Aspectos destacados:Convención de compuestos 2019
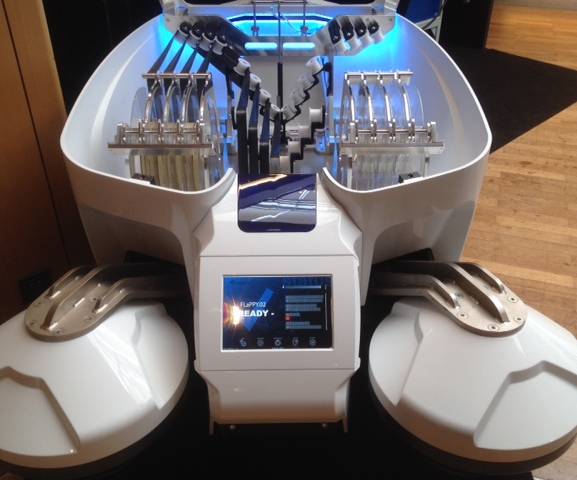
El intrigante prototipo de Flappybot (robot flexible de producción, colocación y ensamblaje autónomo) de DLR es una desviación radical de las grandes y costosas máquinas estáticas comunes en la fabricación de grandes componentes aeroespaciales. Esta unidad AFP autónoma compacta está diseñada para "pasar" directamente sobre el molde. Fuente | DLR
Para que la industria de los compuestos siga creciendo y mejorando su competitividad, debe aprovechar las oportunidades que brindan la digitalización y la automatización. Dos conferencias recientes centradas en la industria aeroespacial en Alemania analizaron lo que podría deparar el futuro de la fabricación de compuestos.
Visitando la fábrica del futuro en Stade
Future Factory for Composites fue el tema de la Convención de Composites de este año en Stade, Alemania, que se llevó a cabo del 12 al 13 de junio. Organizado conjuntamente por CFK Valley e.V. (Stade, Alemania) y Carbon Composites e.V. (Augsburgo, Alemania), el evento atrajo una asistencia récord de casi 450 personas. Una fuerte presencia en los EE. UU. Resultó de una colaboración con la Iniciativa de Fabricación y Materiales Avanzados de Utah (UAMMI, Kaysville, Utah, EE. UU.) Como red de socios y los Estados Unidos como país socio.
En la presentación inaugural, titulada "Digitalización:transición de la fabricación asistida por computadora a la automatización asistida por humanos", el Dr. Jan Stüve, director del Centro de Tecnología de Producción Ligera del Centro Aeroespacial Alemán (Deutsches Zentrum für Luft- und Raumfahrt; DLR; Stade, Alemania) ofreció una muestra del programa por venir. Las tecnologías de fábrica futuras que se están desarrollando en DLR incluyen múltiples robots cooperativos que trabajan juntos para reducir el tiempo de producción y gemelos digitales de máquinas que permiten la optimización de procesos. Otra área clave se refiere a los robots autónomos móviles para escenarios de producción flexibles. Estos incluyen el prototipo FlappyBot, un compacto Unidad de colocación de fibras que se desplaza sobre el molde. Stüve advirtió sobre los peligros potenciales de la automatización excesiva y discutió cómo la digitalización debería reinvolucionar a los seres humanos en el proceso de fabricación.
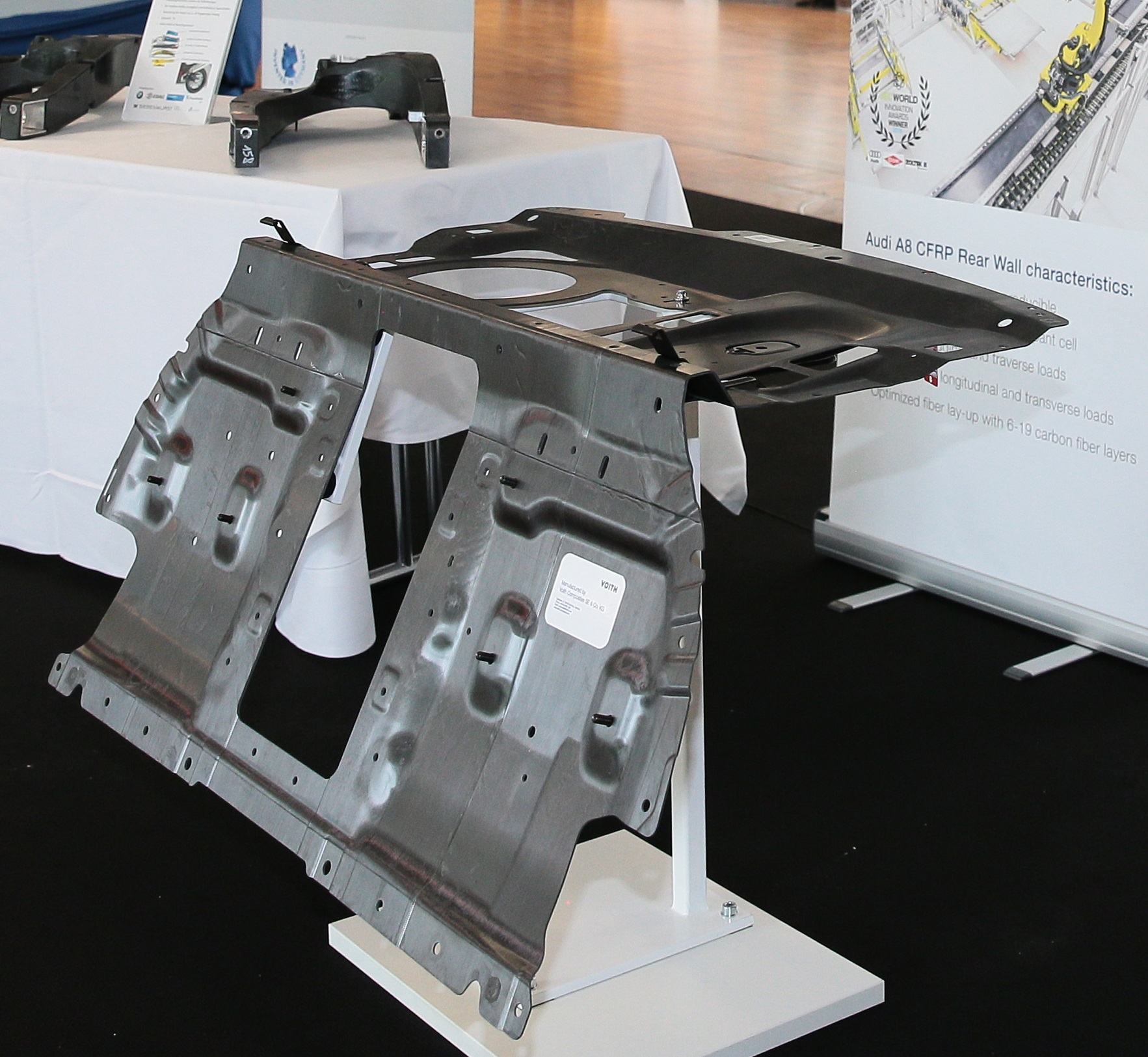
La pared trasera del Audi A8 CFRP, el componente más grande del habitáculo, es fabricada por Voith Composites en un proceso altamente automatizado que permite volúmenes de producción de 65.000 componentes por año. Fuente | CFK Valley
En una segunda conferencia magistral, "Fabricación rápida y compuestos termoplásticos:tendencias y tecnologías", el Dr. Robert G. Bryant, ingeniero de materiales senior del Centro de Investigación Langley de la NASA (Hampton, Va., EE. UU.), Alejó a los delegados de los confines del fábrica terrestre hacia la construcción en el espacio. Una presencia humana a largo plazo en el espacio requerirá refugio y plataformas como primer paso. El desarrollo de cohetes cada vez más grandes para colocar estructuras cada vez más complejas fuera del planeta no es económicamente sostenible. Las soluciones requieren fabricación local o cercana. El uso de un proceso de colocación avanzada de cinta (ATP) sin herramientas que permita la consolidación in situ de piezas de compuestos termoplásticos podría ser la respuesta. En esta nueva técnica, dos robots ATP trabajan uno frente al otro, uno para depositar la cinta termoplástica preimpregnada y el otro actúa como herramienta. La fabricación sin herramientas podría reducir el costo de la fabricación aeroespacial, mejorando la economía de la exploración espacial y beneficiando a otros sectores del mercado (obtenga más información en “Proceso de desarrollo de compuestos termoplásticos sin herramientas de General Atomics Aeronautical”).
Sostenibilidad
Los avances en la fabricación también deben ir acompañados de reducciones en el impacto ambiental. En ese sentido, en la próxima sesión, Jörg Spitzner, fundador de Spitzner Engineers GmbH (Finkenwerder, Alemania), argumentó que para cumplir los objetivos climáticos se necesitan tecnologías de emisiones negativas. La compañía de Spitzner afirma que su concepto patentado de turbina eólica Blancair mejora la eficiencia de la turbina y elimina el CO 2 de la atmósfera. El aire se introduce en un módulo de filtro montado en la góndola, donde el CO 2 se separa para su almacenamiento y reciclaje en la producción de combustibles sintéticos y otras aplicaciones. El aire limpio se libera a través de las aberturas en las puntas de las palas del rotor. Un video que explica el concepto está disponible en el sitio web de Blancair.
Los organizadores de la sesión también presentaron un concepto para la evaluación inteligente de la ecoeficiencia en la producción de compuestos (DLR) y preimpregnados endurecidos a temperatura ambiente fuera del autoclave con capacidad de fuego, humo y toxicidad (FST) (TCR Composites; Ogden, Utah, EE. EE. UU.).
Empoderamiento a través de la simulación
Durante el resto del primer día de la conferencia, la atención se centró en la simulación.
El Dr. Lars Herbeck, director de tecnología de Voith Composites (Garching, Alemania), habló sobre cómo la máquina de colocación automatizada de fibra (AFP) Voith Roving Applicator simplifica la cadena de proceso, lo que permite un proceso de preformado automatizado eficiente con tiempos de ciclo reducidos. Él describió la simulación estructural y de proceso realizada para la línea de fabricación automatizada que es capaz de producir 65,000 componentes por año para la pared trasera trasera de plástico reforzado con fibra de carbono (CFRP) del Audi A8.
Mark Bludszuweit de MET Motoren- und Energietechnik GmbH (Rostock, Alemania) explicó cómo la simulación ofrece información sobre la mejor manera de cargar piezas en un autoclave, lo que permite la optimización del proceso de curado y una mayor productividad. Un gemelo digital desarrollado para el autoclave más grande en las instalaciones de Stade de DLR puede funcionar en paralelo con el proceso real o más rápido para ofrecer predicciones del comportamiento de la pieza.
Otros temas de desarrollo de procesos virtuales cubrieron el modelado de procesos SMC (ESI Group; Chartres-de-Bretagne, Francia) y la simulación de procesos de paneles sándwich para comprender los problemas de arrugas preimpregnados y aplastamiento del núcleo en el autoclave (Airbus Helicopters; Marignane, Francia).
Pasando al modelado de seguridad virtual, Jochen Rühl de Reichenbacher Hamuel GmbH (Dörfles-Esbach, Alemania), parte de Scherdel Gruppe, discutió cómo un enfoque basado en simulación para manejar el polvo y las partículas producidas durante el mecanizado de piezas de CFRP ha brindado beneficios a clientes tales como como Airbus y Premium Aerotec (Augsburg, Alemania). Las simulaciones de mecanizado y la visualización de distribuciones de partículas ayudan a los fabricantes a cumplir con la estricta legislación de salud y seguridad y mejoran los resultados del mecanizado, así como también reducen el tiempo de inactividad y el mantenimiento de la máquina, todo lo cual finalmente se traduce en un menor costo por pieza.
La sesión de simulación también mostró un proyecto patrocinado por Boeing sobre el modelado de costos virtuales de la fabricación de compuestos, teniendo en cuenta las complejas interacciones entre el diseño, la producción y las finanzas para identificar los generadores de costos (Instituto de Tecnología de Massachusetts; Cambridge, Massachusetts, EE. UU.), Y un concepto de planificación de fábrica digital basado en el modelado simulado de cadenas de valor óptimas de compuestos (Fraunhofer IGCV; Augsburg, Alemania).
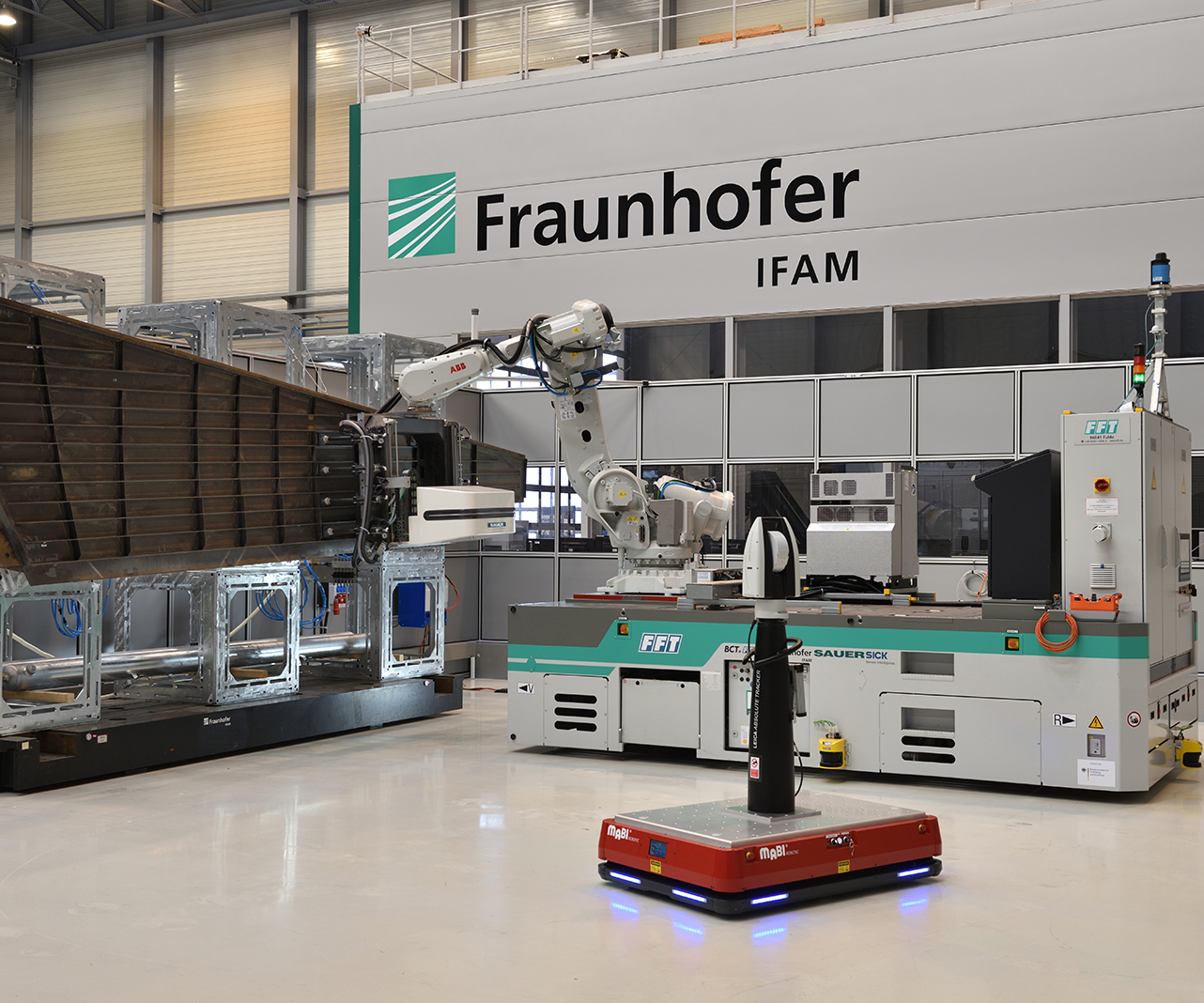
El concepto de mecanizado móvil MBFast18 está compuesto por un vehículo guiado automatizado, un robot y una máquina CNC portátil y ofrece una mayor productividad en la fabricación de piezas de grandes CFRP para aviones. Fuente | Fraunhofer IFAM
Ganadores de premios
Este año, dos proyectos compartieron el Premio a la Innovación CFK Valley y el premio en metálico de 7.500 €.
El primer lugar (y 4.500 €) fue para el proyecto de sistemas robóticos móviles MBFast18, que desarrolló un sistema de mecanizado CNC móvil basado en vehículos guiados automatizados (AGV) para piezas de aviones grandes de CFRP.
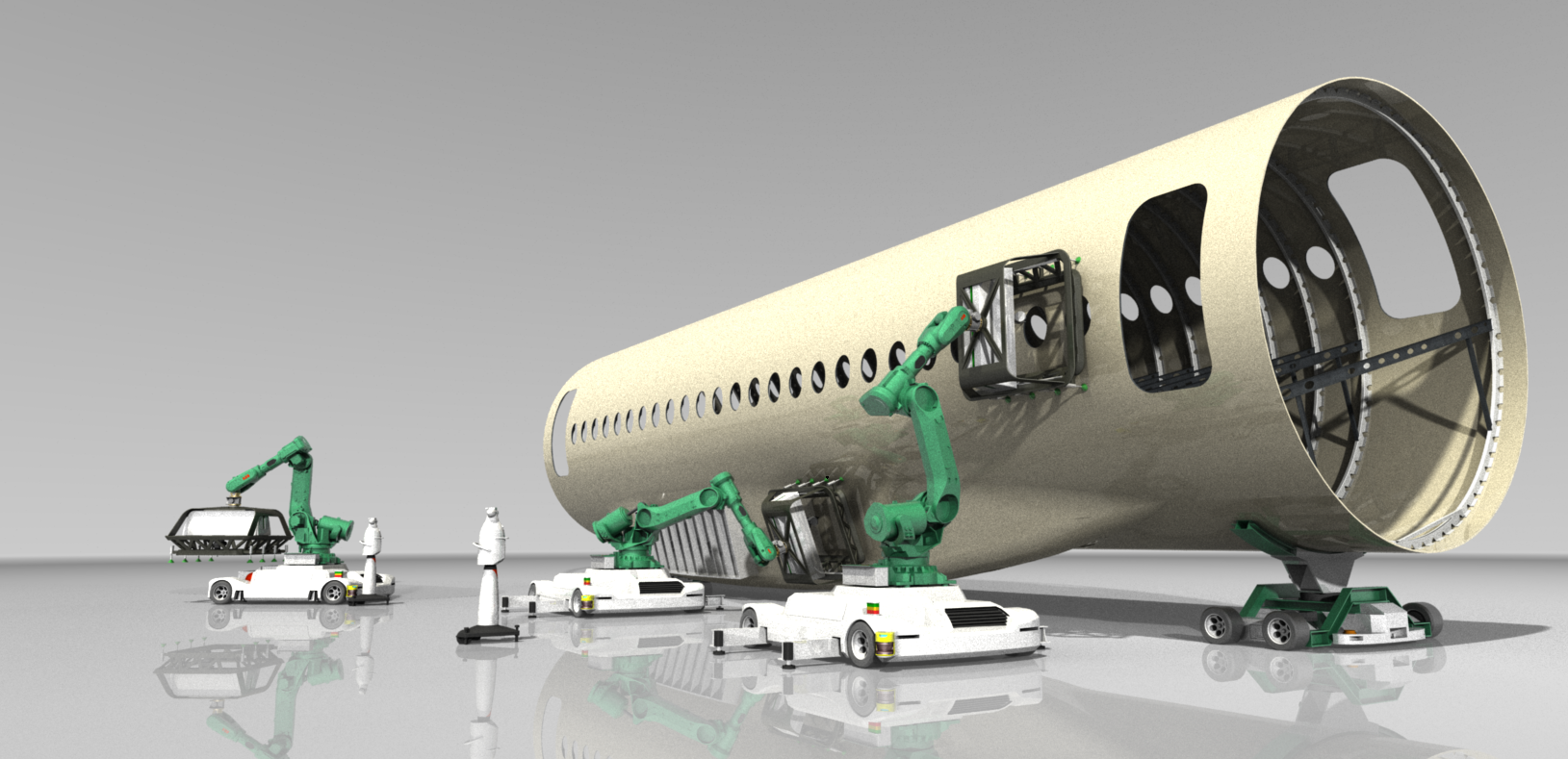
Fuente | Fraunhofer IFAM
En comparación con los costosos sistemas de mecanizado estáticos de la actualidad para grandes estructuras de aeronaves, los sistemas robóticos móviles más pequeños permiten una fabricación flexible y una mayor productividad.
El sistema MBFast18 emplea una plataforma autónoma de 4,6 metros de largo construida por FFT Produktionssysteme GmbH &Co. KG (Fulda, Alemania), sensores de navegación y seguridad suministrados por SICK AG (Waldkirch, Alemania) y una máquina CNC de 5 ejes de SAUER. / DMG MORI (Suhl y Bielefeld, Alemania). Un rastreador láser móvil desarrollado por el Instituto Fraunhofer de Tecnología de Fabricación y Materiales Avanzados (IFAM; Stade, Alemania) posiciona el robot con precisión. La unidad de perforación, con un espacio de trabajo de hasta 0,5 metros cuadrados, se sujeta al componente mediante pinzas de vacío; Las posiciones de perforación se calculan y transmiten a la máquina mediante un software desarrollado por BCT GmbH (Dortmund, Alemania). Este concepto también es aplicable a las operaciones de manipulación y montaje y a otras industrias como la energía eólica y ferroviaria.
Vea un video sobre el proyecto MBFast18:
El segundo lugar fue para la start-up Hyconnect GmbH (Hamburgo, Alemania) por su tecnología de unión de compuestos metálicos FAUSST. Inicialmente, la empresa se dirige al sector de la construcción naval, donde la unión de materiales compuestos al metal es una barrera importante para una adopción más generalizada de materiales compuestos. La solución FAUSST emplea un tejido híbrido que consta de fibras metálicas y de vidrio tejidas por urdimbre que permite unir mecánicamente metales y materiales compuestos. El lado de fibra metálica se une a un perfil de acero que se puede soldar a estructuras metálicas, y el otro lado se lamina al componente compuesto. Se dice que la tecnología patentada acelera significativamente el proceso de diseño y unión. Actualmente se están probando aplicaciones de prototipos iniciales.
Vea una introducción al proceso de adhesión a FAUSST:
Habilitación mediante automatización
El segundo día vio el galardonado proyecto MBFast18 explorado con más detalle en las presentaciones de Christoph Brillinger, gerente de proyectos de Fraunhofer IFAM, y el Dr. Gregor Graßl de FFT, quien discutió los desafíos de desarrollar procesos inteligentes y sistemas de control de plantas para operaciones de múltiples robots. . Jerome Berg, ingeniero de planta de Northrop Grumman Innovation Systems (Clearfield, Utah, EE. UU.), Describió la fabricación automatizada de largueros de aviones Airbus en las instalaciones de la compañía en Utah utilizando un proceso AFP desarrollado internamente, y Uwe Lang de Evonik Resource Efficiency GmbH (Darmstadt , Alemania) introdujo "Sandwich Technology 4.0", una tecnología de fabricación automatizada para altas tasas de producción que emplea el material de núcleo de espuma ROHACELL de la empresa. En colaboración con DLR y el centro tecnológico de Airbus, CTC GmbH (Stade, Alemania), se demostró un proceso de preformado altamente automatizado para la puerta del tren de aterrizaje delantero de un avión.
Vea un video del proceso de preformado:
En un viaje a la realidad virtual, Felix Hünecke, jefe de desarrollo comercial de ABSOLUTE Reality GmbH (Hamburgo, Alemania), mostró cómo se pueden crear, editar y complementar modelos 3D de edificios con imágenes, documentos y videos para crear entornos virtuales que pueden ser visto desde cualquier parte del mundo. La empresa creó un recorrido en 3D por una sala de producción de DLR en Stade.
Dé un paseo por la sala de producción de DLR:
Felix Schreiber, CEO, ARK Group (Aquisgrán, Alemania), discutió el proceso y los beneficios de costos de los datos estructurados de la máquina en una línea de producción automatizada de moldeo por transferencia de resina (RTM), mientras que Sascha Backhaus de CTC GmbH discutió la automatización modular en la fabricación de compuestos y el Hybr -Proyecto iT, que está desarrollando equipos donde humanos y robots trabajan juntos con sistemas de asistencia basados en software.
Ningún evento sobre la futura fábrica podría descuidar el tema de la inteligencia artificial (IA), y Amir Ben-Assa, CMO de Plataine (Waltham, Mass., EE. UU.) Discutió las oportunidades y desafíos de implementar IA en la fabricación de compuestos. Presentó aplicaciones prácticas de la IA, desde alertas (por ejemplo, retrasos en la producción o problemas de calidad) hasta recomendaciones (por ejemplo, selección optimizada de materiales). Los asistentes digitales basados en inteligencia artificial en Google Glass podrían ser otra posibilidad, ya que ofrecen interacción del usuario "manos libres" con la inteligencia artificial en el piso de producción y presentación de alertas visuales y de audio en tiempo real.
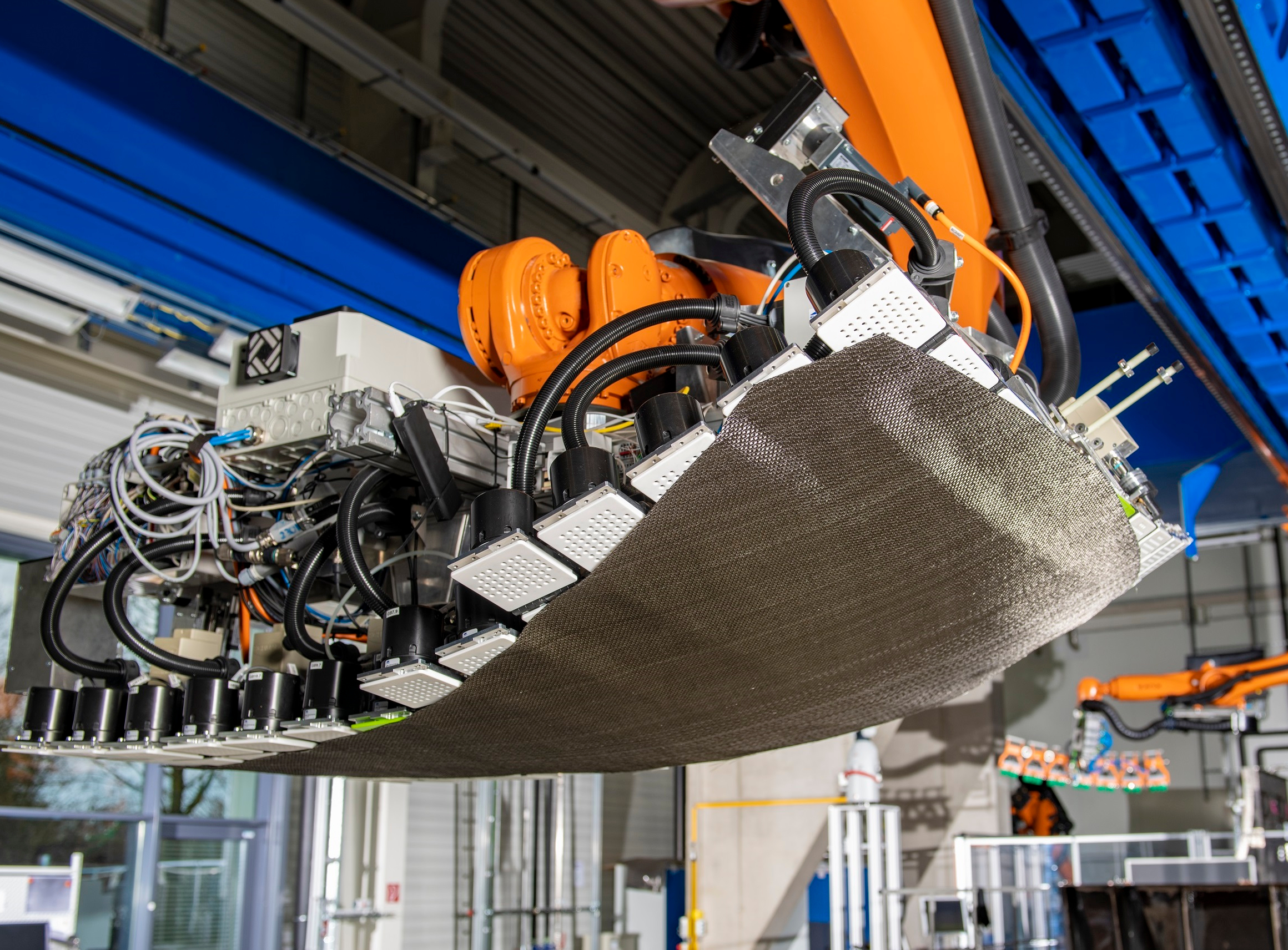
La celda de robot multifuncional de ZLP Augsburg se diseñó para permitir el desarrollo de procesos integrados para la fabricación de grandes componentes compuestos a escala industrial. Fuente | DLR
Otros temas incluidos:
- Detección de fibra óptica para la monitorización inteligente de procesos en grandes estructuras compuestas (MT Aerospace AG; Augsburg, Alemania);
- Un sistema de control inteligente para la fabricación automatizada de compuestos (National Composites Centre, Bristol, Reino Unido);
- Un sistema de control de calidad basado en modelos para el termoformado de componentes pequeños (Faserinstitut Bremen e.V .; FIBER, Bremen, Alemania);
- Un proceso para el moldeo por compresión de termoplásticos discontinuos reforzados con fibra para aplicaciones aeronáuticas, basado en una automatización flexible y escalable a piezas de gran tamaño (ACT Aerospace; Gunnison, Utah, EE. UU.);
- Un proceso RTM isotérmico que ofrece tiempos de ciclo reducidos para la producción de piezas de CFRP de gran volumen (Airbus Helicopters)
- Producción a gran escala de perfiles termoplásticos complejos de fibra de carbono de alto rendimiento para puntales, tuberías y ejes de transmisión utilizando preformas de cinta casi en forma de red y conformado por inyección (herone GmbH; Dresden, Alemania). Obtenga más información sobre herone y este proceso en "Conformado por inyección para estructuras termoplásticas unificadas de alto rendimiento".
Diez años de progreso en Augsburgo
En un evento separado, el quinto coloquio de DLR sobre tecnología de producción el 15 de mayo contó con cerca de 200 invitados reunidos en su Centro de Tecnología de Producción Ligera (Zentrum für Leichtbauproduktionstechnologie, ZLP) en Augsburg. El evento celebró el décimo año de ZLP en Augsburgo, donde hoy aproximadamente 60 empleados se concentran en la automatización y digitalización de la producción de compuestos.
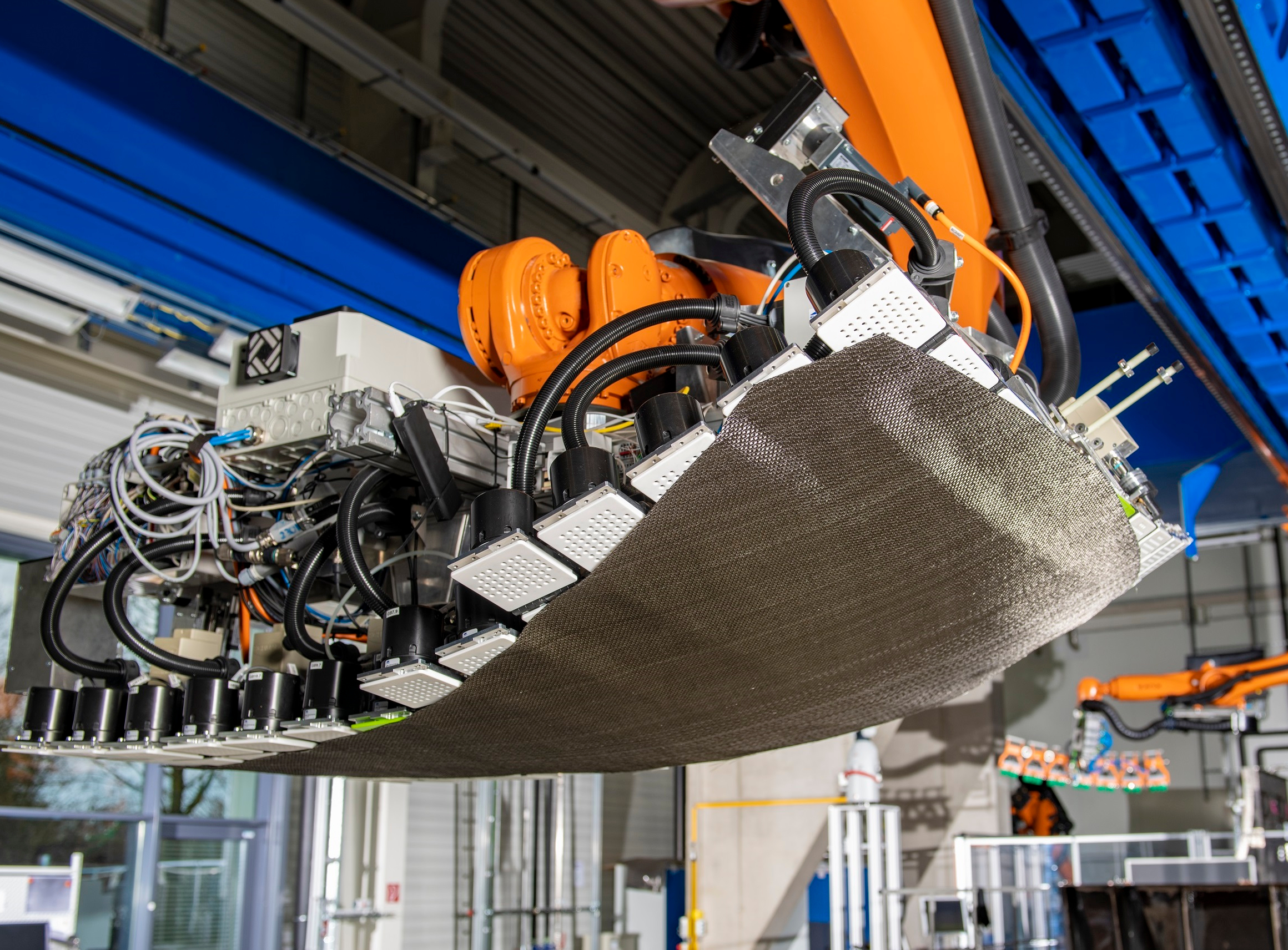
Una pinza robótica para drapeado automatizado, parte del proceso de fabricación integrado de ZLP Augsburg para componentes estructurales a gran escala. Fuente | DLR
El día comenzó con dos presentaciones de la Universidad de British Columbia (UBC; Vancouver, Canadá), que inició una cooperación con DLR en 2016. El profesor Dr. Anoush Poursartip, codirector de la Digital Learning Factory Initiative de UBC, presentó el concepto de una fábrica de aprendizaje para composites inspirada en los hospitales de enseñanza médica. La fábrica de aprendizaje de materiales compuestos, que se ubicará en el campus de Okanagan de la UBC, se diseñará para integrar la investigación y la educación con las actividades industriales. Un gemelo digital alojado en UBC Vancouver combinará datos de la fábrica física con simulación para optimizar los procesos de producción de compuestos aeroespaciales. A continuación, el profesor Dr. Homayoun Najjaran de UBC y Marian Körber de DLR analizaron la optimización de procesos de fabricación complejos en un entorno virtual y cómo la experiencia de UBC en técnicas de aprendizaje automático e inteligencia artificial se está utilizando para reducir el tiempo y el costo del desarrollo de sistemas robóticos en DLR. . Se utilizó un método de aprendizaje profundo para capacitar a la pinza robótica de ZLP para el drapeado automatizado, una parte clave de la cadena de procesos automatizados de las instalaciones de Augsburg para la fabricación de piezas grandes de CFRP. La pinza, que cuenta con 127 módulos de succión con fuerza de succión variable, reconoce y recoge el material cortado; los módulos asumen la geometría necesaria para colocarlo en posición en el molde.
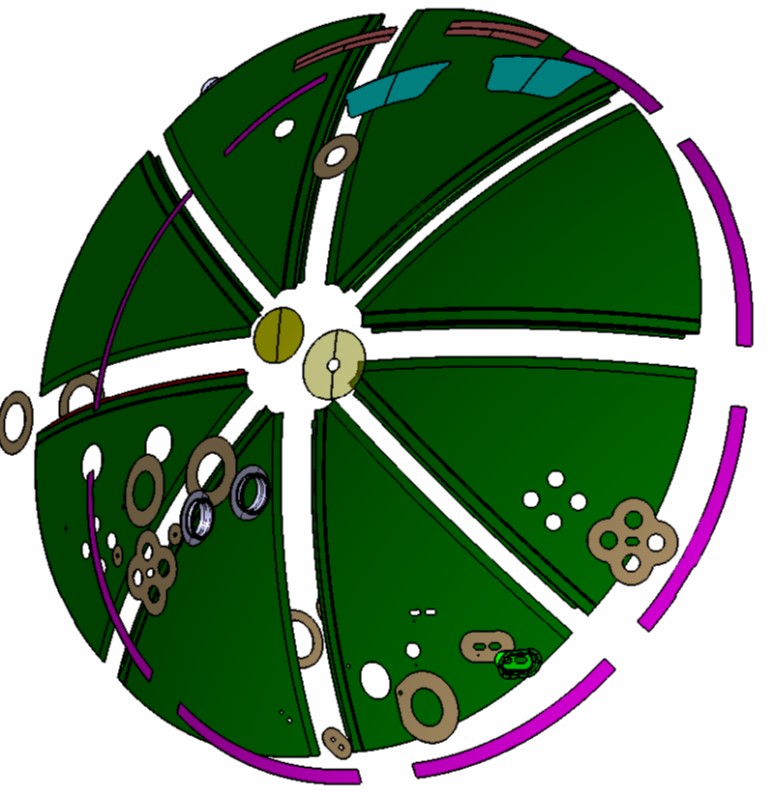
Los componentes compuestos termoplásticos para el diseño de mamparo de presión trasera de Premium Aerotec se unen mediante una técnica de soldadura por resistencia desarrollada en ZLP Augsburg. Fuente | Aerotec Premium
Las tecnologías de termoplásticos son otro enfoque para ZLP Augsburg. Ralph Männich y Alexander Sänger de Premium Aerotec GmbH describieron un proyecto para desarrollar el primer mamparo de presión trasera (RPB) termoplástico del mundo para aviones de pasillo único. La compañía está colaborando con ZLP Augsburg, Toray Advanced Composites y el Instituto de Materiales Compuestos (IVW) en un diseño que consta de ocho segmentos de CFRP con largueros integrados unidos mediante una tecnología de soldadura por resistencia desarrollada por ZLP. Los procesos automatizados con tiempos de ciclo cortos permiten una producción de gran volumen. La finalización de la tecnología (hasta TRL 6) está programada para 2020 y la implementación está prevista para 2021/2022. En el Salón Aeronáutico de París de junio, Premium Aerotec mostró un demostrador 1:1 para un avión de la serie Airbus A320. En comparación con los mamparos de presión A320 actuales hechos de componentes de aluminio remachados, se dice que la pieza termoplástica ofrece las mismas propiedades mecánicas con un ahorro de peso del 10-15% y una reducción del 50% en el tiempo de producción. En la siguiente charla, el Dr. Stefan Jarka y Manuel Endraß de DLR continuaron con el tema de la soldadura termoplástica, profundizando en las capacidades de unión y NDT de ZLP Augsburg, y su papel en el proyecto RPB.
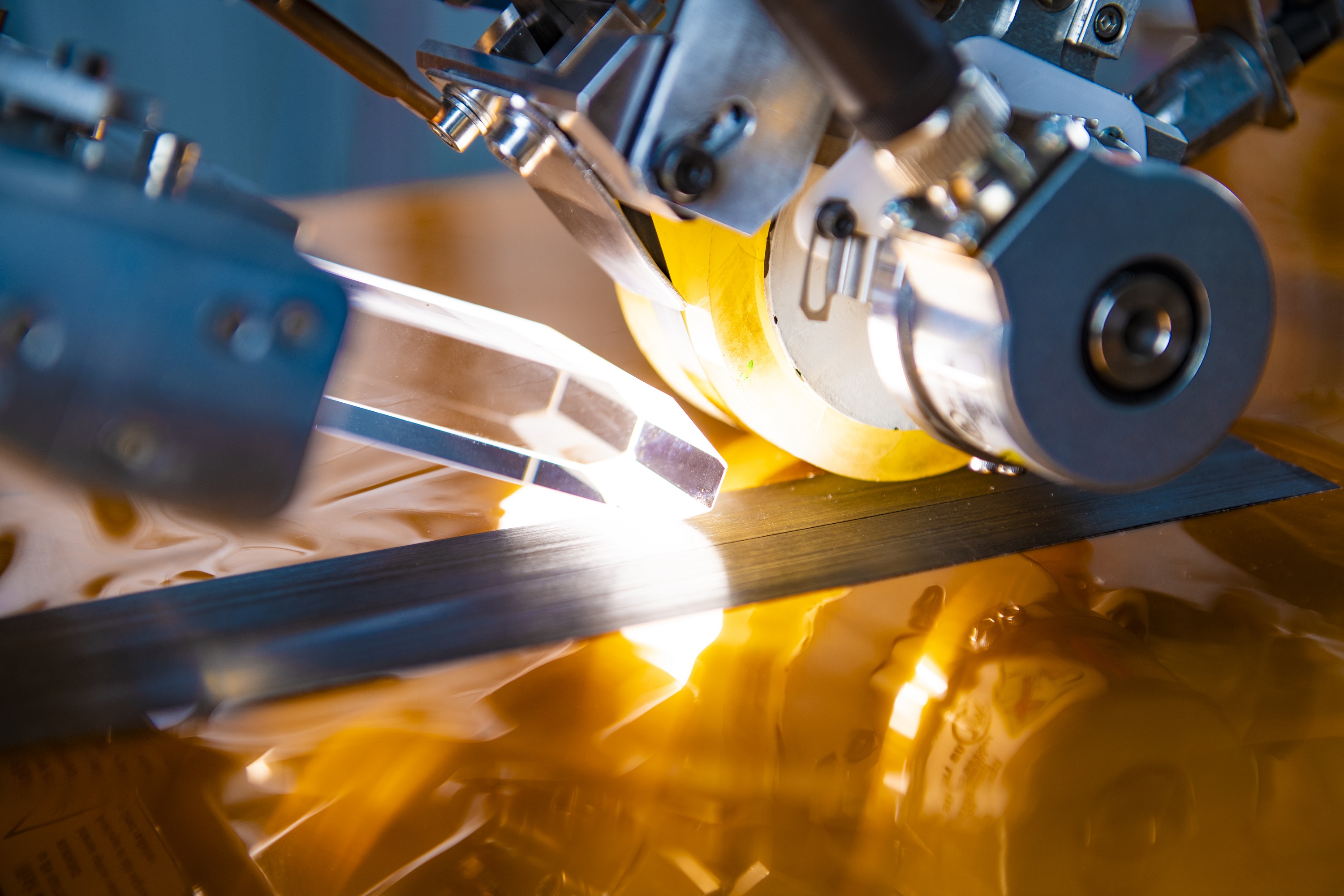
ZLP Augsburg está investigando AFP in situ basado en lámpara flash de compuestos termoplásticos, una solución de energía pulsada que elimina los recintos de seguridad requeridos para AFP basado en láser. Fuente | DLR
Los compuestos termoplásticos también ofrecen oportunidades en aplicaciones espaciales. Las presentaciones de Ralf Hartmond, MT Aerospace AG y Lars Brandt, gerente de proyectos para aplicaciones relacionadas con el espacio en DLR, describieron el desarrollo de una etapa superior termoplástica reforzada con fibra de carbono para la próxima generación de Ariane lanzacohetes. Brandt detalló el trabajo de DLR en la selección de materiales para el tanque de hidrógeno líquido (LH 2 ) tanque, donde el PEEK de fibra de carbono y el PAEK de bajo derretimiento (LM) son prometedores, y el desarrollo de un proceso de AFP compuesto termoplástico in situ para permitir un enfoque de fabricación aditiva ajustada. ZLP está comparando un nuevo proceso de AFP in situ asistido por lámpara de flash con el AFP tradicional asistido por láser.
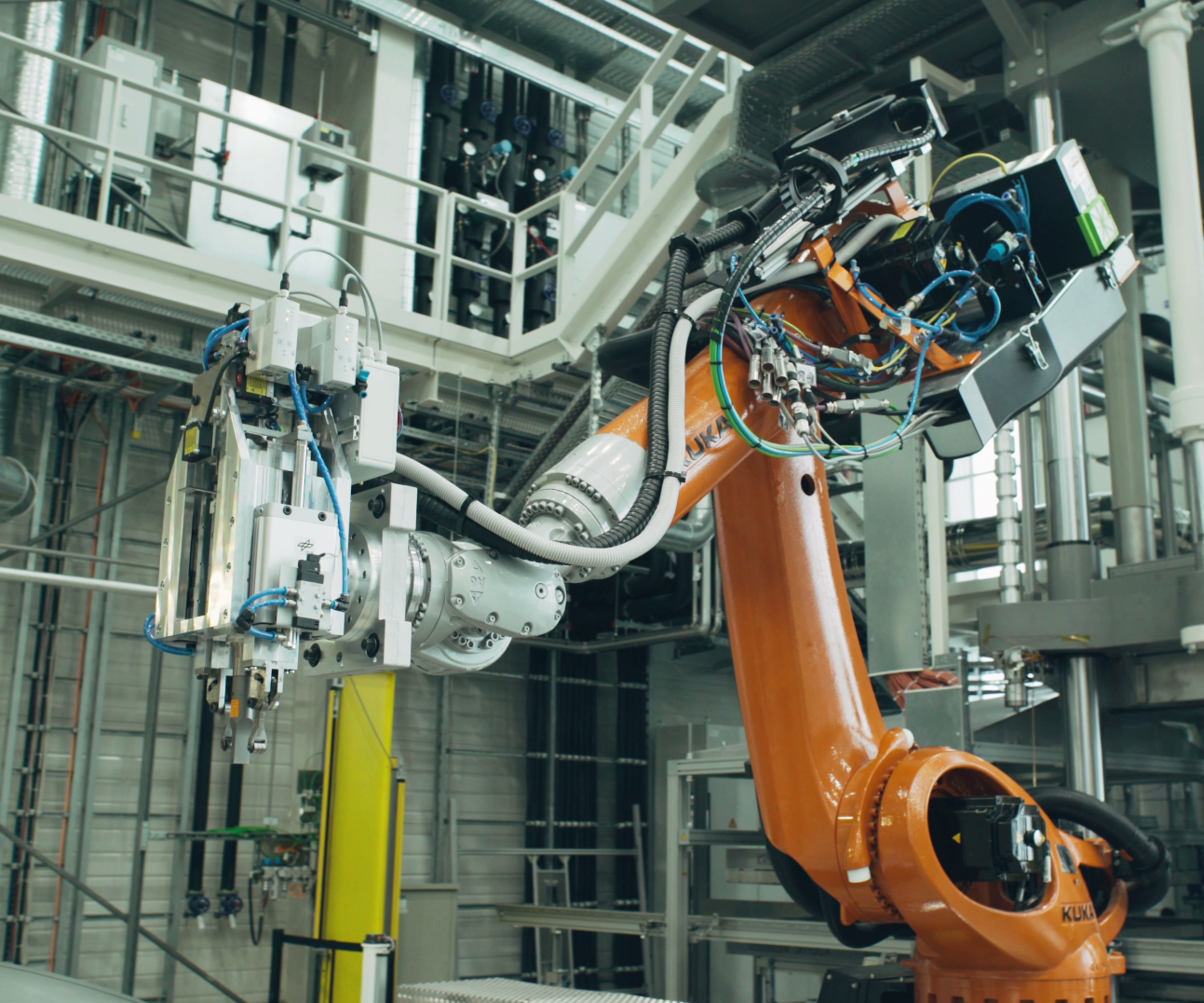
Unir tecnologías será clave para la introducción exitosa de compuestos termoplásticos en futuras aplicaciones aeroespaciales. ZLP en Augsburgo ha desarrollado un sistema de soldadura ultrasónica continua basado en un robot que consiste en un efector final montado en un robot KUKA QUANTEC KR210 sobre una pista lineal de 7 m. Esto se ha demostrado en componentes que incluyen un panel de fuselaje reforzado y un mamparo de presión trasero. Fuente | DLR
El día concluyó con un discurso de apertura que invita a la reflexión del profesor Dr. Michael Kupke, director de ZLP Augsburg, titulado "Digitalización y producción flexible". Preguntó si el auge de la economía de las plataformas digitales presenta oportunidades o riesgos para los fabricantes de compuestos, y señaló que la TI se está convirtiendo en una competencia central y debe tratarse como una ventaja competitiva de valor agregado en lugar de un centro de costos. También dijo que hay un cambio de paradigma en curso desde la planificación detallada a la autoorganización (producción ajustada) y la automatización combinada con la digitalización. La IA, dice, hace posible la producción autónoma y flexible. Sin embargo, concluyó Kupke, es fundamental valorar e integrar las habilidades humanas, que son vitales para la toma de decisiones y la mejora de procesos.
Resina
- Cuatro preguntas candentes para la fabricación aditiva en 2019
- 25 hitos clave que impulsaron la fabricación aditiva en 2019
- 3 predicciones de fabricación para 2019
- Los 10 principales avances en tecnología de fabricación de materiales compuestos
- Fabricación de materiales compuestos:Fabricación de materiales compuestos
- Más de JEC World 2019
- Vista previa de JEC World 2019:SABIC
- Personas en materiales compuestos - Enero de 2019
- La tecnología de automatización destaca la seguridad y la fabricación flexible
- 2019:predicciones de fabricación
- Prácticas recomendadas de marketing de fabricación para 2019