5 consideraciones de pulido para mejorar el acabado superficial
Se puede mejorar el acabado de la superficie haciendo ajustes en uno o más de estos puntos:parámetros operativos, rectificado de ruedas, tamaño de grano, suministro de refrigerante y estado de la máquina.
El rectificado de producción CNC de precisión brilla cuando las piezas requieren tolerancias geométricas estrictas y acabados superficiales de calidad. Típicamente, los acabados superficiales en el rango de 32 micropulgadas Ra hasta tan solo 4,0 micropulgadas Ra y mejores son los números que se necesitan lograr. Comparativamente, una operación tradicional de fresado o torneado podría lograr un acabado de alrededor de 125 micropulgadas a 32 micropulgadas Ra.
Si el objetivo es mejorar el acabado de la superficie actual de 20 micropulgadas Ra a 17 micropulgadas Ra, simplemente aumentar la velocidad de la rueda y/o reducir ligeramente la velocidad de alimentación podría ser suficiente. Sin embargo, si se requiere un acabado superficial más fino, se deben abordar estos cinco factores.
1) Parámetros operativos de molienda
Ajustar los parámetros de rectificado puede ser la solución más fácil y rápida para mejorar el acabado superficial de una pieza. Estos son los parámetros clave y las acciones recomendadas para hacerlo con éxito.
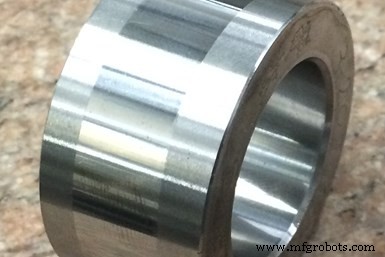
Esmerilado superficial/alimentación lenta:
- Aumente la velocidad de la rueda. Este es un buen punto de partida. Sin embargo, asegúrese de que la rueda esté clasificada para funcionar a la nueva velocidad. La velocidad máxima de funcionamiento (MOS) se indicará en el costado de la rueda.
- Reducir la velocidad de avance.
- Reduzca la profundidad de corte.
- Aumente el número de pases de arranque.
Esmerilado de diámetro externo (OD)/diámetro interno (ID):
- Aumente la velocidad de las ruedas. Como se mencionó anteriormente, la rueda debe estar calificada para funcionar a la nueva velocidad. La velocidad operativa máxima se indicará en el costado de la rueda.
- Reduzca la profundidad de corte por revolución.
- Reduzca la velocidad de trabajo (rpm):es posible que sea necesario ajustar la velocidad de avance para mantener la profundidad por revolución.
- Aumente el tiempo de permanencia/desconexión.
- Utilice la oscilación (una práctica común en el rectificado de diámetro interior por inmersión).
Muchas rectificadoras hoy en día tienen controladores de velocidad variable, por lo que se puede cambiar la velocidad de la rueda simplemente editando el programa CNC o ajustando el controlador de velocidad del husillo. Otras máquinas pueden requerir el cambio manual de poleas y correas.
La reducción de las tasas de avance también se puede llevar a cabo editando el programa CNC o ajustando el control de la tasa de avance. Sin embargo, este enfoque puede aumentar el tiempo del ciclo, lo que no siempre es una buena opción, particularmente en una operación de producción donde el tiempo del ciclo es crítico. En aplicaciones donde el tiempo de ciclo no es crítico, reducir la velocidad de avance puede ser una buena opción para mejorar el acabado de la superficie de la pieza de trabajo.
Cuando se aumenta la velocidad del disco y se reducen la profundidad de corte y la velocidad de avance, el disco puede desafilarse. Esto aumenta la posibilidad de daño térmico a la pieza de trabajo y puede aumentar las fuerzas de rectificado. Por lo tanto, se debe tener cuidado al ajustar estos parámetros para no introducir otros problemas en el proceso.
2) Revestimiento de muela abrasiva
Las condiciones de preparación para muelas abrasivas convencionales y superabrasivas se pueden manipular para ayudar a mejorar el acabado de la superficie. Por lo general, esto se logra disminuyendo la velocidad transversal del rectificado y/o reduciendo la profundidad por pasada durante el rectificado. La reducción de la profundidad del rectificado hace que la acción del rectificado sea menos agresiva y da como resultado una cara de la muela más suave, lo que generalmente mejora el acabado de la superficie de la pieza de trabajo. La reducción de la velocidad transversal del vestido reduce el avance del vestido, que es la distancia que recorre la rueda en una rotación de la rueda. El cable de preparación se puede aplicar a cualquier proceso de preparación en el que la herramienta de preparación atraviesa la cara de la rueda. Sin embargo, el cable de preparación no se aplica a las operaciones de preparación por inmersión. Ajustar el plomo es una buena manera de mejorar el acabado superficial en los procesos existentes.
Lo mejor es calcular la relación de superposición del diamantado (que tiene en cuenta el ancho del diamantado) al desarrollar un nuevo proceso o cambiar el tipo de herramienta de diamantado. La relación de superposición es la cantidad de veces que cualquier punto en la cara de la muela abrasiva entrará en contacto con la cara de la rectificadora a medida que la rectificadora se mueve por la rueda (Tabla 1).
La relación de superposición del revestimiento determina la condición de la superficie de la cara de la rueda. Esto, a su vez, determina la rugosidad de la superficie de la pieza de trabajo. Cuando aumenta la relación de superposición, la pulidora golpea la misma arena en la rueda más veces, creando una fina topografía en la superficie de la rueda. Esto hace que la cara de la rueda se vuelva desafilada y cerrada, lo que da como resultado un acabado superficial más fino en la pieza de trabajo.
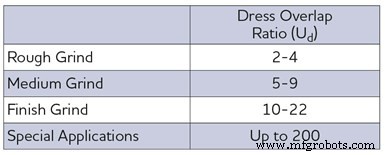
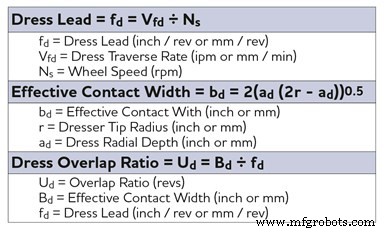
Sin embargo, se debe tener cuidado para asegurarse de que la cara de la rueda no esté demasiado cerrada después de un pulido muy fino. Una cara de muela cerrada puede dar como resultado una mayor potencia de esmerilado debido a que la superficie de la muela está desafilada y podría causar daño térmico a la pieza de trabajo. La Tabla 2 muestra las ecuaciones para determinar la relación de adelanto y superposición.
3) Composición de la muela abrasiva:tamaño de grano
El tamaño del grano de la muela abrasiva tiene un efecto directo en el acabado de la superficie. Cuanto mayor sea el tamaño del grano, más grueso será el acabado. Es importante seleccionar el tamaño de grano correcto según los requisitos de acabado de la pieza de trabajo. La Tabla 3 muestra los tipos de grano, tamaños y sugerencias para varios requisitos de acabado.
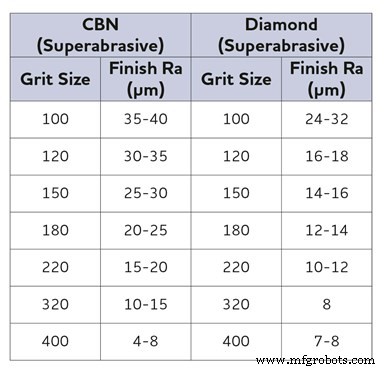
Antes de realizar un cambio en el tamaño del grano, se recomienda repasar la rueda con parámetros menos agresivos. Reducir el tamaño del grano probablemente signifique que será necesario reducir las tasas de alimentación y, como resultado, los tiempos de ciclo podrían aumentar. Los tamaños de grano más pequeños no pueden eliminar material a una tasa de eliminación tan alta como los tamaños de grano más gruesos. Además, se pueden inducir daños térmicos en una pieza de trabajo cuando se utilizan tamaños de grano más pequeños.
La composición de una muela abrasiva convencional incluye el tipo y el tamaño del abrasivo, la estructura de la muela (separación de granos), el grado (dureza de la unión) y el tipo de unión. La composición de una muela abrasiva superabrasiva incluye el tipo y el tamaño del abrasivo, la concentración del abrasivo y el tipo y grado de unión. Los abrasivos convencionales incluyen óxido de aluminio, carburo de silicio y abrasivo cerámico; y los superabrasivos incluyen diamante y nitruro de boro cúbico (cBN).
Antes de pedir una rueda con un tamaño de grano más pequeño, se recomienda ponerse en contacto con un fabricante/distribuidor de ruedas abrasivas para encontrar la mejor composición de rueda para una aplicación.
4) Suministro de refrigerante
Si la aplicación de refrigerante es insuficiente, las virutas de rectificado pueden volver a introducirse en la zona de rectificado. Las virutas pueden causar rayones en la pieza de trabajo, lo que a menudo se experimenta en el rectificado de interiores. Es fundamental asegurarse de que la boquilla de refrigerante esté dirigida correctamente hacia la zona de esmerilado y que haya suficiente flujo de refrigerante y presión para eliminar las virutas del área. Apuntar con precisión a toda la zona de esmerilado puede ser clave para lograr un acabado superficial uniforme en toda la pieza. En algunos procesos de alta tasa de eliminación, puede ser necesario ajustar la presión del refrigerante para que coincida con la velocidad de la rueda para evitar quemar la pieza. Esto también ayuda a eliminar las virutas de la zona de pulido.
Las virutas también pueden adherirse a la muela, en algunos casos. Esto puede suceder en un esmerilado más agresivo o cuando se esmerilan ciertos metales que tienden a adherirse a la muela abrasiva. En estas aplicaciones, es posible que sea necesario implementar boquillas de depuración. Las boquillas depuradoras suelen ser dispositivos de alta presión (500-1000 psi) y bajo índice de flujo que se dirigen después de la zona de esmerilado para eliminar las virutas de la estructura de la rueda.
Sin embargo, es poco probable que las boquillas depuradoras sean la respuesta para el esmerilado interior debido a la cantidad limitada de espacio en el orificio de la pieza. En estos casos, se debe usar refrigerante de inundación. Sin embargo, para el diámetro exterior y el rectificado superficial/de avance lento, las boquillas depuradoras a menudo se pueden implementar sin interferir con la pieza o los accesorios.
Un filtrado deficiente del refrigerante también puede afectar negativamente el acabado de la superficie y/o causar rayones en la superficie de la pieza. Si las partículas no se filtran, se pueden bombear de regreso a la zona de molienda junto con el refrigerante. Cuando se sospecha que el filtrado es la causa de los rayones y el mal acabado, es posible que se deba usar un filtro de micrones más pequeños. Una regla general para el pulido de carburo, por ejemplo, es usar un filtro que filtre partículas, como mínimo, más grandes que el 10 % del tamaño de grano de la rueda (consulte la Tabla 4).
Ampliar Ampliar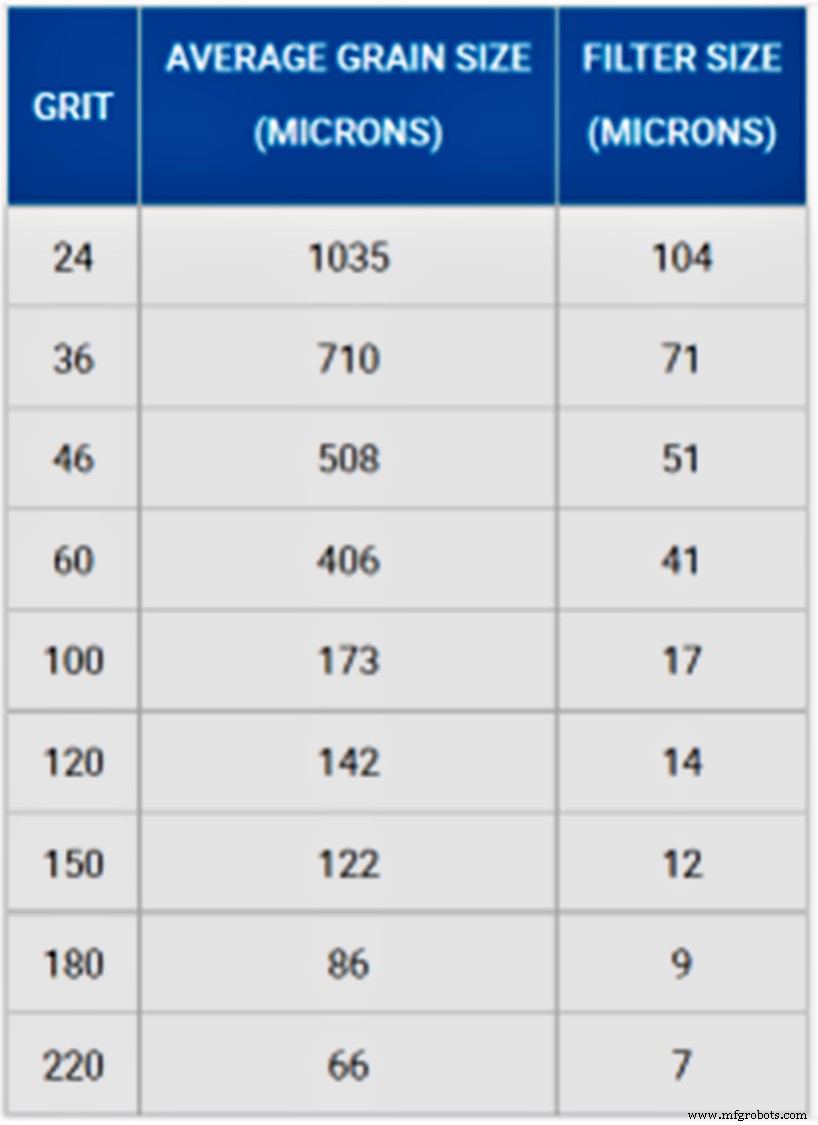
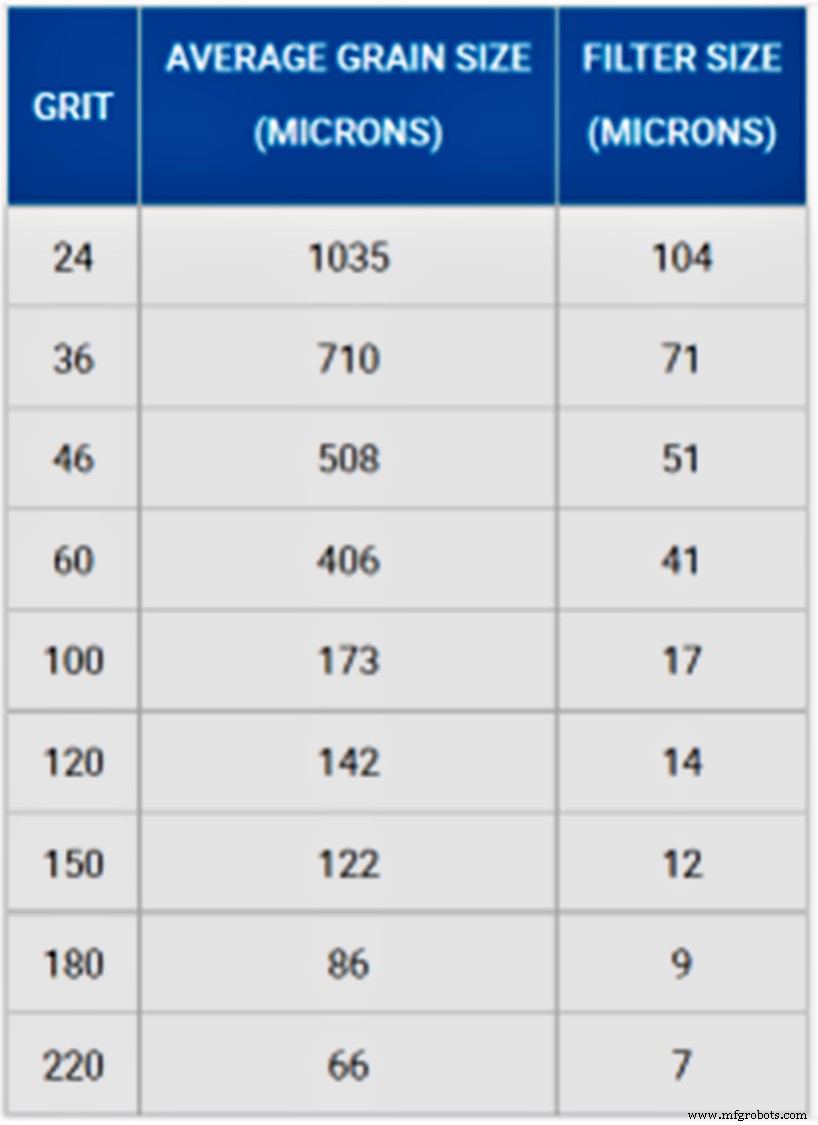
El tipo de refrigerante también puede influir en el acabado de la superficie, por lo general, debido al impacto de la lubricidad en el desgaste de la rueda. El refrigerante de aceite puro generalmente promueve un menor desgaste de las ruedas y, por lo tanto, un acabado superficial más consistente.
5. ESTADO DE LA MÁQUINA
Los factores relacionados con la máquina rectificadora pueden afectar el acabado de la superficie de la pieza de trabajo. Estos incluyen:
Equilibrio del conjunto rueda/cubo: Si el conjunto de la muela abrasiva no está equilibrado a un nivel aceptable, puede provocar vibraciones y/o un acabado superficial deficiente. El equilibrado se puede realizar utilizando equipos como un equilibrador estático, un equilibrador dinámico/manual o un equilibrador automático montado en la máquina. La precisión requerida de la pieza de trabajo y el acabado de la superficie determinarán el tipo de equipo que se utilizará.
Los sistemas de balanceo automático que se montan directamente en el husillo de rectificado son la mejor opción de balanceo. Este sistema mueve automáticamente los pesos dentro de un buje para contrarrestar el desequilibrio rueda/buje. Los balanceadores automáticos están limitados a máquinas de mayor tamaño, como las máquinas de avance lento y de tipo OD y, por lo tanto, no son prácticas para ruedas de diámetro pequeño.
El siguiente mejor método para equilibrar es el sistema de equilibrado de tipo dinámico/manual, que se puede utilizar en todo tipo de máquinas. Equilibra el conjunto rueda/cubo directamente en la máquina pero requiere el movimiento manual de los pesos de equilibrio.
Finalmente, el equilibrado estático, que se realiza fuera de la máquina, tiene sus limitaciones en cuanto a los niveles de equilibrado que puede alcanzar. Sin embargo, es mejor que no equilibrar y, en algunas aplicaciones, funciona bien.
Dicho esto, no todas las ruedas requieren equilibrio. Algunas ruedas pequeñas que tienen poca masa no tienen el peso necesario para crear un desequilibrio problemático. Por lo tanto, a menos que estas ruedas pequeñas funcionen a velocidades muy altas o si la máquina o el sistema (cápsula) no está rígido, no es necesario equilibrarlo. Además, es posible que las ruedas utilizadas para aplicaciones de menor precisión o de desbaste no requieran balanceo.
Rigidez de la máquina: La rigidez deficiente de la máquina puede provocar una calidad deficiente de la pieza de trabajo. Con el tiempo, los cojinetes del husillo pueden desgastarse y aflojarse. Los rodamientos también pueden dañarse si la máquina se ha estrellado. Siempre que sea posible, los cojinetes del husillo deben revisarse de forma periódica o continua utilizando un equipo de análisis de vibraciones. Este equipo es una gran herramienta para ayudar a predecir los problemas que se avecinan con los cojinetes del husillo que podrían resultar en una pieza de trabajo de mala calidad. Los métodos de fijación y fijación deficientes también pueden provocar vibraciones o desviaciones y, en última instancia, un acabado superficial deficiente.
Sistema de vendaje: El pulido correcto de la rueda es fundamental para lograr un buen acabado superficial, por lo que el sistema de pulido debe estar en buenas condiciones. Las herramientas estacionarias deben reemplazarse si están dañadas o desgastadas. Las herramientas rotativas, como el husillo de rectificado, deben revisarse en busca de vibraciones, descentramiento y movimiento excesivos.
Mantenimiento de máquinas herramienta: Es crucial seguir las instrucciones del proveedor de la máquina herramienta para la lubricación programada de la máquina, el control de la calidad del aire comprimido, la frecuencia de cambio de filtro, etc. Se deben inspeccionar los cubos de las ruedas y los árboles en busca de daños, así como los accesorios, las lunetas, los centros del contrapunto, etc. La inspección de estos componentes de la máquina debe ser parte de la rutina diaria de mantenimiento preventivo de un taller.
Además del mantenimiento regular, muchas empresas ahora están implementando programas de mantenimiento como el monitoreo basado en condiciones (CBM), mediante el cual la máquina es monitoreada por sensores, como acelerómetros, medidores de temperatura, manómetros, etc. Este mantenimiento predictivo utiliza los datos recopilados de los sensores para establecer tendencias, predecir fallas y ayudar a determinar cuándo es necesario cambiar componentes como los cojinetes.
Aparecido anteriormente en el blog de Norton.
Tecnología Industrial
- Teoría de la muela abrasiva | Metales | Industrias | Metalurgia
- Tipos de acabados superficiales para productos moldeados
- De principio a fin:los fundamentos de la medición de superficies
- Indicadores de acabado de superficie personalizados para lugares de difícil acceso
- Acabado superficial de microfundición
- Rectificado de superficies a la antigua usanza
- Introducción a la amoladora de superficie PLC
- ¿Qué es un acabado de superficie de mecanizado estándar?
- 9 consejos para evitar problemas de acabado superficial de última hora
- Principios de los servicios de rectificado de superficies de precisión
- Inserto de torneado CNC DCMT para el mejor acabado superficial