Moldes CFRP de impresión 3D para flaperones RTM, exoesqueletos y más
Crédito de la foto:Cátedra TU Munich de Carbon Composites (LCC) y QPoint Composite
La Cátedra de compuestos de carbono (Lehrstuhl für Carbon Composites o LCC) se estableció en 2009 en el departamento de Ingeniería Mecánica de la Universidad Técnica de Múnich (TUM, Múnich, Alemania) con financiación de SGL Carbon (Wiesbaden, Alemania). Su misión es realizar I + D en materiales, procesos y aplicaciones de polímeros reforzados con fibra de carbono (CFRP), incluidos proyectos de simulación y pruebas. Una "cátedra" en el sistema universitario alemán es la unidad más pequeña que comprende un profesor y su equipo. El equipo de LCC está dirigido por el Prof. Dr. -Ing. Klaus Drechsler y actualmente emplea a 30 investigadores a tiempo completo. Aunque la financiación de SGL llegó a su fin en 2016, LCC ha continuado su liderazgo en I + D de compuestos, que incluye la construcción del molde para la mitad inferior del Demostrador de fuselaje multifuncional (MFFD), consulte la barra lateral a continuación, y ahora también incluye impresión 3D / aditivos. fabricación.
Este blog comenzó cuando CEAD (Delft, Países Bajos) me informó que LCC había comprado uno de sus sistemas AM flexbot basados en extrusoras para impresión 3D utilizando un brazo robótico. Mi entrevista posterior con el investigador de LCC Patrick Consul, sin embargo, reveló un tesoro de proyectos, incluido COMBO3D, dentro de Clean Sky 2, para imprimir en 3D un molde de compuesto termoplástico RTM para la producción de un flaperón de avión compuesto termoestable, y EMOTION para producir la herramienta. para moldear la mitad inferior del Demostrador de Fuselaje Multifuncional (MFFD) de compuesto termoplástico de Clean Sky 2, así como una herramienta parcial secundaria para demostrar cómo se podría producir el mismo fuselaje mediante consolidación directa in situ (fuera de autoclave). Me pareció interesante toda la discusión sobre cómo TUM ha llegado a este punto y hacia dónde se dirige.
Mitad inferior del molde MMFD
Consulte mi blog de febrero de 2020:"Probar la soldadura LM PAEK para demostradores multifuncionales de fuselaje". Esta barra lateral está tomada del documento de febrero de 2020, "Desarrollo de un demostrador de fuselaje multifuncional" por Bas Veldman, gerente de programa del MFFD en GKN Fokker (Hoogeveen, Países Bajos).
La carcasa de la mitad inferior del MFFD consta de una piel termoplástica, reforzada con largueros, clips y marcos soldados. El proceso de fabricación que se va a demostrar consta de tres pasos clave:
- La cinta preimpregnada para la piel grande del demostrador se coloca sobre una mesa plana e inclinada con la máquina AFP láser existente de NLR.
- Las bandejas se transportan robóticamente con ventosas a un molde de consolidación hembra y se colocan en él sin calentar.
- Después del envasado al vacío, la piel se consolida en un autoclave.
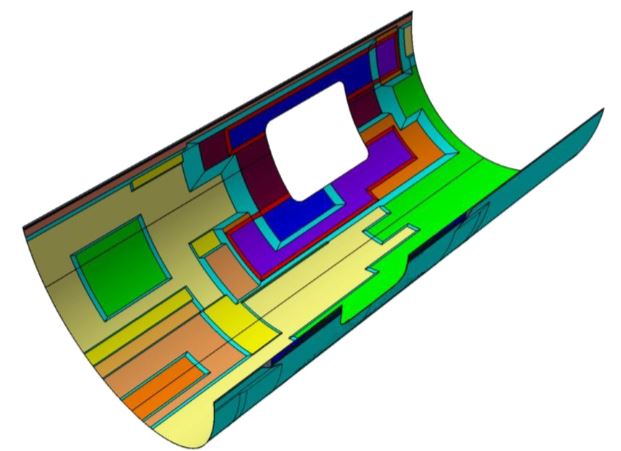
El uso de un molde de consolidación hembra ofrece una superficie mucho más simple (plana) que la de una herramienta macho, al tiempo que controla directamente las limitaciones aerodinámicas en la calidad de la superficie exterior de la piel.
El proyecto MFFD también requiere fuera del autoclave procesos que se investigarán, comenzando en paralelo al gran demostrador de fuselaje multifuncional, en un demostrador posterior de menor tamaño. En particular, compuesto termoplástico in situ Se considerará la fabricación en la que se logra la consolidación durante el laminado, ya que puede eliminar completamente el paso del autoclave y, por lo tanto, reducir la fabricación a un procedimiento de un solo paso.
Molde mejorado para fuselaje termoplástico dentro y fuera de la consolidación de autoclave, o EMOTION (https://cordis.europa.eu/project/id/864474), es el proyecto Clean Sky 2 para producir las herramientas de carcasa inferior MFFD. “Suena simple”, dice Patrick Consul del coordinador del proyecto, TU Munich, “pero en realidad es bastante desafiante ya que necesita ser calentado a 400 ° C. Esto está muy por encima del rango de temperatura en el que Invar36 no tiene un CTE [coeficiente de expansión térmica] significativo ". Invar se usa comúnmente para herramientas de moldeo de materiales compuestos debido a su baja expansión durante los ciclos de curado a alta temperatura. Sin embargo, el CTE de Invar aumenta con la temperatura. "El desafío", señala el Cónsul, "será controlar la expansión térmica durante el calentamiento y enfriamiento para el molde de 8 metros por 4 metros y el revestimiento del fuselaje durante el curado".
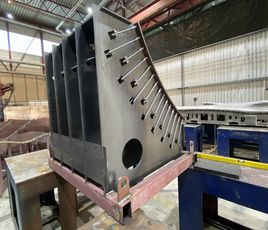
Progresión en la fabricación aditiva
“Somos de 8 a 9 personas trabajando en la fabricación aditiva dentro del LCC”, dice Consul. Comienza la historia de este trabajo con la compra por parte de LCC de una máquina de colocación de cinta compuesta termoplástica asistida por láser de AFPT (Dörth, Alemania) en 2012. Más tarde agregó una máquina Coriolis Composites (Quéven, Francia) para permitir la colocación automatizada de fibras (AFP) ) de preimpregnados termoendurecibles. Las primeras impresoras de escritorio basadas en filamentos se compraron en 2017. "También me uní en 2017 para ayudar con el desarrollo de nuevas aplicaciones y proyectos de investigación, incluida la redacción de propuestas, por ejemplo, para Clean Sky 2". Explica que los proyectos de Clean Sky 2 se adjudican en función de las propuestas enviadas a los gestores de temas en respuesta a las convocatorias de propuestas (CFP) publicadas. LCC tuvo éxito en sus propuestas para el proyecto CFP08 COMBO3D y el proyecto CFP09 EMOTION. Ambos se analizan a continuación.
“Tenemos algunos otros proyectos, algunos de los cuales apuntan a la impresión 3D con refuerzos de fibra continua”, dice Consul. “Otros usan un cabezal de impresión integrado con láser para precalentar el sustrato compuesto para imprimir en piezas de CFRP ya consolidadas o para aumentar la resistencia al corte interlaminar (ILSS) entre capas impresas. Otro proyecto explora aplicaciones de herramientas, por ejemplo, en las que tiene un número reducido de piezas compuestas especializadas ”.
“Estos proyectos están respaldados continuamente por simulaciones numéricas para predecir el comportamiento de las piezas fabricadas con aditivos durante y después del proceso de impresión”, continúa. “El LCC también está involucrado en un proyecto con el Imperial College de Londres que tiene como objetivo fabricar exoesqueletos utilizando CFRP impreso en 3D. Otro proyecto investiga las estructuras de celosía para optimizar las propiedades de las piezas impresas en 3D con respecto a la rigidez, la resistencia o la absorción de energía ”.
Progresión en impresoras

“Empezamos usando una impresora 3D sencilla basada en FDM (modelado por deposición fundida) de Apium (Karlsruhe, Alemania) para imprimir dispositivos de prueba especializados que necesitan una gran rigidez”, explica Consul. “La impresora tenía 3 metros de largo por 1 metro de ancho con una alta producción de material para reducir el tiempo de impresión. Aunque no podía usar fibra continua, estaba bien diseñado para imprimir con PEEK, PEKK y PEEK reforzado con fibra de carbono cortada. No solo usó una cama calentada, sino también una placa calentada alrededor del cabezal de impresión que ayudó a producir una distribución de temperatura homogénea en las impresiones, reduciendo el estrés térmico y asegurando la cristalización ”.
“También tuvimos una impresora Markforged (Cambridge, Mass., EE. UU.) Durante un tiempo y luego obtuvimos una Anisoprint [Esch-sur-Alzette, Luxemburgo]”, dice Consul. Aunque la impresora Markforged habilitó FDM con fibra continua, el equipo de LCC decidió no mantenerla. “El problema que tuvimos fue que el sistema estaba muy cerrado”, explica el Cónsul. “El software de corte de Markforged era demasiado difícil de usar para la investigación porque limitaba severamente lo que podíamos hacer. Solo pudimos imprimir una capa de material de fibra continua y luego una capa de filamento termoplástico reforzado con fibra corta en la parte superior. El rebanador que genera el código no acepta nuestro código G. Entonces, no había forma de decirle a la máquina que lo imprimiera de la manera que queríamos con fibra continua en cada capa, etc. ”
Cuando se le preguntó sobre esto, Markforged explica que sus sistemas nunca fueron pensados para ser usados para investigación, sino que fueron diseñados para ser simples y robustos para un uso generalizado en la fabricación de piezas, utilizando rutas de fibra basadas en reglas y requiriendo poco esfuerzo y tiempo para configurar la cortadora. . Es El software Eiger permite a los usuarios configurar capas individualmente, y Markforged agradece los comentarios y prioriza la mejora de la experiencia del usuario para sus clientes.
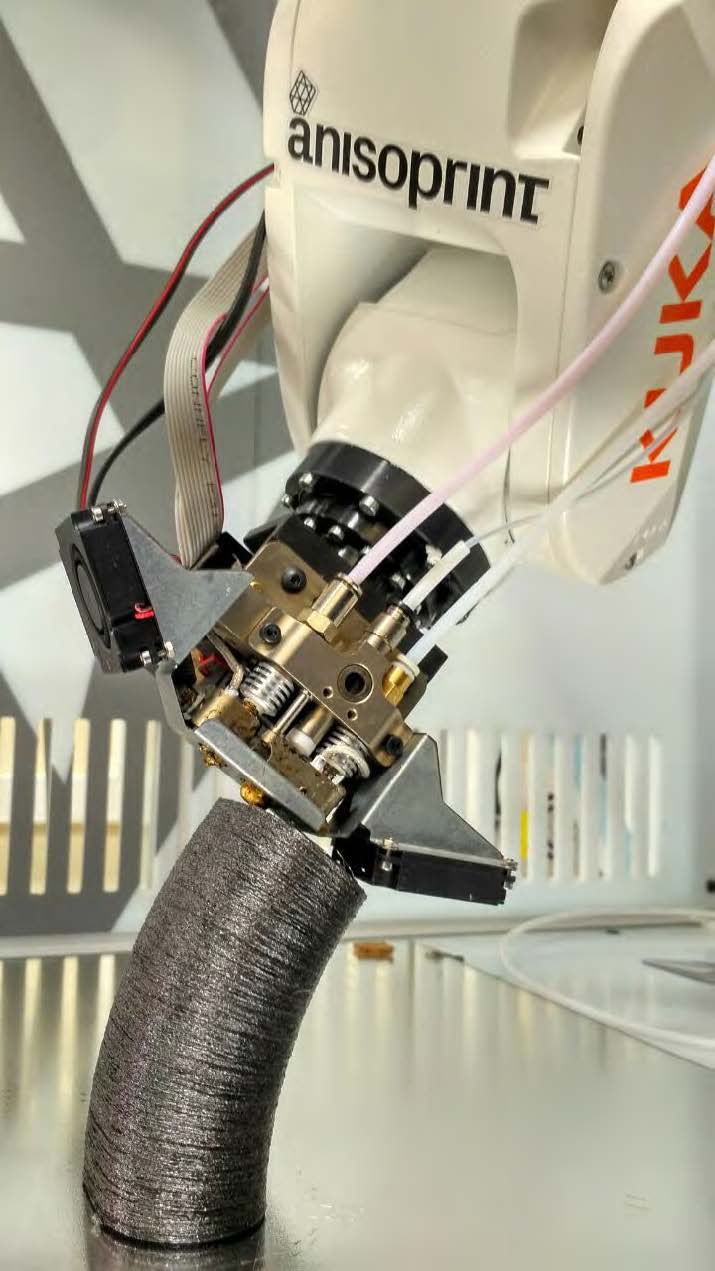
“Anisoprint, que utiliza una cortadora de código G completamente abierta, nos dio más acceso al proceso”, dice Consul. “También es capaz de imprimir fibra de carbono continua y no solo en capas 2D, sino también fuera del plano, en curvas 3D. Tenemos un cabezal de impresión Anisoprint para un pequeño robot Kuka, capaz de producir piezas de 1 metro por 1 metro, que es más grande que la mayoría de las computadoras de escritorio, pero pequeño para un sistema de robot ".
Pero, ¿qué pasa con la matriz dual de Anisoprint materiales termoendurecibles-termoplásticos (TS-TP)? Como explico en mi blog de 2019 sobre Anisoprint “… primero impregna el refuerzo de fibra continua con un termoestable polímero y luego lo extruye en el filamento termoplástico fundido durante la impresión ". Consul responde que la adherencia entre el filamento TS y el TP es bastante buena. “En nuestras primeras pruebas, pudimos obtener un mayor contenido de volumen de fibra en comparación con la impresora Markforged, pero esto se debió a que pudimos modificar el código G. El cabezal de impresión Anisoprint empuja el filamento TS hacia el TP y luego lo coloca. Planeamos usar esa impresora para piezas de exoesqueleto. Es una manera fácil de integrar fibras de mayor resistencia ".
Impresoras de pellets extruidos
La siguiente progresión fue hacia una impresora a gran escala, primero con TP corto reforzado con fibra y luego con TP de fibra continua. “Primero desarrollamos una extrusora montada en un robot, y luego nuestro interés en la máquina CEAD siguió rápidamente. Esperamos que la fibra continua se integre en ambos sistemas el próximo año ”.
Pero, ¿por qué necesitaba la máquina CEAD si ya tenía una extrusora en un brazo robótico? “La extrusora inicial fue la versión beta de una extrusora de pellets Dyze Pulsar, que produce un máximo de aproximadamente 2 kg / h y aproximadamente 1 kg / h con PAEK, pero tiene problemas con más del 20% de carga de fibra de carbono”, dice Consul. “Sin embargo, la producción promedio es menor porque el robot acelera y desacelera a menudo durante la impresión. Para COMBO3D, las mitades iniciales del molde a pequeña escala ya requerían al menos 36 kilogramos, por lo que necesitábamos alrededor de 48 horas para imprimir una sola mitad. También teníamos que tener a alguien siempre con él porque los errores, como una línea de alimentación de material bloqueada o deformación de una pieza, podían ocurrir en cualquier momento ”.
Debido a que el demostrador final COMBO3D es aproximadamente 10 veces más grande que las piezas iniciales a pequeña escala, imprimirlo con este primer sistema de extrusión no fue factible, dice Consul. “Además, algunos de los materiales que nos suministró Victrex tenían una viscosidad más alta y esta primera extrusora no podía proporcionar suficiente torque para extruir esos polímeros. Con la impresora CEAD, tenemos una producción máxima de alrededor de 12,5 kg / h, y después de algunas horas de pruebas, obtuvimos una producción promedio estable de alrededor de 5-6 kg / h. Esto nos permitió imprimir la mitad del molde a pequeña escala en menos de 8 horas y nos permite utilizar un mayor contenido de fibra para reducir la deformación, haciendo que el proceso en general sea más fácil de controlar ”.
“Entonces, si bien la Pulsar ya nos permitió usar gránulos, lograr una alta producción de material y aprovechar los grados de libertad de un robot”, continúa, “la impresora CEAD extiende nuestras capacidades hacia piezas más grandes, mayor contenido de fibra y una gama más amplia de polímeros . La Pulsar cierra la brecha entre nuestras impresoras basadas en filamentos y la CEAD, no solo en la producción, sino también en el tamaño de la boquilla y el detalle resultante de las impresiones ”.
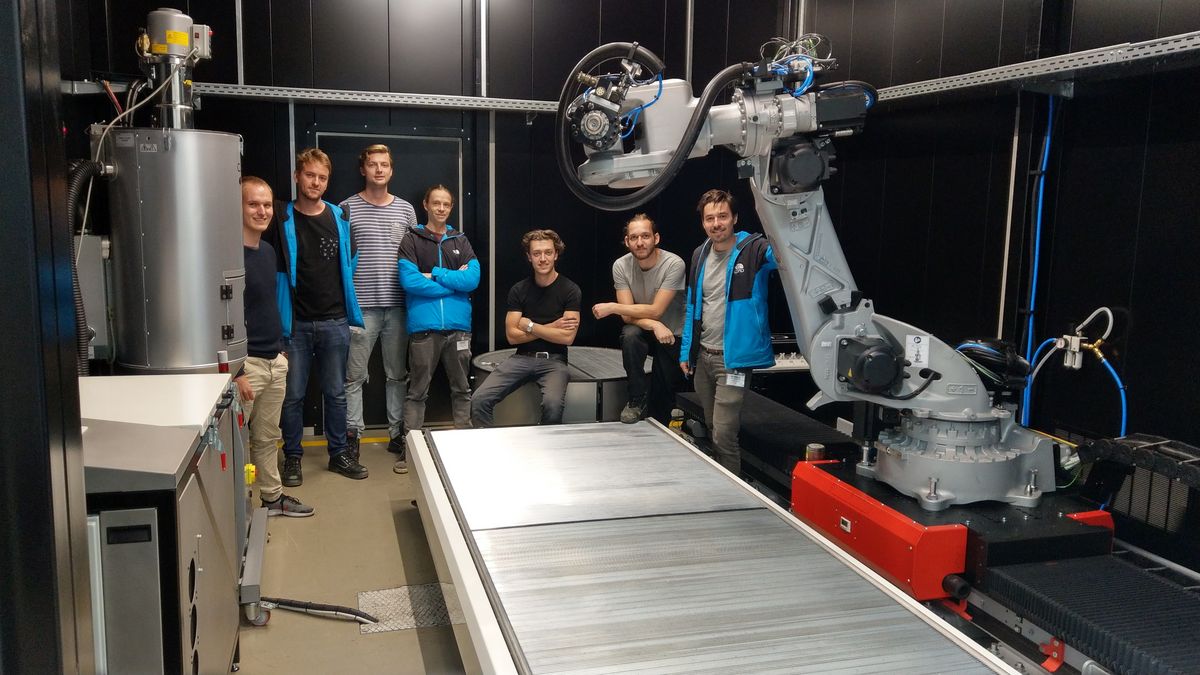
Datos técnicos de CEAD AM Flexbot:
- Datos técnicos de AM Flexbot:
- Impresiones por extrusión a base de pellets de hasta 12,5 kg / h (no reforzadas y reforzadas con fibras cortas)
- Procesamiento de materiales hasta 450 ° C
- Volumen de construcción 3000 x 1200 x 1700 milímetros
- Construya la placa sobre una mesa giratoria o una mesa plana (calentable)
- Reelaboración mediante cabezal de fresado.
COMBO3D
El objetivo de este proyecto Clean Sky 2 es imprimir en 3D un molde para producir un flaperón compuesto demostrador (1,5 por 3 metros) para un gran avión de pasajeros, parte del Paquete de Trabajo A-3.1:Ala multidisciplinar para alta y baja velocidad. El objetivo de utilizar la fabricación aditiva es acortar el tiempo de espera para la producción de herramientas. El proyecto comenzó en enero de 2019 y finalizará en marzo de 2021. Los socios incluyen Alpex Technologies (Mils bei Hall, Austria), el especialista en metales ligeros Leichtmetallkompetenzzentrum Ranshofen (Ranshofen, Austria) y Victrex (Thornton Cleveleys, Reino Unido), proveedor del termoplástico de alto rendimiento. poliariletercetona (PAEK).
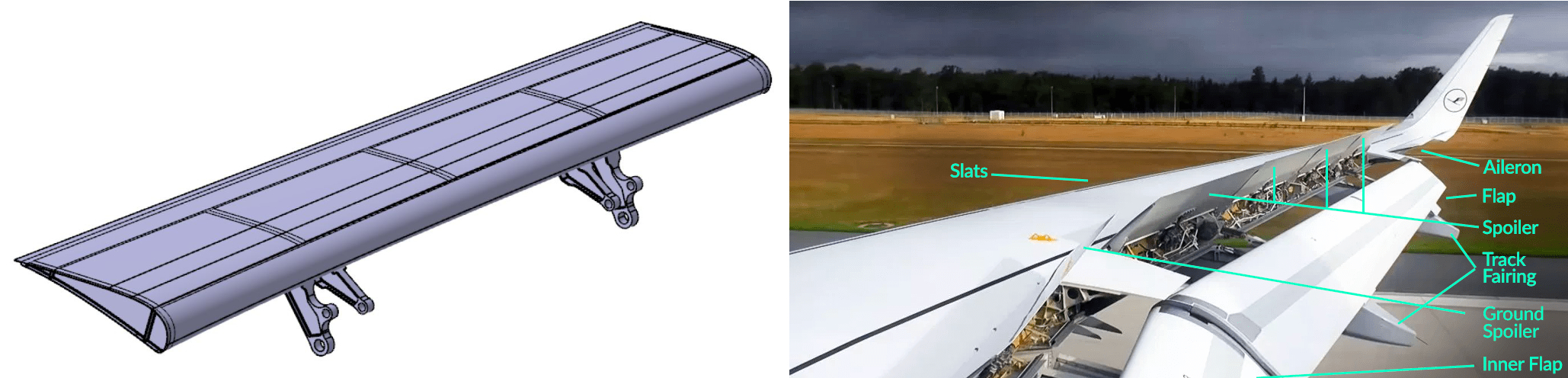
Otra parte clave del proyecto es demostrar que este flaperón de fibra de carbono / epoxi se puede fabricar con moldeo por transferencia de resina (RTM) en lugar de preimpregnado curado en autoclave. La pieza RTM curará a los mismos 180 ° C que las piezas del autoclave. Para garantizar la estabilidad térmica, la herramienta se imprimirá con PAEK corto reforzado con fibra de carbono, que tiene una temperatura de fusión de 305 ° C.
Para acortar el ciclo de curado, el molde impreso en 3D integrará un control de temperatura activo. “Debemos poder calentar y enfriar el molde más rápido en comparación con el autoclave”, señala Consul. “Usaremos una malla de elementos calefactores eléctricos 3 milímetros por debajo de la superficie del molde y también integraremos canales impresos para aceite o aire caliente a 6 milímetros por debajo de la superficie del molde. De esta forma, podemos calentar la superficie del molde muy rápidamente, pero también podemos utilizar los canales para calentar todo el volumen de la herramienta. Nuestro objetivo es lograr una tasa de calentamiento y enfriamiento un 50% más rápida que la del autoclave y estamos seguros de que podemos lograr una tasa al menos un 30% más rápida ".
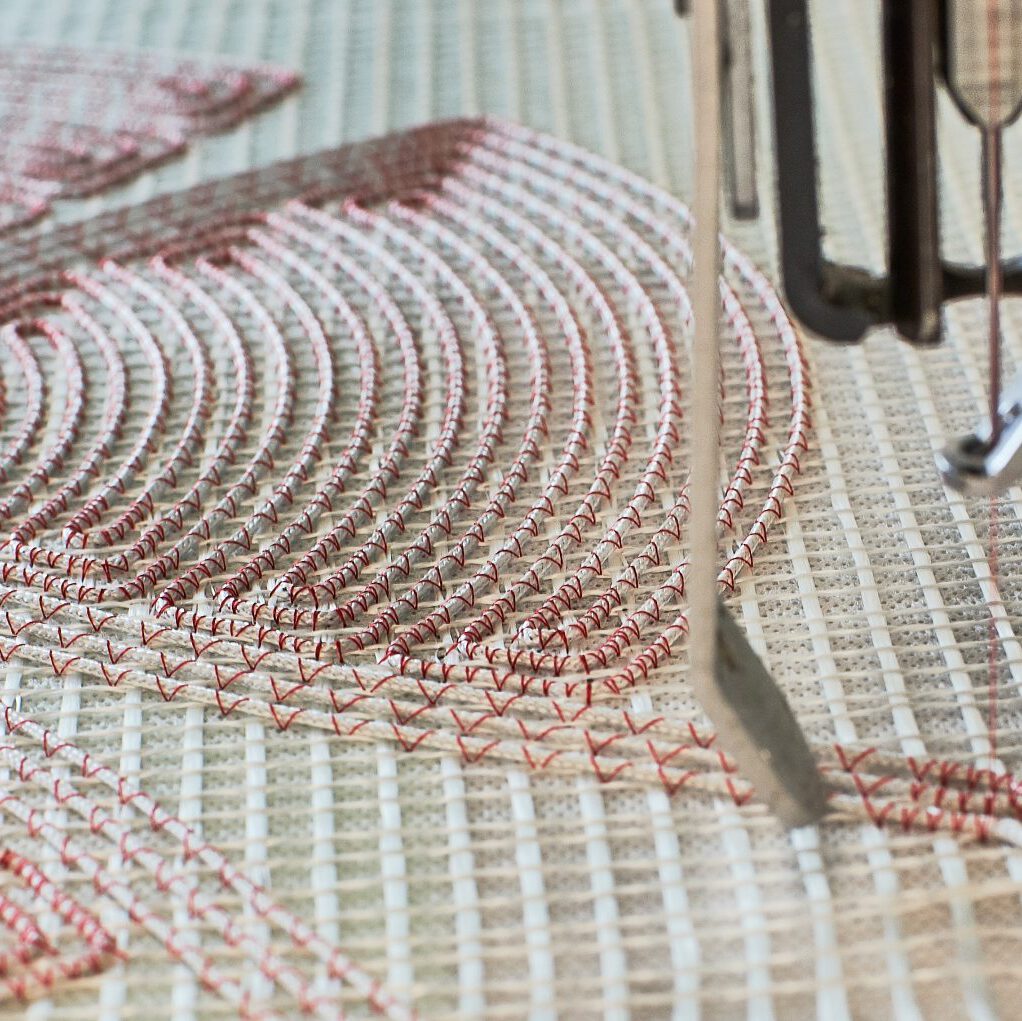
¿Cuáles son los elementos calefactores que se integrarán en la impresión 3D? “Hemos utilizado la colocación de fibras a medida (TFP) de mechas de carbono sobre un tejido de fibra de vidrio como elementos calefactores para realizar diferentes zonas calefactoras en un molde de CFRP para una pala de rotor de helicóptero”, explica Consul. “Esto fue para un proyecto Clean Sky 1 que completamos trabajando con QPoint Composite (Dresden, Alemania). Trabajaremos con un concepto similar en el molde COMBO3D ”.
Todo el desarrollo de la herramienta impresa está respaldado por simulación. El diseño de la herramienta se optimizará implementando el sistema de calefacción y refrigeración en una simulación térmica. También se simulará el proceso de fabricación, lo que respaldará el proceso de impresión al generar conocimiento sobre la distribución de la temperatura durante la impresión y correlacionarlo con la planificación de la ruta.
Instalación de la máquina CEAD y progreso del proyecto
“El sistema CEAD se entregó muy rápidamente:desde el pedido hasta la instalación fueron solo 6 meses”, dice Consul. “Para entonces, habíamos completado las pruebas de materiales, diseñado las herramientas de la placa y habíamos comenzado a imprimir piezas pequeñas. Nos preocupaba que se necesitara mucho tiempo para que el proceso funcionara bien con CEAD AM Flexbot, pero funcionó bien con las primeras pruebas ”.
¿Herramientas de placa? "Es un molde pequeño, que ya integra canales de enfriamiento y elementos calefactores para producir placas de CFRP para pruebas de cupones", explica. “Esta prueba fue para garantizar que la calidad de nuestro molde CFRP RTM impreso en 3D sea comparable al CFRP actual que produce Saab con su proceso de autoclave”.
Desafortunadamente, el proyecto fue interrumpido por COVID-19, "pero ahora todo va bien y nos estamos poniendo al día", dice el Cónsul. ¿Y qué hay del uso de PAEK para el molde impreso en 3D? “El único problema actualmente es que la Tg [temperatura de transición vítrea] para PAEK es de 130-140 ° C, que es más baja que la cura de 180 ° C para la parte de demostración”, señala el Cónsul. "Por lo tanto, todavía tenemos que ver cuántos ciclos podemos completar a la temperatura de curado antes de que ocurra la fluencia o la superficie se dañe".
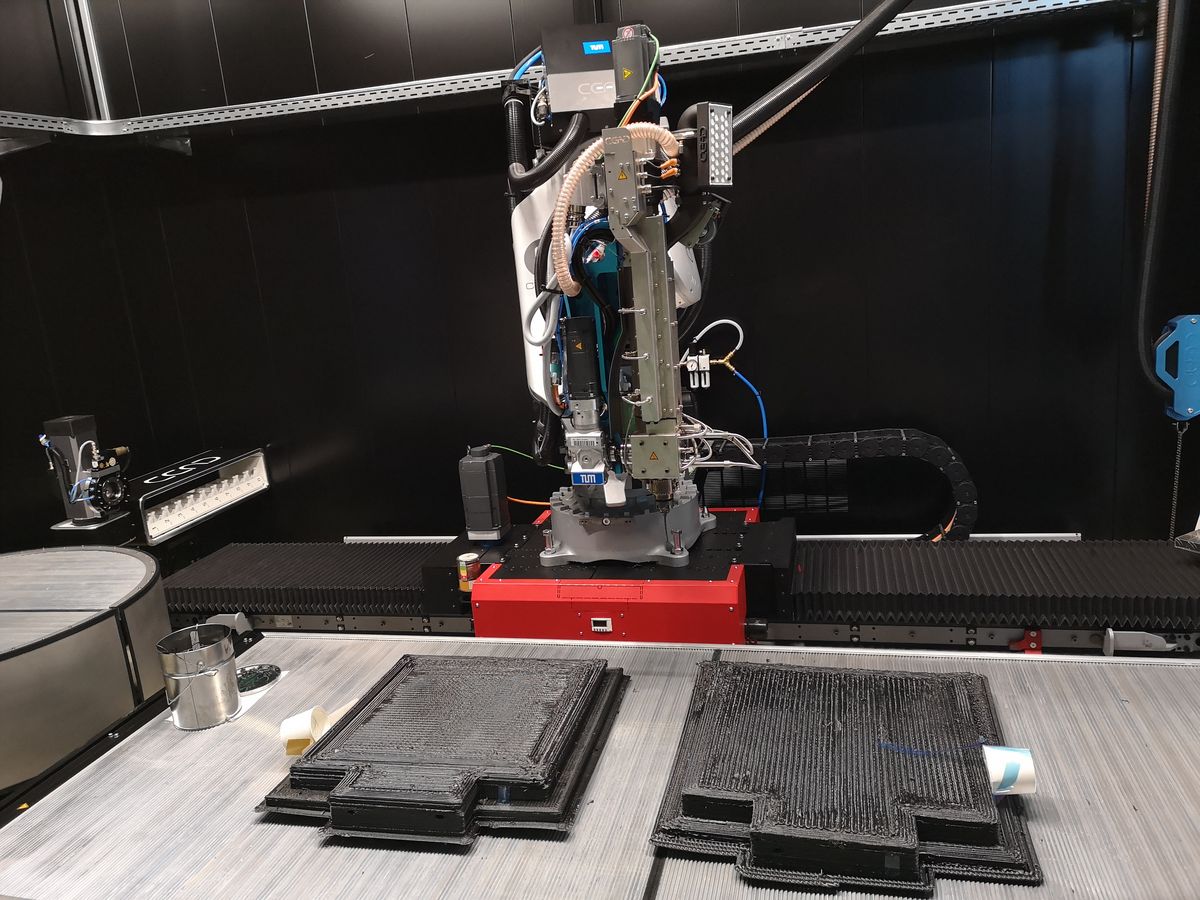
¿Máquina CEAD en otros proyectos?
“Estamos postulando para un proyecto en herramientas aeroespaciales que comienza el próximo año con GKN Aerospace Deutschland (Munich) usando la máquina CEAD y polietersulfona (PESU)”, dice Consul. [Nota:GKN en Alemania fabrica aletas de ala de material compuesto para el A330 y A350, así como alerones para la familia de aviones comerciales Bombardier Global.] “CEAD será parte de este responsable del desarrollo de máquinas para fibras de carbono continuas. También estamos planeando utilizar la máquina CEAD internamente para hacer prototipos de moldes para RTM que de otra manera se habrían subcontratado. Nos brinda un beneficio al acelerar el trabajo ”.
El cónsul señala que PESU tiene una Tg más alta que PAEK. “También es amorfo, no semicristalino, por lo que debería ser más fácil de imprimir, aunque la resistencia a la fluencia podría ser un problema. Lo que estamos tratando de hacer es evitar la PEI (polieterimida). En el pasado, analizamos el tema de la unión del PEI a la resina epoxi. RTM6 [epoxi para RTM] disuelve el PEI, lo que genera una buena adhesión entre los dos. Esto es exactamente lo que no desea en los moldes impresos en 3D que necesitan liberar las piezas, no pegarse a ellas ".
Futuros compuestos impresos en 3D industriales (y volantes)
Al discutir algunos de los otros proyectos que LCC está llevando a cabo en la fabricación aditiva, le pregunto al Cónsul ¿qué ha retenido al CFRP en los exoesqueletos? “Debido a que los exoesqueletos deben adaptarse a cada usuario, las partes están especializadas, por lo que el volumen no es grande”, responde. “Nuestro proyecto tiene como objetivo permitir la producción de componentes de exoesqueleto de miembros inferiores específicos del paciente para permitir la producción de un exoesqueleto específico del paciente en menos de 24 horas. Estos exoesqueletos respaldarán la rehabilitación de los pacientes con accidente cerebrovascular en función de sus perfiles biofísicos y necesidades únicas de rehabilitación médica ". (Consulte el artículo de CW, "El exoesqueleto de C-FREX depende de CFRP ...")
“La gente tiene el concepto de que la impresión 3D puede imprimir cualquier pieza, pero primero hay que tener experiencia con la impresión 3D y con materiales compuestos. Por ejemplo, a menudo hay problemas con la adhesión capa a capa y la anisotropía que deben entenderse. Las piezas compuestas impresas en 3D no tendrán el mismo diseño que las que se fabrican actualmente con plástico y metal ".
Señala que todavía hay problemas que superar para el uso de compuestos impresos en 3D para la producción de piezas de aviones de alto rendimiento, por ejemplo:¿Cómo se diseñan estas piezas para la fabricación aditiva? ¿Cómo identifica las piezas en las que la fabricación aditiva aporta valor? “Las herramientas aeroespaciales son el campo principal de aplicaciones que nuestro equipo está analizando en este momento”, dice Consul. “La impresión 3D del molde encaja bien. Estos moldes deben resistir las mismas condiciones de curado que las piezas, pero hay menos riesgo asociado con los moldes que con las piezas voladoras. Un buen ejemplo son los refuerzos de nervios para alas, donde hay un gran número de piezas diferentes pero no muchos ciclos por pieza. Entonces, esta es una buena forma de generar experiencia con la tecnología. Es demasiado pronto para probar piezas estructurales que volarán. Apuntaremos a esto a largo plazo, pero las herramientas de impresión nos permitirán lograr que el proceso de impresión 3D sea lo suficientemente estable con propiedades de alto rendimiento y también desarrollar la capacidad de predecir con precisión estas piezas y procesos en simulación ”.
Resina
- Por qué la impresión 3D y el software son cruciales para la transformación digital
- Solución de problemas de mantenimiento:más que prueba y error
- Soluciones de impresión 3D para empresas de petróleo y gas
- DSM y Nedcam desarrollarán nuevas aplicaciones para la impresión 3D de gran tamaño
- Masterbatches de color acetal para automoción y más basados en portadores de bajas emisiones
- Automatización para IML y moldes apilables
- Victrex y Bond se asocian para la impresión 3D de piezas PAEK
- Consejos para moldes de impresión 3D
- Consejos para el mecanizado CNC de titanio:aeroespacial y más
- Formlabs ayudará a que la impresión 3D sea más accesible para las pymes
- SIGRABOND® Chemical CFRP para componentes y conjuntos