Supervisión de la fabricación aditiva con un micrófono óptico
Las tecnologías de fabricación aditiva (AM) han tenido una notable adopción en la industria en los últimos años. A medida que la digitalización y la fabricación bajo demanda cambian el aspecto de los sitios de producción hacia líneas operativas completamente automatizadas, los métodos confiables de monitoreo de procesos se vuelven cada vez más importantes.
En el procesamiento de metales basado en láser, es un hecho bien conocido que la emisión óptica y acústica durante el proceso se puede analizar en tiempo real y correlacionar con la calidad final de la pieza. 1,2,3 Este enfoque ofrece un valor significativo, ya que la aparición de poros, grietas u otras faltas de homogeneidad creadas durante el proceso de producción influyen en gran medida en las propiedades mecánicas y aumentan el riesgo de componentes defectuosos. La reacción inmediata a las señales de advertencia del proceso puede reducir el material de desecho y ahorrar tiempo.
Hoy en día, los sistemas ópticos, como pirómetros, cámaras de alta velocidad, cámaras de infrarrojos y fotodiodos, se utilizan ampliamente para monitorear procesos de AM basados en láser en contextos académicos e industriales. 4 A pesar de que brindan información importante sobre la zona de interacción láser-metal, ignoran los aspectos relevantes que suceden después de que el láser se apaga, p. agrietamiento debido al estrés térmico.
Los sistemas de sensores acústicos soportados por estructuras han estado disponibles comercialmente recientemente, por ejemplo, dentro de los procesos de fusión de lecho de polvo (PBF). 5 Sin embargo, los detectores de sonido transmitidos por la estructura enfrentan desafíos cuando se trata de procesos como la deposición de metal por láser (LMD) o la fabricación aditiva por arco de alambre (WAAM) en los que la ruta de la señal ligada a la estructura cambia o incluso puede interrumpirse durante el tiempo de construcción. En tales casos, un sensor acústico acoplado al aire de distancia fija proporciona una solución adecuada.
Una nueva técnica de inspección por ultrasonido
A diferencia de los sensores acústicos convencionales de membrana o piezoeléctricos, el micrófono óptico de banda ancha de XARION Laser Acoustics funciona mediante interferometría. Su principio de detección acinética se basa en ondas de sonido que provocan un cambio en el índice de refracción del aire dentro de la cavidad del interferómetro de 2 mm que se encuentra en la parte superior del cabezal del sensor que se muestra en la Figura 1a. Esto provoca pequeños cambios en la longitud de onda del láser, contenido y reflejado de un lado a otro dentro de la cavidad. La ligera desviación de la longitud de onda provoca una variación de la interferencia y, por lo tanto, de la intensidad de la luz que regresa de la cavidad. A continuación, la variación de intensidad se mide mediante un fotodiodo externo.
Este método de transducción acústica, que funciona completamente sin elementos móviles, proporciona el rango de frecuencia más amplio disponible en el mercado de micrófonos, superando el estado del arte por un factor de 10. Dado que los ruidos de fondo, p. de la maquinaria cercana, normalmente se limitan a frecuencias más bajas (<100 kHz), el rango del micrófono óptico de 10 Hz a 1 MHz permite una separación espectral clara entre la señal de proceso valiosa y el ruido no deseado. El límite superior de esta respuesta de frecuencia está predeterminado en parte por el propio medio, ya que la absorción del aire amortigua considerablemente la propagación del sonido. Por ejemplo, la atenuación de una señal acústica de 2 MHz en el aire es del orden de 640 dB/m. 6
En los siguientes casos, se discuten varias aplicaciones. En todas las configuraciones, la salida eléctrica analógica del sensor se alimenta a un sistema de análisis y adquisición de datos de alta velocidad, que realiza un cálculo FFT en tiempo real y una visualización espectral de la emisión del proceso en el aire.
Deposición láser de metal (LMD)

Un problema común en los procesos LMD es la formación de grietas debido al estrés térmico. Esas grietas pueden ocurrir dentro del tiempo de procesamiento, pero también varios minutos después. El proceso LMD basado en robot, alimentado con alambre o polvo, permite mantener una distancia de medición constante. La ventaja de un sistema acústico acoplado por aire montado en la cabeza del robot es la posibilidad de analizar las señales de la interacción láser-material, así como el comportamiento del material después del láser. En la Figura 2 se muestra un ejemplo de una configuración de medición con una firma acústica correspondiente.
Dado que las señales de grietas tienden a tener una frecuencia de banda ancha, se puede aplicar un filtro de paso alto para detectar con seguridad la aparición de grietas durante y después del proceso sin perturbaciones del ruido de producción. En esta configuración, se aplicó un filtro de 350 kHz a 1 MHz, que mostró la correlación más fuerte con los recuentos de grietas de los métodos de prueba no destructivos de imágenes de rayos X y pruebas de corriente de Foucault, como se describe más detalladamente en la referencia 7.
Fusión de lecho de polvo (PBF)

Para captar la emisión de ultrasonido durante un proceso PBF, el micrófono óptico se colocó dentro de la cámara de construcción, aproximadamente a 30 cm de la placa de construcción, como se muestra en la Figura 1b. En la Figura 3 se muestra una firma de proceso acústico típica, que también demuestra la ventaja del análisis de ultrasonido de alta frecuencia, es decir, la ausencia de reverberación, que en el régimen de frecuencia más baja puede "difuminar" la señal y, posteriormente, la resolución temporal superior del proceso. eventos.
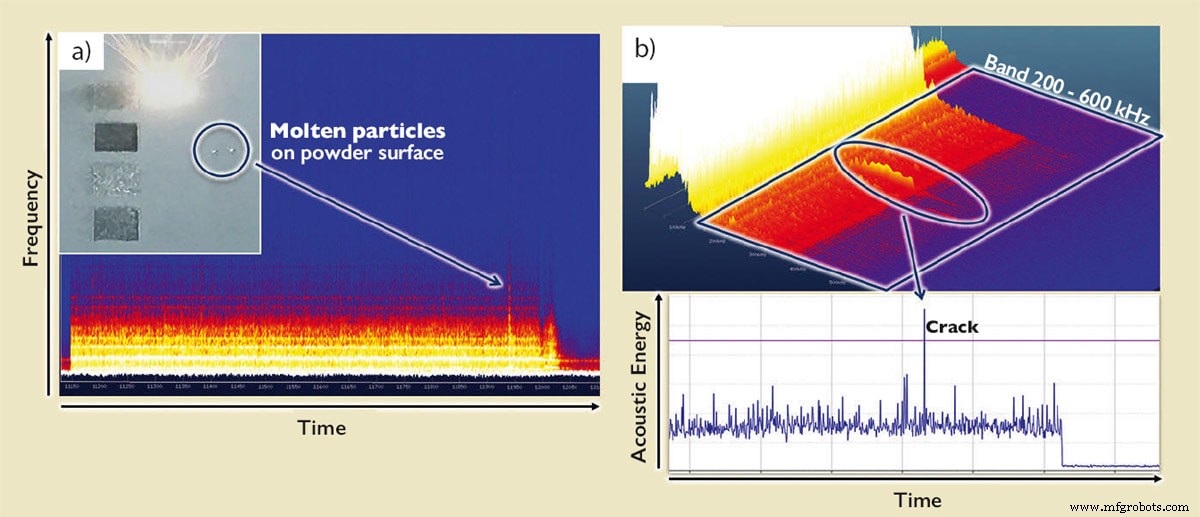
A diferencia de la configuración LMD, PBF emplea galvanómetros de espejo para dirigir el láser de proceso a través del lecho de polvo. Este procedimiento provoca una atenuación de la señal aérea dependiente de la distancia y la frecuencia, que sigue una relación conocida y, por lo tanto, puede tenerse en cuenta si las coordenadas del láser se rastrean simultáneamente. En muchos casos, tampoco es necesario mantener un nivel de tierra de señal constante, p. para la detección de anomalías espectrales a corto plazo. En la Figura 4 se presentan dos ejemplos de estos:La Figura 4a muestra un pico de banda ancha en el espectrograma que se origina a partir de un láser que pasa sobre una partícula fundida en el polvo y la Figura 4b muestra una señal de grieta en la vista del espectrograma 3D (superior) y la respectiva Curva de energía 2D (inferior) integrada en una banda de frecuencia de 200-600 kHz.
Fabricación aditiva por arco de alambre (WAAM)
Se puede aplicar una configuración similar a la de LMD para los procesos WAAM (Figura 5). La firma de la señal acústica difiere mucho, aunque también es de banda ancha hasta 600 kHz. Los fenómenos principales son el ciclo de formación de gotas (bloques distintos que aparecen aproximadamente cada 10 ms), una señal tonal relacionada con la tasa de modulación del arco (aquí:80 kHz) y la emisión de proceso de banda ancha, relacionada con la evaporación del metal.

Dos de los parámetros más críticos para el proceso son la estabilidad del arco y el ciclo de formación. Para monitorear el primero, se puede aplicar un filtro de paso de banda estrecho a la frecuencia de modulación y sus armónicos más altos, y para el último, se puede realizar un análisis FFT en la señal de tiempo filtrada de paso alto, para calcular la tasa de gota comparativamente lenta. sin ruido de fondo.
Conclusión
A través de la disponibilidad de un micrófono de banda ancha sin membrana para las frecuencias ultrasónicas más altas, ahora se puede aprovechar y utilizar información previamente inaccesible para monitorear fenómenos de procesos acústicos en tiempo real. Los desarrollos futuros implican la aplicación de la triangulación para que los orígenes del sonido puedan localizarse para facilitar aún más a los operadores, ingenieros de procesos y fabricantes de máquinas la detección de posibles defectos. Además, se apunta a la inclusión de métodos de IA integrados que se presten a flujos de datos acústicos y faciliten el avance de la tecnología hacia aplicaciones de monitoreo industrial más complejas.
Reconocimiento
Los autores agradecen el apoyo de AIMEN Technology Center (España) y Damon Northeast (Renishaw plc).
Referencias
- D. F. Farson y K. R. Kim:Generación de emisiones ópticas y acústicas en penachos de soldadura láser , Diario de Física Aplicada 85, 1329 (1999);
- M. Bastuck et al.:Überwachung und Qualitätssicherung des Laserschweißprozesses ultrahochfester Karosseriestähle durch integrierte ZfPVerfahren , DGZfP-Jahrestagung – Mi.2.A.4 (2013);
- J Shao e Y Yan:Revisión de técnicas para el monitoreo e inspección en línea de soldadura láser , Journal of Physics:Serie de conferencias 15, 101–107 (2005)
- S. Everton et al.:Revisión del monitoreo de procesos in situ y metrología in situ para la fabricación aditiva de metales , Materiales y Diseño 95 (2016) 0431-445
- Anas Essop, 3D Printing Industry, 10 de diciembre de 2019, consultado el 26 de junio de 2020.
- M. Bajo, Absorción Atmosférica del Sonido, JASA (1990)
- Camilo Prieto et al.:Monitorización de procesos in situ mediante micrófono óptico para la detección de grietas en aplicaciones de Deposición Láser de Metales, datos de medición del Centro Tecnológico AIMEN (España) , Conferencia LANE, entrada de papel industrial (2020)
Este artículo fue escrito por Martin Ursprung, ingeniero de aplicaciones; Thomas Heine, director de I+D; Balthasar Fischer, director ejecutivo; Wolfgang Rohringer, ingeniero de desarrollo; y Ryan Sommerhuber, ingeniero de aplicaciones, XARION Laser Acoustics GmbH (Viena, Austria). Para obtener más información, comuníquese con el Sr. Sommerhuber en Esta dirección de correo electrónico está protegida contra spambots. Necesita habilitar JavaScript para verlo., o visite aquí .
Sensor
- Fabricación de aditivos líquidos:construcción de objetos 3D con líquido
- Fabricación aditiva frente a fabricación sustractiva
- Ventajas de la fabricación aditiva
- Mejora de la fabricación aditiva con ingeniería inversa
- 5 consejos para ayudar a su empresa a tener éxito con la fabricación aditiva
- Proceso frente a fabricación discreta
- 4 aplicaciones que debería producir con fabricación aditiva
- El proceso de fabricación aditiva
- ¿Qué es la fabricación aditiva? Comience con la impresión 3D
- Stratasys:Ser más sostenible con la impresión 3D
- Fabricación aditiva en la industria aeroespacial