Preformado automatizado, Parte 7:Rellenar Gesellschaft
Esta es la última entrega de una serie de siete partes sobre preformas. Para obtener más información sobre esta serie, haga clic en los enlaces a continuación:
FUENTE:Relleno Gesellschaft
Historias de casos de automatización
Las primeras máquinas de Fill se desarrollaron para automatizar la producción de esquís para Fischer. Hoy se necesita el 25 por ciento de los trabajadores para producir el 80 por ciento del volumen de producción anual original. Tenga en cuenta también que los esquís tienen un diseño híbrido, que comprende capas de vidrio y / o compuesto de fibra de carbono, núcleos de madera, bordes de acero y varios tipos de plástico.
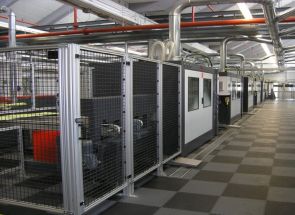
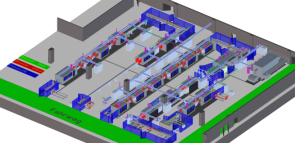
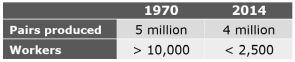
El relleno se proporcionó múltiples generaciones de equipos automatizados para la producción de esquís compuestos.
FUENTE:Presentación CAMX de la Gesellschaft 2017.
BMW
Cuando BMW desarrolló los modelos i3, i8 y los nuevos de la Serie 7, todos los cuales utilizan compuestos de plástico reforzado con fibra de carbono (CFRP), Fill suministró una gama de soluciones de automatización.
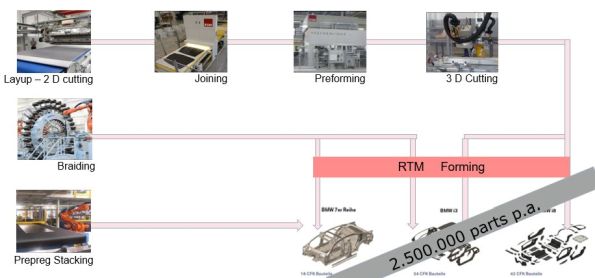
FUENTE:Relleno Presentación CAMX Gesellschaft 2017
Monocascos compuestos
Fill también desarrolló una línea de producción única para Mubea CarboTech capaz de producir monocascos de CFRP para dos modelos de automóviles diferentes:el Volkswagen VW XL1 y el Porsche 918 Spyder. Esta línea automatizada incluía herramientas de moldeo accionadas de varias piezas, prensa de moldeo por transferencia de resina de alta presión (HP-RTM), capacidades de poscurado y mecanizado.
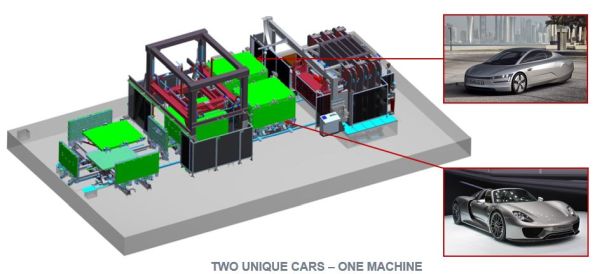
El relleno proporcionó un línea de producción monocasco de material compuesto para Mubea CarboTech.
FUENTE:Presentación CAMX de Fill Gesellschaft 2017
Automatización de diseño
Para el laminado automatizado, Fill ha desarrollado sistemas para una variedad de materiales diferentes, incluida la tela seca de hasta 3 m de ancho (para producción de mayor volumen en BMW). El sistema automático de colocación de casquillos de mástil SpeedLayer 800 para palas de aerogeneradores aplica un preimpregnado de fibra de carbono unidireccional de hasta 800 mm de ancho a una velocidad informada de 1,5 m / sy una precisión de ± 1,5 mm. Puede manipular rollos preimpregnados de 600 kg e integra funciones de validación de procesos y garantía de calidad.
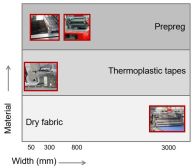
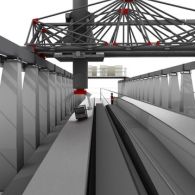
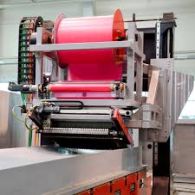
Se ha desarrollado el relleno una gama de sistemas de laminado automatizados (izquierda) que incluyen SpeedLayer 800 para tapas de largueros de palas de viento que utilizan preimpregnado de carbono UD de hasta 800 mm de ancho (derecha).
FUENTE:Presentación CAMX de Fill Gesellschaft 2017
El proyecto Low-Cost Flexible Integrated Composite Process (LOWFLIP) fue una iniciativa de 3 años (octubre de 2013-octubre de 2016) financiada por la UE que incluyó a Fill y otros nueve socios, con el objetivo de automatizar la colocación de preimpregnados para el transporte curado fuera de autoclave (OOA) estructuras. Estaba integrado por tres manifestantes:
- Pared frontal de 2,5 × 2,9 m para un remolque de camión
- Viga transversal automotriz de 1,2 m de largo
- Panel de cono de cola de avión de piel rígida de 1,0 × 1,2 m
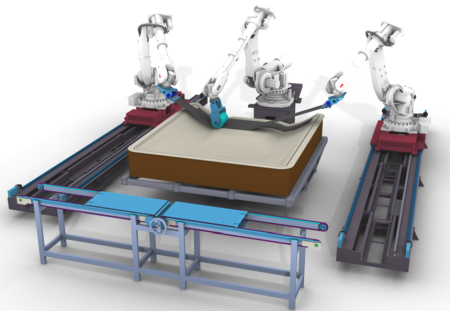
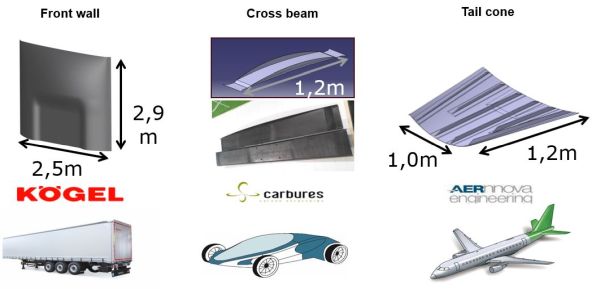
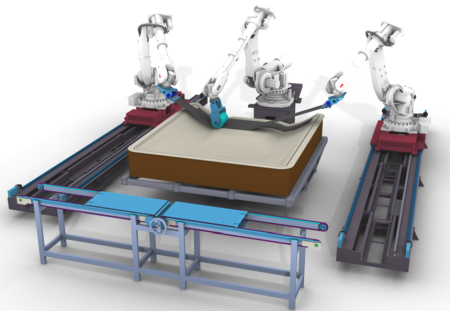
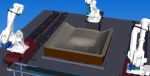
Animación
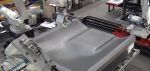
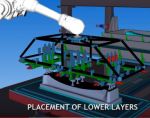
Fill trabajó con nueve socios en LOWFLIP para desarrollar una celda de laminado automatizada para la producción de grandes estructuras de transporte compuestas sin autoclave.
FUENTE:Presentación CAMX de Fill Gesellschaft 2017
"Usamos calentamiento por resistencia eléctrica para calentar el molde hasta 120 ° C", recuerda Wilhelm Rupertsberger, director del Centro de competencia de Fill para materiales compuestos y plásticos. “El material siempre estuvo bajo tensión durante el laminado automático”, agrega, “y logramos un drapeado sin arrugas directamente en el molde. Creamos un proceso humano, pero uno que usa robots para mejorar la repetibilidad ”.
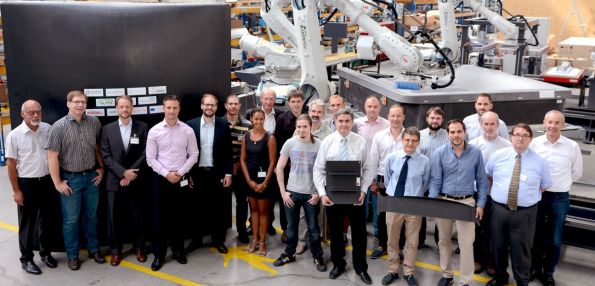
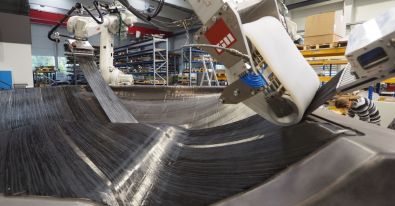
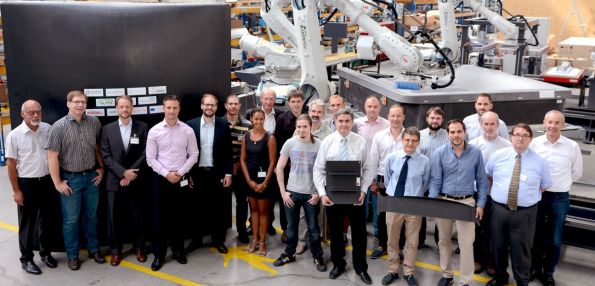
Puedes ver la pared del remolque del camión a la izquierda, así como los demostradores de la viga transversal del automóvil y el panel del cono de la cola del avión en la foto del equipo LOWFLIP de arriba .
FUENTE:Presentación CAMX de Fill Gesellschaft 2017
Sistema multicapa a multicapa
El sistema Multi-Layup de Fill se desarrolló para la producción de piezas de carrocería en blanco (BIW) de automóviles, como paredes traseras y refuerzos de parachoques inferiores, utilizando cintas termoplásticas. Se previó que estas piezas incluirían nervaduras sobremoldeadas y otras características, por lo que el ciclo de laminado de la preforma tendría que coincidir con el ciclo de moldeo por inyección subsiguiente.
Mi publicación de blog posterior a la presentación de JEC 2017 incluía un video del sistema Multi-Layup, que alimentaba cintas de varios rollos, colocando todas las cintas necesarias por capa simultáneamente, en lugar de en serie, una a la vez. De esta forma, logró un tiempo de ciclo de 10-15 segundos por capa.
El relleno ahora ha modificado aún más el sistema y lo ha renombrado como Multicapa. Alimenta, corta y coloca hasta 16 cintas en anchos de hasta 50 mm (cada una de 0,01-0,04 mm de grosor) sobre una mesa giratoria. La cama de colocación de cinta puede producir piezas de hasta 1,6 × 1,6 m. Las cintas se aplican a una velocidad de 500 m 2 / hr:cada 12-15 segundos se aplica una capa de pieza de tamaño completo durante aproximadamente un tiempo de ciclo de 1 minuto por cada preforma terminada. Las capas no están completamente consolidadas, sino que se unen mediante unión térmica. A medida que cada carrete se queda sin cinta, se cambia automáticamente sin detener la máquina.
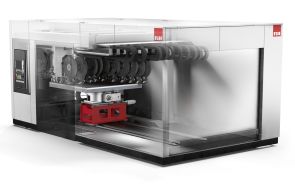
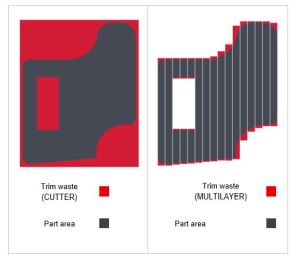
Relleno multicapa automatizado El sistema de preformado permite una reducción significativa del desperdicio de recortes al tiempo que coloca las cintas solo donde se necesitan y las orienta según sea necesario para lograr laminados a medida.
FUENTE:Presentación CAMX de Fill Gesellschaft 2017
A continuación, las preformas acabadas se consolidan en una prensa. “Hemos integrado multicapa con una prensa de consolidación automatizada y una celda de moldeo por inyección Engel que funcionan juntas para ofrecer un ciclo de tiempo de 1 minuto”, dice Rupertsberger. Fill recibió un pedido para el primer sistema multicapa de la Universidad Tecnológica de Swinburne (Melbourne, Australia) a principios de este año y demostrará el equipo en vivo por primera vez en JEC World 2019 (12-14 de marzo, París, Francia).
Prensas RTM e inyección adaptable
Fill ha suministrado varias prensas RTM, incluidas las prensas HP-RTM para SGL Composites.
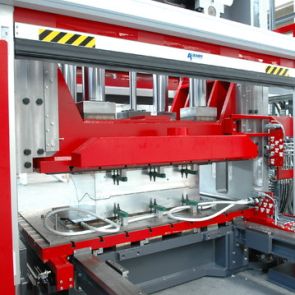
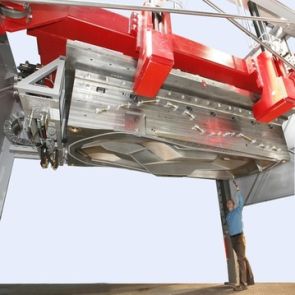
El relleno se proporcionó una amplia variedad de prensas para la producción de composites, incluidas las prensas HP-RTM para SGL Composites (derecha).
FUENTE:Rellenar Gesellschaft
Con Airbus Operations (Stade, Alemania) y el Instituto de Procesamiento de Plásticos (IKV) de la Universidad RWTH Aachen, Fill ha desarrollado una innovadora unidad de inyección adaptativa para RTM inicialmente para estructuras de aerocompuestos. Antes de que las piezas fabricadas con RTM puedan volar en un avión, deben pasar por un proceso de garantía de calidad (QA) costoso y que requiere mucho tiempo. Para acortar este proceso, las herramientas de conformado RTM se han equipado con sensores, lo que permite implementar el control de calidad en línea durante la producción. IKV, Airbus y Fill ahora han integrado estos sensores en el sistema de inyección, eliminando la necesidad de equipar cada herramienta de conformado. Utilizando cartuchos desechables de la misma manera que se utilizan los sistemas de inyección de pistón en los sistemas RTM típicos, la unidad de inyección adaptativa está equipada con una caja de sensor que permite medir y registrar los siguientes datos in situ:
- Temperatura
- Presión
- Viscosidad de la resina
- Densidad de reticulación del sistema de resina
- Temperatura de transición vítrea (Tg).
Al tiempo que se garantiza la calidad de las piezas moldeadas, estos datos también se pueden utilizar para gestionar y controlar el proceso de inyección. Este sistema de inyección adaptable de la Industria 4.0 se está desarrollando para aerocomposites y también se está extendiendo a otras industrias como la automotriz.
Formación de cortinas calientes
En los artículos recientes de la gira, Sara Black y yo escribimos sobre compuestos de alto rendimiento en Israel, notamos que la mayoría de las empresas utilizaban la formación de cortinas en caliente. De hecho, en Elbit Cyclone, nuestro guía turístico Jonathan Hulaty declaró:"No sé cómo se hace este tipo de producción de piezas preimpregnadas de alta velocidad sin formación de cortinas en caliente", refiriéndose a vigas y montantes para ensamblajes de Boeing 787. Las formadoras de cortinas en caliente (HDF) también son consideradas indispensables por FBM e Israel Aerospace Industries. Fill ha suministrado sistemas HDF durante años, incluidas varias unidades en producción en FACC. Básicamente son sistemas de formación al vacío, equipados con infrarrojos u otros tipos de elementos calefactores y una membrana de caucho de silicona reutilizable para calentar y comprimir, reducir el volumen, capas de preimpregnado en sus herramientas antes del curado. El HDF se convierte en una pieza clave en la línea completa de producción de aerocomposites que se muestra a continuación.
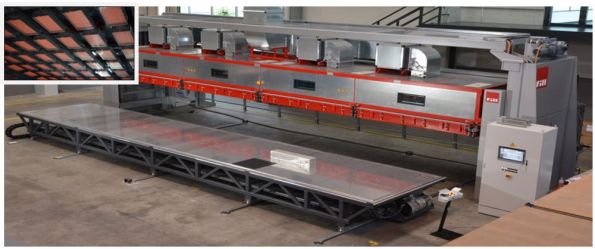
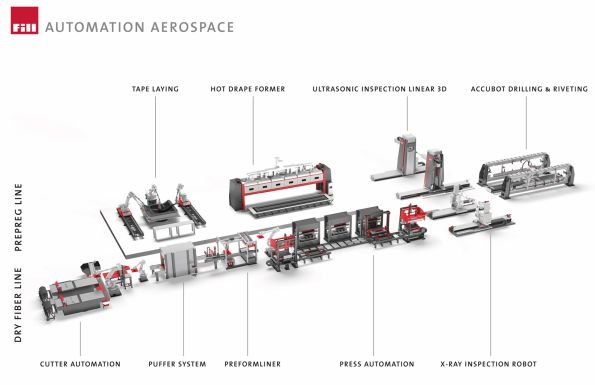
Formación de cortinas en caliente se ha convertido en un habilitador importante para la producción de alto volumen de aeroestructuras de compuestos preimpregnados y está automatizado por Fill como parte de sus soluciones de cadena de proceso completo. FUENTE: Llenar Gesellschaft
Células de producción de Industria 4.0 para CFRP
A finales de 2013, Fill comenzó a desarrollar un sistema de producción para la fabricación de largueros de CFRP, que se utiliza para reforzar las carcasas de las aletas de aterrizaje del Airbus A320, en colaboración con el proveedor de Tier. Tras la instalación, este sistema redujo con éxito el número de estaciones, lo que mejoró el flujo de producción y también mejoró la facilidad de uso. Comprende:
- Almacenamiento automático de herramientas de conformado
- Estación HDF
- Estación de elevación de presión-giro donde los laminados se procesan en largueros.
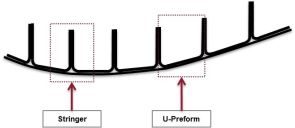
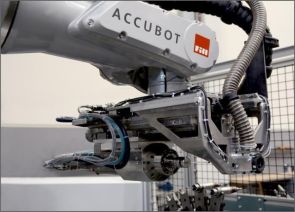
Se ha desarrollado el relleno tres generaciones de celdas de producción automatizadas (derecha) para largueros de flaps de tren de aterrizaje hechos de preimpregnado (izquierda).
FUENTE: Llenar Gesellschaft
En 2017 se puso en marcha un sistema de segunda generación para producir el mismo tipo de piezas. Donde el primer sistema se centró en optimizar estaciones individuales, este último sistema tenía como objetivo minimizar las tareas manuales e integrar toda la logística de la herramienta. Tres áreas clave de desarrollo permiten que este sistema de segunda generación logre una alta reproducibilidad y una productividad significativamente mayor:
- La recuperación y el almacenamiento manual de las herramientas de conformado se sustituyen por una devolución de herramientas totalmente automática, lo que acorta los tiempos del proceso logístico. Esto también ha reducido el requisito de espacio en más del 50 por ciento.
- Una mayor automatización de los subprocesos ha reducido el tiempo improductivo.
- Digitalización de Industria 4.0 de todos los registros y reportes. El software desarrollado por Fill permite la visualización del proceso en todo momento y el registro del historial de cada componente a lo largo de la cadena del proceso. Los sensores detectan la disponibilidad de herramientas y materiales para evitar cuellos de botella y mejorar los pedidos.
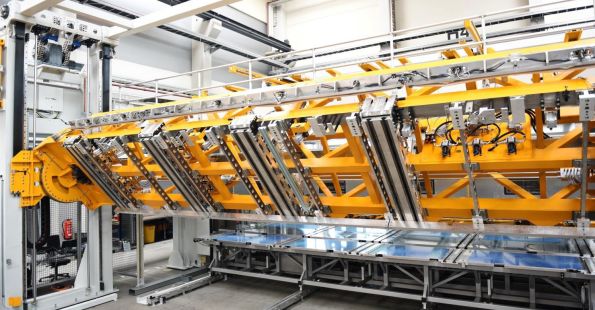
Presione y gire -Estación de elevación utilizada en celdas de producción automatizadas para largueros de flap de tren de aterrizaje A320 y A350.
FUENTE: Llenar Gesellschaft
Fill ahora está trabajando en un sistema de producción de tercera generación para los proyectiles de flaps de aterrizaje destinados al Airbus A350-900. También incluye almacenamiento de herramientas, estación de formación de membranas (HDF), estación de prensado-giro-elevación y retorno automático de herramientas, pero se ha mejorado con un sistema de transporte para herramientas en autoclave, reemplazando los camiones de transporte manual y los tractores eléctricos anteriores por vehículos guiados automatizados (AGV). ). Fill ya está trabajando en sistemas futuros, buscando cómo mejorar aún más la colaboración entre el hombre y la máquina.
Accubot
Incluso antes de que la industria de los materiales compuestos comenzara a verbalizar su futura necesidad prevista de una celda de trabajo de múltiples operaciones, Fill ya estaba desarrollando los primeros prototipos, lo que llama Accubot. La idea era desarrollar un robot preciso utilizando un rastreador láser para la compensación espacial, así como sistemas de medición externos directos. Este robot podría cambiar funciones con efectores finales, convirtiéndose no solo en una celda de prueba no destructiva (NDT) sino también en una celda de mecanizado. Las aplicaciones de Accubot incluyen:
- Perforación
- Remachado
- NDT:ultrasonido con un chorro de agua
- NDT - Rayos X
- NDT:tomografía computarizada
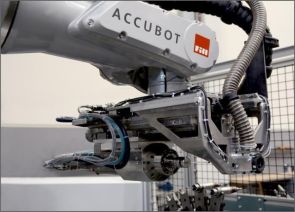
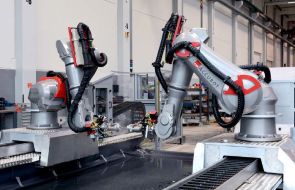
Accubot para taladrar (izquierda) y NDT usando escaneo ultrasónico de alta velocidad (derecha).
FUENTE:Fill Gesellschaft.
FlexHyJoin
Fill es miembro del proyecto financiado con fondos europeos Flexible Production Cell for Hybrid Joining (FlexHyJoin). Este programa de 3 años tiene como objetivo desarrollar un proceso piloto totalmente automatizado para unir soportes / accesorios metálicos con compuestos termoplásticos en aplicaciones automotrices mediante la combinación de tecnologías de unión por láser y unión por inducción. Fill diseñó y construyó la celda automatizada, incluido el software y la integración de las diversas tecnologías.
La investigación y el desarrollo de Fill continúan. Entiende que se requieren sistemas de producción innovadores e inteligentes para hacer que la fabricación de piezas compuestas sea más económica y susceptible de mayores volúmenes. Y se compromete a desarrollar estos sistemas de acuerdo con la escala y las necesidades específicas de sus clientes.
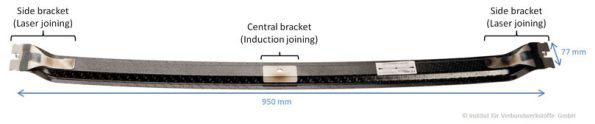
FUENTE:FlexHyJoin.
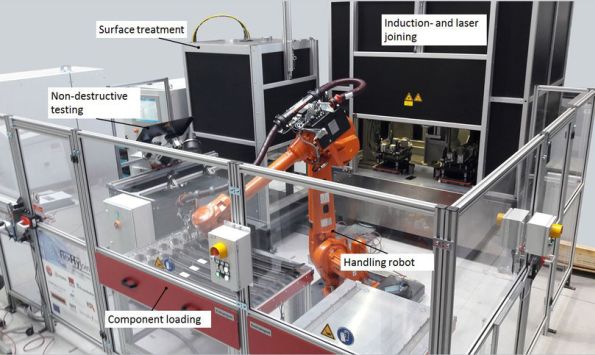
Resina
- Rellenar la presa
- Directivas de preprocesador de C#
- Python strftime()
- Python strptime()
- Sus piezas más fuertes con la impresión 3D de fibra de carbono - Relleno isotrópico Parte 1
- Impresión 3D de alta resistencia - Relleno isotrópico Parte 2
- Introducción a los armónicos:Parte 1
- Sostenibilidad en la fabricación - Parte 3
- El giro es opcional
- Inspección automatizada de datos de tomografía computarizada en línea de conectores electrónicos
- Cilindricidad en GD&T