Cómo fundir metal en una fundición.
La fusión del metal es el proceso que transforma el metal de un tipo sólido a un tipo líquido. El proceso de fusión varía en tecnologías. Aquí proporcionamos una explicación de cómo fundir metal en una fundición, además de los puntos de fusión de metales comunes y el protocolo de seguridad de protección.
La fundición de fundición se ocupa principalmente del trabajo en metal fundido para dar forma a una variedad de aplicaciones de fundición. No es exagerado apreciar que la fusión del metal es el corazón de la fundición.
Fundir metal es un proceso de fundición indispensable que licua el metal sólido para verterlo en el molde y formar la fundición en cualquier forma. Brevemente, en su proceso de trabajo, el metal se coloca en un dispositivo de fusión llamado horno y se sobrecalienta hasta cierto punto de fusión para transformar el material metálico sólido en líquido.
Existen diferentes tecnologías aplicadas en la fusión de metales, en su mayoría depende del tipo de horno de fusión que se utilice. En esta publicación, lo ayudamos a responder la inquietud “Cómo fundir metal” especificando las principales tecnologías de hornos de fusión en las fundiciones actuales, además del punto de fusión de los metales comunes, así como orientación sobre la protección de la seguridad en el proceso de fusión.
¡Quédese con nosotros y descubra el conocimiento!
¿Qué es el metal fundido?
La fusión, también llamada fusión, es un proceso de transición que cambia el estado del material metálico de sólido a líquido al proporcionar suficiente calor.
El proceso de fusión del metal afloja el apretado empaquetamiento de las moléculas de metal. Como resultado, la fusión da como resultado un líquido metálico a partir del material sólido.
La fusión del metal puro y sólido se produce a una cierta temperatura fija llamada punto de fusión, mientras que los materiales metálicos impuros se funden a una temperatura diferente que varía según el tipo y el porcentaje de impureza.
Como el corazón de la fundición, el proceso de fusión del metal proporciona fluido fundido que se puede usar para verter en el molde y se solidifica en una variedad de formas según sea necesario. La fusión de metales es un trabajo que consume mucha energía y representa el 55 % del consumo de energía de la industria metalúrgica.
Es un paso muy importante porque la fusión de metal no solo proporciona el material para el proceso de fundición, sino que también afecta en gran medida la física y la química de los productos de fundición finales.
El proceso de fusión del metal
Aquellas personas que se preguntan cómo fundir metal en la fundición pueden encontrar que el proceso de fundición de metal generalmente involucra estos pasos tan breves:
- Decidir la proporción de mezcla de metales
- Preparación y carga del metal
- Derritiendo el metal
- Refinado y tratamiento del metal fundido
- Transportar el metal fundido
Decidir la proporción de mezcla de metales
Cada aplicación de fundición requiere diferentes propiedades mecánicas del metal que se pueden cambiar ajustando la relación de mezcla de metales. El fabricante de fundición tiene una fórmula para la mezcla de metales de acuerdo con la clase de material y los requisitos específicos.
Por ejemplo, la proporción de mezcla de materiales para la fundición de piezas de aluminio en nuestra fundición de metales suele ser 40 % lingotes de aluminio + 50 % chatarra de aluminio + 10 % otros. En el que el 10% de los demás son algunos materiales aditivos como aleaciones de Zn, Mn, Cu, Si, etc.
Preparación del metal
Los lingotes y la chatarra son la composición principal del material utilizado en el proceso de fusión y ocupan hasta el 80 % de la proporción de mezcla.
Antes de cargarlos en el horno, los lingotes y los desechos de metal (latas, piezas de maquinaria de desecho, contenedores o revestimientos) deben eliminarse la suciedad, además de precalentarse y secarse. Este paso es para eliminar la humedad, evitar la posibilidad de exploración en el horno, limitar la formación de escoria y mejorar la capacidad de fusión.
Particularmente con la chatarra, requiere eliminar la pintura, el aceite de mecanizado y otros contaminantes, comúnmente mediante el proceso térmico.
Cargar y fundir el metal
El horno se carga agregando una fuente de combustible (carbón vegetal, gas natural, electricidad). El metal se carga continuamente en el horno en el proceso de calentamiento en lugar del lote para ahorrar el consumo de energía y la efectividad del trabajo.
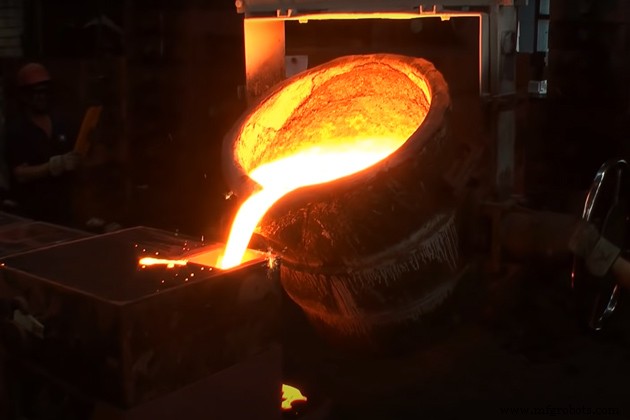
El horno funciona en un entorno extremadamente duro donde el metal fundido, los revestimientos del horno, los gases atmosféricos y los productos de la combustión de los combustibles se encuentran a temperaturas muy altas que requieren un equipo de protección estricto para el trabajador. El horno viene en un tamaño, forma, principio de funcionamiento y energía diferentes, por lo que la capacidad de fusión de cada horno difiere de los demás.
En un punto de fusión fijo, el metal se transforma de sólido a líquido. El punto de fusión varía de un metal a otro, entre 350oC y 2000oC.
Refinado y tratamiento del metal fundido
Este proceso es para desgasificar la masa fundida, eliminar los sólidos indeseables y ajustar la composición de la aleación como se esperaba. Materiales aditivos especialmente algunos ferrosos para aumentar las propiedades mecánicas del metal líquido (resistencia, ductilidad, rigidez, elasticidad).
Este paso es muy importante porque puede afectar la calidad final del colado.
Transportar el metal fundido
Después de la fusión, el líquido fundido se transfiere del horno a la línea de moldeo mediante un sistema de vertido.
Tecnologías de fusión de metales
El corazón del proceso de fusión del metal se basa en el horno de fusión que involucra y afecta directamente la efectividad del proceso de fusión. Existen diferentes tecnologías de fusión que afectan la forma de fundir el metal y deciden qué horno está en uso.
Cómo elegir un horno de fusión
El horno de fusión afecta en gran medida no solo la eficacia operativa de la fundición, sino también los resultados finales de fundición, por lo que es muy importante tener en cuenta qué tecnologías de horno se deben aplicar.
Como sabe, los hornos de fusión de metales varían en forma, geometría, combustible y capacidad.
Los siguientes factores deciden estrictamente qué horno de fusión se adapta a su operación de fundición.
- Disponibilidad de espacio:consulta tu zona de producción. ¿Dónde pondrás el horno?
- Tipo de aleaciones a fundir y su punto de fusión
- Capacidad de fusión y cantidad de metal
- Eficiencia energética
- Inversión de capital
- Coste de operación
- Requisito de mantenimiento
- Cuestión de emisiones y medio ambiente
Por supuesto, no existe una opción única, pero los fabricantes de fundición deben considerar qué criterios son más importantes que otros. Cada fundición de fundición de metales tendrá sus propios criterios de prioridad para elegir el horno de fusión que se ajuste a su demanda y escala de producción.
Después de aclarar estas consideraciones, el segundo paso es seleccionar el que trabaja en su fundición de fundición. Aquí clasificamos los hornos de fusión más populares en las fundiciones de metales en la actualidad. Vamos a comprobarlo.
Tecnologías de hornos de fusión actuales y emergentes en la fundición de metales
Para fundir metal en la metalurgia, se utilizan diferentes tipos de hornos. Se clasifican según la fuente de calor, las propiedades operativas y la construcción del horno.
Los hornos de crisol y cubilote son métodos de fusión tradicionales, mientras que los hornos de arco eléctrico y de inducción son las tecnologías de fusión modernas y avanzadas.
Horno de Crisol
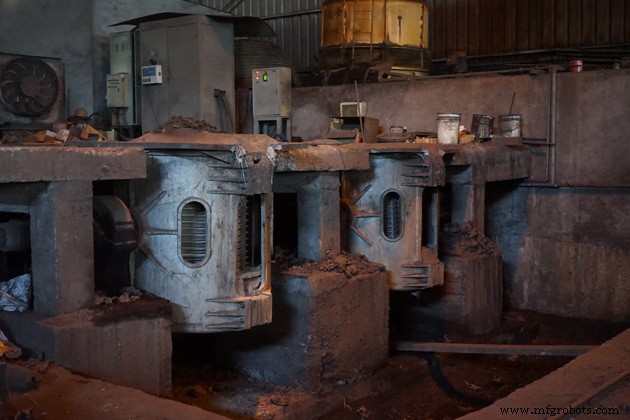
El horno de crisol es el recipiente de fusión más antiguo, simple y original que se utiliza en las fundiciones metalúrgicas. Este dispositivo de fusión básico está hecho de materiales resistentes a altas temperaturas que a menudo son sustancias cerámicas o refractarias.
El horno de crisol puede venir en una taza muy pequeña que generalmente se usa para derretir joyas (oro, plata) a un recipiente más grande que se aplica para trabajos en lotes pequeños.
El combustible de calefacción del crisol suele ser coque, gas, petróleo o electricidad. Mientras que el crisol eléctrico tiene una capacidad máxima de 2,5 ton/h, el crisol de gas o combustible líquido puede derretir hasta 4 ton/h.
El horno de crisol no es un dispositivo de eficiencia energética con más del 60 % de pérdida de calor por radiación.
Este horno es adecuado para metales no ferrosos que se aplican especialmente para la fundición de aluminio. Se desempeñan bien en cualquier aleación de aluminio. Una ventaja es que el crisol es muy fácil de operar y mantener, por lo tanto, ahorra costos. Además, su bajo costo de capital atrae a las pequeñas fundiciones de fundición a invertir su dinero.
Sin embargo, este horno solo se adapta a un volumen de producción pequeño y metal de bajo punto de fusión debido a su baja eficiencia energética.
Hornos de cúpula
El horno de cúpula se considera una de las tecnologías de fusión más económicas. Hoy en día, este horno funde casi hierro gris.
Hablando de construcción, la cúpula se puede hacer en cualquier forma y tamaño, pero su diámetro puede variar de 0,5 a 4 m y su altura es de unos 6-11 m. La cúpula está construida como un recipiente vertical y cilíndrico a modo de gran chimenea.
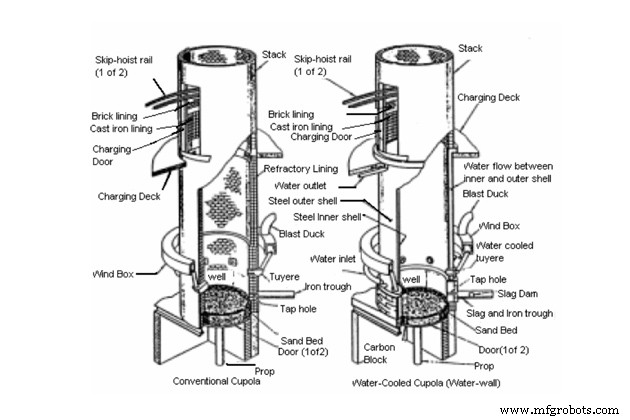
La pared del horno de cúpula generalmente está hecha de acero y está revestida con una pared de ladrillo refractario. El fondo del horno está revestido de manera similar, pero a menudo se usa una mezcla de arcilla y arena, ya que este revestimiento es solo temporal. Algunas cúpulas están equipadas con capas de carcasa de enfriamiento para mantenerlo fresco y se les agrega oxígeno para que el coque se queme más intensamente.
El combustible de calefacción del horno de cubilote es coque y algunos aditivos. Para iniciar un lote de producción, se agregan capas de coque al horno y se encienden con un soplete. Cuando el coque se enciende, el aire se introduce en las capas de coque a través de las rejillas de ventilación. La madera, el carbón o los gases combustibles también se pueden usar como combustible para hornos.
Cuando el coque está lo suficientemente caliente, los metales sólidos se introducen en el horno a través del orificio en la parte superior. Durante el proceso de fusión, tiene lugar la reacción termodinámica entre el combustible y el aire de entrada.
El carbono del coque se combina con el oxígeno del aire para crear monóxido de carbono, que continúa quemándose hasta convertirse en dióxido de carbono. Una cierta cantidad de carbono se disuelve en las gotas de metal líquido que caen y, por lo tanto, aumenta el contenido de carbono en el metal. Este proceso de fusión produce diferentes tipos de grado de hierro y acero.
El horno de cúpula se puede aplicar para derretir cualquier ferroso, principalmente utilizado para la fusión de hierro con gran volumen. Estadísticamente, el 60% del hierro fundido se funde en una cúpula. Su eficiencia energética también es alta, tómese en cuenta alrededor del 40-70%.
Hornos de arco eléctrico
El horno de arco eléctrico (EAF) es un horno que utiliza la energía de un arco eléctrico para calentar y fundir el material.
Va desde 1 tonelada (normalmente para producir arrabio) hasta 400 toneladas (para acero secundario). Los hornos industriales de arco eléctrico pueden alcanzar temperaturas de 1800 °C (3272 °F), mientras que los recipientes de laboratorio pueden alcanzar más de 3000 °C (5432 °F).
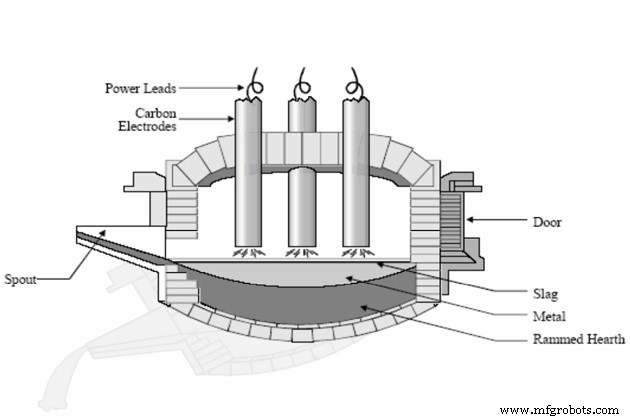
¿Cómo fundir metal con el horno de arco eléctrico?
En el horno de arco eléctrico, el material está en contacto directo con la electricidad del arco y la corriente eléctrica pasa a través del material. Por lo tanto, la fusión es más efectiva que otras tecnologías que utilizan calor externo.
El horno de arco eléctrico se utiliza a menudo para fundir acero (se tiene en cuenta el 87 %), mientras que el 13 % es para fundir hierro. Pueden procesar chatarra triturada de automóviles de acero con elementos residuales altos que no serán efectivos mediante la fusión del cubilote.
Horno de inducción
Un horno de inducción es un horno eléctrico que utiliza el principio de inducción electromagnética. Entonces, ¿cómo fundir metal con esta tecnología de fusión?
El metal se carga en el crisol que rodea la bobina de alambre de cobre que transporta corriente eléctrica alterna. Una vez que se enciende el horno de inducción, la bobina crea rápidamente un campo magnético inverso que penetra sobre el metal. El campo magnético crea corrientes de Foucault, una corriente eléctrica circular que corre dentro del metal. Como resultado, la circulación de estas corrientes crea temperaturas muy altas que derriten los metales.
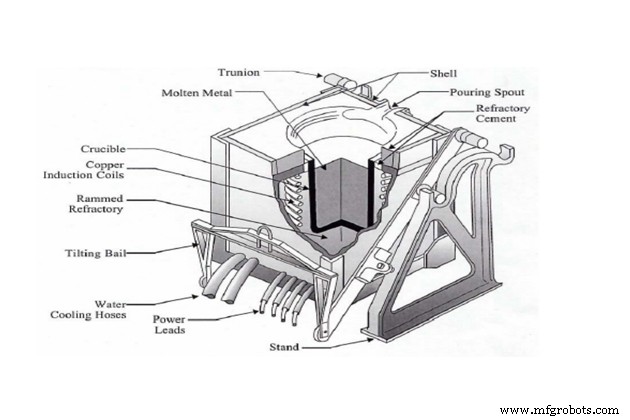
La capacidad de fusión de los hornos de inducción oscila entre menos de 1 kg y 100 toneladas, y se utilizan comúnmente para fundir hierro, acero, cobre, aluminio y metales preciosos.
En comparación con otras tecnologías de fundición de metales, la ventaja de los hornos de inducción es que son limpios, eficientes energéticamente y fáciles de controlar el proceso de fusión.
Sin embargo, los límites del horno de inducción en tipos de chatarra metálica y algunos elementos de aleación pueden perderse debido a la oxidación.
Puntos de fusión de metales
La mayoría de los metales que existen en la tierra tienen su estado normal como sólido. Sin embargo, en las industrias metalúrgicas, especialmente en la fundición de metales y la metalurgia, es necesario licuar el metal para producir un nuevo producto. Para licuar el metal, es necesario calentar el metal hasta su punto de fusión.
Por lo tanto, es tan importante como derretir metal para conocer la temperatura de fusión de las sustancias. Hace que el procesamiento de fundición de metales sea más simple. Los expertos pueden calcular con precisión el tiempo de moldeo, fusión y congelación de los productos de fundición. Esto ayuda a la producción ineficiente, al mismo tiempo, brinda las soluciones de respaldo necesarias para que su trabajo maneje emergencias.
¿Cuál es el punto de fusión?
El punto de fusión, también conocido como temperatura de licuefacción, es la temperatura a la que tiene lugar el proceso de fusión de un metal sólido. Es el punto en el que el metal se transforma de la fase sólida a la fase líquida. El punto de fusión varía de un metal a otro.
En la práctica, el punto de fusión se considera relativo. Es insensible a la presión. Algunas sustancias amorfas, como el vidrio, no tienen un punto de fusión fijo.

¿Qué metal tiene el punto de fusión más alto?
Volfram (W), también conocido como tungsteno, es el metal con el punto de fusión más alto (3422 °C; 6192 °F) , la presión de vapor más baja (a temperaturas superiores a 1650 °C, 3000 °F) y la resistencia a la tracción más alta.
El metal más fácil de fundir
Hasta este punto, el metal con el punto de fusión más bajo es mercurio con un punto de fusión de -38.830C. Es el único metal en la tierra en estado líquido bajo condiciones químicas normales de temperatura y presión estándar.
Actualmente, la principal aplicación del mercurio es su uso como termómetro, presión, manómetro, válvula de flotador, interruptor de mercurio, etc.
Punto de fusión del hierro y el acero
El hierro es el metal más utilizado en el mundo en la actualidad y representa el 95 % de la producción total anual de metales.
El hierro puro es suave y flexible. Pero al agregar el componente de carbono a una tasa de 0,002 % a 2,1 %, se creará una aleación de acero con una dureza, ductilidad y capacidad de carga sobresalientes.
El hierro tiene un punto de fusión de 1538°C mientras que el del acero es de 1370°C . Actualmente, el hierro y el acero son dos metales que se utilizan mucho en el campo de la fabricación mecánica, industria del automóvil, construcción naval, construcción, etc.
Punto de fusión del aluminio
El aluminio tiene un punto de fusión de 933,47K (660,32 °C; 1220,58 °F) . El punto de fusión del aluminio no es alto en comparación con otros metales.
En la tabla periódica, el aluminio se denota Al; Número atómico es 13, densidad 2,9 g/cm3. El aluminio es liviano, suave y tiene una excelente resistencia a la corrosión y una buena capacidad de colado. Es el metal más común en la corteza terrestre. La fundición de aluminio se usa ampliamente en detalles de máquinas, motores y decoración urbana exterior.
Metal | punto de fusión (°C) | punto de fusión (°F) |
Aluminio | 660.32 | 1220,58 |
Aleación de aluminio | 463 – 671 | 865 – 1240 |
Hierro forjado | 1482 – 1593 | 2700 – 2900 |
Hierro, fundición gris | 1127 – 1204 | 2060 – 2200 |
Hierro dúctil | 1149 | 2100 |
Lead | 327,5 | 621 |
Magnesio | 650 | 1200 |
Acero al carbono | 1425 - 1540 | 2600 – 2800 |
Acero inoxidable | 1510 | 2750 |
Guía de seguridad protectora en el proceso de fundición de metales
El proceso de fusión del metal tiene que lidiar diariamente con un calentamiento extremo (podría llegar hasta los 2000° C) que es un entorno de trabajo muy peligroso.
Se puede decir que la fundición es uno de los trabajos más peligrosos que provocan accidentes inesperados en las fundiciones de metales. Lea más sobre cómo funciona la fundición de metales.
Por lo tanto, para proteger la salud y la vida del trabajador y evitar pérdidas y daños a las propiedades de la fundición, existe una guía estricta que los fabricantes de fundiciones de fundición de metales deben tener en cuenta.
Asegurar la infraestructura de fundición
- El área de fusión debe organizarse por separado para evitar el peligro para los trabajadores no autorizados
- Debe haber ventilación y el diseño del techo de la fundición debe ser alto para la circulación de aire
- El horno debe garantizar calidad y seguridad cuando se usa
- Debe estar equipado con un sistema automático o semiautomático para verter y repostar para limitar la exposición humana y los accidentes.
- El equipo a prueba de explosiones e incendios debe estar siempre listo
Garantizar la ropa de seguridad protectora para el trabajador
El trabajador de fundición debe estar equipado con ropa de protección completa durante su turno. Gorro, gafas, guante, máscara, ropa gruesa y calzado son accesorios obligatorios.
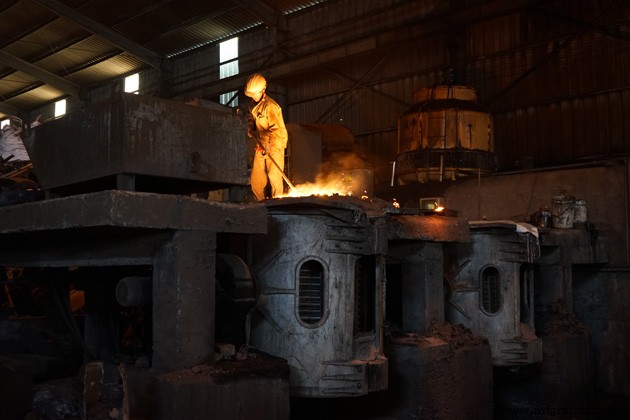
Qué hacer y qué no
- Ponga una señal de precaución para la zona de fusión
- Restringir el acceso de trabajadores no autorizados a la zona de fusión
- Revise periódicamente el horno y el sistema de ventilación y asegúrese de que uno ineficaz se repare inmediatamente
- Limpie y seque el material metálico antes de derretirlo
- Precaliente los hornos y los refractarios antes de usarlos
- Prepare un plan de emergencia
- No permita fumar, comer, beber en la zona de fusión
Resumen
A través del contenido anterior, proporcionamos una explicación detallada de Cómo fundir metal en una fundición . Con suerte, lo actualizará con algunas ideas interesantes sobre el proceso de fusión del metal.
Lea más sobre nuestro blog sobre el procedimiento de fundición en las fundiciones metalúrgicas aquí.
Presentado brevemente, VIC es el fabricante de fundición de metales que se especializa en la fabricación y el suministro de piezas de fundición de metales al mercado mundial. Si lo necesita, comuníquese con nosotros para realizar un pedido y obtener asesoramiento sobre el tratamiento de yeso.
Referencia
Departamento de Energía de los Estados Unidos (2005). Tecnologías de fusión avanzadas:conceptos de ahorro de energía y oportunidades para la industria de la fundición de metales .https://www.energy.gov/sites/prod/files/2013/11/f4/advancedmeltingtechnologies.pdf.
Trabajo Seguro Australia (2013). Guía para la Gestión de Riesgos Asociados al Trabajo de Fundición. https://www.safeworkaustralia.gov.au/system/files/documents/1702/guide-managing-risks-associated-foundry-workl.pdf
Proceso de manufactura
- Cómo funcionan los laminadores en la siderurgia
- En qué se diferencian los elementos metálicos de los no metálicos
- Cómo las impresoras 3D construyen objetos metálicos
- Cómo oxidar metal
- Cómo detener el óxido
- Cómo prevenir la corrosión del metal
- Comprender cómo se realiza el proceso de corte
- Cómo utilizar su máquina perforadora para taladrar metal
- ¿Qué es una Fundición?
- ¿Qué tal una máquina de prensado en frío?
- Cómo usar un torno de metal