Extensión de la vida útil de los activos de automatización
Si se dejan solos, los activos de manejo de materiales se degradarán lentamente y eventualmente fallarán, a menudo en el momento más inoportuno. Pero con un poco de planificación, no solo puede extender su vida útil, sino que también puede optimizar el rendimiento.
Los activos de automatización generalmente evolucionan a través de cuatro etapas distintas:diseño, ejecución, soporte y optimización. Sin embargo, en demasiados casos, la fase de optimización es aleatoria o se ignora por completo. El rendimiento alcanza un pico y luego comienza a disminuir. Este proceso ocurre por muchas razones:las personas que implementaron los sistemas pueden haber seguido adelante y sus sucesores no se sienten comprometidos con el sistema; puede que no existan mecanismos para monitorear el desempeño; o el negocio puede ser tan bueno que hay pocos incentivos para buscar mejoras.
Cualquiera que sea la razón para no optimizar, la economía global actual requiere que los almacenes y los centros de distribución extraigan el máximo valor de sus inversiones en automatización. Esto debería comenzar con una auditoría detallada tanto de los riesgos de no hacer nada como del potencial total de extender la vida útil de los activos de automatización.
Evaluación del riesgo
Una auditoría comienza con un análisis de los activos actuales con miras a extender su vida útil. Cree un perfil de cada activo clave en sus instalaciones, incluidos software, controles, dispositivos eléctricos periféricos y equipos mecánicos. Si no tiene un inventario, los proveedores de cada activo deberían poder proporcionarlo. Desde aquí puede crear un inventario maestro, categorizando la obsolescencia potencial de cada pieza y su importancia estratégica y luego creando un plan para mitigar esos riesgos. Cada capa debe categorizarse según su importancia estratégica para su negocio, de la siguiente manera:
Riesgo crítico: Activos que pueden afectar a todo su sistema. Esto requeriría un plan de recuperación para mitigar los problemas a corto plazo y, a largo plazo, una estrategia presupuestaria para cubrir el reemplazo total, si es necesario, con los costos de reemplazo escalonados en varios ciclos presupuestarios.
Riesgo alto: Componentes que pueden conducir a una falla parcial del sistema. Esto también puede resultar en un tiempo de inactividad prolongado y también requeriría un plan de recuperación y una planificación presupuestaria a más largo plazo, tal vez equilibrando el costo entre los gastos de capital y MRO.
Riesgo medio o bajo: Esto generalmente involucra componentes donde la falla no conduciría a una falla parcial o total del sistema. El tiempo de inactividad es mínimo y los costos de reemplazo generalmente se pueden manejar con los presupuestos de MRO. Una buena estrategia de repuestos destinada a tener a mano los componentes de reemplazo adecuados puede mantener el riesgo bajo control.
Con una comprensión de su riesgo y una buena planificación, puede extender sustancialmente la vida útil de su sistema, minimizar el tiempo de inactividad imprevisto y operar dispositivos mecánicos, de control, de software y eléctricos a su máximo potencial.
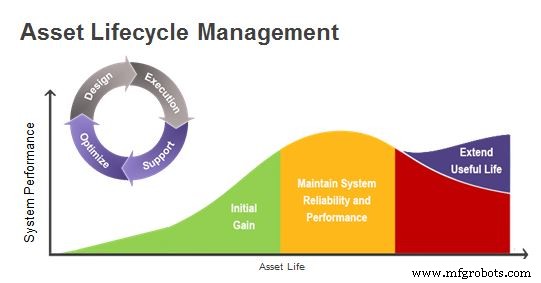
Prolongación de la vida útil del sistema mecánico
El uso de transportadores, clasificadores, sistemas automatizados de almacenamiento y recuperación y otros equipos de capital probablemente representan el mayor riesgo y el mayor gasto de capital en un almacén o instalación de distribución. Todos los sistemas están sujetos a desgaste y degradación del rendimiento con el tiempo. Es posible que se reduzca el tiempo de funcionamiento efectivo, u otros problemas, como la fricción de un componente desgastado que contribuye al ruido que empuja al sistema más allá de los niveles aceptables de OSHA, pueden exigir atención. Cuanto más pueda hacer para extender la vida útil de trabajo de sus sistemas, mayor será el impacto en la rentabilidad.
Si bien el reemplazo total suele ser un gasto de capital importante, la vida útil del sistema a menudo se puede extender al realizar mejoras en el nivel de los componentes. Un clasificador de zapatos que se acerca al final de su vida útil, por ejemplo, a menudo se puede reconstruir. El reemplazo de un componente desgastado podría mantener el clasificador funcionando bien y mantener el tiempo de actividad. O, si hay un problema de ruido, la solución podría ser un producto más nuevo diseñado para un funcionamiento más silencioso. Y si la reconstrucción o el reemplazo de componentes es una opción, a menudo se puede hacer durante el fin de semana antes de la temporada alta.
Otra forma valiosa de administrar el ciclo de vida de su equipo mecánico es una estrategia de repuestos que corresponda a la criticidad y el ciclo de vida proyectado de los componentes clave. Si bien es posible que se haya desarrollado una cuando se compró el sistema, las estrategias de repuestos deben revisarse regularmente a medida que el sistema envejece.
Administración de dispositivos eléctricos
El funcionamiento óptimo del almacén también depende de la fiabilidad de numerosos dispositivos eléctricos, como escáneres, módulos de E/S, actuadores y servomotores. Estos tienen grados de riesgo variables por lo que es importante analizar el riesgo de operar cada dispositivo a medida que envejece. Mientras que algunos proveedores designan la vida útil esperada de cada dispositivo, otros no lo hacen, lo que le permite hacer su mejor estimación.
Un análisis de riesgo eficaz puede proporcionar opciones a las empresas. Por ejemplo, en un análisis de riesgo realizado en servoaccionamientos, los planificadores de automatización identificaron ocho servos Baldor que se encaminaban hacia la obsolescencia, en función de su antigüedad. Una falla en cualquiera de estos podría haber llevado a semanas de tiempo de inactividad antes de que se encontrara un reemplazo. Enfrentando posiblemente $80,000 en gastos de reemplazo, la compañía recibió opciones distintas al reemplazo total inmediato.
Si hubiera algunos repuestos disponibles, la empresa podría comprarlos y reemplazarlos gradualmente. Podría, por ejemplo, reemplazar los cuatro servos más antiguos de inmediato y guardar los que se quitaron para usarlos como copias de seguridad. Esto extendería la vida operativa y brindaría más flexibilidad para distribuir los costos entre gastos de capital y MRO.
Modernización de controladores
La mayoría de los sistemas de manejo de materiales dependen del control PLC. Debido a que su operación es simple, los PLC tienden a durar y la mayoría de los proveedores de PLC anuncian el final de su vida útil con mucha anticipación. Rockwell/Allen Bradley, por ejemplo, ya no es compatible con el PLC TI 45, pero, como se anunció, seguirá siendo compatible con su PLC ControlLogix más reciente.
Cuanto más cerca esté su PLC del final de su vida, mayor será la posibilidad de falla y, si se cae, habrá tiempo de inactividad. Dependiendo de lo que esté en riesgo, la actualización a un PLC más moderno no solo garantiza el funcionamiento, sino que también puede ser una forma de aprovechar más el valor de otros activos.
Además de ser más robustos y confiables, los PLC más nuevos pueden tener suficiente ancho de banda para admitir herramientas analíticas que pueden ayudar a identificar tendencias, lo que puede extender la vida útil de los sistemas que controlan. Además, tener la capacidad de Ethernet puede ayudar a impulsar la integración del sistema de control de almacén (WCS) con otros sistemas de automatización.
Algunas operaciones más pequeñas usan PC para controlar sus plantas. Las PC pueden volverse obsoletas en menos de dos años y, por lo general, es más económico reemplazarlas que actualizarlas.
Software de Gestión de Control de Almacén
La obsolescencia de la plataforma de software que soporta el WCS es una realidad inevitable. Cuando el WCS deja de funcionar, el almacén está inactivo durante lo que podrían ser muchos días, o incluso semanas, de configuración y prueba.
Muchos WCS aún se ejecutan en Windows 2003, que Microsoft ya no admite. Su sistema seguirá funcionando en Windows 2003, pero estará solo si surgen problemas técnicos y puede ser riesgoso conectar aplicaciones heredadas o de terceros a su WCS. Si está ejecutando Windows 2007 y 2008, estará en la misma situación en 2020, cuando Microsoft desconecte esos sistemas. La buena noticia es que Microsoft, como la mayoría de las empresas de software, notifica durante cuánto tiempo admitirán sus productos.
Pero esto también puede brindar una oportunidad. La actualización a la última versión de software compatible podría ser un gasto asequible que maximiza el rendimiento y reduce el riesgo de mantenimiento de otros activos. Con la última versión, por ejemplo, las soluciones de cliente ligero se vuelven posibles, lo que permite la consolidación de la arquitectura de TI en un servidor virtual en lugar de físico. Por una inversión de $250,000 en controles virtualizados, no solo tendría un sistema operativo que sería compatible durante años, sino que también obtendría ventajas en el mantenimiento de software, la recuperación ante desastres y otras áreas, entre las cuales se encuentra la eliminación de la necesidad de dispositivos físicos. servidores.
Mantenimiento de la mejora
Aunque nos hemos centrado en la fase de optimización del ciclo de vida de la automatización, que a menudo se descuida, todas las fases operativas son fundamentales para la mejora continua. La atención a extender el ciclo de vida en la fase de diseño podría manifestarse en un diseño con tecnologías abiertas u objetos de ingeniería reutilizables, de modo que los sistemas puedan incorporar las mejores soluciones sin tener que abandonar toda la inversión.
En la fase de ejecución, la gestión de activos puede mejorarse mediante los sistemas de ejecución de almacenes, que coordinan las operaciones para que los recursos humanos y el equipo se operen y utilicen de manera eficiente. Y es la fase de soporte donde se implementan la gestión de repuestos, el monitoreo de condición, el mantenimiento preventivo y otras estrategias para sostener cualquier medida de optimización que deba tomarse.
Wynright Corp. (Elk Grove, IL), una subsidiaria de propiedad total de Daifuku North America, es un proveedor de sistemas inteligentes de manejo de materiales.
Sistema de control de automatización
- Automatización:Software del sistema de visión actualizado
- Los efectos positivos de la automatización agrícola
- Un sistema de automatización adaptable en acción
- El sistema de automatización promueve la accesibilidad y la maniobrabilidad
- STAEDTLER:el valor de la automatización en la fabricación
- Comprender el valor de la automatización en la fabricación
- Consejos prácticos para prolongar la vida útil de sus punzones
- Usted conoce mejor su sistema de automatización industrial, esto es lo que traemos a la mesa
- El elemento humano de la automatización
- El poder de la IA en la automatización industrial
- Cálculo del costo del ciclo de vida de su sistema compresor