El control conectado
Internet y la computación basada en la nube están cambiando la forma en que los fabricantes operan las máquinas herramienta CNC. ¿Tu tienda está preparada para ello?
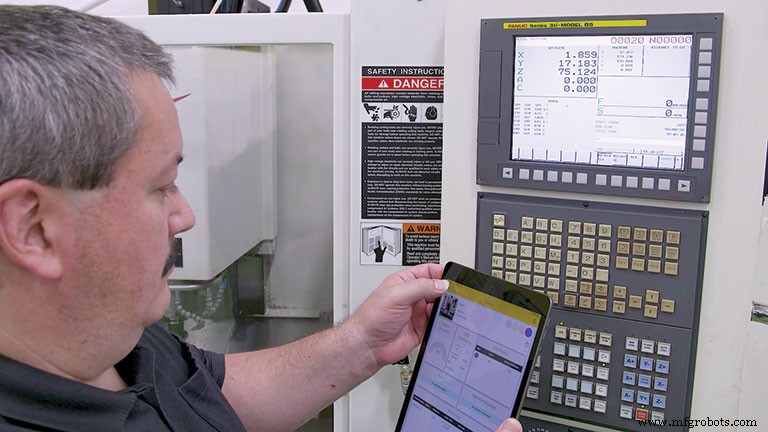
Los puertos Ethernet comenzaron a aparecer en tornos CNC y centros de mecanizado hace más de 20 años. El estándar de comunicación de máquina herramienta MTConnect hizo su debut oficial en EE. UU. en la IMTS 2010 en Chicago. Los fabricantes comenzaron a hablar sobre la computación en la nube y el Internet Industrial de las Cosas (IIoT) poco después, términos que se generalizaron cuando el economista alemán Klaus Schwab publicó un artículo en 2015 que afirmaba que el mundo había entrado en una Cuarta Revolución Industrial.
Bienvenido al 2021. A estas alturas, debería ser evidente para los propietarios de talleres de mecanizado, los programadores de CNC y los ingenieros de fabricación que la industria del mecanizado ha cambiado significativamente en las últimas dos décadas. Las máquinas herramienta CNC son mucho más inteligentes de lo que eran antes, capaces de generar cantidades significativas de datos sobre todo lo que sucede detrás del vidrio. El software de fabricación también se ha vuelto más inteligente y ofrece interoperabilidad y capacidades basadas en la nube con las que solo se soñaba en el cambio de siglo.
Si toda esta magia técnica es algo bueno o no, está en debate. Algunos podrían argumentar que la vida en el taller ya es lo suficientemente desafiante:¿quién necesita Big Data y maquinaria inteligente cuando apenas hay suficientes horas en el día para sacar las piezas por la puerta? Otros ven la Industria 4.0 y todo lo que implica como el camino claro a seguir para los fabricantes, y cualquiera que no lo adopte pronto estará fuera del negocio.
Obtención de FOCAS
La verdad se encuentra en algún punto intermedio. Paul Webster, director de F.A. Engineering en FANUC America Corp., con sede en Rochester Hills, Michigan, señaló que las máquinas herramienta CNC han estado listas para la red y la Internet desde antes del año 2000. Las tiendas que eligen ignorar esta capacidad todavía funcionan bien, gracias, y continuarán haciéndolo en los años venideros. Y, sin embargo, pocos argumentarían que la conectividad de la máquina-herramienta y la mayor visibilidad de los procesos de mecanizado habilitados nunca es algo malo y puede marcar la diferencia entre un trabajo rentable y uno que olvidaría pronto.
“Presentamos nuestra API FOCAS (interfaz de programación de aplicaciones) a principios de los 90, así como fibra óptica y luego puertos Ethernet, por lo que conectar un CNC ha sido fácil desde hace bastante tiempo”, dijo. "La parte difícil siempre ha sido averiguar qué datos necesita y qué va a hacer con ellos una vez que los tenga".
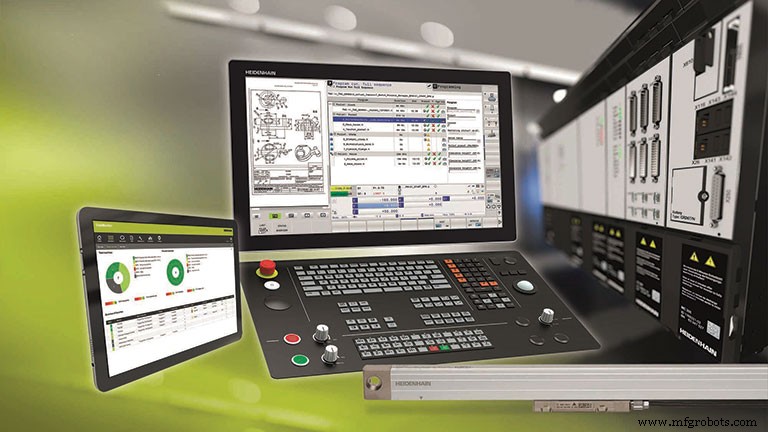
Estos datos incluyen historiales de alarmas, velocidad de avance y ajustes de anulación del husillo, temperaturas del servomotor y del husillo, consumo de energía, variables macro y mucho más, todo lo cual puede extraerse de la máquina herramienta de forma continua y automática. Agregue a esto varias entradas proporcionadas por el operador (número de trabajo, estado de producción, consumo de herramientas de corte e incluso información sobre la calidad de la pieza) y obtener una imagen completa de las actividades del taller no es más difícil que mirar el tablero de cualquier software de monitoreo que recopile estos datos. .
En el caso de FANUC, se trata de MT-LINKi, una plataforma de análisis independiente de la marca capaz de monitorear más de 1000 máquinas herramienta CNC a la vez, así como FASData, un programa de monitoreo de producción. Otros fabricantes de controles ofrecen soluciones similares, al igual que muchos fabricantes de máquinas herramienta, proveedores de herramientas de corte y desarrolladores de software de terceros. Todos brindan los medios para recopilar lo que ciertamente es una montaña de datos y presentarlos de una manera que tenga sentido para los humanos, brindándoles la capacidad de reaccionar ante tendencias y problemas potenciales mucho antes de que puedan afectar negativamente los niveles de producción.
El enigma de la nube
Entonces, la pregunta es cuál es el mejor lugar para almacenar estos datos y albergar el software utilizado para analizarlos. ¿Deberían estar ambos ubicados en la nube en una instalación de alojamiento externa y administrados por especialistas dedicados en hardware y software? ¿O es más apropiada una instalación “en las instalaciones”, utilizando cualquier talento interno de TI que posea el taller?
Webster y los demás entrevistados para este artículo coincidieron en gran medida en que, si bien el primero suele ser el enfoque más seguro y rentable, muchos talleres se muestran nerviosos acerca de los programas de piezas y los datos de producción que salen de sus instalaciones. También lo hace Gisbert Ledvon, director de desarrollo comercial para máquinas herramienta en Heidenhain Corp., con sede en Schaumburg, Illinois. Señaló que los clientes pueden instalar el software StateMonitor de la compañía donde lo deseen, pero promueve las instalaciones en el sitio siempre que sea posible.
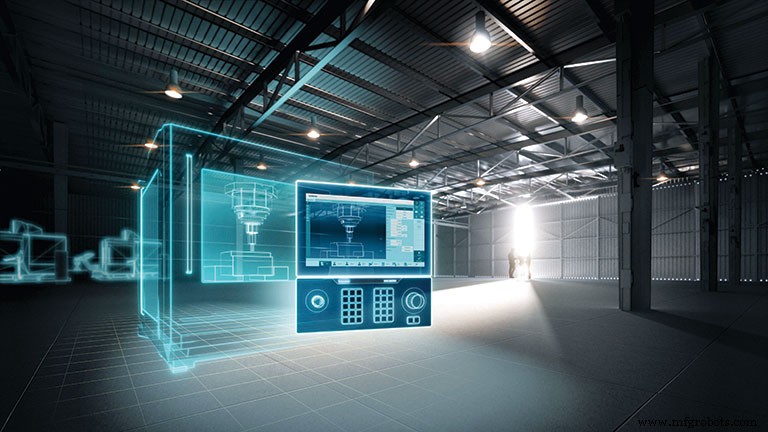
“Nuestra filosofía es que los clientes deben proteger su propiedad intelectual y, para nosotros, eso significa conectar sus máquinas herramienta y sistemas de software a una red corporativa debidamente protegida”, dijo. “Ha habido muchos casos en los que las tiendas han sido pirateadas y obligadas a pagar rescates. Por supuesto, estos ataques generalmente se realizan a través del correo electrónico y no a través del control de la máquina herramienta, pero no obstante, es una preocupación. Es por eso que la NTMA (Asociación Nacional de Mecanizado y Herramientas) ha comenzado a ofrecer seminarios que muestran a los fabricantes cómo pueden protegerse contra este tipo de ciberdelincuencia”.
A pesar de esto, Ledvon admite que la nube es una tendencia tecnológica que solo ganará impulso. Lo que se necesita para mitigar los riesgos asociados son buenas prácticas de limpieza de TI. Instale un firewall robusto entre la red de la tienda y el mundo exterior. Evite las conexiones directas de CNC a la nube descargando archivos externos, programas de software y parches a un servidor interno seguro, luego verifíquelos con un software antivirus antes de distribuirlos. Capacite a todos los usuarios de computadoras sobre cómo administrar contraseñas, detectar correos electrónicos y sitios web maliciosos y proteger la información corporativa. La lista continúa.
“Teniendo en cuenta que el control es el centro neurálgico de cualquier máquina herramienta, no creo que la conveniencia del acceso a la nube valga el riesgo de exposición a Internet”, dijo Ledvon. “Sin embargo, nada de esto impide que los fabricantes implementen una estrategia de Industria 4.0. Por todos los medios, deben conectar en red sus máquinas herramienta y comenzar a recopilar datos para su análisis. Si lo hace, les dará la información necesaria para configurar las máquinas más rápido, reducir los tiempos de ciclo, maximizar la vida útil de la herramienta y obtener todas las demás ventajas que ofrecen los controles CNC y los sistemas de software actuales”.
Talento nativo
Otro componente de Industria 4.0 es el gemelo digital, que en este caso se refiere a una representación virtual pero muy precisa y completa de una máquina herramienta CNC. Según Vivek Furtado, jefe de digitalización:máquinas herramienta de Siemens Industry Inc., Elk Grove Village, Illinois, los gemelos digitales agilizan el diseño y la implementación de maquinaria CNC, lo que en última instancia hace que los fabricantes sean más eficientes.
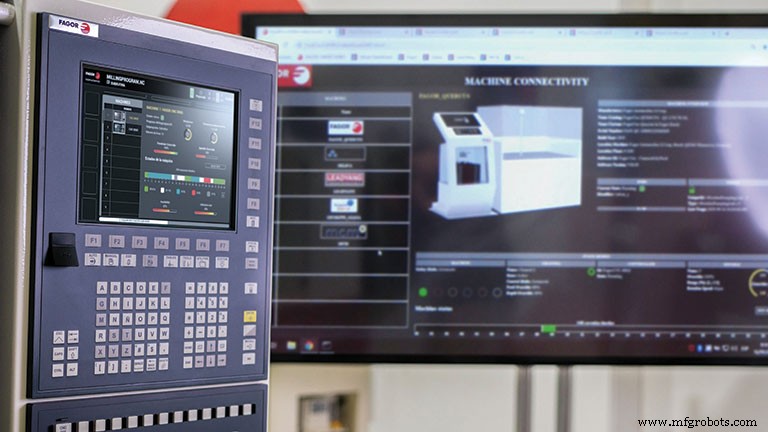
“Nuestro controlador SINUMERIK One se conoce como nativo digital, ya que se construyó desde cero para admitir el gemelo digital y otras tecnologías habilitadoras”, dijo. “Ofrece a los fabricantes de máquinas herramienta CNC la capacidad de crear una versión virtual de un torno o centro de mecanizado que contiene todas sus cinemáticas y características operativas. Esto reduce en gran medida el tiempo de ingeniería y los costos de desarrollo, y asegura que el producto satisfará las necesidades de los usuarios finales”.
Los controladores con capacidad de gemelos digitales sirven para otros propósitos. Aceleran la capacitación de los nuevos empleados y reducen la posibilidad de que uno de ellos choque con una costosa máquina herramienta. Permiten a los estimadores cotizar trabajos con mayor precisión, a los ingenieros desarrollar procesos de fabricación optimizados y a los programadores de CNC validar el código G y la selección de herramientas de corte antes de enviar el trabajo al taller. Una vez allí, facilitan el funcionamiento de la máquina herramienta con gráficos mejorados y una mayor facilidad de uso.
Cualquiera que tenga un sistema CAM de alta gama o un software PLM podría decir que puede lograr la mayor parte de esto sin un control CNC avanzado. Y aunque no se puede discutir que las capacidades de estas y otras plataformas de software han aumentado drásticamente en los últimos años, las máquinas herramienta que participan en el hilo digital brindan a los talleres mecánicos una herramienta importante, que mejora el intercambio de datos y cierra el ciclo de la interoperabilidad.
Adaptarse y Superarse
Dejando a un lado el hermanamiento digital, Furtado sugirió que los controladores CNC se están volviendo mucho más inteligentes y fáciles de usar, con funciones y características que cualquier usuario de teléfono inteligente reconocerá. “La mayoría de nosotros recordamos que una vez usamos nuestros teléfonos para llamar a la gente”, dijo. “Hoy, te permiten controlar tu salud, buscar información, hacer pedidos de productos, etc. Las nuevas generaciones de controladores ofrecen una funcionalidad similar. Son capaces de procesar información y preparar datos de manera que permitan que sus operadores humanos u otros sistemas los utilicen de manera más eficaz”.
Esta inteligencia se extiende también al proceso de mecanizado. Siemens, FANUC y proveedores de soluciones de terceros, como Caron Engineering, ofrecen capacidades de control adaptativo que monitorean continuamente las cargas del husillo y el eje, la vibración de la máquina y factores similares que afectan la vida útil de la herramienta de corte y la calidad de la pieza. Estos sistemas inteligentes luego ajustan los parámetros de mecanizado en tiempo real, optimizando la eliminación de material y eliminando problemas potenciales.
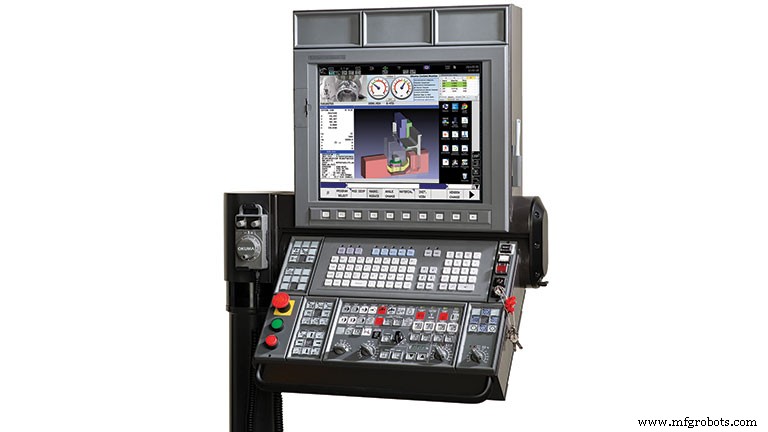
Fagor Automation Corp., Elk Grove Village, Illinois, es otro proveedor de control con la vista puesta en el premio Industria 4.0. Harsh Bibra, director general para Norteamérica de Fagor, explicó que su control ARFS (Adaptive Real-time Feed and Speed) hace todo esto y más, pero señaló que este tipo de tecnología basada en sensores también se puede utilizar para el mantenimiento predictivo.
“También ofrecemos nuestro paquete de conectividad i4.0”, dijo. “Esto permite a los usuarios recopilar datos de mecanizado, por supuesto, pero también hacer cosas como enviar alertas basadas en condiciones, ajustar la máquina herramienta y actualizar su firmware, cambiar la configuración de parámetros, etc., todo desde un dispositivo móvil o una computadora remota”.
El mayor cuello de botella
Bibra ve grandes cambios por delante. Aparte del mayor uso de sensores y acelerómetros con capacidad IIoT en máquinas herramienta, junto con controladores más inteligentes, las propias fábricas se volverán más inteligentes. La inteligencia artificial (IA), mucho más allá de las capacidades de adaptación que acabamos de mencionar, prevalecerá, lo que abrirá las puertas a la toma de decisiones automatizada necesaria para la fabricación generalizada sin interrupciones.
Todo esto, literalmente, ganará velocidad dado el desarrollo y posterior despliegue de las redes celulares 5G, sugirió Bibra. Estos no solo aumentarán el ancho de banda de Internet y reducirán la latencia, sino que posiblemente aliviarán los temores de piratería mencionados anteriormente. “Los controles del futuro estarán equipados con 5G, y los datos que generan se pueden enviar de forma inalámbrica a velocidades de hasta 10 gigabits por segundo (Gbit/s) a los llamados dispositivos de borde”, dijo. “Esperamos que, dentro de unos años, esta tecnología transforme fundamentalmente la forma en que los fabricantes recopilan información del taller”.
La desventaja de la Industria 4.0 es la falta de trabajadores calificados capaces de comprender y trabajar con tecnología avanzada. Bibra dijo que será necesario volver a capacitarse a medida que los fabricantes se vuelvan más expertos en tecnología. Sin embargo, cualquier preocupación sobre el conocimiento tribal y la pérdida de experiencia debido a la deserción y jubilación de los empleados debería convertirse en historia antigua.
Visita la tienda
Jim Kosmala, vicepresidente de ingeniería y tecnología de Okuma America Corp., Charlotte, Carolina del Norte, atribuye gran parte de la mayor conectividad actual al uso de controles basados en PC. “Mucha gente olvida que Okuma no solo fabrica máquinas herramienta, sino que también fabrica sus propios servosistemas y controladores. Estos se ejecutan en Microsoft Windows y usan un chip Intel, los cuales brindan una fácil conectividad”.
Los controles basados en PC también facilitan la instalación de varios programas de software en el control; por ejemplo, al comienzo de la pandemia de COVID, los clientes de Okuma podían colaborar con otros usando Microsoft Teams, compartiendo pantallas o dando a otros el control remoto según fuera necesario. “Esa es la idea detrás de nuestra tienda de aplicaciones”, dijo Kosmala. “Los usuarios pueden descargar e instalar lo que necesiten directamente en el control OSP, eliminando la necesidad de una PC separada. Representa posibilidades completamente nuevas para la colaboración y la conectividad”.
Una de estas aplicaciones es Connect Plan de Okuma, que permite a los usuarios monitorear máquinas herramienta CNC y recopilar datos operativos. Funciona con la mayoría de las máquinas herramienta de cualquier marca o antigüedad, así como con robots y otras formas de automatización. Sin embargo, según Kosmala, Connect Plan utiliza un algoritmo de IA para ver la información disponible e identificar tendencias que un ser humano podría pasar por alto.
Considere al gerente de un departamento de torneado, quien se da cuenta después de semanas de mirar los informes de recopilación de datos y los tableros de control que cierto torno siempre arranca 10 minutos tarde cada mañana gracias al hábito del café del operador, o que la temperatura del husillo en el molinillo más cercano al el departamento de envíos cae cada vez que abren la puerta de carga. Kosmala explicó que la IA detecta estas tendencias mucho más rápido que un ser humano, lo que brinda a los supervisores la capacidad de abordar áreas problemáticas potenciales antes. Además, esta información se almacena en una base de datos, por lo que cuando el supervisor deja la empresa, no hay pérdida de conocimiento.
“Deming nos dijo que sin datos, eres solo otra persona con una opinión”, dijo Kosmala. “El IIoT y la Industria 4.0 se tratan de recopilar esos datos y hacer uso de ellos, en última instancia, convertirlos en conocimiento. Ese es el primer paso para cualquier persona en este viaje. Ahora tenemos conferencias virtuales y la capacidad de verificar el estado de la máquina o los niveles de producción desde cualquier lugar y acceso a herramientas remotas que simplifican la automatización. Si puede hacerlo sin tener que ir a la planta, mucho mejor. Se trata de aumentar la eficiencia y el tiempo de actividad de la máquina, los cuales se logran más fácilmente con los controladores CNC modernos”.
Sistema de control de automatización
- ¡¿Qué hago con los datos ?!
- Democratizando el IoT
- El futuro de los centros de datos
- Conceptos básicos de los paneles de control eléctrico
- Aprendizaje automático en el campo
- Integración del Internet industrial de las cosas
- La nube en IoT
- Al borde de la gloria:posibilitando una nueva era de máquinas de Internet
- El decodificador permite el monitoreo conectado de los datos de cada máquina
- Los múltiples beneficios de las fábricas inteligentes conectadas con IIoT
- Beneficios de un taller de máquinas conectado