Proceso de deposición y propiedades de recubrimientos compuestos de Ni-P-Al2O3 sin electrodos en una aleación de magnesio
Resumen
Para mejorar la resistencia a la corrosión y la resistencia al desgaste del recubrimiento de níquel-fósforo (Ni-P) no electrolítico sobre una aleación de magnesio (Mg). Ni-P-Al 2 O 3 los revestimientos se produjeron sobre una aleación de Mg a partir de un baño de revestimiento compuesto. El Al 2 óptimo O 3 la concentración se determinó por las propiedades del baño de galvanoplastia y los revestimientos. Evolución del crecimiento morfológico de Ni-P-Al 2 O 3 Se observaron recubrimientos compuestos en diferentes momentos utilizando un microscopio electrónico de barrido (SEM). Los resultados muestran que nano-Al 2 O 3 las partículas pueden ralentizar la reacción de reemplazo de Mg y Ni 2+ en la etapa inicial del proceso de deposición, pero casi no tiene ningún efecto sobre la velocidad del proceso de reducción autocatalítica de Ni-P. Las pruebas de anticorrosión y microdureza de los recubrimientos revelan que el Ni-P-Al 2 O 3 Los recubrimientos compuestos exhiben un mejor rendimiento en comparación con el recubrimiento de Ni-P debido al espaciado del plano de cristal y al tamaño de grano más apropiados de Ni-P-Al 2 O 3 revestimientos. La prueba de choque térmico indica que el Al 2 O 3 las partículas no tienen ningún efecto sobre la adherencia de los revestimientos. Además, la vida útil del baño de revestimiento compuesto es de 4.2 rotación de metal, lo que sugiere que tiene una aplicación potencial en el campo de las aleaciones de magnesio.
Antecedentes
Las aleaciones de magnesio (Mg) han atraído una gran atención e investigación científica debido a su baja densidad, alta resistencia específica y excelente maquinabilidad [1, 2]. Por lo tanto, las aleaciones de Mg se utilizan generalmente en los campos aeroespacial, electrónico y automotriz [3, 4]. Sin embargo, la aplicación de aleaciones de Mg se ha visto limitada debido a los indeseables defectos en la resistencia a la corrosión y al desgaste [5, 6]. Por lo tanto, se han desarrollado para las aleaciones de Mg métodos anticorrosión y antifricción de superficies, como película de oxidación de microarco, revestimiento de conversión química, pulverización térmica, deposición física de vapor, galvanoplastia y galvanoplastia [7,8,9, 10, 11, 12, 13].
El enchapado de níquel-fósforo (Ni-P) no electrolítico es una de las tecnologías de superficie más efectivas para las aleaciones de Mg, ya que tiene excelentes ventajas integrales de bajo costo, eficiencia, resistencia a la corrosión y resistencia al desgaste [14, 15]. Por lo tanto, el recubrimiento de Ni-P no electrolítico juega un papel importante en el campo anticorrosión de las aleaciones de Mg. Para mejorar aún más el rendimiento del revestimiento de Ni-P, nanopartículas, por ejemplo, SiC, ZrO 2 , TiO 2 , SiO 2 y Al 2 O 3 , etc., se añaden generalmente en un baño de galvanoplastia para preparar recubrimientos compuestos de nanopartículas de Ni-P [16,17,18,19,20]. Según estudios previos [20,21,22,23], el rendimiento del revestimiento de Ni-P se mejora de forma eficaz mediante nanopartículas. Aunque los recubrimientos compuestos de nanopartículas de Ni-P tienen un rendimiento relativamente alto en comparación con el recubrimiento de Ni-P, hay tres problemas que deben tenerse en cuenta. En primer lugar, las nanopartículas son fáciles de agregar y forman el centro activo en el baño de galvanoplastia no electrolítico, lo que reduce la estabilidad de la solución de galvanoplastia. En segundo lugar, los parámetros del proceso del baño de recubrimiento compuesto generalmente determinan el contenido y la distribución de nanopartículas en los recubrimientos, y también son factores clave para mejorar las propiedades de los recubrimientos. En tercer lugar, el proceso de co-deposición de nanopartículas con Ni-P es otro factor de influencia en las propiedades del recubrimiento. Por tanto, vale la pena prestar atención a estos factores. Nano-Al 2 O 3 las partículas son un abrasivo barato, que tiene una alta dureza y una buena estabilidad química [24, 25]. Se puede dispersar bien en el baño de niquelado no electrolítico. Por lo tanto, Ni-P-Al 2 O 3 Los recubrimientos compuestos se emplean generalmente como recubrimientos anticorrosión y antidesgaste para proteger el sustrato de acero o cobre. Sin embargo, solo unos pocos informes se centraron en el Ni-P-Al 2 electrolítico O 3 revestimiento sobre un sustrato de aleación de magnesio [20, 22, 26]. Además, el estudio del proceso de crecimiento del Ni-P-Al 2 O 3 el recubrimiento sobre aleaciones de Mg y la estabilidad del baño de revestimiento compuesto es bastante rara. Por lo tanto, más detalles sobre el rendimiento del baño compuesto y el proceso de co-deposición de Ni-P-Al 2 O 3 necesita ser estudiado.
En el presente trabajo, para mejorar aún más las propiedades del revestimiento de Ni-P sobre el sustrato de aleación de Mg, empleamos el sistema de sulfato de níquel y ácido láctico como sal principal y agente complejante, respectivamente, en el baño de galvanoplastia. Mientras tanto, nano-Al 2 O 3 Se añadió polvo al baño de galvanoplastia de Ni-P no electrolítico. Para obtener un baño de recubrimiento de material compuesto no electrolítico adecuado para la aleación de Mg AZ91D, se evaluaron los parámetros del proceso de este baño mediante la velocidad de deposición y las propiedades del recubrimiento. Además, se llevó a cabo una prueba de ciclo periódico para evaluar la vida útil y la estabilidad del baño de galvanoplastia en las condiciones óptimas del proceso. Estudiar el efecto de nano-Al 2 O 3 Se discutieron partículas sobre el proceso de crecimiento de los recubrimientos, el comportamiento de deposición y la estructura de fase del recubrimiento de Ni-P. Además, las propiedades, incluida la resistencia a la corrosión, la microdureza y la adhesión de los recubrimientos, se analizaron en función de la morfología y la estructura. Los resultados mostraron que las propiedades del Ni-P-Al 2 O 3 Los revestimientos compuestos eran preferibles a los del revestimiento Ni-P, y el baño de revestimiento compuesto no electrolítico tenía una buena estabilidad durante la vida útil. Por lo tanto, nuestros resultados en este trabajo son una referencia útil para la aplicación de recubrimientos compuestos de nanopartículas de Ni-P no electrolíticos en una aleación de Mg.
Métodos
Preparación de los recubrimientos compuestos
En este trabajo se empleó como material experimental la aleación de Mg fundida a presión AZ91D con un tamaño de 2 cm × 1 cm × 0,5 cm, que contiene composición química en% en peso:8,5 Al, 0,34 Zn, 0,1 Si, 0,03 Cu, 0,002 Ni , 0,005 Fe y 0,02 otros y el resto de Mg. El sustrato AZ91D fue pulido sucesivamente con no. Papel de 500 y 1000 SiC, enjuagado con agua desionizada y sumergido en solución alcalina durante 5 min a 65 ° C, seguido de decapado con ácido en una solución de ácido crómico (CrO 3 200 g / L) durante 60 s. Después de eso, el sustrato de aleación de Mg se sumergió en una solución de ácido fluorhídrico con una concentración de 380 mL / L para el tratamiento de activación aproximadamente 10 min. El sustrato de Mg se limpió con agua desionizada en cada paso. La composición básica del baño y las condiciones de funcionamiento del niquelado no electrolítico para aleaciones de magnesio se ilustraron de la siguiente manera:35 g / L NiSO 4 ⋅6H 2 O, 35 g / L de ácido láctico, 30 g / L de Na 2 H 2 PO 2 ⋅H 2 O, 10 g / L de NH 4 HF 2 , 3 mg / L de agente estabilizador, pH 4.5 ~ 7.0 y temperatura 70 ~ 90 ° C. El baño de galvanoplastia no electrolítico se mantuvo en un vaso de precipitados de vidrio, que se colocó en un baño de agua controlado por termostato. Se utilizó un agitador eléctrico con pantalla digital para proporcionar fuerza de agitación. El tamaño de partícula promedio del nano-Al 2 O 3 partículas es de aproximadamente 50 nm. El nano-Al 2 O 3 las partículas se dispersaron adecuadamente en el baño bajo la condición de onda ultrasónica antes de la galvanoplastia.
Pruebas para la tasa de deposición y la estabilidad de los baños de galvanoplastia
Estudiar el efecto de nano-Al 2 O 3 partículas en la tasa de deposición del baño de niquelado no electrolítico, la tasa de deposición se expresa en Eq. (1).
$$ v =\ frac {\ Delta w \ times {10} ^ 4} {\ rho St} $$ (1)donde v , ρ , S , t y △ w representan la tasa de deposición (μm / h), la densidad del revestimiento de Ni-P (~ 7,9 g / cm 3 ), área de superficie del sustrato de Mg (cm 2 ), tiempo de deposición (h) y peso del revestimiento (g), respectivamente. Además, el contenido de nano-Al 2 O 3 Las partículas en el recubrimiento se estimaron mediante el método de pesaje utilizando una balanza electrónica (AR2140, Ohaus). Para evaluar la estabilidad del baño de galvanoplastia no electrolítico, se empleó una prueba de ciclo periódico (o volteo de metal, MTO) para evaluar la vida útil y la estabilidad del baño. Aquí, 1 MTO ha definido que el peso de la deposición de Ni es equivalente a la concentración inicial de Ni 2+ en la bañera. Tomando 1 L de baño de enchapado como ejemplo, se obtienen aproximadamente 7,8 g de Ni del baño \ (\ left ({C} _ {{\ mathrm {Ni}} ^ {2 +}} =7.8 \ kern0.5em \ mathrm {g} / \ mathrm {L} \ right) \) con respecto a 1 MTO. Además, una nueva solución de mezcla (\ ({\ mathrm {Ni}} ^ {2 +}:{\ mathrm {H}} _ 2 {\ mathrm {PO}} _ 2 ^ {2 -} =1:3 \) en relación molar) se añadió al baño de galvanoplastia cuando el baño tenía una tasa de deposición baja. La prueba de estabilidad finalizó hasta la descomposición del baño de galvanoplastia. Por tanto, la expresión de MTO se puede presentar como Eq. (2).
$$ \ mathrm {MTO} =M / m $$ (2)M y m representan el peso de deposición acumulativo de Ni y la concentración de Ni 2+ en el baño de galvanoplastia, respectivamente.
Caracterización de materiales
La morfología de la superficie del revestimiento se observó utilizando un microscopio electrónico de barrido (SEM, Hitachi S-4800). La estructura del recubrimiento fue estudiada por el difractómetro de rayos X (XRD, D / Max-2200, Japón) con un CuK α radiación ( γ =0,154 nm).
Medición electroquímica
Se realizó una prueba de polarización potenciodinámica en un analizador electroquímico (CHI800, Chenhua, China). El experimento electroquímico se llevó a cabo en una solución acuosa de NaCl al 3,5% en peso utilizando una configuración clásica de tres electrodos, que consistía en un electrodo de trabajo (muestra, 1 cm 2 ), un contraelectrodo (platino) y uno de referencia (electrodo de calomelanos saturado). Durante el experimento de barrido potenciodinámico, la muestra se sumergió primero en la solución de electrolito durante 30 minutos para estabilizar el potencial de circuito abierto ( E 0 ). El gráfico de Tafel se transformó a partir de los datos registrados y la densidad de la corriente de corrosión ( i corr ) se determinó extrapolando la sección en línea recta de las líneas Tafel anódicas y catódicas. La velocidad de barrido del experimento fue de 5 mV / sy se realizó a 25 ° C. Las microdurezas de la aleación de magnesio con varios recubrimientos compuestos se evaluaron utilizando un probador de microdureza HXD-1000 con un indentador Vicker a una carga de 100 gy un tiempo de duración de 15 s. Se llevó a cabo una prueba de choque térmico para evaluar la adherencia de los revestimientos [23]. Se describió de la siguiente manera:en una atmósfera de aire, el sustrato de Mg con revestimiento de Ni-P o Ni-P-Al 2 O 3 El revestimiento se colocó en un horno de resistencia de caja de alta temperatura y se calentó a 250 ± 10 ° C a una velocidad de calentamiento de 20 ° C min −1 luego se enfría en agua fría. Este proceso se repitió 20 veces.
Resultados y discusión
La Figura 1 muestra los efectos de la concentración de nano-Al 2 O 3 partículas, velocidad de agitación, pH y temperatura en la tasa de deposición, y Al 2 O 3 contenido de revestimientos compuestos. Como se ve en la Fig. 1a, la tasa de deposición tiene una ligera disminución con el aumento de Al 2 O 3 concentración de partículas de 0 a 15 g / L. Por otro lado, el Al 2 O 3 El contenido de los revestimientos compuestos aumenta gradualmente mientras que la concentración de Al 2 O 3 partículas aumenta de 0 a 10 g / L. Sin embargo, en cambio, disminuye cuando la concentración de Al 2 O 3 partícula es superior a 10 g / L. Este cambio se debe a la agregación de partículas a altas concentraciones, lo que debilita el comportamiento de codeposición de Ni-P con Al 2 O 3 . En la Fig. 1b, cuando la velocidad de agitación se establece en 300 ~ 400 rpm, la tasa de deposición y el Al 2 O 3 El contenido de los revestimientos compuestos es de 18 μm / hy 3,6%, respectivamente. Los resultados demuestran que la dispersividad de Al 2 O 3 La partícula en el baño de galvanoplastia es mejor en este rango de velocidad de agitación. En cuanto al baño de recubrimiento compuesto ácido, el efecto del valor de pH sobre la velocidad de deposición y el Al 2 O 3 El contenido de revestimientos se muestra en la Fig. 1c. La velocidad máxima de deposición es de hasta 18,5 μm / h cuando el valor de pH está dentro del rango de 6,0 ~ 6,5, mientras que el Al 2 O 3 el contenido de recubrimientos casi aumenta con el valor del pH. La Figura 1d muestra que tanto la tasa de deposición como el Al 2 O 3 El contenido de revestimientos compuestos aumenta con la temperatura, ya que se mejora la actividad de iones y partículas, y la velocidad de reacción del baño compuesto también se acelera a alta temperatura. Sin embargo, la estabilidad del baño de galvanoplastia y la porosidad de los revestimientos empeoran a altas temperaturas (> 85 ° C) [13, 22]. Con base en los resultados del análisis anterior, los parámetros preliminares del proceso y las condiciones operativas del baño compuesto se determinan para la aleación de magnesio, es decir, 35 g / L de NiSO 4 ⋅6H 2 O, 35 g / L de ácido láctico, 30 g / L de Na 2 H 2 PO 2 ⋅H 2 O, 10 g / L de NH 4 HF 2 , 10 g / L de nano-Al 2 O 3 partículas, 3 mg / L de agente estabilizador, pH =6,0 ~ 6,5, T =85 ° C, y velocidad de agitación a 350 rpm.
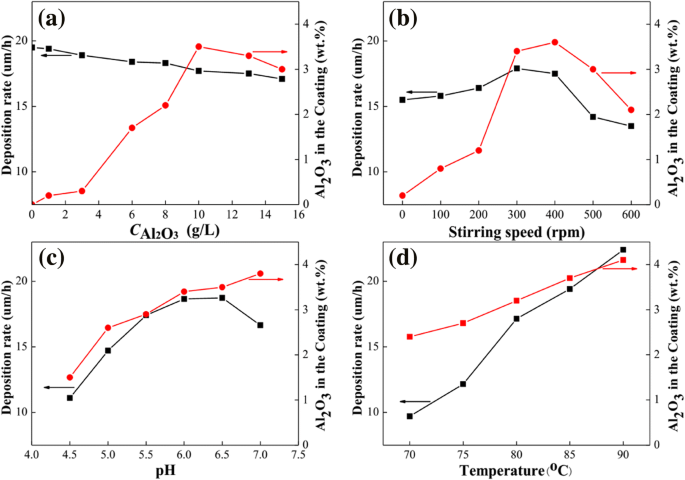
Efectos de los parámetros del proceso sobre la velocidad de deposición y el Al 2 O 3 contenido de revestimientos
Para investigar el proceso de deposición de Ni-P-Al 2 O 3 recubrimientos, el cambio de las imágenes de morfología de la superficie de la aleación de magnesio con el tiempo de reacción de deposición se muestra en la Fig. 2. Para el análisis comparativo, la Fig. 2a-c representa el proceso de deposición del recubrimiento de Ni-P, mientras que la Fig. 2d-f muestra el co -proceso de deposición de Ni-P-Al 2 O 3 (3,6% en peso) de revestimientos compuestos. La figura 2a es la imagen morfológica de la inmersión del sustrato de Mg en el baño de galvanoplastia durante 0,5 min, con una gran cantidad de partículas de estructura cúbica distribuidas en su superficie. Estas partículas cúbicas se confirman como MgF 2 , que se forma principalmente en el proceso de activación de la HF, de acuerdo con los informes de la literatura [23, 27]. Sin embargo, la morfología de la imagen de la Fig. 2d es claramente diferente de la de la Fig. 2a. La principal diferencia muestra que el MgF 2 las partículas de la figura 2d son menores que las de la figura 2a. Además, muchos nano-Al 2 O 3 se observan partículas en la superficie del sustrato de Mg. El cambio de morfología se origina en Al 2 O 3 Partículas que impactan continuamente en la superficie de la aleación de magnesio a alta temperatura y proceso de agitación. Cuando el tiempo de recubrimiento de Ni-P no electrolítico es de hasta 5 min, como se ve en la Fig. 2b, las partículas de Ni crecen gradualmente y luego cubren toda la superficie de la aleación de magnesio. Pero para el recubrimiento de material compuesto no electrolítico (ver Fig. 2e), las partículas de Ni más grandes y nano-Al 2 O 3 se observan partículas en la superficie de la aleación de magnesio, y el Ni-P-Al 2 O 3 Los recubrimientos no cubren completamente el sustrato de Mg en 5 min. Indica que la tasa de crecimiento de Ni-P-Al 2 O 3 recubrimientos en el baño de material compuesto es más bajo que el recubrimiento de Ni-P en el baño sin Al 2 O 3 partículas. Ésta es una evidencia que respalda la causa de la baja tasa de deposición en el baño de revestimiento compuesto. Cuando el tiempo de galvanoplastia no electrolítico se lleva a cabo durante 30 min, la morfología del recubrimiento de Ni-P y Ni-P-Al 2 O 3 los revestimientos se muestran en la Fig. 2c, f, respectivamente. En cuanto al revestimiento de Ni-P, la superficie presenta una estructura densa y nodular con un tamaño medio de 3 μm. Pero en la Fig. 2f, el tamaño nodular promedio de Ni-P-Al 2 O 3 Los revestimientos compuestos es aparentemente más pequeño que el revestimiento de Ni-P. Además, se puede observar claramente que el nano-Al 2 O 3 partículas incrustadas en el revestimiento de Ni-P. Es importante destacar que, desde el punto de vista de la distribución de la superficie de Al 2 O 3 partículas, la distribución de Al 2 O 3 partículas en la Fig. 2f es significativamente menor que en la Fig. 2c, e. Este resultado indica que la deposición de Ni-P es dominante, mientras que la deposición de Al 2 O 3 las partículas se vuelven subordinadas después de un tiempo de reacción de deposición de 5 min. También se pueden obtener inferencias similares a partir del contenido relativo de Al 2 O 3 partículas en los revestimientos (Fig. 1). En otras palabras, el efecto de Al 2 O 3 Las partículas en el proceso de deposición están presentes principalmente en la etapa inicial del niquelado no electrolítico.
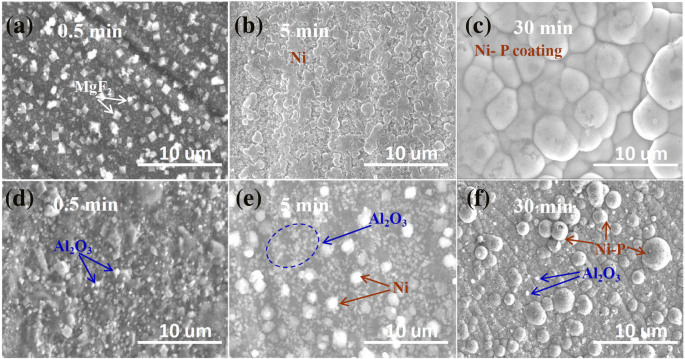
Morfología de la superficie del revestimiento de Ni-P (arriba, a - c ) y Ni-P-Al 2 O 3 revestimientos compuestos (fondo, d - f ) en diferentes momentos de deposición
Para explorar el efecto de nano-Al 2 O 3 partículas en la estructura del recubrimiento de Ni-P, los patrones XRD de la aleación AZ91D Mg, recubrimiento de Ni-P y Ni-P-Al 2 O 3 Los revestimientos compuestos se analizan en la Fig. 3. Como se ve en la Fig. 3, el ángulo de difracción de los planos cristalinos de la aleación de magnesio se concentra principalmente en el rango de 30 ° ~ 70 °, por ejemplo, α (10 \ (\ overline {1} \) 0) 32,2 °, α (0002) 34,2 °, β (10 \ (\ overline {1} \) 1) 36,8 °, etc. En cuanto a la aleación de Mg revestida con revestimiento de Ni-P, el patrón de difracción del revestimiento de Ni-P exhibe un pico que se ensancha y una difracción de alta intensidad a 44,7 ° que puede atribuirse al plano cristalino (111) de una fase cúbica centrada en la cara (fcc) de níquel (Tabla 1) [28]. Además, la existencia de un pico tan ancho indica la formación de un revestimiento de Ni-P con una estructura cristalina amorfa mixta. Después de recubrir el Ni-P-Al 2 O 3 (3,6% en peso) de revestimientos compuestos, se pueden encontrar evidentemente tres nuevos picos de difracción a 25,6 °, 43,5 ° y 73,2 °. Estos picos se atribuyen a los picos de difracción característicos de Al 2 O 3 en comparación con la tarjeta PDF no. 88-0826. Por lo tanto, Ni-P-Al 2 O 3 Los revestimientos compuestos se depositan sobre la superficie de la aleación de Mg. Además, el pico de difracción del plano cristalino (111) de Ni se desplaza a 45,2 ° (ver Tabla 1) en Ni-P-Al 2 O 3 recubrimientos compuestos, lo que sugiere nano-Al 2 O 3 las partículas tienen cierta influencia en el espacio de Ni en el plano cristalino (111). Según la fórmula de Bragg, nλ =2 d pecado θ ( n =1, 2, 3, ..., λ = 0,154 nm, d y θ representan el espaciado interplanar y el ángulo de difracción, respectivamente), el (111) espaciado del plano cristalino de Ni se reduce aproximadamente un 3% en Al 2 O 3 partículas. Además, tanto los picos de difracción (111) de Ni en el revestimiento de Ni-P y Ni-P-Al 2 O 3 los revestimientos compuestos se ajustaron mediante la función de Gauss, respectivamente. El resultado muestra que el ancho completo a la mitad del máximo (FWHM) de este pico de difracción en Ni-P-Al 2 O 3 recubrimientos compuestos es más amplio que en el recubrimiento de Ni-P (Tabla 1). Según la fórmula de Scherrer, D = Kγ / B porque θ ( D , K , B representan grano cristalino, constante de Scherrer y FWHM, respectivamente), el grano cristalino de Ni-P-Al 2 O 3 los recubrimientos compuestos se reducen aproximadamente un 8% en Al 2 O 3 partículas en comparación con el revestimiento de Ni-P. Esto implica que nano-Al 2 O 3 Las partículas refinan el tamaño del grano cristalino de Ni, lo que es consistente con el resultado observado de SEM anterior.
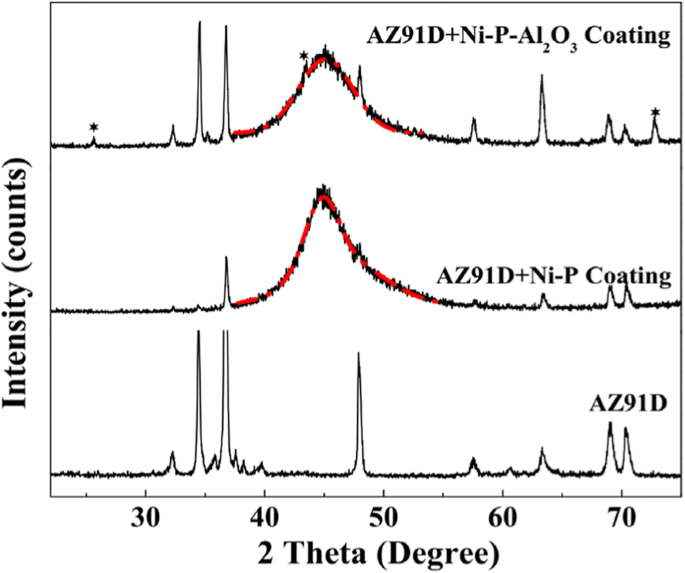
Patrones XRD del sustrato AZ91D, revestimiento de Ni-P y Ni-P-Al 2 O 3 (3.6% en peso) recubrimientos compuestos
La Figura 4 y la Tabla 2 muestran las curvas de polarización y los parámetros anticorrosión del sustrato de aleación de Mg AZ91D, revestimiento de Ni-P y Ni-P-Al 2 O 3 revestimientos compuestos en una solución acuosa de NaCl al 3,5% en peso a temperatura ambiente, respectivamente. La reacción del cátodo en las curvas de polarización corresponde al desprendimiento de hidrógeno, mientras que las curvas de polarización anódica son los procesos de reacción característicos más importantes de la resistencia a la corrosión [29]. Para el sustrato de aleación AZ91D Mg, se observa un proceso anódico controlado por activación cuando el potencial aplicado aumenta en la región anódica. Además, se disuelve seriamente en solución de electrolitos, y su potencial de corrosión ( E corr ) se lee en - 1,47 V. Pero para E corr del recubrimiento de Ni-P, muestra un cambio positivo significativo a - 0,51 V en comparación con el sustrato de aleación de Mg (- 1,47 V), y la densidad de corriente de corrosión ( i corr ) evidentemente disminuye de 1.4 × 10 −4 A / cm 2 del sustrato a 3,1 × 10 −6 A / cm 2 del revestimiento de Ni-P (ver Tabla 2). En cuanto a Ni-P-Al 2 O 3 (1,7 ~ 4,2% en peso) revestimientos compuestos, aquí, el Al 2 O 3 El contenido de los revestimientos se obtiene mediante el método de pesaje. Como se ve en la Tabla 2, todas las E corr del desplazamiento positivo del revestimiento compuesto y i corr de los recubrimientos compuestos disminuyen en comparación con el recubrimiento de Ni-P, lo que sugiere que Ni-P-Al 2 O 3 los revestimientos tienen un mayor rendimiento en cuanto a resistencia a la corrosión. Aquí, el recubrimiento de Ni-P con 3.6% en peso de Al 2 O 3 muestra la E más alta corr (- 0,35 V) y i más bajo corr (4,5 × 10 −7 A / cm 2 ). Sin embargo, el E corr y i corr de Ni-P-Al 2 O 3 (4,2% en peso) se cambian a - 0,41 V y 1,0 × 10 −6 A / cm 2 , respectivamente. Puede ser que Al 2 O 3 Las partículas aumentan la porosidad del revestimiento de Ni-P y reducen el rendimiento de los revestimientos compuestos. Por lo tanto, el Al 2 O 3 El contenido de revestimientos compuestos tiene un efecto importante sobre la resistencia a la corrosión de los revestimientos compuestos. También está relacionado con la estructura, incluido el espaciado del plano cristalino y el tamaño de grano de los recubrimientos (Fig. 3).
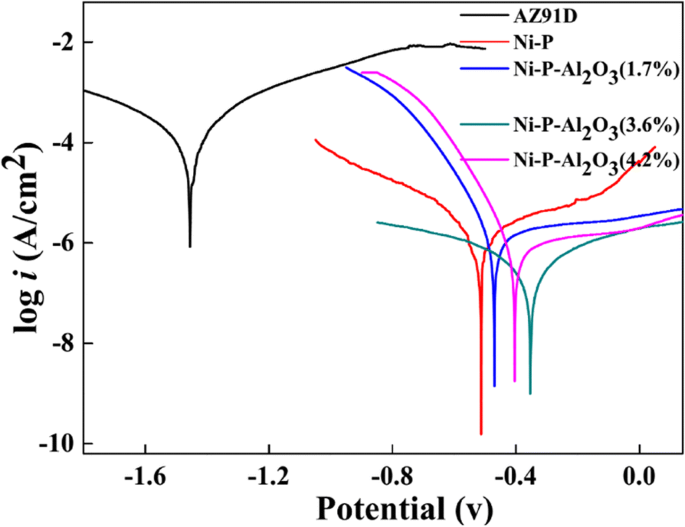
Curvas de polarización del sustrato AZ91D, el revestimiento de Ni-P y el Ni-P-Al 2 O 3 revestimientos compuestos
Para probar la microdureza de los recubrimientos, se determinó el espesor promedio de todos los recubrimientos en 18 μm, que se estimó mediante la tasa de deposición y el tiempo de deposición. Los resultados de las pruebas de microdureza del sustrato de aleación de Mg y los recubrimientos con diferentes Al 2 O 3 Los contenidos se muestran en la Fig. 5. Como se ve en la Fig. 5, la microdureza de la aleación AZ91D Mg desnuda es de solo 120 HV, mientras que la microdureza del sustrato de aleación de Mg recubierto con un recubrimiento de Ni-P es de hasta 520 HV. Es más alto que el sustrato alrededor de 400 HV, lo que indica que el revestimiento de Ni-P puede mejorar eficazmente la dureza del revestimiento del sustrato. Como resultado, la resistencia al desgaste del sustrato de aleación de Mg se ve reforzada por el revestimiento de Ni-P. Además, el Ni-P-Al 2 O 3 Los revestimientos compuestos muestran una tendencia considerable al aumento de la microdureza cuando el contenido de Al 2 O 3 en el revestimiento aumenta de 0 a 3,6% en peso. Por lo tanto, Ni-P-Al 2 O 3 (3.6%) los recubrimientos compuestos muestran el valor de dureza más alto a 638 HV. La razón se origina en nano-Al 2 O 3 partículas que optimizan la estructura de fase (ver Fig. 3) de la aleación de Ni-P y mejoran la microdureza de los recubrimientos. Sin embargo, el contenido de Al 2 O 3 en los revestimientos compuestos alcanza el 4,2% en peso y, en cambio, la microdureza de los revestimientos disminuye a 576 HV. Esto significa que un mayor contenido de nanopartículas puede afectar las estructuras cristalinas de Ni-P y provocar un rendimiento desfavorable de los revestimientos compuestos.
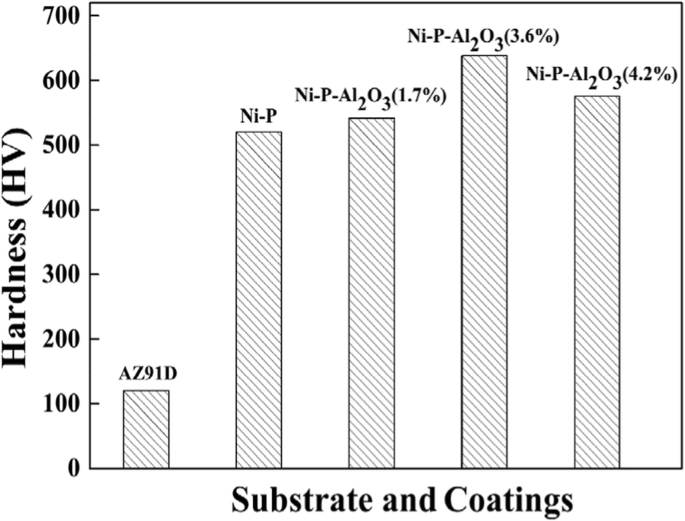
Dureza del sustrato AZ91D, el revestimiento de Ni-P y el Ni-P-Al 2 O 3 revestimientos compuestos
La adhesión entre los revestimientos y el sustrato de aleación de Mg se llevó a cabo mediante una prueba de choque térmico de acuerdo con la sección del experimento. Mediante pruebas de 20 ciclos, tanto el revestimiento de Ni-P como el de Ni-P-Al 2 O 3 Recubrimientos compuestos bien adheridos al sustrato de aleación de Mg. Los defectos, como grietas, ampollas y desconchado, no se observaron durante el proceso de prueba, lo que indica que el Ni-P o Ni-P-Al 2 O 3 Los revestimientos tenían una buena adherencia con el sustrato de aleación de Mg contra el proceso de choque térmico. Además, también se observaron imágenes de morfología de la sección transversal entre los recubrimientos y el sustrato de aleación de Mg utilizando SEM. Como se observa en la Fig. 6, se manifiesta además que no hay ningún defecto aparente entre los recubrimientos y el sustrato a través de la prueba de choque térmico. Es importante destacar que la prueba de choque térmico y la observación de la sección transversal indican que nano-Al 2 O 3 las partículas no tienen ningún efecto sobre la adhesión de los revestimientos compuestos.
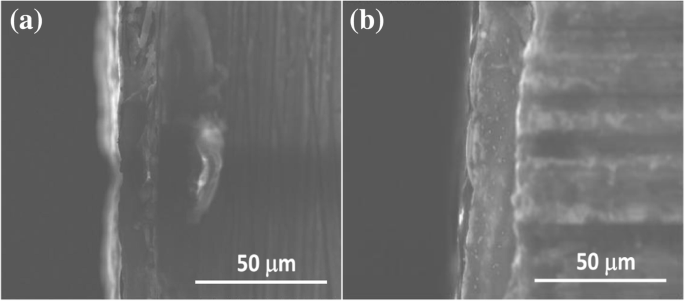
Imágenes de morfología de sección transversal del revestimiento de Ni-P ( a ) y Ni-P-Al 2 O 3 (3,6% en peso) revestimientos compuestos ( b )
En el presente trabajo, baños de galvanoplastia de 1 L sin y con nano-Al 2 O 3 Se prepararon partículas (10 g / L), respectivamente. Aquí, el contenido de fuente de níquel inicial en el baño de galvanoplastia se calculó como 7,8 gy la capacidad de carga del baño se estableció en 0,5 dm 2 / L. De acuerdo con las reglas de la prueba de ciclo periódico (véase la sección experimental), se evaluó en primer lugar el MTO del baño de galvanoplastia de Ni-P no electrolítico y se obtuvieron aproximadamente 48,2 g de aleación de Ni-P. Aquí, el contenido de níquel del 90% se identificó en el revestimiento de Ni-P mediante el análisis de EDS (ver Fig. 7). Por tanto, el contenido de níquel en el revestimiento se puede calcular en 43,4 g. Es decir, el MTO del baño de galvanoplastia sin Al 2 O 3 partículas es 5.6 usando la ecuación. (2). En cuanto al Ni-P-Al 2 no electrolítico O 3 baño de recubrimiento compuesto, un total de 38,8 g de Ni-P-Al 2 O 3 los revestimientos se depositaron desde el baño de material compuesto. De manera similar, se determinaron 86,45% de Ni, 9,84% de P, 1,96% de Al y 1,75% de O mediante análisis EDS (Fig. 7). Por lo tanto, el contenido de níquel en los revestimientos compuestos se puede calcular como 33,5 gy el MTO del baño compuesto es 4,2. A partir de los resultados de la prueba de ciclo periódico, el ciclo de servicio del baño de revestimiento compuesto es 1,4 MTO menos que el del baño de revestimiento de Ni-P no electrolítico. Significa que nano-Al 2 O 3 las partículas reducen la vida útil del baño de galvanoplastia no electrolítico. Sin embargo, el Ni-P-Al 2 O 3 el revestimiento compuesto todavía tiene una aplicación potencial en el campo de las aleaciones de magnesio.
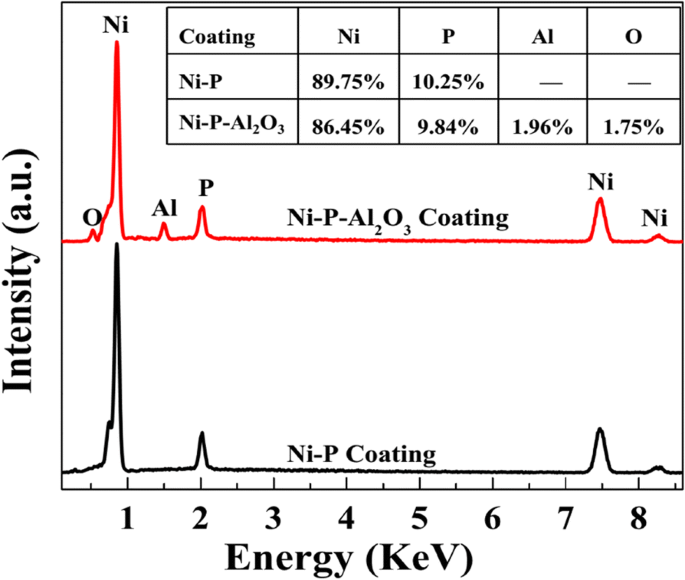
Los espectros EDS del recubrimiento Ni-P y Ni-P-Al 2 O 3 revestimientos compuestos
Conclusiones
En resumen, obtuvimos un baño de recubrimiento compuesto no electrolítico y las condiciones de funcionamiento para depositar conjuntamente el Ni-P-Al 2 O 3 recubrimientos sobre aleación de magnesio, es decir, 35 g / L NiSO 4 ⋅6H 2 O, 35 g / L de ácido láctico, 30 g / L de Na 2 H 2 PO 2 ⋅H 2 O, 10 g / L de NH 4 HF 2 , 10 g / L de nano-Al 2 O 3 partículas, 3 mg / L de agente estabilizador y pH =6.0 ~ 6.5, T =85 ° C, y velocidad de agitación a 350 rpm. La caracterización morfológica y el análisis de la estructura de fase de los recubrimientos compuestos demostraron que nano-Al 2 O 3 las partículas tuvieron una influencia importante en el proceso de crecimiento y las estructuras de fase (espaciamiento del plano cristalino y tamaño de grano) de los recubrimientos. 3,6% en peso de Al 2 O 3 El contenido mejoró eficazmente la microdureza y la resistencia a la corrosión del revestimiento de Ni-P. Además, la prueba de adhesión mostró que casi no había diferencia entre el revestimiento de Ni-P y el de Ni-P-Al 2 O 3 revestimiento. La prueba de vida útil identificó que el MTO del baño de recubrimiento compuesto no electrolítico era de aproximadamente 4. En una palabra, Ni-P-Al 2 electrolítico O 3 el revestimiento compuesto es una tecnología importante para expandir la aplicación de la aleación de magnesio.
Abreviaturas
- E 0 :
-
Potencial de circuito abierto
- i corr :
-
Densidad de corriente de corrosión
- Mg:
-
Magnesio
- MTO:
-
Rotación de metales
- Ni-P:
-
Níquel fósforo
- SEM:
-
Microscopía electrónica de barrido
- XRD:
-
Difracción de rayos X
Nanomateriales
- Propiedades y usos del contrapeso de aleación de tungsteno
- Propiedades y usos de las bolas de aleación de tungsteno
- Propiedades y aplicaciones de la aleación de cobre de tungsteno
- Aplicaciones y propiedades de la aleación de tungsteno, níquel y hierro
- ¿Qué es la aleación de cobalto y cuáles son las propiedades de la aleación de cobalto?
- Propiedades del aluminio y características de la aleación
- Preparación y propiedades magnéticas de nanopartículas de espinela de FeMn2O4 dopadas con cobalto
- Hacia los nanofluidos de TiO2:Parte 1:Preparación y propiedades
- Compuesto híbrido Nanoestructurado de sílice / oro-celulosa-Amino-POSS mediante el proceso Sol-Gel y sus propiedades
- Propiedades y aplicaciones de la aleación de cobre y níquel
- VDM® Aleación 40 B