Nuevos enfoques para fabricar piezas para el parche de aceite
El fracking ha dado lugar a grandes cambios en la zona petrolífera y en el mecanizado de piezas.
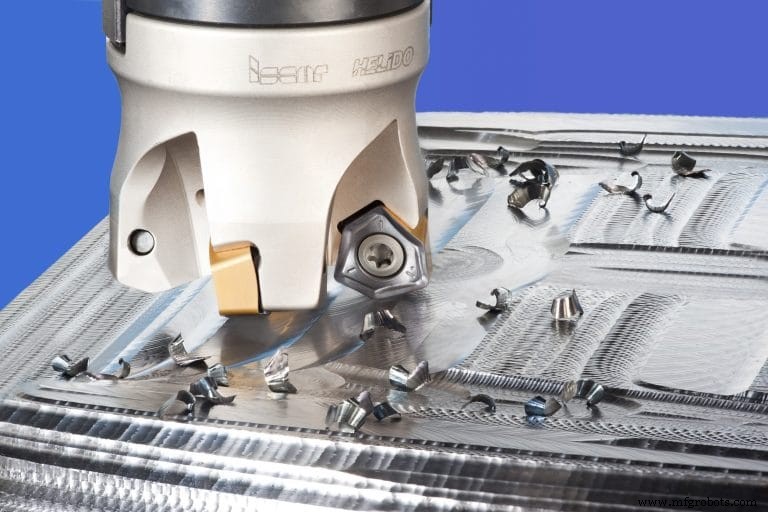
Rod Zimmerman, del fabricante de herramientas de corte Iscar Metals, vive en una agradable zona verde en un suburbio de Fort Worth. Sin embargo, a media milla de su casa, una compañía petrolera ha excavado un agujero vertical de 2286 m (7500 pies) de profundidad, desde el cual ha abierto nueve líneas laterales, cada una de aproximadamente media milla. Está bombeando fluido de fracking en estas líneas a 9000 psi para extraer el gas natural. Es un ejemplo tan bueno como cualquiera de la ubicuidad de la revolución del fracking y la increíble tecnología involucrada.
Y aunque la revolución puede no estar literalmente “en todas partes”, Salvatore Deluca, gerente de producto de otro fabricante de herramientas de corte, Allied Machine &Engineering, dijo que las gigantescas instalaciones de fracking en su condado se llaman “ciudades”. Excepto que, a diferencia de Dallas-Fort Worth, estas "ciudades" se encuentran en el lejano Ohio, un estado que anteriormente no era conocido por el petróleo. No sorprende, entonces, que los grandes cambios en el parche de aceite hayan llevado a grandes cambios en el mecanizado de piezas para el parche de aceite.
Hacer frente al bloque del fracking
Como se mencionó anteriormente, la fracturación hidráulica (más comúnmente llamada fracking) recupera gas y petróleo de las formaciones de esquisto perforando la tierra e inyectando una mezcla de agua, arena y productos químicos en la roca a una presión extremadamente alta. Generar esa presión requiere bombas gigantes, un componente clave de las cuales es el "extremo fluido" o "bloque de fracking" y sus válvulas, pistones y revestimientos.
La alta presión y la abrasividad del lodo bombeado a través de estos bloques provocan un rápido desgaste y agrietamiento. Y dado que los operadores de campos petroleros necesitan mantener alta presión, se ven obligados a reemplazar los extremos de fluido cada pocos días, según Paul Best, especialista de productos en Allied Machine, Dover, Ohio. Best dichos extremos fluidos se mecanizan a partir de bloques sólidos de acero y generalmente tienen aproximadamente 3 'de alto, 4' de ancho y 2-3' (0,61-0,91 m) de espesor. Con contornos complejos, numerosos canales, de tres a cinco orificios pasantes (cada uno de hasta 8″ [203,2 mm] de diámetro) y de tres a cinco orificios transversales que se cruzan, los extremos fluidos requieren grandes cantidades de fresado, taladrado y roscado.
Zimmerman, vicepresidente de ventas, Zona Oeste de Iscar, dijo que los extremos fluidos tradicionalmente se fabricaban con acero de aleación de la serie 4000, pero para combatir el desgaste, los usuarios están probando “aleaciones más exóticas como material de acero inoxidable 17-4 PH, acero inoxidable súper dúplex y 15-5 inoxidable.” Deluca estimó que aproximadamente la mitad de los extremos fluidos que ve ahora son una variante de un acero inoxidable pretemplado y la proporción continúa creciendo.
Gayle Vollmer, servicios de ingeniería de Hartwig en Houston (distribuidor de Okuma en el área) dijo que también hay un movimiento para usar materiales más duros para las partes de un bloque de fracking que son más susceptibles al desgaste, y un intento de rediseñar bloques de fracking para que más componentes son fácilmente reemplazables. Pero supuso que la demanda actual de alta producción ha puesto esa investigación "en un segundo plano".
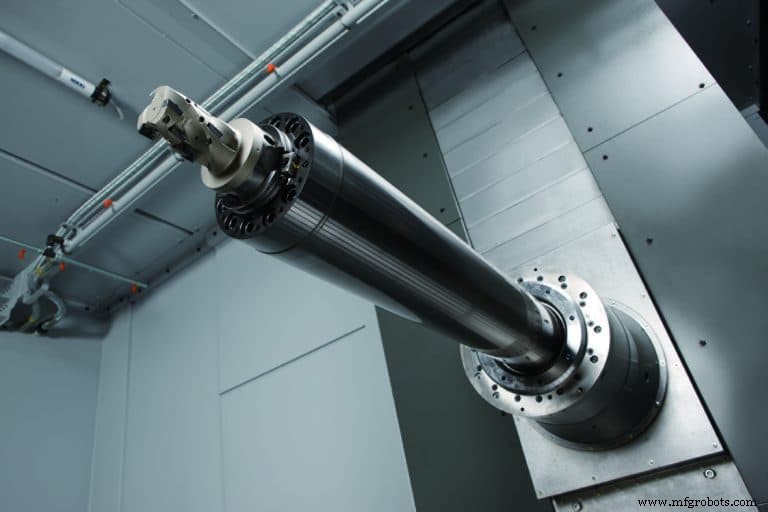
Ya sea que esté hecho de 4340 o de un acero inoxidable más duro, abordar un extremo de fluido prácticamente requiere una gran mandrinadora o un centro de mecanizado horizontal. Jason Schooley, gerente regional de ventas de JTEKT Toyoda Americas, Arlington Heights, Illinois, dijo que el objetivo es realizar tantas operaciones como sea posible en una sola máquina, lo cual es doblemente importante en una pieza que es tan grande y difícil de mover.
Schooley dijo que mientras que las fresadoras suelen tener mesas más grandes para piezas aún más grandes, las horizontales como la FH1250SX de Toyoda son casi cuatro veces más rápidas. Esto se debe en parte a un husillo de 6000 rpm accionado por engranajes (opcionalmente 8000 rpm o un husillo de par alto de 15 000 rpm) y una velocidad de avance rápida de 1654 ipm (42 m/min). La máquina está construida sobre una base de hierro fundido Meehanite para una máxima rigidez con guías de rodillos cilíndricos para una mayor velocidad, mientras que la transmisión de doble husillo de bolas en los ejes Y y Z aumenta la estabilidad del mecanizado durante el corte pesado.
El FH1250SW también tiene una pluma en el eje W para operaciones de taladrado profundo y mandrinado. Agregó que en los últimos años, "varios fabricantes de máquinas herramienta han optado por un cabezal de eje U incorporado" o un eje W, que se desplazan paralelos al eje X o al eje Z, respectivamente. Esto hace posible cambiar el centro de rotación de una herramienta de torneado fija, una característica útil cuando se cortan agujeros grandes u otros contornos grandes. Esto se debe a que los extremos fluidos no solo tienen orificios grandes, sino que los orificios a menudo tienen "forma de botella" en el interior, por lo que no se pueden perforar simplemente. Para las máquinas que no tienen un eje U incorporado, los usuarios pueden agregar un cabezal de "alimentación" que realiza la misma función, siendo D'Andrea uno de esos proveedores.
Hay desventajas en el montaje de un cabezal grande en un husillo giratorio, incluida la posible interferencia de piezas y la incompatibilidad con el suministro de refrigerante a través del husillo. La opción del mercado de accesorios también necesita su propia unidad externa y es posible que no sea posible cambiar automáticamente el equipo como lo haría con otros cambios de herramientas.
Pero Schooley dijo que la interferencia no es un problema en las aplicaciones de bloques de frack si el recorrido del eje Z de la máquina es lo suficientemente largo como para evitar que el cabezal adicional se extienda más allá de la línea de medición. Con 1.850 mm de recorrido en el eje Z y 200 mm desde la punta del husillo hasta la banda muerta del centro de la mesa, la máquina 1250 aborda bloques de frack sin interferencias. Agregó que Toyoda ha desarrollado aún más la capacidad de cambio automático para sus cabezales de contorneado para "ayudar a nuestros clientes a mantenerse a la vanguardia en una industria tan volátil como el petróleo".
Según la experiencia de Schooley, las herramientas de mandrinado modulares disponibles de Innovative Tooling Solutions y otros vienen con refrigerante a través del husillo como característica estándar y muchos talleres que fabrican bloques de frack utilizan una fresadora de mandrinado horizontal dedicada con un cabezal de contorneado para terminar los orificios. Toyoda también ofrece centros de mecanizado horizontales de eje hueco con 1560 lb-pie de torque para operaciones de servicio pesado. Schooley dijo que el husillo de eje hueco de 4000 rpm combina el alcance y la fuerza necesarios para perforar y perforar profundamente, lo que permite que las piezas de trabajo que antes requerían dos operaciones se completen en una sola máquina. El palet giratorio de 360 000 posiciones de la máquina proporciona la máxima flexibilidad para el mecanizado pesado en una variedad de piezas de trabajo.
Okuma America Inc., Charlotte, N.C., ha desarrollado una opción de programación llamada Turn-Cut que permite que un centro de mecanizado horizontal imite un torno en el corte de elementos circulares y angulares en piezas grandes y desequilibradas sin usar un cabezal en U. Como explicó Ted Winkle, coordinador del centro tecnológico de Okuma en Houston:“En lugar de rotar la pieza, lo que sería difícil o imposible para algunas piezas grandes, giras la herramienta alrededor de la pieza. Y en lugar de que un cabezal en U mueva la herramienta fuera del centro del eje de rotación, Turn-Cut interpola esos ejes en X e Y mientras también alimenta una herramienta de torneado de un solo punto en Z”.
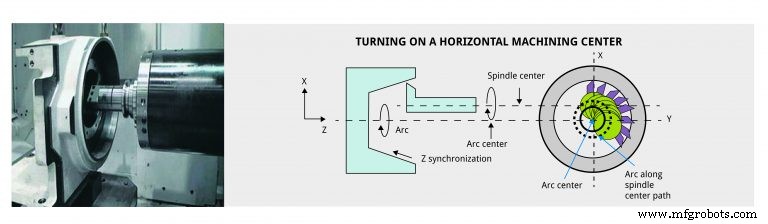
Winkle cree que Turn-Cut desempeñará un papel más importante en la industria del petróleo y el gas para piezas como los bloques de fracking porque “a medida que las perforaciones aumentan de diámetro, se necesita mucho torque para ejecutar una herramienta sólida para hacer un orificio de ese tamaño. Tener capacidad de corte por giro, a diferencia de un cabezal en U y todas las costosas herramientas asociadas con eso, es un beneficio”.
Por otro lado, Turn-Cut no es barato porque requiere un software adicional para aceleración, desaceleración y sincronización especializadas, además de escalas de vidrio y enfriamiento de husillo de bolas. Pero obtendrá una mayor precisión para una variedad de piezas con estas características y aumenta la probabilidad de poder terminar las piezas en una sola configuración.
Schooley respondió que la técnica requiere mucho movimiento repetitivo en la misma área de los husillos de bolas y las guías (cuanto menor sea el diámetro, más ocurrirá) y esto podría disminuir la vida útil de la máquina.
Por otra parte, dijo Winkle, a menos que use esta capacidad con frecuencia en partes del mismo tamaño, no tendrá un movimiento excesivo en la misma área. Y si no necesita la capacidad con frecuencia, no podría justificar el gran gasto de un eje U, por lo que Turn-Cut sería una opción más lógica. Como cualquier función de máquina herramienta, existen ventajas y desventajas.
Cielo de caballos de fuerza
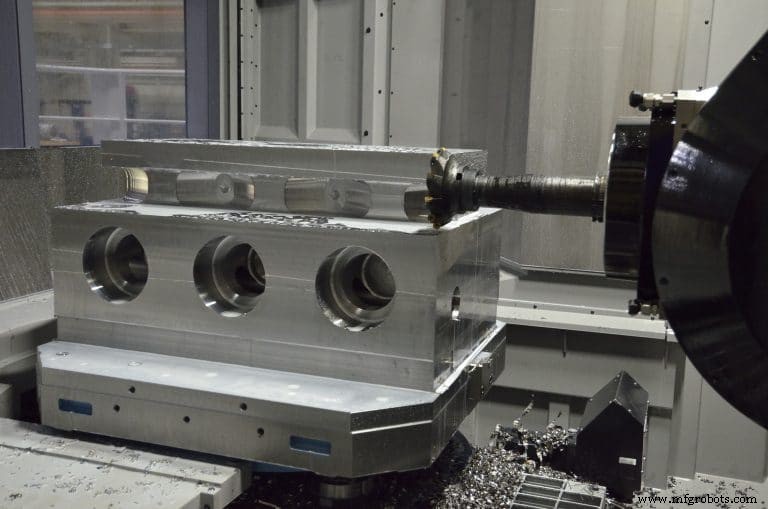
Para Makino Inc., Mason, Ohio, las plataformas de referencia para piezas como bloques de fracking son sus centros de mecanizado horizontal de cinco ejes T1 y T2. David Ward, gerente de marketing de productos, dijo que ambas máquinas tienen husillos de transmisión directa que son "ideales para los desafiantes aceros inoxidables y de alta aleación que se usan en esta industria".
El T1 tiene un husillo HSK100 de 12 000 rpm con 143 hp y un par nominal de servicio de 740 ft-lb. El husillo T2 más grande utiliza una interfaz HSK125 para la rigidez radial. El husillo T2 de 4000 rpm ofrece 200 HP y 1107 ft-lb de potencia nominal y par de torsión.
Ward añadió que ambos husillos mantienen sus valores de par máximo hasta las 1000 rpm. "Al llevar los valores de par máximo hasta este punto, se garantiza que el husillo podrá aprovechar los nuevos avances en la tecnología de herramientas de corte, como los recubrimientos de plaquitas de alta temperatura".
Winkle observó que la zona petrolera está dominada por máquinas CAT 50, pero estuvo de acuerdo en que el contacto frontal proporcionado por las interfaces HSK y BIG Plus sería una ventaja “si tiene un voladizo largo. Pero dado que la mayoría de las fuerzas de mecanizado son axiales, no importa mucho qué tipo de husillo elija. Siempre que sea carnoso. “Aproximarse a un bloque de frack con una máquina de husillo ISO 40 sería un ejercicio inútil”, dijo.
Las fuentes coincidieron en que el refrigerante a alta presión es esencial para la eliminación del calor y las virutas en muchas aplicaciones de petróleo y gas, o como lo expresó Zimmerman de Iscar, “casi independientemente de la aplicación. Cuando se trabaja profundamente en un orificio en un extremo de fluido, es fundamental eliminar las virutas y es difícil hacerlo. Una herramienta de fresado alimentada con refrigerante es, con mucho, el camino a seguir en este tipo de aplicaciones”.
Entonces, si la máquina no viene con esta capacidad, los usuarios la agregan con unidades de proveedores como ChipBLASTER. “Ni siquiera consideraría comprar una máquina fresadora hoy en día sin refrigerante de alta presión a través del husillo”, dijo Zimmerman. “Es un cambio de juego tanto para el fresado como para el taladrado”. La única excepción es una situación en la que no puede dirigir el refrigerante al filo de corte. En ese caso, el refrigerante "a veces funciona en tu contra y es mejor secar a máquina para evitar el agrietamiento térmico de los insertos", dijo.
Deluca dijo que los fabricantes de máquinas herramienta han respondido a esta demanda de tal manera que ahora comúnmente encuentra máquinas con una bomba suministrada por el OEM que entrega 1,000 psi a 20 gpm. Ward dijo que el T1 de Makino ofrece 26 gpm a 1000 psi, mientras que el T2 proporciona la misma presión a 53 gpm.
Avances en herramientas de corte
Si bien es posible que le encante tener un monstruo de alta potencia para sus bloques de fracking, Deluca de Allied Machine dijo que se han enfrentado cada vez más al desafío opuesto:la necesidad de perforar agujeros grandes con máquinas enfocadas en el fresado donde las velocidades del husillo son más altas pero la potencia máxima es de 40 a 50.
“Las empresas que fabrican estas piezas suelen ser de tamaño pequeño a mediano y, por lo general, no se dedican a fabricar bloques de frack”, dijo. “Y muchas personas desconfían de centrarse en este mercado y gastar medio millón de dólares en una máquina para una industria que funciona como una montaña rusa. Así que tuvimos
que desarrollar una herramienta que pudiera cortar un orificio de 4″ de diámetro a velocidades de husillo mucho más altas y velocidades de avance mucho más bajas que nuestros productos de perforación tradicionales”.
El desafío de perforar bloques de fracking va más allá del tamaño de los agujeros requeridos. “Los cortes interrumpidos son inherentes a la fabricación de bloques de extremos fluidos, ya que los orificios transversales se taladran perpendiculares a los orificios existentes”, dijo Best de Allied Machine. “Debido a la forma resultante de los orificios que se cruzan, los bordes exteriores de la broca seguirán enganchados en el corte, mientras que el borde interior no. Esto puede desestabilizar el taladro, lo que puede destruir la herramienta y dañar la integridad del bloque de fracking”.
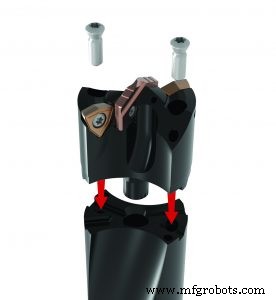
Además, si el cliente está economizando al usar material que no ha sido tratado térmicamente, el taladro podría experimentar variaciones significativas. Deluca de Allied dijo que normalmente eso significa que un operador debe monitorear constantemente el proceso o correr el riesgo de fallas catastróficas en la perforación a los pocos segundos de golpear una cavidad en la fundición, lo que podría arruinar una pieza en la que ha invertido horas. Los talleres también experimentan variaciones en los materiales de un bloque a otro, lo que dificulta la elección de los parámetros de operación y perforación perfectos.
Allied ha enfrentado estos desafíos con una herramienta de "próxima generación" llamada APX. Cuenta con un sustrato de carburo más resistente y un recubrimiento patentado para soportar el impacto de golpear un bolsillo. "Puede astillar la herramienta y escuchará un chillido", dijo Deluca, "pero aún podrá terminar el agujero".
Agregó que Allied abordó las dificultades de la perforación de agujeros cruzados agregando un limpiador al inserto para mejorar la estabilidad, además de almohadillas de desgaste para proporcionar estabilidad adicional cuando el piloto sale a un espacio vacío o un agujero cruzado. “También recomendamos aligerar el avance y mantener la misma velocidad al perforar orificios de salida en ángulo para que la herramienta no quiera empujar o caminar. Por lo general, no es necesario al perforar la línea principal o los orificios transversales, pero solo hay un límite de ingeniería que puede poner en una herramienta para compensar el corte interrumpido extremo de los orificios en ángulo".
Para el fresado, Zimmerman dijo que la plaquita de seis puntas de doble cara HeliDo H600 de Iscar funciona extremadamente bien para este tipo de material. "También ofrecemos Mill 4 Feed, una plaquita cuadrada de un solo lado con una geometría más positiva para un corte más suave que requiere menos potencia".
Su mensaje principal es que, dado que Iscar lleva mucho tiempo comprometida con la industria del petróleo y el gas y solo contrata maquinistas experimentados, puede desarrollar el proceso óptimo para un cliente y elegir entre una amplia variedad de herramientas. "Tenemos muchos estilos de fábricas de piensos y podemos optimizar una fábrica de piensos en función de la aplicación, el material y la máquina, teniendo en cuenta su rigidez, potencia y par".
Multitarea y automatización
Es probable que los bloques de fracking de 9500 lb no lleven a pensar en "automatización", pero Makino y otros constructores ofrecen soluciones que permiten que un operador opere varias máquinas. Para los bloques de frack, eso generalmente significa un cambiador de tarimas giratorio que cambia entre una pieza fundida en bruto y una pieza terminada en menos de un minuto. Después de eso, el operador tiene mucho tiempo para retirar la pieza terminada.
Con tiempos de ciclo de unos pocos minutos, los tubos de las pistolas de fracking se encuentran en el otro extremo del espectro. Y dado que son un “artículo de un solo uso”, dijo Vollmer, “las tasas de producción son astronómicas. Se hacen miles todos los días.”
Como resultado, la pieza es ideal para la automatización, y Hartwig y Okuma trabajaron juntos para ofrecer varias opciones. Estos incluyen robots para carga/descarga y sistemas de alimentación de barras como los que se utilizan para piezas pequeñas en máquinas de torneado de estilo suizo, excepto que aquí manejan diámetros de 2 a 4″. El enfoque más rápido alimenta el material en una máquina de doble husillo, mecaniza un extremo y luego alimenta la pieza directamente en el subhusillo para trabajar en el otro extremo.
Vollmer dijo que las piezas requieren torneado, roscado y algo de fresado, idealmente usando herramientas vivas para este último, una característica a la que Winkle se refirió como “uno de los mayores cambios en la industria en los últimos años”. El fracking y la perforación direccional son nuevamente una gran razón para esa transición.
Sin embargo, para muchas de las piezas en gran parte cilíndricas que se necesitan en las operaciones actuales de "fondo de pozo", el torno ideal tiene más que herramientas motorizadas y una torreta o dos. Tiene un cabezal giratorio y capacidad de fresado multieje como la serie de torno-fresado MULTUS de Okuma.
“Las piezas necesarias tanto para la fase de perforación como para la de terminación son mucho más complejas que con los pozos verticales tradicionales”, explicó Winkle. “Tienes que poder abrir y cerrar válvulas para cambiar zonas de producción. Las piezas tienen tuberías hidráulicas a través de ellas, así como equipo de monitoreo electrónico”.
Esto requiere orificios transversales y características fresadas intrincadas en el diámetro exterior e interior, por lo que las máquinas necesitan un posicionamiento de cinco ejes y aproximadamente nueve ejes de movimiento de la máquina para cortar una pieza en un extremo y cambiar los husillos para trabajar en el otro.
Los hilos son otro desafío. Winkle dijo que hay literalmente cientos de tipos y que las tolerancias son estrictas:"Más 1,5 mil, menos nada". Esto se debe a que en el petróleo y el gas, las roscas no solo mantienen unidas las piezas, "tienen que sellar perfectamente y soportar una enorme tensión de tracción de la gigantesca cadena de piezas que se adentra a kilómetros de profundidad en el agujero", dijo Winkle. “Y tienen que lidiar con la expansión térmica y la carga de choque. Este componente de sellado y soporte de carga no existe en ninguna otra industria".
Cortar estos hilos requiere una máquina rígida y una configuración que resista las vibraciones. Kyle Downs, director de gestión de proyectos y marketing de SMW Autoblok, Wheeling, Illinois, dijo que todo esto se complica por el hecho de que “el material entrante es muy inconsistente. La automatización del centrado de tuberías en forma de gancho, dobladas y/u oblongas se puede lograr con dos escenarios, ya sea un mandril de autocentrado y compensación 3+3, o un mandril de compensación y una solución de centrado montada en contrapunto, que normalmente también es un mandril. .”
Finalmente, la adición de la capacidad de deposición de metal por láser a las máquinas de remoción de metal agrega nuevas posibilidades, como lo demuestra la nueva serie LASER EX de Okuma. Si, por ejemplo, tuviera una pieza con solo algunas características sobresalientes, podría agregar esas características al cuerpo principal, en lugar de eliminar las características de un stock más grande. Eso es potencialmente un ahorro enorme en el tiempo de mecanizado.
Winkle agregó que también se pueden fusionar materiales diferentes, combinando, por ejemplo, Inconel y acero inoxidable, lo que “nunca es posible con tecnología puramente sustractiva. La unión es tan fuerte o más fuerte que si se mecanizara a partir de un sólido”, dijo.
Eso tiene un potencial inmediato en petróleo y gas para agregar las almohadillas de desgaste necesarias en los conjuntos de perforación o agregar las aletas laterales que se usan para evitar que la tubería raspe el diámetro interno de la carcasa de un pozo a medida que se mueve a través de una curva en un pozo direccional. Okuma también ofrece la capacidad de cementar una zona de material hasta aproximadamente 50 Rockwell usando el mismo láser con una apertura diferente.
Sistema de control de automatización
- Nueva certificación para Lubrication Elite
- Defensa de los chips neuromórficos para la informática de IA
- Repensando la fabricación inteligente para la nueva normalidad
- Si los datos son el aceite nuevo, ¿quién es su refinador?
- Para las cadenas de suministro, la experiencia del cliente es el nuevo diferenciador
- Preparar su cadena de suministro para el futuro para la nueva normalidad
- La pandemia está impulsando un nuevo modelo para la toma de decisiones en la cadena de suministro
- La nueva ola de desafíos para los fabricantes de equipos industriales
- Las 5 mejores piezas de Stromag para su plataforma petrolera
- Encontrar las piezas correctas de la máquina:consejos para ingenieros
- ¡Gracias por los recuerdos!