¿Qué es el sistema de compuertas? ¿Cuántos tipos y cómo diseñar?
En la fundición en arena, el sistema de vertido de metal es extremadamente crucial porque su diseño afecta la calidad de la fundición y reduce el desperdicio de metal en el sistema de vertido. En este artículo, VIC le brindará una visión detallada del sistema de activación en el proceso de fundición.
¿Qué es el sistema de gating en fundición?
En la fundición de metales, el sistema de entrada en fundición es un sistema de vertido de metal que conduce el metal fundido a la cavidad del molde. El metal fluye hacia abajo desde el recipiente de vertido hacia el bebedero y pasa a través del corredor y las compuertas antes de ingresar a la cavidad del molde.
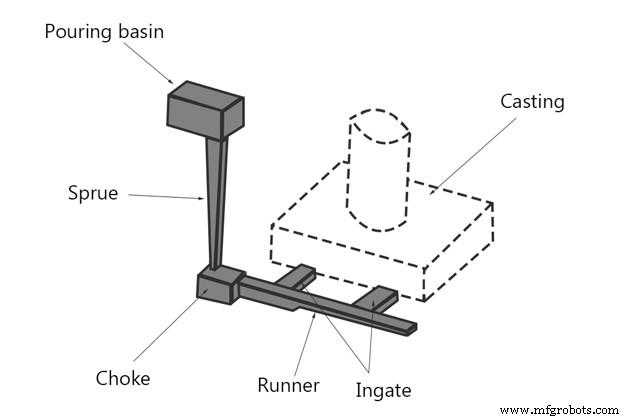
El diseño de un sistema de compuerta requiere una cuidadosa consideración de acuerdo con la tecnología, los materiales y las piezas fundidas.
Este sistema determina el caudal de metal a la cavidad del molde.
Si el caudal es demasiado rápido, existe el riesgo de corrosión, mientras que si la velocidad es demasiado lenta puede hacer que el metal se enfríe antes de llenar la cámara, lo que Afecta directamente a la calidad de la fundición.
La forma y el tamaño del sistema de inyección en la fundición se organizan correctamente al hacer el molde. Si el sistema de compuerta no está diseñado correctamente, puede causar graves defectos de fundición.
Envíame un mensaje privado para obtener ayuda:https://sites.google.com/view/hrv-job/
Funciones del sistema de inyección en la fundición en arena
El sistema de inyección en fundición está diseñado para servir a los siguientes 4 objetivos principales :
- Llene la cavidad del molde con suficiente metal en el menor tiempo posible sin tener que aumentar la temperatura del metal.
- El metal fluye suavemente, minimizando la turbulencia que provoca que el aire quede atrapado durante la fundición.
- El sistema de inyección establece el rango de temperatura adecuado para que, durante el proceso de enfriamiento del metal, se produzca una contracción en el sistema de inyección, no en las piezas fundidas.
- Combinado con sistema de eliminación de impurezas metálicas.
Requisitos de diseño del sistema de compuertas
Un sistema de inyección bien diseñado en la fundición debe cumplir los siguientes requisitos:
- Buen control del flujo de metal. Sin impacto, sin salpicaduras, continuidad suave y constante.
- No introduzca escoria, impurezas ni gases en la cavidad del molde.
- Rellena la cavidad del molde rápidamente, no reduce la dilución del metal.
- Controlar la temperatura en la cavidad del molde para enfriar el metal de manera estable.
- Capaz de agregar metal y no desperdiciar mucho metal.
- Fácil de desmontar después de que la fundición se haya solidificado.
- Rendimiento de fundición económico y maximizador.
Si el sistema de control está diseñado incorrectamente, pueden ocurrir los siguientes errores :
- Metales oxidantes.
- Corrosivo para el moho.
- Causa la contracción de los objetos en el molde.
- Haga que el metal penetre en la pared del molde.
- Fundición fresca y desigual.
Diagrama del sistema de puertas
El sistema de inyección en la fundición en arena incluye:
1. Vertedor o taza de vertido
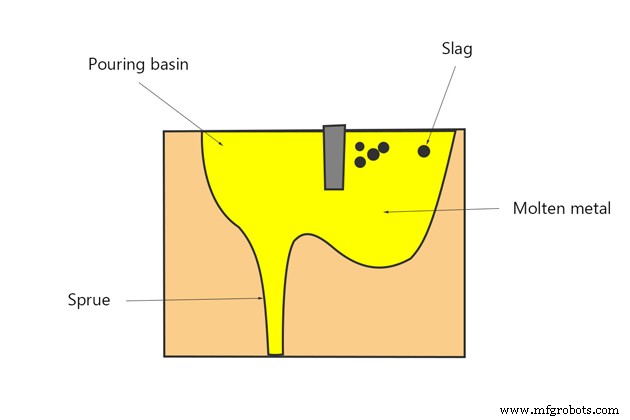
La cubeta de vertido es la entrada en forma de embudo, ubicada en la parte superior del sistema, donde se vierte el metal de las cucharas al molde .
El depósito de vertido ayuda a regular el caudal de metal líquido y reduce la turbulencia en la entrada del bebedero, y ayuda a separar los sedimentos y la escoria antes de entrar en el bebedero.
2. Bebedero
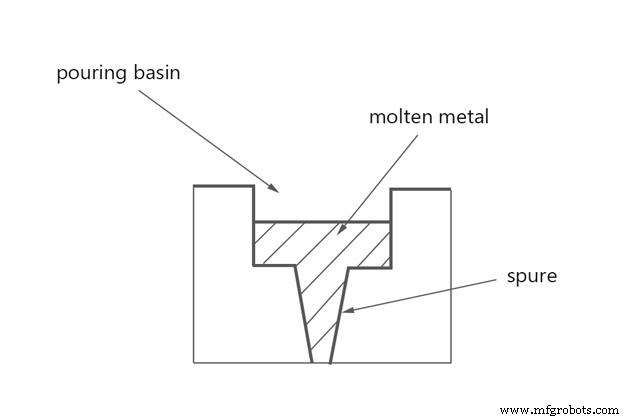
La colada de bebedero es un pasaje vertical desde el depósito de vertido hasta el corredor y las compuertas. El metal líquido que baja por el bebedero vertical pierde presión pero aumenta la velocidad por efecto de la gravedad.
La sección transversal del bebedero puede ser circular, cuadrada o rectangular (preferiblemente circular ). El bebedero está diseñado para disminuir para evitar la aspiración de aire . Extremo más grande arriba para recoger metal, mientras que el extremo más pequeño se conecta al corredor.
El pie del bebedero se gira en ángulo recto con respecto a la corredera para evitar la caída libre del metal líquido, lo que se conoce como pozo del bebedero.
3. Puerta cruzada o corredor
El corredor en fundición es un canal horizontal que conecta el pozo del bebedero con las compuertas. El metal líquido fluirá desde el bebedero hasta el corredor y llenará la cavidad del molde apropiadamente. Runner tiene el efecto de disminuir la velocidad del metal líquido cuando está en caída libre en un bebedero de alta velocidad.
El corredor debe llenarse con metal fundido para evitar la escoria entre en la cavidad y asegure un flujo constante.
4. Ingate (o puerta)
Ingate es el final del camino y donde comienza la cavidad del molde. Conduce el metal líquido que fluye desde el corredor hacia la cavidad del molde. Dependiendo de las características del casting, hay diferente número de entradas.
Hay dos tipos de puertas:puerta grande y puerta pequeña. La puerta pequeña se utiliza para ralentizar la colada sólida, mientras que la puerta grande se utiliza para acelerar la colada sólida.
La puerta no debe tener bordes afilados, ya que pueden agrietarse durante el vertido, de modo que la arena pueda quedar atrapada en el metal fundido en la cavidad del molde.
Tipos de compuertas en fundición:
Gate se divide en 3 categorías:
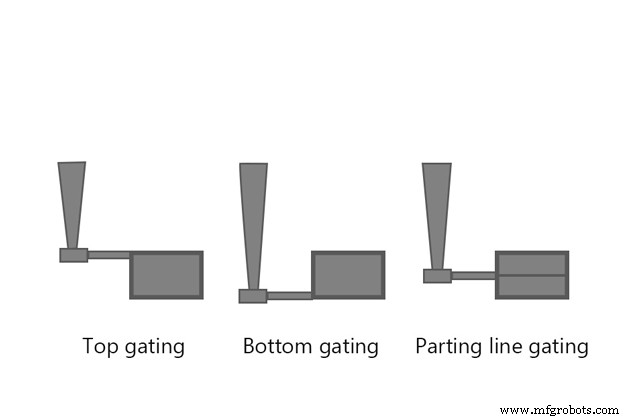
- Puerta superior :la puerta está en la parte del molde de la cubierta.
Las desventajas de la compuerta superior son la alta turbulencia del flujo de metal y la superficie de fundición deficiente.
- Puerta inferior :la puerta está en la parte del molde de arrastre. En la entrada inferior, el metal líquido llena la parte inferior de la cavidad del molde y aumenta gradualmente en la pared del molde.
La puerta inferior tiene la ventaja de generar menos caos y erosión de arena que la puerta superior.
La desventaja de la compuerta inferior es que el flujo de metal puede obstruirse debido a la solidificación antes de que el molde esté lleno. El rango de temperatura generado por la puerta inferior es difícil de alcanzar el estándar causando una solidificación desigual.
- Puerta lateral de línea divisoria :es la puerta ubicada a lo largo de la línea de separación. El compartimento por debajo de la línea de separación se llena con metal líquido a través de la entrada superior, mientras que el compartimento por encima de la línea de separación se llena con la entrada inferior. Este tipo de puerta resuelve las desventajas de los dos tipos anteriores.
Tipos de sistema de compuerta
Hay dos tipos de sistemas de gating:Sistema de gating presurizado y Sistema de apertura sin presión . La elección del sistema de colado correcto con la relación de área correcta definirá la calidad de la colada.
1. Sistema de compuerta presurizado
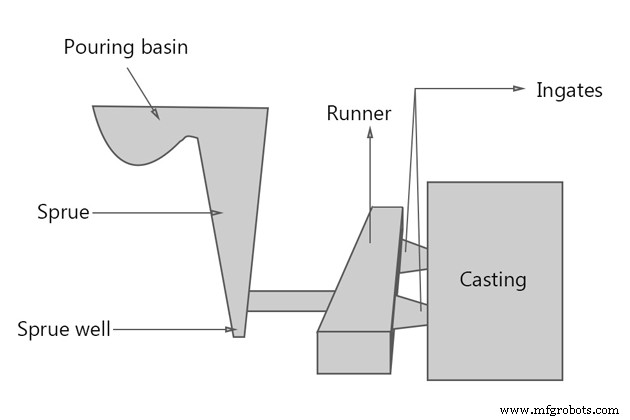
El sistema de inyección presurizado es un sistema de inyección cuya superficie de sección transversal disminuye gradualmente hacia la cavidad del molde (más pequeña que el área más estrecha del canal de bajada). El área de entrada se minimiza para ejercer presión sobre el sistema. En las puertas, el caudal de metal líquido es casi igual.
El bebedero siempre está lleno de metal creando contrapresión, lo que reduce la aspiración de aire.
Aquí, el metal que siempre está funcionando a altas velocidades se vuelve más caótico y es fácil crear corrientes de Foucault en las puertas que conducen a la erosión.
Este sistema da especial prioridad al moldeo por inyección con materiales de fundición.
2. Sistema de compuerta no presurizado
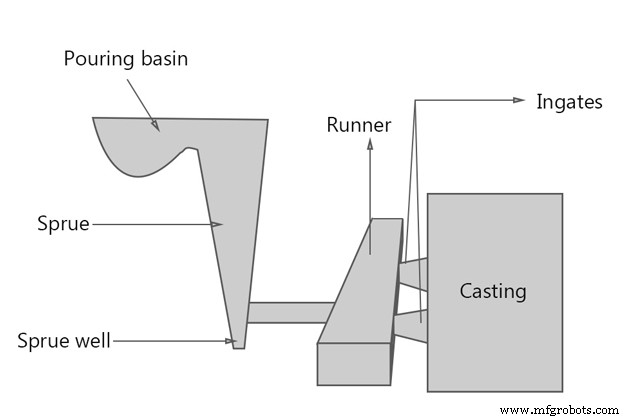
El sistema de inyección sin presión es un sistema de inyección cuya superficie total de las puertas aumenta gradualmente hacia la cavidad del molde (más grande que el área más estrecha del bebedero). El flujo de metal líquido en las puertas es diferente.
Proporción de activación
La relación de entrada es la relación entre el área transversal del bebedero, el área transversal total de los corredores y el área transversal total de las entradas.
La fórmula para la relación de activación es As:Ar:Ag.
Con el sistema de activación presurizado, la relación de activación suele ser 1:2:1 o 1:0,75:0,5. Este sistema se denomina “Sistema de control de puerta ” porque ingates controlan el flujo del metal .
Con el sistema de activación sin presión, la relación de activación suele ser 1:2:2 o 1:3:3 o 1:1:3. Este sistema se denomina "Sistema de control de estrangulamiento ” porque el estrangulador controla el flujo del metal .
Tabla de relación de activación para varios materiales:
Materiales | Proporción de activación |
Aluminio | 1:2:1 1:1.2:2 1:2:4 1:3:3 1:4:4 1:6:6 |
Aluminio bronce | 1:2.88:4.8 |
Latón | 1:1:1 1:2:3 1.6:1.3:1 |
Cobre | 2:8:1 3:9:1 |
Hierro dúctil | 1.15:1.1:1 1,25:1,13:1 1.33:2.67:1 |
El principio hidráulico utilizado en los sistemas de compuertas
Número de Reynolds
Este es el número que ayuda a predecir los tipos de flujo con diferentes flujos de líquido. La naturaleza del flujo en el sistema de compuerta se puede establecer calculando el número de Reynolds:
Re = ρuL/µ = uL/v
Re:Número de Reynold
ρ:densidad del fluido (kg/m3)
u:velocidad del flujo (m/s)
L:dimensión lineal característica (m)
µ:viscosidad dinámica de fluidos (Pa.s)
v:viscosidad cinemática del fluido (m2/s)
- Si Re> 2000, el flujo es estable.
- Si Re <2000, el flujo es caótico.
Si el flujo es turbulento, los granos de arena en el molde saldrán disparados del molde y el sistema de compuerta entrará en la cavidad del molde provoca problemas como la contaminación de la fundición, la aspiración de aire en el molde y la erosión de la pared del molde.
Ecuación de Bernoulli
Los metales líquidos pasan por diferentes canales en el molde de acuerdo con el teorema de Bernoulli de que la cabeza total permanece constante en cualquier sección.
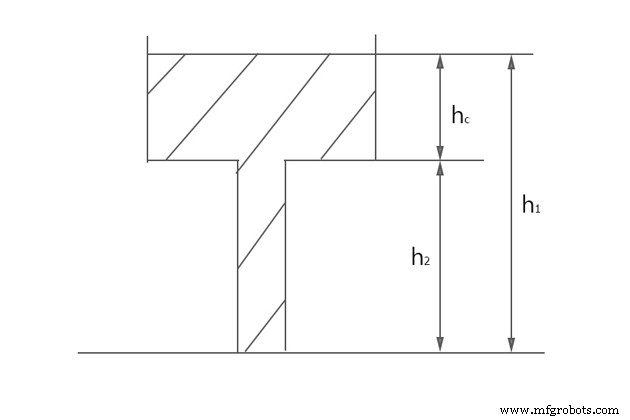
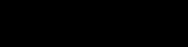
h:altura potencial (m)
p:presión (Pa)
V:velocidad del metal fundido (m/s)
w:peso específico del líquido (N/m2)
g =9,8 (m/s)
ρ:densidad del fluido (kg/m3)
El sistema de compuerta debe diseñarse de modo que el metal líquido esté siempre lleno. Todas las secciones transversales y los cambios de dirección deben evitar las esquinas pronunciadas y aprovecha las esquinas redondeadas .
Cómo diseñar un sistema de compuertas
Para diseñar el sistema de vertido, el diseñador debe cumplir con los requisitos de diseño como se describió anteriormente. Aquí están las fórmulas para calcular y diseñar un sistema de compuerta adecuado.
Haga clic aquí para ver los detalles.
1. Calcular el tiempo de vertido
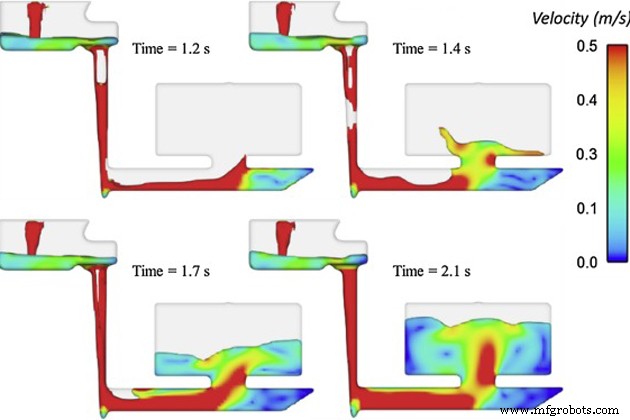
El tiempo de vertido es el momento en que el metal llena la cavidad del molde. Cuanto mayor sea el tiempo de vertido, mayor será la temperatura de vertido y no se garantiza el llenado del molde. Cuanto más corto sea el tiempo de vertido, más caótico el flujo de metal en el molde provoca la erosión del troquel y una contracción excesiva.
El tiempo de vertido debe optimizarse en función de estos factores:
- Materiales de fundición
- La complejidad del casting
- Tamaño del yeso
- Espesor de la sección
La fórmula para calcular el tiempo de vertido óptimo:
- Con material de hierro fundido gris con un peso inferior a 450 kg:
t=K(1.41+T/14.59)√W
K =fluidez del hierro (pulgadas) / 40
K:factor de fluidez
T:espesor medio de la sección (mm)
W:masa de fundición (kg)
- Con material de hierro fundido gris con un peso superior a 450 kg:
t=K(1.236+T/16.65)∛W
- Con fundición de acero:
t=(2.4335-0.3953logW)√W
- Con hierro dúctil:
t=K₁√W
K₁=2,08 para secciones más delgadas.
K₁=2,67 para secciones de 10 a 25 mm de espesor.
K₁=2,97 para secciones pesadas.
- Con fundiciones de aleación de cobre:
t=K₂∛W
- Las piezas fundidas con paredes delgadas y formas complejas pesan hasta 450 kg:
t=K₃∛W'
W’:masa de la fundición con compuertas y contrahuellas (kg)
Grosor (mm) | K₃ |
1,5 – 2,5 | 1,62 |
2,5 – 3,5 | 1,68 |
3,5 – 8,0 | 1,85 |
8,0 – 15,0 | 2.20 |
- El peso de lanzamiento oscila entre 450 kg y 1000 kg:
t=K₄∛(W'T)
Grosor (mm) | K₄ |
<10 | 1,00 |
10 – 20 | 1,35 |
20 – 40 | 1,50 |
> 40 | 1,70 |
2. Bebedero de diseño
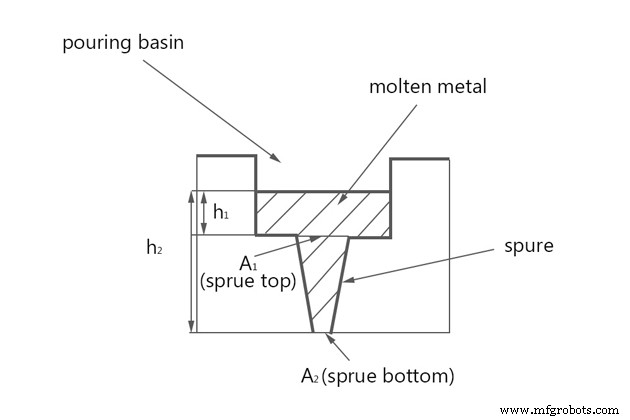
El diseño ideal del bebedero es que la parte superior grande termina y se estrecha hacia abajo como una parábola. Sin embargo, para facilitar la producción, se recomienda utilizar un cilindro cónico . El nivel de calificación mínimo es del 5%.
La sección transversal circular de salida del bebedero se diseña en función del área del estrangulador y la relación de entrada. Esto ayuda a reducir las perturbaciones y la pérdida de calor. .
La fórmula de cálculo del bebedero:
A₁/A₂=√h₂/√h₁
h1 y h2:cabeza de presión estática de metal en el bebedero superior y en el bebedero inferior.
A1 y A2:el área de la sección transversal respectiva.
Diseño del pozo del bebedero :Un diseño razonable del pozo del bebedero es hacer un cilindro del doble del diámetro de la salida del bebedero y del doble de la profundidad del canal. Un filete colocado entre el pozo y el canal ayudará a que el metal se desplace perpendicularmente con suavidad. .
3. Estrangulador de diseño
El estrangulador es un área de control colocada en el pozo del bebedero para controlar el flujo de metal líquido que fluye hacia la cavidad del molde para que el molde se llene en el tiempo de vertido calculado.
El área de estrangulamiento juega un papel importante en los sistemas de compuerta porque el área permite que el metal pase a través de un flujo constante y constante. El estrangulador tiene la relación más pequeña del sistema de activación en comparación con las otras partes y el área de la sección transversal es más pequeña en el área de control.
Fórmula para calcular el área de estrangulamiento:
A=W/(dtC√(2gH))
A:área de estrangulamiento (mm)
t:tiempo de vertido (s)
d:densidad de masa del metal fundido (kg/mm3)
Al:d =2500
Cu, Fe, Ni, Co:d =7000
C:eficiencia del sistema de gating utilizado (=0,8)
W:peso de lanzamiento incluyendo comederos y canales de entrada (kg)
g =9,8 m/s2
H:altura del bebedero (mm), calcular H por:
- Con puerta superior:H =h
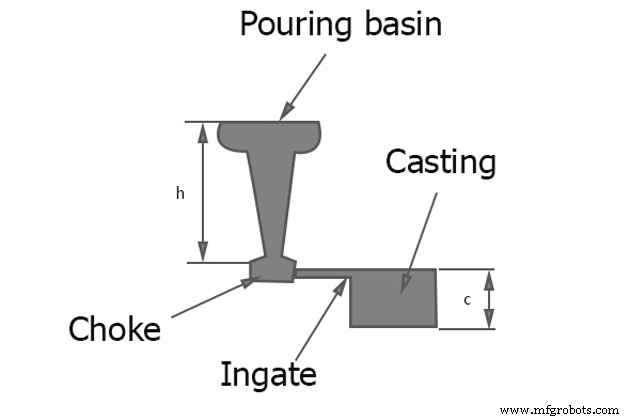
- Con puerta inferior:H =h – c/2
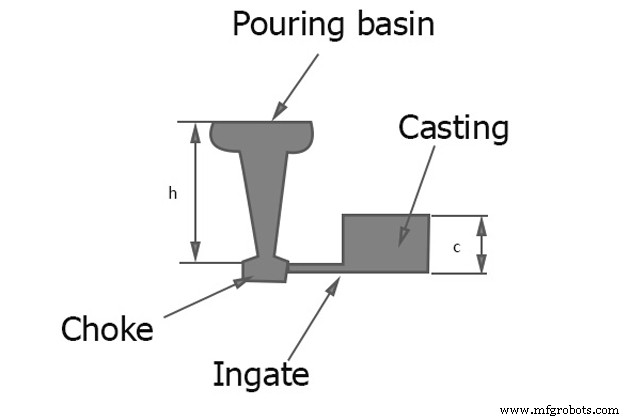
- Con compuerta de línea divisoria:H =h – P²/2c
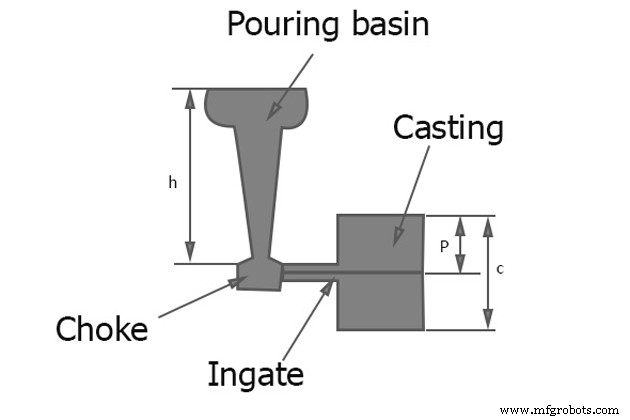
4. Corredor de diseño
El área transversal total del canal debe ser mayor que la salida del bebedero para reducir la velocidad del flujo de metal desde el bebedero hasta las puertas.
La relación de prioridad entre la salida del bebedero y la sección transversal del canal es de 1:2. Mayores proporciones pueden provocar la separación del flujo y la aspiración de aire.
Si hay múltiples entradas, el área de la sección transversal del corredor después de cada paso por la entrada debe disminuir gradualmente por un área igual a la del ingate para asegurar un flujo constante.
5. Diseño Ingate
Ingate debe hacerse más grande que la salida del bebedero para acelerar el metal por debajo del límite.
- Ingate debe tener una sección transversal más pequeña para facilitar el transporte.
- El volumen de la relación en el área de la superficie de enfriamiento debe ser menor que la relación de la parte conectada para evitar un punto caliente local.
- El área de la superficie de la sección transversal del ingate debe ser proporcional al tamaño del área de fundición conectada. Cuanto mayor sea el área de fundición, mayor será el flujo requerido, lo que dará como resultado una entrada más grande.
6. Diseño Riser (o alimentador, cabecera)
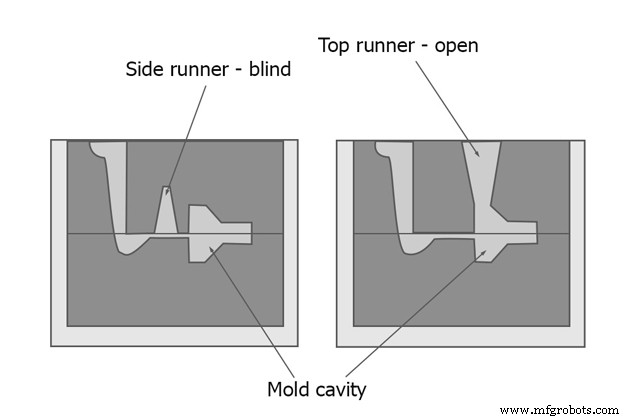
El Riser es una cavidad de metal fundido en un molde, lista para suministrar metal a la cavidad del molde para compensar la contracción a medida que el metal se enfría. Se coloca en la posición de solidificación final de la fundición, y se encuentra en estado líquido durante el mayor tiempo. El Riser también es donde se liberan los gases generados dentro del molde durante el proceso de fundición.
Diseño óptimo de bandas:
- Tamaño del elevador :La relación volumen/superficie de la mazarota debe ser mayor que la del colado para mantener un estado líquido. Si no se puede cumplir esta condición, el metal debe mantenerse líquido calentándolo externamente o usando un material exotérmico en el tubo ascendente.
- Posición de la contrahuella :la distancia de las contrahuellas debe calcularse correctamente en función de la distancia de alimentación de metal de las contrahuellas.
- Forma del elevador :la forma recomendada para la mazarota es cilíndrica porque se supone que la globular es la mejor pero es difícil de lanzar. La parte inferior del elevador debe ser hemisférica para aumentar la relación volumen/área de superficie.
¿Cómo comprobar la eficacia del diseño de puertas?
El diseño del sistema de gating se prueba a través de las siguientes técnicas:
- Agua en molde transparente :la cámara de rayos X de alta velocidad registra el llenado del molde y se puede observar el defecto.
- Radiografía de alta velocidad :la cámara de rayos X de alta velocidad registra el llenado del molde y se puede observar el defecto.
- Molde abierto :se corta parte del molde superior en la cavidad del molde y la cámara gira hacia atrás el flujo de metal líquido que llena la cavidad del molde.
- Sensor de hilo de contacto :los alambres se colocan en diferentes partes del molde, cuando la línea de metal toque el alambre se registrará con una grabadora miltichannel.
- Agua en molde transparente :La adición de gotas de aceite o marcadores de color facilitará el registro de las velocidades en diferentes áreas.
VIC es uno de los principales fabricantes de fundición de fundición de aluminio y hierro fundido. Nos estamos centrando en la fabricación de pesas rusas con alta calidad. Si tiene alguna pregunta o necesita cooperación con la fundición de metales, no dude en contactarnos por correo electrónico:[email protected]
Leer más:
Cómo calcular la contracción de fundición de aluminio
Cómo mejorar el acabado de la superficie de aluminio
¿Cómo se fabrican las pesas rusas mediante fundición en arena?
Referencias:
- Ingeniería de fundición y soldadura por el Dr. Ahmed Salad Abou Taleb
- https://en.wikipedia.org/wiki/Reynolds_number
- https://en.wikipedia.org/wiki/Bernoulli%27s_principle
- http://www.ijrerd.com/
Proceso de manufactura
- ¿Qué es una máquina virtual? Tipos y ventajas
- Diseño de sistema de puerta | Casting | Ciencias de la fabricación
- ¿Qué es la impresión 3D? - Tipos y cómo funciona
- ¿Qué es la soldadura por arco? - Tipos y cómo funciona
- ¿Qué es la soldadura? - Tipos y cómo soldar
- ¿Qué es la soldadura fuerte y cómo soldar metal?
- ¿Qué es la forja? Definición, proceso y tipos
- ¿Qué son los martillos de potencia? - Tipos, diseño y funcionamiento
- ¿Qué es la chapa metálica? Definición, tipos y usos
- ¿Qué es la fundición de metales? Definición, tipos y procesos
- Sistema de compuerta:definición, función, tipos, diagrama