Los módulos OptiPath y Force de CGTechs demuestran ser complementarios
Hace tres años, el desarrollador de software de Vericut, CGTech, habló con los programadores Don Lahr y Mike Triplett del taller de trabajo aeroespacial y médico Ultra Machining Company (UMC) sobre su uso del módulo de mecanizado basado en el conocimiento OptiPath de Vericut. Los hombres habían instalado recientemente una actualización que incluía una personalización que le habían pedido a CGTech que hiciera en su nombre.
La solicitud de mejora, Vericut SCR n.° 16986, simplificó los cambios de velocidad de alimentación a través de variables macro accesibles para el operador, optimizó las configuraciones y eliminó la necesidad de involucrar a la oficina de programación para un ajuste variable simple.
Lahr y Triplett todavía están en UMC hoy, al igual que Cory Mahn, un empleado de 12 años que se unió al departamento de programación poco después de la actualización de personalización. En ese momento, hubo una discusión sobre el módulo Force recién lanzado de CGTech, una herramienta de optimización de trayectorias basada en la física que se dice que reduce los tiempos de ciclo en un 25 % o más, pero UMC no tenía planes inminentes de implementación.
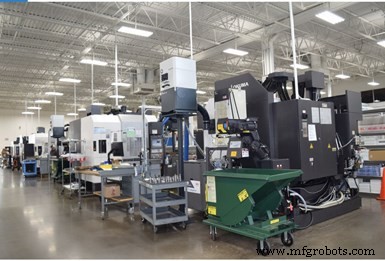
UMC, un taller de trabajo aeroespacial y médico en Monticello, Minnesota, alberga docenas de modernas máquinas herramienta CNC. La empresa ha utilizado Vericut de CGTech durante más de 15 años.
Esos planes cambiaron en febrero de 2020, cuando la empresa realizó su primera prueba de Force en un trabajo bastante prolongado. “Recortamos alrededor de un 10 % del tiempo de ciclo en ese número de pieza, lo que terminó ahorrando a la empresa casi $13,000”, dice Lahr. Los resultados fueron lo suficientemente impresionantes como para que la alta gerencia aceptara invertir en el software. "No es un ahorro tan grande como los que hemos logrado desde entonces con Force, pero definitivamente abrió algunos ojos al valor de seguir adelante".
La pieza de trabajo en cuestión es un componente médico hecho de acero inoxidable 304L que mide aproximadamente 2 × 3 × 0,5 pulgadas. La herramienta más grande que usó UMC es una fresa de extremo de carburo de cuatro ranuras de 0,75 pulgadas, la más pequeña de solo 1/32 de pulgada, con profundidades de corte axial de 0,001 o 0,002 pulgadas por pasada. Lahr señala que Force brindó el mayor beneficio durante las operaciones de desbaste y semiacabado, pero agrega que incluso con herramientas muy pequeñas como las descritas anteriormente, ayudó a optimizar las trayectorias de la herramienta hasta el punto de que la rotura del cortador se redujo a cero mientras que el tiempo de ciclo a menudo mejoraba. . "Definitivamente también hay un beneficio para la vida útil de la herramienta", agrega.
Actualizaciones del sitio y un impulso de automatización
Los cambios recientes en UMC también influyeron en la decisión de la empresa de comenzar a usar Force. La empresa todavía se encuentra en su segunda generación de propiedad familiar, pero el número de empleados se ha duplicado a casi 200 personas. También ha aumentado el número de máquinas herramienta CNC. Ahora hay un puñado de centros de mecanizado verticales de cinco ejes Okuma M460V-5AX, un par de centros de mecanizado verticales de cuatro ejes MB-46VAE de Okuma y tres centros de mecanizado de cinco ejes Matsuura MX-520, dos con grupos de palets de cuatro estaciones.
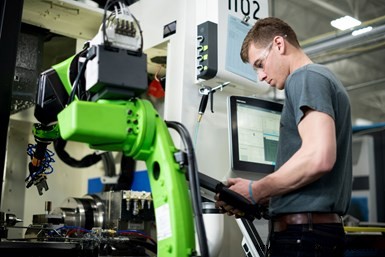
Debido a la escasez de mano de obra calificada, UMC y otros talleres descubren que la atención automatizada de máquinas se vuelve más importante con cada año que pasa.
A pesar del mayor número de empleados, la automatización del taller va en aumento. “Es difícil encontrar trabajadores calificados, por lo que hemos estado agregando robots a algunos de nuestros tornos y fresadoras”, dice Mahn. “Esto brinda la oportunidad de funcionar con poca atención o incluso sin supervisión en algunos casos, a pesar de que el tamaño de nuestros lotes es bastante pequeño. También hemos mejorado nuestra sujeción de piezas en algunas de las máquinas y estamos preconfigurando las herramientas fuera de línea”.
Comparación de OptiPath y Force
En el momento de escribir este artículo, la empresa ha optimizado 20 números de pieza diferentes con Force. Hasta ahora, las mejoras en la duración del ciclo han oscilado entre el 3 y el 28 %, pero Lahr se apresura a señalar que UMC recuperará su inversión tres o cuatro veces durante el primer año.
Quienes estén familiarizados con la optimización de trayectorias podrían preguntarse:si UMC ya estaba usando OptiPath, ¿por qué invertiría en Force? Después de todo, ambos productos prometen tiempos de ciclo más cortos y una vida útil mejorada de la herramienta, y ambos resuelven problemas con la desviación del cortador, vibraciones en las esquinas y eventos de mecanizado igualmente indeseables. ¿Significa esto que la inversión de UMC en OptiPath fue una pérdida de dinero? En absoluto, explica Gene Granata, gerente de producto de CGTech para Vericut.
“Force y OptiPath son productos diferentes que utilizan diferentes enfoques para la optimización, pero cada uno se complementa con el otro”, dice. “OptiPath, por ejemplo, no realiza ninguna medición de las fuerzas de corte. En su lugar, utiliza un método volumétrico de optimización o uno que mide el grosor de la viruta. La fuerza también mide el grosor de la viruta, pero tiene controles y equilibrios adicionales, incluido el control de las fuerzas de corte o la potencia del husillo, y predice la desviación de la herramienta. En cualquier caso, la eliminación de material se mantiene constante mediante el ajuste de la velocidad de avance y la subdivisión de los movimientos de la trayectoria según sea necesario para mantener unas condiciones de mecanizado casi ideales constantes para cada herramienta”.
Diferentes herramientas para diferentes situaciones
En última instancia, ambas piezas de software tienen sus propios casos de uso óptimos. Granata sugiere usar Force en materiales duros y difíciles de mecanizar, donde los picos leves e instantáneos en las cargas de herramientas pueden significar grandes problemas con los cortadores y los husillos de la máquina. Por otro lado, recomienda OptiPath para metales blandos como el aluminio, el acero dulce y el hierro fundido gris, donde el objetivo principal es limpiar el material lo más rápido posible (en lugar de mantener una carga de viruta constante), o para situaciones en las que el corte de la herramienta las condiciones nunca se acercan a niveles inseguros de fuerza de corte o potencia del husillo.
Según Granata, muchos clientes de OptiPath continúan usando sus estrategias OptiPath probadas y verdaderas cuando comienzan a usar la optimización Force, especialmente con materiales más duros o difíciles de mecanizar, y usan OptiPath cuando cortan con ciertas herramientas que favorecen este método de optimización. Dicho esto, enfatiza que no existe un enfoque único para la programación.
“Depende de las estrategias que prefieran los usuarios”, dice. “Si es un usuario avanzado de OptiPath, probablemente sería más apto para agregar Forzar optimización a su licencia de OptiPath e invocar ambas. herramienta por herramienta, cuál usar. Los programadores pueden incluso cambiar las estrategias durante una ruta de herramienta para lograr la optimización más efectiva. Los dos son complementarios para ofrecer la mayor cantidad posible de estrategias de optimización".
Las experiencias del equipo de programación de UMC parecen respaldar esta teoría. Mahn señala que Force ha reducido aún más el tiempo de ciclo en un promedio de 5 a 6 % en los trabajos que el equipo ejecutó anteriormente a través de OptiPath. Como beneficio adicional, Mahn y Lahr también descubrieron que Force reduce el tiempo total de programación. “Con Force, no necesitamos ser tan exactos con la creación de trayectorias en nuestro software CAM”, dice Lahr. “Quizás el ajuste más grande para mí ha sido dejar que Force haga lo suyo. A menudo sugerirá una velocidad de alimentación que es al menos el doble de lo que yo hubiera usado, pero si lo dejas pasar, Force lo hace bien”.
Equipo industrial
- Rutronik:módulos y SoC inalámbricos multiprotocolo de Redpine Signals
- Timken adquirirá los rodamientos QM y la transmisión de potencia
- Fabricación aditiva con composites en la industria aeroespacial y de defensa
- Historia de éxito:rápido ROI y crecimiento de la empresa
- Tres pasos para gestionar el riesgo de proveedores y la fuerza mayor
- Las 5 principales características distintivas de un equipo experto y líder en fabricación de moldes
- Torno Toolroom
- Torno CNC
- Empresa de servicios de Internet y telecomunicaciones, WBL Services, implementa Fluke Connect®
- ¿Qué es la interoperabilidad y cómo puede lograrla mi empresa?
- Diferencias entre mantenimiento preventivo y correctivo