Obra maestra con uso intensivo de compuestos:Corvette 2020, Parte 2
A principios de este año, la primera entrega del Chevrolet Corvette de octava generación Los autos deportivos (C8) de General Motors Co. (GM, Detroit, Michigan, EE. UU.) salieron rodando de la línea de ensamblaje de GM en Bowling Green, Kentucky, EE. UU. Descrito como el " Corvette de entrada más rápido y potente "En los 67 años de historia del modelo, también es el Corvette que más materiales compuestos y el primero en presentar una configuración de motor central. El Corvette Stingray 2020 no solo hermoso y rápido, pero está adornado con una serie de características de lujo. Sin embargo, no te dejes engañar por la buena apariencia y los rápidos tiempos en la pista:hay muchas innovaciones en compuestos en este automóvil. CW La cobertura en dos partes del uso de compuestos en este vehículo comenzó en la edición de julio de 2020. Esta es la parte 2.
Estructura de la carrocería:parte B
El nuevo Corvette presenta no uno sino dos baúles que, combinados, tienen capacidad para 12,6 pies cúbicos / 0,36 metros cúbicos de carga. Ambos troncos se producen en resina de poliéster insaturado de éster vinílico / fibra de vidrio cortada al 42% en peso (VE-UP), pero utilizan diferentes procesos impulsados por requisitos geométricos y mecánicos. El maletero delantero ( frunk ) es un compuesto de moldura de lámina flotante (SMC) de gravedad específica (SG) de 0.95 moldeado por compresión, mientras que el maletero trasero se forma mediante el proceso patentado PRiME (Refuerzo preposicionado que garantiza la excelencia en la fabricación), una variante de moldeo por compresión líquida (LCM). El SMC flotante y el proceso PRiME fueron desarrollados por el procesador Molded Fiber Glass Co. (MFG, Ashtabula, Ohio, EE. UU.). MFG produjo todas las piezas estructurales de SMC y LCM'd en el automóvil.
“Aunque ambos espacios se caracterizan por paredes de poco calado y largo, el frunk es más pequeño que el maletero trasero y podría moldearse por compresión ”, explica Chris Basela, Corvette ingeniero jefe de estructura de la carrocería. “El maletero trasero necesitaba un mayor rendimiento mecánico y tenía una geometría difícil de llenar con una carga SMC. Debido a que el proceso PRiME nos permite cambiar la longitud de la fibra, podríamos usar un refuerzo preposicionado más largo en nuestra preforma. Hacer fluir la resina [no el vidrio] resultó ser el mejor enfoque ".
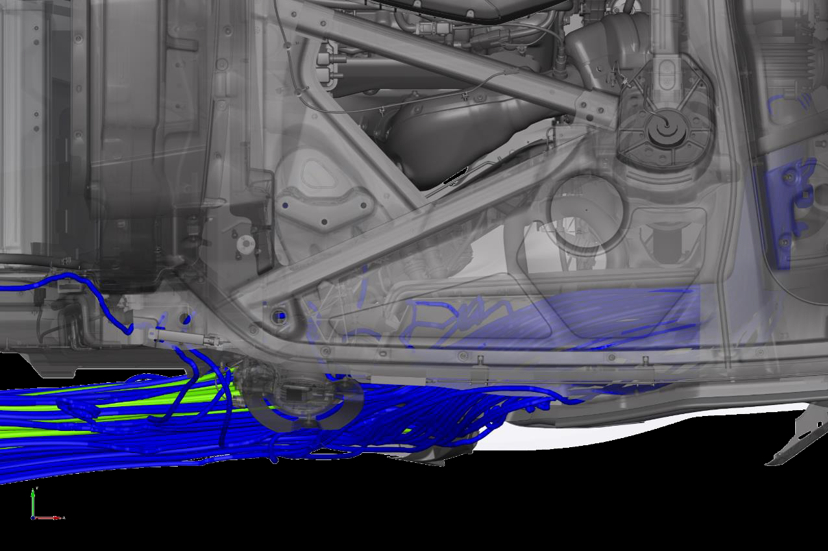
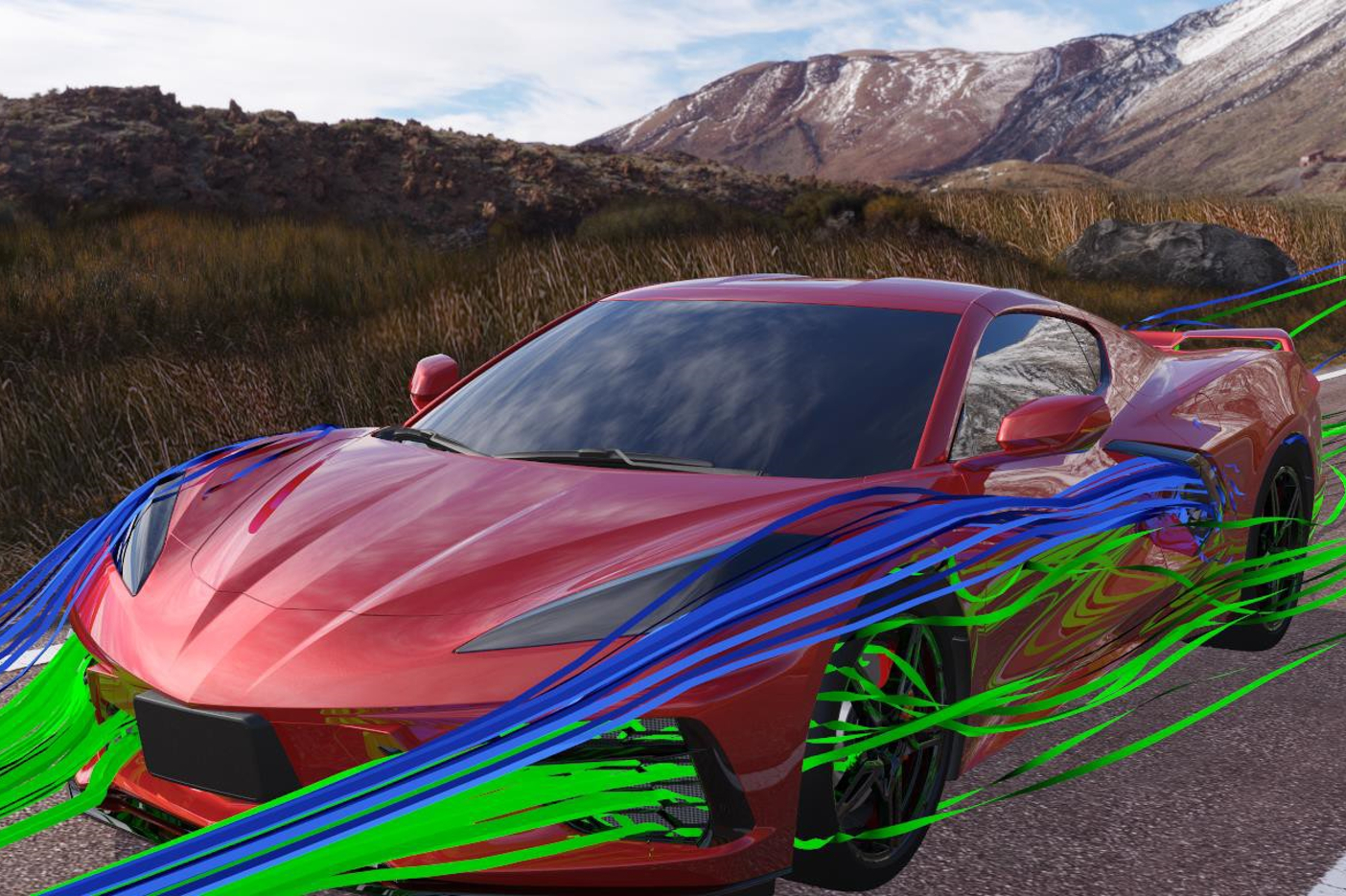
La ingeniería inteligente y un nuevo material fueron clave para enfriar el motor del C8. Múltiples vías de enfriamiento primarias (entradas traseras detrás de cada puerta, ventilaciones de la caseta de gobierno delantera y entradas de enfriamiento externas) alimentan conductos de inducción altamente complejos que canalizan el aire a través del vehículo y a través del motor, antes de la expulsión a través de ventilaciones de malla de aluminio y apliques SMC a ambos lados de la mampara de vidrio que muestra el Corvette motor. Los apliques están hechos con el flotador MFG (0.95-SG) SMC (vidrio picado / resina UP-VE). Bajo en compuestos orgánicos volátiles (COV), el material reduce las emisiones y elimina la necesidad de resonadores en los conductos de inducción traseros, al tiempo que reduce el costo y la masa (2,4 kilogramos) en comparación con tecnologías alternativas.
El enorme marco envolvente trasero visible para el cliente - 64 por 69 por 24 pulgadas (163 por 175 por 61 centímetros) - que rodea la mitad trasera del compartimiento de pasajeros está moldeado por compresión en SMC 1.2-SG endurecido. Este material híbrido reforzado presenta fibra de carbono al 15% de fracción de volumen de fibra (FVF) y fibra de vidrio al 30% FVF, con una resina UP de bajo VOC, formulada para resistir el calor del compartimiento del motor. El marco forma la base dimensional de todos los paneles interiores y exteriores traseros, pero su diseño flexible permite su uso para múltiples variantes de modelos. Gracias a la consolidación significativa de piezas, se eliminaron los accesorios secundarios, aumentando el espacio interior del paquete, reduciendo el ruido / vibración / dureza (NVH), proporcionando una mejor estructura de la carrocería y rendimiento de sellado, mejorando la visibilidad de la escotilla trasera y reduciendo la masa (15%) y el costo en comparación con el marco saliente. “Dado el tamaño de esta pieza, que mide casi 6 por 6 pies de alto y 2 pies de profundidad, tuvimos que hacer que el material fluyera cuesta arriba en el molde, así que todos estábamos un poco preocupados en la primera toma”, recuerda Basela.

Igualmente interesante es el mamparo (marco de la ventana central), que fue formulado a medida por MFG para resolver los desafíos de alto calor y ruido, ya que esta parte de la cabina se encuentra directamente sobre el motor V8. El refuerzo de fibra de vidrio combinado con relleno de grafito de berilio en resina VE-UP de bajo VOC amortigua la transmisión de sonido en el compartimiento de pasajeros de manera tan efectiva que elimina la necesidad de contramedidas secundarias para amortiguar el sonido. Eso, a su vez, redujo los costos, aumentó el espacio interior del paquete y la comodidad de los pasajeros, y mejoró el sellado de la carrocería y NVH. "Con un peso específico de 2,2, esta es la primera pieza compuesta a la que me han pedido que agregue masa en lugar de quitarla , ”Se ríe Basela.
Cierres y molduras
Los paneles exteriores de la carrocería están todos adheridos (interior / exterior), pintados y endurecidos 1.2-SG SMC (22-28% de fibra de vidrio FVF / resina UP, según el componente) de Continental Structural Plastics (CSP), una empresa del Grupo Teijin (Auburn Hills, Michigan, EE. UU.). Al atornillar los cierres compuestos, GM logra el estilo agresivo, la aerodinámica y la integración de enfriamiento funcional del C8, con un aligeramiento rentable en múltiples variantes de modelos que utilizan piezas comunes. Todos los paneles de la carrocería están pintados en línea en un "sistema skuk" en la posición del vehículo, utilizando el innovador proceso robótico de lijado en húmedo de Bowling Green.
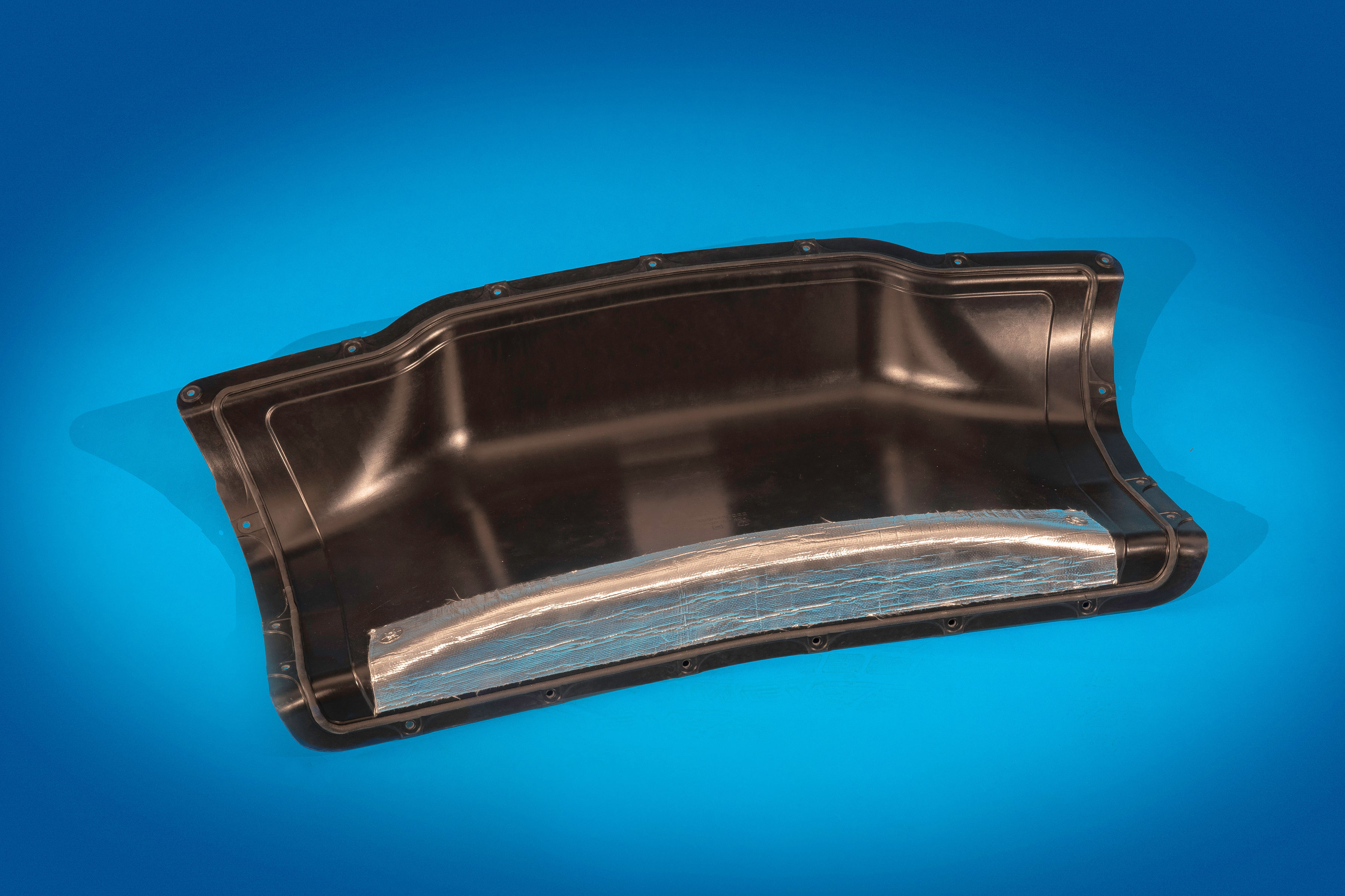
Otra innovación implica el uso de una junta de espuma elastomérica de silicona tixotrópica de una parte aplicada a la parte trasera de las puertas de servicio SMC, que están ubicadas en el maletero trasero (una en coupés, dos en convertibles), y permiten el acceso del cliente al aire. sistema de filtrado. Debido a la proximidad al compartimento del motor, el elastómero de espuma en el lugar (FIP) de alto rendimiento (Silastic 3-8186 de Dow, Inc., Midland, Michigan, EE. UU.) Se especificó para resistir temperaturas de uso continuo de hasta 392ºC. ° F / 200 ° C a la vez que proporciona un sello duradero con excelente resistencia al fraguado por compresión, incluso después de repetidos ciclos de apertura / cierre. GM informa que la mayoría de las otras espumas y juntas troqueladas se habrían derretido o roto bajo la exposición continua a tales temperaturas. Después de dispensar, la junta aplicada se trata térmicamente a 167 ° F / 75 ° C durante 10 minutos para expandir la espuma, eliminando el costo de troquelado y el desperdicio. Las puertas en sí son SMC templado (vidrio FVF al 42% en una matriz VE-UP). Los escudos térmicos, producidos por Gentex Corp. (Carbondale, Pensilvania, EE. UU.) Que utilizan telas de aramida de Kevlar aluminizadas resistentes al calor y a la abrasión (fibra de DuPont de Nemours, Inc., Wilmington, Del., EE. protección térmica.

GM también utilizó su sistema de equilibrio de ruedas de precisión totalmente automatizado de segunda generación en el C8. Desarrollados con The 3M Co. (St. Paul, Minnesota, EE. UU.) Y ESYS Automation (Auburn Hills, Michigan, EE. UU.), Los contrapesos de ruedas compuestos de alta densidad (5.8-SG) con propiedades magnéticas adaptadas reemplazaron los contrapesos metálicos estampados tradicionales en acero pintado, zinc o plomo que tienen una masa específica y deben aplicarse a mano sobre ruedas. El nuevo sistema utiliza grandes carretes de cinta extruida con respaldo adhesivo que contienen un 67% en volumen de una aleación de acero postindustrial, resistente a la corrosión y totalmente reciclable en una base de fluoropolímero. El sistema automatizado examina cada rueda, luego corta y aplica segmentos de cinta de peso personalizado en incrementos más pequeños y precisos para mejorar la conducción y reducir el desgaste de los neumáticos. También reduce el tiempo y el costo de ensamblaje, simplifica el inventario, elimina los desechos y la mano de obra y se ofrece en más colores que los pesos de metal.
Los techos Coupé están disponibles en tres niveles de acabado:pintado SMC endurecido de baja densidad (de CSP); policarbonato (PC) transparente con revestimiento duro; y compuesto de fibra de carbono con revestimiento transparente / tejido expuesto con bordes pintados (de deBotech Inc., Mooresville, Carolina del Norte). CSP también suministra varios paneles SMC 1.2-SG endurecidos de Clase A para sistemas de techo retráctil modelo convertible.
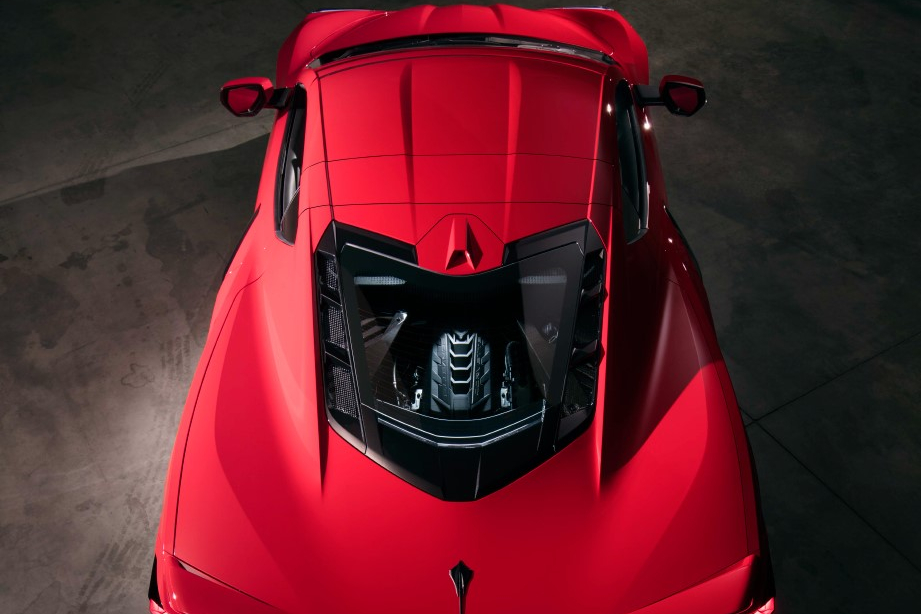
Otros paneles de molduras exteriores incluyen la fascia delantera superior e inferior pintada de poliolefina termoplástica (TPO), esta última con conductos integrados para dirigir el aire a los frenos (solo paquete Z51) e intercambiadores de calor externos. La rejilla exterior y las rejillas de ventilación de los frenos están pintadas con acrilonitrilo butadieno estireno (ABS).
La fascia trasera superior está moldeada en color (MIC) TPO, pero el ensamblaje de la fascia trasera inferior está pintado de Clase A, 1.2-SG SMC (vidrio / resina UP), debido a la proximidad de la pieza a las puntas de escape calientes. El excelente rendimiento mecánico de SMC permitió a GM diseñar un voladizo trasero corto sin apoyo y utilice espacios más grandes entre los accesorios sin que se comben. SMC también distribuye las cargas de manera eficiente sobre un área más grande durante choques traseros a baja velocidad que los termoplásticos. Los soportes y los sensores de asistencia de estacionamiento traseros están unidos al SMC. Se dice que esta es la primera vez que se utilizan los parachoques de SMC en vehículos de gran volumen.
Las aplicaciones de la trampilla trasera cuentan con PC / ABS pintado para el panel superior, SMC con malla de aluminio para las ventilaciones laterales y una aplicación inferior de SMC para acomodar la carga térmica directamente sobre el motor. Estos paneles SMC son producidos por Quantum Composites Inc. de LyondellBasell (Bay City, Michigan, EE. UU.). Los interruptores de liberación de la manija de la puerta son PC / ABS, mientras que la ventilación de entrada de aire trasera es SMC. El coche base tiene un spoiler ABS pintado moldeado por soplado y la rejilla de salida de aire trasera es ABS pintado moldeado por inyección. Los apliques del pilar A y del cabezal están pintados en ABS, al igual que las tapas de los espejos retrovisores laterales exteriores y las rejillas de entrada del radiador. Dependiendo del paquete de opciones, una parte inferior del ala delantera SMC endurecida y un divisor / difusor frontal de compuesto de fibra de carbono o TPO moldeado por soplado - carbono / epoxi con revestimiento transparente / tejido visible producido por deBotech utilizando preimpregnado de Solvay Composite Materials (Alpharetta, Ga., EE. UU.):Aportan estabilidad aerodinámica adicional. Un difusor trasero en SMC endurecido se acopla a la fascia trasera inferior del SMC en SMC pintado Clase A de MFG.
El paquete de molduras de fibra de carbono premium presenta varios acentos de fibra de carbono con revestimiento transparente / tejido visible por dentro y por fuera, incluidas cubiertas de espejos, inserto de rejilla frontal, divisor frontal, alerón de accesorios, cubiertas del compartimiento del motor, placas de interruptores de puertas interiores, molduras de balancines, instrumentos- bisel del grupo de paneles, cubiertas de las manijas de las puertas, apliques de cuartos y placa de control de conducción. Estos componentes son producidos por deBotech, SMI Composites LLC (Comer, Ga., EE. UU.) Y Plasan Carbon Composites (Wixom, Michigan, EE. UU.).
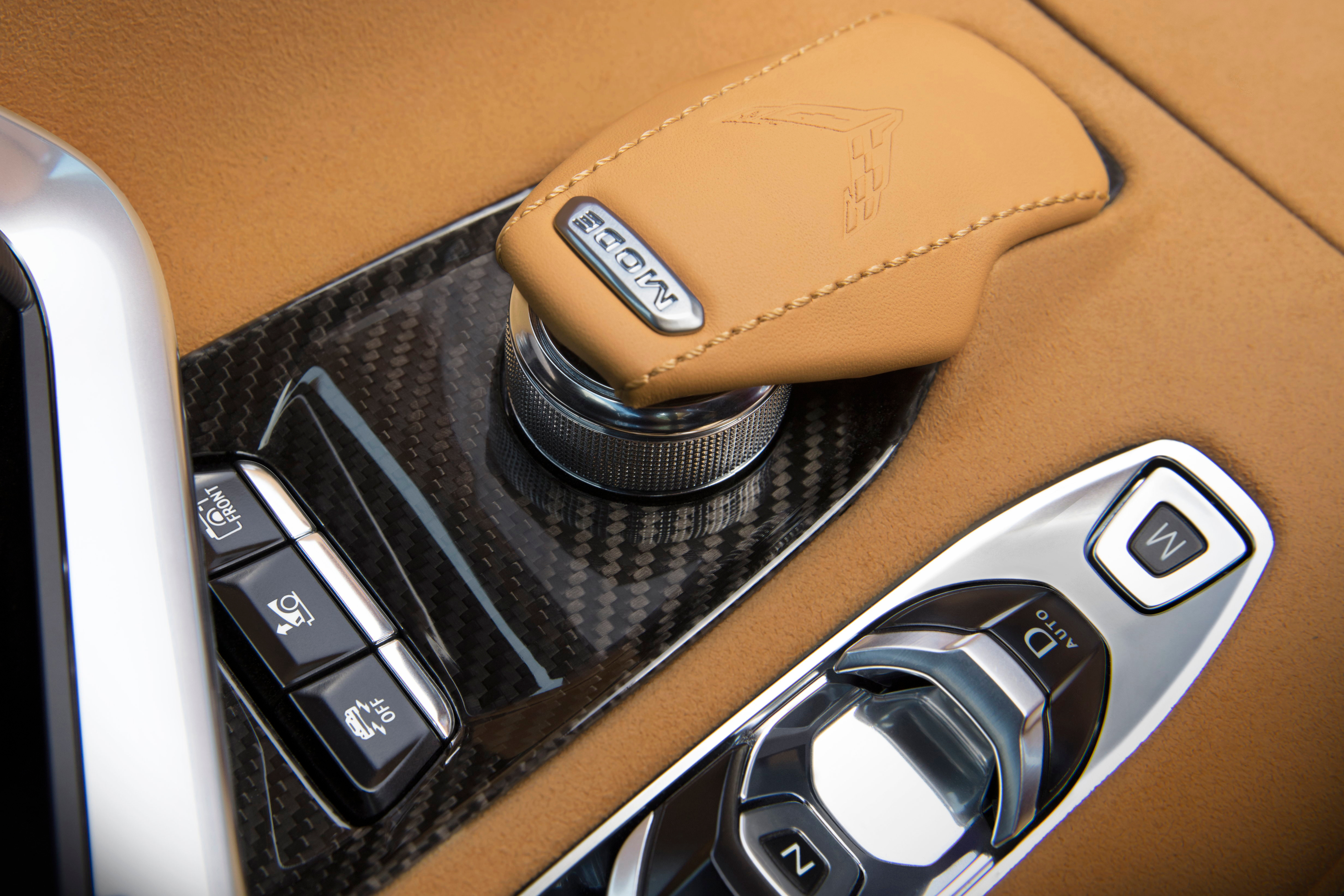
Tecnología avanzada
El Corvette 2020 ya ha ganado muchos premios prestigiosos de la industria, incluido el Auto del año de MotorTrend 2020, el Premio a la asociación PACE (Contribuciones a la excelencia del proveedor de automoción principal) de 2020 Automotive News y varios premios de la Society of Plastics Engineers (SPE), incluido el Premio al equipo de ingeniería de vehículos 2019 . "Aunque el nuevo Stingray's La arquitectura de motor central ha dominado los titulares, sin importar dónde esté el motor, delante o detrás del conductor, durante ocho generaciones, Corvettes siempre hemos avanzado el estado del arte en tecnología de materiales automotrices ”, agrega Tadge Juechter, ingeniero en jefe ejecutivo de Global Corvette. "El avance de la tecnología está en el corazón de lo que hacemos".
Resina
- 10 ventajas de la computación en la nube en 2020
- El futuro de la impresión 3D:12 conclusiones clave de la AM Landscape Digital Conference 2020 de AMFG (Parte 1)
- El futuro de la impresión 3D:12 conclusiones clave de la AM Landscape Digital Conference 2020 de AMFG (Parte 2)
- Liderazgo de mantenimiento, Parte 3
- Introducción a los armónicos:Parte 1
- Sostenibilidad en la fabricación - Parte 3
- Tendencias y desafíos de 2020 afectados por el Covid-19:Parte I
- El giro es opcional
- ¿Qué es un número de pieza?
- Mecanizado de piezas pequeñas
- Cilindricidad en GD&T