Reduciendo la brecha entre CFRP y CMC
Los materiales que permiten estructuras de alto rendimiento a temperaturas de servicio superiores a 500 ° F / 230 ° C son limitados. Las opciones son básicamente metales como el titanio y aleaciones como Inconel, poliimidas (PI) o composites de matriz cerámica (CMC). Todos estos son significativamente más costosos que los compuestos convencionales de polímero reforzado con fibra de carbono (CFRP), pero el CMC ha ganado interés debido a su baja densidad, aproximadamente un tercio de la de Inconel y la mitad de la de titanio. La desventaja de CMC ha sido los largos tiempos de procesamiento necesarios para fabricar piezas, poco menos de 30 días, según un artículo de abril de 2019 en el American Ceramic Society Bulletin . .
Sin embargo, Pyromeral (Barbery, Francia) ha desarrollado una familia de productos que cierra esta brecha, ofreciendo un rendimiento de hasta 1.500 ° C con un procesamiento más parecido al CFRP, produciendo piezas en aproximadamente una semana. “Hemos desarrollado una química novedosa que permite matrices de vitrocerámica avanzadas reforzadas con fibras continuas sin el largo paso de infiltración por fusión”, explica el director de marketing y ventas de Pyromeral, Guillaume Jandin. La compañía ofrece materiales PyroKarb, PyroSic y PyroXide reforzados con fibras de carbono de alto módulo, carburo de silicio y óxido de aluminio, respectivamente, típicamente en forma de tejidos de sarga de dos por dos, lo que da como resultado compuestos con una fracción de volumen de fibra (FVF) de 50 %.
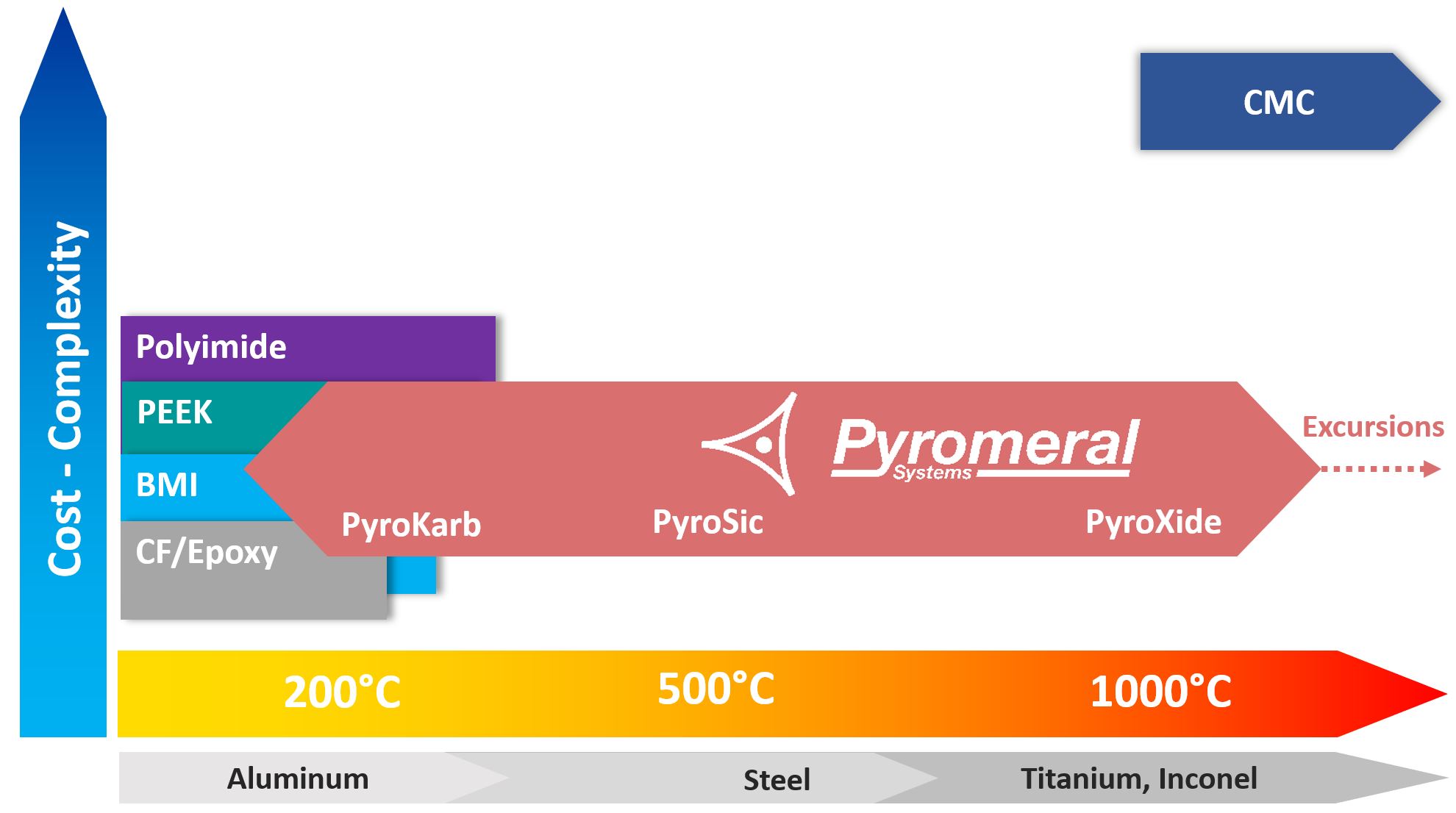
Factores de rendimiento térmico
Jandin explica que, si bien los tres materiales Pyromeral pueden funcionar por encima de los 1000 ° C durante menos de 1 hora, PyroKarb ofrece un servicio a largo plazo (menos de 1000 horas) a 200 ° C y hasta 100 horas a 500 ° C. PyroSic ofrece un servicio a largo plazo a 500 ° C y hasta 100 horas a 800 ° C. PyroXide ofrece un servicio corto hasta 1.500 ° C, muy cerca del rendimiento de Ox-Ox CMC, pero a un costo menor.
“El rendimiento térmico en piezas reales depende de muchos factores”, dice Jandin. “Estos incluyen el tipo de calor (radiativo, convectivo), si hay flujo de aire para ayudar a enfriar algunas áreas de la pieza y también qué propiedades estructurales se requieren, por ejemplo, un escudo térmico no estructural o una pieza semi-estructural. También es fundamental que los materiales funcionen a alta temperatura continua o en flashes de corta duración ”, añade. “PyroSic y PyroKarb funcionan bien con este último, como ciclos repetidos de 1000 ° C durante una décima de segundo, enfriar y luego repetir. Su bajo coeficiente de expansión térmica (CTE) de aproximadamente 3,10 -6 µm / m / K es un beneficio en comparación con los metales, que tienden a tener un CET superior a 10,10 -6 µm / m / K. Estos tipos de metales incurren en estrés para adaptarse a los ciclos térmicos rápidos de alta temperatura y se degradan debido a la fatiga, mientras que nuestros materiales no lo hacen ”.
Procesamiento similar al CFRP, aplicaciones de alta temperatura
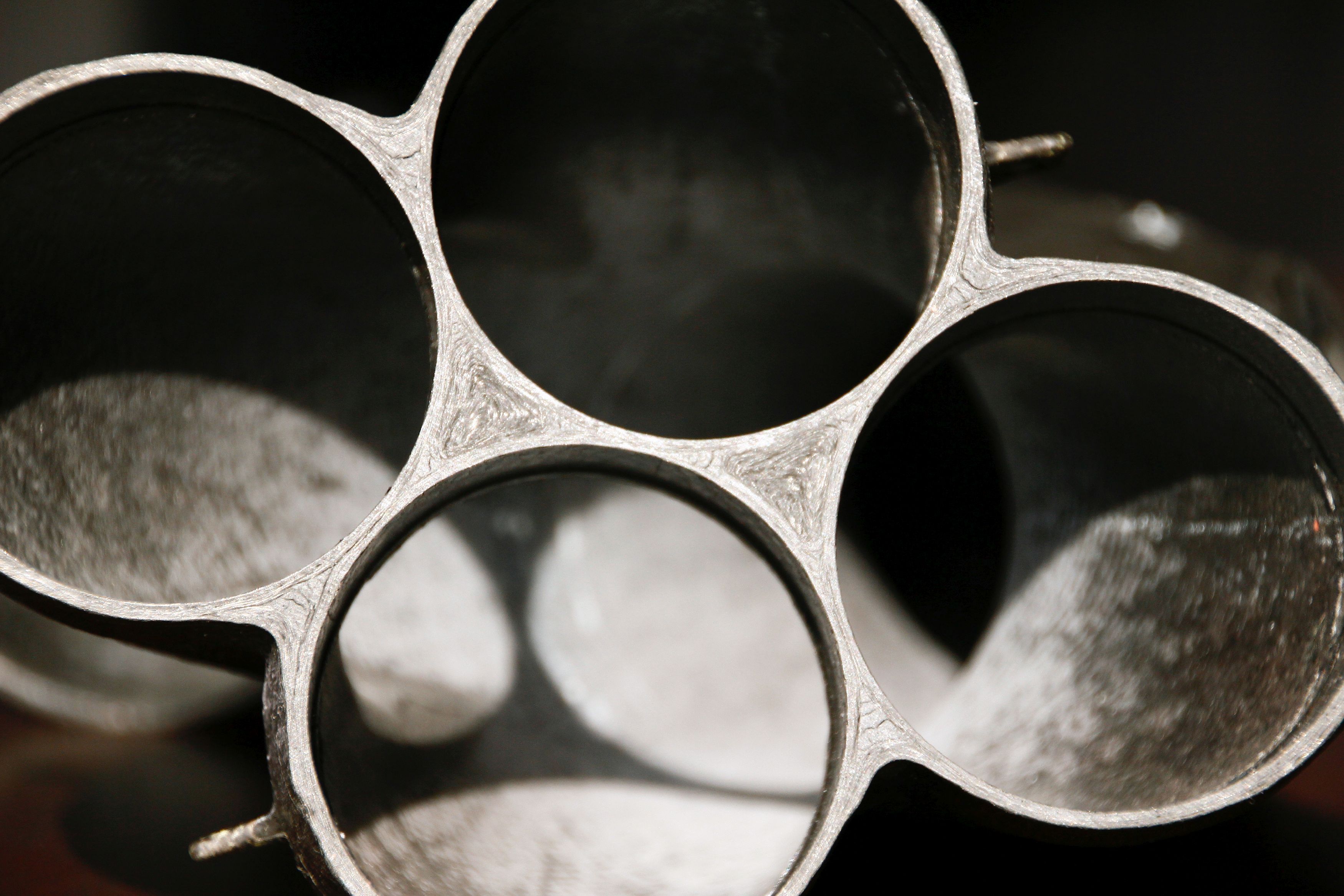
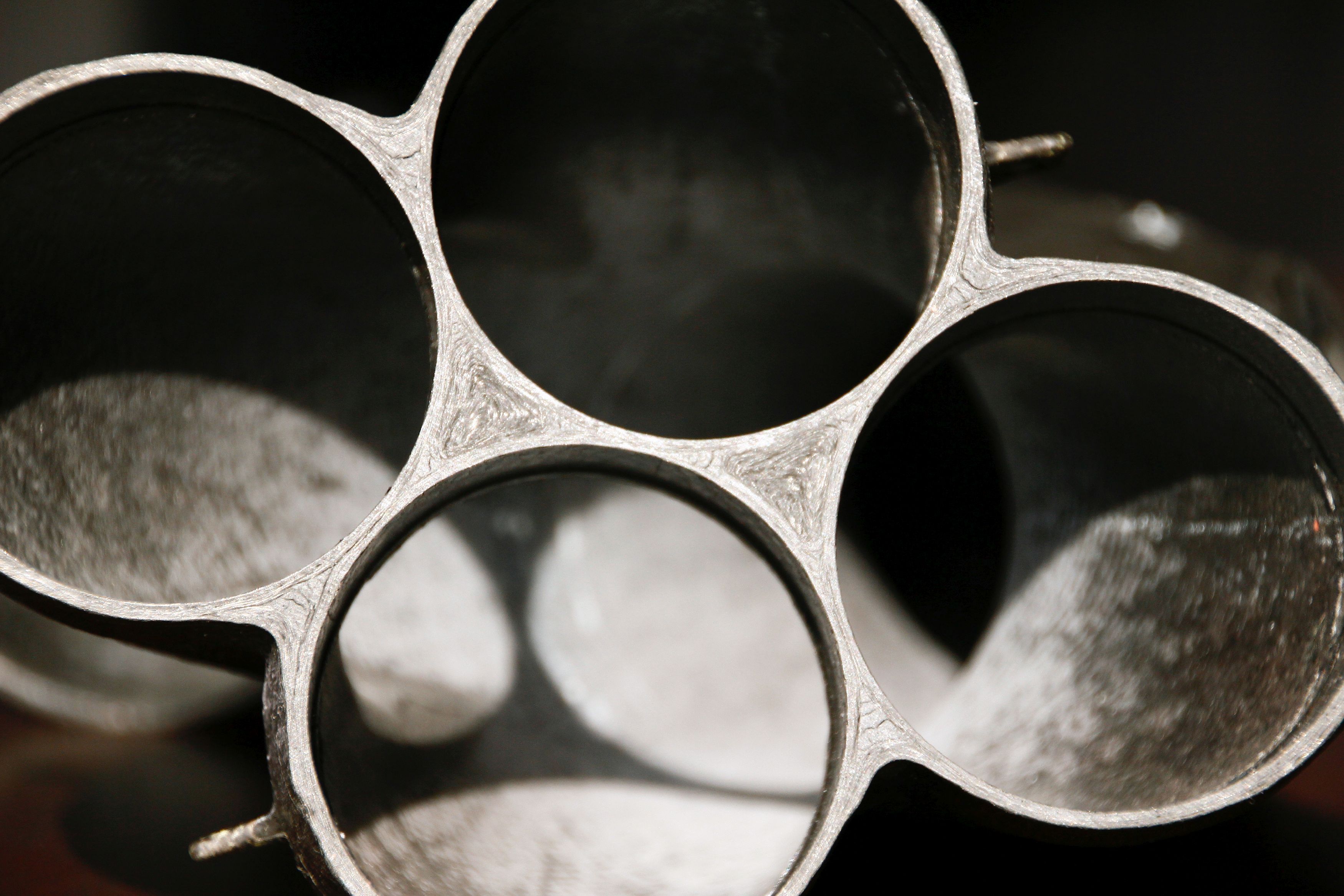
“Inventamos nuestros materiales de matriz para que fueran líquidos a temperatura ambiente y usamos máquinas de impregnación para crear preimpregnados”, señala Jandin. Los preimpregnados se colocan sobre herramientas CF / epoxi. “No trabajamos con herramientas de metal porque nuestra matriz es alcalina y podría reaccionar”, agrega. "El siguiente paso es la densificación en autoclave a 100 ° C y 6 bar durante aproximadamente 12 horas". Las piezas se desmoldan y luego proceden, de forma independiente, a través de un proceso térmico de dos etapas a 500-1.000 ° C que completa la ceramización de la matriz, lo que da como resultado componentes estructurales.
Pyromeral tuvo un éxito temprano en los autos de carrera de Fórmula 1. “Nuestros materiales se utilizan en escudos térmicos alrededor de los motores y también alrededor de los frenos, que alcanzan temperaturas de 500-700 ° C”, dice Jandin. “Durante la temporada de F1 2012-13, todos los coches, excepto Sauber, utilizaron nuestros materiales como piezas para dirigir los gases de escape del motor (800 ° C). Estas estructuras también resistieron la vibración tanto del escape como del chasis. Ahora tenemos componentes en todas las carreras de autos en F1 ”.
“Además, podemos integrar aislamiento de alto rendimiento en nuestros materiales para resistir caídas de 700 ° C con un espesor de 6 milímetros”, continúa. "Por ejemplo, fabricamos componentes que permiten que una caja de cambios de un coche de carreras de F1 hecha de CF / epoxi, que debe permanecer por debajo de 180 ° C, se asiente a 20 milímetros del turbocompresor a 900-950 ° C". Otras aplicaciones incluyen un escudo térmico PyroXide calificado para Ariane 5 vehículo de lanzamiento y piezas para el Ariane 6 , así como salidas de escape PyroSic para grandes vehículos aéreos no tripulados (UAV).
Pyromeral se ha asociado con Composite Resources (Rock Hill, S.C., EE. UU.) Para expandir su mercado en los EE. UU. (Consulte “La construcción de un nicho de fabricación de compuestos”). Las empresas son similares en tamaño y comparten una larga trayectoria en las carreras. "Nuestra experiencia en el diseño y fabricación de piezas complementa el enfoque de Pyromeral en la química y el rendimiento de los materiales", dice el director de desarrollo comercial de Composite Resources, Melvil Clauson.
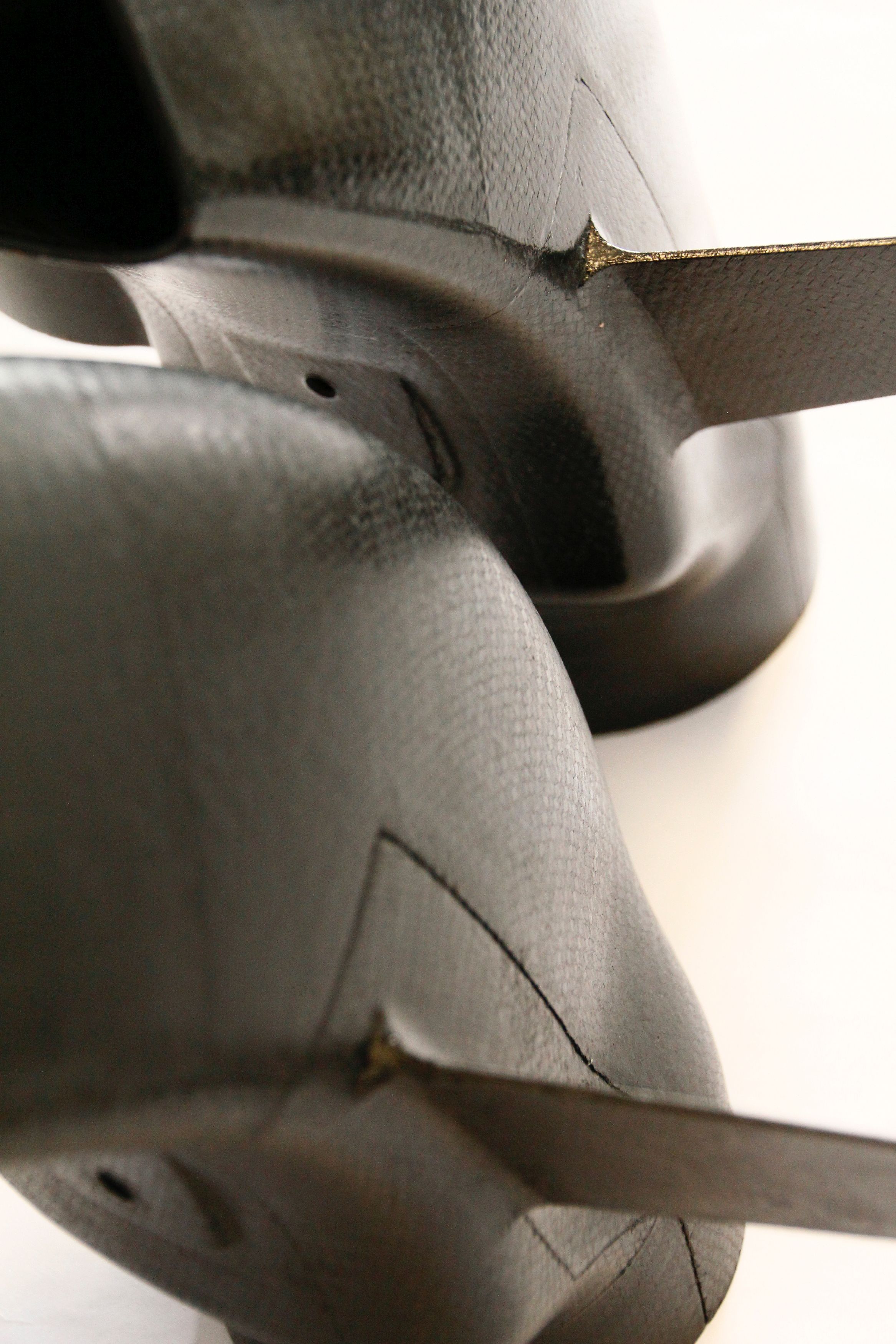
Las dos empresas están trabajando para satisfacer las demandas de los clientes de una mayor resistencia a la temperatura y para caracterizar la alta transparencia de radiofrecuencia (RF) de PyroXide para su uso en antenas y radomos. "Estamos viendo interés en los aviones supersónicos y las aplicaciones de defensa de base muy amplia más allá de la Fuerza Aérea, así como en los motores a reacción comerciales", señala Clauson.
“Los productos piromerales también miran hacia el futuro”, dice Clauson, “porque no contienen sustancias a base de petróleo, solo agua como solvente. Los otros componentes son minerales, lo que nos permite procesar piezas al final de su vida útil en polvo que se puede reutilizar en otras aplicaciones ”.
Resina
- ¿Cuál es la diferencia entre la nube y la virtualización?
- ¿Cuál es la diferencia entre sensor y transductor?
- Reduciendo la brecha entre ventas y producción para una gestión fluida del flujo de trabajo
- El vínculo entre confiabilidad y seguridad
- Mejora de la relación entre operaciones y mantenimiento
- Las diferencias entre los agentes de aduanas de México y los EE. UU.
- ¿Cuál es la diferencia entre Industria 4.0 e Industria 5.0?
- La diferencia entre motores de CC y CA
- Materiales de fricción industrial:la diferencia entre pastillas y zapatas de freno
- Las diferencias entre el código G y el código M
- La diferencia entre presión y caudal