. Charlie Wood (Gerente de Ingeniería Computacional) brindó liderazgo en el diseño de sellos. Hallee Deutchman (directora de materiales y tecnología de fabricación) se puso en contacto con nuestros socios y el equipo legal antes de lanzar el diseño. Sheila Seles (Administradora sénior de contenido) y Austin Belisle (Especialista en contenido) empaquetaron, publicaron y promocionaron nuestro diseño.
La lista de reconocimientos anterior no solo pretende dar crédito a las personas que contribuyeron a este proceso, sino también demostrar el poder de la cultura empresarial para hacer posible cosas nuevas. Trabajamos en este proyecto fuera de nuestras responsabilidades normales y estructuras de equipo porque queríamos crear un producto que pudiera tener un impacto en el mundo más allá de Fast Radius. Este espíritu también cruzó las fronteras de la empresa; estamos agradecidos por P33 y todos los médicos que contribuyeron con su tiempo y experiencia. Si no aprendemos nada más de esta pandemia, espero que sigamos teniendo la intención de fomentar una cultura de diversidad, humildad y colaboración mientras trabajamos para responder a los desafíos globales apremiantes.
Nuestro diseño está disponible y listo para imprimir. Puede encontrar archivos CAD e instrucciones en nuestro sitio web.
¿Listo para fabricar tus piezas con Fast Radius?
Inicia tu cotizaciónTecnología Industrial
- El futuro es… Colaboración
- Artículo en la revista MRO
- La marca dos
- Entre bastidores de nuestro blog
- Los efectos de COVID-19 en la fabricación
- Los beneficios tangibles de la realidad virtual en el espacio de la ingeniería
- Tableau, los datos detrás de la información
- La historia detrás de nuestro video más popular
- La importancia detrás de la detección de descargas parciales
- La verdad detrás de la lubricación y el exceso de grasa
- El futuro de la ingeniería de mantenimiento