La digitalización aumenta la producción de celdas de autopartes en un 20 %
Los aumentos en el tamaño y la cantidad de sus pedidos llevaron al fabricante de autopartes Felss Rotaform LLC (New Berlin, WI) con sede en Wisconsin a expandir sus operaciones a través de una nueva celda de atención de máquinas de doble robot. La empresa es un proveedor de piezas de precisión utilizando sus procesos de estampación rotativa, formación axial y formación de extremos de tubos. Para cumplir con los objetivos de mejora continua de procesos de la empresa, la nueva celda tenía que ser más segura, rápida y flexible que sus celdas de fabricación anteriores.
Para abordar la naturaleza compleja de la automatización, la empresa se puso en contacto con Siemens y el integrador de sistemas IAS Inc. (New Berlin, WI) debido a su trayectoria en innovación y experiencia en robótica integrada y tecnologías de control. Seis meses más tarde, Felss Rotaform se encontró operando una célula de fabricación integrada y digitalizada que batía los récords de productividad y rentabilidad de la empresa.
Mientras revisaba los requisitos para su celda robótica de próxima generación, Felss Rotaform tenía varios objetivos. En primer lugar, quería aumentar la productividad mediante la implementación de nuevos PLC de alta velocidad para lograr tiempos de respuesta de ciclo completo más cortos para cada pieza individual.
En segundo lugar, quería explorar una solución de seguridad más avanzada que garantizara un mejor control de quién ingresaba a la celda. En las celdas más antiguas, una máquina podría encenderse accidentalmente cuando una persona de mantenimiento estaba presente en la celda, poniendo a esa persona en riesgo de sufrir lesiones. Para evitar esto, Felss Rotaform quería un proceso automatizado para garantizar que la celda estuviera vacía una vez que se reiniciara.
En tercer lugar, quería más flexibilidad para los cambios de celdas, lo que permitiría a la empresa probar y ofrecer una gama de productos más diversa para sus clientes. Las celdas más antiguas requerían que se reprogramara toda la celda cada vez que se realizaba un nuevo proceso, lo que podía demorar días en ejecutarse.
El objetivo inicial de Felss Rotaform era un tiempo de respuesta de ciclo completo de 48 segundos para cada pieza en la nueva celda (mucho más rápido que cualquiera de sus celdas más antiguas). El diseño y la implementación de la solución aceleraron el proceso completo de producción de piezas hasta en 38 segundos, una mejora de la eficiencia del 20 %. Una vez que se implementó la nueva celda, el tiempo de inactividad pasó de días a horas para cambios complejos y, para cambios programados típicos, lo que antes tomaba ocho horas ahora solo toma 15 minutos, según Chad Due, ingeniero de controles eléctricos de Felss Rotaform.
“Esta nueva celda puede producir en dos turnos lo que antes se necesitaban tres. Esto nos permite producir 600 piezas adicionales en un período de 24 horas. Además, la rentabilidad de la célula aumentó un 13%”, dijo Due.
Richard Parkhurst, gerente de cuentas de Siemens, sabía que IAS estaría en una posición sólida para lograr los objetivos de Felss Rotaform. “Algunos integradores realizan estrictamente el desarrollo de software y otros están más capacitados para construir y ensamblar el hardware. IAS aportó una combinación de todas las habilidades y conocimientos necesarios, incluidas las capacidades de robótica e ingeniería de seguridad”, dijo.
IAS reconoció que los productos de Siemens serían fundamentales para ayudar a Felss Rotaform a lograr sus objetivos al proporcionar la velocidad, confiabilidad, flexibilidad y seguridad requeridas. Por ejemplo, se diseñó una red troncal de comunicaciones digitalizadas Siemens PROFIsafe basada en Ethernet en la celda para controlar la seguridad de las máquinas y el perímetro. Se proporciona una comunicación segura entre los diversos PLC y robots. PROFIsafe transmite información de estado desde los dispositivos dentro de la celda al PLC principal y proporciona
una gran ventaja sobre la tecnología anterior porque tanto la comunicación estándar como la segura se realizan a través de un solo sistema de bus.
Todos los sensores y actuadores dentro de la solución PROFIsafe se pueden programar libremente dentro del concepto de seguridad distribuida, independientemente de su estación de E/S. Esta flexibilidad permite a los operadores apagar los actuadores de forma selectiva. Otras ventajas incluyen comunicaciones a prueba de fallas, diagnósticos avanzados y capacidades de intercambio en caliente, que ayudan a reducir el tiempo de inactividad.
Los PLC Siemens Simatic S7-1500 con interfaz Profinet integrada también desempeñaron un papel importante en el aumento de las velocidades operativas. El bus de backplane de alta velocidad, con su alta tasa de baudios y su eficiente protocolo de transmisión, brinda una ventaja de rendimiento crucial para el procesamiento rápido de señales.
Según Simon Vancina, ingeniero de aplicaciones de IAS y principal programador de robótica y PLC, “El PLC S7-1513F fue una gran elección para este proyecto debido a su velocidad, variedad de tarjetas de expansión de E/S disponibles, controlador de seguridad programable funcionalidad, factor de forma relativamente compacto y bajo costo”.
El TIA Portal de Siemens desempeñó un papel fundamental en el ahorro de tiempo y recursos de ingeniería al programar todos los PLC y HMI. El uso del TIA Portal reduce el tiempo de comercialización mediante herramientas de simulación, herramientas de productividad del programador y diagnósticos adicionales.
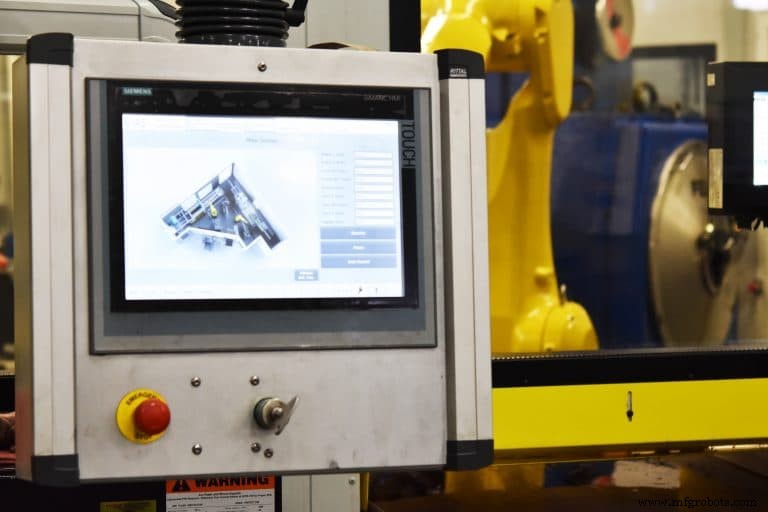
“TIA Portal me permite escribir código de la manera que quiero escribirlo y cambiar de un lenguaje de programación a otro cuando lo necesito”, dijo Vancina. “Por ejemplo, con TIA Portal podría elegir Ladder Logic para hacer que las secciones lógicas simples sean más fáciles de leer y luego, en la siguiente línea de código, cambiar a algo como Texto estructurado para implementar cálculos o controles de proceso más complejos. Casi todos los PLC permiten el uso de los diversos lenguajes de programación IEC 61131-3, pero TIA Portal le permite combinarlos de una manera única y efectiva. Esta es una característica muy conveniente que nos permite reducir nuestro tiempo de desarrollo de código y nos permitió tener este sistema en línea mucho más rápido”.
Con la implementación del proyecto, Felss Rotaform inmediatamente vio beneficios más allá de sus objetivos principales. Los grandes fabricantes de automóviles siempre buscan probar nuevos productos. Cuentan con sus proveedores para que los ayuden en el proceso de prueba. Los proveedores más receptivos en la fase de prueba a menudo son recompensados con nuevos negocios.
La nueva celda de fabricación de Felss Rotaform se diseñó teniendo en cuenta las pruebas de productos. Puede ejecutar seis números de pieza nuevos diferentes en una semana, lo que lleva un mes entero en otra celda.
La nueva celda también es mucho más avanzada en su capacidad para detectar piezas defectuosas. Para fabricantes como Felss Rotaform, la trazabilidad juega un papel clave en la reducción de los costos operativos. La celda puede ayudar a evitar que se envíen piezas defectuosas al detectar las piezas defectuosas y colocarlas en un contenedor separado, incluso detener la celda y alertar al operador si los defectos ocurren con demasiada frecuencia. Si se envía una pieza defectuosa y el cliente la encuentra, podría significar la devolución de un envío completo, lo que le costaría al proveedor cientos de miles de dólares.
IAS y Siemens actualmente están probando dos celdas robóticas similares que se implementarán en 2018 e incluirán un mejor seguimiento del mantenimiento para una fabricación digital más avanzada. El nuevo sistema rastrea cuánto tiempo ha estado funcionando una máquina e indica cuándo las partes críticas clave se acercan a sus umbrales de tiempo de ciclo proyectados.
Una solución que se está explorando es MindSphere, un sistema operativo abierto de Internet de las cosas (IoT) basado en la nube que sirve como una plataforma conectada con aplicaciones que brindan una variedad de funciones, como reducir los riesgos de seguridad y mejorar la disponibilidad de las máquinas y plantas conectadas.
Además, el nuevo sistema incorporará análisis predictivos para enviar una alerta sobre posibles problemas al control maestro de una celda. “El nuevo sistema te dice qué necesita ser reemplazado y qué tipo de pieza necesita el sistema. Escaneas la pieza antes de instalarla y te dice si es la pieza correcta para esa máquina”, dijo Vancina.
Para obtener más información de Siemens, visite www.siemens.com o llame al 847-640-1595; de IAS, vaya a www.iasworldwide.com o llame al 866-243-2402.
Sistema de control de automatización
- Ganadores del premio a la innovación automotriz SPE 2019
- Moldeo por inyección:Celda de robot simple para corte de puertas No necesita programación
- Creación de una mejor amortiguación:tecnología de transportadores en el núcleo de la celda de moldeo sin luces
- Renegade aumenta la producción de preimpregnados de fibra de carbono de alta temperatura
- Alltec se expande en el mercado norteamericano
- Digitalización de Instalaciones de Producción
- La torreta de acabado reduce el tiempo de ciclo
- La celda de torneado automatiza la producción de acoplamientos de aceite
- Producción de piezas de alto volumen
- Portal de pórtico adecuado para la producción en línea de piezas pequeñas
- El software mejora la precisión de las piezas impresas en 3D