Los 4 mayores errores de diseño para el moldeo por inyección
Muchas empresas recurren a los servicios de moldeo por inyección para producir de forma rentable un gran volumen de piezas idénticas. El moldeo por inyección de plástico consiste en fundir termoplásticos en un barril calentado antes de inyectar el material fundido en un molde de metal preciso y duradero a través de una boquilla presurizada. Una vez que el material se ha enfriado y endurecido, se expulsa la pieza y se repite el proceso. Las empresas utilizan este proceso de fabricación para producir de todo, desde carcasas para dispositivos electrónicos hasta botellas de agua.
El moldeo por inyección es un proceso complejo y un error puede causar fallas cosméticas, comprometer la integridad del producto y dar lugar a costosos rediseños. La buena noticia es que la mayoría de estos problemas se pueden evitar siempre que siga las mejores prácticas de diseño. Estos son 4 de los errores más comunes que debe tener en cuenta al diseñar una pieza para moldeo por inyección.
4 de los errores de moldeo por inyección más comunes y cómo solucionarlos
1. Diseño con muescas
Un socavado es cualquier superficie rebajada, protuberancia, ranura, voladizo, rosca, encaje a presión u otra característica que impide que una pieza salga expulsada de su molde. Las socavaduras pueden generar mayores costos de fabricación, complejidad de las piezas y requisitos de mantenimiento del molde, por lo que es mejor eliminar cualquier socavación potencial siempre que sea posible.
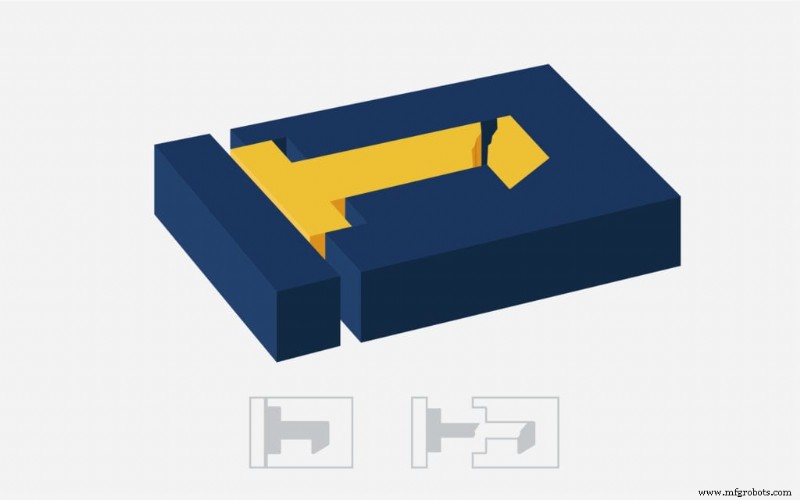
Si tiene un socavado que es esencial para el diseño de su pieza, hay algunas formas de mejorar la expulsión de la pieza. Reorientar las características problemáticas para que queden paralelas a la línea de dibujo es una solución rentable. Esto permite que la pieza sea expulsada sin sufrir daños, eliminando la socavación. Si tiene piezas con muescas internas o caras sin ángulos de desmoldeo, también puede usar elevadores para facilitar el proceso de expulsión. Es posible que pueda formar características socavadas mediante un diseño inteligente de orificios y ranuras en la pieza, en los que nuestros ingenieros de Fast Radius pueden guiarlo.
2. Tener espesor de pared no uniforme
Tener un espesor de pared uniforme ayuda a que el plástico fundido fluya a través de la cavidad del molde en una sola dirección, lo que permite que el material llene la cavidad con mayor precisión. Sin embargo, dado que las paredes más delgadas se enfrían más rápido que las paredes más gruesas, las variaciones en el grosor de la pared pueden causar hundimientos, deformaciones, tiros cortos y más.
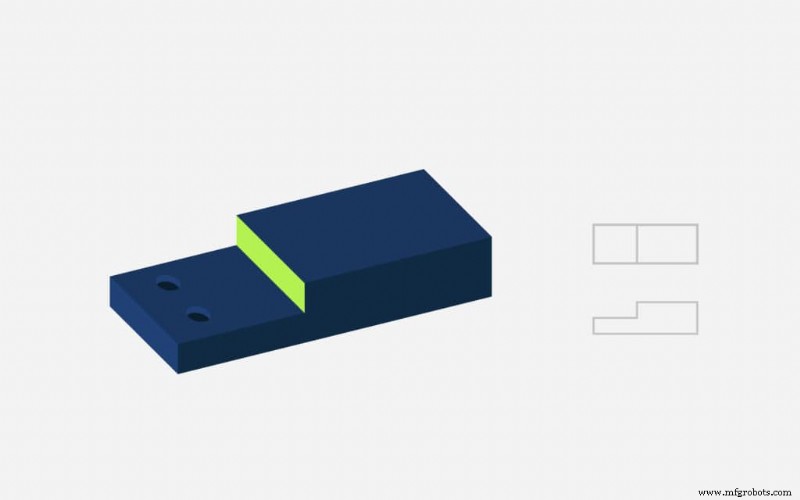
Para evitar estos problemas y asegurarse de que todas las áreas de su pieza se enfríen al mismo ritmo, utilice espesores de pared uniformes. Los espesores de pared entre 1,2 mm y 3 mm son los mejores en la mayoría de los casos. Si debe tener paredes de distintos grosores, debe:
- Haga que la transición entre secciones delgadas y gruesas sea lo más gradual posible — La mejor práctica de diseño es usar núcleos y nervaduras en lugar de cambiar el grosor de la pared o minimizar los cambios cuando sean necesarios.
- Utilice el grosor correcto de la costilla y el saliente — Las nervaduras y las protuberancias no deben exceder del 40 al 80 % del espesor de la pared de la base con un radio de la base del 25 al 40 % del espesor de la pared.
- Eliminar el plástico de las zonas más gruesas — Esto se denomina perforación y puede ayudar a mantener uniformes las secciones de la pared.
3. Olvidando los ángulos de inclinación
Agregar tiro, una ligera conicidad a cada superficie vertical de la pieza, es esencial para una expulsión suave. Una pieza diseñada sin tiro puede adherirse al molde, y la falta de tiro también puede causar líneas de arrastre antiestéticas si las paredes verticales de la pieza rozan contra el molde de metal durante la expulsión. Al agregar una conicidad suave, puede proteger su pieza contra la fricción, garantizar un acabado uniforme y reducir el desgaste, las roturas y las deformaciones durante la expulsión.
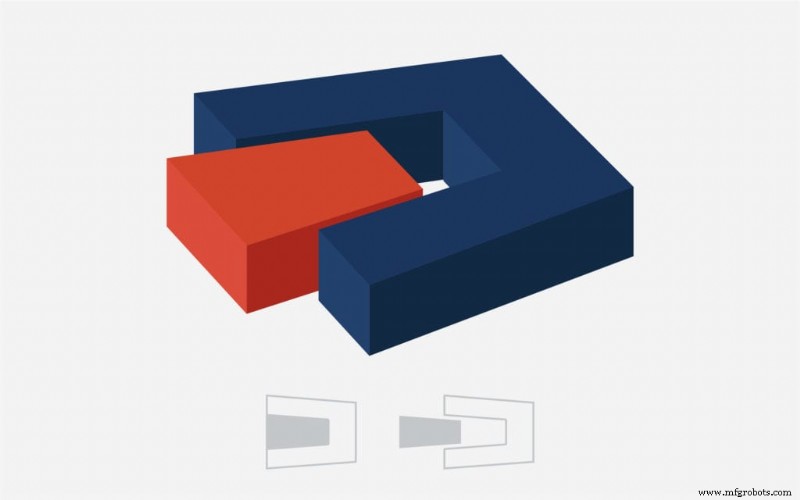
Los grados del ángulo de inclinación dependen de varios factores, desde el grosor de la pared hasta la textura de la superficie. Deberá considerar la tasa de contracción del material, la función de uso final de la pieza y la profundidad de dibujo para determinar el ángulo de inclinación correcto, por lo que es mejor conectarse con un socio de fabricación experimentado para obtener una evaluación precisa. Como regla general, debe usar al menos 1,5 a 2 grados de inclinación y agregar 1 grado por cada pulgada de profundidad de la cavidad. Si su pieza tiene una superficie muy texturizada, es posible que necesite ángulos de inclinación de 5 grados para evitar líneas de arrastre.
4. Incluyendo esquinas afiladas
Los bordes afilados y las esquinas no solo requieren más presión para llenarse, sino que a menudo hacen que las piezas se adhieran al molde durante la expulsión. Dado que las esquinas afiladas también dificultan que las granallas fluyan a través de los moldes, pueden generar vacíos o áreas donde las burbujas de aire quedan atrapadas. Estos pueden causar daños estéticos, aumentar la concentración de tensión y provocar fallas en las piezas, por lo que es importante redondear los bordes y las esquinas internos y externos siempre que sea posible.
Cuando diseñe esquinas, recuerde modelar sus esquinas para que tengan un grosor de pared uniforme. Eso significa que las esquinas internas se redondean al 50 % del grosor de la pared y las esquinas externas al 150 %.
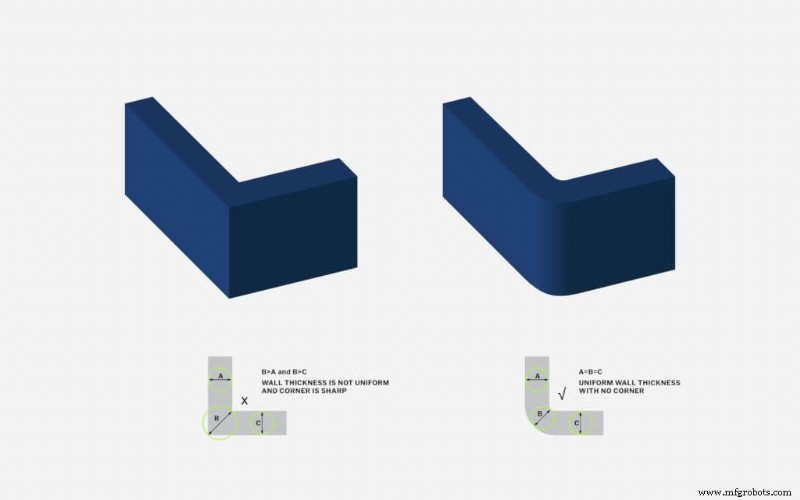
Evite defectos en piezas moldeadas por inyección con Fast Radius
Los errores de diseño de moldeo por inyección pueden retrasar la producción semanas, aumentar los costos y dar como resultado piezas deficientes o incluso inutilizables. Tomarse el tiempo para tomar decisiones de diseño reflexivas al comienzo de su proyecto es esencial y le ahorrará tiempo y dinero a largo plazo. Sin embargo, hay mucho que tener en cuenta, por lo que trabajar con un socio experimentado en moldeo por inyección como Fast Radius puede ayudarlo a obtener el diseño correcto la primera vez.
Cuando se asocie con Fast Radius, obtendrá acceso a nuestro equipo de ingenieros, asesores y expertos en diseño que pueden ayudarlo durante todo el proceso de fabricación. Ya sea que necesite ayuda para incorporar sutilmente el borrador en su diseño o para decidir un grosor de pared adecuado, Fast Radius puede ayudarlo a diseñar la mejor pieza posible. Contáctenos hoy para comenzar con el diseño de su próximo proyecto de moldeo por inyección.
¿Quieres saber más? Consulte nuestro centro de recursos para obtener más información sobre la selección de materiales, cuándo usar un molde de una sola cavidad o de varias cavidades, y más.
¿Listo para fabricar tus piezas con Fast Radius?
Inicia tu cotizaciónTecnología Industrial
- ¿Cuáles son los errores comunes que se deben evitar al diseñar para la fabricación?
- ¿Por qué el diseño del ángulo de salida es esencial para el moldeo por inyección?
- Materiales para moldeo por inyección de reacción (RIM)
- Consejos de diseño para moldeo por fundición
- Diseño de puertas de moldeo por inyección:una guía definitiva para la fabricación de plástico
- Ángulo de inclinación para moldeo por inyección:guía de diseño y prácticas recomendadas
- La importancia del espesor de pared uniforme en el moldeo por inyección [Guía]
- Por qué necesita el diseño para la fabricación en moldeo por inyección
- Opciones de materiales para moldeo por inyección
- Consejos y trucos de diseño de moldeo por inyección de pared delgada
- Las limitaciones del moldeo por inyección de bajo volumen