Obra maestra con uso intensivo de compuestos:Corvette 2020, Parte 1
Para la Parte 2, lea “Obra maestra con uso intensivo de compuestos:Corvette 2020, Parte 2”.
El tan esperado Chevrolet Corvette de octava generación (C8) de General Motors Co. (GM, Detroit, Michigan, EE. UU.), Que ha estado generando elogios desde su revelación oficial el 18 de julio de 2019, comenzó la producción comercial a principios de este año. El nuevo Corvette Stingray Los convertibles y cupés son notables no solo por su belleza y el hecho de que GM ha producido un cohete de motor central de alto rendimiento, legal para la calle, a partir de menos de $ 60,000 USD, un tercio del precio de un motor central de rendimiento comparable. automóviles, pero también cuentan con una impresionante variedad de contenido compuesto nuevo y genuinamente innovador, que describiremos aquí y en la Parte 2 el próximo mes.
La nueva configuración del motor lo cambia todo
La ingeniería de GM entró en el diseño preliminar sabiendo que estarían trabajando en un vehículo de motor central:el primer Corvette de producción. en ocho generaciones para lucir esa configuración. “Desarrollamos la arquitectura del motor delantero tanto como pudimos para mejorar el rendimiento, por lo que cambiar a un diseño de motor central fue el siguiente paso lógico para mejorar un automóvil que ya era excelente y ser el líder del segmento”, explica Tadge Juechter, ingeniero en jefe ejecutivo de GM. -Global Corvette . Equipado con el paquete de rendimiento Z51, el Corvette Stingray 2020 Puede acelerar de 0 a 60 mph (0-97 kmh) en 2,9 segundos y alcanzar velocidades máximas de 194 mph (312 kmh). Empujar el motor hacia la parte trasera del vehículo afectó muchas cosas, incluido el centro de gravedad del automóvil, la posición relativa de los ocupantes, la ubicación de la transmisión y el diseño de los paneles debajo de la carrocería y el almacenamiento del maletero. El diseño del motor central también introdujo temperaturas de funcionamiento más altas y ruido en nuevas áreas del automóvil.
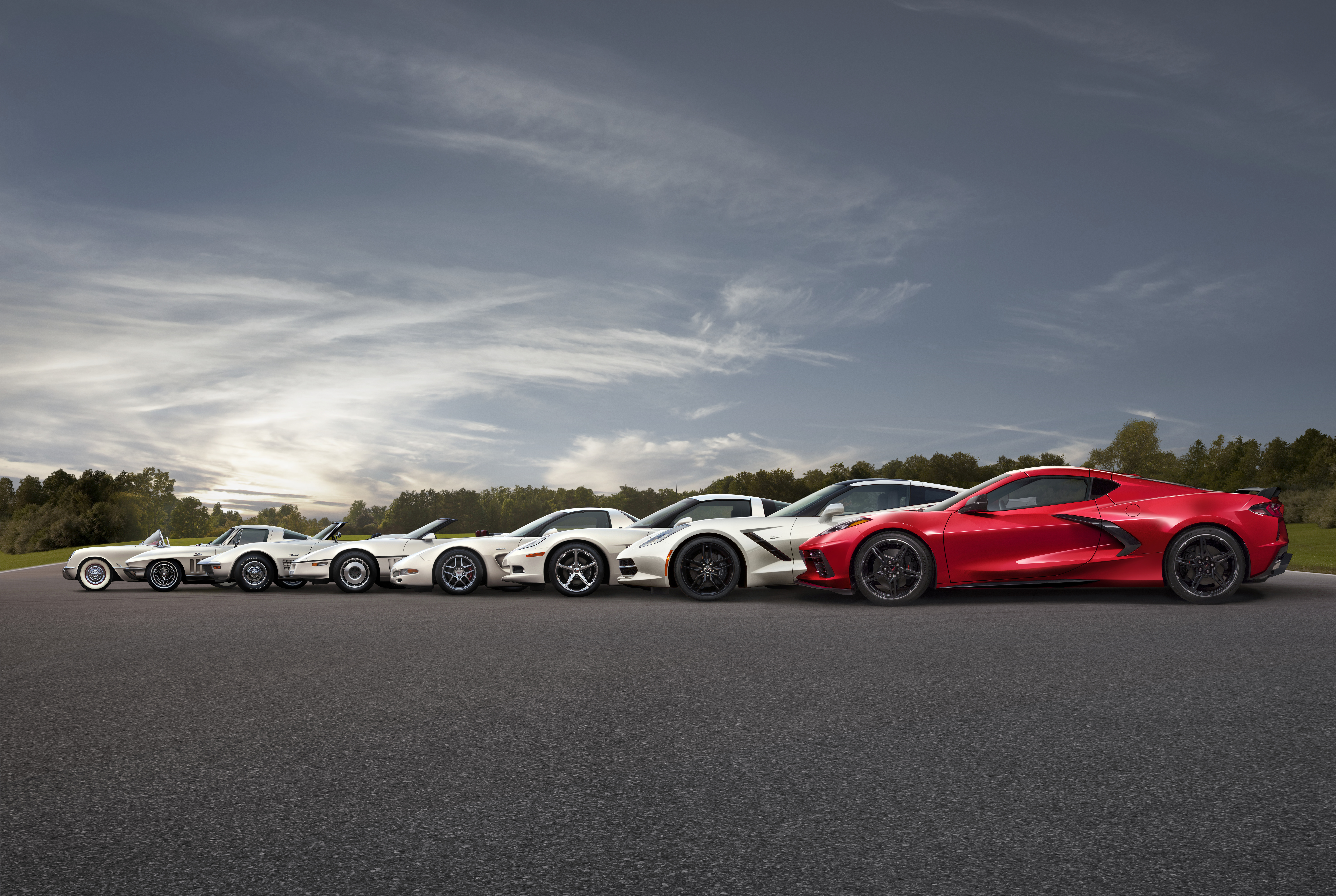
"Debido al motor central, tuvimos que hacer las cosas de manera diferente", explica Ed Moss, Corvette Responsable del grupo de ingeniería de estructura de la carrocería. “Desde el principio, tuvimos muchas discusiones sobre cómo diseñar la estructura de la carrocería. En un momento, todo estaba sobre la mesa mientras discutíamos la mejor manera de diseñar y construir cada sistema. Por ejemplo, debatimos el metal frente al compuesto para las timoneras. Si hubiéramos conservado las timoneras compuestas del C7, tendríamos que unirnos al pilar de la bisagra [pilar A], que está inmediatamente adyacente a la rueda delantera en un vehículo de motor central, dejando muy poco espacio para el paquete. Fuimos con el metal allí. Incluso discutimos brevemente los paneles de carrocería de metal versus compuestos. Sin embargo, hubiera sido económicamente inviable crear las líneas de estilo del C8 en colores metálicos ".
"Un verdadero desafío al que nos enfrentamos fue cómo manejar la inducción de aire", recuerda Chris Basela, Corvette ingeniero jefe de estructura de la carrocería, explicando la necesidad de un método diferente para canalizar el aire de enfriamiento hacia y a través del motor V8 de aspiración natural de 495 caballos de fuerza y 6.2 litros, que genera 470 libras-pie (637 Newton-metros) de torque. “Probamos todo tipo de diseños que obligaban al aire a tomar caminos realmente tortuosos, creando remolinos y flujos que no queríamos. Se necesitó mucho trabajo iterativo con el equipo del tren motriz para desarrollar la mejor ruta para el flujo de aire porque el automóvil necesita respirar libremente sin restricciones. También necesitábamos acceso a la caja de aire y tuvimos que trabajar alrededor del espacio del maletero trasero. Otro problema fue el calor y el ruido del motor en el compartimiento de pasajeros, porque los ocupantes ya no se sientan detrás del motor, sino que se colocan directamente frente a él. Y éramos especialmente conscientes de la calidad del aire de la cabina, ya que las leyes habían cambiado en Europa y en otros lugares desde el C7, por lo que trabajamos muy duro para reducir los COV [compuestos orgánicos volátiles] ”.
“Incluso averiguando cómo ensamblar el coche fue un desafío ”, añade Moss. “Con un diseño de motor delantero, tiene un capó largo y un compartimiento de motor grande, lo que brinda a los operadores mucho espacio para construir el automóvil desde el interior del compartimiento, incluso con la viga del parachoques delantero ya soldada. En el Corvette de motor central , con su clip frontal muy corto, mantenemos la parte delantera del automóvil abierta a medida que se construye el vehículo, luego atornillamos el parachoques delantero ”.
“Fue todo un acto de equilibrio conseguir las formas adecuadas, al tiempo que nos aseguramos de que nuestros proveedores pudieran producir las piezas y nuestro equipo en Bowling Green [el Corvette de GM con sede en Kentucky planta de ensamblaje] podría ensamblarlos ”, continúa Basela. "Al final, solo hubo un material compuesto remanente del cuerpo del C7 al C8". Se trataba de un compuesto para molduras de láminas (SMC) resistente de clase A, gravedad específica (SG) 1,2 desarrollado para el Corvette 2016 y se utiliza en una variedad de cierres exteriores en el nuevo vehículo.
Arquitectura del vehículo
Durante cuatro generaciones (C5-C8), Corvettes han presentado una estructura de carrocería multimaterial de tres capas:el marco , generalmente una mezcla de aluminio o acero, esta vez con una pieza de compuesto reforzado con fibra de carbono (CFRP); la estructura de la carrocería , que es en gran parte compuesto adherido para capitalizar el diseño y la flexibilidad de fabricación; más liquidaciones integradas (paneles de la carrocería), que han sido compuestos desde Covette's Debut en junio de 1953. Esta estructura híbrida en capas no solo proporciona un peso ligero asequible en altos volúmenes de producción, especialmente para automóviles de esta clase de rendimiento, sino que también permite producir múltiples variantes de vehículos con una baja inversión en herramientas. De hecho, para el C8 actual, GM logró producir todos los paneles de carrocería compuestos de Clase A (interiores y exteriores adheridos) tanto en el modelo base coupé como en el convertible utilizando solo 20 herramientas.
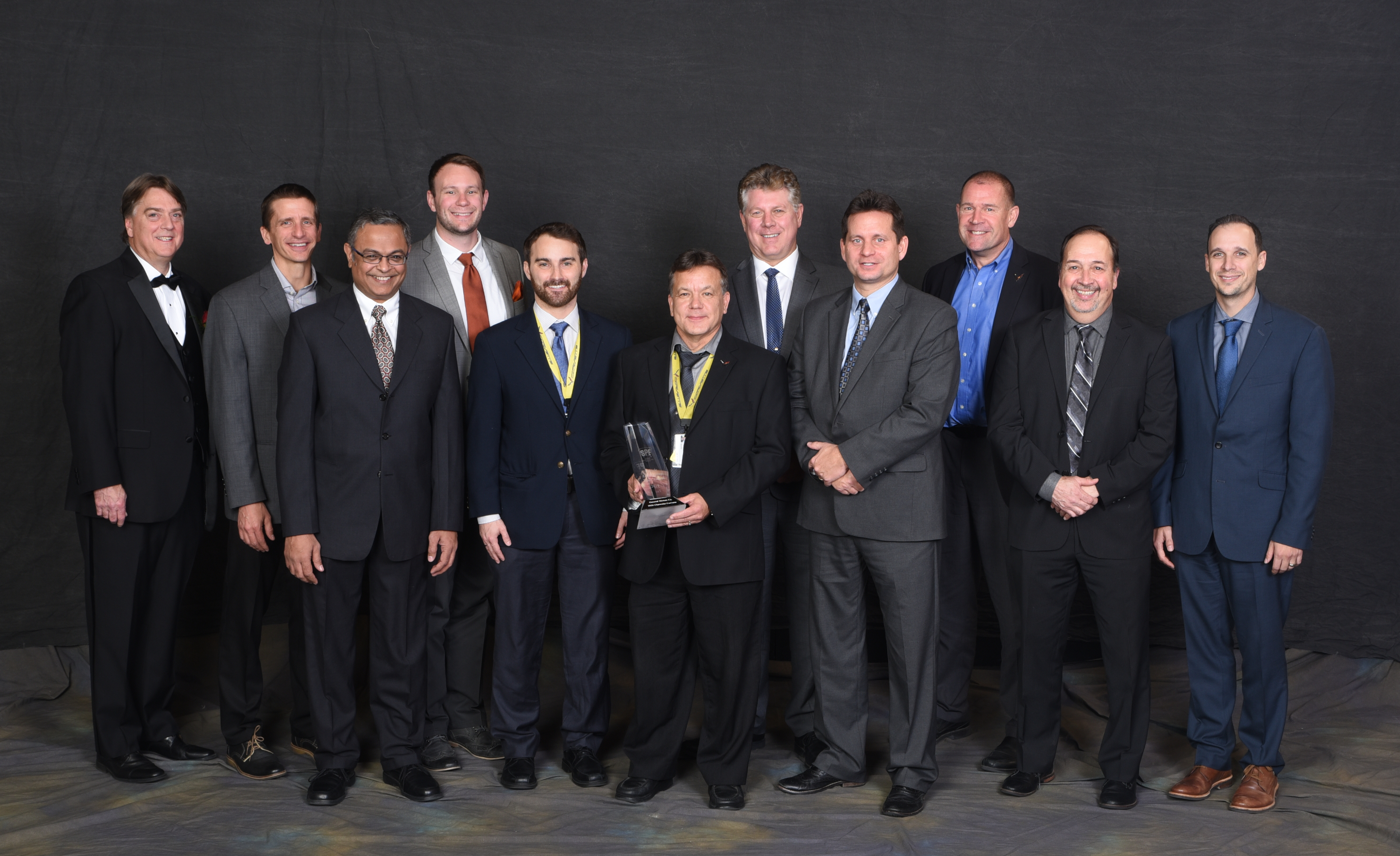
Además, Corvettes siempre se han diseñado con una arquitectura de techo abierto, independientemente de si son en realidad descapotables o cupés con paneles de techo fijos o desmontables. Debido a que los vehículos de techo abierto generalmente son menos rígidos que los de techo fijo, un enfoque importante para cada Corvette ' La ingeniería es siempre crear la base más rígida posible para mejorar la suspensión y la dirección. Históricamente, los túneles (transmisiones de alojamiento y ejes de transmisión en vehículos con motor delantero) han dominado Corvette estructuras de la carrocería y han sido los habilitadores clave para lograr una alta rigidez a la torsión. En el caso del nuevo Corvette , GM logró una rigidez aún mayor. Sin el techo, la carrocería del C8 es un 53,78% más rígida que un competidor de motor central de alto rendimiento de referencia, un 29,27% más rígida que un segundo competidor de motor central de alto rendimiento y un 13,79% más rígida que el C7. Dos piezas compuestas contribuyeron de forma importante a la rigidez del vehículo:una directamente fijada a la estructura del bastidor (viga del parachoques trasero) y otra fijada a la parte inferior de la carrocería (cierre del túnel inferior).
Estructura del marco
El marco del C8 es en gran parte de aleación de aluminio con una pieza de CFRP desarrollada para cumplir con los estrictos objetivos de GM en dólares por kilogramo. En contraste, el marco del C7 era completamente de aluminio y el C6 era principalmente de acero.
La única pieza compuesta directamente montada en el marco que viaja con la carrocería en blanco (BIW) a través del proceso de recubrimiento de óxido electroforético (que GM llama ELPO), es una viga de parachoques trasera CFRP única. Esta parte ayuda a endurecer el cuadro y contribuye al rendimiento del impacto trasero. Su forma curva, posible gracias a un proceso novedoso llamado pultrusión de radio desarrollado por Thomas GmbH + Co. Technik + Innovation KG (TTI, Bremervörde, Alemania), le permite adaptarse a las señales de estilo trasero y encajar en un espacio de paquete limitado mientras mantiene la integridad dimensional cerca. al calor del compartimento del motor. Como la primera pieza pultruida curva de la industria automotriz (vea nuestra característica completa sobre esta pieza en la edición de mayo de 2020 de CW), Shape Corp. (Grand Haven, Michigan, EE. UU.) Produjo la viga hueca de dos cámaras en equipos desarrollados y construido por TTI. La viga pesa solo 1,3 kilogramos y cuenta con un ojo de gancho de remolque adherido / atornillado capaz de 25 kilonewtons de fuerza de extracción.
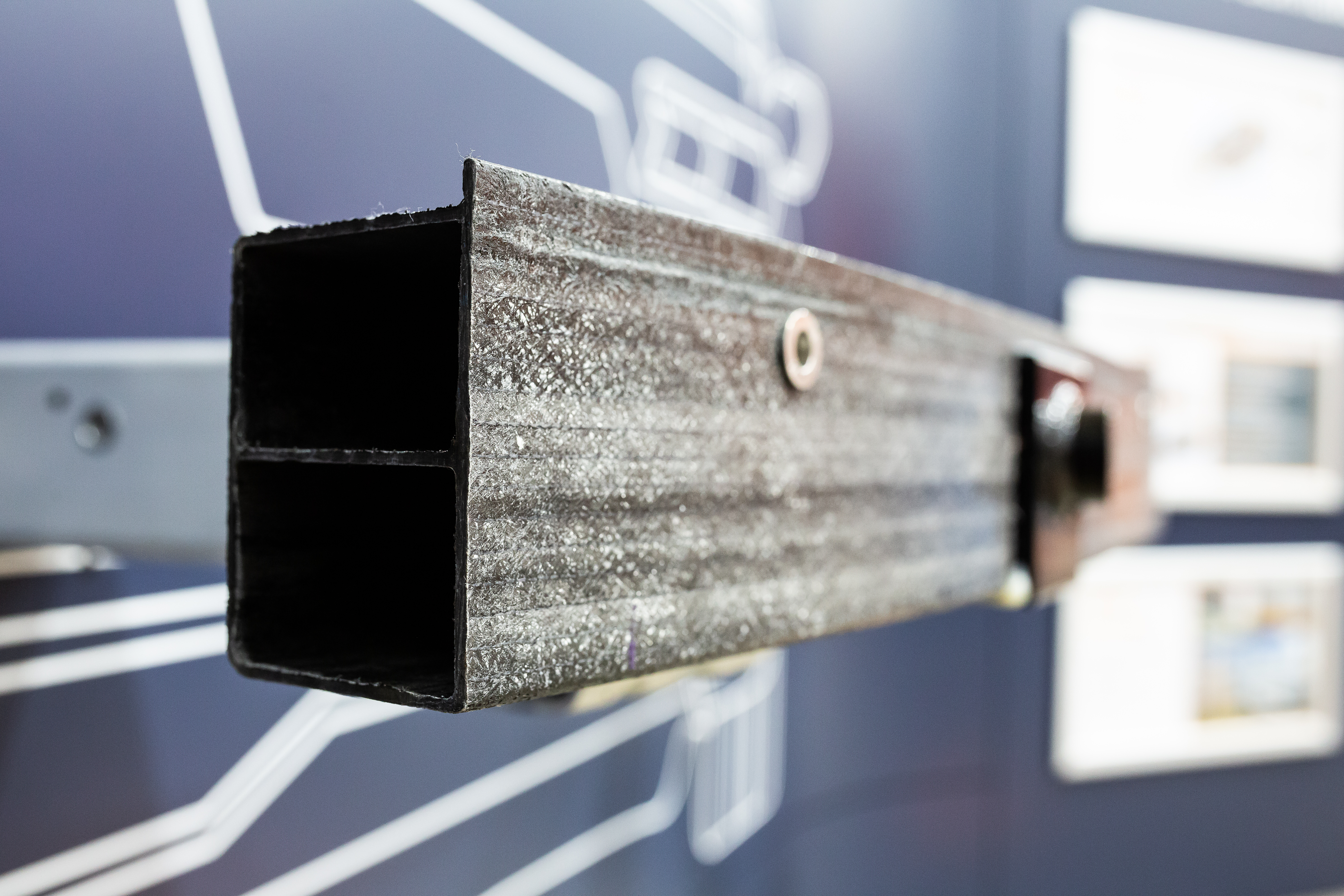
Estructura de la carrocería:parte A
Prácticamente todos los componentes de la estructura de la carrocería del C8 son compuestos y están adheridos y / o atornillados al marco después de que este último se somete a ELPO. Las partes compuestas notables en este nivel incluyen los cierres estructurales de la parte inferior de la carrocería y el piso, que cubriremos en este número, y los maleteros delanteros y traseros, los conductos de inducción y el borde trasero y el mamparo, que cubriremos, junto con los paneles de la carrocería y las molduras. , el mes que viene.
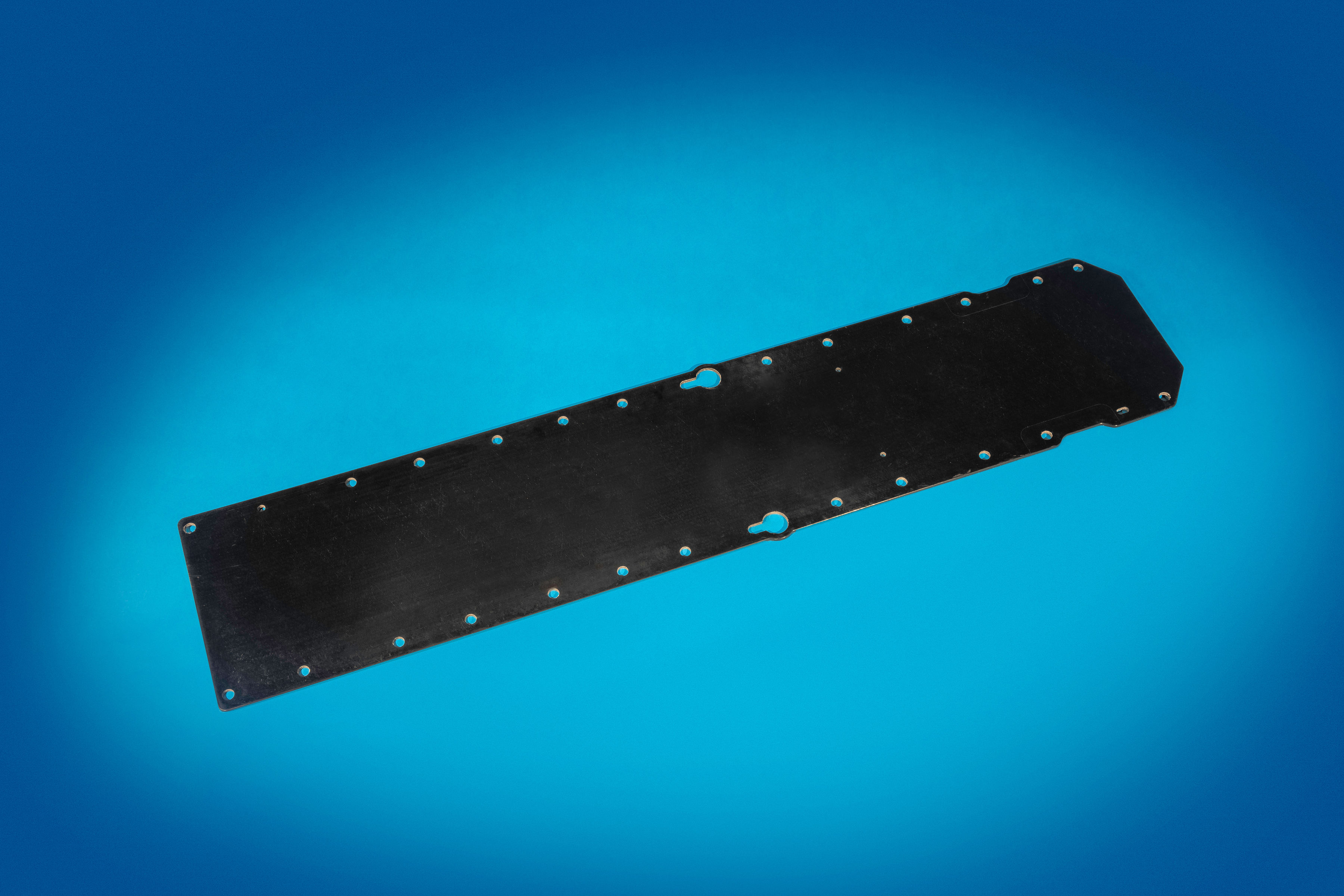
El cierre estructural desmontable del túnel inferior en el C8, que actúa como puerta de acceso, contribuye con más del 10% de la rigidez torsional del vehículo y actúa como una ruta de carga principal durante un choque. Este panel de compuesto híbrido consta de tres capas de preforma de fibra de vidrio. Estos consisten en fibras continuas / tejidas y cortadas / aleatorias al 38% de fracción de volumen de fibra (FVF), con velos agregados a las capas de la cara superior e inferior en cada pila para mejorar el acabado de la superficie. Las preformas de vidrio se intercalan con dos capas de preformas fabricadas con fibra de carbono de módulo estándar T700 12K de Toray (Tokio, Japón) en forma de tejido biaxial NCF al 21% FVF y una matriz de éster de vinilo (VE). El cierre es producido por Molded Fiber Glass Co. (MFG, Ashtabula, Ohio, EE. UU.) Utilizando su proceso patentado PRiME (Refuerzo preposicionado que garantiza la excelencia en la fabricación), un tipo de moldeo por compresión líquida (LCM).
Aparte de un solo cierre de aluminio cerca de las ruedas traseras que es parte del soporte del motor, los paneles restantes de la parte inferior de la carrocería consisten en SMC moldeado por compresión o termoplásticos moldeados por inyección. Entre otros beneficios, estos paneles reducen la turbulencia y el arrastre de los bajos, mejoran la eficiencia del combustible y mantienen la humedad, el polvo y las piedras fuera del motor y la línea de transmisión del vehículo. Además, proporcionan la base dimensional para múltiples interfaces exteriores e interiores.
La baja densidad pero estructural Los paneles SMC presentan nuevas formulaciones (en este caso, fibra de vidrio cortada al 40% FVF / resina de poliéster insaturado (UP)) desarrolladas por MFG. El material se llama SMC "flotante" porque la densidad de cada panel es menor que 1.0 (SG promedio =0.97) y por lo tanto puede flotar en el agua. MFG produjo todas las piezas estructurales de SMC y LCM'd en el automóvil.
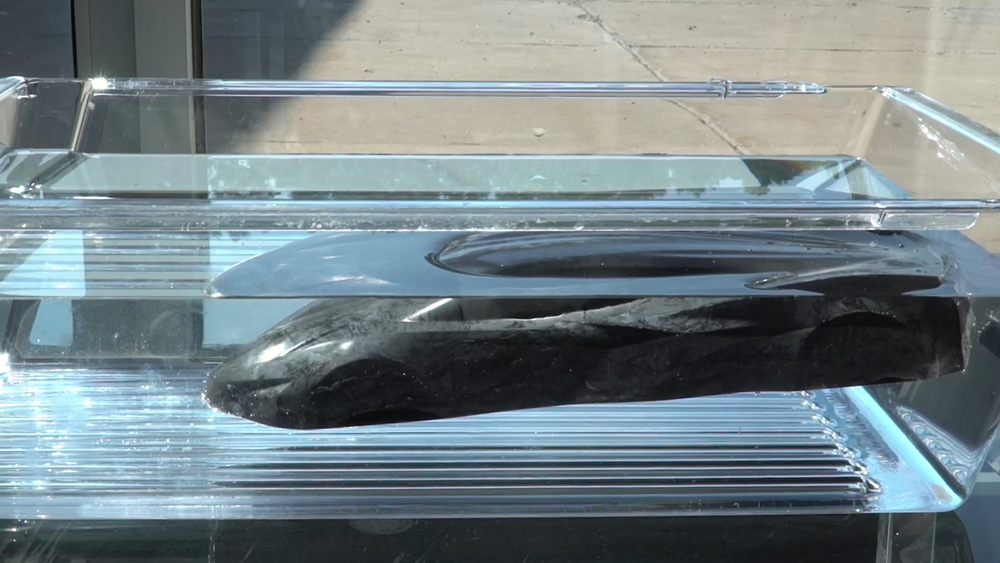
El vehículo también tiene un piso híbrido optimizado para flexión torsional y protección contra impactos de postes laterales (enganchando los paneles de balancines y el túnel, al que está unido). Los paneles del piso cuentan con aluminio estampado que da a la cabina adherido a láminas de compuesto 1.5-SG que da a la carretera (60% en peso de fibra de vidrio / VE continua y tejida) producida mediante el proceso PRiME. Antes de unir por calor ambas capas con el adhesivo estructural de poliuretano Pliogrip 9100 de Ashland Global Holdings Inc. (Wilmington, Del., EE. UU.), MFG limpia y prepara los materiales.
Todas las piezas de material compuesto unidas directamente al marco C8 se someten primero a ablación con láser, un proceso desarrollado por GM, MFG y Adapt Laser Systems LLC (Kansas City, Mo., EE. UU.) Para el Corvette 2016. y adaptado de un método de la industria de compuestos para la limpieza de moldes. La ablación láser reemplaza el lijado manual y reduce la mano de obra, el tiempo y el costo, elimina el polvo y mejora la repetibilidad. La trayectoria del láser, el ángulo de ataque y el nivel de energía se pueden personalizar para el material y la geometría de cada pieza. Para maximizar la flexibilidad de fabricación, toda la parte inferior de la carrocería, incluido el piso, está conectada al marco y a sí misma mediante uniones y tornillos.
En la edición de agosto de CW, continuaremos cubriendo la innovación de compuestos en el nuevo Corvette , reanudando con componentes adicionales al nivel de las estructuras de la carrocería y terminando con cierres exteriores (paneles de la carrocería), además de molduras y mejoras adicionales. Vea la Parte 2.
Resina
- 10 ventajas de la computación en la nube en 2020
- El futuro de la impresión 3D:12 conclusiones clave de la AM Landscape Digital Conference 2020 de AMFG (Parte 1)
- El futuro de la impresión 3D:12 conclusiones clave de la AM Landscape Digital Conference 2020 de AMFG (Parte 2)
- Liderazgo de mantenimiento, Parte 3
- Introducción a los armónicos:Parte 1
- Sostenibilidad en la fabricación - Parte 3
- Tendencias y desafíos de 2020 afectados por el Covid-19:Parte I
- El giro es opcional
- ¿Qué es un número de pieza?
- Mecanizado de piezas pequeñas
- Cilindricidad en GD&T