¿Qué son los Procesos de Tratamiento Térmico?
El tratamiento térmico se define como un proceso combinado de calentamiento y enfriamiento de un metal para cambiar las propiedades físicas y mecánicas de un material. El tratamiento térmico se utiliza para homogeneizar la aleación de metal fundido para mejorar su capacidad de trabajo a temperaturas muy altas, para cambiar la microestructura de tal manera que se logren las propiedades mecánicas deseadas. Para realizar el proceso de tratamiento térmico, la seguridad es la primera prioridad de la persona que lo está tratando, ya que en el proceso se libera gran cantidad de calor, si algo sale mal puede resultar en problemas muy serios. El proceso de tratamiento térmico se realiza en el horno y los hornos donde la temperatura cambia según los requisitos y el metal en el proceso debe realizarse, además de esto, los gases se utilizan para controlar la atmósfera para el proceso particular de tratamiento térmico. Cuando el metal entra en contacto con la atmósfera, existe la posibilidad de que el metal pueda reaccionar con la atmósfera y participar en la reacción química. En la atmósfera, muchos gases y humedad están presentes que pueden afectar el proceso de tratamiento térmico, por lo que antes de realizar cualquier proceso de tratamiento térmico, se debe mantener la atmósfera del espacio en particular. Reduce el efecto de la oxidación sobre los componentes que se están tratando.
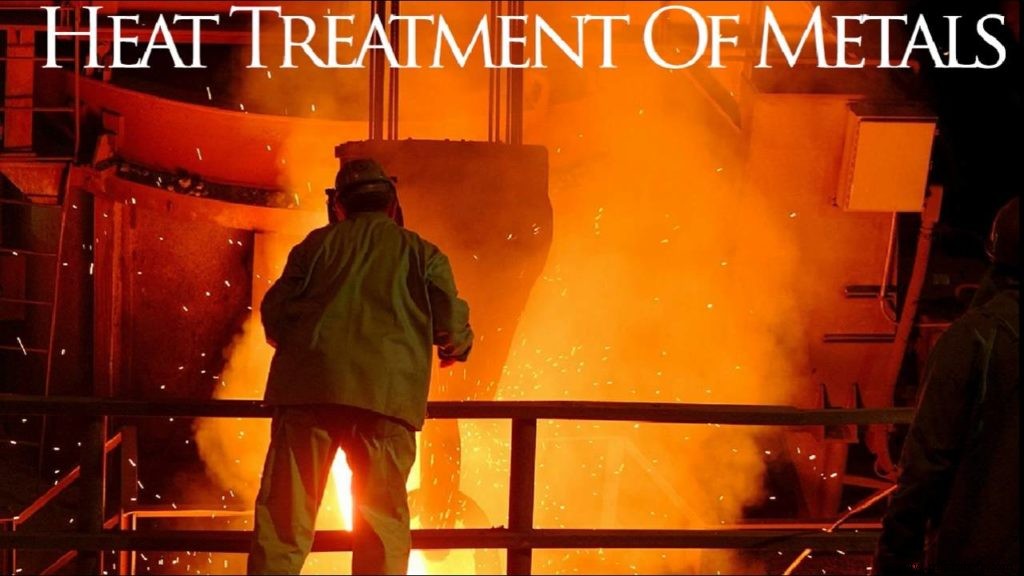
El tratamiento térmico está asociado con el aumento de la resistencia del material, pero no solo con la resistencia. También cambia los aspectos de fabricación, como mejorar el mecanizado, la formabilidad y, cuando la operación supera, el material restaura su ductilidad al enfriarse.
El objetivo del proceso de tratamiento térmico.
- Refine el tamaño del grano.
- Aumenta la maquinabilidad del material
- Eliminar la tensión residual interna.
- Eliminar los gases que fragilizan el acero.
- Cambia la composición de la superficie por difusión.
- Para lograr las propiedades mecánicas, físicas o químicas deseadas del material.
- Reblandecer el acero endurecido.
Los parámetros que afectan la composición y las propiedades materiales del metal son los siguientes.
- Ambiente
- Revestimiento de superficie
- Difusión superficial
- Refrigeración
- Calefacción
- Entrada de trabajo
- Tiempo
Clasificación del Proceso de Tratamiento Térmico:
El tratamiento térmico se puede clasificar en los siguientes tipos.
Proceso común de tratamiento térmico:
- Homogeneización
- Recocido
- Normalizando
El tratamiento utilizado para cambiar las propiedades de la superficie (química).
- Carburado
- Nitruración
- carbonitruración
- Carburación nitro
El tratamiento utilizado para cambiar la estructura de fases.
- Endurecimiento
- Templado
- Endurecimiento por inducción.
Proceso de tratamiento especial
- Sinterización
La introducción básica de todos estos procesos de tratamiento térmico se proporciona a continuación.
Proceso común de tratamiento térmico:
La homogeneización es un proceso de tratamiento general cuando el material entra en funcionamiento que antes del inicio del tratamiento real, se realiza la homogeneización para mantener la misma temperatura en todo el material que se está tratando. También se realiza para reducir el efecto de extracción de muestras causado por la composición química no uniforme.
Como dice la palabra, primero el material se calienta a una temperatura muy alta y luego se enfría lentamente. Es uno de los procesos de tratamiento térmico que se utiliza para aumentar la ductilidad del material y reducir la dureza. Cuando la dureza y la ductilidad del material cambian, se reduce la dislocación en la estructura cristalina de un material. El material se está calentando a la temperatura prefijada, manténgalo así durante un cierto tiempo y luego comience a enfriarse lentamente a temperatura ambiente. Si el material es acero, se lleva a cabo calentando el acero justo por encima de la temperatura crítica del acero, es decir, 727 grados centígrados, y se deja enfriar lentamente.
Etapas del proceso de recocido
- Etapa de recuperación
- Etapa de recristalización
- Etapa de crecimiento del grano.
Es el proceso de tratamiento térmico en el que el material se calienta por encima de los 910 grados centígrados para completar la austenización. Una vez que el material llega a la etapa de austenización, se enfría en presencia de aire para obtener la perlita fina, que tiene buena dureza y ductilidad. El proceso de normalización se utiliza para el material ferroso para mejorar las propiedades mecánicas del material.
Química de superficie:
1. Carburación
Proceso de tratamiento térmico superficial de carburación, que se realiza en la superficie del material con el fin de aumentar la dureza y la resistencia al desgaste del metal. Como su nombre lo indica, hay una adición de carbono en la superficie del metal, especialmente acero con bajo contenido de carbono a la temperatura predeterminada. También se denomina proceso de cementación en el que la parte del material con bajo contenido de carbono se calienta a altas temperaturas en presencia de una atmósfera de gas rica en carbono. Cuando el material se calienta a una temperatura alta en un entorno con alto contenido de carbono, permita la difusión de átomos de carbono directamente en la superficie de la pieza donde se debe realizar el proceso de cementación. La cantidad de carbono que se difunde en la superficie del metal depende del potencial de carbono de la atmósfera, la temperatura de calentamiento y el tiempo de exposición del material a esa temperatura. Para endurecer tanto el material de la carcasa como el del núcleo, se debe realizar un enfriamiento rápido. Una vez realizado el temple, la parte cementada del material se templa para lograr los requisitos del cliente. Mejora dramáticamente la ductilidad y dureza del material.
Diferentes métodos de carburación
Carburación de paquete
Carburación de gas
Carburación de vacío
Carburación líquida
Ventajas de la carburación:
- Se puede realizar tanto en partes simples como complejas.
- Aumenta la dureza superficial del material.
- Aumenta la resistencia al desgaste y la resistencia a la fatiga del material.
También es un proceso de tratamiento térmico, como su nombre lo indica, el nitrógeno se agrega a la superficie del material, especialmente el acero. Hay dos métodos involucrados en el proceso de nitruración, a saber, el proceso gaseoso y el proceso de plasma. En el proceso de nitruración, la parte del material se calienta a 600 grados Celsius en presencia de gas y amoníaco disociado y la dureza se logra mediante la formación de amoníaco en la superficie de la parte metálica. En el proceso gaseoso, el amoníaco disociado actúa como fuente, mientras que en el caso del plasma, el ion nitrógeno se difunde sobre la superficie del material. En la nitruración de gas, no se requiere el proceso de enfriamiento rápido y desarrolla la carcasa dura en la parte del material a bajas temperaturas. En la nitruración por plasma no es posible la penetración del agujero ciego y es un proceso muy restringido.
Ventajas de la nitruración
- Aumenta la vida de fatiga.
- Aumenta la resistencia al desgaste y la corrosión
- Se puede lograr una mayor dureza que la dureza cementada.
- No es necesario apagarlo.
- Distorsión mínima de la pieza.
- Alta dureza superficial y resistencia al desgaste.
- Aumenta la resistencia a la fatiga entre un 30 y un 100 %.
- Debido a una temperatura más baja, se reduce la distorsión.
- Bueno para aplicaciones de alta temperatura.
- Aumenta la resistencia a la tracción y el límite elástico.
También es un proceso de cementación y se utiliza para producir una superficie dura y resistente al desgaste en materiales de acero de baja calidad. La cementación con nitroferrítico difunde nitrógeno y carbono en la caja de una pieza de trabajo por debajo de la temperatura crítica de 650 grados Celsius. A esta temperatura, la microestructura de la pieza de trabajo o material no se convierte en fase austenítica, permanece en la fase ferrítica, por eso se denomina nitrocarburación ferrítica.
El tratamiento utilizado para cambiar la estructura de fase:
- Endurecimiento
- Templado
- Endurecimiento por inducción.
1.Endurecimiento
Se utiliza básicamente para metales ferrosos. El metal se calienta a una temperatura predeterminada y luego se enfría rápidamente colocando el metal calentado en el tanque lleno de agua. También se puede enfriar al aire para endurecer el metal. Aumenta la dureza y la resistencia del metal pero al mismo tiempo aumenta la fragilidad del metal.
Cuando el acero se calienta, sus propiedades cambian, como el aumento de la dureza y la fragilidad, lo que es más importante para la aplicación práctica. Cuando el metal se calienta, se expande y, al enfriarse, su forma se contrae. Durante el enfriamiento del metal, se establecen tensiones internas. Entonces, el metal se templa una vez que la dureza se realiza en la superficie del metal para aliviar las tensiones internas y reducir la fragilidad. En el templado, el metal de proceso se calienta a una temperatura específica y permite el enfriamiento en el aire quieto. La temperatura de templado es más baja que la temperatura de dureza.
El endurecimiento por inducción es un proceso de tratamiento superficial utilizado para endurecer la superficie de los componentes de acero y aleaciones. Las piezas metálicas se colocan dentro de la bobina de cobre refrigerada por agua.
Esta bobina de cobre está conectada a la corriente alterna. Se suministra corriente a la bobina de cobre y las partes metálicas se calientan por encima de la temperatura de transformación. En este proceso, la parte central del metal no se ve afectada por el calor. La parte se mantiene dentro de la bobina de cobre enfriada con agua hasta que se logra la profundidad de dureza deseada. Una vez que se logra la dureza, se enfría en el aceite o en algún otro medio, según el material y la dureza requerida.
Proceso de tratamiento especial
1. Sinterización
La sinterización es un proceso de tratamiento térmico; se aplica a un compacto de potencia para impartir la fuerza y la integridad del material. El metal se calienta por debajo de la temperatura de fusión del material que evita la licuefacción. El proceso de sinterización reduce la porosidad del material y mejora las propiedades del metal, como la resistencia, la dureza, la conductividad térmica, etc.
Esta es la introducción básica del proceso de tratamiento térmico. Si tiene alguna consulta sobre este artículo, pregunte comentando. Si te ha gustado este artículo, no olvides compartirlo en las redes sociales. Suscríbase a nuestro sitio web para obtener más artículos informativos. Gracias por leerlo.
Proceso de manufactura
- ¿Qué es el tratamiento térmico? - Proceso y métodos
- ¿Qué es el mantenimiento de aguas residuales?
- ¿Qué es la madera tratada térmicamente?
- ¿Qué es un número de calor?
- Beneficios del tratamiento térmico al vacío en punzones y matrices
- Tratamiento térmico para metales:lo que necesita saber
- Comprensión del tratamiento térmico de solución, recocido, nitruración
- Proceso de tratamiento térmico del acero.
- 3 etapas del proceso de tratamiento térmico
- Tratamiento térmico de aluminio y aleaciones de aluminio
- Tratamiento térmico de cobre y aleaciones de cobre.