Rendimiento total efectivo del equipo:qué es TEEP y cómo puede usarlo para mejorar la programación
Hay una razón por la que la gente compra cajas de herramientas. Si bien cada herramienta cumple su propósito, tener solo una a su disposición limita enormemente lo que puede lograr. Tener todas sus herramientas, por otro lado, le permite hacer más y resolver una gama más amplia de problemas.
De manera similar, ningún equipo de mantenimiento o gerente de planta debe buscar solo un KPI de mantenimiento para rastrear y mejorar la producción. Existen múltiples métricas de mantenimiento, y categorías de métricas, porque cada una proporciona información diferente que lo lleva a tomar una serie de acciones diferentes.
Hoy, veremos el rendimiento total efectivo del equipo, o TEEP, y cómo su equipo de mantenimiento puede usarlo junto con OEE y OOE para mejorar la programación y la producción en su empresa.
¿Qué es TEEP?
El rendimiento total efectivo del equipo (llamémoslo TEEP de ahora en adelante) existe en la misma familia de métricas de mantenimiento que la efectividad general del equipo (OEE) y la efectividad general de las operaciones (OOE). Las tres métricas tienen en cuenta el rendimiento, la calidad y la disponibilidad de la máquina para medir el rendimiento general del equipo. Donde difieren estas métricas radica en cómo definen la disponibilidad.
Por sí solo, TEEP mide su potencial total para la capacidad del equipo. Define la disponibilidad en función de todos tiempo disponible:365 días al año, 7 días a la semana, 24 horas al día. Cuando mide el TEEP, se pregunta:"¿Cuánto podríamos estar produciendo si no hubiera límites para la programación?"

El TEEP se calcula multiplicando el rendimiento, la calidad y la disponibilidad, donde la disponibilidad se define como el tiempo de producción actual dividido por todo el tiempo disponible.
Por ejemplo, si hiciera funcionar una máquina las 24 horas del día, los 7 días de la semana durante una semana y produjera productos perfectos sin detenerse una vez, TEEP sería del 100%. Si esa misma máquina funcionara 16 horas al día sin detenerse, la disponibilidad sería del 67% (16 horas divididas entre 24 horas). Digamos que también operó al 90% del rendimiento potencial (rendimiento) y produjo productos perfectos el 88% del tiempo (calidad). El TEEP del activo sería del 53% (0,9 x 0,88 x 0,67).
Por supuesto, ninguna planta funciona las 24 horas del día, los 365 días del año. Es por eso que TEEP es útil en comparación con las otras métricas de su familia.
Comparación de TEEP con OEE
Como métrica, TEEP está más estrechamente relacionada con OEE, así que primero distingamos entre estas dos métricas.
Mientras que TEEP mide el potencial de un activo capacidad, OEE mide el nivel actual de productividad de un activo. Se calcula, al igual que TEEP, multiplicando la disponibilidad, el rendimiento y la calidad de un activo, donde la disponibilidad se calcula como el tiempo de ejecución total del activo dividido por el tiempo de producción planificado de ese activo.
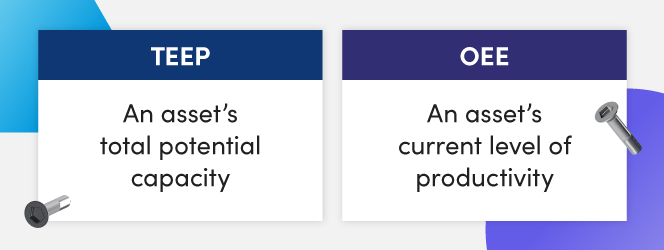
OEE se diferencia de TEEP en que se basa en la realidad del programa de producción actual. Supone que la cantidad máxima de tiempo que puede funcionar un equipo no puede ser mayor de lo que ya es.
Debido a que OEE es una métrica del estado actual, les brinda a los equipos de producción y operadores una lectura bastante precisa sobre el desempeño de sus equipos y si cualquier cambio en la disponibilidad, el rendimiento o la calidad podría aumentar la capacidad. Debido a que la OEE está estrechamente relacionada con la producción, es una métrica que muchas instalaciones monitorean en tiempo real para determinar si se pueden realizar mejoras.
Comparación de TEEP con OOE
De manera similar a TEEP y OEE, OOE (efectividad general de las operaciones) se calcula una vez más multiplicando el rendimiento, la calidad y la disponibilidad, donde la disponibilidad se define como el tiempo de producción real dividido por el tiempo de operación.
El tiempo de funcionamiento incluye el tiempo de producción planificado de un activo (como OEE), más cualquier tiempo no planificado durante el cual un activo podría desconectarse.
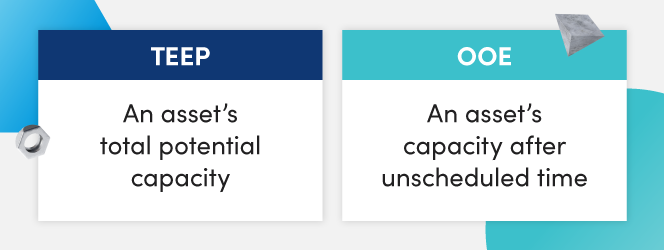
Cómo utilizar TEEP
Ahora que tenemos estas métricas, y las diferencias entre ellas, claras, hablemos de cómo se pueden usar juntas. Podemos pensar en estas tres métricas como una especie de sistema en cascada, donde TEEP mide el rendimiento total efectivo (o potencial) del equipo, OOE mide el rendimiento actual de su equipo teniendo en cuenta el tiempo no programado y OEE mide todo como está ahora.
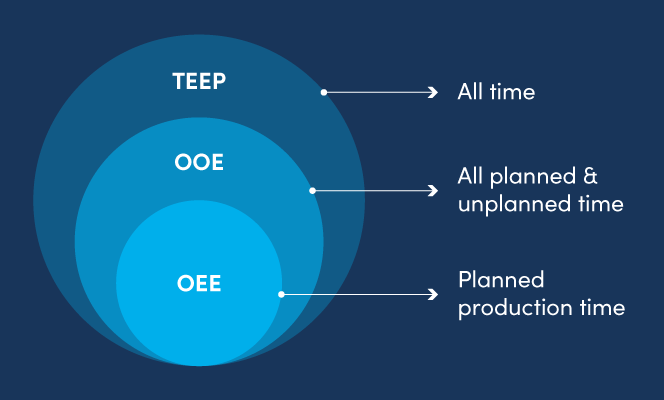
Hablamos con Stuart Fergusson, Director de Ingeniería de Soluciones en Fiix, para analizar estos tres escenarios. "TEEP es un par de pasos eliminado de una verdadera métrica de mantenimiento", dice. "Es útil a nivel empresarial para alguien como un gerente de planta porque ayuda a informar las decisiones de programación".
En otras palabras, calcular TEEP le ayuda a responder preguntas como, “¿Deberíamos introducir nuevos turnos? ¿Vale la pena pasar las vacaciones? ¿Qué pasaría si pasáramos los fines de semana? ”
Stuart agrega que algunas personas se apresuran a pasar a métricas como TEEP porque en realidad no están calculando la OEE correctamente. Esto sucede cuando el mantenimiento se realiza durante el tiempo de inactividad no se cuenta para OEE. Como ejemplo, piense en una fábrica que cierra los fines de semana y realiza todo el mantenimiento durante ese tiempo. El tiempo de mantenimiento no se cuenta aquí en contra de la producción, lo que podría darle una idea exagerada de lo que realmente es su OEE. Si el mantenimiento se cuenta como planificado tiempo de inactividad, tiene una idea muy diferente de lo que es su OEE y de lo que realmente es capaz de lograr.
Tome este ejemplo:supongamos que calcula su OEE como 90% en función de los 5 días a la semana que su maquinaria funciona. Con una OEE tan alta, parece que sería sencillo aumentar la capacidad sin comprar ningún equipo nuevo. Pero, ¿qué sucede si utiliza el tiempo de inactividad los fines de semana para realizar todo el mantenimiento de rutina? Ese tiempo no está disponible para más producción, porque siempre está bloqueado por mantenimiento, pero está desechando su OEE porque no está incluido en la ecuación.
Stuart sugiere calcular OEE, OOE y TEEP como lo haría normalmente, y luego examinar los deltas entre cada métrica. Al investigar las diferencias entre cada métrica, puede comenzar a ver dónde se pueden realizar cambios en la programación para mejorar la producción.
“Podrías hacer funcionar tu equipo muy, muy bien tres días a la semana y aún así obtendrías un puntaje TEEP bajo”, dice. "Pero en comparación con la OEE, puede mirar ese delta y decir:'Tendríamos que agregar X miembros del personal para mejorar nuestra OEE'".
Cómo TEEP puede ayudarlo a planificar
TEEP se puede mejorar cuando el rendimiento, la disponibilidad o la calidad mejoran, y probablemente sea más útil cuando no tiene ideas sobre cómo podría mejorar su OEE dado su programa de producción actual.
TEEP se puede utilizar como punto de referencia para comparar cómo está planificando actualmente los programas de producción de su planta. A diferencia de OEE y OOE, le da una idea de cuánto está sin usar su equipo. Nuevamente, Stuart advierte que su utilidad tiene sus límites. “Solo debe rastrear y poner una métrica frente a las personas que tienen la capacidad de cambiarla”, dice. “No hay nada que un operador pueda hacer para afectar el tiempo total disponible. Además de eso, no pueden programarse para otro turno ".
Pero cuando los operadores, los equipos de mantenimiento y los gerentes de planta trabajan juntos (sí, ha escuchado esto antes con respecto al mantenimiento productivo total), está claro cómo pueden usar sus propias métricas (como MTTR para el mantenimiento) para mejorar la capacidad de producción general del equipo. . Cuando estas áreas funcionales pueden trabajar juntas para mejorar la capacidad teniendo en cuenta las realidades y limitaciones de toda la operación, comienza a surgir una imagen holística de lo que una planta es realmente capaz de lograr.
Mantenimiento y reparación de equipos
- ¿Qué es SCADA y cómo puede mejorar la eficiencia de producción?
- Cómo la señalización y el etiquetado pueden mejorar la confiabilidad
- ¿Qué puede hacer para mejorar el mantenimiento y la confiabilidad?
- 5 causas de fallas en el equipo (y lo que puede hacer para evitarlas)
- Cómo los gerentes de mantenimiento pueden mejorar su programa de salud y seguridad
- ¿Qué es la soldadura con electrodo revestido? - Equipo y cómo hacerlo
- ¿Qué es MQTT y cómo pueden usarlo las empresas de automatización industrial?
- ¿Qué es la galvanización y cómo puede mejorar las piezas metálicas?
- Embragues industriales:¿Qué son y cómo se usan?
- Microcontrolador PIC18:qué es y cómo usarlo
- ¿Qué es un designador de referencia y cómo lo usamos en ensamblaje?