Inspección de soldadura para ensamblajes críticos para la seguridad
Hay mucho en juego para los fabricantes que producen piezas de automóviles. Los conductores y pasajeros de automóviles confían en la calidad de la soldadura para resistir las condiciones para las que fue diseñada. Un error no detectado durante el proceso de fabricación podría dejar a una empresa vulnerable o algo peor, especialmente cuando la pieza en cuestión es "crítica para la seguridad" de un ensamblaje.
Los asientos de los automóviles, por ejemplo, están en contacto directo con los pasajeros; por lo tanto, las soldaduras del asiento se consideran críticas para la seguridad. Esta clasificación dicta un protocolo particular previo a la producción. Aunque los requisitos de los OEM varían, tienden a ser consistentes con la práctica de la industria y se implementan con pequeñas diferencias según la pieza, la planta y el equipo industrial que se utilice. Estos son los elementos básicos de un protocolo:
Protocolo de preproducción
- Parámetros de configuración - Establecimiento de parámetros de soldadura y verificación de su aceptabilidad. Esto se puede hacer cortando y grabando secciones de soldadura para verificar la penetración de la soldadura (15-20%).
- Proceso de lanzamiento - Un proceso establecido para liberar o aprobar la producción una vez que se haya verificado lo anterior.
- Gestión de cambios - Los cambios de variables esenciales más allá de ciertos límites requieren una revalidación mediante pruebas de corte y grabado.
- Garantía de calidad - Se pueden seleccionar piezas al azar de la producción para cortar y grabar a una frecuencia dictada por el OEM.
La soldadura robótica ha ayudado a mejorar enormemente la calidad de las piezas al colocar siempre las soldaduras en el mismo lugar con parámetros de soldadura programados. El cumplimiento de los procedimientos anteriores ayuda a producir un producto soldado de calidad. Los OEM automotrices se han estado enfocando en soldaduras críticas para la seguridad, y esto ha resultado en la revisión de algunos elementos clave:
Protocolo de Producción
- Seguridad - Verificar que personal calificado tenga acceso a los equipos y que no se realicen cambios que afecten negativamente la calidad.
- Monitoreo de arco - La implementación de un sistema de monitoreo de arco puede ayudar a verificar que el proceso esté bajo control y puede permitir que se reduzca la frecuencia de las pruebas destructivas. El monitoreo del arco verifica que los parámetros de soldadura cumplan con los límites establecidos. Las soldaduras fuera de los límites se marcan para una inspección adicional.
- Trazabilidad - Realice un seguimiento de los cambios y los resultados de la soldadura, y mantenga la capacidad de registrar la fecha, la hora y el número de serie donde se han producido los cambios de piezas.
En Yaskawa Motoman, nos tomamos el tiempo para conocer los requisitos de fabricación y trazabilidad de nuestros clientes. A lo largo de los años, hemos desarrollado varias mejoras de E/S y software para nuestros controladores que permiten a los fabricantes realizar inspecciones de soldadura fiables y trazables.
Funciones de seguridad
Función de contraseña
El sistema de seguridad estándar de una contraseña global de varios niveles es conveniente para que varios técnicos mantengan varias celdas de robot dentro de una planta. Sin embargo, las contraseñas globales corren el riesgo de ser compartidas entre el personal de la planta, sin control de qué se cambia y quién lo cambia.
La función de contraseña del controlador DX de Yaskawa crea una base de datos de usuarios con contraseñas y autorizaciones de nivel de seguridad. Los usuarios deben iniciar sesión para operar el robot; la función de registro registrará el nombre de usuario y los cambios realizados.
Se ha agregado software al controlador DX200 para permitir el control de contraseña remota por PLC. Los ingenieros de control pueden implementar la lógica para usar controles basados en plantas/células para administrar usuarios e inicios de sesión de forma remota en función de sus credenciales internas de empleados o sistema de seguridad.
Niveles de seguridad
- Nivel de operación - De forma predeterminada, este nivel básico permite que cualquier persona se mueva o recorra un programa, pero no cambiar ningún punto o configuración de soldadura.
- Editar nivel - Permite al usuario realizar programas y cambiar configuraciones de soldadura, pero no permite el acceso a parámetros o datos de nivel superior.
- Modo de gestión - Proporciona acceso completo a los parámetros y funciones de mantenimiento.
- Nivel de seguridad - Permite el acceso para configurar y administrar los límites de software confiables de control y la lógica de seguridad implementada en los controladores DX (Unidad de Seguridad Funcional - FSU).
Lo que estos niveles permiten a los usuarios hacer y acceder está definido por el sistema. El nivel al que la administración controla el acceso variará según la ubicación de la planta.
Función de registro
Muchos controladores de robot más nuevos vienen con una función de registro estándar que realiza un seguimiento de los cambios que se realizan en el sistema por fecha y hora. Por ejemplo, un operador del turno de día puede ver si alguien del turno de noche hizo un cambio. El robot mantiene un archivo local de la última serie de cambios, por lo que un guardado de datos de rutina puede mantener un registro histórico de la actividad del usuario. El robot también puede usar Seguridad de contraseña, lo que requiere que los usuarios inicien sesión para realizar cambios. Los nombres de usuario también se anotan cuando se realizan cambios.
Función de edición de reenseñanza de seguridad
El nivel de operación no permite que los usuarios cambien los puntos del programa, pero algunas empresas permitirán que los operadores o técnicos de primer nivel realicen cambios menores para la variación de piezas. Safety Re-Teach permite a los usuarios del nivel de operación modificar los puntos programados dentro de un rango 3D definido por el modo de gestión. Esto normalmente se establece en unos pocos milímetros, y un gerente puede limitar la cantidad de cambio de ángulo para la antorcha o el eje externo. Los usuarios del nivel de operación no pueden cambiar los parámetros de soldadura, por lo que las variables de soldadura esenciales no se modifican. Esto evita pruebas destructivas repetitivas. Safety Re-Teach se puede habilitar mediante un parámetro en el modo de gestión en cualquier controlador DX.
Monitoreo de arco
Como proveedor de robots que integra sistemas de soldadura y se basa en un historial de empresas conjuntas con una empresa de soldadura, Yaskawa Motoman tiene una amplia experiencia en el control del arco. Hemos diseñado nuestras interfaces de soldadura para respaldar la capacidad de monitoreo de arco que los fabricantes de fuentes de energía pueden haber integrado.
Se puede acceder a las funciones integradas de Miller Insight Centerpoint™ y Lincoln Electric Production Monitoring™ desde el dispositivo de aprendizaje del robot. WeldCube, de Fronius, se comunica directamente con la(s) fuente(s) de energía. Yaskawa y Fronius están trabajando para que el resultado del monitor se informe en los bits de estado de la soldadora.
El desafío de cumplir con los mandatos "críticos para la seguridad" también implica presentar claramente los resultados de soldadura del monitoreo del arco de la fuente de energía en un formato útil. El mejor formato es resaltar los resultados del monitor en un diagrama de pieza en una HMI de celda de robot. De esa manera, los operadores de la estación de soldadura pueden detectar fácilmente las irregularidades y reaccionar rápidamente. Los operadores deben inspeccionar visualmente las soldaduras marcadas por el sistema, con resultados de monitor fuera de rango, para juzgar si las soldaduras son conformes o no conformes.
Si bien el controlador del robot puede informar el estado del monitor de arco localmente en una HMI, los fabricantes de fuentes de energía también ofrecen software diseñado para informar los resultados del monitor de arco de forma remota, a través de una computadora personal o un software basado en la nube.
Punto central de Miller Insight
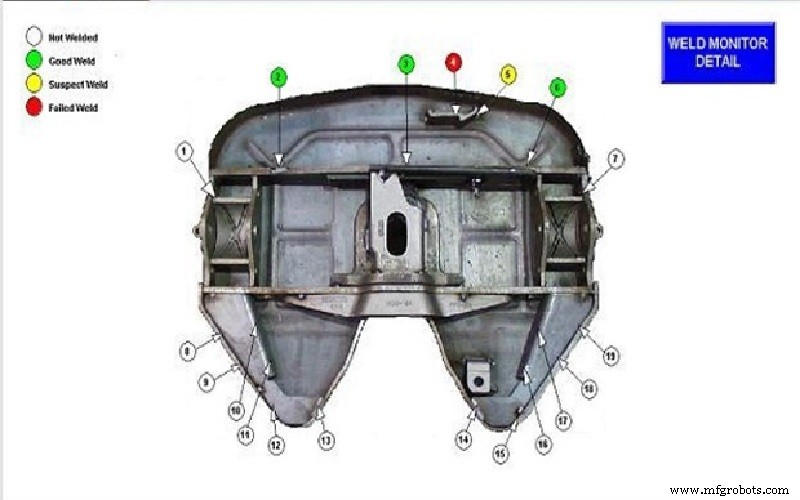
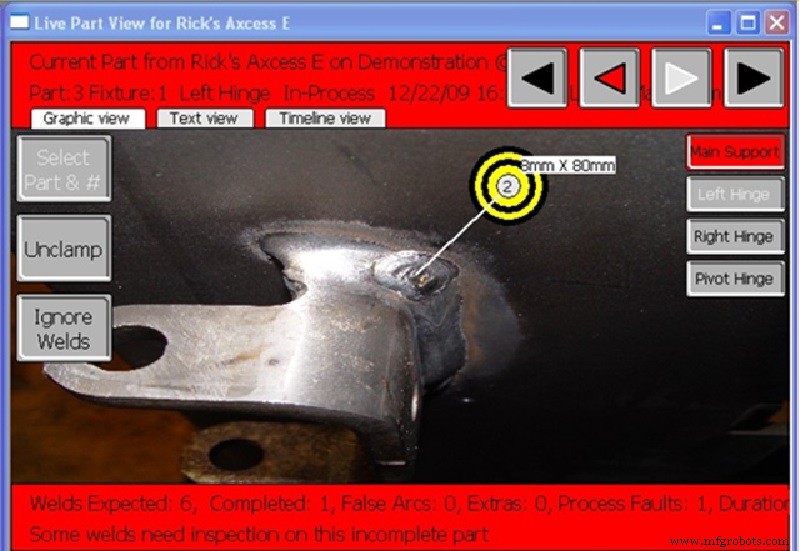
Trazabilidad
Los OEM automotrices no solo les piden a sus proveedores que fabriquen buenas piezas, sino que les piden que implementen sistemas de calidad para proporcionar "trazabilidad" que asociará los resultados de soldadura de una pieza con su número de serie. El objetivo es poder rastrear hasta un punto en la producción cuando se sabía que las piezas eran conformes si se detecta una pieza no conforme.
Para ayudar a los fabricantes a cumplir con la trazabilidad, los datos de monitoreo del arco de la fuente de poder de soldadura y el controlador del robot, además de cualquier dato específico de la pieza al que se deba acceder de forma remota y finalmente registrar en el PLC, se deben capturar y asociar con el número de serie de la pieza. Cómo armonizar esta combinación de datos, y la dificultad para hacerlo, depende de lo que un fabricante pueda integrar de forma inmediata, sin comprometer los protocolos de seguridad internos.
Variables de cadena
Un truco consiste en utilizar una función de creación de variables de cadena desde el controlador del robot para crear identificadores únicos como mecanismo de seguimiento. Hay una combinación de variables que se utilizan para almacenar números o incluso posiciones, y estas variables difieren según el formato y la cantidad de dígitos. Las variables de cadena pueden ser una combinación de caracteres o números de hasta 32 caracteres. Se pueden llamar para mostrar un mensaje en el colgante o para otros usos.
En el caso de la producción de automóviles, los hemos utilizado para contener la información del número de serie de la pieza en particular que se está produciendo. Los ingenieros de control pueden usar la comunicación ethernet para "leer" los valores de un PLC o lector de código de barras y podemos pasarlos a otros dispositivos.
E/S simultáneas
Yaskawa Motoman utiliza E/S simultáneas (CIO) para realizar un control lógico programable y comunicar datos entre el robot y la fuente de alimentación. Si bien se usa para la configuración de soldadura, también se puede usar para pasar los resultados del monitoreo del arco entre la fuente de alimentación y el robot. Para trazabilidad, lo hemos utilizado para concatenar los resultados de soldadura para cada ubicación de soldadura y enviarlo, con el número de serie de la pieza, al PLC de la planta para un registro de la pieza. También tomamos el número de serie de la pieza y lo enviamos a un estampador que graba el número de serie en las piezas que pasan por el monitor de soldadura.
Recientemente, entregamos un sistema que tomará datos de inspección de soldadura del Lincoln Electric Production Monitor y se los presentará al operador en una representación gráfica de la pieza. Resaltará, en verde o rojo, los resultados del monitor en cada ubicación de soldadura, en función de estar dentro o fuera de los límites. El monitoreo de CheckPoint™ (un software externo) está diseñado para almacenar datos en la nube. El CIO permitió el acceso inmediato a los resultados del Monitor de producción para que se pudiera presentar al operador mientras se producía la pieza.
Implementación
El manejo de los datos de monitoreo de soldadura debe considerar el control de producción, junto con los requisitos de trazabilidad y registro histórico. Los datos que se capturan en el camino se usan de manera diferente en toda la organización, y esas necesidades deben considerarse para cada función en cada paso.
Si bien el uso de datos de monitoreo de soldadura debería facilitar que los operadores en el piso verifiquen la calidad de la pieza, el personal de supervisión puede usar los datos históricos para administrar planes de calidad y solucionar problemas. Las características de seguridad hacen que sea casi imposible desviarse de los protocolos y parámetros establecidos, y el monitoreo del arco brinda indicaciones gráficas en tiempo real de las soldaduras que necesitan una inspección adicional.
Con el PLC como destino final, los datos de soldadura específicos de la pieza se registran, almacenan y rastrean. Puede llevar una cantidad considerable de trabajo inicial llegar a la armonización completa de los datos; sin embargo, los resultados son clientes confiados y calidad mejorada que también pueden ayudar a asegurar el futuro de su operación.
Robot industrial
- Temperaturas críticas para superconductores
- Por qué la excelencia en confiabilidad es imperativa para la seguridad
- Las 10 reglas de codificación de la NASA para redactar un programa crítico de seguridad
- Consejos de seguridad en el lugar de trabajo para maquinistas CNC
- Desarrollo de una nueva era para una seguridad alimentaria más inteligente
- Un caso para actualizar camiones viejos
- Estrategias para la preparación adecuada de soldaduras
- 5 consejos de seguridad para preparar equipos pesados
- Las inspecciones garantizan la seguridad en los equipos de alquiler
- Consejos de seguridad para la soldadura de tanques de combustible
- Comprender la inspección de soldadura