Control basado en sensores de herramientas de corte, las máquinas herramienta pasan de la mesa de dibujo a la corriente principal
Un factor clave de éxito para las iniciativas de Industria 4.0 e IIoT (Industrial Internet of Things) es la aparición de más y mejores sensores en los centros de mecanizado, e incluso en las propias herramientas de corte. Estos sensores proporcionan los datos y la conectividad que son la base de la "fábrica del futuro".
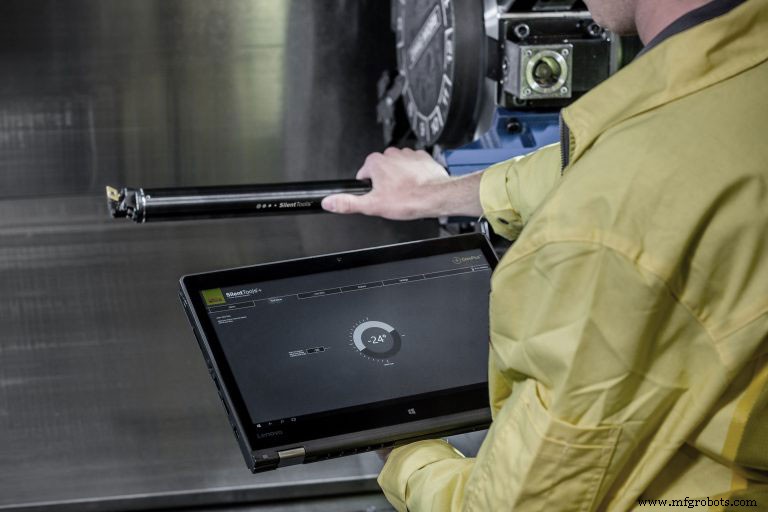
Pero, lejos de ser futurista, hay una gama de "sensores inteligentes" disponibles en la actualidad, que recopilan datos y muestran a los operadores el estado de sus máquinas y el proceso de corte de metales. La evolución se logra mediante la medición cada vez más precisa de la posición de la pieza y la forma geométrica de la pieza terminada, así como la configuración y control de las herramientas utilizadas en el proceso.
Manufacturing Engineering pidió a varios expertos de la industria que evaluaran el estado actual de los sistemas de control de corte basados en sensores y que también observaran la bola de cristal para ayudar a identificar futuras oportunidades.
Ahora y en el futuro
En el área de control y optimización basados en sensores, ¿dónde estamos en el continuo desde el tablero de diseño hasta los productos maduros? La respuesta a esa pregunta es:"Depende".
“Para la medición básica y el control adaptativo, estamos bien avanzados en la curva de aprendizaje”, dijo Frank Powell, gerente de producto para productos de molienda en Marposs Corp. (Auburn Hills, MI). “Las máquinas herramienta se pueden equipar con una variedad de sensores y transductores en proceso. En el primer nivel, estos sensores se utilizan para la protección de la máquina, ya que un sistema puede reaccionar 1000 veces más rápido que un operador ante una tensión de fuerza inesperada o una posible colisión. La tecnología avanza a través de la medición cada vez más precisa de la posición de la pieza y la forma geométrica de la pieza terminada, así como la configuración y control de las herramientas utilizadas en el proceso.”
En términos de Industria 4.0, la tecnología de fabricación digital de herramientas de corte está mucho más cerca de la mesa de dibujo que de un producto maduro, según Neil Munson, especialista en ventas técnicas de Silent Tools en Sandvik Coromant (Fair Lawn, NJ). “Estamos al borde de un cambio de paradigma en nuestra industria. De hecho, estamos dando el salto inicial hacia herramientas de corte inteligentes basadas en sensores en nuestra empresa”, dijo.
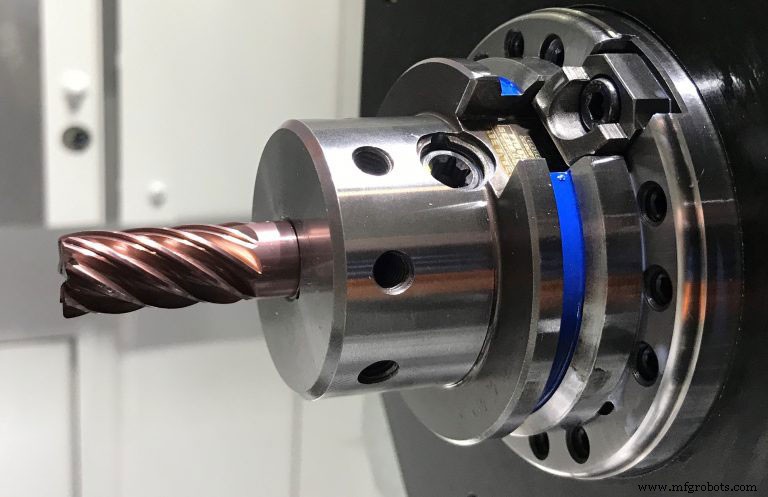
Joe Volansky de BadAxe Tooling Solutions tenía una opinión un poco diferente. “Los productos están probados y bien a lo largo de la curva de aprendizaje, y se pueden aplicar de formas revolucionarias”, dijo Volansky. “En nuestro caso, estamos introduciendo un producto para operaciones de fresado basado en ciencia comprobada, que presenta una solución de una forma completamente nueva al borde de la física de las máquinas”. BadAxe Tooling Solutions es una alianza de tres empresas estadounidenses:Briney Tooling Systems (Bad Axe, MI), Fullerton Tool Co. (Saginaw, MI) y BlueSwarf LLC (State College, PA).
“Mi opinión es que estamos en el medio de la curva en términos de desarrollo”, dijo Wade Anderson, gerente especialista en productos y gerente de Centros tecnológicos de Okuma America Corp. (Charlotte, NC). “Para la eficiencia básica del equipo y la capacidad de comunicarse con dispositivos periféricos, hay una serie de soluciones listas para usar listas para usar ahora mismo. Sin embargo, las tecnologías de inteligencia artificial (IA) y realidad aumentada (AR) son más prometedoras”.
Con la gran cantidad de datos que ahora se generan a partir de equipos en el taller, las tecnologías emergentes a las que se refiere Anderson son esenciales, según Andy Henderson, vicepresidente de ingeniería de Praemo (Kitchener, ON). "En el mundo de la automatización, ha habido una evolución muy 'física' desde la década de 1970", dijo Henderson. “La próxima frontera es la evolución 'mental':agregar inteligencia a los datos utilizando IA y aprendizaje automático (ML). En el continuo, estas tecnologías están maduras y se utilizan continuamente en los espacios personales y de consumo (Google, Amazon, Facebook, etc.). Las aplicaciones dentro de la industria manufacturera se han rezagado, pero el software que utiliza estas tecnologías, como Razor, está ayudando a los talleres a darse cuenta del valor de la IA y el ML”. Razor es un producto de Praemo que se conecta a fuentes de datos, recopila información y brinda información y recomendaciones sugeridas para ayudar a los usuarios a tomar medidas preventivas para reducir el tiempo de inactividad del equipo, optimizar los procesos de producción y administrar los riesgos.
¡Regla de los sensores!
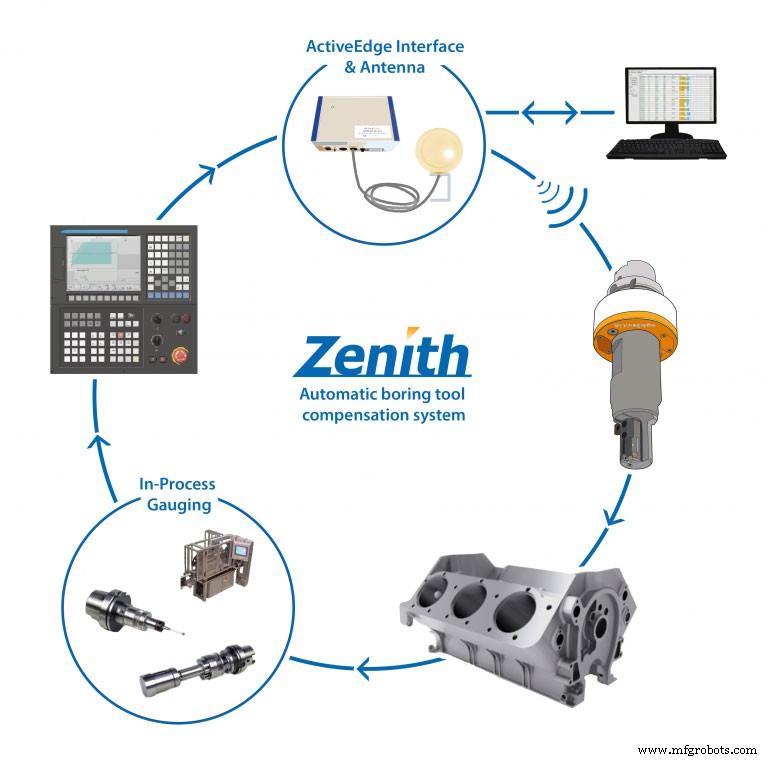
Todos nuestros expertos de la industria coincidieron en el papel clave que juegan los sensores. Hay un viejo adagio:"Lo que se mide, se gestiona". Aunque no se sabe quién lo dijo (algunos sugieren a Lord Kelvin, otros a Peter Drucker), subraya el hecho de que cualquier intento de controlar u optimizar una máquina debe basarse en datos rápidos, precisos y confiables en el punto de contacto clave, donde la herramienta de corte se encuentra con la pieza de trabajo.
Técnicamente hablando, la tecnología para recopilar, distribuir y analizar datos con éxito para el control adaptativo estaba disponible mucho antes del interés actual en la Industria 4.0 y el IIoT. Históricamente, los equipos de medición en proceso pueden remontar sus orígenes a más de 60 años (por ejemplo, el calibre de Mario Possati para verificar piezas durante el rectificado). Sin embargo, los principales avances en sensores han ocurrido mucho más recientemente.
Tecnología reciente
Uno de estos avances es una herramienta de perforación que compensa automáticamente el desgaste del filo de corte. “Independientemente de lo sofisticada que sea una máquina herramienta CNC, no puede compensar automáticamente el desgaste del filo de corte en una herramienta de perforación”, dijo Anthony Bassett, presidente de Rigibore Inc. (Mukwonago, WI). “Nuestra herramienta ActiveEdge alimentada por batería automatiza el dimensionamiento en proceso de los bordes de corte de la herramienta de mandrinado. Utiliza tecnología inalámbrica para ajustar de forma remota múltiples diámetros de filo de corte en una sola herramienta, optimizando el rendimiento del proceso y eliminando la necesidad de intervención del operador”.
Forjando en un nuevo territorio en el área de fresado está el sistema de software y ensamblaje BadAxe Smart Tool. BadAxe reemplaza el ensayo y error con la física para alcanzar de inmediato el "punto óptimo" de una máquina cuando se inicia, según la compañía. Usando mediciones de los patrones de frecuencia de vibración residentes para una combinación específica de máquina, husillo, portaherramientas y herramienta, los algoritmos y análisis patentados de la compañía calculan la zona de estabilidad óptima para que opere la máquina. Portaherramientas y herramienta preequilibrados y ensamblados, además de una interfaz de software optimizada para máquinas individuales.
“Todo el mundo sabe que la vibración y el traqueteo son los principales factores limitantes en el mecanizado de alta velocidad”, dijo Volansky de BadAxe. “Por lo general, los operadores usan prueba y error para encontrar el avance, la velocidad, el ancho de corte y la profundidad de corte correctos. En muchos casos, piensan que se han topado con la pared en términos de rendimiento cuando, en realidad, se encontraría una operación sin vibraciones en una configuración contraria a la intuición donde existen tasas de remoción de metal mucho más altas. Nuestro producto define esa configuración inmediatamente desde la puesta en marcha, independientemente del paso por encima, el corte de ranuras completas o las esquinas. Se ha demostrado que la tecnología subyacente aumenta significativamente el retorno de la inversión de un trabajo por parte de organizaciones como Boeing Phantom Works, el Departamento de Defensa de EE. UU. y otras”.
BadAxe está construyendo una gran base de datos para diferentes combinaciones de máquinas y ensamblajes. Si la máquina de un cliente no está en la base de datos, se puede realizar una prueba única para determinar su dinámica de configuración.
Sandvik Coromant está dando el paso de los sensores en el proceso a los sensores en la herramienta con la introducción de su sistema inteligente SilentTools+. herramientas de corte. “SilentTools+ son soluciones de herramientas antivibratorias que brindan una gran perspectiva de los procesos de mecanizado con voladizos largos en los que los operadores suelen estar a ciegas”, dijo Munson.
“El mecanizado con voladizo largo en una instalación de alta tecnología es un desafío porque [los operadores] quieren tener el control del proceso hasta la punta de corte”, dijo. “Tenemos sensores incorporados dentro de nuestras SilentTools que se comunican a través de Bluetooth con una interfaz gráfica para que un operador tenga ojos y oídos dentro de la máquina cerrada y en el interior de una perforación. Además, tiene una función que permite una configuración rápida y sencilla al determinar cuándo la punta de corte está en el centro”.
Con el sistema SilentTools+, la desviación de la herramienta, la vibración, las fuerzas de corte, la carga de la herramienta y la temperatura se controlan en tiempo real. "Debido al conocimiento de todas estas áreas, creemos que las tasas de desecho se reducirán y se obtendrán ganancias de productividad, lo que generará ahorros reales", agregó Munson.
¡Información por favor!
Si bien parte de la salida del sensor es solo para información, el valor agregado es cuando las señales del sensor se procesan y se usan para controlar la calidad de la pieza y la condición de la herramienta. Los fabricantes pueden minimizar las trayectorias de herramientas y el tiempo de mecanizado, mejorar el acabado de la superficie, maximizar la vida útil de la máquina y mecanizar de manera eficiente piezas más complejas, como aquellas con geometrías complejas, paredes delgadas, cilindros huecos y ejes delgados.
Anderson dijo:“El Sistema de Monitoreo de Okuma es un buen primer paso. Permite hasta 64 entradas diferentes que se pueden personalizar según las necesidades específicas del proceso. Tenemos clientes que han podido medir el tiempo de inactividad de la máquina y analizar los datos de OEE [efectividad general del equipo] para determinar que una cosa simple fue apagar la máquina cuando un operador estaba ocupado en otro lugar. Al usar el sistema de monitoreo, el operador [puede ser alertado] de que se avecina un problema potencial que se puede evitar con una acción preventiva”.
Henderson de Praemo cree que el camino hacia el éxito en la fabricación pasa, en última instancia, por la montaña de datos que generan las herramientas en las aplicaciones de corte de metales. "Estos datos son una 'materia prima' valiosa para la optimización", dijo. “Los algoritmos para analizar datos en nuestro software Razor pueden filtrar grandes cantidades de datos para encontrar interrelaciones y patrones que un humano con una hoja de cálculo nunca descubriría. Las tecnologías de IA y ML se utilizan para desarrollar modelos que ayudan a los operadores y gerentes a llegar a conclusiones claras muy rápidamente y a tomar medidas basadas en conclusiones basadas en datos. Si bien la inteligencia es artificial, imita muy de cerca la forma en que los humanos en el mundo de la fabricación abordan las cosas. La única diferencia es que no se ve abrumado por grandes cantidades de datos. Cuanto más tiempo se recopilen los datos, y cuantos más datos se recopilen, más aprenderá Razor”.
Habilidad comprobada
Los sistemas actuales han demostrado su capacidad para mantener el proceso de corte, anticipando cuando algo no está bien y notificando a un operador o a la máquina para que tome medidas correctivas, según Powell de Marposs. “La decisión de notificar solo o tomar acciones automáticas la dicta el cliente”, dijo. "Técnicamente, tenemos muchas capacidades de control automático que en algunos casos no se utilizan".
Un nuevo sistema de Marposs llamado BLÚ es el resultado de más de 50 años de experiencia en rectificadoras y otras máquinas herramienta. Combina todas las aplicaciones de control de procesos y monitoreo de máquinas herramienta en un solo sistema para monitoreo de procesos y herramientas en tiempo real, control adaptativo y mitigación de fallas con un tiempo de procesamiento y muestreo rápido. Powell dijo:"BLÚ está diseñado para integrarse casi a la perfección con la máquina herramienta para ayudar al operador en cualquier modo:configuración, manual o automático".
El corazón del sistema es un nodo maestro alojado dentro del gabinete de la máquina. Tiene una estructura de bus para conectar otros nodos para mediciones en la máquina, monitoreo de emisiones acústicas, balanceo de ruedas (esmerilado), retracción de herramientas y otras funciones.
El sistema Zenith es un sistema automático de circuito cerrado para operaciones de perforación, según Bassett de Rigibore. “Los sistemas tradicionales son puramente mecánicos sin retroalimentación continua a la máquina perforadora”, dijo. “Zenith proporciona retroalimentación al control de la máquina para confirmar que la herramienta se ha ajustado en la cantidad deseada. Esta retroalimentación del sensor de posición evita que se mecanice una pieza defectuosa”.
¿Hasta dónde puede llevarnos esta tecnología?
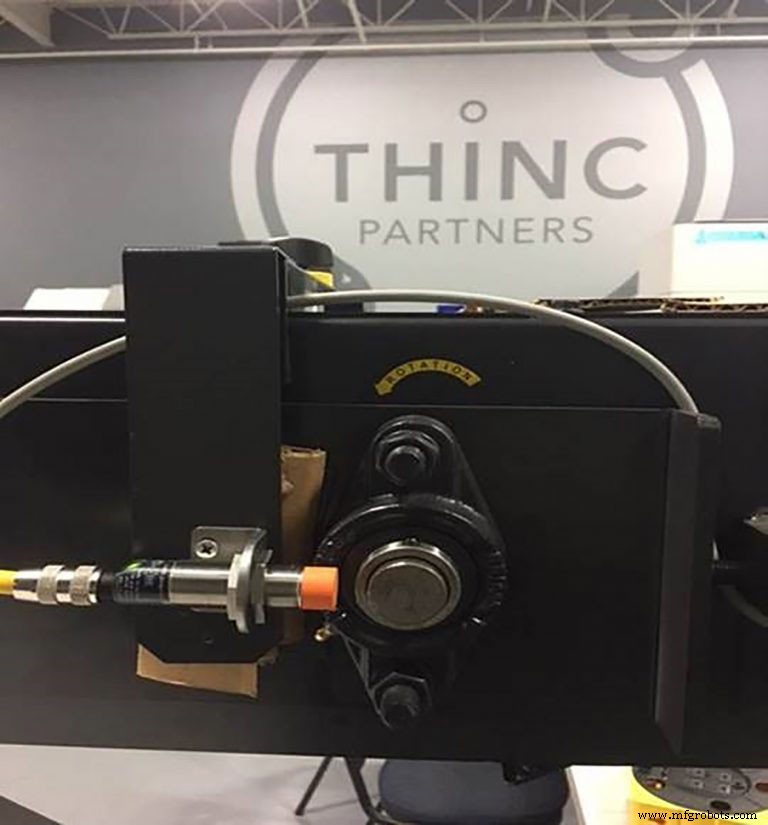
“No veo necesariamente un juego final para las soluciones de herramientas de corte digitales o basadas en sensores”, dijo Munson de Sandvik Coromant. “En los talleres de maquinaria y las instalaciones de fabricación modernas, los sensores y el uso de IIoT en las herramientas de corte se volverán más omnipresentes en los próximos cinco a 10 años, siguiendo el camino de las aplicaciones [de productos] de consumo. Para nosotros, la progresión natural es la integración de nuestras SilentTools+ en los controles de la maquinaria CNC. Hoy en día, es un sistema independiente con una vista de proceso en vivo. Estamos trabajando con fabricantes de máquinas-herramienta y socios de software CAM para pasar de un sistema independiente a control de máquinas e integración de procesos”.
Anderson de Okuma estuvo de acuerdo. “La tecnología y, lo que es más importante, la implementación de la tecnología generará nuevas tecnologías”, dijo. “Hace muchos años pensé que un espejo retrovisor con atenuación automática en un vehículo era ridículo. Ahora, no compraría un vehículo sin uno. De manera similar, en nuestra industria, las nuevas tecnologías ayudarán a desarrollar nuevos mercados para avances alternativos”.
Powell de Marposs estuvo de acuerdo en que nunca debería haber un final del juego. “Creo que existe la tecnología para monitorear todos los parámetros y variables clave”, dijo. “Ciertamente, hay áreas que se pueden mejorar, y estamos trabajando diariamente para desarrollar sensores que sean más rápidos y sensibles, y software que pueda procesar los datos de los sensores de manera más rápida e inteligente. Dentro de 10 años, estoy seguro de que habrá al menos un cambio de juego, un avance técnico que hará que un taller de máquinas sea más eficiente y productivo. Cuando el juego cambie, nosotros cambiaremos con él”.
Volansky de BadAxe cree que su compañía tiene un cambio de juego en este momento. “El ritmo de desarrollo está aumentando”, dijo. “Los clientes no quieren esperar cinco o diez años. Tenemos un producto que redefine la eficiencia y ayuda a las máquinas herramienta a operar en los límites de la física. Sin embargo, el siguiente paso para nosotros será eliminar nuestro conjunto de herramientas de la ecuación incorporando nuestra detección de vibraciones y análisis de datos patentados directamente en la máquina y su lógica”. De esta manera, la máquina solo funcionará en su estado más optimizado, sin que el operador tenga que probar y error, agregó.
Como dijo Bassett de Rigibore:“Algunos objetivos de desarrollo para nosotros son el pedido automático de herramientas de carburo utilizando el control CNC, un cambio hacia una menor intervención de los operadores, ajustes realizados desde una ubicación central y la entrada de un modelo sólido en la máquina CNC mientras otro proceso está en funcionamiento. Los principales límites a los que nos enfrentamos hoy en día son la incompatibilidad y la falta de estándares entre los diferentes fabricantes de máquinas CNC y fabricantes de controladores de máquinas”. Al final, un enfoque patentado limitará el crecimiento y, en última instancia, es más costoso para un cliente que desea agregar fácilmente nuevas funciones, concluyó Bassett.
Según Henderson de Praemo, algunas personas definen la fabricación sin luz, sin intervención humana, como el juego final. “Personalmente, pienso en apagar las luces como algo similar a la búsqueda de la paz mundial”, dijo. “Para la industria manufacturera, es un concepto por el que es atractivo esforzarse, pero que no será alcanzable en muchas situaciones. Sensores integrados en herramientas y redes de herramientas; software que recopila, organiza y analiza datos sin problemas; y las máquinas herramienta que están conectadas en red a una fuente de inteligencia de fábrica nos acercan mucho más a esa fábrica apagada. Esto no significa que las máquinas reemplacen a las personas. Los libera para hacer un trabajo menos servil, más satisfactorio y definitivamente más productivo. Es similar a la llegada del CNC, que automatizó el control manual de los centros de mecanizado. Permitió que las personas trabajaran de manera más segura y productiva”.
Sistema de control de automatización
- Solución de corte para la industria de alfombras - Máquina de corte digital
- Solución de corte para la industria cinematográfica - Máquina de corte digital
- Máquina de corte láser y digital:la mejor solución de corte para la industria de telas / textiles
- La cadena de suministro está obteniendo nuevos talentos de más generaciones e industrias
- Nueva máquina construida y un cliente de Inglaterra aprendió a operar esta máquina CNC
- Universal Robots se asocia con Phillips Machine Tools India
- Operaciones de máquinas de torno y herramientas de corte de torno
- ¿Qué es el torneado mecánico?
- Herramientas multifuncionales que todos los talleres mecánicos deberían tener
- Una comparación rápida de máquinas herramienta CNC
- Control integrado de funciones de máquina herramienta